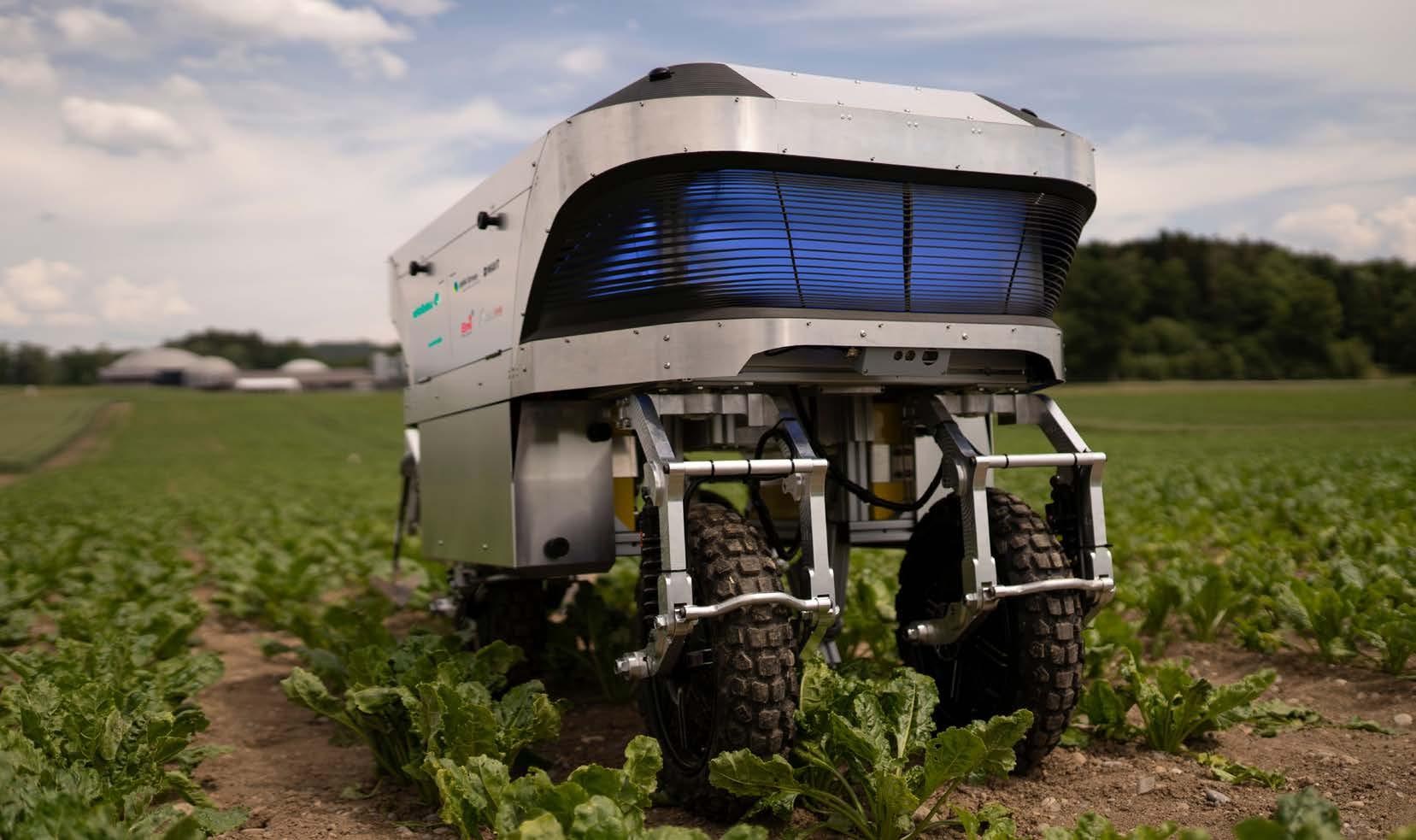
13 minute read
AUTOMATION
Das Fokusprojekt «Rowesys» der ETH Zürich zeigt eindrücklich, wie Schäden an Menschen und Umwelt mithilfe der Digitalisierung und smarter Technologie minimiert werden können.
Scheurer Swiss in ETH-Fokusprojekt involviert
Advertisement
Roboter aus dem 3D-Drucker
Die Scheurer Swiss unterstützt das Fokusprojekt «Rowesys» – Robotic Weeding System – der ETH Zürich mit ihrem Engineering-Know-how und liefert 3D-gedruckte karbonverstärkte Roboterkomponenten.
Das für seine langjährige Expertise mit Faserverbundtechnologien bekannte Engineering-Unternehmen Scheurer Swiss GmbH unterstützt das Projekt «Rowesys» – Robotic Weeding System – der ETH Zürich als Goldsponsor mit ihrer Engineering-Ex
Der Agrarroboter wurde mit hauchdünnen karbonverstärkten Kunststoff-Lamellen ausgestattet, die mit LEDs hinterlegt wurden, um jederzeit den Roboterstatus anzuzeigen.
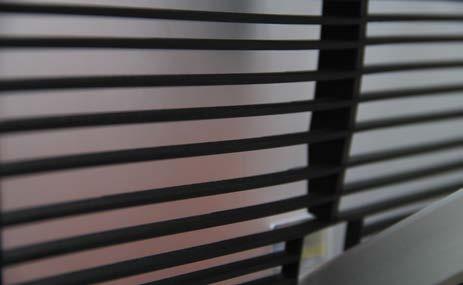
pertise und druckt im Auftrag des Teams karbonverstärkte 3D-Komponenten für den Agrarroboter. Zehn motivierte ETHStudierende verfolgen mit dem Konzept das Ziel, eine nachhaltige Alternative für den Herbizideinsatz in der Landwirtschaft zu entwickeln. Ihr autonomer Agrarroboter zur Unkrautentfernung ist soeben in den Praxistest gegangen.
Karbon revolutioniert den Ackerbau
Das von der Scheurer Swiss unterstützte Fokusprojekt «Rowesys» der ETH Zürich zeigt eindrücklich, wie Schäden an Menschen und Umwelt mithilfe der Digitalisierung und smarter Technologie minimiert werden können. Mit diesem Ziel vor Augen arbeiten zehn motivierte ETH-Studenten mit Unterstützung von acht ExpertenCoaches und Sponsoren seit dem vergangenen September an der Entwicklung des Agrarroboters «Rowesys». Das zugrundeliegende Konzept basiert auf mechanischer Unkrautvernichtung. Daraus entstanden ist ein funktionsfähiger Prototyp für Zuckerrübenfelder, weil diese eine relativ hohe Verwendung von Herbiziden voraussetzen. «Rowesys» erfüllt die Anforderungen an einen autonomen Agrarroboter hinsichtlich Effizienz, Zuverlässigkeit, Autonomie, Sicherheit und Benutzer freundlichkeit bereits zu einem grossen Teil. Nicht zuletzt dank der Verwendung von kosteneffizientem karbonverstärktem Material aus dem 3D-Drucker, das nebst den monetären Vorteilen auch praktisch
grenzenlose Designmöglichkeiten bietet. So wurde der Agrarroboter etwa mit hauchdünnen karbonverstärkten Kunst stoff-Lamellen ausgestattet, die mit LEDs hinterlegt wurden, um jederzeit den Roboterstatus anzuzeigen.
Leichtbau auf dem Feld
Ein anderes filigranes Bauteil wiederum dient als Schnittstelle zwischen dem Aluminium-Chassis und der Elektronik des Roboters. Die aussergewöhnliche Form des Verbindungsstücks ist so konstruiert, dass kein Gramm überflüssiges Material verbaut wird, um den Roboter nicht unnötig zu beschweren. Gleichzeitig muss das Bauteil ultra-stabil sein, um die Verbindung zu halten. «Nur mit der Technologie des karbonverstärkten 3D-Drucks ist es überhaupt möglich, eine so passgenaue, filigrane und dennoch stabile Komponente herzustellen. Wir haben das RowesysTeam mit unserem Know-how im Bereich der Faserverbundtechnologien beratend unterstützt und unsere langjährige Expertise aus der Entwicklung von hocheffizienten Composite-Bauteilen für den Motorsport operativ in die Entwicklung und den 3D-Druck der karbonverstärkten Komponenten für den Agrarroboter einfliessen lassen», erklärt Dominik Scheurer, CEO der Scheurer Swiss GmbH.
Scheurer unterstützt das Projekt «Rowesys» – Robotic Weeding System – der ETH Zürich als Goldsponsor.
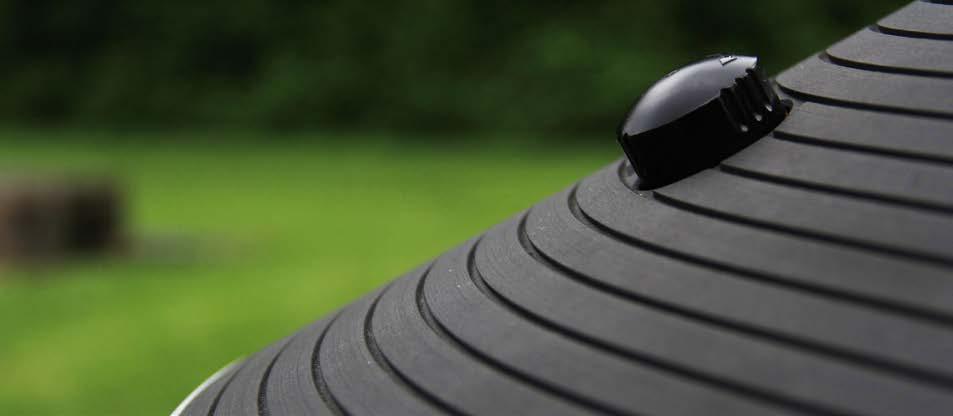
Der Agrarroboter soll Pestizide ersetzen
Der Agrarroboter zieht kleine Pflüge durch den Boden, die das Unkraut zwischen den Pflanzenreihen vernichten, indem sie die Wurzeln aus dem Grund an die Oberfläche reissen, wo das Unkraut austrocknet. Der Roboter fährt autonom durch die Reihen, erkennt das Ende des Feldes mithilfe der eingebauten Kameras und wechselt zur nächsten unbearbeiteten Reihe. Dieser Prozess wird wiederholt, bis das Ende des Feldes erreicht ist. Der Praxistest hat gezeigt, dass mit «Rowesys» sowohl der Einsatz von Herbiziden, als auch die Verschmutzung des Grundwassers, der Luft und der produzierten Güter massiv reduziert werden können. «Motiviert hat mich an diesem Projekt neben dem Bezug zum Gelernten und der Chance, im Teamwork praktische Erfahrungen zu sammeln, besonders die Nachhaltigkeit in Bezug auf den herbizidfreien Zuckerrübenanbau. Denn bislang existieren in diesem Bereich der Agrarwirtschaft keine Investitionen in eine nachhaltigere Produktion», so Nico Burger, Software & Controls Team Rowesys.
Kontakt Scheurer Swiss GmbH Industriestrasse 27 CH-8604 Volketswil +41 52 202 26 00 info@scheurer.swiss www.scheurer.swiss
FT » Rover PLAST A «DEDUST PRO»/«
«DeDust Pro» setzt neue Masstäbe fürs Entstauben «Rover Plast A FT» – flexible Bearbeitungen – Bearbeitungslösungen
Mit einem maximalen Rohgasvolumen von 1,2 m 3 ist eine kontinuierliche Abreinigung der Filterelemente während des Betriebes zulässig. Bei einem Brand wird die Ein- und Austrittsklappe geschlossen und somit wird das Feuer erstickt.

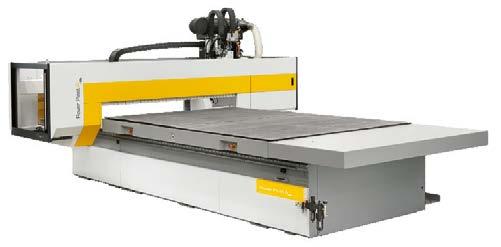
Die verschiedensten Materialien können individuell bearbeitet werden. Die Einzelanfertigungen ermöglichen eine grosse Flexibilität in der Produktion und Kundenwünsche können optimal ausgeführt werden.
Besuchen Sie unseren Online-Shop www.ineichen.ch/shop Ineichen AG
Maschinen und Anlagen für die Holz- und Kunststoffverarbeitung Luzernerstrasse 26 I CH-6294 Ermensee Telefon +41 41 919 90 20 I www.ineichen.ch I info@ineichen.ch
Automatisiertes ERP für automatisierte Transporte
Mehr Transparenz für Unternehmensprozesse
Eine Produktionsmaschine meldet den Abschluss der aktuellen Palette. Daraufhin stimmen sich die Transportroboter im Lager untereinander ab, welcher von ihnen den Auftrag mit den geringsten Zeit- und Energiekosten ausführen kann. Dieser holt die produzierten Artikel ab und transportiert sie vollständig autonom und millimetergenau zum vorgesehenen Lagerplatz. Was bisweilen noch nach Utopie klingt, ist dank der Lösungen des österreichischen Robotik-Spezialisten Agilox schon heute Realität.
Die Technik hinter den Robotern basiert auf einem Plug-and-Play-System: Der Kunde erwirbt die gewünschte Anzahl an Geräten und ist daraufhin in der Lage, diese selbst in seine Werksumgebung zu integrieren. Im Gegensatz zur branchenüblichen Implementierungszeit von Tagen oder Wochen erfolgt die Einrichtung der Agilox-Roboter innerhalb weniger Stunden. Möglich wird dies unter anderem, da der Robotik-Spezialist zur Abstimmung der Roboter untereinander auf Schwarmintelligenz statt einen zentralen Fleet-Manager setzt. Zur dynamischen Orientierung im Raum tastet ein Laser die Umgebung ab. So ist es den Robotern möglich, sich ohne Hilfsmittel auf bis zu zwei Millimeter genau in beliebigen Umgebungen zu positionieren.
Altes System konnte nicht Schritt halten
Ursprünglich gegründet wurde Agilox 2009 – damals als Intrest OG – als Spezialist im Bereich Automatisierung von intralogistischen Prozessen und Softwareentwicklung rund um Warehouse-Management-Systeme. Erst als 2013 im Zuge eines Kundenprojekts der Bedarf an innovativen fahrerlosen Transportsystemen deutlich wurde und das Unternehmen beschloss, sein Geschäftsmodell daraufhin auszurichten, begann Agilox mit der Nutzung einer kleineren ERP-Lösung eines lokalen Anbieters. «Ein wirklich gutes Produkt, das uns viele Jahre lang zuverlässige Dienste erwiesen hat», erinnert sich Franz Humer, CEO und Mitgründer der Agilox Services GmbH. «Allerdings richtet sich die Lösung hauptsächlich an Elektrotechnik-Betriebe. Damals beschäftigten wir ca. 13 Mitarbeiter, heute

Mit der Entwicklung und Produktion der Roboter änderten sich die bestehenden Prozesse deutlich, was kontinuierlich Anpassungen am ERP-System erforderte.
sind es 55. Wir sind der Lösung schlicht und einfach entwachsen.»
Dynamischer Wandel
Mit der Entwicklung und Produktion der Roboter änderten sich die bestehenden Prozesse deutlich, ein Wandel, der sich dynamisch vollzog – und damit kontinuierlich Anpassungen am ERP-System erforderte. Als kleines Unternehmen war es für den damaligen ERP-Anbieter entsprechend eine Herausforderung, mit benötigten Anpassungen im System in derselben Geschwindigkeit nachzuziehen. Darüber hinaus lag der Funktionsschwerpunkt der Altlösung auf dem Fertigungsbereich. Zur Herstellung seiner Transportroboter fokussiert sich Agilox hingegen auf Entwicklung, Montage und Life-Time-Service, benötigte Fertigungsteile werden überwiegend extern in Auftrag gegeben.
Bedienfreundlichkeit als Entscheidungsfaktor
Im Frühjahr 2019 beschloss das Unternehmen den Umstieg auf eine neue ERP-Lösung. «Dadurch, dass wir unser System immer wieder an unterschiedliche ERPLösungen ankoppeln, hatten wir naturgemäss bereits einen guten Überblick über
die am Markt verfügbaren Produkte», erklärt Humer. «Wir wussten von Anfang an, dass wohl nur zwei oder drei Systeme wirklich für unsere Anforderungen infrage kommen.» Deren Anbieter kontaktierte Agilox mit einem Lastenheft. Zu den zentralen Anforderungen zählte unter anderem ein leistungsstarkes Material-Management. So sollte die Lösung in der Lage sein, unterschiedliche Artikeltypen aus mechanischer und Elektrotechnikkonstruktion sowie Handelsware und Verkaufsartikel effizient abzubilden. Auch eine starke Versionierung war in diesem Kontext wichtig, denn die Roboter werden kontinuierlich weiterentwickelt und verbessert.
Einfach im Unterhalt
Darüber hinaus verfolgte Agilox das Ziel, alle benötigten Prozesse vollständig im Standard abzubilden. «Hier unterscheiden wir uns vielleicht ein wenig von anderen Unternehmen», räumt der Geschäftsführer ein, «aber unsere Mitarbeiter sind sehr offen dafür, auch eigene Prozesse an das ERP-System anzupassen. Viel wichtiger ist uns die Vorgabe, keine Individualentwick lungen zuzulassen, da wir eine einfache Wartbarkeit und Release-Fähigkeit des Systems sicherstellen wollen.» Besonders dieses Kriterium war einer der entscheidenden Aspekte, die am Ende des Auswahlverfahrens den Ausschlag für die Asseco-Lösung gaben. «Hinzu kam aus unserer Sicht noch die Benutzerfreundlichkeit, durch die sich APplus im Vergleich zu den anderen Systemen auszeichnete», ergänzt Humer.
Qualitätsmanagement und internationaler Austausch
Die künftige APplus-Nutzung soll für mehr Automatisierung, Effizienz und Transparenz in den Prozessen sorgen. So wird etwa im Qualitätsmanagement die Datenbasis bislang sehr komplex erfasst. Vorgänge wie Reklamationen oder Lieferantenbewertungen werden manuell in Excel-Listen gepflegt und sind damit nicht automatisiert in den Gesamtprozess eingebunden. Indem die entsprechenden Informationen künftig auch in APplus gepflegt werden, will Agilox den Qualitätskreislauf zwischen der Praxis und den Schlussfolgerungen, die sich daraus wiederum für die Entwicklung ziehen lassen, stärken. Die internationale Zusammenarbeit zwischen der österreichischen Zentrale und der Niederlassung in den USA soll durch die Einführung ebenfalls effizienter werden: Auch die amerikanischen Kollegen werden künftig mit APplus arbeiten. Be reits eine Million US-Dollar Umsatz wurden im vergangenen Jahr in diesem Markt mit Vertrieb, Service und Inbetriebnahme generiert. Hierzu agiert die österreichische Zentrale – wie für alle Niederlassungen – als Zulieferer. Die Abstimmung für entsprechende Aufträge erfolgt bislang papierbasiert und telefonisch, Bestellungen der TT-188_render_1-2 Niederlassung werden wie reguläre Aufträge behandelt und verarbeitet. In Zukunft soll diese Zusammenarbeit in Form von Intercompany-Prozessen optimiert wer den, sodass Aufträge aus den USA beispielsweise unmittelbar einen Warenausgang auslösen oder einen Gegenbeleg im System der Zentrale erstellen. Die konkrete Umsetzung wird derzeit in engem Austausch mit den Spezialisten der Asseco erarbeitet.
Unsere Temperier Lösungen für Sie
Universale Temperiergeräte bis 150°C Wasser Temperiergeräte bis 90°C Druckwasser Temperiergeräte bis 160°C Öl Temperiergeräte bis 360°C Kühlgeräte von -25°C bis +40°C
tool-temp.ch
TT-1398_render_1-2
TT-1398
Live-Start im Dezember
«Nicht nur in Bezug auf die Realisierung solcher Funktionen, auch generell sind wir mit der Beratung durch Asseco sehr zufrieden», resümiert der Geschäftsführer. «Wir hatten eine sehr klare Vorstellung davon, was wir benötigen und in welchem Zeitrahmen die Implementierung stattfinden sollte. Bei der Planung haben wir hier TT-DW160_9kW_render_1-2 von der hohen technischen Kompetenz unseres Beraters sehr profitiert.» Nach der Schulungsphase seiner Mitarbeiter werden seit Juli erste Module wie CRM und Zeiterfassung produktiv genutzt. Bis Dezember soll APplus 7.0 schliesslich vollständig im Einsatz sein – passend zum Bezug der neuen Unternehmenszentrale.
P 0
TT-142_render_1-2
5
50 100 Pressure Druckentlastung Décharge de pression Pressure release -1 0 -15 0 bar psi 0 15 150 200 10
TT-142
Kontakt Asseco Solutions AG Amalienbadstr. 41c D-76227 Karlsruhe +49 721 91432-900 de.info@assecosol.com www.assecosol.com
Forscherteam entwickelt automatisierten Qualitätsregelkreis
Intelligente Qualitätssicherung
Die Fertigung hochintegrierter mechatronischer Baugruppen ist für die Automobilzuliefererindustrie von grosser Bedeutung. Nicht zuletzt durch die zunehmende fahrzeuginterne Vernetzung steigt die Komplexität der Baugruppen. Neben hohen Anforderungen an den Montageprozess besteht auch ein erhöhter Prüf- und Dokumentationsbedarf. Um allen Qualitätsansprüchen zu genügen, wird aktuell zumeist auf teure manuelle Montage und Überprüfung zurückgegriffen.
Im Rahmen des Projekts «Gekoppelte automatisierte Prüf- und Montageprozesse unter Einbindung kollaborierender Robotik» (RoMonA) entwickeln Forscherinnen und Forscher einen Ansatz zur intelligenten Qualitätssicherung mit kollaborierenden Robotern. «Wir wollen eine Methode erarbeiten, mit der Fehlertrends, die wir bei der Qualitätsprüfung erkennen, zu einer automatischen Programmmodifikation der Montageroboter führen», sagt Gerhard Schreck, Abteilungsleiter Prozessautomatisierung und Robotik beim Fraunhofer IPK. Experten von der Hiersemann Prozessautomation GmbH prüfen, wie eine intelligente Aufgabenverteilung zwischen Mensch und Roboter auf Basis von Prüfund Prozessdaten gesteuert werden kann. «Wir versprechen uns von dem Projekt, dass der Aufwand für nachträgliche, manuelle Qualitätssicherungsschritte um bis zu 20 Prozent reduziert und der Ausschuss um bis zu 10 Prozent verringert werden kann», so Holger Klempnow, Geschäfts führer der Klero GmbH Roboterautomation, einem weiteren Projektpartner.
Demonstratoren als Praxistest
Bis Herbst 2021 werden zwei Demonstratoren bei den beteiligten Systemintegratoren und Anlagenlieferanten implementiert sein, um die theoretischen Ergebnisse zu validieren. Begleitet wird das Projekt von der Mercedes-Benz AG, welche in der Rolle als assoziierter Anwendungspartner am Standort Berlin einen ersten Anwendungsfall für die Projektergebnisse zur Verfügung stellen wird. Die entwickelten Lösungsbausteine sollen dort zur Entlastung der Mitarbeiter bei Routineaufgaben und zu einer

Mit ihrem Projekt entwickeln Forscherinnen und Forscher einen Ansatz zur intelligenten Qualitätssicherung mit kollaborierenden Robotern.
deutlichen Erhöhung der Anlagenverfügbarkeit führen. Das Projekt RoMonA wird mit Mitteln des BMBF unter dem Förderkennzeichen 02P19K052 gefördert. Die Fördermass nahme «KMU-innovativ: Produktionsforschung» richtet sich an kleine und mittlere Unternehmen mit dem Ziel, deren Innovationspotenzial zu stärken sowie die Forschungsförderung für KMU im Rahmen des Programms «Innovationen für die Produktion, Dienstleistung und Arbeit von morgen» attraktiver zu gestalten. Das Fraunhofer-Institut für Produktionsanlagen und Konstruktionstechnik IPK betreibt angewandte Forschung und Entwicklung für die gesamte Bandbreite industrieller Aufgaben – von der Pro duktentwicklung über den Produktionsprozess und die Wiederverwertung von Produkten bis hin zu Gestaltung und Management von Fabrikbetrieben. Zudem legt das Institut besonderen Wert darauf, produktionstechnische Lösungen auch über den industriellen Bereich hinaus anwendbar zu machen, etwa in den Feldern Verkehr und Sicherheit.
Kontakt Fraunhofer IPK Pascalstrasse 8-9 D-10587 Berlin +49 30 39006-0 gerhard.schreck@ipk.fraunhofer.de www.ipk.fraunhofer.de
«Smart Gear» macht Industrieroboter leistungsfähiger und intelligenter
Innovatives Getriebeprinzip
Der Doktorand Philipp EIsele entwickelte ein kompaktes Getriebe mit intelligenter Sensorik, das doppelt so hohe Übersetzungen wie bisherige Getriebe erreicht und neue, smarte Services ermöglicht.
Im Rahmen seiner Masterarbeit an der TU Graz entwickelte Philipp Eisele 2019 ein Konzept für einen kollaborativen Roboter, also einen Industrieroboter, der mit Men schen zusammenarbeitet. Als Doktorand am Institut für Fertigungstechnik der TU Graz entwickelte er das Konzept weiter – und ist heute Erfinder von «Smart Gear». Das ist ein innovatives und mittlerweile patentiertes Antriebssystem, das derzeit als Prototyp umgesetzt wurde und eine Zäsur in der Antriebstechnik darstellen könnte.
Leichtgewicht mit smartem Innenleben
Das innovative Getriebeprinzip erlaubt doppelt so hohe Übersetzungen wie bei bisherigen Koaxialgetrieben, da Eisele auf umlaufende Zahnräder verzichtet und stattdessen Kolben für die Leistungsübertragung nutzt. «Im Vergleich zu herkömmlichen Getrieben ermöglicht das patentierte System eine Verdopplung des Übersetzungsverhältnisses bei gleichzeitiger Erhöhung des zu übertragenden Drehmoments.» Dadurch kann die Baugrösse und damit das Gewicht im Vergleich zu bestehenden Getrieben halbiert werden, ohne an Wirkung zu verlieren. Der «Smart Gear»-Prototyp besteht aus Stahl und Aluminium. Der Aufbau erfolgt modular, die einzelnen Komponenten können dadurch in der Massenfertigung günstig produziert werden und durch unterschiedliche Kom binationen ein breites Produktspektrum abdecken. «In der Praxis werden Antriebe also kleiner, leichter und günstiger», fasst Eisele die Vorteile zusammen. Der Einsatz von «Smart Gear» ist bei Industrierobotern, Hebevorrichtungen oder Positioniereinrichtungen möglich. Die zentrale Stärke von «Smart Gear» liegt im verfügbaren Platz im Gehäuse, der
Bild: Fotoatelier Robert Frankl
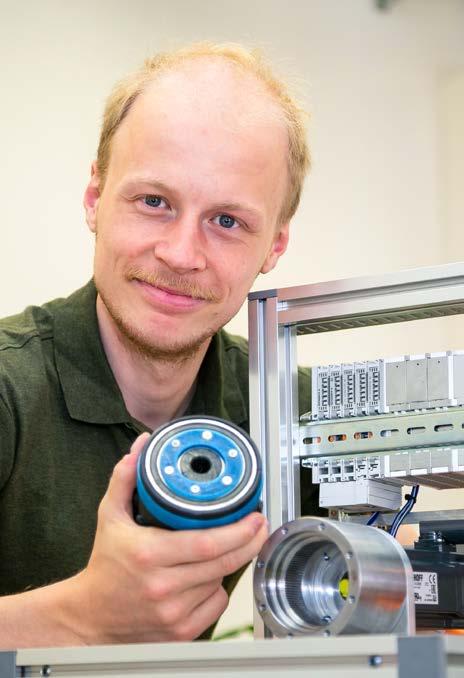
TU Graz-Doktorand Philipp Eisele mit einem Kunststoffmodell (Massstab 1:1) sowie mit dem Original-Stahlgehäuse von «Smart Gear» im Prüfstand platziert: Noch in diesem Jahr soll die Vorserienproduktion der patentierten Antriebstechnologie anlaufen.
durch den Wegfall der umlaufenden Zahnräder entstanden ist, wie Eisele erklärt: «Wir können den Hohlraum für intelligente Sensorik nutzen, die völlig neue Services ermöglicht.» So lässt sich das Getriebe beispielsweise mit Cloud-Diensten oder mit lokalen Firmen-Netzwerken verbinden, wodurch Unternehmen neben der Mechanik auch Leistungsdaten und den Getriebe-Zustand überwachen und somit ihre Produktionsprozesse effizient managen können.
Lohnende Bezahlmodelle
Darüber hinaus eröffnet die Vernetzung des Getriebes neue Geschäftsmodelle, mithilfe derer die Anschaffungskosten gering gehalten werden können. Eisele nennt exemplarisch drei Arten: «Es können – wie bei Pay-by-Use-Modellen – nur jene Stunden verrechnet werden, in denen sich das Getriebe dreht. Das Unternehmen bezahlt faktisch nur die tatsächliche Einsatzdauer. Mit dem System ist auch eine vorherseh bare Wartung möglich. Diese maximiert die Einsatzzeit und reduziert die Kosten für das Unternehmen. Ausserdem lässt sich die maximale Leistung softwareseitig beschränken und kann je nach Bedarf freigeschaltet werden, was ein Leistungs-Upgrade ermöglicht, ohne das Getriebe austauschen zu müssen.» Mit diesem Geschäftsmodell gewann «Smart Gear» im Jahr 2019 die zwölfte Ausgabe der Gründungsgarage – einem Kooperationsprojekt von TU Graz und Uni Graz, das Studierende zu Gründerinnen und Gründern von morgen ausbildet – und lockte damit auch Investments an.
Mit Geschäftspartnern weiterentwickeln
Noch in diesem Jahr soll die Vorserienproduktion starten; es laufen bereits erste Gespräche mit Roboterherstellern und Unternehmen aus der produzierenden Industrie, die «Smart Gear» in ihre Produkte integrieren wollen. Eisele denkt schon einen Schritt weiter: Er möchte die Fertigung durch innovative Fertigungsprozesse und neue Materialien noch günstiger und effizienter gestalten.
Kontakt TU Graz | Institut für Fertigungstechnik Rechbauerstrasse 12 A-8010 Graz +43 316 873 7175 philipp.eisele@tugraz.at www.tugraz.at