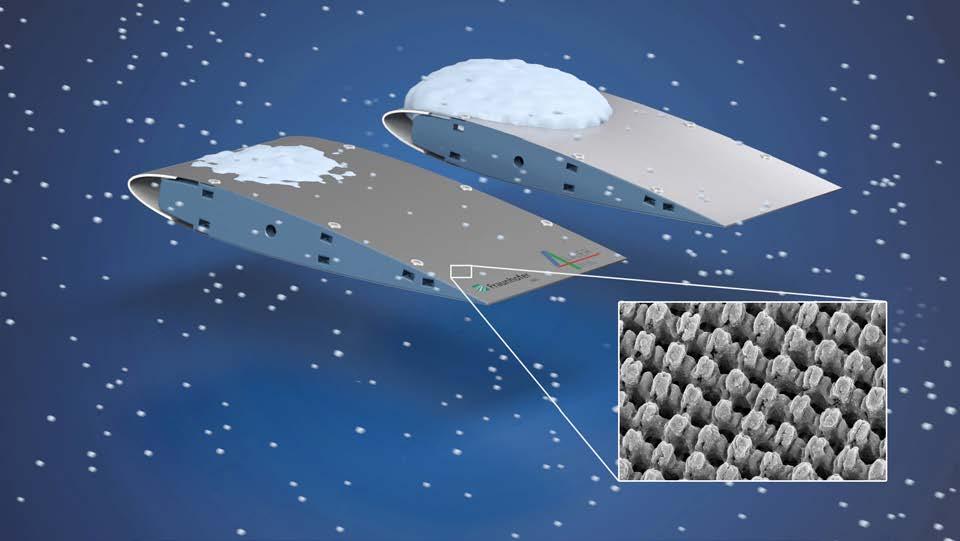
14 minute read
OBERFLÄCHEN
Flugzeugoberflächen schnell und umweltschonend enteisen
Laserfunktionalisierte Oberflächen
Advertisement
Eis auf Flugzeugoberflächen birgt potenzielle Gefahren: Der Treibstoffverbrauch steigt, die Aerodynamik wird gestört und der erzeugte Auftrieb sinkt – die Funktionsfähigkeit des Flugzeugs wird beeinträchtigt. Mit der Direkten Laserinterferenzstrukturierung lassen sich Oberflächenstrukturen gestalten, die Anti-Icing effektiv ermöglichen.
Die Bildung von Eis stellt im Flugverkehr ein Sicherheitsrisiko dar. Setzt sich eine dünne Frostschicht auf den Tragflächen oder an anderen neuralgischen Punkten wie dem Heck ab, so hat dies negative Auswirkungen auf die Aerodynamik des Flugzeugs. Der Auftrieb kann reduziert und der Luftwiderstand erhöht werden. Eisaggregation an Sonden und Sensoren führt zu Fehlern beim Messen der Luftgeschwindigkeit, was im Flugbetrieb sicherheitskritisch ist. Aus diesen Gründen müssen die Maschinen bereits vor dem Start von Schnee und Eis befreit werden. Am Boden entfernen Spezialfahrzeuge mit chemischen Mitteln die weisse Schicht. Die gefrierhemmenden Chemikalien sollen die Eisbildung zudem verhindern. Allerdings sind diese Flüssigkeiten umweltschädlich und teuer. 400 bis 600 Liter fallen für die Enteisung an. Auch in der Luft müssen die Flugzeuge vor der frostigen Gefahr geschützt werden. Hierfür sorgen zusätzliche technische Präventionsmechanismen in Form sogenannter «Ice Protection Systems». Diese Heizelemente erhöhen jedoch den Treibstoffverbrauch.
Ökologisch nachhaltig
Mit der Direkten Laserinterferenzstrukturierung (englisch: Direct Laser Interference Patterning, kurz DLIP – siehe Kasten) hat ein Forscherteam des Fraunhofer IWS in enger Zusammenarbeit mit dem Kooperationspartner Airbus und der TU Dresden ein Verfahren entwickelt, mit dem sich komplexe, mäanderförmige Oberflächenstrukturen im Mikrometer- und Submikrometerbereich generieren lassen, die das Anhaften von Eis verhindern oder stark reduzieren. Die Besonderheit: Die For scherinnen und Forscher kombinieren die DLIP-Technologie mit Ultrakurzpulslasern,
Eisschutz durch Laserstrukturierung
sodass mehrstufige Mikrostrukturen auf 3D-Tragflächen in einem Ein-Schritt-Ver fahren erzeugt werden. Das Ergebnis: Zum einen können sich Teile des anhaftenden Eises unter bestimmten Vereisungsbedingungen von alleine lösen, zum anderen ist eine um 20 Prozent geringere Heizleistung beim technischen Enteisen erforderlich. Das bringt zahlreiche Vorteile mit sich: Es sind weniger umweltschädliche Enteisungsmittel erforderlich, die Wartezeit für die Fluggäste während der Enteisung reduziert sich und der Energie- sowie der Treibstoffverbrauch im Flugbetrieb sinken ebenso wie das Fluggewicht infolge der potenziell kleineren Heizaggregate. Mit herkömmlichen Technologien ist eine Kombination der beiden Effekte bislang nicht möglich.
Tests im Windkanal in Kooperation mit Airbus
Dies waren die Ergebnisse einer gezielten Prozessentwicklung mit Vorarbeiten durchgeführt an der TU Dresden gefolgt von der finalen Demonstratorstrukturierung am Fraunhofer IWS, die anschliessend im Windkanal von Airbus getestet wurden. Die Untersuchungen wurden mit einem strukturierten «NACA-Profil» – einer miniaturisierten und realitätsnahen Tragfläche – sowie mit einem unstrukturierten NACAProfil als Referenz durchgeführt. Dabei brachten die Experten die optimierte Struktur auf das komplex geformte dreidimensionale NACA-Profil auf und testeten unter realen Bedingungen bei Windgeschwindigkeiten zwischen 65 bis 120m/s, Lufttemperaturen unter minus zehn Grad Celsius und verschiedenen Feuchtewerten.
Das Verfahren ist grossflächig anwendbar
Die Projektpartner demonstrierten in den Windkanalversuchen, dass das Eis auf der strukturierten Oberfläche nur selbstlimitierend wachsen kann und nach einer definierten Zeit wieder von alleine abfällt – ohne dass ein zusätzliches Beheizen der
Oberfläche notwendig ist. Zusätzlich zeigten die Experimente, dass das Eis bei einer Heizleistung von 60 Watt auf dem unstrukturierten Profil erst nach 70 Sekunden verschwindet, sich jedoch auf dem strukturierten Pendant bereits nach fünf Sekunden vollständig zurückbildet – bei gleicher Heizleistung. Das entspricht einer Beschleunigung von über 90 Prozent infolge des Einsatzes der DLIP-Technologie. Um das Eis auf dem unstrukturierten Demonstrator ebenfalls innerhalb von fünf Sekunden zu beseitigen, waren 25 Prozent Quelle: Airbus mehr Heizleistung bzw. 75 Watt erforderDas NACA-Profil mit der wasserabweisenden strukturierten Oberfläche. lich. «In einer tollen Kooperation mit Airbus zeigten wir erstmals realitätsnah, welOberfläche erzielen und so die Zahl der ckelt haben, ist ein Versuch, herkömmliche che Potenziale die grossflächige Anhaftpunkte für Eis deutlich reduzieren. Technologien durch umweltschonende, Laseroberflächenstrukturierung beim AntiWir werden die Ergebnisse bald wissenkostengünstigere Alternativen zu erset Icing erschliessen kann. Mit unserem schaftlich publizieren.» Elmar Bonaccurso, zen.» Im nächsten Schritt wollen die ProDLIP-Ansatz realisierten wir erstmals mulMaterialwissenschaftler bei Airbus und jektpartner die Methode optimieren und tiskalige Oberflächen mit MikrometerauflöProjektpartner, ergänzt: «Die Bildung von für verschiedene Luftzonen auslegen. Dasung auf einem komplexen Bauteil wie Eis ist besonders bei der Landung gefährrin werden auch Ergebnisse einfliessen, dem NACA-Profil und zeigten zugleich die lich. Wenn das Flugzeug bei Minusgraden wie sie derzeit durch reale Flugtests mit konkreten Vorzüge gegenüber anderen Ladurch die Wolken fliegt, gefriert das Was einem A350 gewonnen werden, an dem serverfahren», sagt Tim Kunze, Teamleiter ser innerhalb von Millisekunden auf der eine per DLIP bearbeitete Oberfläche ander Gruppe Oberflächenfunktionalisierung Oberfläche. Dies kann die Funktionsfähiggebracht wurde. am Fraunhofer IWS. Sein Kollege Sabri keit von Steuerelementen wie Landeklapkontrolliert überlagert. Der aus der Überlagerung resultierende Interferenzeffekt – Alamri ergänzt: «Die Anwendung von Mikro- und Nanostrukturen auf Metall bewirkt, dass sich Wassertropfen nicht mehr pen und Vorflügel stören, die Aerodynamik ist dann beeinträchtigt. Derzeit nutzen wir die heisse Luft der Triebwerke, um die Schlüsseltechnologie etabliert anheften können. Dieser Effekt ist der NaOberflächen der Flügel zu beheizen. Die Mit dem Direkten Laserinterferenzstruktutur entlehnt und im Allgemeinen als Lotuswasserabweisende Struktur, die wir gerieren durch Kurz- und Ultrakurzpulslaser Effekt bekannt. Mit unserem neuen DLIPmeinsam mit den Forschern vom Fraunhohat das Forscherteam eine SchlüsseltechVerfahren können wir eine fragmentierte fer IWS im EU-Projekt Laser4Fun entwinologie etabliert, die vielseitig einsetzbar ist, etwa wenn technische Oberflächen
Direct Laser Interference Patterning (DLIP) ponenten in kalten Klimaregionen vereist
Jeder kennt das Phänomen des Interferenzeffekts aus dem Physikunterricht: Ein sind. Die Technologie eignet sich aber
Lichtstrahl, der einen Doppelspalt passiert, bildet bei Überlagerung ein periodisches auch für komplett andere Anwendungen
Muster aus hellen und dunklen Linien – ein sogenanntes Interferenzmuster. Zwar wie den Produktschutz, biokompatible Imerzeugen die Experten vom Fraunhofer IWS die Muster auf anderen Wegen – gleich plantate oder verbesserte elektrische bleibt aber, dass Licht beim Direkten Laserinterferenzstrukturieren (engl.: Direct Steckkontakte. Die Forschenden können
Laser Interference Patterning – DLIP) überlagert werden muss. die funktionalen Mikrostrukturen grossflä
Das Verfahren eignet sich zum Herstellen von nano- und mikrometergrossen Strukchig sowie mit hohen Prozessgeschwindigturen und ermöglicht gezielte Oberflächentopographien für eine Vielzahl von Ankeiten aufbringen und für eine Vielzahl wendungen. Beim Direkten Laserinterferenzstrukturieren wird ein kohärenter Laservon Anwendungen Vorteile erzielen, die so strahl in zwei oder mehr Strahlen geteilt und auf der Oberfläche des Bauteils bislang nicht denkbar waren. wie Windkraftanlagen oder andere Komdie «periodische Modulation der Laserintensität» – erlaubt das Aufbringen definier Kontakt ter Strukturen auf 2D- und 3D-Bauteilen. Verschiedene Strukturgeometrien können Fraunhofer-Institut für Werkstoffmithilfe der DLIP-Technologie grossflächig mit Flächenraten von bis zu einem Quaund Strahltechnik IWS dratmeter pro Minute aufgebracht werden. Die technologischen Prinzipien des DLIPWinterbergstrasse 28
Verfahrens sowie die daraus resultierenden Oberflächeneffekte entwickelt das D-01277 Dresden
Fraunhofer IWS dabei in enger Kooperation mit der TU Dresden unter dem Dach +49 351 83391-3661 des «Centers for Advanced Micro-Photonics (CAMP)». tim.kunze@iws.fraunhofer.de www.iws.fraunhofer.de n
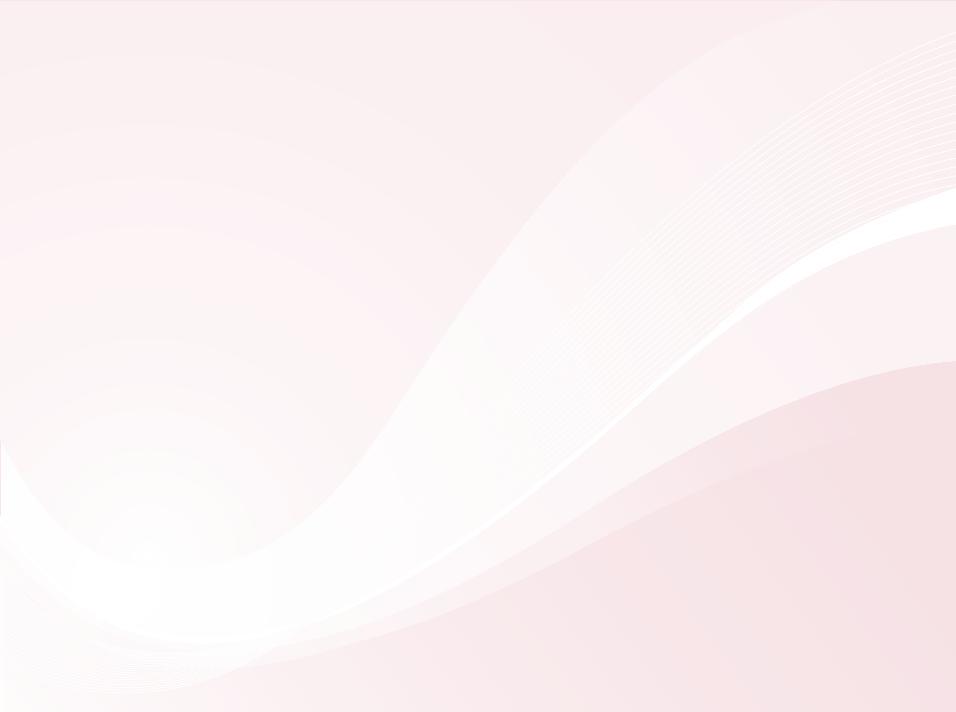
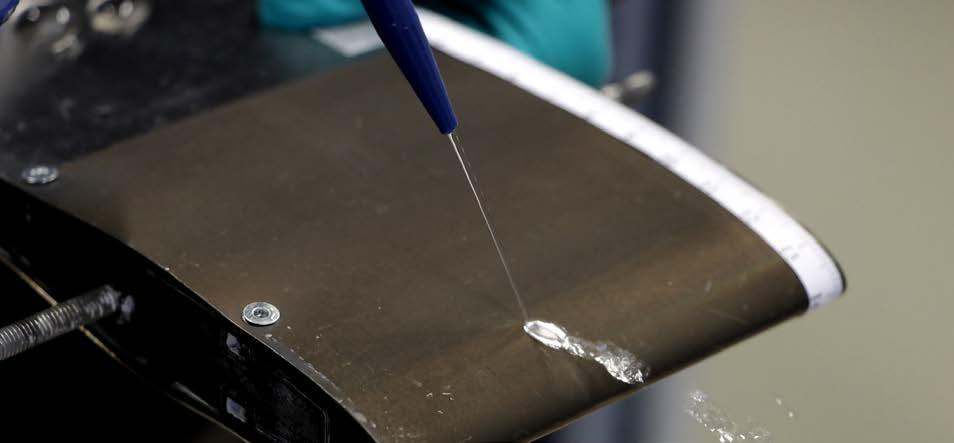
Strukturelle Fügebereiche effektiv und effizient reinigen
Oberflächen für Klebungen vorbereiten
Um Gewicht einzusparen, kommen in der Automobilindustrie immer mehr Baugruppen aus Kunststoffen und Leichtmetallen zum Einsatz, die miteinander verklebt werden. Dabei ist insbesondere beim Verbinden struktureller Komponenten eine zuverlässige Vorbehandlung der Fügebereiche ein Muss.
Leichtbau ist in der Automobilindustrie kein neues Thema. Im Zuge der weiteren Verringerung von CO ² -Emissionen und Elektromobilität gewinnt es jedoch weiter an Aktualität. OEM und Zulieferer setzen deshalb auch bei Karosserieteilen wie beispielsweise Türen, Fahrzeugdächern, Kofferraum- und Heckklappen sowie Motorhauben vermehrt auf leichtere Materialien wie Aluminium und Kunststoffe. Darüber hinaus ermöglichen veränderte Produktions- und Fügetechnologien wie das Verkleben statt Schweissen, Nieten oder Schrauben Gewichtseinsparungen. Um bei strukturellen Verklebungen beispielsweise von Karosserieteilen oder Batteriegehäusen die erforderliche Haftfestigkeit zu gewährleisten, werden sehr hohe Anforderungen an die Sauberkeit und Benetzbarkeit der Fügebereiche gestellt.
Partiell und trocken reinigen
Klassische nasschemische Reinigungsprozesse mit wasserbasierenden Medien oder Lösemitteln scheiden bei diesen Aufgabenstellungen aus verschiedenen Gründen aus. Dazu zählen, dass die Fügebereiche üblicherweise eine deutlich höhere Sauberkeit aufweisen müssten als der Rest des Bauteils und sich diese Reinigungsprozesse nicht oder nur mit extremem Aufwand in eine Fertigungs- beziehungsweise Montagelinie integrieren lassen. Favorisiert werden daher trockene Verfahren wie die umweltverträgliche quattroClean-Schneestrahlreinigungsverfahren der acp systems AG. Sie kommt in vielen Industriebereichen zur ortsselektiven oder ganzflächigen Reinigung bei Bauteilen aus praktisch allen Werkstoffen zum Einsatz. Da die Reinigung materialschonend erfolgt, lassen sich auch sensible Substrate behandeln. Das Verfahren verwendet flüssiges Kohlendioxid als Reinigungsmedium, das als Ne
Der Kleberauftrag kann direkt oder nach einer zwischengeschalteten Aktivierung erfolgen.
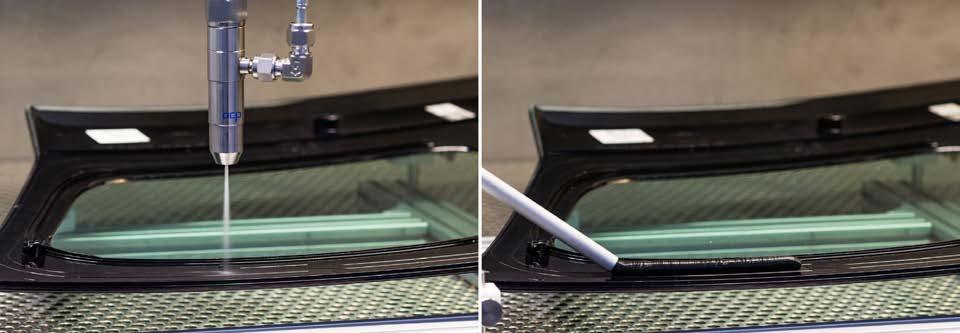
benprodukt bei chemischen Prozessen und der Energiegewinnung aus Biogas entsteht und daher umweltneutral ist. Es wird durch die verschleissfreie Zweistoff-Ringdüse geleitet und entspannt beim Austritt zu feinem CO ² -Schnee. Dieser Kernstrahl wird in einem separaten, ringförmige Druckluft-Mantelstrahl gebündelt und auf Überschallgeschwindigkeit beschleunigt. Beim Auftreffen des gut fokussierbaren Schnee-Druckluftstrahls auf die zu reinigende Oberfläche kommt es zu einer Kombination aus thermischem, mechanischem, Sublimations- und Lösemitteleffekt. Das Zusammenspiel dieser vier Wirkmechanismen entfernt partikuläre (z.B. Staub, Späne, Abrieb, Mikrograte) und filmische (z.B. Trennmittel, Ziehöle, Emulsionen, Silikone, Schmauchspuren) Verunreinigungen reproduzierbar. Abgelöste Verunreinigungen werden durch die aerodynamische Kraft der Druckluft weggeströmt und durch eine integrierte Absaugung entfernt. Automatisierbarer Reinigungsprozess Die vor über 20 Jahren entwickelte quattroClean-Technologie zählt zu den effizientesten, effektivsten und vielseitig einsetzbarsten, trockenen Verfahren. Im Vergleich zu anderen Trockenreinigungsverfahren wie beispielsweise Atmosphärendruckplasmaund Laserreinigung ermöglicht sie durch verschiedene verfahrensbedingte Eigen schaften eine höhere Prozesssicherheit im Serieneinsatz. Dazu zählen der robuste Prozess und das grosse Arbeitsfester. Positiv wirkt sich darüber hinaus aus, dass während der Reinigung keine Erwärmung der zu behandelnde Bauteilbereiche stattfindet. Die Skalierbarkeit des Industrie 4.0-kom
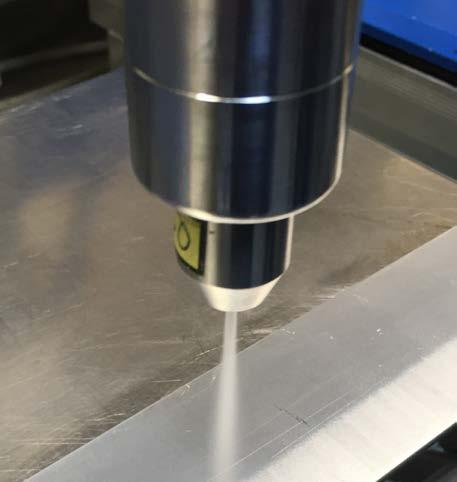
patiblen quattroClean-Systems ermöglicht,
Bei der partiellen Reinigung struktureller Fügebereiche, beispielsweise von Karosserieteilen oder Batteriegehäusen, sorgt das kalte, trockene quattroClean-Verfahren durch den robusten Prozess mit grossem Arbeitsfenster stabil für bedarfsgerechte Sauberkeit.
es einfach und platzsparend an unterschiedliche Anwendungen und Bauteilgeometrien anzupassen. Alle Prozessparameter wie Volumenströme für Druckluft und Kohlendioxid, Anzahl der Düsen, Strahlbereich und -zeit werden durch Versuche im acp-Technikum exakt an das jeweilige Bauteil, die Applikation, die Materialeigenschaften sowie die zu entfernenden Verunreinigungen angepasst. Sie können als teilespezifische Programme in der Anlagensteuerung hinterlegt werden. Auf Standardmodulen basierend erarbeitet acp massgeschneiderte Anlagenkonzepte – sowohl als Standalone-Lösungen als auch für die Integration in Fertigungslinien und verkettete Produktionsumgebungen.
Klebevorbehandlung auf Kunststoff und Metall
Für die Vorbehandlung (Entfernung von Trennmittelrückständen und Aktivierung der Oberflächen) zwei zu fügender Bauteile – gefertigt aus faserverstärktem Polyamid (PA) und unverstärktem PA – hat sich das quattroClean-Verfahren gegen über der Atmosphärendruck-Plasmareinigung durchgesetzt. Gründe waren, dass bei den mit Plasma gereinigten Bauteilen die Anforderungen der nach dem Verkleben erfolgten, zerstörenden Haftfestigkeitsprüfung nicht erfüllt wurden. Ausserdem erforderten die engen Prozessfenster der Plasmareinigung, dass Parameter wie Einwirkzeit, Abstand und Auftreffwinkel des Plasmas sehr genau eingehalten werden, um eine Wirkung auf der Oberfläche zu erzielen und eine Überaktivierung des

Das Zusammenspiel der vier Wirkmechanismen ermöglicht, partikuläre und auch filmische Verunreinigungen reproduzierbar von Kunststoffen (mit und ohne Faserverstärkung) sowie metallischen Bauteilen automatisiert inline zu entfernen.
Kunststoffs zu vermeiden. Für diese Anwendung erarbeitete acp gemeinsam mit dem Unternehmen einen mehrstufigen Prozess, in dem die Bauteile automatisiert gereinigt, aktiviert und verklebt werden. Bei einem asiatischen OEM ging es um die Entfernung minimaler Rückstände des beispielsweise beim Umformen von Karosserieteilen aus Aluminium verwendeten Ziehöls vor dem Verkleben. Das Unternehmen führte dazu vergleichende Versuche mit der Plasma-, Laser- und quattroClean-Reinigung durch. Während sich das Plasmaverfahren hier als nicht zielführend erwies, konnte mit der Laserreinigung das Ziehöl zwar entfernt werden. Allerdings kam es durch die Erwärmung des Bauteils während der Reinigung zu unerwünschten Nebeneffekten, die ebenso wie die vergleichsweise geringe Prozessgeschwindigkeiten Ausschlusskriterien waren. Neben den erzielten Sauberkeitswerten, der hohen Prozessgeschwindigkeit und -sicherheit konnte das quattroClean-Verfahren durch seine «Un empfindlichkeit» und Wirtschaftlichkeit überzeugen. Entsprechend den Berechnungen des OEM ermöglicht es im Vergleich zu einem nasschemischen Prozess Investitionseinsparungen um den Faktor vier, die laufenden Betriebskosten verringern sich um über 50 Prozent.
Kontakt acp systems AG D-71254 Ditzingen +49 7156 48014-0 info@acp-systems.com www.acp-systems.com
Schweizerische Normen-Vereinigung (SNV)
Sulzerallee 70, Postfach CH-8404 Winterthur/Switzerland www.snv.ch
Standards create opportunities!
Normen schaffen Chancen, geben Orientierung und Sicherheit. Dafür setzen wir uns täglich ein, zusammen mit unseren Normenexperten! Diese stellen wir in diesem Jahr ins Rampenlicht und widmen ihnen monatlich eine Story auf unserer Webseite.
Schauen Sie regelmässig auf www.snv.ch rein und lassen Sie sich inspirieren!
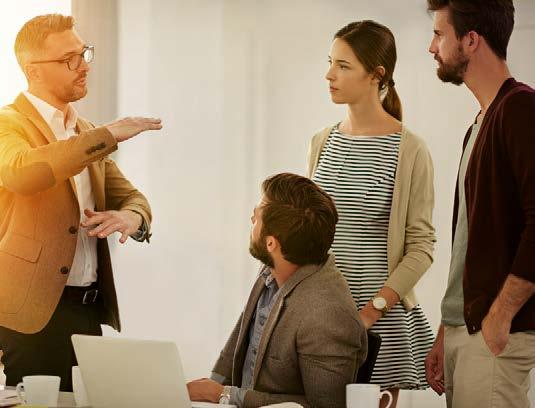
Funktionale Premium-Oberflächen im Trend
Das Interieur wird das neue Exterieur
Ein sich wandelndes Mobilitätsverhalten und die wachsende Autonomie der Autos werden das Fahrerlebnis des Benutzers tiefgreifend verändern. Die Ausstattung im Fahrzeuginnenraum ist auf dem Weg, ein Schlüsselelement bei der Kaufentscheidung zu werden.
Die Megatrends CASE (Connected – Autonomous – Shared – Electric) bringen die Automobilindustrie derzeit aus dem Gleichgewicht: Denn nicht nur das Fahr zeug selbst, sondern auch das Fahrerlebnis steht vor einem Wandel. Durch die zunehmende Autonomie des Autos werden sich die Fahrzeuginsassen weniger auf den Verkehr konzentrieren müssen – und mehr Zeit für Arbeit, Entertainment oder einfach nur Entspannung haben. Als Folge dieser Entwicklung wird sich der Schwerpunkt der Aufmerksamkeit beim Kunden vom jahrzehntelang dominierenden Exterieur zum Interieur verlagern. In den letzten Jahren haben Automobilhersteller und Zulieferer eine Vielzahl von Konzepten für den Fahrzeuginnenraum vorgestellt – so auch Asahi Kasei mit dem Konzeptfahrzeug AKXYTM. Doch wie entwickelt sich eigentlich der Bedarf beim Kunden? Was erwartet der Autonutzer vom zukünftigen automobilen Interieur? Im Oktober 2019 führte Asahi Kasei Europe gemeinsam mit dem Kölner Marktforschungsinstitut Skopos eine repräsentative Umfrage durch und befragte dabei insgesamt 1200 Autonutzer in Deutsch land, Frankreich, Italien und Grossbritannien zu ihren Präferenzen für den automobilen Innenraum der Zukunft.
Interieur als entscheidender Faktor beim Kauf
Ein Kernergebnis der Studie zeigt: Die Markentreue beim Autokauf geht zurück. 18,3 % aller Umfrageteilnehmer in den vier wichtigsten europäischen Automobilmärkten werden sich beim Kauf des nächsten Autos für eine andere Marke entscheiden, 34,9 % sind noch unentschlossen. Fahrzeughersteller müssen mehr als die Hälfte aller Fahrzeugbesitzer aufs Neue
Umfrage zum Fahrzeuginnenraum der Zukunft.
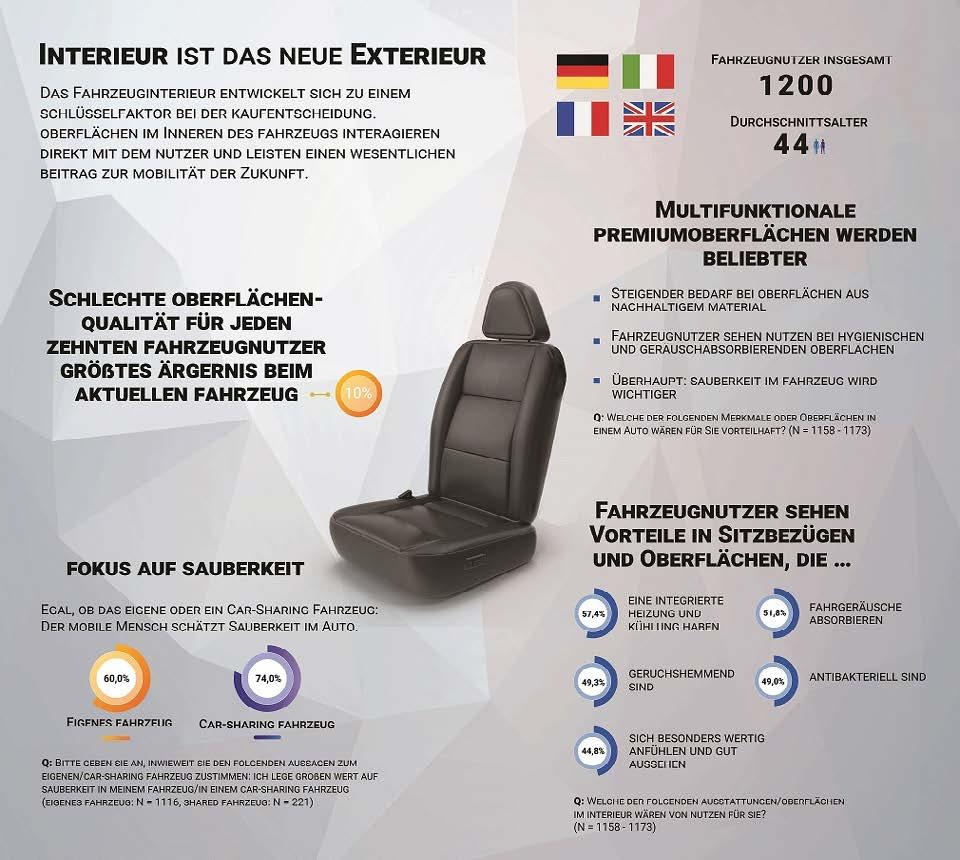
überzeugen. Aber welche Faktoren spielen aus Nutzersicht überhaupt eine Rolle? «Liebe auf den ersten Blick»: Jahrzehntelang war das Exterieur der entscheidende, emotionale Faktor beim Autokauf. Diese «Emotionalisierung» wird nun nach und nach auf den Fahrzeuginnenraum übertragen. Teilweise unterstützt durch neu aufkommende Antriebstechnologien und Mobilitätsmodelle wird die Fahrzeuginnenraum neben dem Exterieur, dem Treibstofftyp und dem Treibstoffverbrauch zu einem immer wichtigeren Faktor. Beim Kauf des aktuellen Autos war die Innenausstattung (z. B. Sitze, Oberflächen usw.) für 54,8 % wichtig, verglichen mit 57,2 %, die dem Exterieur mehr Aufmerksamkeit schenkten. Mit Blick auf den Kauf des nächsten Autos steigt die Bedeutung des Interieurs um 5 Prozentpunkte (59,8 %), die des Exterieurs um 4 Prozentpunkte (61,4 %). Heiko Rother, General Manager Business Development Automotive bei Asahi Kasei Europe, zur zunehmenden Bedeutung des Fahrzeuginterieurs: «Die Kundenerwartungen ändern sich nicht über Nacht, aber dennoch viel schneller, als wir es in der Vergangenheit gesehen haben. Mehr als die Hälfte der Autokäufer in Europa sind bereit, die Marke zu wechseln. Eine grosse Chance für die OEMs, neue Kunden zu gewinnen, in dem sie überzeugende Technologien
einsetzen, die alle Sinne berühren und die Emotionen und Bedürfnisse der Menschen ansprechen.»
«Ja» zu nachhaltigen Oberflächenmaterialien
Als direkte Schnittstelle zwischen Fahrzeug und Nutzer müssen Oberflächen im Fahrzeuginnenraum für das Auge attraktiv und angenehm für die Haut sein. Darüber hinaus sind sie der bestimmende Aspekt dafür, wie er/sie den Innenraum des Fahrzeugs wahrnimmt – und noch wichtiger: das Fahrerlebnis. Einer von zehn Umfrageteilnehmern (10,3%) sieht die schlechte Verarbeitungsqualität von Oberflächenmaterialien im Innenraum als grösstes Ärgernis in seinem aktuellen Auto. 44,8% aller Teilnehmer sehen einen Vorteil in Oberflächen, die besonders hochwertig aussehen und sich besonders gut anfühlen – zum Beispiel für Sitze, Armaturen oder Dachhimmel – im Vergleich zu nur 11,4%, die dies nicht tun. Ein Drittel aller Teilnehmer (32,5%) wäre bereit, für diese Oberflächen als Zusatzausstattung einen angemessenen Preis zu zahlen. Während das Wort «angemessen» natürlich streng subjektiv ist, zeigt es doch die wachsende Bedeutung von Innenoberflächen. Nach dem Oberflächenmaterial selbst befragt, glauben 57%, dass nachhaltige Materialien für Sitzbezüge und Oberflächen in den nächsten 5 bis 10 Jahren immer wichtiger werden, während Echtledermaterialien aus Sicht der Teilnehmer an Bedeutung verlieren.
Schlüsselfaktoren beim Kauf des aktuellen/nächsten Fahrzeugs.
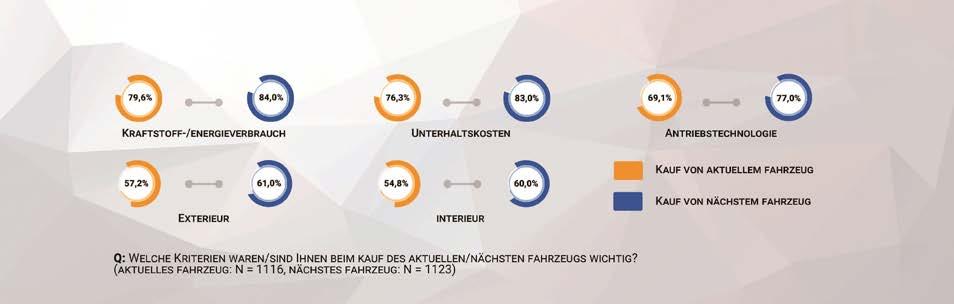
Hygienische und schallabsorbierende Oberflächen
Neben der Optik und Haptik zeigen die Ergebnisse der Umfrage einen wachsenden Bedarf nach Innenoberflächen mit weiteren Funktionen, die das Fahrerlebnis insgesamt verbessern. Nach zusätzlichen Funktionen der Sitzbezüge und Oberflächen befragt, sehen 49 % aller Umfrageteilnehmer einen Nutzen in antibakteriellen Eigenschaften. Betrachtet man die Altersstruktur genauer, so zeigt sich, dass Autofahrer im Alter von 18 bis 39 Jahren einen stärkeren Nutzen antibakterieller Oberflächen sehen, insbesondere im Vergleich zu den Teilnehmern über 59 Jahre. Der gleiche Trend lässt sich bei Sitzbezü gen und Oberflächen mit geruchshemmenden Eigenschaften feststellen. 49,3 % sehen einen Nutzen in diesen Oberflächen, die von den Autonutzern im Alter von 18 bis 39 Jahren wiederum sehr geschätzt werden. Während insgesamt ein Bedarf an hygienischen Oberflächen besteht, ist ein stärkerer Bedarf bei den jüngeren Altersgruppen zu beobachten, die auch eher bereit sind, zusätzliche Kosten für diese Oberflächen in Kauf zu nehmen. Mit dem sich verändernden Fahrerlebnis im Auto wird sich auch die Geräuschwahrnehmung verändern. Bereits heute betrachten 16,1% der Umfrageteilnehmer das Fahrgeräusch als grösstes Ärgernis im aktuellen Fahrzeug. Mit Blick auf das Automobil der Zukunft wird die Unterdrückung von Strassen- und Motorgeräuschen noch wichtiger werden. Während verschiedene Materialien und Technologien im Fahrzeuginnenraum dieses Problem lösen können, leisten auch sichtbare Oberflächen im Innenraum ihren Beitrag. 51,8 % sehen einen Nutzen in geräuschabsorbierenden Sitzbezügen und -oberflächen, 35,9 % sind sogar geneigt, diese Oberflächen gegen zusätzliche Kosten zu buchen.
Kontakt Asahi Kasei Europe GmbH Sebastian Schmidt Am Seestern 4 D-40547 Düsseldorf +49 211-2806-8139 sebastian.schmidt@asahi-kasei.eu www.asahi-kasei.eu
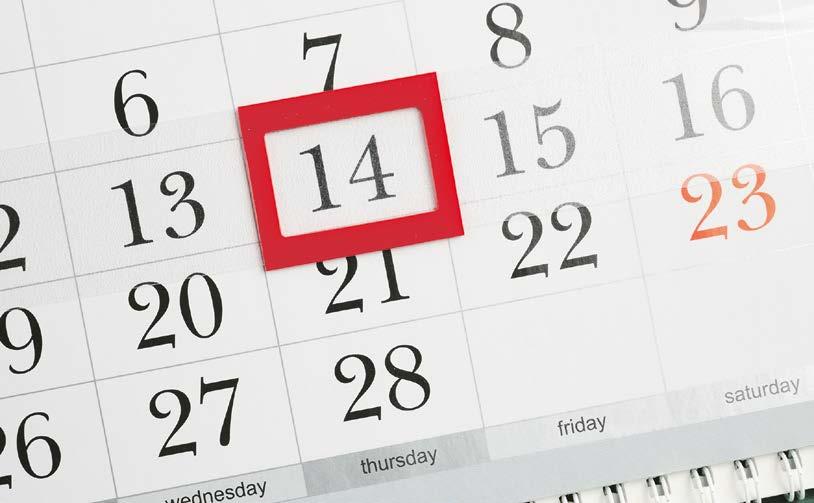
Termine und Online-Kurse
COVID-19 bedingte Änderungen
Es empfiehlt sich, vorgängig beim Veranstalter nachzufragen, ob und wann die Events stattfinden.