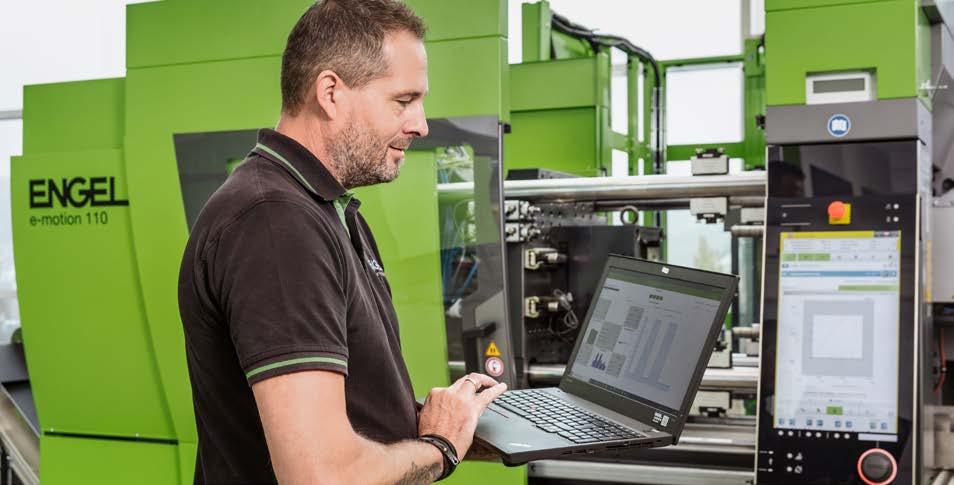
14 minute read
MASCHINEN/ PERIPHERIE
Smart Service und intelligente Assistenz im Fokus
Das volle Potenzial ausschöpfen
Advertisement
Wie lässt sich bei Schwankungen im Rohmaterial eine durchgehend hohe Produktqualität erhalten? Wie kann selbst bei Reiserestriktionen eine hohe Anlagenverfügbarkeit und Produktivität gesichert werden? – Antworten auf diese brennenden Fragen liefert Engel während der Chinaplas 2021 vom 13. bis 16. April in Shenzhen, China.
«Covid-19 hat die Digitalisierung in der Kunststoffindustrie beschleunigt», sagt Gero Willmeroth, President East Asia and Oceania von Engel. «Unsere Kunden investieren zunehmend in digitale Lösungen. smart service und intelligente Assistenz sind in den letzten zwölf Monaten noch stärker in den Fokus gerückt.» Diese Trends spiegeln sich im Engel Exponat wider. Die vollelektrische und holmlose e motion 80 TL Spritzgiessmaschine ist mit zahlreichen digitalen Produkten aus dem inject 4.0 Programm ausgerüstet. Während intelligente Assistenzsysteme der iQ-Serie die Kunststoffverarbeiter unterstützen, das volle Potenzial der Spritzgiessmaschine auszuschöpfen, selbst wenn nicht durchgehend qualifiziertes Personal anwesend ist, geht es bei digitalen Serviceprodukten darum, eine hohe Produktivität zu sichern, um auch im Fall von Krisen lieferfähig zu bleiben.
Sich selbst optimierende Spritzgiessmaschine
Die Mensch-Maschine-Schnittstelle spielt in der Fabrik der Zukunft eine grosse Rolle. Werden die Produktionsprozesse durch Verfahrensintegration und Automatisierung komplexer, muss ihre Steuerung und Kontrolle umso einfacher und intuitiver werden. Hier steigern intelligente Assistenzsysteme die Prozessfähigkeit und Qualität, ohne dass sich der Maschinenbediener zusätzliches Spezialwissen aneignen muss. Während der vier Messetage lassen sich in der CC300 Steuerung der e-motion 80 TL Maschine schwankende Prozessbedingungen simulieren, um das automatische Nachregeln durch die Assistenzsysteme auf dem Maschinendisplay zu verfolgen. So hält beispielsweise iQ weight control das eingespritzte Schmelzevolumen über den gesam-
Bilder: Engel Digitale Serviceprodukte erhöhen die Verfügbarkeit von Maschinen und Anlagen und sichern auch im Fall von Krisen eine hohe Produktivität und durchgehende Lieferfähigkeit ab.
ten Spritzgiessprozess konstant, und iQ clamp control ermittelt auf Basis der Werkzeugatmung die optimale Schliesskraft.
Mehrere hundert Prozessparameter im Blick
Engel entwickelt sein Angebot an intelligenten Assistenzsystemen kontinuierlich weiter. Zu den jüngsten Produkten, die in Shenzhen präsentiert werden, gehören iQ process observer und iQ melt control. Lassen sich mit Assistenzsystemen bislang einzelne Arbeitsschritte des Spritzgiessprozesses optimieren, analysiert der neue iQ process observer über alle vier Phasen des Spritzgiessprozesses – Plastifizieren, Einspritzen, Kühlen und Entformen – kontinuierlich mehrere hundert Prozessparameter, um Drifts automatisch zu erkennen. In Form von Klartextmeldungen weist das System auf ungünstige Prozesseinstellungen und -zustände sowie dafür mögliche Ursachen hin. «Dies hilft dem Anwender, die Stabilität über den Gesamtprozess zu optimieren und Fehler schnell zu beheben», sagt Willmeroth. Ziel von iQ melt control ist es, sowohl das zu verarbeitende Material als auch die mechanischen Komponenten der Plastifiziereinheit zu schonen. In der Praxis wird oft schneller dosiert, als es der Zyklus erfordert, was sich auf die Produktqualität, aber auch die Lebensdauer der Schnecke auswirken kann. iQ melt control ermittelt deshalb die optimale Dosierzeit. Statt mit maximal möglicher Geschwindigkeit zu dosieren, nutzt das System die Kühlzeit des Bauteils im Werkzeug vollständig zum Dosieren aus und sichert dabei eine sehr gute Schmelzehomogenität.
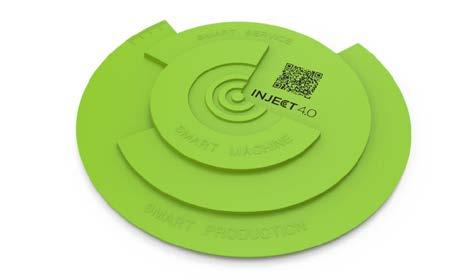
Wie sich das Potenzial der Digitalisierung ausschöpfen lässt, demonstriert Engel mit der Herstellung von inject 4.0 Logos auf einer e-motion 80 TL Spritzgiessmaschine
Simulation und reale Welt vereint
Neu ist auch sim link, eine gemeinsame Entwicklung von Engel und Autodesk, dem Anbieter der Simulationssoftware Moldflow. «Bis heute bleiben viele Erkenntnisse aus der Simulation von Spritzgiessprozessen an der Maschine ungenutzt», erklärt Willmeroth die Motivation. Mithilfe der Software lassen sich jetzt nicht nur die mittels Moldflow optimierten Parameter in einen Einstelldatensatz umformen und direkt in der Spritzgiessmaschine verwenden, sondern umgekehrt auch Prozessparameter und Messergebnisse aus der Spritzgiessmaschine in das Simulationsprogramm von Autodesk importieren. «Wir öffnen damit einer neuen Herangehensweise bei der Optimierung laufender Produktionsprozesse die Tür», so Willmeroth. «Die Simulation beschleunigt die Einstellung, die Rüstprozesse und die Prozessoptimierung und steigert damit deutlich die Produktivität. Simulation wird zunehmend auch für kleinere spritzgiessverarbeitende Betriebe zu einem leistbaren Wettbewerbsvorteil.»
Produktivität auch im Krisenfall absichern
Um die Verfügbarkeit von Maschinen und Fertigungszellen zu steigern, setzt smart service auf Onlineunterstützung und die
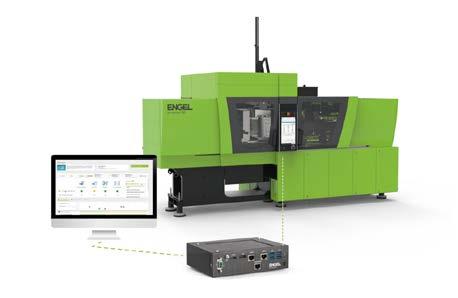
Der iQ process observer analysiert über alle Phasen des Spritzgiessprozesses mehrere hundert Prozessparameter und weist auf ungünstige Prozesseinstellungen und -zustände hin. Mit sim link lassen sich Simulationsdaten direkt in die Spritzgiessmaschine übertragen und umgekehrt Messdatensätze aus der Maschinensteuerung in das Simulationsprogramm importieren.
zustandsbasierte, vorausschauende Instandhaltung. Durch Covid-19 ist vor allem e connect.24 noch stärker in den Fokus der Kunststoffverarbeiter gerückt. Über das Onlinesupport- und Fernwartungstool kann sich der Engel-Servicemitarbeiter von extern auf die jeweilige Spritzgiessmaschine aufschalten, um in allen Supportfällen ohne Zeitverlust zu reagieren. Die Bildschirmseiten der Maschinensteuerung werden über eine sichere Internetverbindung übertragen. Da der Datenzugriff in Echtzeit erfolgt, wird der aktuelle Maschinenzustand abgebildet. So sehen sowohl die Maschinenbediener vor Ort im Betrieb als auch der externe Support dieselben Produktionsdaten, sie können sich beraten und gegenseitig anleiten. Bei Bedarf lässt sich die Fertigungszelle aus der Entfernung steuern. Ein weiterer Nutzen ist, dass der Anwender bei einer Störung per E-Mail informiert wird. Mit diesen Möglichkeiten sichert e connect.24 eine sehr hohe Anlagenverfügbarkeit, auch wenn Reisen nicht möglich sind oder die Produktion zeitweise mannlos läuft. Engel arbeitet im Service nicht mit externen Kräften, sondern setzt ausschliesslich auf eigene Servicetechniker. «Wir haben hier in China umfangreiche Ressourcen und unterstützen unsere Kunden in der Landessprache», betont Willmeroth.

Kontakt Engel (Schweiz) AG Hungerbüelstrasse 17 CH-8500 Frauenfeld +41 52 725 07 57 info.ch@engel.at www.engelglobal.com
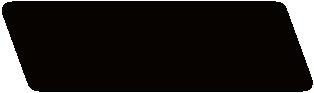
Ihr zuverlässiger Partner, wenn es um Peripherie in der Kunststoffverarbeitung geht!
Bedienung so einfach wie ein Smartphone
Kein Handbuch und keine Schulung notwendig
Kürzeste Stillstandzeiten
Schritt-für-Schritt-Anleitung in Wort und Bild
Integriertes Fernwartungstool
Einfachste und schnelle Unterstützung bei Unklarheiten
Modernste Kommunikation mit OPC-UA
zur Plug-and-Play Anbindung an die Spritzgießmaschinen
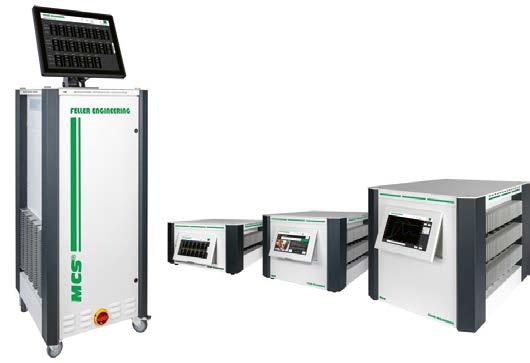
KUMA Solution GmbH | Neuweg 31A | CH-4852 Rothrist | Tel +41 62 794 37 41 | info@kuma-solution.ch | www.kuma-solution.ch
Neue Fertigungszelle für Hochleistungspolymere
Breites Spektrum unterschiedlicher Prüfkörper
Die Entwicklung der Polymere von morgen beginnt mit dem Verständnis der chemischen und mechanischen Eigenschaften sowie des Verarbeitungsverhaltens der Materialien. Im Technikum für Spritzguss und Extrusion bei BASF in Ludwigshafen produziert eine neue vollautomatisierte Spritzgiesszelle von Sumitomo (SHI) Demag mehr als 4000 verschiedene Versuchseinstellungen pro Jahr..
Im Mittelpunkt der Zelle steht eine hochpräzise, vollelektrische IntElect mit 1000 kN Schliesskraft. Neben den wichtigsten Entscheidungskriterien wie kompakter Bauweise, Energieeffizienz und Wiederholgenauigkeit schätzt das 30-köpfige Team im Technikum die verbesserte Komfort- und Sicherheitsausstattung, wie den niedrigen Geräuschpegel aber auch voll digitalisierte Lösungen für den automatischen Werkzeugwechsel und die Robotersteuerung. Der Linear-Roboter SDR 5-35S erfüllt dabei zwei Aufgaben. Zum einen sorgt er für die vollautomatische Platzierung von 12 unterschiedlichen Wechseleinsätzen aus einem Magazin in die Spritzgiessmaschine. Zum anderen entnimmt derselbe Roboter mit seinem multifunktionalen Greifer den Prüfkörper aus dem Werkzeug und gibt ihn an einen kleinen Yaskawa GP8 6-AchsGelenkarmroboter weiter, der die Teile auf einer spindelangetriebenen Stanze ablegt, die den Anguss abtrennt. Das vorhandene Werkzeugeinsatz-Konzept und die weitere, Sonderfunktionen enthaltende Spritzeinheit wurden in die neue Fertigungszelle integriert. Erweiterungen erfuhr die Zelle durch die Einbindung der Temperiergeräte-Steuerung und die Anbindung an das neu eingeführte Manufacturing Execution System (MES).
Werkzeugwechsel
Viele der Prüfkörper, die im BASF Technikum verarbeitet werden, sind glasfaserverstärkte, oft auch mit Flammschutz ausgerüstete Hochtemperatur-Thermoplaste. Infolgedessen erreichen die Schmelzetemperaturen bis zu 400 °C und die Werkzeugtemperaturen bis zu 180 °C. Das Werkzeugmagazin kann über den Roboter mit 12 Wechseleinsätzen bestückt werden. Dank der Integration von HB-Therm Temperiergeräten in die Sumitomo (SHI) Demag Maschinensteuerung erfolgen die Wechsel der Einsätze in die Spritzgiessmaschine auch bei hohen Werkzeugtemperaturen automatisiert und damit sicher und effizient. Markus Hausmann, leitender Ingenieur für Automationssysteme bei Sumitomo (SHI) Demag, erklärt: «Um eine sichere Werkzeugentnahme durch den SDR-Roboter zu garantieren, wird die Temperatur auf 80 °C gesenkt und der Druck im Einsatz herabgesetzt. Dafür muss unsere Maschinensteuerung nahtlos mit dem MES von BASF kommunizieren.» Das MES der BASF benachrichtigt die Zelle, wann das Ende der aktuellen Versuchseinstellung ansteht und übergibt den Befehl zum nächsten Werkzeugwechsel an die Fertigungszelle. Unmittelbar im Anschluss an die Herstellung des letzten Probekörpers wird der Wechseleinsatz von dem integrierten Temperiergerät geregelt abgekühlt. Als nächstes wird der Einsatzwechsel über Ausgangs- und Eingangssignale mit der Zellensteuerung synchronisiert und der neue Werkzeugdatensatz über die Roboterschnittstelle übertragen. Nach dem Einsatzwechsel heizen die Temperiergeräte wieder auf. Der automatische Betrieb läuft an und sobald die Werkzeugtemperatur erreicht ist, wird die Produktion einer neuen Versuchseinstellung gestartet. Für BASF stellt die Problemlösung für die anspruchsvollen Stanzaufgaben eine herausragende Ingenieursleistung innerhalb des gesamten Projekts dar. Aufgrund des umfassenden Einsatzgebietes testet BASF ein breites Spektrum an Materialien – von weichen und zähen bis steifen und spröden Polymeren. Darüber hinaus gibt es viele unterschiedliche Probengeometrien. So variieren die Wanddicken zwischen 0,5 und 4 mm. Viele BASF Prüfkörper werden gemäss ISO 294 produziert. Die Norm definiert die Anforderungen an das Angusssystem und die Geometrie der Proben. «Die Formteiltrennung mittels Stanzen ist Voraussetzung, denn es verändert die Materialeigenschaften nicht und es bilden sich keine Staubpartikel», erklärt Hausmann.
Digitale Integration
Das BASF Team fährt jeden Tag eine Vielzahl unterschiedlicher Versuchseinstellungen auf der Fertigungszelle. Dies bedeutet, dass das MES der Zelle jeweils verschiedene Material- und Prozessparameter, Prüfteilgeometrien und Temperaturen vorgibt. Jeder einzelne Spritzgusszyklus wird anschliessend digital erfasst und dokumentiert. Angelika Homes, leitende Projektingenieurin bei BASF, erläutert: «Das neue System zeichnet aus, dass jeder einzelne Zyklus und eine Vielzahl von Daten aufgenommen werden, was uns vertiefte Einblicke ermöglicht. Diese Daten sind ungemein wertvoll, da sie den kompletten Bearbeitungsablauf repräsentieren und wir tiefgreifende Rückschlüsse ziehen können, wie sich das Material unter bestimmten Bedingungen verhält und wie ein Kunde es später verarbeiten kann.»
Kontakt Sumitomo-Vertretung CH: Mapag Maschinen AG Weissensteinstrasse 2B CH-3000 Bern 5 +41 31 380 86 00 info@mapag.ch www.mapag.ch
Flexibel automatisieren mit Robotern
Maschinenbau für Spezialisten
Die Robotec Solutions AG wurde 1983 gegründet. Das Unternehmen mit Sitz in Seon hat sich auf Industrierobotik und Sondermaschinenbau spezialisiert. In den letzten Jahren verschob sich der Schwerpunkt in Richtung Medizinaltechnik und Pharmaindustrie. Aktuell steht in der Produktionshalle die grösste Anlage der Firmengeschichte. Robotec automatisiert damit die Reinraumproduktion für Pipetten und Verbrauchsmaterial für PCR-Test.
Nick Koch erklärt: «In der Vergangenheit lag ein Schwerpunkt unserer Projekte bei der Beschickung von Fräs- und Drehmaschinen, hauptsächlich in der Uhrenindustrie.» Koch ist Gründer und Geschäftsführer seit Beginn. Heute geht es bei vielen Projekten um die automatisierte Entnahme von Spritzgussteilen. Auch nachgelagerte Prozesse wie Qualitätskontrolle, Verpackung oder Palettierung bieten die Roboterspezialisten an. Die Produktpalette umfasst sechsachsige Roboterarme, kollaborative Roboter bis hin zur mobilen Robotik.
Robotertechnologie ist gefragt
«Wir achten darauf, dass wir das gesamte Knowhow unserer Anlagen im Haus behalten können. Das mechanische Engineering sowie die Entwicklung der Software und der Elektronik findet alles intern statt», sagt Koch. Die Roboterarme selbst stammen hauptsächlich von Fanuc oder Stäubli. Aktuell beschäftigt Robotec rund 30 Mitarbeitende und ab Sommer drei Lernende. Koch: «Wir konnten im vergangenen Jahr um sechs Vollzeitstellen aufstocken, allein durch das Wachstum des Marktes.» Die Robotertechnologie bietet Vorteile gerade auch für die Reinraumproduktion. Die Ingenieure achten auf aufgeräumte Konzepte und bauen mit möglichst wenigen bewegten Teilen. Das heisst, die Anlage ist später einfach zu reinigen und zu warten.
Platz für frische Ideen
Vor zwei Jahren hat Robotec ein neues Gebäude gebaut, «alles aus Holz und mit einer Solaranlage auf dem Dach», sagt Koch und fügt an: «Nachhaltigkeit und eine
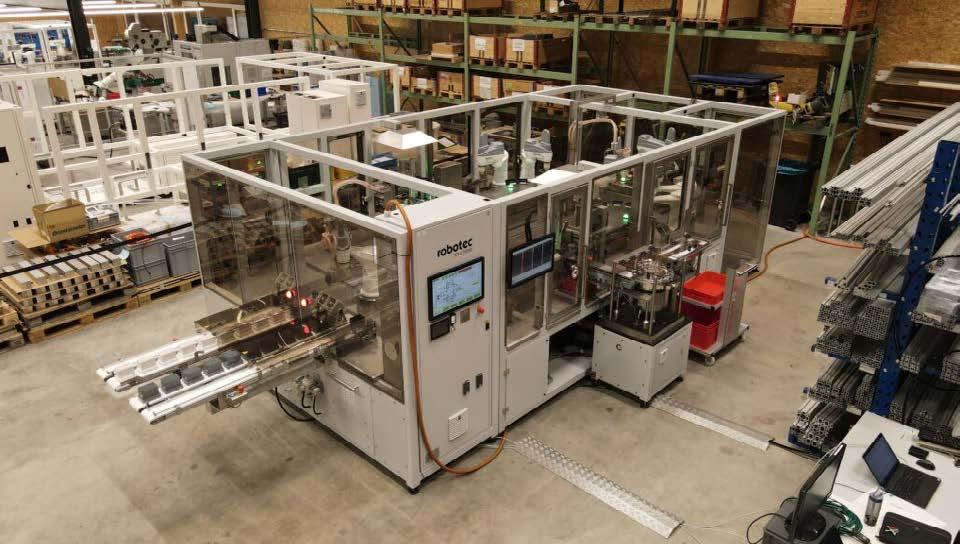
Aktuell produziert Robotec viele Anlagen für die Kunststofffertigung im Reinraum.
angenehme Arbeitsatmosphäre sind uns wichtig.» Der Neubau ist die logische Konsequenz aus dem Wachstum des Unternehmens. Die helle Produktionshalle verfügt über einen Kran und LKW können auf einer Ebene be- und entladen werden. So grosse Anlagen wie sie heute hier stehen, hätten am alten Standort nicht realisiert werden können. Sieht man sich in der Halle um, wird schnell klar, dass es sich um Sondermaschinenbau handelt. Koch: «Der grösste Teil sind kundenspezifische Anlagen. Wenn wir 3 bis 4 gleiche Maschinen pro Jahr machen können, ist das für uns schon eine Serie.» Der Geschäftsführer formuliert es so: «Wir sind keine Firma mit einem Produktkatalog. Bei uns steht immer die Lösung im Vordergrund.» Es geht um den Dialog mit dem Kunden und um Projekte. Die Spanne reicht dabei von kleinen Anlagen ab ca. 80 000 EUR und geht hinauf bis zu Projekten mit einem Budget weit über 1 Mio. EUR. Die grösste Anlage der Firmengeschichte
Aktuell produziert Robotec viele Anlagen für die Kunststofffertigung im Reinraum. Eine davon automatisiert die nachgelagerten Prozesse bei der Herstellung von Pipettenspitzen für PCR-Tests. 7 Scara-Roboter sind für das Teilehandling installiert. Träger mit jeweils 96 Spitzen gelangen über Förderbänder in die Maschine. Der erste Roboter verteilt die Träger auf ein Magnet-Shuttlesystem. Danach fahren die Spitzen nacheinander die verschiedenen Roboterstation ab. Bei einer ersten Kontrolle wird mit Kameras Innen-, Aussendurchmesser und die Braue der Kunststoffteile überprüft. Eine Station weiter werden Filter in die Spitzen eingepresst. Dann überprüft ein Laserscanner ob die Filter richtig sitzen. Anschliessend folgen zwei Roboter von denen der eine Schlechtteile aussortiert und der andere Gutteile einsortiert, sodass in jedem Rahmen 96 korrekt montierte Spitzen in der geforderten Qualität stecken. Schliesslich
werden die Pipettenspitzen in die Verpackung eingelegt, mit einem Label versehen und verlassen die Anlage. Es ist die grösste Maschine, die Robotec je gebaut hat. Sie läuft im Mehrschichtbetrieb und verarbeitet in wenigen Sekunden 96 Spitzen. Die Techniker bauten diese Anlage in der Rekordzeit von 6 Monaten. Die erste wurde in Deutschland bereits in Betrieb genommen, und drei weitere werden in der Schweiz ausgeliefert. Koch: «Es ist nicht alltäglich, dass wir die Entwicklung so schnell vorantreiben. Aber mit Corona befinden wir uns in einer besonderen Situation, und wir wollten unseren Beitrag zum Gesundheitssystem leisten.»
Flexible Lösungen
Ein wichtiger Pfeiler der Unternehmensstrategie ist die Kunststoffbranche. «Wir machen schon lange Spritzgussentnahme. Robotec kommt immer dann ins Spiel wenn es etwas mehr braucht, z.B. Einlegeteile, Inspektion oder nachgelagerte Montageschritte», erklärt Koch. Projekte aus der Kunststoffindustrie haben in den letzten Jahren stark zugenommen. Gerade im Medtech-Bereich oder in der Fertigung von technisch anspruchsvollen Spritzgussteilen. Die Anwendungsmöglichkeiten sind sehr breit. Koch: «Früher war ein Roboterarm neben einer Spritzgussmaschine viel zu teuer. Aber heute drängt sich eine solche Lösung auf, gerade wenn man mehr als nur die reine Entnahme machen möchte. Hier punkten Roboterlösungen vor allem mit ihrer Flexibilität.»
Smart Manufacturing Days & Robotik Workshops Robotec organisiert Workshops für Robotik. Interessierte, die noch wenig Erfahrung auf dem Gebiet haben, können die Grundlagen kennen lernen und an aktuellen Projekten erleben, was machbar ist. Ende April finden die Smart Manufacturing Days statt, eine grosse Hausmesse mit den neusten Technologien, sofern es die Covid-Situation sowie die Vorgaben des BAG erlauben.
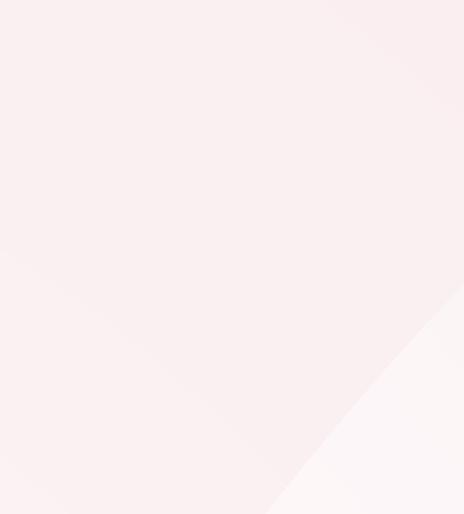

Handling von Pipettenspitzen.
Einfache Bedienung
Im Spritzguss müssen grosse Serien gleicher Teile verarbeitet werden. Eine Maschine liefert vielleicht 16 Kavitäten im 12-Sekunden-Takt. «Das ist eine hohe Kadenz, die die Anlage beherrschen muss. Gerade bei nachgelagerten Prozessen ist es aber oft so, dass der Kunde alle paar Tage auf ein anderes Produkt umrüstet. Da kommt wieder die Flexibilität der Industrieroboter zum Zug», sagt Koch. Die Umrüstung funktioniert heute oft menügeführt über ein Front-End. Der Bediener kann über die Oberfläche die Umrüstung vornehmen und wird von der Software dabei unterstützt. In der Entwicklung solcher Front-Ends stecken viele Stunden Entwicklungsaufwand, die sich aber lohnen. Koch: «Das ist eine unserer Stärken, dass wir komplexe Anlagen einfach bedienbar machen.»
Enge Kundenbeziehung
Bei der Anlagensteuerung gibt es heute zwei Trends. Entweder sie läuft über eine SPS, dann meistens von Siemens, oder sie läuft proprietär, auf der Roboter-Software selbst. Koch erklärt: «Die Hälfte unserer Anlagen besitzen keine SPS mehr. Ein grosser Vorteil dabei ist die Langlebigkeit.» Robotec arbeitet eng mit den Roboterlieferanten zusammen und bietet eine Ersatzteilverfügbarkeit von bis zu 20 Jahren. Im Sondermaschinenbau sind langfristige Beziehungen wichtig. «Wir haben eine intensive Kundenbindung auch wegen dem Service», sagt Koch. Bis eine Anlage sauber läuft braucht es ein gewisses Feintuning vor Ort. Danach betreut das Aftersales Team den Kunden weiter und oft folgen weitere Projekte in denen z.B. die Anlage auf neue Teile angepasst wird. Koch: «Durch die Flexibilität der Robotik können wir für neue Teile passende Greifer konstruieren, die Anlage umprogrammieren und erweitern.» Koch ergänzt: «Das ist ein grosses Plus der Robotec. Wir kennen unsere Maschinen genau. Die ersten, die wir gebaut haben werden bald 20 Jahre alt und laufen heute noch.»
Automatisierung als Chance
Automatisierung ist eines der grossen Trendthemen. Das liegt nicht zuletzt daran, dass produzierende Unternehmen an Schweizer Standorten einen hohen Automationsgrad anstreben müssen, um im internationalen Umfeld mithalten zu können. Koch: «In der Schweiz gibt es viele Beispiele, die zeigen, wenn man weitgehend automatisiert, kann man im internationalen Wettbewerb mithalten. Damit ist der Standort Schweiz gut gewählt, weil er ein stabiles Umfeld bietet.» Diese Entwicklung schlägt auch auf die Projekte bei Robotec durch. Koch: «Die Anlagenkomplexität nimmt zu, speziell was die Software betrifft. Das liegt an der immer dichteren Vernetzung der verschiedenen Maschinen.» Dabei müssen Benutzerschnittstellen einfach und verständlich bleiben. Ausserdem legen Kunden immer mehr Wert auf die Dokumentation der Anlage und gerade was Projekte in der Medizintechnik betrifft, müssen viele Regularien eingehalten werden. «Konnten wir früher noch Projekte mit 200 Stunden durchführen, so starten die Zeitbudgets heute erst bei etwa 400 bis 500 Stunden», sagt Koch. Robotec unterstützt seine Kunden, damit sie in der Schweiz hoch automatisiert produzieren können. Nick Koch: «Man darf nicht vergessen, die Automation kommt erst im Nachhinein, wenn der Prozess der Produktion klar ist. Es ist nicht so, dass die Robotik die Schweizer Wirtschaft rettet. Es ist umgekehrt: wenn wir keine produzierenden Unternehmen haben, können wir keine Robotik anbieten. Deshalb ist es wichtig, dass die Produktion in der Schweiz bleibt.»
Kontakt Robotec Solutions AG Birren 16 CH-5703 Seon +41 62 775 90 00 www.robotec-ag.com