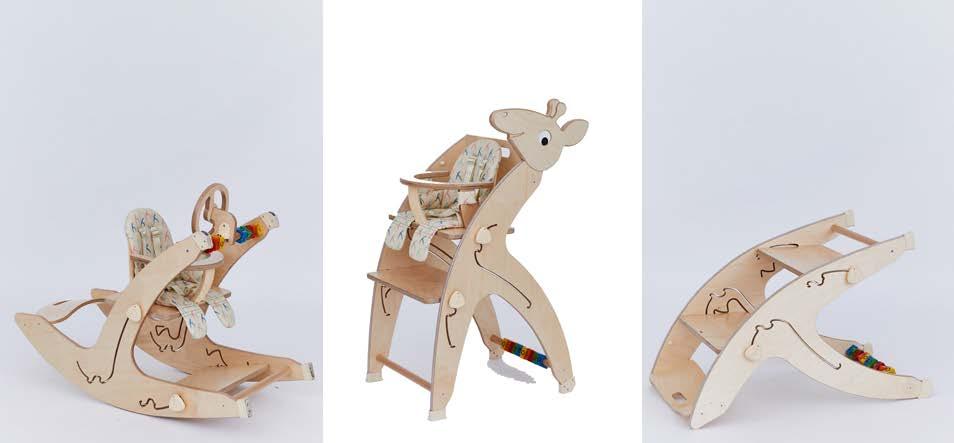
12 minute read
ADDITIVE MANUFACTURING
Start-up entwirft mit QuarttoLino ein ergonomisches Möbel
Multifunktionaler Kinderhochstuhl
Advertisement
QuarttoLino ist ein Kinderhochstuhl, kann aber auch als Schaukel, Tisch oder Treppe verwendet werden. Moderne Technologie und das Know-how von Experten des Kunststoff-Clusters in Österreich halfen bei der Umsetzung.
QuarttoLino ist ein mit moderner Technologie entwickeltes Premiumprodukt für anspruchsvolle Eltern. Das Möbelstück ist «Made in Austria»: qualitativ hochwertig, funktionell, sicher, praktisch und schön. Welche Bedeutung die Zusammenarbeit in Netzwerken wie dem Kunststoff-Cluster hat, zeigt sich bei diesem Produkt. Die Kombination Holz-Kunststoff bietet eine Reihe von Vorteilen gegenüber der Konkurrenz. Additive Tooling hat bei der Entwicklung für den Durchbruch gesorgt. Die für Klein- und Mittelserien geeignete und relativ junge Technologie ermöglichte es, die Erstserie des multifunktionellen Kinderhochstuhls mög lichst wirtschaftlich zu produzieren. Sitzen, Krabbeln, Essen, Schaukeln – über diese Konstruktion freut sich wohl jedes Kind. Der vom gleichnamigen Start-up aus Traun entwickelte QuarttoLino ist ein Kinderhochstuhl, der neben seiner Kernfunktion, ein Kleinkind ergonomisch richtig und sicher am Esstisch sitzen zu lassen, über drei weitere Funktionen verfügt. Er kann mit wenigen Handgriffen zu einer Schaukel, zu einem Kindertischchen mit Sessel, einer kleinen Treppe oder einem grossen, niedrigen Sessel umfunktioniert werden. Geburtshelfer war der Kunststoff-Cluster in Österreich.
Kreatives und innovatives Trio Das Team von QuarttoLino e.u – ein Startup Unternehmen – ist verantwortlich für
Der Kindersessel ist multifunktional, qualitativ hochwertig und auch optisch ansprechend.
Produktentwicklung und -design und übernimmt künftig den Vertrieb. Die Tischlerei Friedl aus Traun produziert die Hauptteile aus Holz. Die Transfercenter für Kunststofftechnik GmbH (TCKT) ist als anwendungsorientiertes Forschungsinstitut für die Kunststofftechnik zuständig. Im Holzmodell entstand das gewünschte Design des neuen Produktes. Einzelne Teile des Stuhls wurden nun in einem Kooperationsprojekt des Kunststoff-Clusters neu entwickelt: Denn die gewünschten Funktionalitäten des Produktes können nur durch Einsatz und Entwicklung einzelner Teile aus Kunststoff ermöglicht werden. Die Kombination Holz-Kunststoff bietet eine Reihe von Vorteilen: Wirtschaftlich keit, gleichbleibende Qualität und vor allem sicherheitstechnische Vorteile. Die Produkte müssen sehr strenge TÜV-Vor schriften erfüllen, sollen dabei aber ihre Funktionalität behalten. Einige der notwendigen Teile des Kinderhochstuhls wären sehr schwer oder unmöglich aus den Werkstoffen Holz oder Metall herzustellen. Damit bleibt die Entwicklung aus dem System «Holz/Kunststoff» als einzige technische Möglichkeit übrig. Generell müssen alle Teile durch ihre Funktionalität und durch einfaches Bedienen überzeugen. Zusätzlich sollten sie extrem robust sein und teils extremen Kräften standhalten.
Kunststoff punktet mit höherer Lebensdauer Die Rollen des Endproduktes halten Kräften von 150 kN stand, sind aber nicht zu hart, um Fussböden zu beschädigen. Die richtige Werkstoffauswahl war entscheidend. Der geringere Verschleiss von Kunststoff gegenüber Holz und die damit
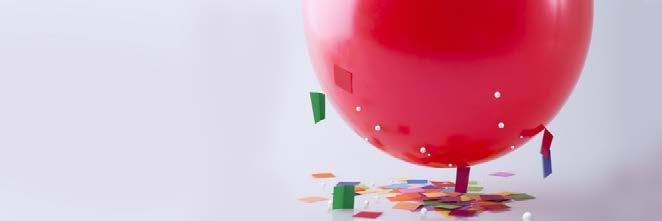

HAUG BIEL AG
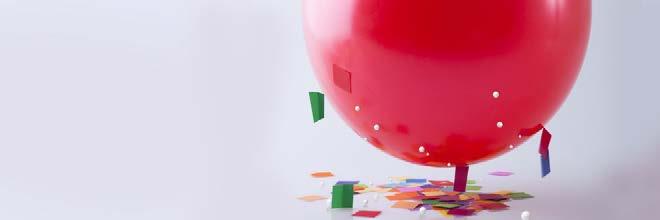
Johann-Renfer-Str. 60 Postfach CH-2500 Biel/Bienne 6 Tel.: +41 (0) 32 344 96 96 Fax: +41 (0) 32 344 96 97 info@haug.swiss www.haug.swiss
Spritzguss-Einsätze machten die Fertigung wichtiger Teile möglich. Bild: TCKT
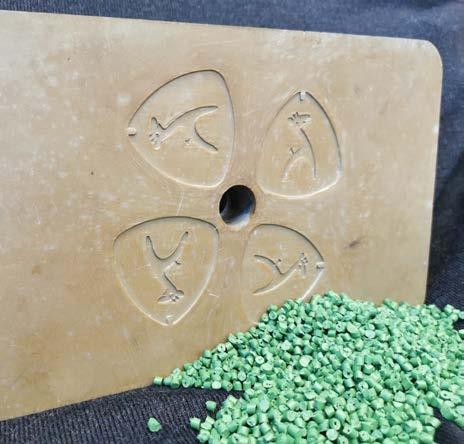
verbundene höhere Lebensdauer dieser Teile war ein Grund, warum bei den ausgewählten Teilen dem Werkstoff Kunststoff der Vorzug gegeben wird. kleinen Grösse sollen sie Kräften bis zu 25kN standhalten. Getestet wurde der QuarttoLino auf 150 Kilogramm und somit ist er auch ein vollwertiges Möbel für Erwachsene. Auch wenn Teile aus Kunststoff kaputt gehen sollen, so gibt es kaum kleine «Absplitterungen», welche bei Kinderartikeln sehr gefährlich und verboten sind. Nennenswerte Auswirkungen auf die Umwelt und den Energie- und Ressourcenverbrauch sind vor allem im Recycling von Kunststoff zu sehen. Weiter ist die Herstellungszeit der Kunststoffteile gegenüber Holzteilen wesentlich kürzer, was zu Energieeinsparungen führt.
Junge Technologie Additive Tooling im Einsatz Das Transfercenter für Kunststofftechnik stellt mittels Additive Tooling SpritzgussEinsätze für die Werkzeuge her. Additive Tooling ermöglichte, die Erstserie möglichst wirtschaftlich zu produzieren. Erst wenn der Verkauf angelaufen ist, sollen die sehr kostenintensiven Werkzeuge aus Metall hergestellt werden. Einige Teile sind generell nur sehr schwer oder überhaupt nicht aus den Werkstoffen Holz oder Metall herzustellen, um die sehr strengen Vorschriften (z.B. TÜV) erfüllen zu können und dabei ihre Funktionalität zu behalten.
Robust und ökologisch
Durch das Projekt ergeben sich wesentliche technische Vorteile für Zielgruppen. Ihren Bedürfnissen angepasst, werden die Teile deutlich leichter im Gewicht und in der Handhabung, Reinigung und Pflege. Generell verschleissen Teile aus Kunststoff viel weniger, als aus Holz gefertigte Teile. Dadurch bekommen die Kunden eine er höhte Lebensdauer der Teile. Weiter sind sie sehr leicht zu bedienen. Die Stecksysteme werden durch einen «Fingerdruck» betätigt, wobei sie im geschlossenen Zustand eine hohe Sicherheit bieten. Bei der Rückenlehne wurde zusätzlich eine gewisse Elastizität gewonnen, was zu ergonomischerem Sitzen führt. Trotz ihrer relativ
Kontakt Quarttolino Kremstalstrasse 96 A-4050 Traun +43 676 674 01 24 office@quarttolino.com quarttolino-childrens-furniture-store. business.site
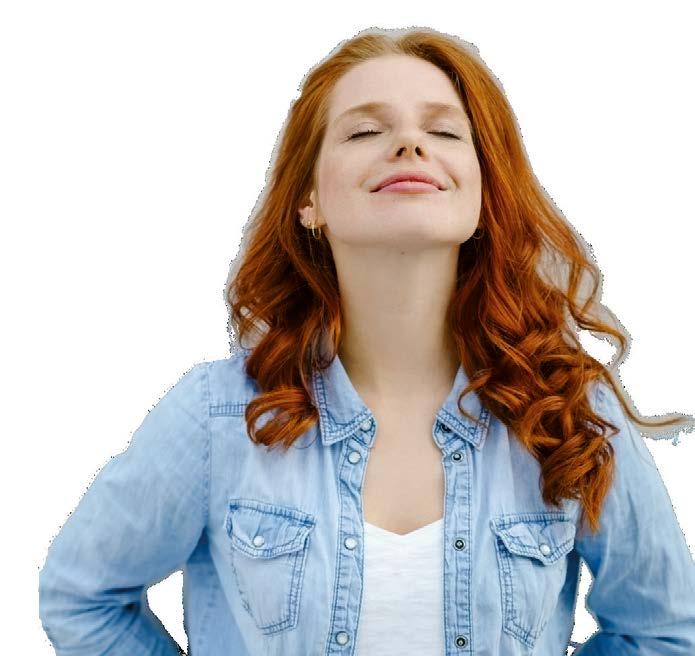
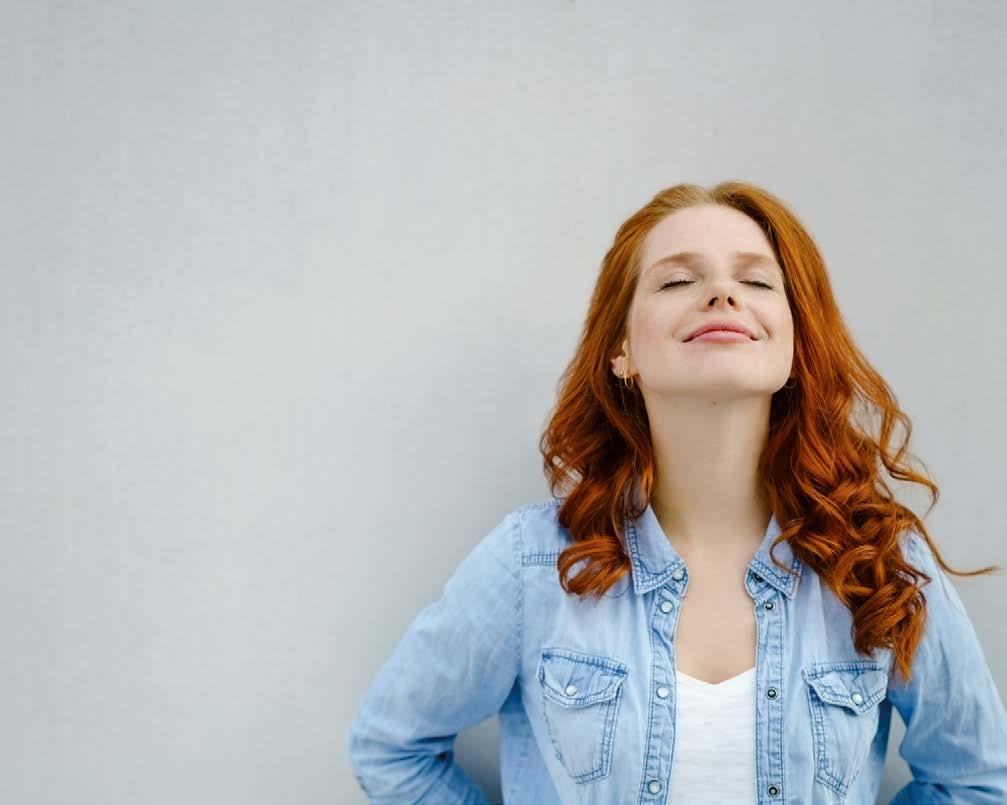

GRAVIMAX gravimetrische Dosiergeräte
Vier Jahre, drei Roboter, acht Partner
Im BMBF-Forschungsprojekt ProLMD entstehen neue Hybrid-Prozesse, die konventionelle Fertigungsverfahren mit Laserauftragschweissen (auch bekannt als Laser Material Deposition, LMD) zu einem neuen Fertigungsansatz vereinen.
Nikolaus Fecht¹
Den Beginn markiert 2016 eine Forschungsidee. «Es geht um die Entwicklung wirtschaftlicher und robuster Systemtechnik für das LMD-Verfahren, basierend auf einem Knickarm-Roboter, sowie ihre Inte gration in eine Prozesskette für hybride Fertigung», blickt Jan Bremer, Wissen schaftler am Fraunhofer-Institut für Lasertechnik ILT aus Aachen, zurück. «Dabei bewegen wir uns entlang der Prozesskette für die roboterbasierte hybrid-additive Fertigung und erforschen verschiedene, dafür notwendige Technologien. Das Spektrum der Inhalte deckt dabei alles ab – von Bearbeitungsköpfen, Roboter- und Schutzgassystemen über die Schweissprozesse bis zur Qualitätssicherung und Software.» Was hybrid konkret in der Praxis heisst, zeigen drei Anwendungen der Projektpartner MTU Aero Engines (Aufbau von Funktionselementen an einer Triebwerkskomponente), Airbus (Bauteilverstärkung durch 3D-Verrippung) und Mercedes-Benz (Anpassung eines Presswerkzeuges in der Karosseriefertigung). Im Mittelpunkt steht die lokale Verstärkung oder Veränderung von konventionell gefertigten Bauteilen. Im Projekt liegt der Fokus auf der Ferti gung, die entwickelten Technologien erlauben jedoch auch Reparaturanwendungen.
Verschiedene Fertigungsverfahren kombinieren «Diese Beispiele zeigen, was wir unter hybrider Fertigung verstehen», sagt Wissenschaftler Bremer. «Es ist die flexible Verbindung der Vorteile aus verschiedenen Fertigungsverfahren, da sie beliebige kon
Roboterforschungszelle mit Optikwechselsystem beim Draht-Laserauftragschweissen am Fraunhofer ILT. Bild: Fraunhofer ILT

ventionelle Herstellverfahren mit LMD zu einer durchgängigen Prozesskette vereint.» Die Flexibilität zeigt sich auch im Projekt bei den Industriepartnern, die ihre Demonstratoren vor der LMD-Funktionalisierung durch Rollformen (Airbus), Giessen (Mercedes-Benz) oder Schmieden (MTU) herstellen. Für den Wissenschaftler ist es ausserdem ein schönes Beispiel, wie sich komplexe Variantenvielfalt in der Herstellung vereinfachen lässt. «Man fängt zum Beispiel mit dem Stanzen und Besäumen eines Basis teils immer auf die gleiche Art und Weise an», erklärt Bremer. «Die Varianten werden dann später mit Hilfe von LMD hergestellt. Der Anwender kann also weiterhin seine Stanzanlage nutzen, um dann aber z. B. Verstärkungen additiv aufzutragen. Durch das LMD-Verfahren und die in ProLMD entwickelten Technologien können wir dabei flexibel und automatisiert agieren. Das entspricht unserer Leitidee: Additive Manufacturing – aber nur dort in der Prozesskette, wo es Mehrwert bedeutet.» Mit diesem Ziel im Visier arbeiten die Aa chener zusammen mit insgesamt sieben Industriepartnern an einer hocheffizienten, modularen LMD-Zelle, die sich mit geringem Aufwand in eine bestehende Prozesskette integrieren lässt. Für maximale Anwendungsflexibilität wer den Prozesse mit Draht und auch Pulver als Zusatzwerkstoff entwickelt. Am Fraun
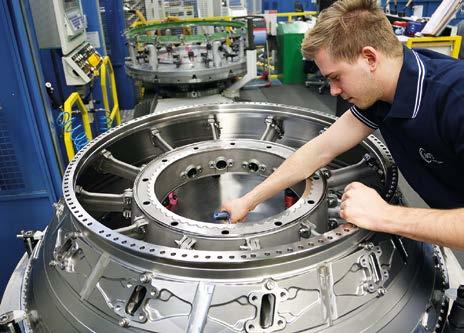
Bild: MTU Aero Engines 3D-Druck im Massstab XXL: Das Turbinenzwischengehäuse eines GEnx-Triebwerks ist Demonstrationsbauteil des Projektpartners MTU Aero Engines für die hybrid-additive Fertigung durch Laserauftragschweissen (LMD) mit dem neuen Bearbeitungskopf.
hofer ILT entstand u. a. eine Bearbeitungsoptik zur Erzeugung eines Ringstrahls für das koaxiale Laserauftragschweissen, die im ProLMD-Verbundprojekt weiterentwickelt und genutzt wird. Diese Optik erzeugt einen Ring mit gleichmässiger Intensitätsverteilung und bietet damit Richtungsunabhängigkeit beim Schweissen. Im Rahmen des Projektes werden dabei Prozesse mit Auftragsraten im Bereich von 1 bis 2 kg/h bei hoher geometrischer Auflösung entwickelt.
Eine Roboteranlage für Grossbauteile Doch warum kommt ein mehrachsiger Kuka Roboter zum Einsatz? «Für ihn spricht der sehr grosse Bauraum, seine Flexibilität und die einfache Zugänglichkeit», erläutert Bremer. «Wir können in der Versuchsanlage mithilfe von bis zu acht Achsen ein fast beliebig komplexes Bauteil von allen Seiten bearbeiten. Die Anlagentechnik lässt sich dabei mit Robotern erstaunlich preiswert realisieren.» Fokus des Projektes ist die Bearbeitung von komplexen Grossbauteilen. «Bauteile bis zu 1,2 Tonnen Gewicht und einem Durchmesser von zwei Metern können wir auf der Roboteranlage bearbeiten», berichtet der Wissenschaftler. Die Aufgabenteilung der weiteren Projektpartner ist klar definiert: Der Geschäftsbereich Lasertec des Kuka-Standorts in Würselen übernimmt die Projektleitung und Zellintegration des Roboters, während sich die Laserline GmbH aus Mülheim-Kärlich um die Auslegung und Entwicklung von Strahlquelle und Optik kümmert. Die M. Braun Inertgas-Systeme GmbH, Garching (bei München), ist für den Bau einer Schutzgaszelle zuständig, während die Dortmunder BCT Steuerungs- und DVSysteme GmbH Software und anlagenintegrierte Messtechnik entwickelt.
Fachübergreifende Lösungen entwickeln Flexibel wird die Plug-in-Lösung, weil sie nach dem Blackbox-Prinzip funktioniert. «Uns interessiert nicht, was vorher oder nachher mit dem Bauteil passiert», betont Bremer. «Wir arbeiten nicht ein statisches CAD-Modell ab, sondern nutzen dank ro buster Systemtechnik und Software in adaptiven Prozessen auch die reale Geometrie. Durch intelligente Algorithmen kann sich die Zelle auch extremen Bauteilabweichungen anpassen und diese kompensieren.» Die Betonung liegt dabei bei Hardund Software auf robust – vom Laserkopf, Roboter bis hin zum flexiblen Schutzgaskonzept und geeigneter angepasster Bahnplanungsalgorithmen. Ein Hinweis, dass das Fraunhofer ILT nicht nur den Schweissprozess weiterentwickelt, sondern auch weitere wichtige Aspekte wie den Einfluss der Robotergenauigkeit auf die Prozesssi cherheit und Bauteilqualität erforscht. Während Kuka in Würselen den Roboter in einer flexiblen Schutzgaszelle oxidationsempfindliche Werkstoffe wie Titan prozesssicher schweissen lässt, arbeiten die Aachener mit einer weiteren Roboteranlage ohne Schutzgaszelle bei den nickelund eisenbasierten Werkstoffen mit lokal aus der Düse ausströmendem Schutzgas. Wenn die Auftragsrate höher ausfällt, verwenden sie nach Bedarf zusätzlich eine wenige Zentimeter grosse Schutzgasglocke. «Auf diese Weise kommen alle drei Lösungen mit deutlich weniger teurem Schutzgas aus», so Bremer. Innovative Prozesse sind dabei nicht nur Forschungsgegenstand, sondern auch Alltag am Fraunhofer ILT. «Bei den ersten Versionen der lokalen Schutzgasglocke hatten wir bei höheren
Bild: Kuka.

Schutzgaszelle: Dank der Nutzung eines fasergeführten Systems kann der Kuka-Roboter nahezu uneingeschränkt arbeiten und auch komplexe Geometrien realisieren.
Auftragsraten thermische Probleme», berichtet der Forscher. «Da unsere Forscherkollegen im pulverbettbasierten selektiven Laserschmelzen (Laser Powder Bed Fusion, LPBF) aber bereits seit einigen Jahren an der Verarbeitung von Kupfer arbeiten, konnten wir mit ihrer Unterstützung auf einer Forschungsanlage das Bauteil mit innenliegenden Kühlstrukturen additiv aus
Ein neuer Bearbeitungskopf ermöglicht Draht-LMD in hybriden Prozessen. Bild: Fraunhofer ILT
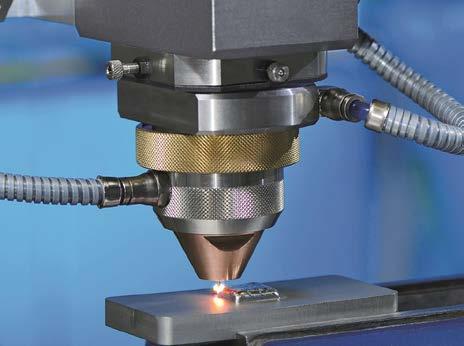
Kupfer fertigen und das Problem so lösen.» Für ihn ist es ein Beispiel dafür, was sich ergeben kann, wenn ein Institut fachübergreifend Lösungen entwickelt.
Kompakte Bearbeitungszelle für KMU Mehr über die Erfolge von proaktiver Teamarbeit zeigt sich beim Blick in die Entwicklungshallen am Fraunhofer ILT. In Aachen stehen eine grosse und eine kompaktere Roboterzelle für die additive Fertigung. Auf diese neueste Entwicklung sind die Projektteilnehmer besonders stolz: Mit zusätzlicher finanzieller Unter stützung durch das BMBF entsteht eine preiswertere Variante der ProLMD-Roboteranlage für kleine und mittlere Unternehmen (KMU). «Wir haben die Lösung von einem 3,1 m langen Roboterarm mit 90 kg Traglast auf etwa 2 m und 60 kg Traglast herunter skaliert», berichtet der Wissenschaftler. «Am grossen Roboter zeigen wir ein flexibles Wechselsystem mit Drahtund pulverbasierten Bearbeitungsköpfen, in der kleinen Zelle geht es um pulverbasiertes LMD, maschinenintegrierte Geometrievermessung und das neue CAMModul.» Mit der neuen Zelle beweisen die Aache ner in Zusammenarbeit mit den Projektpartnern, dass sich auch eine kompakte Zelle für KMU realisieren lässt, die nochmals deutlich weniger als ein typisches Bearbeitungszentrum kostet.
Kontakt Fraunhofer-Institut für Lasertechnik ILT Steinbachstrasse 15 D-52074 Aachen +49 241 8906-0 www.ilt.fraunhofer.de n
Intelligente Greifer machen Produktionsanlagen effizienter und sicherer
Industrie-Greifer aus dem 3D-Drucker
Die nächste Generation moderner Industrie-Greifer denkt mit und wird passgenau nach Kundenwünschen hergestellt. Das gelingt durch die Integration von Sensoren zur Druck- oder Temperaturmessung schon während der Fertigung der Greifer im 3D-Drucker. Produktionsanlagen und Fabriken werden dadurch effizienter, flexibler und sicherer.
Dr. Christian Schäfer-Hock¹
«Bald werden auch die Greifer in der industriellen Produktion mitdenken und damit viel Zeit und Geld sparen», ist Ines Dani, Hauptabteilungsleiterin für Funkti onsintegration und Leichtbau am Fraunhofer IWU, überzeugt. Die Forscherin kennt den Markt für Greiftechnik in der Produktion und sieht einen neuen Weg zu mehr Qualität und Flexibilität, der auch die Pro duktionssicherheit erhöht: Das Einbringen von Sensoren in die Greifer selbst – schon während ihrer additiven Herstellung im 3D-Drucker. Dani: «Wir kennen und nutzen die Vorteile der additiven Fertigung: individuelle Anpassung an den Einsatz in der Produktionsanlage, komplexe Geometrien, Gewichtsreduktion oder bionisches Design. Neu ist, dass wir durch feinste Sensoren Druck- oder Temperaturmessungen während des Greifvorgangs vornehmen können. Stellen Sie sich vor, Ihre Fabrik meldet sich bei Ihnen, wenn der Greifdruck zu gross ist und sie könnten ihn flexibel anpassen. Dadurch wird weniger Material verschlissen.»
Zahlreiche Anwendungsmöglichkeiten Intelligente Greifer haben das Potenzial, die Produktion zu beschleunigen. Wenn sie drucksensibel sind, ermöglichen sie schnellere und direktere Zugriffe an Stellen eines Werkstücks, die bisher nicht für das Greifen geeignet waren. Zudem kann so ein Greifer an unterschiedlich beschaf fenen Stellen eines Werkstückes ansetzen.
Beispiel für additiv gefertigte Industrie-Greifer im Einsatz

Das spart Platz in der Produktionsanlage. Qualitätssteigerungen sind ebenfalls möglich, da nun dünnere Bauteile als bisher gegriffen werden können und zugleich ihr Zustand mittels Temperaturmessung näher bestimmt werden kann. Bei hitzesensiblen Bauteilen kann die Druckstärke am Greifer in Abhängigkeit von der gemesse nen Temperatur festgelegt werden. Besondere Messanlagen zur Bestimmung der Temperatur eines Bauteils können entfallen. Die Produktionssicherheit in einer Fabrik lässt sich durch intelligente Greifer effizient steigern. Der Greifer meldet sich nicht nur, wenn der Greifdruck zu gross ist, sondern auch wenn er zu klein ist und damit das zu transportierende Bauteil nicht sicher gegriffen wird. Ein intelligenter Greifer regelt in diesem Fall automatisch nach und ver hindert, dass Bauteile herunterfallen.
Sensoren im Druckprozess einsetzen Das Team um Dani nutzt das Verfahren der additiven Fertigung durch selektives Laserstrahlschmelzen (kurz: LBM). Es dient der werkzeuglosen Herstellung metallischer Komponenten mit geometri
Sensorintegrierter Industrie-Greifer aus additiver Fertigung Bilder: Fraunhofer IWU
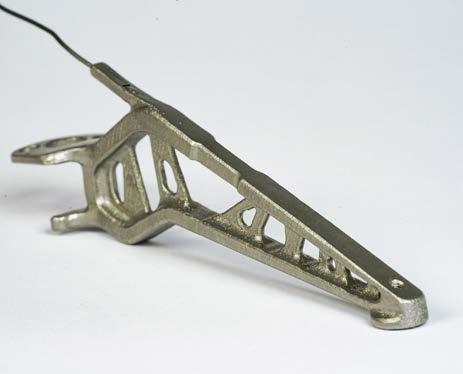
schen Besonderheiten, die sich mit klassischen Fertigungstechnologien nicht herstellen lassen. «Man muss sich das wie in einem 3D-Drucker vorstellen. Wir legen nacheinander dünne Schichten aus Aluminium- oder Edelstahl-Pulver übereinander und verfestigen mit einem Laser die Stellen, die wir für die gewünschte Form benötigen.», erläutert Dani. «Während dieses Prozesses setzen wir mittels eines kleinen Roboters die Sensoren punktgenau und hochstabil dort ein, wo sie später messen sollen. Wir nennen das In-situ-Integration. Auf diesem Weg ist die Montage weniger aufwändig.»
Kontakt Fraunhofer-Institut für Werkzeugmaschinen und Umformtechnik IWU Reichenhainer Strasse 88 D-09126 Chemnitz +49 371 5397-1311 www.iwu.fraunhofer.de