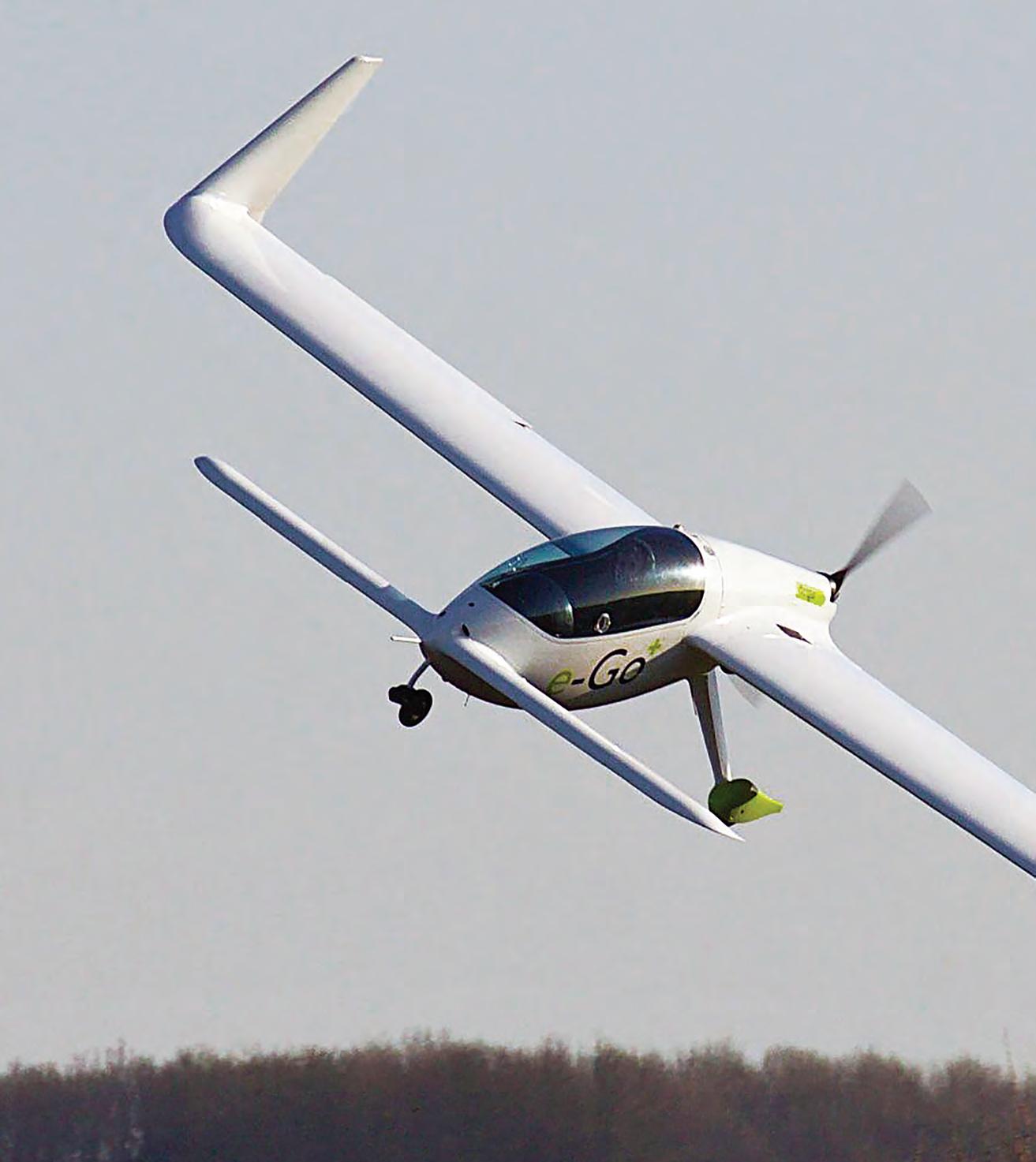
16 minute read
FLIGHT TEST
Here Goes!
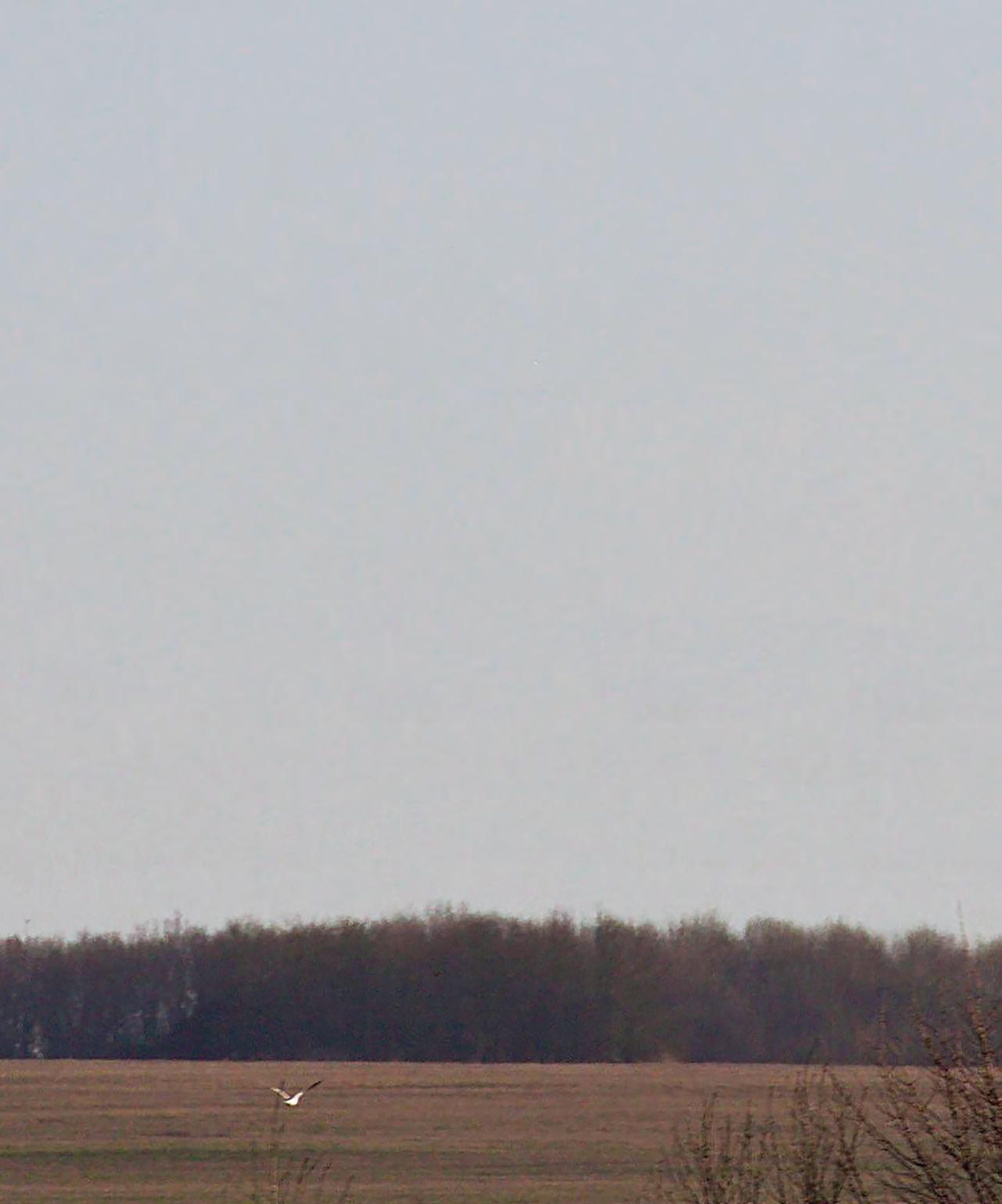
Francis Donaldson flies the e-Go, a bold attempt at a high-performance composite SSDR
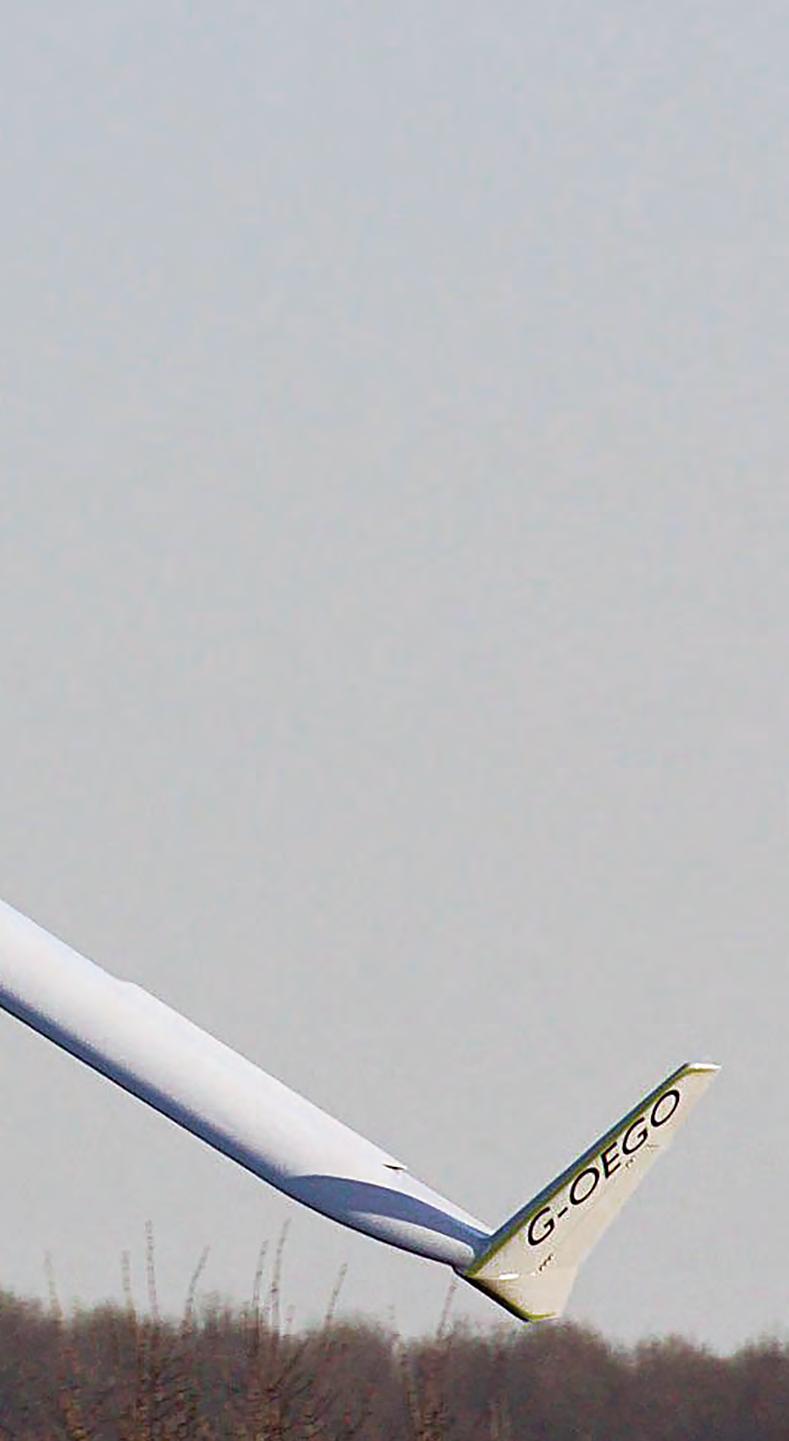
e-Go Green Credentials: 6.8 litres per hour at 80kt

Flight Test
Back in 2007, when the CAA chose to deregulate the airworthiness procedures for lightweight single seat microlights, the LAA (or PFA, as we were then) ran a design competition to try to stimulate activity in this new ‘SSDR’ (single seat, deregulated) category. Entries were many and varied and ranged from ‘ultra-simple retro’ to ‘modern-sophisticated’.
Competition winner
The competition winner in the state-of-the-art category is the subject of this month’s review, an all-composite canard initially called the e-plane. At that time only a ‘paper exercise’ that had demonstrated its prowess in the digitally generated output of Italian designer Giotto Castelli’s PC. Giotto comes from a background of professional aircraft design and certification in large aircraft, where he had done a stint working at Marshalls, and previously at Pilatus, Airbus, Raytheon and others. The aircraft, renamed e-Go, was a joint project between Giotto and entrepreneurial LAA’er Tony Bishop. Tony shared the project management as an active business consultant in consumer products and having past experience in the aeronautical engineering field. Also as co-owner of an MCR-01 which he built with Giotto, he brought a wealth of experience to the party. The aim was to create a uniquely efficient SSDR, using composite materials to achieve outstanding performance, sleek looks and a comfortable, modern interior, in a package that would allow quick dismantling into small components that could be stowed in an enclosed trailer.
In the vacuum left by the demise of the UK’s onceproud light aircraft manufacturing industry, the two Cambridge-based enthusiasts found that their design had created a fair amount of interest and they set out to build a prototype. Work started initially in their homes where, on a passing visit, I saw a fuselage mock-up in the sitting room and early attempts to mould the wing skins in the garage.
As the project gained momentum, and the prototype took shape, a small industrial unit was set up in farm buildings at nearby Main Hall Farm Airstrip to progress the work. In keeping with the modern concept, finance, apparently to the tune of almost a million pounds, came from web-based crowd funding SyndicateRoom, and was topped up by local entrepreneurs determined to see the project fly. The number of people involved escalated rapidly to create a 10-strong team under the guidance of Malcolm Bird, experienced Cambridgeshire tech entrepreneur. They were backed by many volunteers, keen to lend their high-level skills and be involved with bringing the embryonic single seater from concept to flight.
Professional design
The fact that the aeroplane was to be deregulated meant that the designers had scope to innovate to their heart’s content, knowing that they’d only have to justify their decisions to themselves – and if all went well, to
prospective customers. While Section S, the UK design code for microlights, was there for guidance, as an SSDR there would be no requirement to comply with it, and no regulators looking over the designer’s shoulders.
Nevertheless, Giotto’s team built sample structures and load tested them, and worked as far as possible within Section S, just as they would for an approved microlight. With the aerodynamics of a canard aircraft being less easily predicted than a conventional layout, the e-Go’s external form was tested and to a degree, optimised in Cambridge University’s large wind tunnel. A 1/3 scale radio-controlled model was also built and flown to check the likely flying characteristics.
The natural comparisons for the e-Go’s canard pusher form are inevitably Burt Rutan’s Varieze and Long-Ez of the 1970s and 1980s. Like Rutan’s designs, the e-Go enjoys a very short fuselage, just long enough to package the crew and engine, while main wing sweepback extends the aeroplane’s effective length.
The canard, which unlike the Rutan designs is low set, is unswept and of high aspect ratio, which is important in ensuring that at high angle of attack the canard will stall before the main wing, so tending to restore level flight.
The low-set position of the e-Go’s canard is interesting because this influences the way that the downwash from the canard affects the airflow over the main wing, which in turn affects the spanwise lift distribution on the wing, and hence its induced drag. When the inboard part of the main wing encounters downwash from the canard, the main wing’s incidence in this area is effectively reduced and it loses lift. Rutan’s designs include large triangular wing strakes alongside the fuselage, which in effect increase the wing chord and area inboard, helping to preserve the ideal elliptic spanwise lift distribution despite the downwash field inboard.
The canard’s placement also facilitates the e-Go’s more curvaceous fuselage more so than the Rutan designs, creating a more sloping canopy line, which gives it a better view from the cockpit. Despite the pilot’s seat base effectively resting on the fuselage floor, the small size of the cockpit and the modestly reclined seating position means that the fuselage has more of a belly than the Rutan types, giving the e-Go a rather Below The e-Go is designed to dismantle into relatively small parts for road transport. uniquely ‘fish-like’ side profile. The lowered nose also allows the noseleg of the e-Go to be much shorter than on the Rutan types, and with the nosewheel enclosed in a small spat, avoids the need for it to be retractable. Beauty is in the eye of the beholder, but the e-Go’s form seems to bring to mind the styling of exotic and very expensive sports cars from Giotto’s native Italy.
Change of wing construction
The original plan was to lay up the e-Go’s wing skins flat on a glass surface, using a Melinex release layer, which would create a smooth paint-ready surface on one side. The cured skin would then be wrapped around the spars and ribs to create a high-quality close tolerance wing. This, it was hoped, would save weight compared to a Rutan-style wet lay-up mouldless composite wing, and avoid all that soul-destroying work needed to fill and sand the surface finish, while also avoiding the cost of a conventionally female-moulded wing construction.
Conservatively, the wings, which were designed to quickly unbolt from the fuselage, incorporated a two-spar design which reduced the reliance on the wing skins to provide torsional strength, meaning that the skins didn’t need to be of sandwich cored type. As it turned out, the wrapping of a flat skin didn’t work out. Counter-intuitively (for me, anyway) it was found that being able to wrap a flat skin round it would impose constraints on the choice of aerofoil profile and washout – unless the right aerofoils are chosen it would be like trying to wrap silver foil round an Easter egg without it creasing. Tony developed a computer program to solve that puzzle, but then it turned out that even with the right choice of profiles, the wrapped skin wouldn’t produce the quality of finish that the team were looking for – a finish that would do justice to the e-Go’s ‘super car’ style. The wing skin was therefore switched to being wet laminated on the prototype. The pre-production aircraft then utilised moulds for all composite parts but retained the internal structure of the prototype wing.
Rotary engine
The engine selected for the e-Go was the Wankel rotary type Rotron 300 LCR water cooled, single-rotor unit, fitted with a belt reduction drive to the propeller.
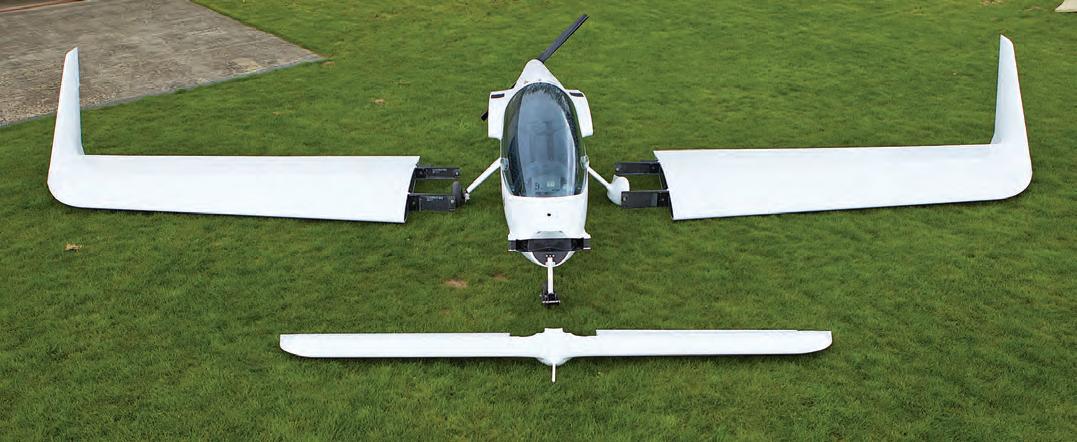
Fuel injected, and with dual-plug ignition, this tiny unit produces 27hp at 7,300rpm for a weight of only 12kg (30kg dry installed), from a displacement of just 300cc.
This choice was no doubt driven by the punitive empty weight limit of 115kg imposed on SSDRs at the time the aircraft was designed, meaning that to allow the e-Go’s relatively sophisticated format, every kilogram had to be saved to keep within the limit of the regulation. Unfortunately, ‘you don’t get owt for nowt’, and this little gem of a powerplant, sold normally for military drone applications, comes with a high price tag.
As it turned out, by the time the prototype e-Go was nearing completion, the CAA were already considering eliminating this empty weight limit for SSDRs and expanding the class to include all single seat microlights, meaning a max loaded weight of up to 300kg was available. Fortunately, the e-Go had been designed with some extra strength and wing area in hand which meant that it was possible to clear it with an empty weight that slightly overshot the original 115kg target.
Test flying
The e-Go team were very fortunate in recruiting professional test pilot Keith Dennison as the project pilot, bringing the professionalism so important in this dangerous element of the project, but also the enthusiasm to resolve the inevitable challenges that would be faced in developing the canard’s handling. Keith had experience of a huge range of aircraft types (including Shuttleworth’s priceless fleet), and critically as it turned out, a good ‘pair of hands’. When the prototype first took flight, in October of 2013, it was found to be incredibly sensitive in pitch, while also challenging laterally at its minimum speed due to a combination of low yaw stability and aileron drag – not a good combination! Keith was able to resolve a mild PIO in pitch after the first take-off, and despite these challenges, carried out a textbook first flight and landing – and a few days later, demonstrated the aircraft to the press!
The e-Go team set to and one by one addressed each of the handling aspects in turn – an elevator with a different hinge and leading edge slot geometry which gave much better ‘feel’ and normal pitch sensitivity, and Previous page G-OEGO, the pre-production aircraft in flight. It is undeniably attractive and a high-quality product.
Below left The pre-production model’s nicely trimmed cockpit is reminiscent of a contemporary sports car.
Below right The aircraft is ready to be put into production if a cost cutting exercise can be achieved. seemed to make the aircraft ride out gusts better. Larger fins of a different shape to increase the directional stability. And ailerons with a different nose profile to reduce the yawing moments due to aileron drag. On the second example of the e-Go, which was their pre-production aircraft, the main undercarriage was moved forwards so as to reduce the static weight on the nosewheel, which allowed the canard to lift it off the ground at lower airspeed, giving a shortened take off run. Engine cooling was also improved, using an electric fan to blow air through the engine’s cooling radiator when the aircraft was on the ground.
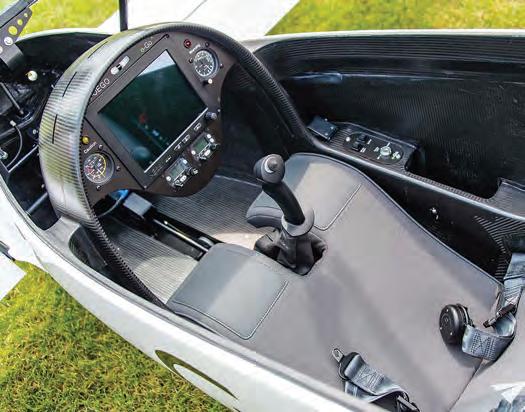
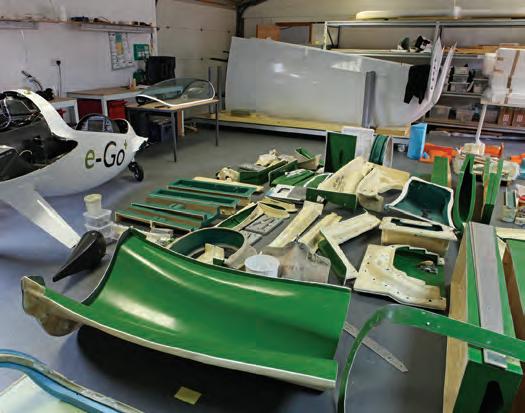
Liquidation
Fully sorted, the e-Go was displayed very energetically by Keith at several airshows in 2015-16, showing itself (after confirming that CAA had no objections) fully capable of effortless looping and rolling. It was, it seemed, ready to go into full production after the pre-production e-Go was handed over to lead customer William Burnett, in June of 2016.
Sadly however, despite all the effort, and with plans for multi-seat derivatives, electric-powered versions, pilotless and even military applications, the e-Go company ran out of funds in late 2016 after expending a reputed £1.7m, being unable to raise the additional finance to enter production.
After the staff were laid off, designer Giotto Castelli bought back the rights to the design, along with the prototype aircraft and the tooling and CNC programmes.
Since then, Giotto has sought alternative ways of putting the e-Go into production, using parts manufactured outside of the UK to reduce costs and allow a lowering of the aircraft’s price to a more attractive level. He is also designing an electric power option and thinking about other derivatives, including the lucrative market for aircraft in the pilotless surveillance role which would better fit with the relatively high cost Rotron engine.
Invitation to fly
Having watched the e-Go’s story develop over the years, visited the Main Hall Farm base, seen the prototype demonstrated and lamented the company’s financial demise, I was delighted to get a call from Giotto in late
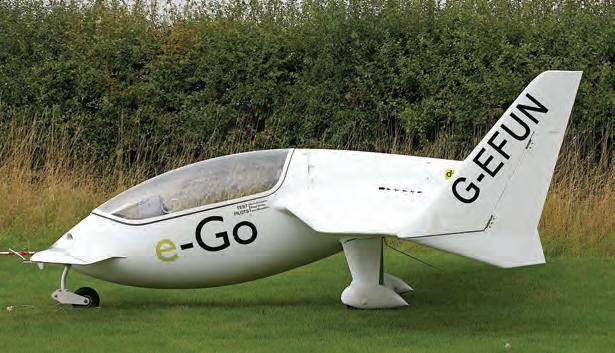
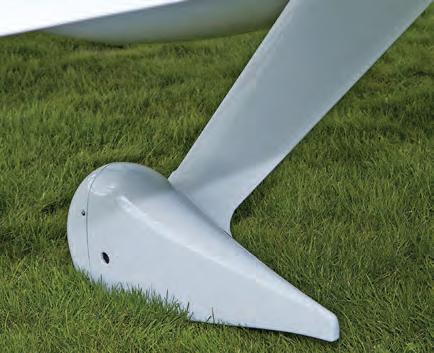
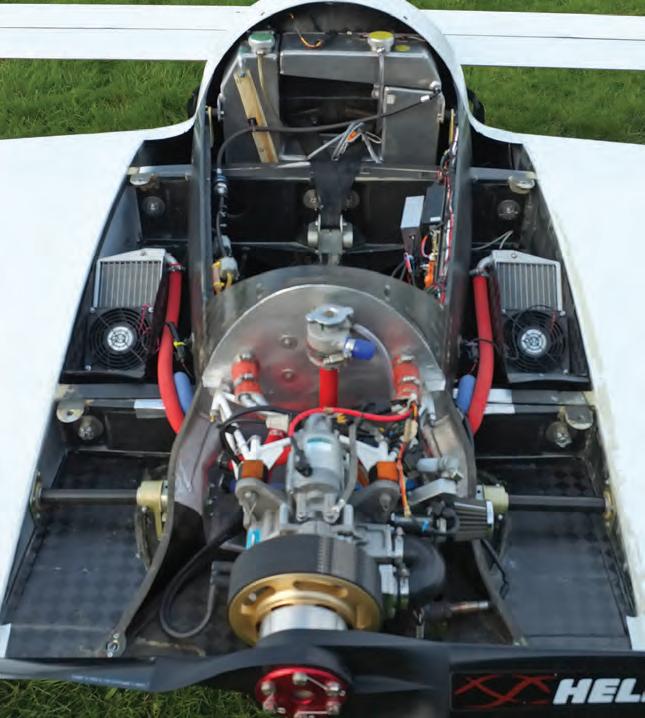
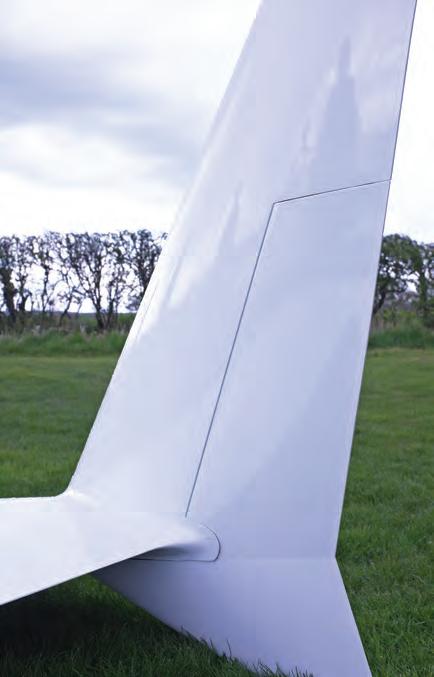
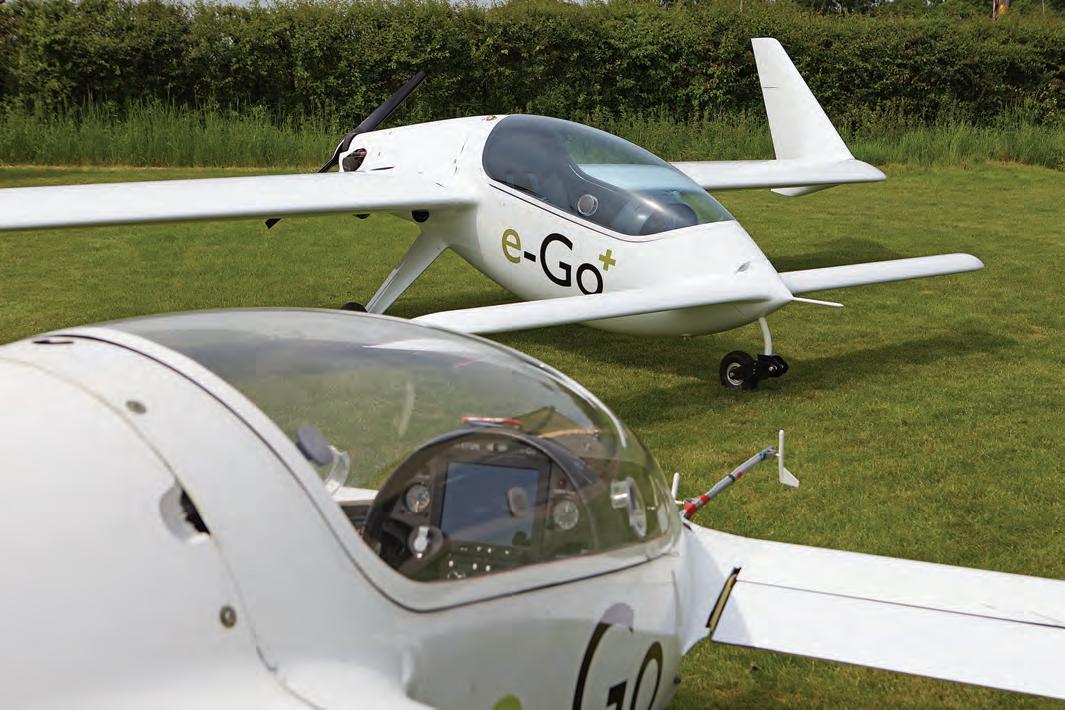
2019, telling me that he had got the prototype flying and inviting me to fly it. As one of those who had ploughed through all the paperwork as one of the judging team for the PFA’s SSDR design competition back in 2007, I was particularly interested to see how the aircraft performs in real life, a dozen years later. While the company had been enthusiastic in copying me their newsletters over the years as the project came together, they had been consistent in keeping anyone other than their company pilots from flying it, thus there had been no independent magazine reviews. Not surprising, perhaps to keep the precious prototype safe – but then again, might the aircraft’s handling be harbouring some terrible defect? I’ve been lucky enough to fly a number of SSDR machines over the years, including the Eindekker, miniature Cub-like Escapade Kid (now the TLAC Sherwood Kub) and the swan-necked, ride-on Vierra. None of these machines have any pretentions of high efficiency, so a better comparison with the e-Go would be the Colomban Luciole, which achieves similar cruise speeds to the e-Go on the 25hp of a converted four-stroke industrial vee-twin. The Luciole has only 4.6 sq metres of wing to the e-Go’s 11.5 sq metres, making the Luciole an SEP rather than a microlight despite having an empty weight of less than 100kg. The Luciole thus has a wing loading twice that of the e-Go, meaning a higher stall speed but, on the plus side, a smoother ride in turbulence. Would the e-Go seem very rough in comparison?
Giotto and I met up at his home base of Gransden on a rather overcast day, with a chill wind blowing from the east, favouring the main runway in an uphill direction. During a comprehensive brief, Giotto was kind enough to de-panel the machine to show me the works – after half a lifetime checking designs of sport aircraft, I wasn’t going to fly it without having a good look over it first.
Quality construction
The structural heart of the aircraft is the main moulded carbon bulkhead behind the cockpit, which integrates the wing attachments, main undercarriage and seat belt attachments. Glued to the fuselage, forward of this bulkhead is the moulded seat pan. This itself is a work of art, which also integrates with the fuselage shell to create not only a very strong crash cell but also a sculptured cockpit interior with built-in apertures for the pilot’s bits of kit – car interior-style. While in the prototype example the cockpit is untrimmed and bears many signs of its required function, and the scars of development changes, if smartly trimmed, together with the moulded instrument panel unit this could clearly be a cockpit of a style and quality to match its sports car image.
Giotto quizzed me about my weight while I did the walk round, and in response decided to remove some of the lead ballast that normally lives in the nose. With Opposite top far left The prototype, G-EFUN, as flown by Francis for this air test..
Opposite top left The beautifully faired main undercarriage, hydraulic disc brakes and composite legs are used.
Opposite middle far left The rear fuselage of the pre-production aircraft. Note substantial main spar/undercarriage / seat belt anchorage, belt reduction Rotron engine, and fan assisted twin engine cooling radiators.
Opposite middle left The rudders act independently for yaw control and together to act as an airbrake to steepen the approach.
Opposite bottom Thus far the only two e-Gos in existence, the prototype G-EFUN in the foreground, and the pre-production aircraft, G-OEGO behind. such a lightweight aircraft as this, where the pilot weighs almost as much as the aeroplane, such things are crucial to proper cg position – the more so with a canard in which you’re sitting well ahead of the empty cg.
Generous cockpit
To climb aboard the prototype, the transparent cockpit cover detaches altogether, so once seated one really needs outside help to re-fasten it. Later examples would have hinged canopies. Once enclosed, it’s noticeable that for such a lightweight aeroplane, the cockpit is generous in size and there’s no feeling of claustrophobia under the bubble. There’s a central stick and a rather lightweight pair of rudder pedals combined with brake pedals. These are about the only thing I rather took exception to, being seemingly flimsy and spongy and not inspiring confidence. They have since been re-designed.
Looking around for the throttle, Giotto pointed to an electrical slider, like something off a music console, on the left side of the cockpit, which operates the throttle via a model aircraft servo mounted alongside the throttle body in the engine compartment – and it worked! This would be the nearest I have yet come to ‘fly-by-wire’ – such are the freedoms of the SSDR category. On the right-hand side of the cockpit was an array of miniature switches to do with managing the electrics, primarily the engine. On this prototype, it was somewhat sobering to see that these tiny and identical switches, which have labels that, looking rather obliquely, I was hard-pressed to read, control not only my master electrics but also the fuel pump (without which the engine will stop); the electronic ignition (without which the engine will stop); the water pump (ditto – but more expensively) the oil pump (you’ve guessed it), and the engine cooling fan (which I must activate if the engine gets hot, otherwise…)
There’s a simple mechanical pitch trimmer, but no flaps of course, for flaps on a canard’s wing would act like elevators and cause a big change in trim. Instead, if you press both rudder pedals simultaneously, both of the rudders move outboard, creating extra drag and steepening the glidepath – the e-Go can fly so slowly anyway, but despite its fixed gear is so clean that extra drag is the only thing you’d want of flaps anyway.
Getting underway
Being the first flight of the day, the rotary engine took a few presses of the electric starter to spring to life. The engine sounds a bit uncertain of itself below about 3,000rpm but smooths out beautifully when you open it up. Taxying out on Gransden’s wet and tussocky grass, I was pleasantly surprised how well the little wheels coped.
With no propeller slipstream acting on the twin wingtip rudders, steering on the ground relies completely on the differential brakes, which were rather