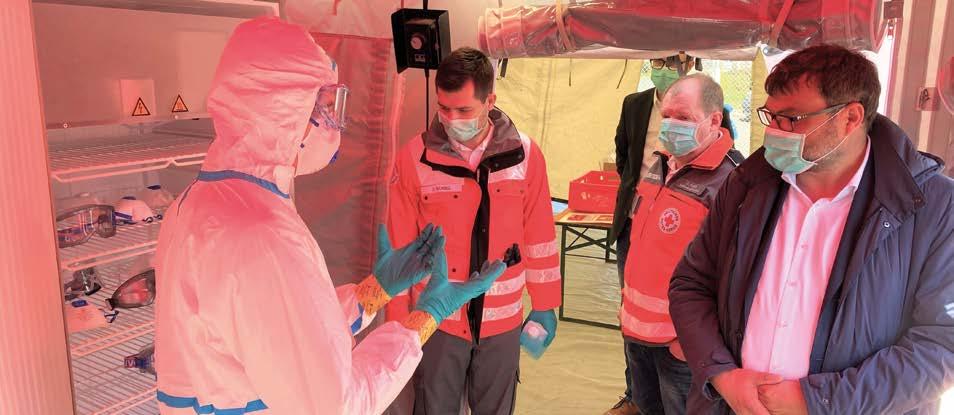
9 minute read
OBERFLÄCHEN
Einweg-Schutzkleidung durch Plasma desinfizieren
Plasma als Chance in der Corona-Krise
Advertisement
Plasmatreat will grösser in das Desinfektionsgeschäft einsteigen und damit in der Corona-Krise Lösungen bei der Desinfektion von Schutzkleidung vorhalten.
Ein Prototyp eines Reinigungsautomaten für Schutzbekleidung wird derzeit bereits vom Bayrischen Roten Kreuz eingesetzt, in der technischen Uniklinik München befindet sich ein weiterer Automat in der klinischen Testphase und auch die amerikanische Yale Universität hat Interesse bekundet. Die Idee: Einweg-Schutzkleidung durch ein sicheres und einfaches Verfahren zu desinfizieren. Der eigentliche Wegwerfartikel kann dann ein weiteres Mal benutzt werden. In der derzeitigen Pandemielage werden Schutzmasken und Schutzanzüge immer knapper – durch das Desinfektionsverfahren mit Plasma können schnell und mit wenig Aufwand bereits benutzte Masken desinfiziert und noch einmal benutzt werden.
Keime lassen sich mit Plasma abtöten Plasmatreat ist führend in der atmosphärischen Plasmaforschung und -anwendung. Die Plasmatechnologie ist vielfach einsetzbar. Spezialisiert hat sich das Unternehmen bisher auf die Oberflächenvorbehandlung und liefert Lösungen für die Luftfahrt, die Elektronik, die Verpackungstechnik, den Automobilbau oder die Textilfertigung. Plasma entsteht, wenn Luft und Hochspannung zusammenkommen – z.B. wenn es beim Gewitter blitzt. Das Licht des Blitzes besteht aus reinem Plasma, einer gasförmigen Materie. Ein Lichtblick in der derzeitigen CoronaKrise, denn Plasma zeichnet sich u.a. dadurch aus, dass es mit Hilfe eines speziellen Verfahrens hervorragend desinfiziert. Selbst besonders stabile multiresistente Keime lassen sich mit Plasma abtöten – so die Ergebnisse jahrelanger Forschung im mikrobiologischen Labor im PlasmatreatTechnologiezentrum.
Einwegartikel wie Schutzkleidung und -masken können nach der Behandlung mit Plasma wiederverwendet werden. Bild: Michael Will/BRK
Plasma im Einsatz gegen Corona
«Wenn wir Plasma jetzt erfolgreich in der Corona-Krise anwenden können, wird unsere Forschung enorm vorangetrieben und das noch ausstehende Zulassungsverfahren könnte beschleunigt werden. Denn noch befinden wir uns in einem Graubereich. Wir wissen, dass unser Verfahren wirkt und haben auch ausreichend Beweise – zugelassen ist das Verfahren aber noch nicht. Dieser Prozess dauert unglaublich lang», erklärt Geschäftsführer Christian Buske. Das erste Plasma-Desinfektionsverfahren wird bereits in Bayern angewandt. Plasmatreat arbeitet seit Jahren eng mit dem Bay rischen Roten Kreuz zusammen. Das BRK ist katastrophenerfahren und hat die EbolaKrise zum Anlass genommen, neue Wege der Desinfektion zu gehen. Herkömmliche Desinfektionsmöglichkeiten sind im Kampf gegen Viren wie Ebola oder Corona sehr begrenzt (Transportprobleme, Nachschubschwierigkeiten, begrenzte Haltbarkeit, nicht überall anwendbar, häufig sind es chemische Keulen, die textilschädigend wirken). Der wenig aufwändige und darüber hinaus noch umweltfreundliche Plasmaeinsatz kommt da gerade recht. Derzeit sind 3 Plasma-Infektionsautomaten aufgebaut und einsatzbereit – weitere könnten sofort in Serie gehen. Dass das nötig ist, spüren Buske und seine Mitarbeitenden nahezu täglich: «Wir bekommen viele Anrufe und Anfragen mit Hilferufen von Ärzten und Kliniken, aber auch Privatpersonen und Unternehmern. Schutzmasken werden knapp – da ist Desinfektion eine Lösung.» Längst arbeitet Plasmatreat an weiteren Lösungen im Bereich der Desinfektion. Leitungswasser wird mit Plasma bereichert und dadurch zum einfachen aber genialen Desinfektionsmittel. Auch hier laufen im Plasmatreat-Technologiezentrum seit Jahren die Versuchsreihen. Für Buske und sein Team bestätigt sich derzeit die über dem Unternehmen schwebende Vision: «Plasma hilft uns, Innovation mit Nachhaltigkeit zu verbinden und die Welt ein bisschen sicherer zu machen.»
Kontakt Plasmatreat GmbH Queller Strasse 76–80 D-33803 Steinhagen +49 5204 99 60 0 www.plasmatreat.de
Sol-Gel-Beschichtung erhöht die Produktivität von Werkzeugeinsätzen
Das Entformungsverhalten optimieren
Um Formteile leichter aus Spritzgiesswerkzeugen entfernen zu können, haben Wissenschaftler von Innovent eine Beschichtung für Werkzeugeinsätze mittels Sol-Gel-Technologie realisiert, welche sich sogar bei bereits eingebauten Teilen anwenden lässt.
Kaum ein Beschichtungsverfahren ist so vielseitig wie die Sol-Gel-Technik. Diese eignet sich zur Schichtapplikation auf verschiedenen Substratmaterialien (z. B. Glas und Metall, aber auch auf temperaturempfindlichen Werkstoffen wie Polymeren oder Textilien). Neben den nichtmetalli schen, anorganischen oder hybridpolymeren Beschichtungen lassen sich damit auch Pulver, Partikel und Fasern herstellen. Durch die Vielfalt an möglichen Precursoren, Zusätzen (z. B. Gleitadditive und Nanopartikel) sowie über eine definierte Einstellung der Reaktionsbedingungen ist eine breite Palette an Schichteigenschaften zugänglich. Über einen Auftrag der Sole mittels Sprühdüse können somit anwendungsnah Beschichtungen auf Werkzeugeinsätze aufgebracht werden, ohne diese aus deren Halterung ausbauen zu müssen. Eine Integration des Beschichtungsvorganges in den Reinigungszyklus der Werkzeuge (wobei diese ohnehin ausgebaut werden) ist allerdings ebenso möglich. Anwendungsnahe Ermittlung der Entformungskraft Für die Beschichtung von Werkzeugen und deren Komponenten stehen mehrere stabile Sole zur Verfügung, aus denen haftfeste sowie trennaktive Schichten generiert werden können. Diese lassen sich im Bedarfsfall über ein eigens ausgearbeitetes Regime auch wieder von diesen entfernen. Mittels angepasster Schichtanalytik kann eine Überwachung des Zustandes der Beschichtung ebenfalls am eingebauten Werkzeug erfolgen. Um eine Abformung unter Realbedingungen untersuchen zu können, wurde ein spezielles Testwerkzeug genutzt. Dieses verfügt über einen Kraftsensor, der in das Auswerferpaket integriert ist und eine Erfassung der benötigten Entformungskraft erlaubt. Zudem wurden wechselbare Einsätze für das Werkzeug vorgesehen, welche flexibel mit verschiedenen anti-adhäsiven Beschichtungen versehen werden können. Effektive Sol-Gel-Beschichtungen Mit den beschichteten Werkzeugeinsätzen liess sich die benötigte Entformungskraft generell deutlich reduzieren (durchschnittlich um 40 %). Dieser Effekt fiel jedoch abhängig von der eingesetzten Form masse sowie der Rauheit der Substratoberfläche sehr unterschiedlich aus. Für Formteile aus Polyamid ergab sich dabei das höchste Potenzial. Die Entformungskraft konnte auf vergleichsweise glatten Einsätzen (Rz = 3,5 µm) um bis zu 60 % mit dieser Formmasse vermindert werden. Durch eine Reduzierung der Entformungskraft sowie daraus resultierend der Zykluszeit und des Energiebedarfs ergaben sich ebenso signifikante wirtschaftliche Effekte. Dies beinhaltet sowohl eine Steigerung der Produktivität (höherer Durchsatz) und der Werkzeugstandzeit als auch eine Senkung der Ausschussrate und der Energiekosten. Kontakt Innovent e.V. Technologienentwicklung Jena Prüssingstrasse 27B, D-07745 Jena +49 3641 2825-10 bg@innovent-jena.de www.innovent-jena.de n Aufnahme eines unbeschichteten Einsatzes (links) sowie Wärmebildaufnahmen eines Werkzeugeinsatzes mit Beschichtung, nachdem Abformversuche damit durchgeführt wurden und nach Entfernung der Schicht (rechts). Bild: Innovent 0_IR_Ins_1-3q_183x85_fbg_Rohstoffland.pdf 1 11.10.12 11:06 0_IR_Ins_1-3q_183x85_fbg_Rohstoffland.pdf 1 11.10.12 11:06 0_IR_Ins_1-3q_183x85_fbg_Rohstoffland.pdf 1 11.10.12 11:06
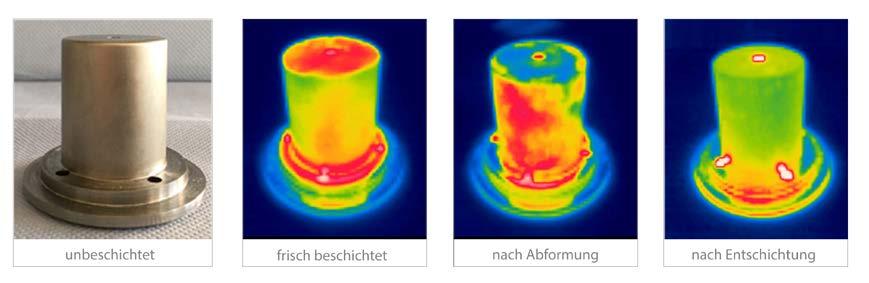
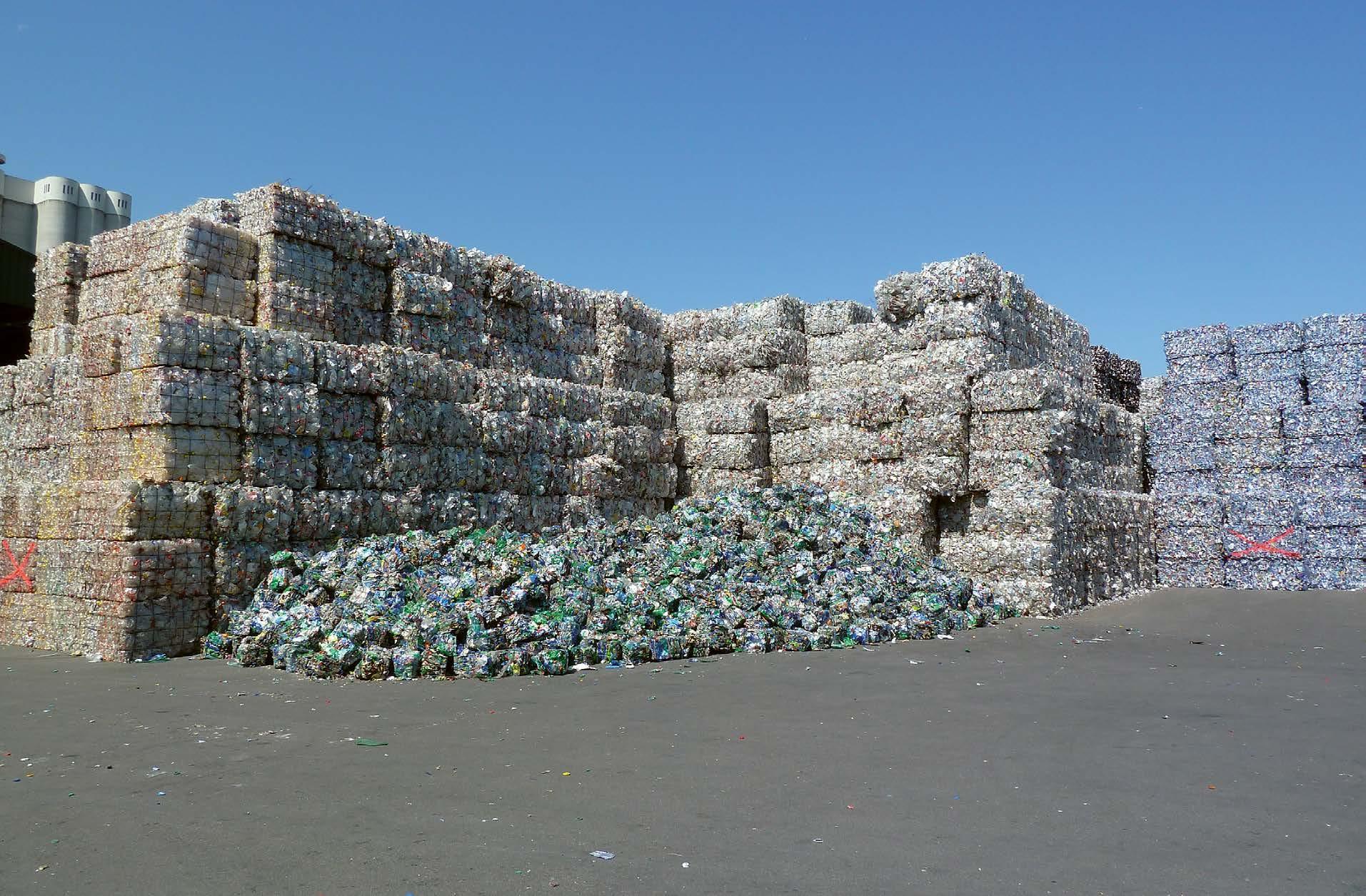
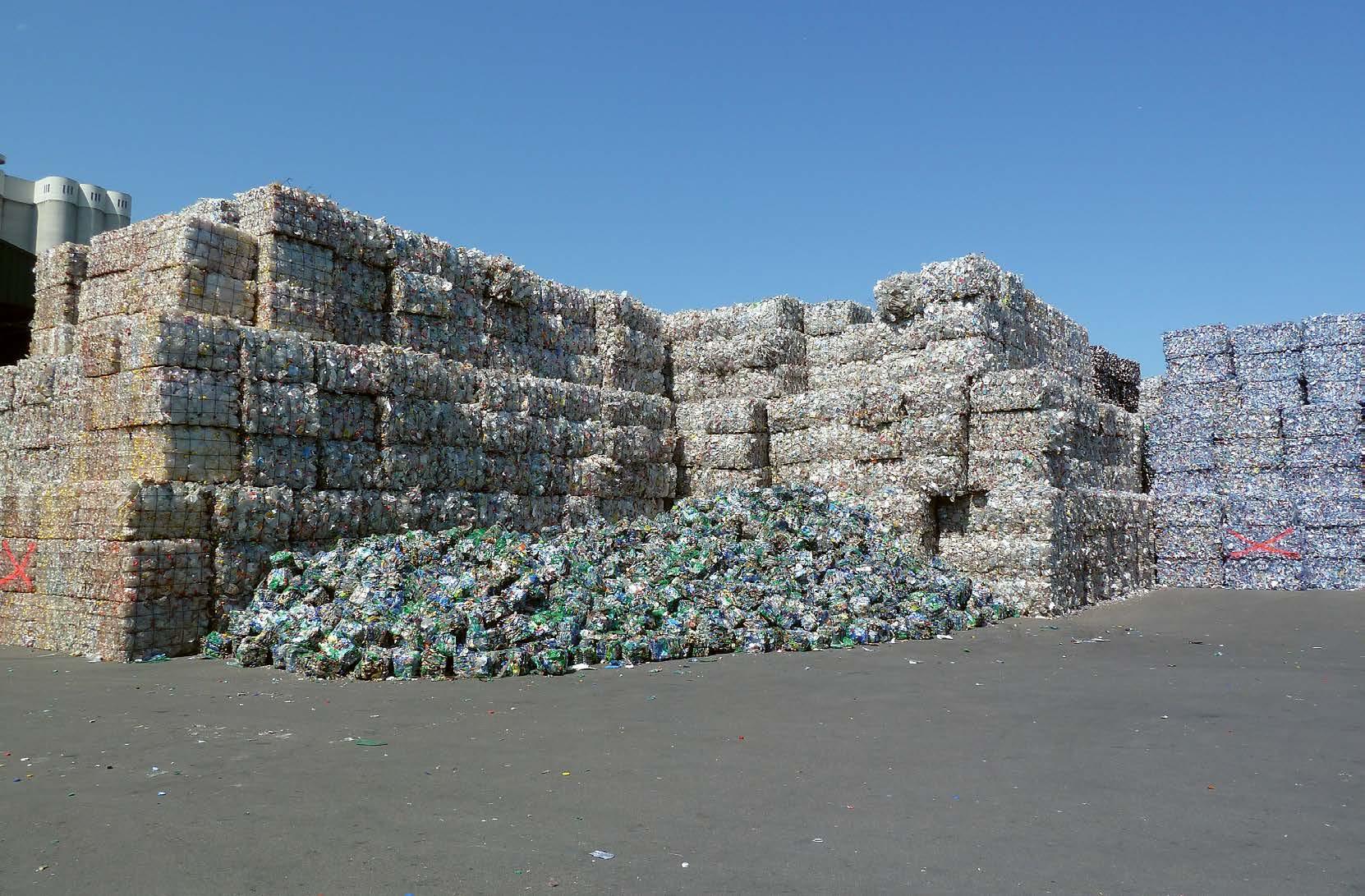
Rohstoffland Schweiz InnoRecycling fördert Ressourcen
Vom Nischenprodukt zur etablierten Beschichtungstechnologie
Nachhaltige Beschichtung für PET-Flaschen
Mit der Plasmax-Beschichtungstechnologie und der daraus resultierenden Verpackungslösung FreshSafe-PET bietet KHS der Getränke- und Nahrungsmittelindustrie eine umweltfreundliche und nachhaltige Lösung mit einem Produktschutz.
Wenn Bernd-Thomas Kempa, seit 2012 verantwortlich für Vertrieb & Service von Plasmax und heute Head of Global Account Management Plasmax Barrier Technology, und Joachim Konrad, seit 2014 verantwortlich für die Technik als Director Plasmax Barrier Technology und heute Leiter Produktdivision Grossmaschine, diskutieren, fallen immer wieder die Begriffe Beharrlichkeit, Überzeugung und Vertrauen. Zusammen mit ihrem Team sind die beiden sozusagen die Wegbereiter für die Transformation der KHS-Plasmax-Beschichtungstechnologie von einer Nischenlösung hin zur markterprobten und bewährten Verpackungslösung FreshSafe-PET für die Getränke- und Nahrungsmittelindustrie.
Veränderte Verpackungspräferenzen Begonnen hat die Geschichte von FreshSafe-PET, auch bekannt unter dem Namen Plasmax, genau genommen bereits Anfang der 2000er-Jahre. Damals gingen die Schott AG und die SIG Corpoplast wegen sich verändernder Verpackungspräferenzen der Industrie ein Joint Venture zur Plasmabeschichtung von PET-Flaschen ein. Damit bündelten sie die Expertise eines internationalen Herstellers von Glas und Glaskeramik mit dem Know-how eines Verpackungsherstellers und Maschinen bauers für die Kunststoffverarbeitung. Das Portfolio der Schott AG beinhaltete auch eine Beschichtung aus Glas, die ergänzend an der Innenseite von Behältern aus Glas aufgetragen wurde. «Damit wurden hoch sensible pharmazeutische Produkte vor der Migration von Stoffen geschützt», erklärt Kempa. Im Rahmen des Joint Ventures wurde der Prototyp der ersten Maschinengeneration
Eckes-Granini ging 2006 als erstes europäisches Unternehmen der Fruchtsaftbranche mit der FreshSafe-PET-Technologie in den Markt. Bilder: KHS Gruppe
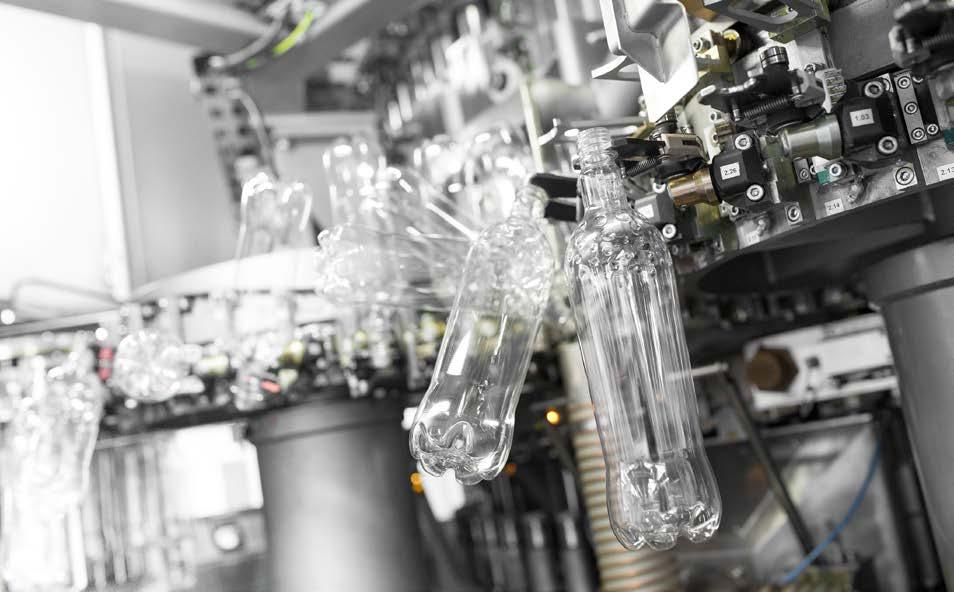
der Plasmax entwickelt und 2002 schliesslich die erste Plasmax-Maschine mit einem Ausstoss von 10000 Flaschen pro Stunde in der Schweiz getestet. Zudem erhielt Plasmax die lebensmittelrechtlichen Zulassungen in Europa, den USA und Japan. Zwei Plasmax-Maschinen 12D wurden schliesslich für den Schutz hochwertiger, sensibler Produkte nach Japan ausgeliefert. 2006 ging Eckes-Granini als erstes europäisches Unternehmen der Frucht saftbranche mit der Technologie in den Markt. «Stetes Entwicklungsziel war und ist es, nur eine Maschine einzubinden, die den Gegebenheiten der Abfüllbetriebe und den Erwartungen der Kunden ent spricht», sagt Kempa. Insbesondere die Anlagenverfügbarkeit musste von Anfang an auf einem etablierten Branchenniveau sein. «Sieht man den heutigen Erfolg und die wachsende Nachfrage, kann man sagen: Es hat sich gelohnt. Wir haben uns im Team dabei immer eine gewisse Start-upMentalität bewahrt», ergänzt Konrad.
Nachweis für die Getränkeindustrie
«Mit der Auflösung des Joint Ventures und der Übernahme der Plasmax-Technologie durch KHS im Jahr 2008 erhielten wir eine starke Rückendeckung. Das kleine Team als Teil eines globalen Unternehmens war aber auch aufgefordert, den Nachweis zu erbringen, dass diese Technologie ebenso im Umfeld der Getränkeindustrie nachhaltig lauffähig ist», erzählt Kempa. «Ohne die Unterstützung der KHS und der Konzernmutter Salzgitter AG wäre die erfolgreiche Transformation der Technologie und damit das Erreichen eines Break-even nicht möglich gewesen. Aber auch ohne die spezielle Art der Zusammenarbeit, inklusive des enormen Zusammenhalts und Willens des gesamten Teams, wäre dieser Erfolg ebenso wenig möglich gewesen», so Kempa. Diese Unterstützung und das Vertrauen wuchs auch auf Kundenseite: Neben weiteren Maschinenverkäufen folgte 2010 der
Prototyp der grösseren zweiten Generation der Plasmax-Beschichtungsmaschine mit einer Leistung von bis zu 27500 1-Liter-Flaschen pro Stunde für Eckes. 2014 erwarb das Unternehmen für sein Werk in Fallingbostel den weltweit ersten FreshSafe Block, eine mit einer KHS-Streckblasmaschine verblockte Anlage mit einem Ausstoss von bis zu 32000 0,75-Liter-Flaschen pro Stunde. «Mit Eckes-Granini verbindet die KHS eine jahrzehntelange vertrauensvolle Zusammenarbeit, in der Lösungen zum beiderseitigen Nutzen implementiert werden konnten. So hat Eckes schon sehr früh die Chancen einer weiterentwickelten PET-Verpackung erkannt, um einen optimalen Schutz für ihre sensitiven Getränke zu ermöglichen», erzählt Kempa.
Das Angebot kontinuierlich erweitert «Eckes-Granini hat die Chancen gesehen und zeigte sich offen für neue Entwicklungen und Prozesse. Denn man darf nicht vergessen: Für alle Beteiligten war es zunächst Neuland», sagt Konrad. Von den Erkenntnissen, die aus der intensiven Zusammenarbeit gewonnen wurden, profitierten beide Seiten. Sie halfen, innovative Prozesse praxisorientiert zu optimieren und ganz neue Lösungen zu entwickeln. So hat KHS sein Plasmax-Angebot im Laufe der Jahre kontinuierlich erweitert. Der Maschinenbauer bietet mittlerweile neben der Standard-Beschichtungsmaschine und dem InnoPET FreshSafe Block auch eine Plasmax 2Q/4Q für den niedrigen Leistungsbereich und einen InnoPET FreshSafe TriBlock mit Streckblasmaschine und
Bernd-Thomas Kempa und Dr. Joachim Konrad (v.l.)
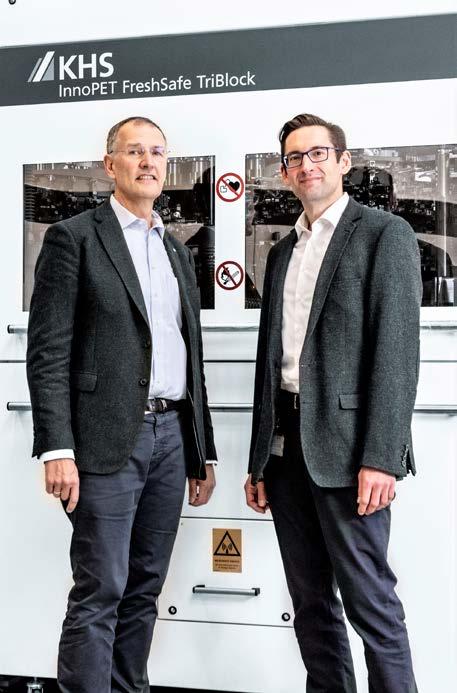
Füller-/Verschliesser-Kombination an, der eine Leistung von bis zu 48000 Flaschen pro Stunde bietet. «FreshSafe-PET kombi niert hohen Produktschutz mit einer nachhaltigen Recyclingmöglichkeit. Gleichzeitig können durch Einsparung von PET-Material die Kosten reduziert werden», erklärt Kempa. Für die Kaufentscheidung der Kunden spielen mehrere Faktoren eine Rolle. Bei FreshSafe-PET gelangen beispielsweise keine unerwünschten Stoffe von aussen in das Produkt hinein – und wertvolle Bestandteile wie Vitamine können nicht austreten. Dank der Plasmax-Barrieretechnologie bleiben sensitive und karbonisierte Getränke bis zu zehnmal länger haltbar als
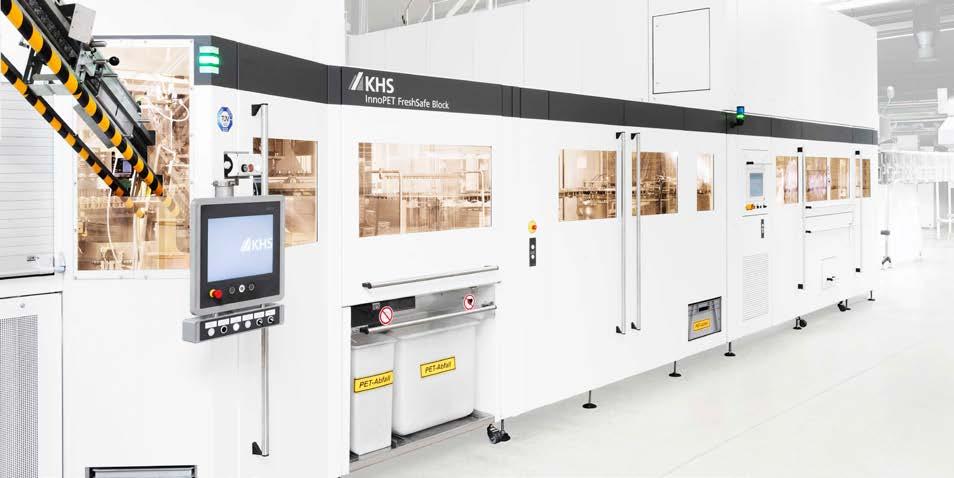
in der herkömmlichen PET-Flasche. Besonders für Abfüller, deren Produkte weite Transportwege zurücklegen, ist das ein entscheidender Faktor. Zudem schützt die hauchdünne Glasschicht sensible Produkte zuverlässig vor Frische- und Qualitätsverlust – und trägt damit auch wesentlich zum Umweltschutz bei. «Denn je zuverlässiger der Produktschutz, desto geringer die Lebensmittelverschwendung», sagt Konrad. Die Barrierelösung ist daneben auch für die Beschichtung von PET-Behältern aus Rezyklat (rPET) sowie für biologisch abbaubare Behälter geeignet. Den entscheidenden Faktor im Bereich Umweltschutz sehen Kempa und Konrad neben der Gewichtsreduktion in der vollständigen Recyclingfähigkeit von FreshSafe-PET. Die Beschichtungstechnologie ermöglicht mit ihrer Vermeidung von verschiedenen Materialkomponenten eine sortenreine Wiederaufbereitung des PETMaterials und erlaubt so eine hundertprozentige Recycelbarkeit der Behälter.
Geringerer Materialeinsatz führt zu Kosteneinsparungen Neben den Aspekten Umwelt und Produktschutz spielt auch das Thema Wirtschaftlichkeit eine bedeutende Rolle. Durch den Einsatz der KHS-Technologie sinkt einerseits das Flaschengewicht im Vergleich zu Behältern mit Additiven, was zu einem geringeren Materialeinsatz und damit zu Kosteneinsparungen führt. Abfüller können andererseits auf günstigere Standard-PET-Preforms umsteigen, wo durch die Kosten pro Flasche nochmals sinken. «All diese Faktoren haben dazu geführt, dass FreshSafe-PET sich von der ersten Vision zu einer nachgefragten und nachhaltigen Verpackungslösung entwickelt hat», so Kempa. «Und wir sind überzeugt, dass das Thema einer umweltgerechten Verpackung zukünftig mit der Verantwortung einhergehen wird, den CO ² -Abdruck weiter zu verringern.»
Kontakt KHS Corpoplast GmbH Meiendorfer Strasse 203 D-22145 Hamburg +49 40 67907 0 www.pet.khs.com