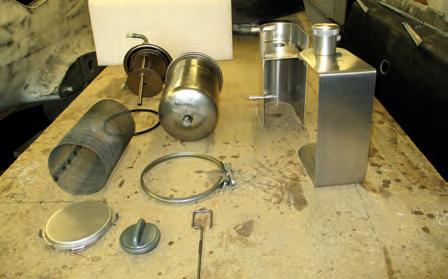
6 minute read
Project News
Having compiled this column for more than five years now, I have never known a month where there has been no new project registrations. New starts are typically thinner on the ground as the flying season gets going, and we more typically see a move to constructors finishing their projects and getting them into the air for the first time. Aircraft cleared for first flight can be found at the end of this column.
First of all, a plea from Dudley Pattison, who has been in touch, and is now looking for willing members with partially complete projects who’d like to display their creations in this year’s homebuilder tent at the LAA Grass Roots Fly-In at Popham on 2,3 4 September. Interested? Project News would be happy to put you in touch.
Blue Two is not only a scratch built aircraft but an own design, one off, nearing completion with LAA member, Andy Best.
Andy has provided updates from time to time – actually year to year – and I suspect this may be the last but one, as the craft is looking decidedly like an aeroplane. Recently, he found himself with an unforeseen problem when finalising the engine fit out. There wasn’t quite enough room under the bonnet for the Rotax remote sump or oil can! In such a situation we’d all probably throw around a selection of Old English, I’m sure Andy must have, and then he set about resolving the issue. After all, you don’t reach the closing stages of such a project without being pragmatic in the face of adversity, do you? Most would soon start considering some shapley bulges in the cowl, but Andy has analysed the problem at its root and reinvented the oil container. In the process the dipstick has been made redundant – excellent, I bet that would make some people very uncomfortable, but the thing only exists because of past design inefficiencies anyway. What a marvellous idea, ‘design out’ the need for it. Have a look at Andy’s lubricating adventure below and see what you think.
Have you had to come up with a novel approach to a problem in your build? Project News would love to hear about your success in beating the odds in sub-structures and systems, it doesn’t have to be a tale of a complete aircraft.
To get in touch with Project News, and tell your story, report a milestone or just to send a picture, email: projectnews@laa.uk.com Please share your story!
Blue Two (LAA 388-15251) A carbon-composite, two-seat original design
By Andy Best
Building your own aircraft can seem a rather daunting task but, like all big jobs, if it’s broken down into small ‘bite size’ chunks the whole thing becomes much more manageable. I also think it’s important for your own sanity to tackle only one job at a time. I know our esteemed ‘other halves’ will say ‘you men can’t multitask, like we have to’, and I agree, with good reason.
One of my ‘bite size’ aircraft building tasks was installing the oil system for the Rotax 912 engine. This meant mounting the oil cooler and working out the routing for the oil pipes. It can be quite a tricky job, to avoid the water pipes, the engine mounting frame and especially the hot exhaust pipes. Then came the mounting of the Rotax oil tank. And, as every builder knows, there are days when things just don’t go right. Well, I had one of those days. The oil tank would not fit in my engine bay without fouling the engine covers. Oh dear!
However, years ago, I had designed and made a dry sump oil tank for a Formula Ford 1600 racing car, which worked well. So I thought, why not make my own oil tank for the aeroplane?
‘Dry sump’ engines pump the hot engine oil out to a remotely mounted oil tank, from where it is drawn back into the engine through an oil cooler and then into the main oil pump. This has two advantages. One is that, in the absence of a normal deep sump, the overall engine height is reduced allowing it, in racing cars anyway, to be mounted lower. The second benefit is because of the height of the oil tank, oil flow into the oil pick up pipe is always maintained, even under high sideways ‘g’ loading. Now, of course non-aerobatic aircraft are incapable of producing high sideways loading. Relative to the aircraft, the loads produced are virtually always in a vertical aeroplane. In light of the above, one wonders why Rotax thought it was a good idea to introduce the complications of a dry sump system in the first place…
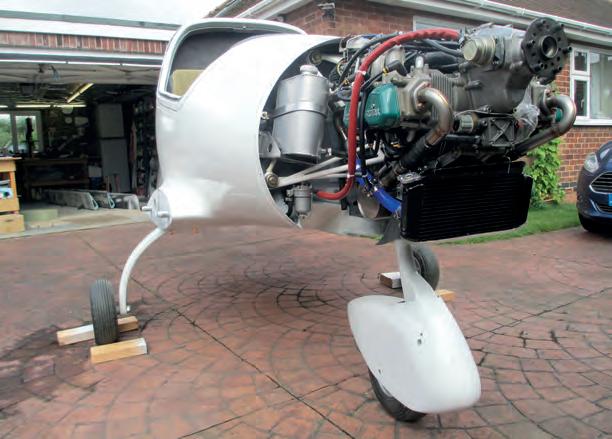

My overall design thinking is to keep things simple and reduce the parts count to a minimum. This saves manufacturing time, cost and weight, which is all good news for us aircraft builders.
The 912 engine requires four litres of oil, three litres in the oil tank and the rest in the engine, the oil filter, the pipes and the oil cooler. My tank has an internal volume of four litres which allows room for de-aeration and expansion. The main body of my tank is made from two bent pieces of 2mm thick aluminium sheet. The third sheet aluminium part is the baffle plate, which is set at a height in the tank, such that when the oil just covers the plate, I know I have three litres of oil in the tank. This gets rid of the need to have a dipstick. The feed pipe from the engine is placed above the baffle plate and directs the oil flow onto the side wall where it spreads out allowing any entrained air to separate out.
If the oil was allowed to splash down into the main reservoir there would be a danger of foaming. And drawing a mixture of oil and air through the oil pump and engine bearings is definitely not good news.
The pick up pipe delivering oil back through the cooler to the engine is about 20mm up from the bottom of the tank, so that any sludge or dirt that falls to the bottom of the tank is less likely to be picked up.
The third pipe is the breather pipe, situated in the filler neck. Thus, the tank is not pressurised, its contents remaining at the ambient prevailing air pressure. The Rotax engine is, I believe, quite unique, in that rather than having a scavenge pump to return oil to the tank, it relies instead on crankcase pressure, created from piston blow by. If this pressure becomes excessive, due to high piston bore wear, then the breather air flow will become large and as it carries oil mist with it, some depletion of the oil level in the tank will result. This will show up when the underside of the fuselage becomes streaked with oil.
Unlike the Rotax tank, I feel no need for a drain plug in the tank. On changing the oil at 50 hours, I would always remove the tank anyway and wash it carefully, with petrol, to clean out any sludge or debris. The gauze screen, for me, serves no real purpose either, as there is no reason for anything that could be removed by it to enter the oil system. The magnetic drain plug, at the front of the engine block and the oil filter itself, should be much more effective in capturing any metallic debris.
I assembled the tank parts with small strips of masking tape and took it to my local Rally car prep shop. They spend all day TIG welding aluminium fuel tanks and the like, and for about £50, did a superb job welding my tank. They also did an excellent job TIG welding my stainless steel exhaust system, but that’s another story…
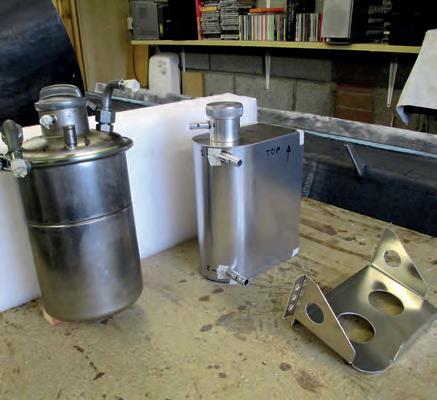
Cost wise, the filler neck and screw on cap were about £20 from Merlin Motorsport, the aluminium sheet about £40 and the stub pipes about £15, giving me a grand total (with welding) of £125. The cheapest (and some sources were a lot dearer) new Rotax oil tank that I could find was €765.9.
And weight wise, at 712g, my tank was 852g lighter than the Rotax tank which weighed in at 1.5kg.
The picture of the assembled tanks also shows my mounting bracket which has been bonded to the firewall of the aeroplane. The tank, which gets hot from the oil, at around 100°C, is insulated from the carbon fibre firewall and the mounting bracket by a 10mm thick layer of dense foam. I certainly didn’t want the epoxy resin in the firewall to get that hot, as it starts to soften at around 70°C.
I have run the engine a couple of times now and all seems to be well but it pays to be vigilant, and as with any prototype – always expect the unexpected.