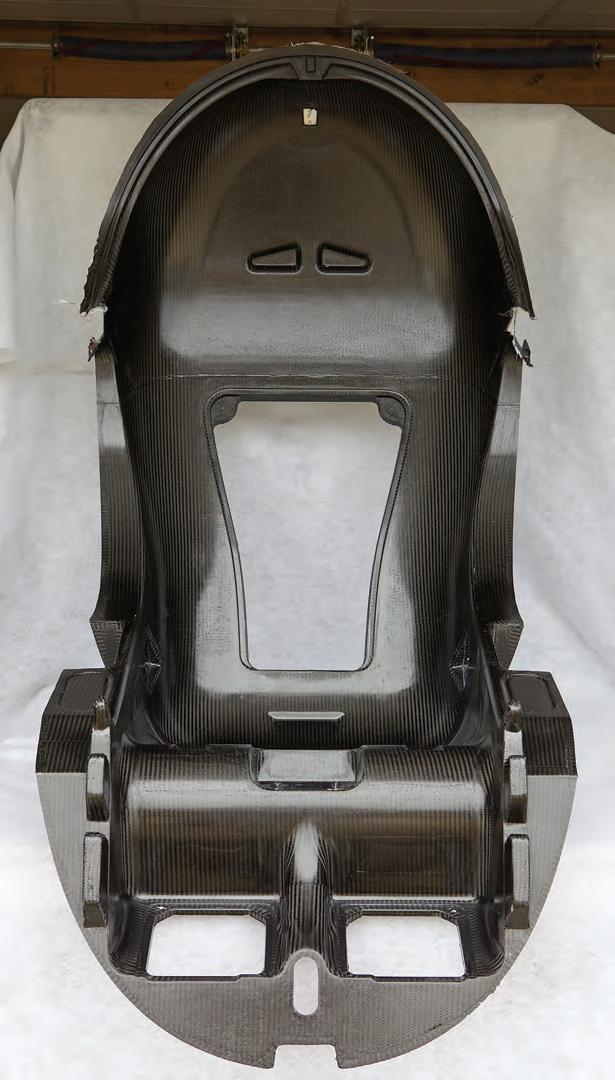
9 minute read
FIBREGLASS REVISION
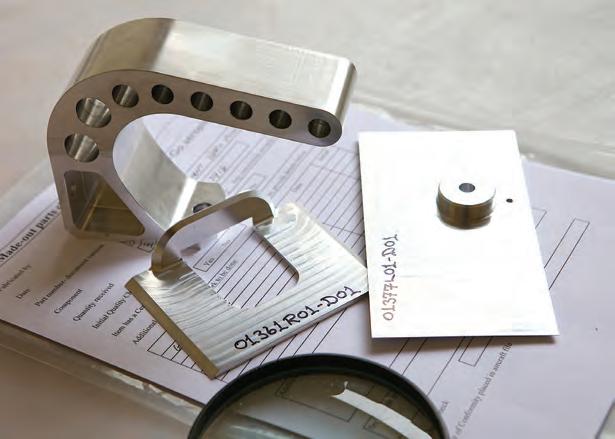
ineffective, partly because of the not very satisfactory brake pedal arrangements. Exactly as predicted, the red coolant temperature caution light came on as I got to the hold, so I activated the cooling fan which quickly brought the temperature back in range.
Getting airborne
Checks complete, I turned to point up Gransden’s grassy slope, and unleashed the full ‘27 horses’. Acceleration was modest, clearly held back by the soggy grass, and I watched the miniature ASI with more than usual interest as we slowly accelerated up the hill. I had been told the canard wouldn’t lift until over 50kt, and until it lifts the wings won’t fly her off. Passing what felt like the runway’s half-way mark, the speed seemed to be creeping through 40kt all too slowly, and with the far hedge now looming in the windscreen, and uncertain of the brake effectiveness, I decided to abort. If in doubt – ask. After a quick conflab with Giotto, in which he confirmed that I was getting full power, and suggesting I make sure not to inadvertently ride the brakes, I had another go using a strip of shorter cropped grass up the centre of the runway. Gritting my teeth while boring past the halfway mark, this time the speed did indeed keep rising, knot by knot. It takes willpower to keep the elevator neutral, knowing that to deflect it prematurely will only cause extra drag and prolong matters further, and you feel a bit redundant just sitting there waiting for the speed to rise. Then as the speed nudged 50kt, in an instant all concerns were dismissed as the canard lifted a couple of inches – six inches – and then the main wheels unstuck and we were away. Mindful of the early reports, I was wary of finding a sensitive elevator or shopping trolley-like directional characteristics as we climbed out, but was happy to find that the e-Go felt perfectly at home now that it was in its natural element.
Inspiring handling
Climbing at 60kt and 7,000rpm, the rotary engine felt smooth, willing and not overly loud, taking us to circuit height at something over 500ft/min. Levelling out under the low overcast, the speed rose to just over 80kt at 7,300rpm, although at this speed we were being bounced around too much for comfort (the effect of that low wing loading) so we were happier (and presumably burning a lot less fuel) at a more modest 70kt at 6,500rpm. Visibility was excellent, other than the relatively small bit of real estate masked by the narrow canard – one’s conscious of the elevators in front of you, moving in unison with your stick movements. At a sensible height you can bring the speed back and back and see the canard working to keep holding the nose up, but eventually the nose will sink gently of its own accord against full back stick, speed indicating about 30kt, with no inclination for either wing to drop. Open the throttle again and she will climb with the stick kept right back – better not try that with any conventionally configured aircraft!
I had seen videos of Keith Dennison manoeuvring the e-Go with gusto, and when you fly it that temptation’s clearly strong, thanks to the combination of powerful but not overly light aileron and elevators, the stall-proof behaviour and the wonderful panoramic view. Rudder and aileron are easily coordinated in lock-to-lock reversals of bank, and with max ‘alpha’ available with no risk of departure, the e-Go is a lot of fun. Or of course, you can cruise straight and level…
Landing
When it came to the landing, I was expecting to find difficulty with a very flat glide, and carefully managed my energy to void overshooting. I need not have worried – with the rudders turned out as airbrakes, and looking for an approach speed of 50kt, we ended up needing to use a bit of power to ‘rumble in over the hedge’ as pre-war fliers used to put it. Which was no bad thing, I prefer to avoid approaching with the engine at idle in case of oiling up the plugs, or with a carburetted engine, icing it up – neither of which helps if you have to unexpectedly go-around.
Taxying back to a grinning Giotto, who freed me from the canopy with the ego-crushing news that I was probably the heaviest pilot to fly an e-Go to date! Knowing Giotto of old, I comforted myself that this was meant as a scientific statement and not intended as a side swipe – I had, after all, just joined a very small elite group of e-Go pilots! Now how to get out? Only then did I realise that the cockpit’s sills are quite high, and raising yourself out will be reminiscent of exercises on the parallel bars in the school gym… actually it turns out to be a non-event, when you can step on the seat. It might be more challenging with classy trimmings and muddy shoes.
In summary
Perhaps the most remarkable thing about the e-Go was how ‘normal’ it felt in flight, despite its very light weight and canard layout. Opposite top left The complex seat moulding is typical of the quality carbon moulding.
Opposite bottom left The alloy parts are also nicely designed and produced. Once in the air, it lacks none of the penetration of a ‘proper’ aeroplane, for this is one SSDR which can buck into a reasonable headwind and still reach its destination without running out of fuel on the way. Overall, I was very impressed by this confidenceinspiring airframe, the powerplant, the cruise performance and the handling. While the controls might seem sensitive when transitioning from a C152 or Cherokee, I didn’t think they stand out as such when compared to those of other single seat homebuilts. With the better brakes now incorporated, the repositioned main gear to shorten the take off, and the other changes the e-Go team had already made, my impression was that the aeroplane would be truly ‘customer ready’.
If only it could be made for that elusive thing, a sensible price, I’m sure it would find many takers – and that is something Giotto is currently researching, so keep an eye out for possible announcements in the not too distant future. ■
E-GO Specifications
General characteristics
Crew: One Span: 8m (26.3 ft) Wing area: 11.5 m2 (123.8 ft2) G limits: +4, -2 Min empty weight: 150kg (303lb) Gross weight: 270kg (594lb) Powerplant: 27hp Rotron e-Go Fuel capacity: 27 litres Performance
Stall speed: Vs 35 KIAS (65km/h) Cruise speed: Vc 90 KIAS (167km/h) Max level speed: Vh 90 KIAS (167km/h) Never exceed sp. Vne 120 KIAS (222km/h) Climb rate: 900ft/min (4.6m/s) Range @ 100 TAS 396nm (733km) @ 66 TAS: 424nm (786km) Ceiling: 10,000 ft (3050m)
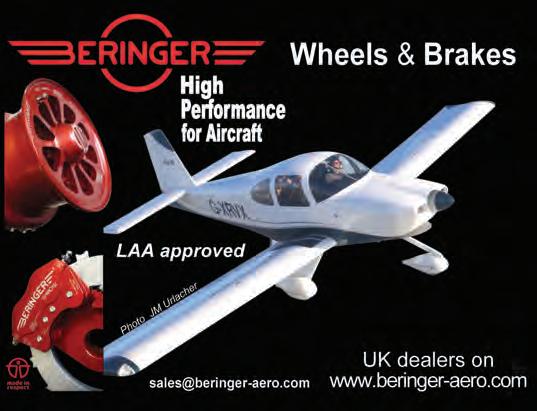


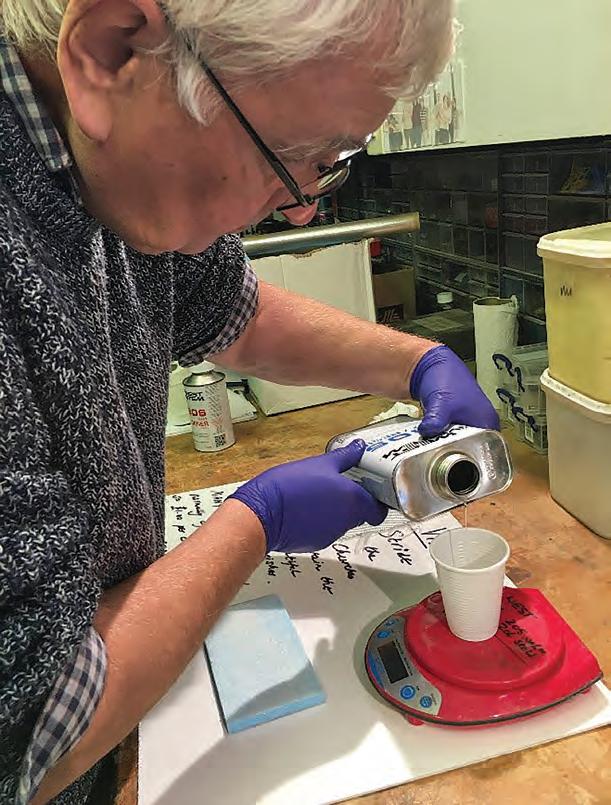
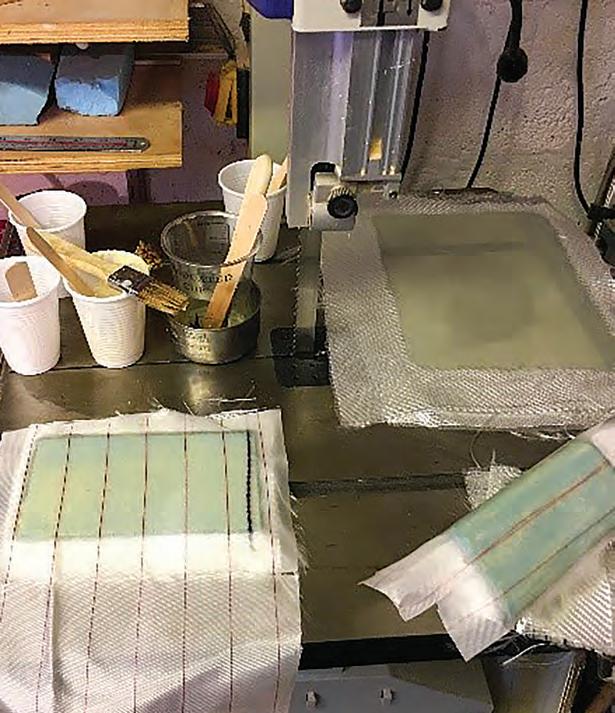

A bonding experience
A trio of friends, who met at their local Strut many years ago, get together for a spot of fibreglass revision – and more besides – as Phil Hall reports
Back in September last year, I was fortunate enough to be invited by my fellow Gloster Strut member and friend, Tim Houlihan, to join him on what turned out to be a wonderful tour of France, Spain and Portugal, with the Europa Club, in his tri-gear Europa G-RIXS.
With many landings on hard as well as grass surfaces, the spats inevitably get a fair amount of rough treatment and, as with so many fibreglass spats, they develop cracks that need repairing. This is not just a weakness on the Europas of course, I have had my RV-7 spats repaired twice – and now have a spare set in reserve as back up.
Fortunately, Tim and I have a very good friend, John
Bean, also a Gloster Strut member, who had been telling me I should revise my fibreglassing skills. I am the
Inspector for his Europa and I hadn’t done any ’glass work for over 10 years. In fact not since he had finished his mono-wheel G-VPSJ.
As John’s wife was away on a cycling holiday, John invited Tim and I round for a weekend ‘glassing’ course which, as it would include an overnight, would also include a few different ‘glasses’ in the evening. As usual,
John had prepared everything to perfection…
1 Preparation of the workshop
Ensure the workshop is insulated, and warm (at least 20°C) and ventilated.
2 Understanding fibreglass cloth
Discussion took place around car repair fibreglass mat, then BID (woven bidirectional cloth) ideal to drape round complex compound curves; UNI (unidirectional cloth) which has strength in one direction only (the line if the fibres); bi-axial cloth which is woven with its fibres layered at 45° – effectively two UNI’s, and final a brief discussion about carbon fibre cloth, which we were not going to use on this course.
We then discussed the importance of sharp scissors and knife blades for cutting the cloth to size for any job. I soon relearned that wearing gloves and rolling up your sleeves is a good idea. Fibreglass cloth is not very pleasant material, which can get into your pours very easily and can cause an allergic reaction. Top far left Cutting cloth, without gloves, not a clever idea. Like resin it the glass fibres can cause an allergic reaction!
Top left Careful resin weighing, lesson learned, and gloves worn.
Below far left Three practice examples using the different cloths – and many used mixing pots
Below left Laying up the first sheet of glass to practice the methodology.
3 Resin, mixing and thermal runaway
The merits of polyester and epoxy resins were next on the agenda. Most importantly, they must never be mixed, to do so will result in weak bonding.
Great emphasis was placed on correct mixing of the resin and hardener and getting them to the right ratios using sensitive scales. Also, mixing pots should preferably be those with a wide base to help with the avoidance of thermal runaway once the two liquids are mixed – the resin and pots can get surprisingly hot! Gloves are also essential here as an allergic reaction to the epoxy is even more serious.
4 Fillers and strengthening
Microballoons (Micro) and flox are as the principal fillers to mix with the resin. Microballoons have no structural strength, whereas flox, made from ground cotton fibre, gives great strength when mixed into the resin.
5 Unwaxed dacron (peel-ply)
When laying up fibreglass it leaves a very shiny surface, which has poor mechanical bonding qualities and is poor for painting or other further processes. To avoid this, unwaxed Dacron is used, known as peel-ply. This is wetted (applied) to the surfaces and once dry, is ripped