
15 minute read
VERFAHRENTSTECHNIK
from ChemieXtra 1-2/2020
by SIGWERB GmbH
Die Schattenseite des IIoT ernst nehmen
Hacker machen Jagd auf Datensammler
Advertisement
Durch eine umfassende Vernetzung von Anlagen und Prozessen können Chemieunternehmen die Effizienz steigern und neue Geschäftsmodelle entwickeln. Das stellt hohe Anforderungen an die Cyber-Sicherheit. Sowohl die in sich geschlossenen operativen Technologien (OT), die zur Überwachung der Anlagen dienen, als auch IT-Ökosysteme mit Partnern entlang der Lieferkette müssen besser geschützt werden. Vor allem aber muss Cyber-Sicherheit als Chefsache ernst genommen und strategisch neu aufgesetzt werden.
Götz Erhardt¹, Herbert Kunzmann¹
Es kann jeden treffen – jederzeit. Rund um die Uhr attackieren Cyber-Kriminelle mit Viren, Trojanern oder anderer Malware IT/OT-Systeme. Bekannt sind derzeit etwa 800 Millionen Schadprogramme, gut 390000 Varianten kommen täglich hinzu. Nur in der öffentlichen Wahrnehmung griffen Hacker lange bevorzugt dort an, wo Kundendaten als Beute locken – etwa, um Online-Konten bei Banken oder Internetshops zu kapern und so schnelles Geld zu machen. Tatsächlich sind aber auch Unternehmen der Chemie-, Pharmaindustrie sowie Energieversorger bei Cyber-Krimi nellen beliebt. Accenture-Studien zum Thema Cyber-Sicherheit zeigen, dass sich die Bedrohungslage durch Cyber-Angriffe weltweit verschärft und Unternehmen mehr Geld denn je ausgeben, um sich mit den Kosten und Folgen immer komplexerer Angriffe auseinanderzusetzen. Weltweit könnten die mit Angriffen verbundenen Kosten und Umsatzeinbussen in den nächsten fünf Jahren über alle Branchen hinweg auf bis zu 5,2 Billionen Dollar steigen. Denn sowohl die Zahl der erfolgreichen Angriffe als auch der im Schnitt verursachte Schaden stieg in den vergangenen fünf Jahren um rund 70Prozent.
Erpressung, Spionage oder Sabotage Tatsächlich scheinen die Grundstoff- und Chemiebranche besonders verlockend für Hacker zu sein: Die Trans-Alaska-Pipeline
Cyber-Kriminalität stellt im Zuge von IIot eine ernsthafte Bedrohung für Chemie- und Pharmaunternehmen weltweit dar.
etwa muss täglich im Schnitt rund 22 Millionen Cyber-Attacken abwehren und bezeichnet das als eines der drei grössten Risiken für das Unternehmen. Wer tief genug ins Computersystem eindringt, kann erpressen: Angreifer verschlüsselten z.B. per «LockerGoga» Daten und forderten Lösegeld für den Freigabecode. Er kann Geschäftsgeheimnisse stehlen: Mithilfe von «Winnti» haben Hacker versucht, wertvolle Daten von deutschen Konzernen zu erbeuten. Ausserdem kann er schlicht sabotieren, mit möglicherweise verheerenden Folgen: Hacker sollen versucht haben, die Sicherheitsmechanismen eines Gaswerks in Saudiarabien so zu manipulieren, dass diese bei Fehlfunktionen eine Explosion nicht verhindern. So eine Form der digitalen Sabotage könnte viele Menschenleben kosten. Gerade dieses Beispiel zeigt, warum die Chemieindustrie ihre Bemühungen um IT/ OT-Sicherheit weiter intensivieren muss. Viele Konzerne setzen auf die Vorteile von Digitalisierung sowie Industriellem Internet der Dinge (IIoT) und vernetzen dafür auch früher weitgehend mit IT-Insellösungen betriebene Anlagen – etwa, um mit den Betriebsdaten mit einem digitalen Zwilling eine effizientere Steuerung zu simulieren oder die Lieferkette zu verbessern. Dann muss die OT solcher Anlagen genauso gut geschützt sein wie die via Internet und Cloud laufende Konzern-IT – bis zur letz
ten Ventilsteuerung in der hintersten Ecke des Geländes, falls diese digital angebun den und nicht für reinen Handbetrieb ausgelegt ist. Jede Schnittstelle bietet einen Angriffspunkt: Unlängst hätte ein Verschlüsselungstrojaner fast die Anlagensteuerung eines Chemieunternehmens lahmgelegt, weil ein Ingenieur versehentlich eine smarte Kaffeemaschine per WiFi mit dem Internet wie auch mit dem OT-System verbunden hatte. Auf dem Umweg über die Kaffeemaschine war die Schadsoftware in die Anlagensteuerung eingedrungen. Oft passiert so etwas auch über Geschäftspartner. Jede zweite Cyber-Attacke erfolgt in Form des sogenannten Inselhüpfens, gerade in der Industrie. Digitale Schädlinge springen dabei entlang der Lieferkette von einem Unternehmen zum nächsten. Alle Partner müssen bei Gegenmassnahmen also an einem Strang ziehen. In den Führungsetagen der Chemiekonzerne wird dieses Thema durchaus ernstgenommen. 80Prozent der von Accenture befragten Top-Manager sind überzeugt, dass die Cyber-Sicherheit durch gemeinsame Anstrengungen ver bessert werden sollte. Wachsende Komplexität in der Zusammenarbeit mache es unmöglich, sich innerhalb eines Partnernetzwerks punktuell von Betrieben abzuschotten, bei denen Zweifel an der ITSicherheit bestehen. Es fehlen aber noch passende Lösungen – und kritische Selbsteinschätzung: 77 Prozent der Be fragten meinen mit Blick auf ihre ITSicherheit, dass professionelle Partner unentbehrlich seien. Gleichzeitig ist kaum jeder Dritte überzeugt, dass seine Partner sich so gut um IT-Sicherheit kümmern würden wie die eigene Organisation. Es gibt also noch eine ganze Menge für mehr Vertrauen und Vertrauenswürdigkeit zu tun. Dabei hätten gerade Chemieunternehmen beste Voraussetzungen für IT/OTSicherheit auf Topniveau: Die Branche ist geprägt von einer Philosophie der Sicher heit. Über Jahrzehnte hinweg wurden Produkte und Prozesse immer sicherer, weil kleinste Fehler beim Betrieb einer Chemieanlage grosse Folgen haben können. Nun gilt es, diese Erfahrung und Tradition in die digitale Welt zu bringen – mit einer
markant steileren Lernkurve. Was sich bei Anlagen über Jahre hinweg optimieren liess, gilt es, beim IT-Einsatz angesichts der enormen Zahl von Cyber-Angriffen eher in Wochen als Monaten zu verbessern.
Cyber-Sicherheit zählt zu den Aufgaben des CEO Vor umfassenden Investitionen in technische und organisatorische Lösungen sowie der Mitarbeiterschulung braucht es grundlegende Antworten auf die Frage, wie das Unternehmen für sich sowie als Teil eines Ökosystems mit Partnern arbeiten soll. Der Übergang zum digital ausgerichteten Geschäftsmodell muss begleitet werden von wirkungsvollen Massnahmen für Cyber-Sicherheit, die dieses neue Geschäftsmodell ermöglichen. Das sind Chefentscheidungen – und deshalb sollten Massnahmen zur IT-Sicherheit konzernweit einheitlich überwacht sowie optimiert werden. Ist die Richtung klar, können IT-Experten und Fachabteilungen die einzelnen Themen wie das Erkennen von Angriffen sowie das Response Management betrachten – und beispielsweise ein Sicherheitsprotokoll von ganz oben absegnen lassen, das die Abschaltung aller PCs binnen einer Stunde vorschreibt, um eine Virusinfektion einzudämmen. Im Schnitt dauert es heute noch immer 206 Tage, bis verdächtige Aktivitäten überhaupt entdeckt werden. Für mehr Cyber-Sicherheit müssen Unternehmen sich mit Partnern entlang der Lieferkette koordinieren: Mithilfe der BlockchainTechnologie könnte man Bestellungen z.B. transparenter und weniger angreifbar abwickeln. Externe Spezialisten für Schutzmassnahmen können regelmässig Angriffe auf Konzern-IT sowie OT-Systeme simulieren und so testen, ob bzw. wie gut Cyber-Attacken bemerkt und abgewehrt werden. Diese Erkenntnisse sollten in die kontinuierliche Verbesserung der CyberSicherheit einfliessen. Das wäre auch der erste Schritt von einer rein defensiven IT-Sicherheit hin zu einem offensiven System, in dem die erstklassige Sicherheitsarchitektur als Verkaufsargument beim Aufbau neuer Geschäftsbeziehungen dient.
So schützen sich Chemieunternehmen vor Attacken
Chemiekonzerne sollten auf globaler Ebene mit anderen Unternehmen sowie Regierungen und Aufsichtsbehörden kooperieren. Die Zusammenarbeit ihrer Führungskräfte und Experten mit externen Spezialisten erleichtert es, potenzielle Angriffe zu erkennen und wirkungsvolle Gegenmassnahmen zu entwickeln. Jedes Unternehmen muss sich intensiv mit den Grundprinzipien der Cyber-Sicherheit beschäftigen und sein Geschäftsmodell konsequent schützen – in der eigenen Organisation ebenso wie bei seinen Partnern entlang komplexer Lieferketten. So entsteht digitales Vertrauen innerhalb des gesamten Ökosystems. Investitionen in IT/OT-Sicherheit müssen Priorität bekommen – auch ohne sofort messbare Rendite. Es gilt, neue Technologien anzuwenden, moderne Software zu installieren, IIoT-Security zu beherrschen, Update-Funktionen auf mobilen und IIoT-Geräten zu aktivieren sowie sich auf die Quantum-Herausforderung vorzubereiten. Selbst wenn die Technik perfekt scheint, bleibt der Risikofaktor Mensch. Die Mitarbeiter brauchen nicht nur eine moderne IT-Ausstattung, sondern müssen ihre Geräte auch richtig bedienen können. Zudem sollte ihnen ein Grundverständnis für verschiedene Arten von Cyber-Attacken sowie generell eine hohe Sensibilität für das Thema vermittelt werden.
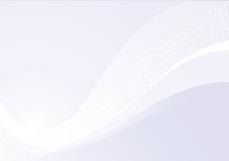
Kontakt Uwe Kissmann Accenture AG Frauenmünsterstrasse 16 CH-8001 Zürich +41 44 219 88 89 uwe.kissmann@accenture.com www.accenture.com
Staubfreies, gut rieselfähiges Granulat mit definierter Korngrösse.
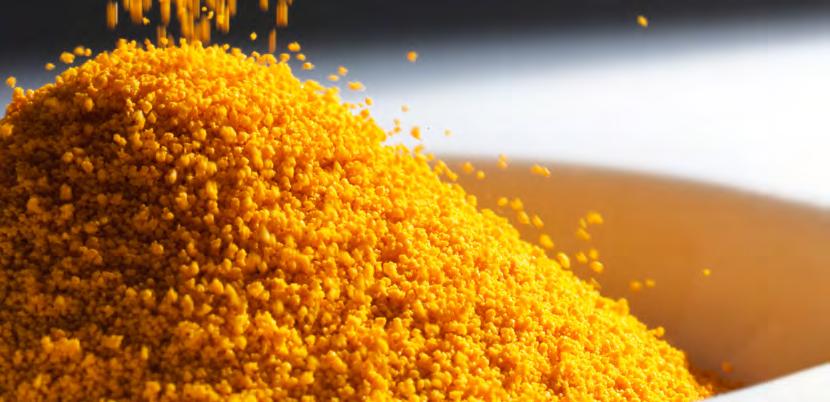
Instantprodukte
Staubfreies Granulat statt Pulver
Instantprodukte zeichnen sich durch eine sehr schnelle Löslichkeit in Flüssigkeiten aus. Ihr Einsatzspektrum ist sehr weit und sie kommen nicht nur als Fertigprodukte zum Einsatz, sondern der Instanteffekt kann auch für innovative Vor- oder Zwischenprodukte genutzt werden. Im Gegensatz zur Pulverform – eine klassische Form von Instantprodukten – weisen Granulate erhebliche Vorteile in der Anwendung auf.
Pierrette Meyer¹
Outdoor-Sportler und Wander-Begeisterte kennen das Problem: Wo es auf leichtes Gepäck ankommt und sauberes Wasser leicht verfügbar ist, sind Instantprodukte für die (Zwischen-) Verpflegung beliebt. Die Zubereitung ist jedoch mit Tücken verbunden: Das pulverförmige Produkt fällt stossweise aus der Packung, deren Ecken sich erst durch Schütteln entleeren lassen, und überzieht die nähere Umgebung mit einem feinen Staubfilm; das Pulver kann nur ungenau dosiert werden, setzt sich im Wasser ab und bildet Klumpen; Pulverreste in angebrochenen Tüten verklumpen und werden unbrauchbar. «Schuld» daran ist die charakteristische, sehr feine und amorphe Partikelstruktur von Pulvern.
¹ Erbo Spraytec AG, Bützberg Weites Spektrum an verschiedenen Granulaten.

Besondere Eigenschaften
Als Alternative bietet sich die Herstellung von (Mikro-)Granulaten mittels Wirbel schichttechnologie statt Pulverprodukten an. Granulate zeichnen sich durch eine definierte und enge Korngrösse aus. Die einzelnen Körner bestehen, je nach Herstellungsart, aus einem Agglomerat einzelner Pulverpartikel oder zwiebelschichtartig auf
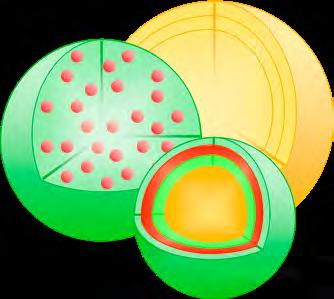
Schematische Darstellung von Verkapselungsmöglichkeiten: Mehrschicht-Coating (im Vordergrund), Matrixverkapselung (in der Mitte) und Sprühgranulierung (im Hintergrund).
gebauten Einzelkörnern. Im Gegensatz zu Pulvern sind Granulate staubfrei, gut fliessund rieselfähig, genau dosierbar, nicht hygroskopisch und die enge Partikelgrössenverteilung verhindert eine Entmischung von kleineren und grösseren Partikeln.
Von «Zwiebelschalen» bis Matrixverkapselung Mittels Wirbelschichttechnologie kann aber nicht nur die physikalische Form der Partikel beeinflusst werden. «Zwiebelschalen»-Granulation, Matrixverkapselung oder (Mehrschicht-) Coating bieten die Möglichkeit, das Produkt mit zusätzlichen Eigenschaften zu versehen. So können zum Beispiel Mineralstoffe, Pflanzenextrakte oder Aromastoffe verkapselt, oder die einzelnen Partikeln mit einer weiteren Substanz (z. B. Riechstoff oder Trennmittel) umhüllt werden. Der Phantasie sind keine Grenzen gesetzt. Das Einsatzgebiet von Sprühprodukten und Mikrogranulaten ist sehr weit. Neben der Getränke- und Lebensmittelbranche Familienbetrieb im bernischen Oberaargau Die Erbo Spraytec AG ist ein Unternehmen der Erbo Group, eines Familienbetriebs in der vierten Generation. Die Gruppe zählt rund 250 Angestellte. Der Sitz der Erbo Spraytec AG befindet sich in Bützberg, einem Dorf der Gemeinde Thunstetten in der Nähe von Langenthal. Quelle: Erbo Spraytec AG
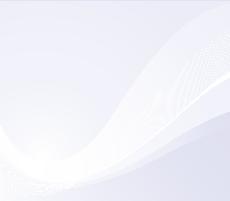
kommen die Produkte auch in der kosmetischen, technischen und chemischen Industrie oder Futtermittelbranche zum Einsatz. Als clevere Vorprodukte können sie auch die Herstellung von innovativen Endprodukten vereinfachen oder ermöglichen. Die Herstellung von innovativen und qualitativ hochwertigen Sprühprodukten erfordert viel Erfahrung sowohl in Hinblick auf die Anlagen-Technologie als auch auf die Eigenschaften der verwendeten Roh stoffe.
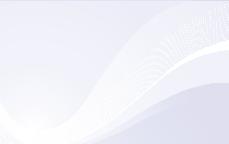
Kontakt Erbo Spraytec AG Industriestrasse 17 CH-4922 Bützberg +41 62 958 88 88 info@erbo-spraytec.ch www.erbo-spraytec.ch
Erfolgreich werben mit der ChemieXtra. Machen Sie den richtigen Zug!

+41 56 619 52 52 · info@sigimedia.ch
Praktische Statistik-Kurse mit Excel!
mit Übungen am PC
Statistische Versuchsplanung und Optimierung am PC Teil A: 14.–15.5.20: Einführung, Screening, Modellierung, Optimierung, grafische Analyse. Teil B: 18.–19.6.20: Optimierung von Formulierungen, eigene spezifizierte Versuche u.v.a. Visualisierung von Labordaten mit Excel 28.–29.4.20 Statistische Analyse von Labordaten mit Excel 16.–17.6.20 Methodenvalidierung in der Analytik 22.–23.6.20 • Alle Methoden werden mit praktischen Beispielen illustriert und direkt am PC geübt. Kein mathematischer Formalismus. • Kursort: Basel. Les cours sont aussi disponibles en français.
AICOS Technologies AG, Sandweg 46, CH-4123 Allschwil, Tel. 061 686 98 76, Fax 061 686 98 88, E-Mail: info@aicos.com Einführung in die multivariate Datenanalyse 18.5.20 Analyse der Stabilität u. Haltbarkeit von Produkten 4.–5.6.20 Statistische Qualitäts- und Prozesskontrolle 8.6.20 Viele weitere Kurse sind auch verfügbar!
www.aicos.com
Mit 90 Prozent weniger Arbeitsaufwand
Neue Sicherheit in der Verfahrenstechnik
Jede und jeder, der mit Chemikalien umgehen muss, weiss, wie wichtig Sicherheitsmassnahmen und -vorschriften sind. Dem erfahrenen Praktiker ist allerdings bewusst, dass gerade die Routine schnell zur Gefahr werden kann. Aus Gewohnheit werden fehlerhafte oder gar gefährliche Praktiken übersehen. Ein geschulter Blick von aussen auf die internen Prozesse kann helfen, ungeahnte Risiken aufzuspüren. Ein Unternehmen schult die Mitarbeiter und deckt Schwachstellen mithilfe eines Worst-Case-Szenarios auf.
Die Betreiber von Chemieanlagen identifizieren Risiken ihrer verarbeitenden Prozesse und gegebenenfalls ergreifen sie Schutzmassnahmen. Eine spezielle Prü fungsmethode ist hierbei nicht gefragt, die Unternehmen führen jedoch in der Regel umfassende Analysen wie das Standardverfahren Paag durch, das sehr zeitaufwendig ist. Dabei müssen sämtliche denkbare Abweichungen von der Sollfunktion erst anhand von zahlreichen Parametern erarbeitet werden. Durch die wiederholte Routine und das immer gleiche Abfragen der Parameter kann es ausserdem zu Fehlern kommen. Um dieser Problematik entgegen zu wirken, hat Verfahrens- und Umwelttechnik Kirchner (VUT Kirchner) den «Process Safety Quick Check» (PSQC) entwickelt: Auf der Grundlage von Worst-Case-Szenarien kann innerhalb kürzester Zeit ein Überblick über die wesentlichen Risiken in einer Anlage gewonnen werden. Durch kritisches Hinterfragen des betriebsinternen Wissens sorgt der eingesetzte Spezialist (der sog. Moderator) für neue Perspektiven bei bereits geprüften Einheiten und korrigiert frühere Analysefehler. Im Oktober 2016 forderte ein Unglück auf dem Gelände der BASF in Ludwigshafen fünf Menschenleben und hinterliess neben zahlreichen Schwerverletzten noch einen zweistelligen Millionenschaden. Ursächlich hierfür war laut eines Berichts der Tagesschau des Fernsehsenders ARD vom 5.2.2019 ein externer Mitarbeiter, der fälschlicherweise eine gasführende Lei tung angeschnitten hatte. Solche Ereignisse zeigen, wie schwierig es ist, sämtliche Gefahrenquellen in komplexen Verarbeitungsprozessen abzudecken. Selbst gängige Analysen wie das Paag-Verfahren, die
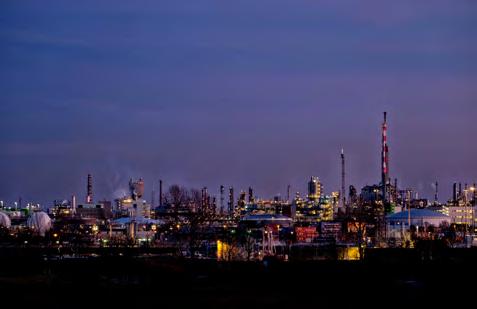
Selbst gängige Analysen wie das Paag-Verfahren, die Gefahrenpotenziale vorab identifizieren und so Unfälle verhindern sollen, können auch nach wiederholter Anwendung noch Lücken aufweisen.
Gefahrenpotenziale vorab identifizieren und so Unfälle verhindern sollen, können auch nach wiederholter Anwendung noch Lücken aufweisen. «Niemand kann sagen, wo das letzte Risiko verborgen ist, eine hundertprozentige Sicherheit gibt es nicht», erklärt Dr.-Ing. Robert Kirchner, Gründer und Geschäftsführer der VUT Kirchner. Trotz dieses Restrisikos muss der Anlagenbetreiber jedoch die Betriebssicherheit gewährleisten. Bei Paag, einem der Standardverfahren in der Risikoanalyse chemischer Verarbeitungsbetriebe, werden nach dem Leitwortverfahren Parameterabweichungen von der Sollfunktion einer bestimmten Pro zesseinheit anhand von R+I-Fliessbildern hinterfragt. Dieser Vorgang nimmt jedoch viel Zeit in Anspruch, da erst eine ausführliche Funktionsbeschreibung der gesamten Anlage erfolgt und zusätzlich mögliche Ursachen, Auswirkungen sowie die erforderlichen Gegenmassnahmen für einen nicht ordnungsgemäss ablaufenden Prozess ermittelt werden müssen. Zudem bleiben Risiken, die aus der Kombination von mehreren Abweichungen resultieren, unerkannt. Auch die häufig auftretende Fluktuation in der Belegschaft und der damit einhergehende Know-how-Verlust machen langfristige Analysen ineffizient und erfordern kurzfristig umsetzbare Aktionskonzepte. Nicht zuletzt kann bei wiederholter Anwendung eine gewisse routinemässige Nachlässigkeit eintreten oder es können sicherheitsrelevante Aspekte bei Änderungen an den Prozesssystemen übersehen werden. Zum Beispiel wenn ein leicht veränderter Rohstoff, der unter der Annahme gleicher Qualität billiger eingekauft wurde,
doch veränderte Eigenschaften aufweist, die erhöhte Ablagerungen verursachen und damit verkürzte Wartungsintervalle notwendig machen.
Worst-Case-Szenarien provozieren Als Alternative und vorbereitende Massnahme zum Paag-Verfahren bietet sich nun der PSQC an. Der «Quick Check» erfordert deutlich weniger Arbeitszeit eines Fachteams und bietet eine solide Grundlage für ausführlichere Untersuchungen. Entwickelt wurde das an Paag und die «Layer of Protection Analysis» (Lopa) angelehnte Verfahren von VUT Kirchner in den Jahren 2017 und 2018 während eines Grossprojekts mit einem internationalen Chemiekonzern. Die Herausforderung bestand darin, ein Risikoranking zu entwickeln, um den bestmöglichen Ansatzpunkt für eine umfassende Analyse zu finden. «Der PSQC diente dabei als ein Voraus wahlverfahren», berichtet Kirchner. Durch den Einsatz des PSQC war es möglich, von den 100 untersuchten Einheiten diejenigen zu identifizieren, bei denen eine tiefergehende Analyse überhaupt erforderlich ist. Auf diese Weise konnte Zeit und damit Geld gespart werden. Der Ablauf des PSQC orientiert sich am Paag-Verfahren: «Der Moderator erarbeitet gemeinsam mit dem Betriebsteam die nötigen Fakten und Beurteilungen. Er formuliert provozierende Worst-Case-Szenarien und fragt gezielt nach Lücken im Wissensstand der Mitarbeiter. Dabei bildet sich eine eigene zwischenmenschliche Dynamik mit neuem Erkenntnispotenzial», so Kirchner. Das Verfahren verläuft wie folgt: Nach einer Einteilung der Anlage in «Check Units», also Einheiten, wird im ersten von sechs Schritten ein erfahrenes Betriebsteam aufgestellt, das sich intern mit den relevanten Sicherheitsfragen vor Ort auseinandersetzt. Es besteht mindestens aus einem Anlagenfahrer, einem Ingenieur, einem weiteren Ingenieur für Prozessleittechnik sowie einem Vertreter des Instandhaltungspersonals. Das Betriebsteam setzt anschliessend in einem zweiten Schritt den Moderator als Experten auf dem Gebiet der Risikoanalyse über die Funktionsweise der Einheit ins Bild und bespricht mit ihm mögliche Ge
fahren. Zur Vorbereitung einer zweiten Sitzung erstellt der Moderator nun vier Worst-Case-Szenarien je Einheit, so dass die schlimmsten denkbaren Ereignisse und deren Verhinderung diskutiert werden können. Diese Szenarien werden wiederum gemeinsam mit dem Betriebsteam betrachtet, ergänzt und nach der Lo pa-Methode bewertet, so dass der Moderator in einem fünften Schritt die wesentlichen Risiken und Massnahmen zur Minimierung in einem Berichtsentwurf zusammenfassen kann. Für die Schlussfassung des Protokolls findet zuletzt eine erneute Überprüfung durch das Betriebs team statt. Somit liegt ein Dokument vor, das als Grundlage für eventuelle Projekte zur Risikominimierung und ausführlichere Sicherheitsanalysen dienen kann.
Vier statt 40 Stunden Zeitaufwand Insgesamt fallen während des PSQC damit nur zwei Sitzungen à zwei Stunden mit dem Moderator an, was einen klaren Vorteil gegenüber der umfangreichen Paag-Analyse darstellt: «Der übliche Ar beitsaufwand für eine Paag-Untersuchung liegt bei ungefähr 40 Stunden bezogen auf eine Einheit. Mit dem PSQC genügt eine reine Teamzeit mit Moderator von gerade einmal vier Stunden», rechnet Kirchner vor. Gleichzeitig verringert sich der Aufwand im Rahmen einer anschliessenden Untersuchung erheblich, da die eingesetzten Mitarbeiter nun besser mit der Thematik vertraut sind. Hier ergibt sich wiederum eine Zeitersparnis von bis zu 50 Prozent. Zusätzlich erzeugt der Moderator in seinen Gesprächen mit dem Betriebsteam eine produktive Konfliktatmosphäre, indem er Wissenslücken auslotet, mit eigenem Know-how ergänzt und das Team konstruktiv unterstützt. Durch die Verteidigungsposition der Betriebsmitarbeiter ergeben sich dynamische Situationen, in denen neue Perspektiven entstehen können. «Ein Fragenkatalog ist leicht abzuarbeiten. Die Schwierigkeit besteht aber darin, das Team vor Ort so zu befragen, dass auch tatsächlich alle relevanten Risiken entdeckt werden», erklärt Kirchner. Denn anders als beim Paag-Verfahren beschränkt sich der PSQC auf wenige Parameter. Durch das Aufstellen von Worst
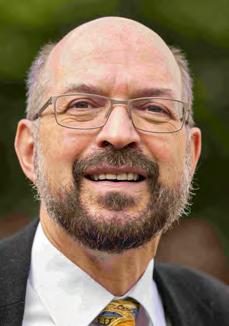
Robert Kirchner, Gründer und Geschäftsführer der VUT Kirchner.
Case-Szenarien für jeweils eine bestimmte Einheit im Betrieb werden jedoch die wesentlichen Risiken erfasst und gleichzeitig das Fundament für weitergehende Unter suchungen gelegt. Damit kann bei guter Vorbereitung von Team und Moderator durch den PSQC das Gesamtrisiko einer Einheit beziffert und mit den anderen Einheiten in einer Rei henfolge sortiert werden. Folglich werden weder Risiken überbewertet noch wesentliche Gefahren vernachlässigt, im Gegenteil: «Das Team findet eher Fehler in früheren Sicherheitsanalysen und konzentriert sich auf neue Erkenntnisse. Andere Analysen zu ergänzen, sicherer zu machen, ist Aufgabe des PSQC», fährt Kirchner fort. So eignet sich das Verfahren nicht nur bei Erstuntersuchungen, sondern auch für die wiederholte Analyse, um unbekannte Risiken aufzudecken und den Aufwand für Sicherheitsanalysen und -investitionen klar zu priorisieren.

Kontakt Verfahrens- und Umwelttechnik Kirchner Dr.-Ing. Robert Kirchner Barfüsserstrasse 20 D-99817 Eisenach +49 3691 7038011 info@umwelttechnik-kirchner.de www.umwelttechnik-kirchner.de