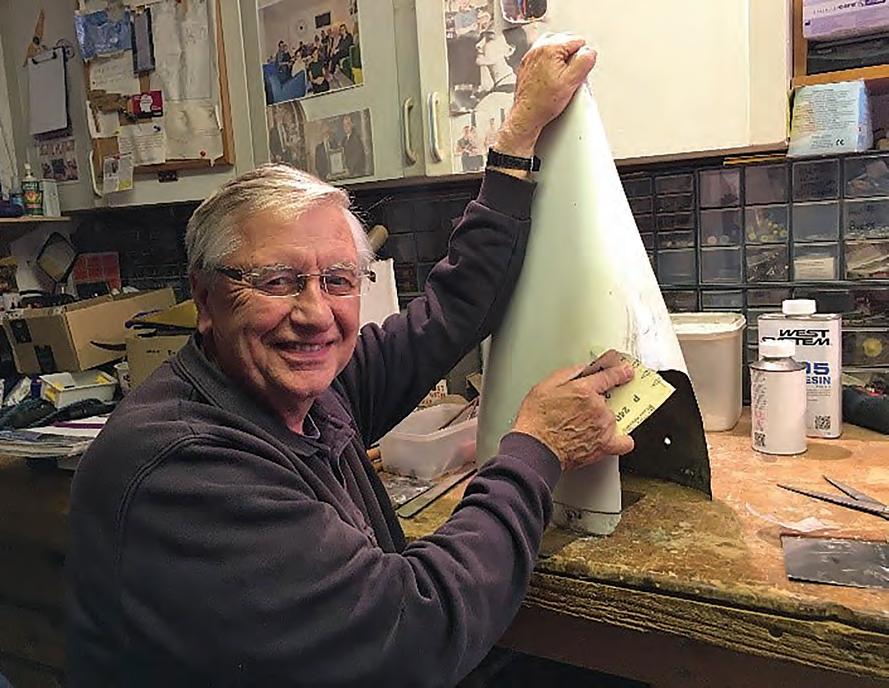
4 minute read
BLOOD, SWEAT AND TEARS
off – leaving a nice matt surface with very good surface texture, giving a good mechanical bond ideal for further layups or other ongoing processes.
6 Practical examples
To ensure a full understanding of the use of the various materials and for practical experience, John got me to produce a sheet of fibreglass, cutting out two UNI cloths, preparing the correct mixture and quantity of resin and laying them up. To help remove it from the working surface we laid it up on a cling film backing, and used peel-ply on the final surface. We then progressed onto building a flat structural plate and a curved shape using BID.
7 Repairing Tim’s spats
Once we had finished the revision of the basics of fibreglassing, we continued to repair Tim’s spats which, after the brush up and practice we’d had, proved to be pleasantly straightforward.
We cleaned up the damaged area with a Dremel and removed a previous repair that had been made with polyester resin and had clearly not adhered well to the epoxy resined spat. We then set about following the same procedures as described above for the repairs.
It worked a treat and was done surprisingly quickly. While waiting for the glass to harden we would inevitably have a coffee and cake break, where serious philosophising took place – such as the discussion on why, when your wife makes a wonderful looking cake do you get told off for eating it! Surely the point of a warm and inviting cake is to eat it…
The following morning was spent cleaning up the spats and rubbing down to make the job look good and inspect it for final quality and strength. Strangely, we were not working at the same speed as the previous day – it had nothing to do with a very convivial evening, you’ll understand… John explained how to identify a crack on a finished surface like a wing or tailplane and what type of repair would then be required. By marking it with a quickdrying, fade-resistant Sharpie felt tip pen, if on grounding down the gelcoat the ink has gone then the crack was only in the surface finishing gel coat, but if it bleeds into the fibreglass structure then a fibreglass repair is needed.
At the end of John’s mini-course I left with three different examples of fibreglass work that I had fabricated and Tim left with repaired spats, which will last him for another season or two, but most importantly a whole lot of renewed knowledge and some great memories.
All in all, it was valuable revision with a good practical purpose – and great fun, which had its origins in three good friends’ original meeting many years ago at our local Strut – thanks to the LAA. ■
Left A happy Tim finishing off a spat before repainting and refitting it to his Europa.
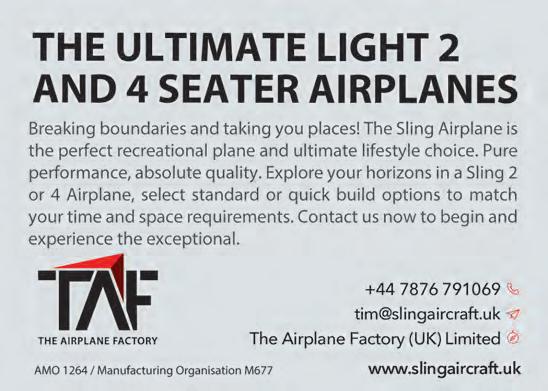
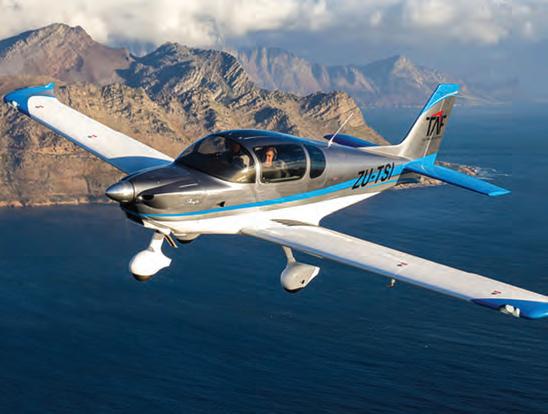


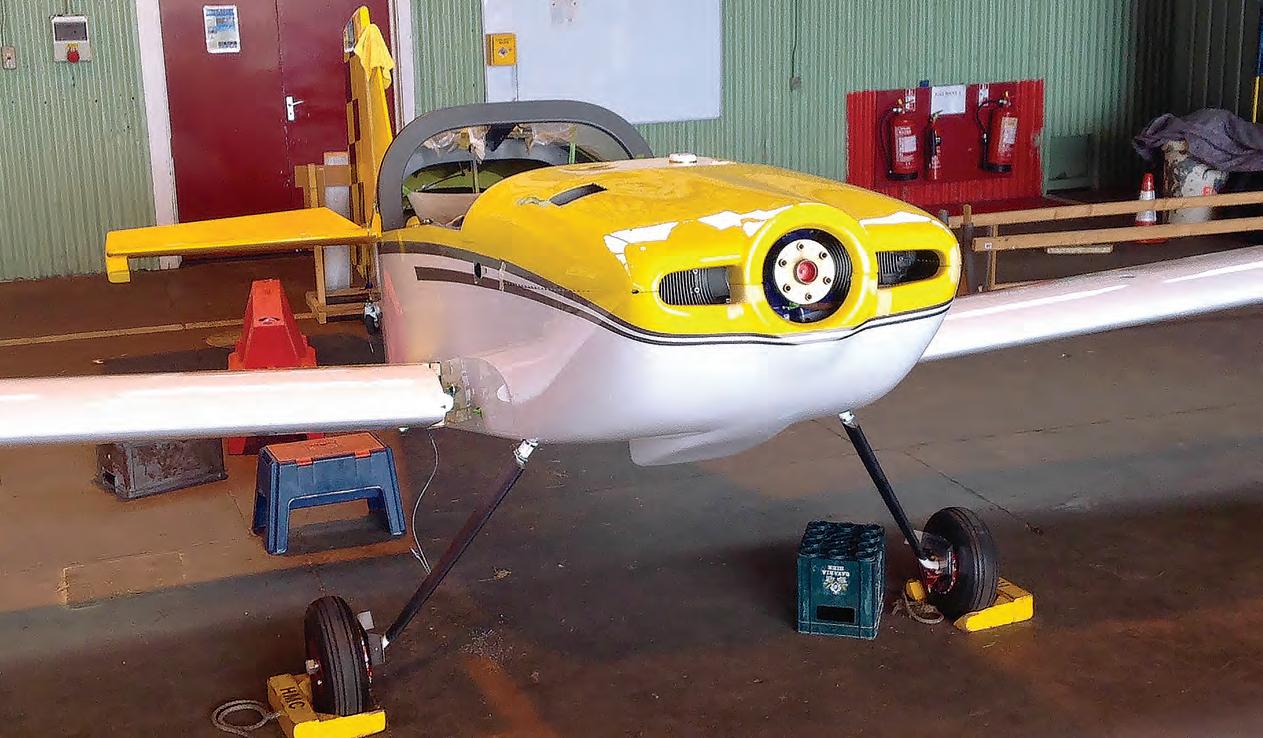
An update on the RAF Flight of the Navigator Project
In summer 2019, we looked at the British attempt to beat the World Speed Record for Circumnavigation of the Earth by serving Royal Air Force Officer (and LAA member of 25 years), Group Captain Mark Manwaring. The aim was to depart Biggin Hill on 20 August 2019 in a cutting-edge (and highly modified) Van’s RV-7, returning approximately 18 days later, thereby smashing the current 26-day by a comfortable margin. So, what has happened since then? Mark explains: “This was always going to be a stretch-date for this World Speed Record attempt. At the start of 2019 it was evident that absolutely everything had to be right first time and, unfortunately, a number of out-sourced elements of work, the sort of things that homebuilders are neither equipped or qualified to do, came in late and sequentially compounded each other.
By the end of June, just three months before departure, Main The sleek lines of the RV-7 promise significant performance (once the canopy and propeller are fitted!) we found ourselves three months behind the schedule! Despite continued blood, sweat and tears, we are sad to announce the 12-month slip of this World Speed Record attempt.” Flight Safety and flying supervision has been at the heart of Mark’s 35-year career as a fast-jet navigator in the RAF, and he is typically military in his approach to debriefing safety issues. “The only person putting pressure on myself was myself. As far back as April I had discussed the potential of a 12-month slip with the team, and all were totally signed-up to the prospect. I knew at the time that the requirement to complete the project in 2019 was artificial and self-generated. From a date perspective, it was an aspiration to mark the 100th anniversary of the first non-stop transatlantic crossing by Alcock and Brown, plus the centenary of the RAF Benevolent Fund. I must say that throughout this period my extensive team of