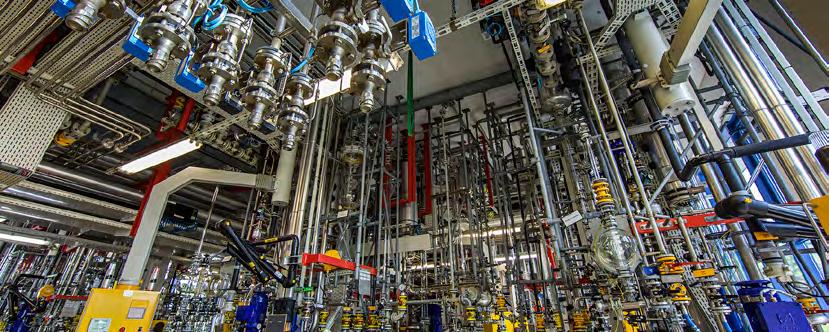
15 minute read
FIRMEN BERICHTEN
from ChemieXtra 1-2/2020
by SIGWERB GmbH
Wer heute eine Anlage für pharmazeutische Produkte betreibt, darf punkto Standardisierung nicht auf der Strecke bleiben.
Gute Herstellungspraxis
Advertisement
Zertifikate für Sensoren
In Bubendorf mit seinen nicht einmal viereinhalbtausend Einwohnern ist man am Hauptsitz der Carbogen Amcis AG mittendrin im Baselbieter Pharma-Cluster. Das Unternehmen hat sich entsprechend spezialisiert auf exklusive Zwischenprodukte für die Grossen der Branche. Hier sorgen Druckmessumformer der Vega für Vereinfachung: In den Prozessen und bei deren Qualifizierung.
Claudia Homburg¹
Pharmaunternehmen sehen sich seit geraumer Zeit Veränderungen ausgesetzt, die das Markt- und Wettbewerbsumfeld umkrempeln. Die Nachfrage nach personalisierten Medikamenten und die Anforderungen an lückenlos nachweisbare Qualität steigen. Treiber der geforderten Innovationen sind oft die kleineren, for schungsnahen Unternehmen, die ihre Prozesse und Genehmigungsverfahren flexibel gestalten und Arbeit wie auch Kosten durch Standardisierung senken. Die Carbogen Amcis AG ist ein solches Unternehmen.
Weniger ist mehr
Die Gleichung ist lang – aber dennoch einfach: Weniger Geräte sind gleich weniger Planungsaufwand, Materialrisiko, Lagerkosten und Zeitaufwand. Ob Pharmaunternehmen für die Zukunft gerüstet sind,
oder ob sie aufgrund hoher Kosten und wegen zu komplexer Prozessmodelle dem Wettbewerb nachrennen werden, das entscheidet unter anderem ihr Grad an Standardisierung in der Fertigung. Dabei wird häufig der Aufwand einer gerechten Qualifizierungsdokumentation, welcher der guten Herstellungspraxis (GMP) entspricht, unterschätzt. Unter dem Aspekt des hohen Qualifikationsaufwands setzt Heiko Kaiser, Senior Manager Engineering und Maintenance bei der Carbogen Amcis AG, jedoch strikt auf möglichst die gleichen Sensortypen. Es war den Ingenieuren um Heiko Kaiser besonders wichtig, Anzahl und Variantenvielfalt aller an ihren Prozessen beteiligten Sensoren und Komponenten stark zu verringern. «Jede Art von Vielfalt macht am Ende des Tages unnötige Arbeit», fasst Kaiser sein Hauptaugenmerk zusammen. «Weniger Varianten sind auch im Handling einfacher und schneller.»
Einheitliche Plattformen
Die Branche steht vor Herausforderungen. Ihre Kosten im Bereich der Forschung und Entwicklung wachsen steil an, die internationalen Regularien für Produktionsanlagen werden komplizierter und dementsprechend auch ihr Dokumentationsaufwand. Seit vielen Jahren kommt dabei der erwähnten GMP eine zentrale Bedeutung zu. Sie definiert bei der Spezifizierung und Validierung von Komponenten und Produkten die Anforderungen an Konformität und ihre Nachweisbarkeit. Damit sehen sich Heiko Kaiser und seine Mitarbeitenden in ihrer praktischen Arbeit, mit der Skalierung von Lebenszyklen oder der Strukturierung des Qualitätsmanagements, zusätzlichen Aufgabenfeldern gegenüber. Die EU-GMP-Regularien fordern durchgängig die gleichen Eignungsnachweise: auch für einzelne, untergeordnete Komponenten und auch in weniger aggressiven Bereichen. Diese reichen von der Designqualifizierung (DQ) über die Installations- (IQ) und Funktions- (OQ) bis hin zur Leistungsqualifizierung (PQ). Die Regularien fordern zudem Belege in Form detaillierter Masterpläne, die die Regelkonformität plausibel widerspiegeln. Die Mitarbeitenden strebten möglichst
Doppelt hält besser: Durch das Sichtfenster lässt sich der Prozess beobachten.
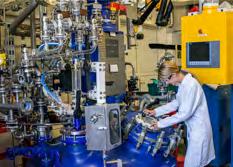
einheitliche Plattformen an, die ihnen helfen würden, ihre Entwicklungs- und Qualifizierungskosten zu kontrollieren. Die gründliche Erstellung lohnt sich, denn sie bleibt keine einmalige Angelegenheit. Letztlich können mit einmal geleisteter Arbeit auch künftige Standorte weltweit flexibel und kostengünstig gestaltet werden. GMP greift international, und sie schafft Wettbewerbsvorteile im um kämpften Markt. Im Einsatz bei der Carbogen Amcis AG sind die Druckmessumformer Vegabar 82, die mit einer keramischen Messzelle ausgestattet sind. Die doppelte Messzellendichtung schafft zusätzliche Flexibilität. Sie sitzt sowohl seitlich als auch zusätzlich vorn am Sensor. Die robuste Keramik membran, die durch den herrschenden Prozessdruck beeinflusst wird, trennt den Sensor sicher von den anspruchsvollen Medien. Ihre Kapazitätsänderung in der abrasionsfesten Messzelle wird – umgewandelt in ein elektrisches Signal – als Messwert ausgegeben. Alle Sensoren bringen die benötigten Werkstoffzertifikate nach 3A, FDA oder EHEDG von Haus aus mit. Unter anderem bestehen die Senso ren aus spezieller Saphir-Keramik in Verbindung mit Polyvinylidenfluorid (PVDF). Entwickelt wurde diese mit hochreiner Al 2 O 3 -Keramik (99,9 %). Schnelle Temperaturschwankungen beeinflussen die Druckmessung bei keramischen Messzellen nicht. Dafür wurde nämlich die Keramik-Grundkörper-Membran auf der druckabgewandten Seite mit Gold beschichtet und bietet nun hohe Beständigkeit, indem sie Temperaturwechsel mit einer Genauigkeit von ± 2 K sofort registriert. Minutenlange Ausfälle, wie bei Keramikzellen durchaus nach wie vor üblich, sind dank dieser Beschaffenheit endgültig ein Phänomen der Vergangenheit.
Die Kleinen müssen das selbst machen Aktuelle Studien legen nahe, dass Modularisierung und Standardisierung zukünftig zu ausgeprägten Differenzierungen der Betriebsmodelle von Pharmaunternehmen führen werden. Zugleich sehen sie dabei reichlich Bedarf und Potenzial für Modelloptimierungen. Die Zeichen der Zeit sind klar. «Wir verbessern und planen sehr weitreichend. Aber natürlich kommt dann wieder der Alltag und unsere Kunden und grosse Projekte stehen vor der Tür.» So bleiben auch für Kaiser manche Punkte, die er mit Blick auf die Verfahrenstechnik zeitnah lösen will, länger offen, als gewünscht. Wie kann er künftig insbesondere Downstream-Prozesse ressourcenbewusst in standardisierter, modularer Form umsetzen? Welche Automatisierungsmassnahmen unterstützen seine modularen Anlagen dabei optimal? Im Jahr 2030 soll die personalisierte Me dizin gemäss konservativeren Prognosen einen Marktanteil von annähernd 30 Prozent haben. «Wir werden in Zukunft immer mehr beweisen müssen», blickt Kaiser in die Zukunft, «die Grossen werden, wo es geht, ihre Kalibrierungen auslagern. Die Kleinen müssen das selbst machen.» Die Aufgaben werden ihm folglich nicht ausgehen, wenn er mit dem beständigen Wandel des Pharmamarktes Schritt hält.
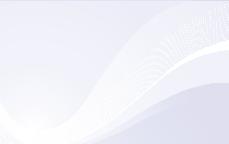
Kontakt Vega Messtechnik AG Barzloostrasse2 CH-8330 Pfäffikon ZH +41 44 952 40 00 info.ch@vega.com www.vega.com
C+S Chlorgas GmbH

Haed-Office Reit 4 94550 Künzing

Tel.: +49 (0) 8547 914 9926 Fax: +49 (0) 8547 914 9921 Mail: info @ chlorgas.de
Die C+S Chlorgas GmbH weiter auf Erfolgskurs

Das Familienunternehmen erweitert den HCl Betrieb in Bitterfeld. Durch erfolgreiche Partnerschaften mit nationalen und internationalen Unternehmen hatte die C+S Chlorgas GmbH ein stetiges Wachstum beim Verkauf von HCl-Gas. Der Erfolgskurs führte zur Entscheidung, die Kapazität um 1000 Tonnen im Jahr zu erweitern.

Damit verbunden sind räumlicheund anlagentechnische Investitionen in erheblichen Ausmassen für Produktion, Abfüllung und Service.
Wir freuen uns auf eine weiterhin harmonische und erfolgreiche Zusammenarbeit mit unseren Partnern und freuen uns auf neue Vertriebspartner.
Schweizer Start-up digitalisiert Labore
Flexible Software für Qualitätssicherung
Das Labor der Micarna in Bazenheid (SG), welche zur M-Industrie gehört, bildet das Herzstück der Qualitätssicherung und analysiert über 15 000 Proben pro Jahr für über 20 Produktionsstandorte in der Schweiz. Als einer der führenden Fleischverarbeiter der Schweiz erfüllt das Unternehmen seit jeher die höchsten Qualitätsstandards. Bis anhin dokumentierten die Laborantinnen die Prozesse und Resultate auf Papier. Nun wagten sie den Sprung in die digitale Welt. Ein junges Start-up half ihnen dabei.
Hier stellte sich also die Frage: «Warum ein gut funktionierender QS-Prozess geändert werden soll?» Für Stefania Cesarano, Laborleiterin der Micarna, ist die Frage nicht «warum» etwas verändert werden soll, sondern «wie gross der Mehrwert» einer Veränderung ist. Für sie war schon immer klar, dass Prozesse stetig optimiert und weiterentwickelt werden müssen. So hat sie die Laborprozesse des Unternehmens in den letzten zwei Jahren standardisiert.
Eine Alternative zu starren Systemen Mit ihrem stetigen Streben nach Optimierung ist Cesarano 2017 auf das Start-up 1Lims gestossen. Damals absolvierten zwei der vier Gründer des Schweizer Startups noch ihr Bachelorstudium an der Zürcher Hochschule für Angewandte Wissenschaften (ZHAW) in Wädenswil. Das Gründerteam konnte aber bereits das Interesse von der engagierten Laborleiterin mit einem Prototyp ihrer Software und dessen innovativen Ansatz wecken. Die Vision von 1Lims war es, eine Qualitätssicherungssoftware zu entwickeln, die es jeder Firma ermöglicht, ihre spezifischen Prozessanforderungen individuell und selbstständig zu konfigurieren. Ent sprechend sollte so eine einfach konfigurierbare und benutzerfreundliche Alternative zu den starren und sehr kostspieligen Systemen entstehen, welche bis anhin auf dem Markt erhältlich waren.
Keine Programmierkenntnisse erforderlich Laut Samuel Schmid, CTO von 1Lims, bestehe die Innovation von 1Lims in der ver
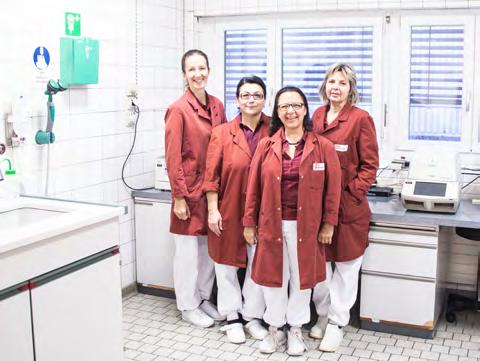
Bild 1: Das Laborteam von Micarna (v. l.): Zorica Samac (Laborantin), Ayfer Kizilkaya (Laborantin), Stefania Cesarano (Laborleitung) und Daniela Jadanza (Laborantin).
wendeten Technologie. Im Gegensatz zu anderen Lösungen für Labor-Informationsund Management-Systeme (Lims) setzt das Start-up auf modernste Web-Technologien wie Angular und NodeJS. In Kombination mit der Microservice-Architektur konnte eine leistungsfähige Lösung entwickelt werden, welche auch einfach und schnell von jedem Nutzer ohne besondere Kenntnisse in der Programmierung konfiguriert werden kann. Ergänzend zu den Standardmodulen für die Qualitätssicherung – wie etwa die Probenverwaltung, die Erstellung von Analysenzertifikaten und Rückführbarkeit – hat sich das Jungunternehmen auch auf die Auswertung und Visualisierung von Daten spezialisiert, welche sich auf der Benutzeroberfläche (siehe Bild 2) individuell zusammenstellen und personalisieren lassen. Ausserdem lassen sich aus den erfassten Daten beispielsweise die Auftragsverteilung, die Auslastung von Teams oder auch verschiedene Trends herauslesen. Nebst der Innovationskraft birgt ein Startup in seiner frühen Entwicklungsphase aber auch Risiken. Stefania Cesarano hat sich dennoch explizit für eine Kooperation entschieden, da sie einen klaren Mehrwert gegenüber herkömmlichen Softwareanbietern feststellen konnte und das Risiko abschätzbar war. Ein wichtiger Punkt war auch die Möglichkeit als Entwicklungspartner, die Software mit zu entwickeln und so ein Produkt zu schaffen, das wirklich effektiv und auch noch benutzerfreundlich ist.
Eindeutiger QR-Code für alle Standorte
Mit der vielversprechenden Partnerschaft wurde das Labor in Bazenheid schrittweise digitalisiert. Nach einer ersten Testphase und kleineren Anpassungen wurde eine Schnittstelle in das vorhandene SAP-Sys tem integriert sowie bestehende Daten importiert. Weiter wurden schweizweit über 20 Produktionsstandorte in das neue System eingegliedert und mit QR-Drucker ausgestattet. Somit können Proben vor dem Versand ins Zentrallabor nur noch mit dem eindeutigen QR-Code ausgestattet werden und so beim Eintreffen in Bazenheid direkt vom System über ein Tablet (bzw. Handscanner) eingescannt und erkannt werden. Ausserdem haben die Standorte so einen direkten Zugang zum Status und der Resultate ihrer Proben – und das über den gesamten Analyseprozess. Ein Jahr nach dem Betriebsstart von 1Lims konnte bereits festgestellt werden, dass die Effizienz der Arbeitsabläufe in der Qualitätssicherung von Micarna um 50 Prozent zugenommen hatte, das Probenvolumen konnte somit gesteigert werden. Die Fehlerquote wurde um mehr als 20 Prozent gesenkt und der Faktor Mensch als Fehlerquelle wurde minimiert. Ebenfalls wurde durch die Digitalisierung der Papierverbrauch im Labor nachhaltig um ganze 90 Prozent reduziert. Das Jungunternehmen konnte sich seitdem im Schweizer Markt als innovative Softwarelösung für die Qualitätssicherung in der Lebensmittel- und Chemiebranche sowie für Komplettlösungen für Auftragslabore etablieren. Die Micarna entwickelte sich gleichzeitig zum Vorreiter in der Labor-Digitalisierung der M-Industrie. Für Cesarano, wie auch für das Team von 1Lims, war das aber erst der Anfang. Sie entwickeln bereits gemeinsam eine Integrationsplattform, welche in der Lage sein soll, alle Laborgeräte schnell und einfach ins interne Software-Netzwerk zu integrie
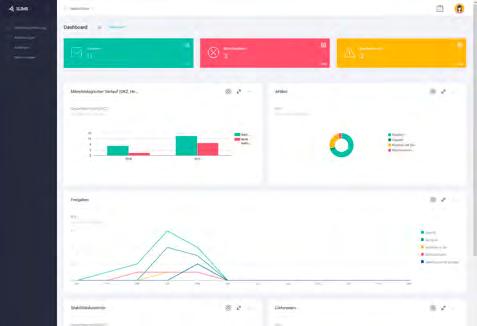
Bild 2: Der Anwender gestaltet die Benutzeroberfläche (das Dashboard) nach Belieben und entscheidet selbst, welche Analysen und Resultate dargestellt werden sollen.
Ihre Botschaft punktgenau platziert!

Bild 3: Philipp Osterwalder, Mitbegründer des Start-ups, begutachtet die Auswertungen der Resultate direkt im Labor.
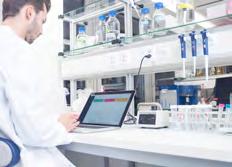
ren. Zudem arbeitet das 1Lims-Team gemeinsam mit anderen Industriepartnern an Themen wie «workflow automation» sowie an der Integration von «Blockchain» (eine dezentralisierte Datenbank) für die gesamte Rückführbarkeit der Wertschöpfungskette als auch an risikobasierten Testplänen und automatisierten Audit-Protokolle. Dieser Erfahrungsbericht zeigt, wie viel Stefania Cesarano und ihr Team zusam men mit 1Lims durch Eigeninitiative, Durchhaltewillen und einer klaren Vision erreichen konnten. Durch die enge Zusammenarbeit wurde auch klar, dass es sich für eine etablierte Firma lohnt, eine Partnerschaft mit einem Start-up einzugehen und genauso umgekehrt. Das Verbinden von Kompetenzen, als auch gemeinsames Entwickeln von Lösungen, bringt alle Beteiligten weiter und birgt eine grosse Innovationsquelle.
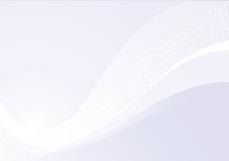
Kontakt 1Lims a Modeso Company c/o Westhive Hardturmstrasse 161 CH-8005 Zürich +41 44 585 20 52 hello@1lims.com www.1lims.com
Hochtemperaturanlage bis 400°C
Eine effektivere Wärmeübertragung
Für einen der grössten deutschen Chemieunternehmen hat der Temperierspezialist Lauda nun eine Wärmeübertragungsanlage entworfen und hergestellt, die auch für die erfahrenen Ingenieure des Unternehmens aussergewöhnlich ist. Denn für eine Arbeitstemperatur von 400°C in grossen Anlagen müssen die Experten wissen, wie sie mit den hohen Arbeitsdrücken umgehen müssen. Dies erfordert Fachkenntnisse aber natürlich auch äusserst stabile Reaktoren.
Das erwähnte Chemieunternehmen benötigte eine Anlage, die eine Arbeitstemperatur von 400°C problemlos erreichen muss. Eingesetzt wird der Heizer im Bereich der Materialforschung, bei sogenannten Scaleup-Versuchen und zur Vorbereitung von Reaktionen, die eine derart hohe Temperatur unbedingt erforderlich machen. «Zum Tagesgeschäft von Lauda gehören Wärmeübertragungsanlagen mit einem Arbeitstemperaturbereich bis 350°C», erklärt Projektleiter Ralph Herbert. «Der Bereich bis 400°C gehört da schon zur Königsklasse.» Dieser werde aber inzwischen vermehrt angefragt, so Herbert, denn er erlaube eine effektivere Wärmeübertragung, ermögliche so einen höheren Durchsatz und damit die Optimierung von temperaturrelevanten Produktionsprozessen. Diese Wärmeübertragungsanlagen nutzen je nach erforderlicher Vorlauftemperatur und Einsatzgebiet verschiedene Arten von Thermalölen (Silikonöl oder eutektische Gemische). Generell werden Sie elektrisch beheizt und erzeugen eine temperierte Flüssigkeitsströmung, welche wiederum die Applikation heizt. Eine Kühloption mittels Wärmetauscher kann je nach Bedarf integriert werden.
Tiefgehende technische Expertise gefragt Das Besondere am Sprung von 350 auf 400°C ist, dass die Ingenieure mit deutlich höheren Arbeitsdrücken umgehen müssen. Auch die applikationsseitig eingesetzten Edelstahlreaktoren müssen grösserer Belastung standhalten. «Liegt der Druck im Wärmeträgerkreislauf bei normalen Wärmeübertragungsanlagen mit Thermalölen noch bei maximal 6 bar, steigt er bei den 400-Grad-Anlagen schon auf bis zu 21 bar,

Königsklasse 400 °C: Anlagen in dieser Temperaturgrösse ermöglichen eine effektivere Wärmeübertragung, einen höheren Durchsatz und damit die Optimierung von temperaturrelevanten Produktionsprozessen.
Die Wärmeübertragungsanlage erreicht problemlos eine Arbeitstemperatur von 400 °C.
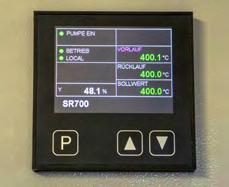
je nach eingesetztem Thermalöl», erklärt Ralph Herbert. Das erfordert besondere Expertise im Rohrleitungsbau sowie in den einzelnen Ausrüstungskomponenten. Lauda selbst fertigt mehrmals im Jahr Wärmeübertragungsanlagen in diesem hohen Temperaturbereich – wobei die Planung und Konstruktion auch immer wieder etwas Besonderes sei, bestätigt Herbert. Das Ingenieurteam plant derzeit Thermalölanlagen bis zur einer maximalen Arbeitstemperatur von 430°C. Für das besagte Unternehmen aus der Chemiebranche wurde die Anlage pünktlich fertiggestellt, im Testfeld von Lauda abgenommen und anschliessend beim Chemieunternehmen gemeinsam in Betrieb genommen.
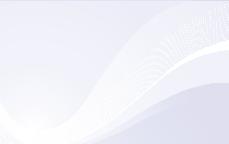
Kontakt Lauda Dr. R. Wobser GmbH & Co. KG Pfarrstrasse 41/43 D-97922 Lauda-Königshofen +49 9343 503 0 info@lauda.de www.lauda.de
Der FWR30 kann einfach mit den passenden Montagesätzen an IBC-Container, Wänden oder Decken montiert werden.

Innovative und mobile Füllstandmessung
Drahtloser Sensor für die Logistik
Das Internet der Dinge (IoT) ermöglicht Unternehmen, immer mehr Informationen aus ihren einzelnen Prozessen zu gewinnen und somit den Prozess zu optimieren. Ein Bereich, der zukünftig hiervon mehr profitieren soll, ist die Logistik. Der Konzern Endress+Hauser hat einen neuen Füllstandsensor entwickelt, der sich besonders für die Logistik eignet. Der neue 80-GHz-Radar-Sensor aus dem Hause des Unternehmens kann nämlich drahtlos über das Mobilfunknetz in Betrieb genommen werden kann.
Die derzeit grössten Informationslücken für Produzenten und Lieferanten stellen schwer zugängliche und mobile Messstellen dar. Rund 85 Prozent aller potenziellen Füllstandsmessungen in Produktionsanlagen oder auf Transportwegen sind zu komplex oder zu kostspielig, als dass sie tatsächlich realisiert würden. Die logische Konsequenz dieses Informationsmangels ist häufig ein Prozessstillstand aufgrund fehlender Bestände. Speziell für die Füllstandmessungen auf Transportwegen wurde der neue Sensor Micropilot FWR30 entwickelt. Dank einem energieeffizienten Radarchip reicht eine einzelne Batterie für die zuverlässi ge Speisung des Geräts und die handliche Grösse sorgt dafür, dass sich der Sensor nahezu überall verbauen lässt. Sofern er mit der Cloud Netilion von Endress+Hauser verbunden ist, ist kein Kabel oder eine sonstige Vorrichtung für die Datenübertragung notwendig. Mit dem Micropilot FWR30 bringt das Unternehmen seinen ersten 80-GHz-Radar-Sensor auf dem Markt, der «wireless»

über das Mobilfunknetz seine Aufgaben wahrnehmen kann.
Einfach und sicher an Messdaten gelangen Die einfache Handhabung steht bei der Realisierung einer solchen Messvorrich tung sicherlich im Fokus: über den kompletten Lebenszyklus des Produktes – von der Bestellung bis zur Inbetriebnahme. Mit der Eingabe des Messbereichs und dem Scannen des QR-Codes (bzw. Eingabe der
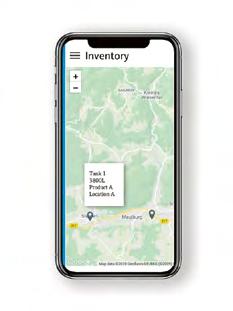

Links: Durch die Lokalisation des Sensors lassen sich z. B. Auslieferungsrouten besser planen. Rechts: Die Historie der Messdaten mit den festgelegten Grenzwerten.
Seriennummer) lässt sich der Sensor in lediglich zwei Schritten in Betrieb nehmen. Dann übermittelt er nicht nur die Füllstanddaten in die Cloud, sondern sendet dem Nutzer Informationen über die Position der Messung, die Umgebungstempe
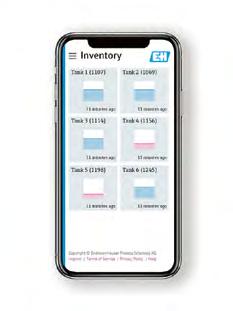
ratur, die Messhistorie sowie den Batteriestatus und die Signalstärke. Darüber hinaus lassen sich Grenzwerte einstellen, die den Nutzer unverzüglich darauf hinweisen, wenn diese unterschritten werden. Aufgrund der häufig eingeschränkten GSM-Netzabdeckung (entspricht dem Mobilfunkstandard 2G) unterstützt der neue FWR30 ebenfalls den Kommunikationsstandard «Narrowband Internet of Things» (NB-IoT). Dieser Standard ist eine Erweiterung des Long-Term-Evolution-Netzes (LTE, entspricht dem Mobilfunkstandard 4G), welches eine hohe Gebäudedurchdringung gewährleistet. Somit können auch Messungen an herausfordernden Lokalitäten bedient werden. Trotz aller Einfachheit wird die Sicherheit der Daten nicht vernachlässigt. Die Cloud Netilion ist mit dem EuroCloud-Zertifikat auf Vier-Sterne-Niveau zertifiziert, welches das höchste Sicherheitsniveau der Prozessautomatisierung bescheinigt.
Die Webapplikation «Netilion Value» bietet eine umfangreiche Grundfunktionalität, wie z. B. eine Benutzeroberfläche (Dashboard) mit den wichtigsten Informationen aller Geräte auf einen Blick.
Massgeschneiderte Funktionalität Jede Applikation bringt ihre eigenen Herausforderungen mit sich. Genauso vielschichtig sind auch die Anforderungen an die Funktionalität der Nutzeroberfläche der
Cloud. Um diesen Anforderungen gerecht zu werden, gibt es in der Cloud Netilion die Möglichkeit, unterschiedliche Abonnements abzuschliessen – je nachdem, wie viele Daten der Nutzer von der Messstelle benötigt. Die Abonnements unterscheiden sich in Anzahl der verbundenen Geräte, in der Aufzeichnungsdauer der Messdatenhistorie sowie im Umfang des technischen Supports. Mit einer Bestandsführung lassen sich Lagerkosten einfach reduzieren und zugleich die Produktivität erhöhen. Sollte ein ERP-System vorhanden sein, so können alle Daten einfach via Anwendungsprogrammierschnittstelle («Application Programming Interface», API) integriert werden.
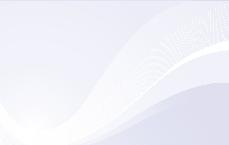
Kontakt Endress+Hauser (Schweiz) AG Kägenstrasse 2 CH-4153 Reinach +41 61 715 75 75 info@ch.endress.com www.ch.endress.com
TOSOH_Ins_58x90_4c_Layout 1 20.12.12 07:47 Seite 1
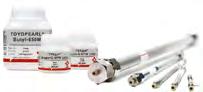
D I S C O V E R N E W S O L U T I O N S F O R L I Q U I D C H R O M A T O G R A P H Y
C
P
Geissbrunnenweg 14 · CH-4452 Itingen BL Tel. 061 971 83 44 · Fax 061 971 83 45 E-Mail: info@sebio.ch · www.sebio.ch