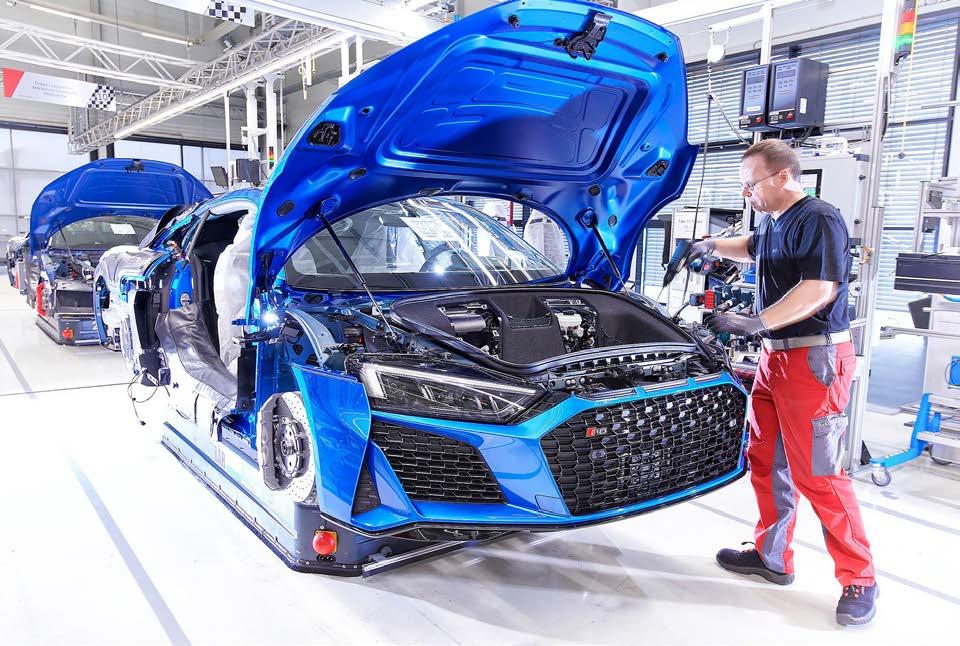
8 minute read
AUTOMATION
Automatisierung in der Automobilbranche
Abschied vom Fliessband
Advertisement
Vom 8. bis 11. Dezember steigt in München die Weltleitmesse für intelligente Automation und Robotik automatica. Ein inhaltlicher Schwerpunkt der Veranstaltung liegt auf der weiteren Flexibilisierung der Automobilproduktion.
Die Automobilindustrie befindet sich im Strukturwandel. Die Diskussion um die Antriebstechnologie der Zukunft ist in vollem Gange. Einige Hersteller setzen auf Elektromobilität, andere schätzen sie eher als Übergangstechnologie ein. Zugleich scheinen die «Verbrenner» zumindest im Moment langlebiger als zwischenzeitlich angenommen. Darüber hinaus sind neue Generationen von Dieselmotoren mit hochwirksamer Filtertechnologie deutlich emissionsärmer als ihre Vorgängermodelle. Weitere zukünftige Antriebsalternativen sind synthetische Treibstoffe, Wasserstoff und Brennstoffzellen. Wie wirkt sich dieses Szenario auf die hochautomatisierte Automobilproduktion aus? Was bedeutet es für die Anbieter von Robotik und Automatisierungstechnik? Kurz: Wie sieht die Automobilproduktion der Zukunft aus? Die Vielfalt der Antriebstechnologien und die daraus resultierende Ungewissheit machen es den Automobilherstellern schwer, diese Fragen zu beantworten. Eins ist aber sicher: Ohne hoch flexible, digital vernetzte Automatisierungslösungen sind die Herausforderungen der Zukunft nicht zu meistern. Gefragt sind nachhaltige, Industrie 4.0-kompatible Lösungen, die Fahrzeugproduzenten, Tier 1-Zulieferer und Systemzulieferer in aller Welt bei der Umsetzung modernster Fertigungsstrukturen unterstützen.
Verzicht auf stationäre Fördertechnik Die automatica als Leitmesse der Automatisierungstechnik zeigt hierfür geeignete Technologien. Vielen dieser Lösungen ist der Verzicht auf die stationäre Fördertechnik gemeinsam. Das bedeutet einen echten Paradigmenwechsel: Mehr als einhundert Jahre dominierte das Fliessband die Automobilfertigung. Heute suchen Auto
Audi fertigt den Supersportwagen R8 in Neckarsulm auf fahrerlosen Transportsystemen.
bauer und Fabrikplaner nach Alternativen für diese zwar hoch effiziente, aber auch unflexible Technik. Erste Schritte wurden bereits vor Jahren im Karosserierohbau vollzogen. Die dort eingesetzten Roboter schweissen, nieten und kleben nicht nur. Sie halten und transportieren auch die Rohkarossen, während ihre maschinellen «Kollegen» sie bearbeiten. Einer der positiven Nebeneffekte: Bei Modellwechseln muss man nicht die kompletten Produktionslinien verschrotten, sondern nur die Roboter neu programmieren.
Neue Ära nicht nur in der Automobilproduktion Dieses Prinzip lässt sich nun auch auf die Endmontage übertragen. Das zeigt Porsche mit der neuen Taycan-Fertigung in Zuffenhausen. Hier wurde, so Albrecht Reimold, Produktionsvorstand des Unternehmens, das Fliessband praktisch abgeschafft. Die Fahrzeuge bewegen sich stattdessen auf Fahrerlosen Transportsystemen (FTS) durch die Fertigung und werden so Schritt für Schritt komplettiert. Das steigert die Flexibilität erheblich. Das Tempo der FTS ist ebenso variabel wie ihre Verweildauer an den Montagestationen, theoretisch müssen die Fahrzeuge auch nicht alle denselben Weg durch die Fertigung nehmen. Zudem lassen sich mehrere Modelle oder Derivate problemlos auf ein und derselben Linie fertigen.
Das ganze Spektrum der flexiblen Automation Das zeigt: Flexibilität ist Trumpf – und das gilt nicht nur für die Automobilproduktion. In der Smart Factory der nahen Zukunft ermöglichen flexible Transportsysteme eine einfachere Anpassung der Produk tions- und Logistikprozesse. In der konsequentesten Umsetzungsform steuern die Produkte, die gefertigt werden, auf autonomen Transportsystemen selbsttätig die
Das Prinzip der flexiblen Automobilfertigung ohne Fliessband lässt sich auch auf andere Industriebereiche übertragen. Bild: Porsche Consulting
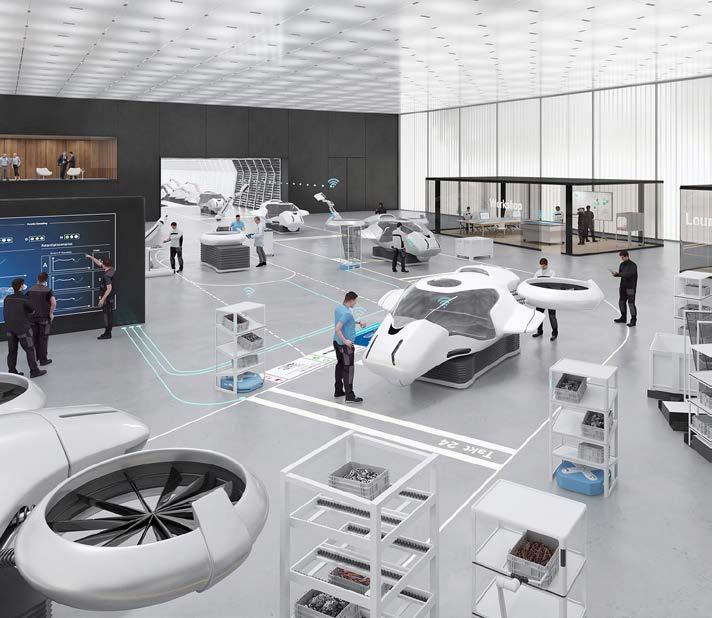
Montagestationen an, die gerade frei sind. Algorithmen und Künstliche Intelligenz unterstützen die Planung und machen die Entscheidungsfindung effizienter. Auf der automatica stellen zahlreiche Anbieter vor, wie sich die smarte, digital vernetzte Produktion realisieren lässt. Neben Robotern spielen dabei auch industrielle Bildverarbeitungssysteme, Greifer und Positioniereinheiten, Sensoren sowie elektronische Steuerrungen eine zentrale Rolle. Die Messe bietet Gelegenheit, all diese Produktgruppen gezielt unter die Lupe zu nehmen.
Cobots rücken den Werker in den Mittelpunkt Darüber hinaus wird auf der automatica eine weitere Entwicklung sichtbar: Moderne Automatisierungskonzepte verzichten nicht auf den Werker, sondern rücken ihn in den Mittelpunkt. Exoskelette und Cobots werden die Beschäftigten körperlich entlasten. Der grösste Entwicklungssprung ist im Bereich der Cobots zu erwarten. Längst sind die kollaborativen Roboter in der Praxis angekommen wie beispielsweise bei Opel in Eisenach: Hier schraubt ein Cobot des dänischen Herstellers Universal Robots Klimakompressoren an Motorblöcke an. Unmittelbar neben den Mitarbeitern, ohne trennenden Schutzzaun, zieht der Roboter alle zwei Minuten drei Schrauben auf exakt 22 Newtonmeter an und seine menschlichen Kollegen übernehmen weiterhin die weniger belastenden vor- und nachgelagerten Arbeiten.
Kontakt Messe München GmbH CH: BTO Solutions Schürch AG Pflanzschulstrasse 3, CH-8400 Winterthur info@bto-solutions.ch, www.bto-solutions.ch www.automatica-munich.com
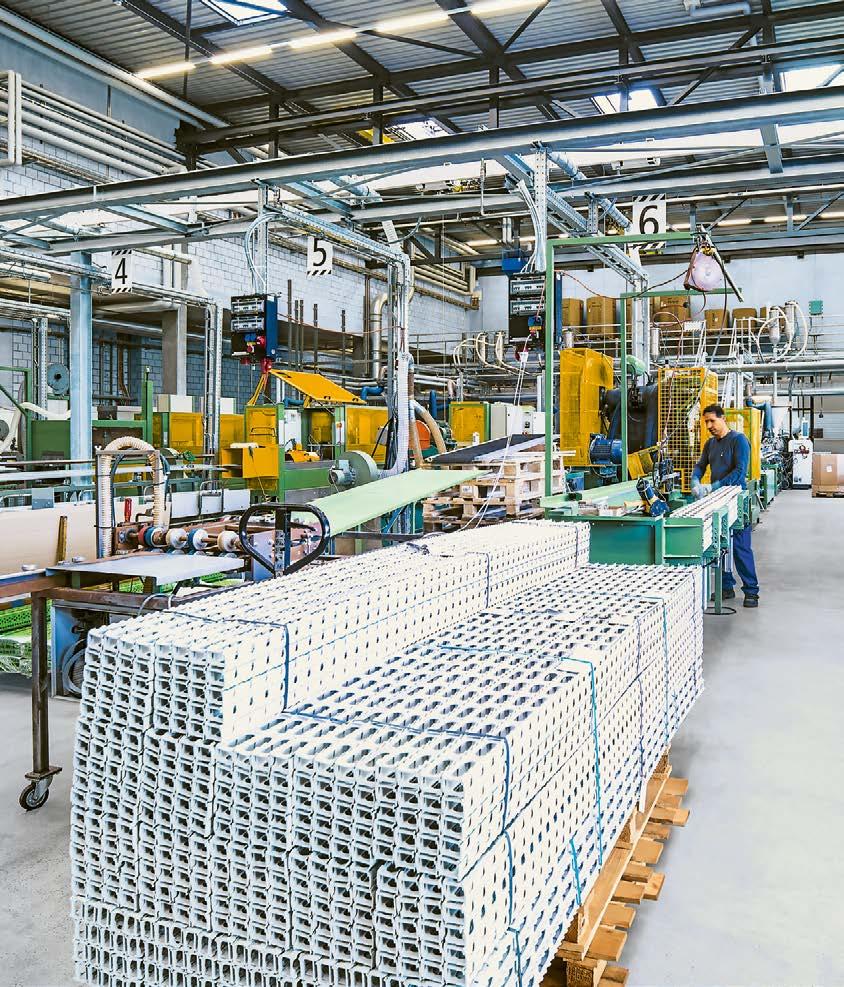
Kunststoffproduktion aus einem Guss Ganzheitliche Lösungen − engineered by IE Der Spezialist für Industriebauten
Eine effiziente Kunststoffproduktion bedingt, dass die Fertigungsprozesse, die Haustechnik und die Architektur von Anfang an aufeinander abgestimmt werden. Das Gebäude muss entsprechend konzipiert sein. Darauf sind unsere erfahrenen Architekten und Ingenieure spezialisiert. Sie achten darauf, dass die Material- und die Personenflüsse kreuzungsfrei verlaufen, der Lagerbereich direkt an die Produktion angebunden ist und das Gebäude später flexibel erweitert werden kann.
Die Beachtung solcher Kriterien entscheidet letztlich über Ihre Wettbewerbsfähigkeit in der hart umkämpften Kunststoffbranche.
Wie immer Ihre Ausgangslage ist − wir haben die ganzheitliche, massgeschneiderte und praxiserprobte Lösung für Sie.
IN IHRER BRANCHE ZU HAUSE
MITARBEITER ALS UNTERNEHMER
ALLE EXPERTEN UNTER EINEM DACH
SICHERHEIT DURCH GARANTIEN
IE Plast Zürich
+41 44 389 86 00 zuerich@ie-group.com www.ie-group.com
Einfache und sichere Wartung von Systemsteuerungen
Digitaler Service aus der Ferne
Weitverzweigte Materialtransport-, Aufbereitungs- und Dosieranlagen verlangen im Fall einer Störung den schnellen Einsatz spezialisierter Mitarbeiter. Um Betriebsunterbrechungen so kurz wie möglich zu halten, wird der Einsatz von Fernwartung immer wichtiger.
Bei Wartungsaufgaben aus der Ferne kann die Remote Maintenance Box von motan äusserst nützlich sein, um ein System unabhängig vom Standort am Laufen zu halten. Die Box enthält einen leistungsfähigen Industrie-PC mit umfangreichen Softwarepaketen für Fernzugriff, Debugging-, Analyse- und Logging-Werkzeugen für Steuerungs- und Netzwerkkomponenten. Für die Konfiguration und Administration sind darüber hinaus alle erforderlichen Werkzeuge standardmässig mit im Paket. Eingebaut in einen Kompaktwandschrank, erlaubt die Remote Maintenance Box den Fernzugriff über Internet oder ein firmeninternes Intranet auf alle ControlNet Steuerungen von motan. Die Bediensprache wird von den überwachten Modulen übernommen, so dass auch der weltweite Einsatz problemlos möglich ist.
Schnelle Analyse
Statt sofort eigenes Personal oder den Service des Anlagenherstellers zu aktivieren, kann die Remote Maintenance Box vorab Klärung bringen: So lassen sich auf jedem PC schnelle Analysen durchführen, Fehler auch in umfangreichen Netzen eingrenzen und die Ursachen benennen. Damit sind schnelle und zielgerichtete Massnahmen möglich. Reaktionszeiten werden stark verkürzt und unnötige Service-Einsätze vor Ort vermieden. Sicherheit statt Schwierigkeit ist hier das Motto. motan setzt zudem bei der Einbindung der Remote Maintenance Box auf die frei am Markt verfügbare Fernwartungs-Software «TeamViewer». Das ermöglicht jedem Servicetechniker den digitalen Zugriff von Zuhause oder von einem anderen Stand ort auf die Anlage, um mögliche Fehler zu beheben.
Remote Maintenance – digitaler Service aus der Ferne

Einfach und trotzdem sicher
Die in vielen anderen Systemen verlangte komplexe Freischaltung und Administration von Firewall-Regeln ist nicht erforderlich. Aber trotzdem hat der Anwender die volle Kontrolle: Die Anschlüsse für das in terne und externe Ethernet sind getrennt, die Vergabe von Zugangsberechtigungen liegt komplett beim Anwender. Nicht zuletzt lässt sich die Remote Maintenance Box ganz einfach per Schalter komplett aus- und wieder einschalten.

Kontakt Motan-Colortronic AG Roggenstrasse 3 CH-4665 Oftringen +41 62 889 29 29 info@motan-colortronic.ch www.motan.com
Teilehandling, Spritzgiessen und Prüfen innert Sekunden
Arbeitszelle amortisiert sich deutlich früher
Um über zehn Prozent hat MartinMechanic die Leistung einer Automationszelle für das Teilehandling zum Umspritzen von Stahlbuchsen und zur nahtlosen Überprüfung dieses Arbeitsvorgangs gesteigert. Ausserdem können auf der Anlage, die parallel zwei Spritzgiessmaschinen bedient, bei einer Zykluszeit von 4,5 Sekunden nun acht statt bislang sechs Varianten ohne Zurüsten produziert werden.
Eigentlich wollte der Kunde aus der Kunststoffbranche nur eine weitere Arbeitszelle gleichen Typs bestellen, als er bei dem Sondermaschinenbauer in Nagold vorstellig wurde. Dabei entdeckte man gemeinsam allerdings noch mehr Potenzial für das Folgemodell. «Das ist schon der Anspruch an uns selbst», sagt Geschäftsführer Claus Martin, «ältere Konzepte bei einer Wiederauflage zu optimieren.» So hat der Kunde jetzt eine Arbeitszelle, deren Anschaffungspreis zwar gleichgeblieben ist. Doch amortisiert sich die Investition unter dem Strich jetzt deutlich früher. Die Maschine sorgt nicht nur für das Teilehandlung zur Ummantelung der Stahlbuchsen mit glasfaserverstärktem Kunststoff in zwei Spritzgiessmaschinen, sondern prüft im Nachgang auch gleich das Ergebnis dieser Arbeit. Dazu legt der Werker die Rohteile an zwei unterschiedlichen Beladeplätzen in Magazinen ab. An jedem Beladeplatz gibt es zwei Schubladen, die im Wechsel mit jeweils 40 Rohteilen bestückt werden. Dabei werden vier Stapel mit je zehn Teilen gebildet. Auf diese Weise sind immer 160 Teile im Umlauf. Über einen Anforderungstaster kann der Werker die Schubladen öffnen und wieder schliessen, sodass der laufende Prozess hierfür beim Nachladen nicht unterbro chen werden muss.
Vorwärmstation für Rohteile
Die vollen Schubladen werden pro Spritzgiessmaschine jeweils von einem ScaraRoboter vom Typ Omron/Yamaha XG600 laufend entleert, in dem er zwei Rohteile mit seinem bis zu 400 Millimeter ausfah renden Z-Hub in einen Pendeltisch einlegt. Dieser dreht sich danach um 180 Grad, um die Teile einem Multilift von Arburg zur
Bild: MartinMechanic

Teilehandling für zwei Spritzgiessmaschinen und zwei Prüfstationen: die MAS242015-11 von MartinMechanic hat eine Zykluszeit von 4,5 Sekunden.
Verfügung zu stellen. Von diesem DreiAchs-Handling, das über einen schwenkbaren Greifer verfügt, werden die beiden Teile aufgenommen und in eine Vorwärmstation mit 16 Abladeplätzen gesteckt, die an den Heizkreislauf der Spritzgiessmaschine angeschlossen ist. Das Multilift-System holt immer zwei auf 65 Grad vorgewärmte Rohteile wieder ab, um sie dann auf der anderen Werkzeugseite gegen die fertig ummantelten Teile aus der Spritzgiessmaschine zu tauschen. Dazu werden sie jeweils in die frei gewor denen Kavitäten des Spritzgiesswerkzeugs eingelegt. Die fertig ummantelten Teile legt der Multilift wieder auf dem Pendeltisch ab.
Acht Stationen am Rundschalttisch Der Tisch ist nicht nur die Schnittstelle zur jeweiligen Spritzgiessmaschine, sondern auch zum Rundschalttisch, den der ScaraRoboter bedient. Auf ihm durchlaufen die fertig ummantelten Teile acht Stationen. Die erste ist eine Wendestation, in die die Bauteilvarianten eingelegt werden, die von oben beschriftet werden müssen. Prüfspitzen messen an der zweiten Station nach dem Fixieren horizontal die Stärke der Kunststoff-Ummantelung, um sie mit der geforderten Soll-Stärke abzugleichen. An der dritten Station senkt sich nach dem Fixieren ein pneumatischer Messdorn auf das Bauteil, um an Hand einer Feinbohrung den Innendurchmesser des Bauteils zu bestimmen. Anschliessend werden die Teile an Station vier mit dem Faserlaser beschriftet. Der DataMatrix-Code enthält das Produktionsdatum, die Serien- und die Chargennummer. An dieser Stelle ist die Anlage mit einer Absaugeinheit mit grossem Filter ausgestattet, um Verunreinigungen und Schmauch zu entfernen. Eine Station weiter wirft ein Scanner nochmals einen prüfenden Blick auf die Beschriftung. Was nicht in Ordnung ist, wandert an Sta tion sechs mit Hilfe des Scara-Roboters auf eine Ablage und von dort in einen Kleinladungsträger. Die Teile, die der Prüfung standhalten, werden auf einem Förderband abtransportiert. Die beiden restlichen Stationen sind wiederum auf das Einlegen neuer, zu umspritzender Teile ausgerichtet.
Kontakt MartinMechanic Friedrich Martin GmbH & Co KG Heinrich-Hertz-Strasse 2 D-72202 Nagold +49 7452-84660 info@MartinMechanic.com www.MartinMechanic.com