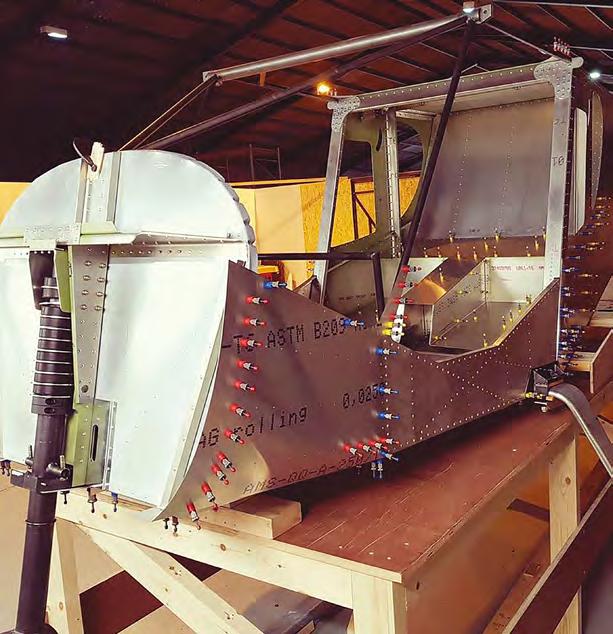
17 minute read
PROJECT NEWS
Zenith CH 750 (LAA 381-15664)
An initial report by Tim Bridge
Nuncats is a registered Community Interest Company (CIC) established to change the shape of E-Mobility in developing countries. They have the blessing of, and indeed have partnered with, the Zenith Aircraft Company to develop an electric power system for an otherwise almost standard Zenith CH 750, plus an off-grid charging station to suit. Their goal is that the whole system could be used to provide really useful rural transport and medical supplies in areas where fuel, roads and infrastructure are a problem in general. The airframe is under construction now and they have just started on the first of the power system elements.
The key aim of the project is to demonstrate the viability and utility of electric powered flight, using cost effective and existing technology. Subsequently, supplying the home market on a commercial basis would then allow charitable organisations to be supplied at cost.
There are NGOs in Africa working on health and conservation projects on tight budgets and in very remote locations, using light aircraft as flying jeeps. Totally ‘off grid’, the supply of fuel can be a challenge, and these aircraft need to be cheap, rugged and easily maintainable. In this environment, some of our Permit to Fly types could be made perfectly suitable.
Rural solar generation is not uncommon in much of Africa and, by tapping into that existing infrastructure, an energy source is potentially available to fuel such an aircraft – after all, sunshine is far more widely available than avgas in the bush.
There are many projects underway by big names in the aerospace world to produce fast, efficient, loadcarrying prototype electric aircraft, stretching the limits of current knowhow to eke out that last little bit of performance. Nuncats’ approach is different. Why design a new aircraft when they can work with what currently exists, sacrificing leading edge performance for economy and quickly bringing it to market. We know it takes a long time for a new type to be developed, so what’s the point for a small gain in efficiency? Its premise is to use what’s already out there and that includes the airframe. As an aside, consider any airfield, many of the aircraft are decidedly vintage, these older craft are unlikely to be scrapped any time soon, so even some of these could be electrified.
For bush operation, an aircraft needs to be rugged and repairable, a delicate composite tadpole would probably not last past the first inevitable mishap – nuts, bolts, pop rivets, aluminium and straight lines make for a much more maintainable structure. The Zenith CH 750 and similar models are just the sort of ‘jeep’ that are needed, and there are a number in the theatre already.
The creative focus in this project is almost purely firewall forward, where an electric motor with sufficient power to replace a Rotax 912 is a tiny affair – imagine a stack of six to eight dinner plates and you just about have the shape and size. So, a new motor mount will be required, and this may well be longer than the original item, and as a result, new cowlings will need to be moulded. All of that space between the firewall and motor can then be filled with power electronics and some of the battery storage. Above The fuselage ready to come off the bench and onto its wheels. Photo: Tim Bridge Meeting 100-hour services in the middle of nowhere also presents its challenges, so the almost total lack of a frequent maintenance requirement upon an electric motor, with perhaps two moving parts as opposed to hundreds within an internal combustion engine, also benefits remote aircraft operation.
Apart from building the airframe, they will create a total system where a practical and useful electric aircraft is the outcome of the project. It is a fact that today the energy density of petroleum spirit cannot be matched by batteries, and it possibly never will. Equally, the simplicity of refuelling by pouring that energy dense liquid into an aeroplane’s fuel tank will be hard to match.
So, their solution is for multiple yet manageable battery packs that are rapidly swapped at turnaround to provide a reasonable range. They even envisage the possibility of a partial battery load so that fuel can be traded for luggage as we would consider in current aircraft.
Solar powered charging stations will hold spare battery packs at the various stop off points along the regular route, with future plans to develop automatic reporting of their charge and availability status by radio or over the internet. Consequently, a modest range of 50 to 70 miles is perfectly adequate to fly a route that is effectively several hundred miles, but made up of multiple legs, as are the existing missions flown by charities. These outlying charging stations, a mesh network, can then take days or perhaps all week to replenish the packs deposited there. This might not be flight as we currently know it but it would enable off grid operations that can both save and improve lives. Closer to home, the endurance would be very suited to flying school one-hour training slots.
While the technology is being sourced and developed, Tim is getting on with the build of the airframe at a good rate of knots.
Started only in January, the fuselage has progressed to a rolling shell, ready for the work to commence firewall forward. He already has three airfields, two grass and one hard, who have agreed to site remote charging stations. Subject to maintaining progress, they hope to be doing ground power and taxi testing later this year, with a view to being on a permit next spring, flying short hops about the county proving that it can be done cheaply and in a way that is robust and sustainable.
You can follow Nuncats’ progress on Facebook, just search for Nuncats. Right Not the final airworthy motor mount, but this will be used for development over the next couple of months. Photo: Tim Bridge
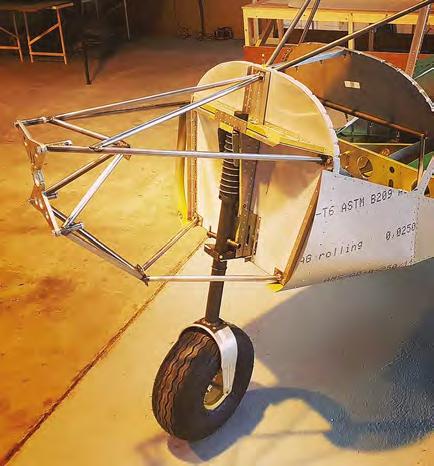
Blue Two
A few more steps further forward and not too many back. By Andy Best
Ido feel a little embarrassed to admit that progress on building Blue Two has been rather slow of late. Like many things in life, the main problem is in your head – subconsciously, I was afraid of breaking the wings during load testing. It sounds a bit pathetic but when you’ve spent countless hours designing, calculating, foam cutting, assembling and doing lay-ups, trimming, sanding, filling, and yet more sanding, you just don’t want to risk wrecking it all. However, reading a few stories of in-flight break-ups puts things into perspective. It has to be done, so I must get on with it.
As a reminder, Blue Two is a 450kg microlight built to BCAR section ‘S’ but also uses some of the load requirements from CS VLA for good measure. Their control surface loading graphs are particularly useful and, as Francis says, they save endless amounts of ‘discussion’ about load levels. The wing area is 113 sq ft and a Rotax 912S provides the power. The structure is from blue foam (Dow Chemical’s Floormate @ 34 kg/m³) sandwiched between Below Progress as of late last summer, an attractive and unique aircraft. Photo: Andy Best layers of carbon fibre, mainly 160 and 200 gm/sq m twill from R-G.de in Germany. The only fibreglass used is the UNI cloth in the main undercarriage legs, which gives them about three times the flexibility of equivalent carbon fibre parts.
The picture of the overall assembly shows where I have got to. All that’s required is to finish the wings, seats, canopy and the wiring, which unless I have a failure of the wings under test, should be completed by the end of the summer (I hope). The engine bay is quite compact and was challenging to complete, but with the world’s most complicated engine installation ever invented by mankind, this was to be expected. In an attempt to reduce cooling drag, the radiator, which has a seven-row oil cooler fastened behind it, has its own airflow ducting. Time will tell whether I have got the duct sizes right. The stainless exhaust was bought as a kit of parts from Aeroweld Ltd., in the Czech Republic for €478. After cutting the tubes and clamping them together (with jubilee clips and metal
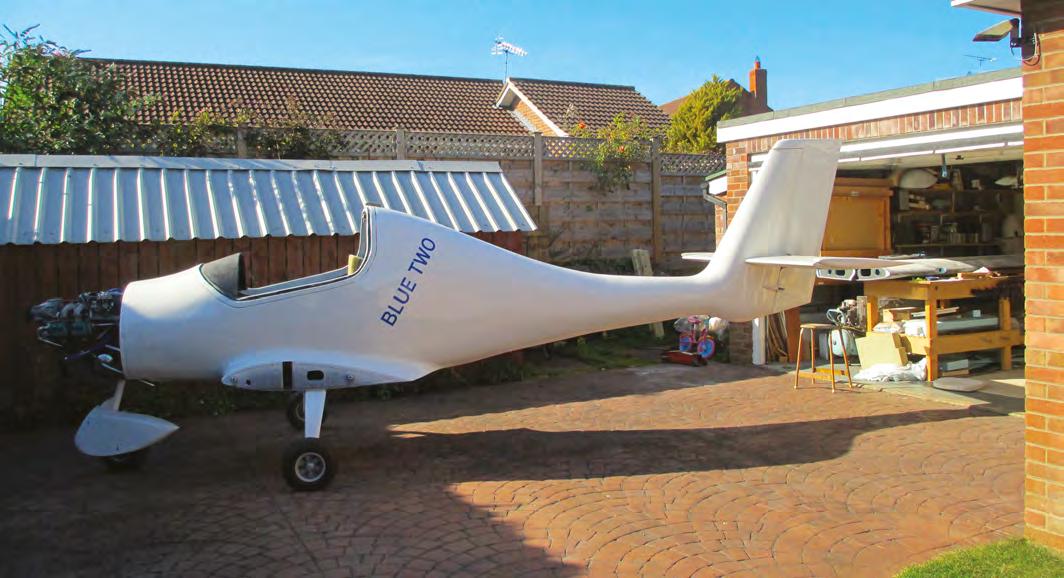
strips) the pipe assemblies were TIG welded by a local rally prep shop.
And so, onto the wiring. Solder or crimp, that is the question. I found convincing arguments for both, so in the end I decided to do both, initially soldering, then crimping over the soldered joint and the insulation and finally covering the connection with heat shrink sleeving. After what seemed like years of sanding, it was quite a pleasure to do the wiring, but it does require some concentration and constant checking. As can be seen from the picture, it rapidly becomes chaotic looking. My advice now would be label everything and buy two to three times the amount of wire that you first think you need. The coloured aviation cable (not PVC) came from Parts4Aircraft. I have tried to keep all the electrical items which are normally found in the engine bay, inside the relatively cool and clean cockpit area. This is not normally a sensible thing to do, as access can be difficult, but because the instrument panel is integral with the canopy surround (like most gliders) and moves out of the way when the canopy opens, access here is OK. The final picture shows the dreaded wing test rig. The wing is mounted upside down so that it can be loaded in the +ve ‘g’ sense. Loading it to just the limit load of 4g (i.e. the maximum load it would normally see in service) requires approximately 1.4 tonnes to be applied, so you can see why the test structure, which simulates the fuselage, is fairly hefty (and why I am nervous). I live in hope and vow to keep going. Right This will be a tightly cowled engine, very neat. Photo: Andy Best
Below right Unusually, most electrical components are mounted on the ‘cool’ side of the firewall, but the panel has hinged up out of shot with the open canopy. Photo: Andy Best
Below The wings mounted off aircraft so that they can be tested to maximum flight load. Photo: Andy Best
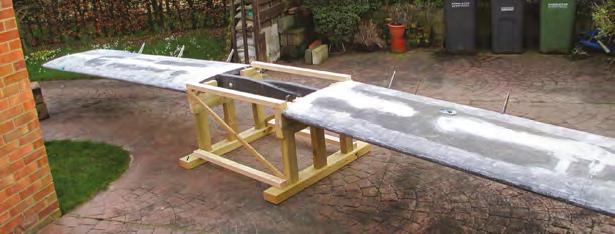
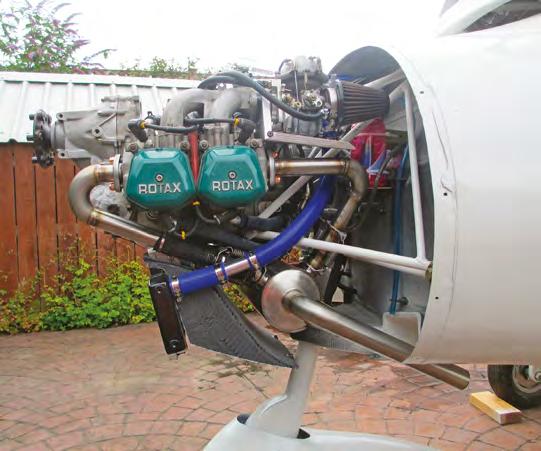
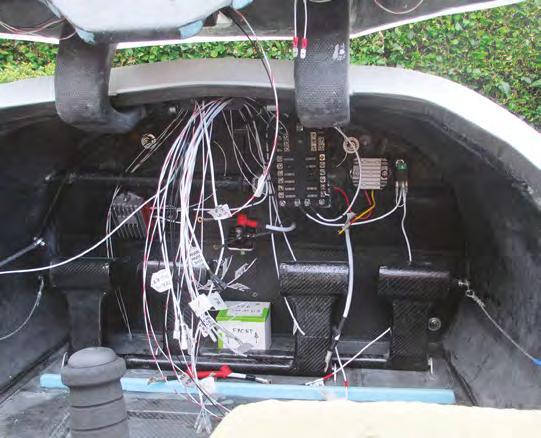
G-CLMZ (s/n 252) Fairchild 24W-41A
By Tony Whitehead
So, with my much loved and enjoyed Morane Saulnier MS.317 moving on to new owners, I had a think about what’s next, the restoration project in the workshop would be a while yet so I casually started looking with a small budget. Nothing much sparked my interest in Europe so the USA beckoned, also, it was going to be hard giving up that glorious Radial engine growl!
I had been keeping an eye on the Fairchild for a while and was surprised it had not sold. It turned out there was an interested party, who was dragging his heels. I left it for a while and conducted more research, finally getting the go ahead for an inspection some weeks later. This I had carried out for me by a local Florida firm, as it was much cheaper than flying out there myself. The inspection was encouraging and after much soul searching and acceptance by the LAA for this Fairchild, I negotiated a deal. Later that day the owner got in touch asking if I had second thoughts! Turns out the previously interested party made an offer 20 minutes after we agreed a deal! My offer and acceptance were honoured, thankfully.
Then the fun began. I had previously obtained quotes from Neel Aviation for shipping from his Lakeland base, but unfortunately the owner cancelled his insurance and was unable to deliver. Meanwhile, Hurricane Dorian threatened Florida and the owner was pushing for payment, needless to say that was delayed.
The ferry job from Indiantown to Lakeland was very kindly sorted by Charles Stence, the aircraft’s maintenance engineer. The price being fuel only, a welcome gesture, plus an insurance contribution. He used an EAA scheme, UK insurers wouldn’t touch it!
Dismantling and shipping went without a hitch. I requested delivery to Barton, my home field, with a crane equipped lorry, which added several hundred pounds to the cost but helped make the unloading relatively easy. The UK handling agents, Ligentia, were very helpful, including arranging the pre-payment of VAT etc. There is no duty to pay and only five per cent VAT
on an Antique. UK registration was straightforward, insurance cover from the LAA scheme very reasonable, and re-assembly was made straight forward by careful labelling of parts at the time of packing.
A major service and very detailed inspection were carried out, plus many small improvements and a general tidying up, and the task was pretty much complete. There were a couple of horrible jobs thrown in, the rubber fuel pipes connecting the fuselage to the wings were rock hard and required replacing. These had been removed for shipping and were labelled appropriately with the additional comment of ‘good luck’! It was a tortuous job. Below Gently does it, modern containers are a great way to transport an aircraft. Photo: Steve Grimshaw
Bottom The Fairchild in the hangar and ready for inspection and re-assembly. Photo: Steve Grimshaw A couple of flap cables were not up to scratch, again a time consuming and fiddly job. But overall, the aircraft and engine were found to be in extremely good condition, in fact better than expected condition if not cosmetically perfect, but I love the used original look.
Paperwork forms from engineering for the application were provided, then more forms for jobs done, history etc., enough to fill a small book. The Permit to Test arrived and was very welcome, and having flown now for a couple of hours, I am happy to report no snags and lots of fun. The Fairchild is showing huge potential, vintage aircraft really are incredible value for money.
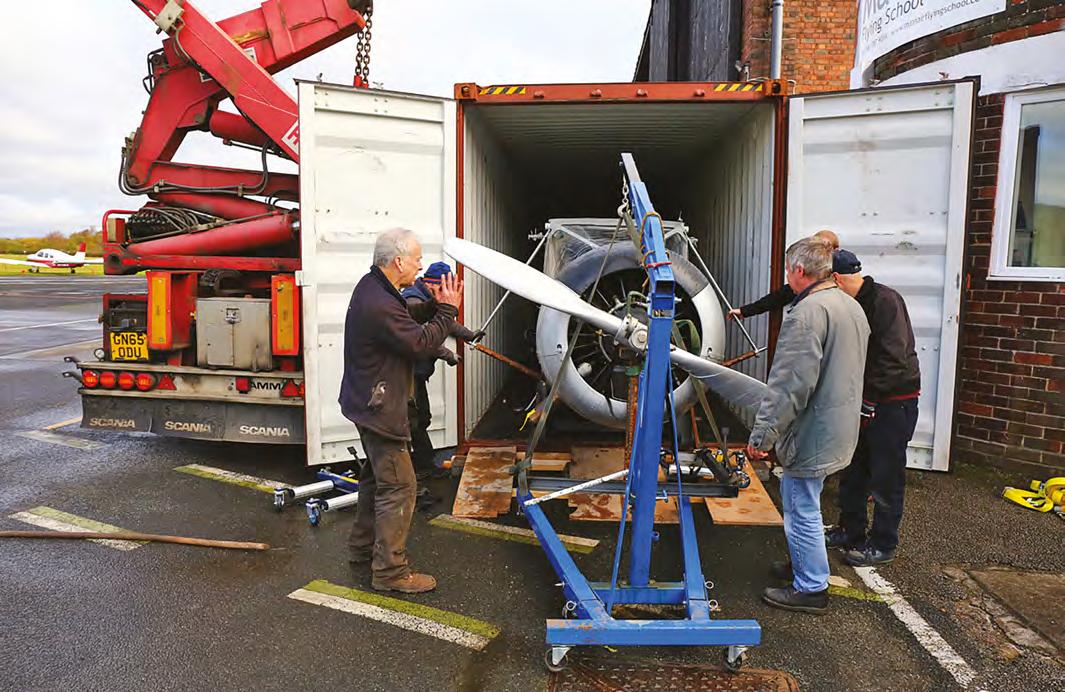
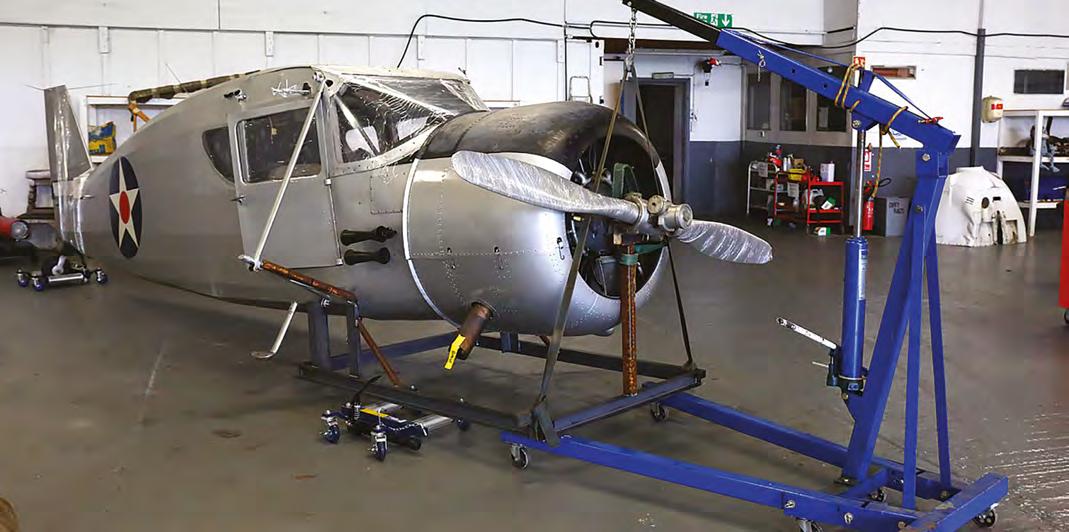
So, importing from the USA – having gone through the process twice now, I’d suggest that it’s not for the fainthearted. Reliable shippers etc. are very important, and Neel Aviation’s work was superb, absolutely no damage and very thorough. The advantages are vintage aircraft at a fair price.
In the UK, obviously early contact with LAA Engineering is critical, thank you Francis, and most important I think is your LAA Inspector. Those who know Nigel Jones will be aware as to why he is so highly respected, he was a huge help. Completion of testing is now at the whim of the weather. For a little background, Fairchild Model UC-61, Serial No. 41-38806 W41A-252 was manufactured by the Fairchild Below Back in her correct environment, the Fairchild on her first flight in the UK. A great looking aircraft now on the LAA register. Photo: Craig Duffy Engine and Airplane Corporation and delivered to the USAAF on 20 December, 1941.
Military service was mainly in Florida until September 1944, when it was dropped from the USAAF inventory and turned over to the Reconstruction Finance Corporation for disposition.
Accepted by the FAA for civilian use, the aircraft has had many subsequent owners in the US. In 1969 the Warner Scarab engine was removed, and the Jacobs R-755 engine and Hamilton Standard constant speed propeller installed. The total hours for the airframe are very low at less than 1,150.n
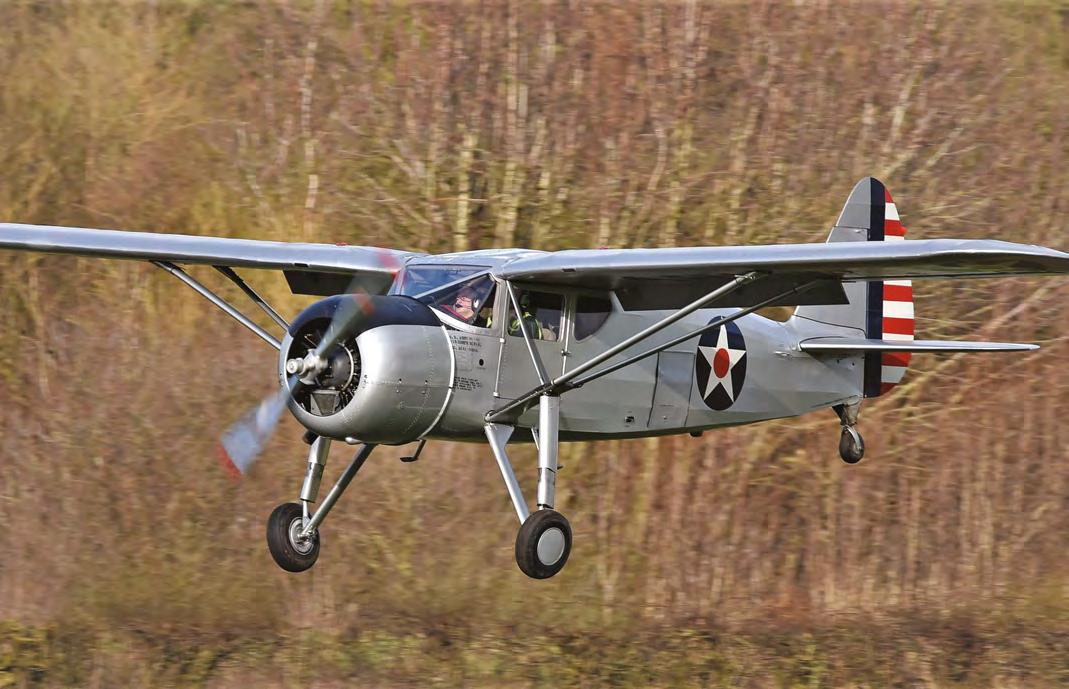
New Projects
If your aircraft has been featured in the New Projects list, please let Project News know of your progress at: projectnews@laa-archive.org.uk
n Sling 4 TSi (LAA 400A-15693) 25/2/2020 Mr S A Lamb, Nettlestead Lodge, Maidstone Road, Paddock Wood, Kent, TN12 6DA n Van's RV-8A (LAA 303-15692) 19/2/2020 Mr K Wingate, 16 Buckwell Road, Kingsbridge,
Cleared To Fly
If your aircraft has featured recently in the magazine and has subsequently completed its maiden flight, Project News would like to hear from you at: projectnews@laa-archive.org.uk
G-CLMZ Fairchild 24W-41A (s/n 252) 20/2/2020 Peter Whitehead. Address held by the LAA. South Devon, TQ7 1NQ n Eurofox 912(S) (LAA 376-15691) 18/2/2020 Mr J A Thomas, Rose Haven, Bourne Lane, Ham Street, Kent, TN26 2HH n Bristell NG5 Speed Wing (LAA 38515690) 17/2/2020 Mr J C Simpson, Badgers, Bower Lane, West Chiltington, West Sussex, RH20 2RH n Sling 4 TSi (LAA 400A-15689) 14/2/2020
n G-ERMN Staaken Z-21 Flitzer (PFA 223-14314) 19/2/2020 Name & Address held by LAA Engineering.
Right An impressive looking Flitzer, awaiting dryer times for flight testing. Photo: Geoff Lloyd Mr A Aliseril Thamarakshan, 6 Beverley Rise, Essex, Billericay, Essex, CM11 2HU n Eurofox 912(S) (LAA 376-15688) 4/2/2020 Dr S Ledingham, Rose Cottage, Temple Sowerby, Penrith, Cumbria, CA10 1SD n Van's RV-10 (LAA 339-15694) 27/2/2020 Name & Address held by LAA Engineering
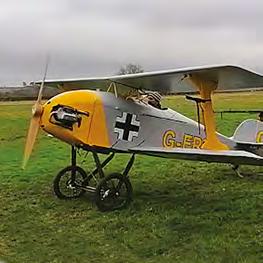
While the technology is being sourced and developed, Tim is getting on with the build of the airframe at a good rate of knots.
Started only in January, the fuselage has progressed to a rolling shell, ready for the work to commence frewall forward. He already has three airfelds, two grass and one hard, who have agreed to site remote charging stations. Subject to maintaining progress, they hope to be doing ground power and taxi testing later this year, with a view to being on a permit next spring, fying short hops about the county proving that it can be done cheaply and in a way that is robust and sustainable.
You can follow Nuncats’ progress on Facebook, just search for Nuncats. Right Not the fnal airworthy motor mount, but this will be used for development over the next couple of months. Photo: Tim
Bridge
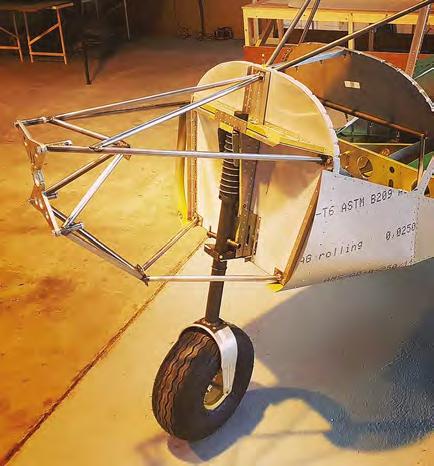
Blue Two
A few more steps further forward and not too many back. By Andy Best
Ido feel a little embarrassed to admit that progress on building Blue Two has been rather slow of late. Like many things in life, the main problem is in your head – subconsciously, I was afraid of breaking the wings during load testing. It sounds a bit pathetic but when you’ve spent countless hours designing, calculating, foam cutting, assembling and doing lay-ups, trimming, sanding, flling, and yet more sanding, you just don’t want to risk wrecking it all. However, reading a few stories of in-fight break-ups puts things into perspective. It has to be done, so I must get on with it.
As a reminder, Blue Two is a 450kg microlight built to BCAR section ‘S’ but also uses some of the load requirements from CS VLA for good measure. Their control surface loading graphs are particularly useful and, as Francis says, they save endless amounts of ‘discussion’ about load levels. The wing area is 113 sq ft and a Rotax 912S provides the power. The structure is from blue foam (Dow Chemical’s Floormate @ 34 kg/m³) sandwiched between Below Progress as of late last summer, an attractive and unique aircraft.
Photo: Andy Best
layers of carbon fbre, mainly 160 and 200 gm/sq m twill from R-G.de in Germany. The only fbreglass used is the UNI cloth in the main undercarriage legs, which gives them about three times the fexibility of equivalent carbon fbre parts.
The picture of the overall assembly shows where I have got to. All that’s required is to fnish the wings, seats, canopy and the wiring, which unless I have a failure of the wings under test, should be completed by the end of the summer (I hope). The engine bay is quite compact and was challenging to complete, but with the world’s most complicated engine installation ever invented by mankind, this was to be expected. In an attempt to reduce cooling drag, the radiator, which has a seven-row oil cooler fastened behind it, has its own airfow ducting. Time will tell whether I have got the duct sizes right. The stainless exhaust was bought as a kit of parts from Aeroweld Ltd., in the Czech Republic for €478. After cutting the tubes and clamping them together (with jubilee clips and metal
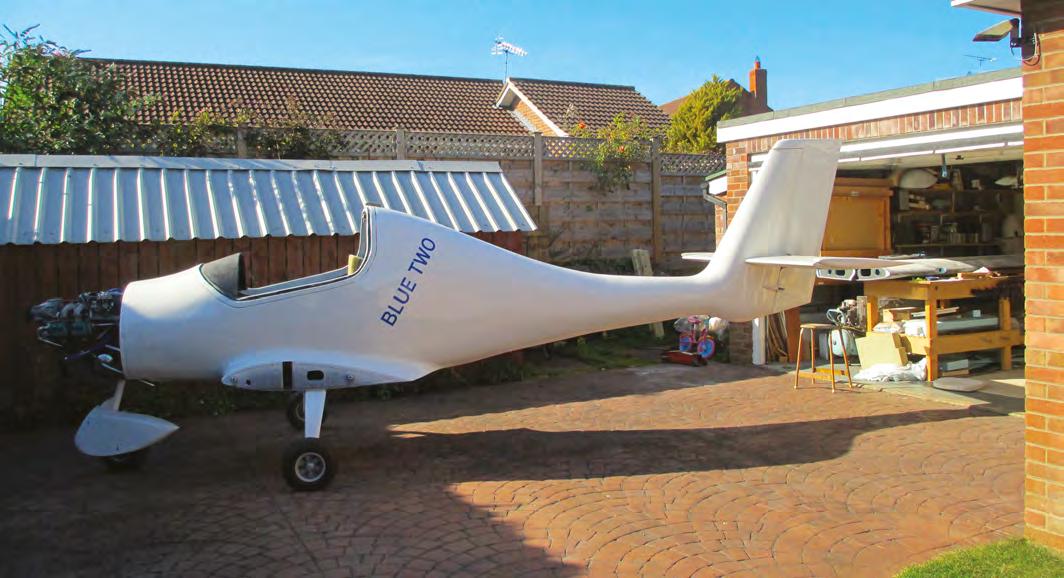