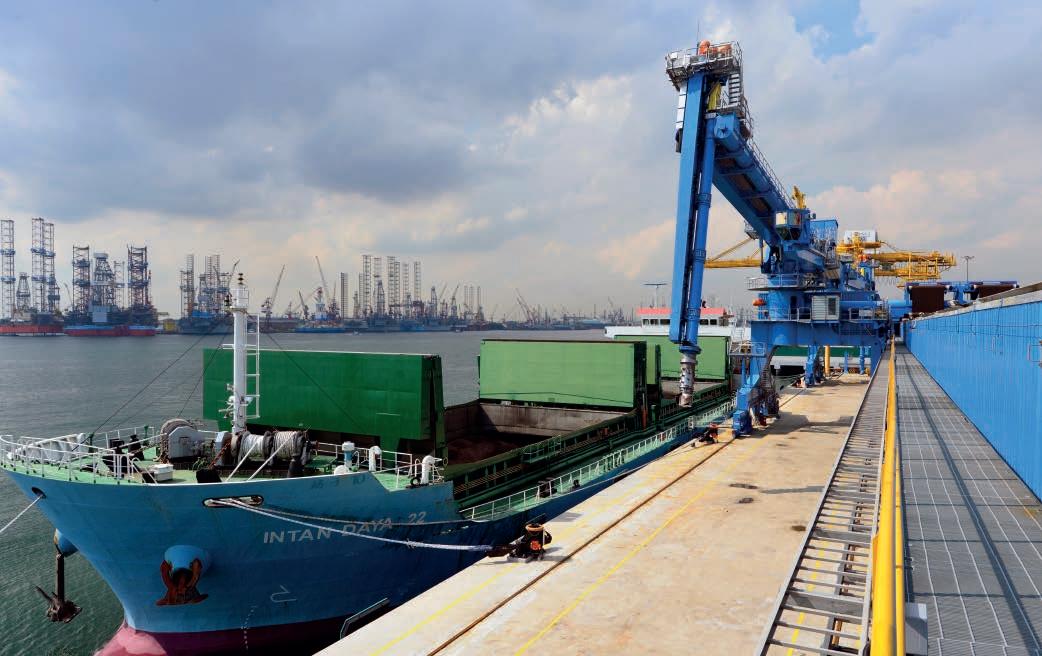
8 minute read
Cost savings delivered through good design
Long-term operational costs are critical to the success of any business, and they can be minimized through good design and continuous development; David Ingvarsson, Sales Manager, Bruks Siwertell explains how
TEXT David Ingvarsson PHOTOS Bruks Siwertell
THERE ARE FEW ELEMENTS IN BUSINESS
that are as important as daily operating costs. They fundamentally impact the profitability of a terminal and can make or break it. It is therefore important that suppliers to industry look to the long-term.
Everything from the number of operators that pieces of dry bulk handling equipment require; the energy that they demand; how quickly they can discharge a vessel and release the jetty; and how much cleaning up the vessel’s holds and jetty requires; all the way through to the life expectancy of consumable parts should be considered. Each of these holds a cost-saving potential that can improve OpEx.
The cost of waste
The ship unloader is a key piece of terminal equipment, and its design and efficiency substantially influence OpEx. For example, by preventing spillage and dust emissions, and therefore the unnecessary loss of cargo, operators minimize waste and they receive all of a shipment. Furthermore, jetty clean-up costs are practically eliminated and the environment is protected. The Siwertell screw-type ship unloader has a totally enclosed operation from its unique counter-rotating inlet feeder up to the jetty belt conveyor. Material enters the vertical screw conveyor from below the surface, minimizing dust creation.
Meanwhile, in comparison, grab cranes and bucket chain-type unloaders always work from the top of the material, and grab cranes can lose up to two percent of a load through spillage. Spillage and dust creation are often the reasons why operators choose to switch to Siwertell unloaders.
A ship unloader’s design and efficiency substantially influences OpEx
DAVID INGVARSSON, SALES MANAGER, BRUKS SIWERTELL
Efficiency drives profitability
Unloading efficiency has a huge impact on OpEx. Bruks Siwertell defines unloading efficiency by comparing the actual through-ship unloading capacity against the rated capacity. For example, a Siwertell screw-type unloader has a very high through-ship efficiency, above 70 percent. Its inlet device has vanes that deliver a filling factor of around 80 percent and its rotational speed is steplessly controlled by the operator to deliver a continuous, effective and efficient unloading profile.
Again, in comparison, the throughship efficiency of a grab unloader stands at around 50 percent. A bucket chain unloader typically has a higher through-ship efficiency than a grab crane, but substantially less than a Siwertell unloader.
The main reason for a grab crane’s lower efficiency is related to its non-continuous operation; its need to travel deeper into a hold as the unloading operation continues; and its lack of flexibility in the hold. The lower efficiency for the bucket chain unloader is also related to its lack of ability to operate in the hold.
The Siwertell unloader’s higher efficiency translates into faster vessel turnarounds and improved jetty utilization rates, increasing the profitability of a terminal. For example, some operators switching to Siwertell unloaders report a reduction in unloading days of 50 percent, translating into a 50 percent reduction in berth occupancy, with returns on investment achieved in less than two years.
Furthermore, because of their higher through-ship efficiency, Siwertell ship unloaders need a lower rated capacity to reach the same average capacity as a grab or bucket chain unloader. This means costs savings on the initial equipment investment, and cost savings on the downstream jetty conveyors, because these can also have a lower capacity. The energy consumption demands of dry bulk handling equipment should also not be underestimated when considering OpEx. Screw-type conveyors have minimal energy consumption demands because of their smooth operating profile and the steady rotation of the screw conveyor.
Capacity cost curves
Higher capacities generally demand higher investment costs, but this varies considerably depending on the type of dry bulk handling equipment specified. For Siwertell technology, it is mainly the maximum ship size to be handled that influences the size and capacity of the unloader.
Taking coal as an example, Siwertell ship unloaders can be delivered with rated capacities of up to 3,000t/h. Capacities for grab unloaders maximize at around 2,000t/h, while bucket chain conveyor-type unloaders are normally limited at a rated capacity of about 2,500t/h.

By preventing spillage and dust emissions, operators minimize waste
Siwertell ship unloaders are lower in weight compared with grab or bucket chain unloaders, so huge cost savings can be made on the jetty as it can be designed for much lower wheel and corner loads. Increasing the capacity of grab cranes and bucket chain unloaders significantly increases their weight, to an unfeasible level in some cases, and therefore the cost of the jetty.
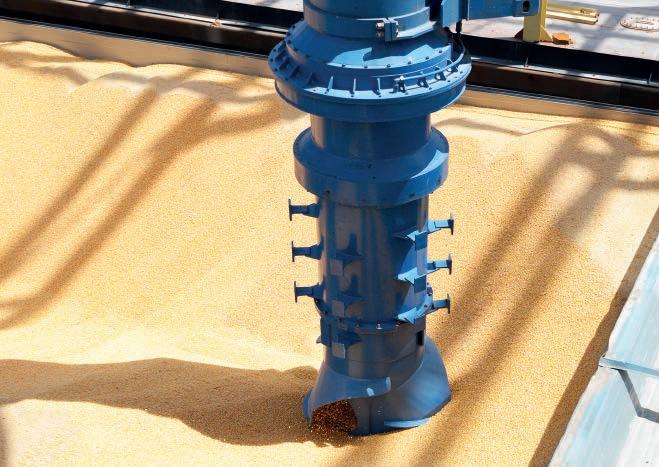
It all adds up
Ship damage impacts OpEx. A grab is often slung to reach under the hatch coamings during unloading operations; a slinging grab is not easy to control, so collision risks are much higher than with a Siwertell unloader.
All Siwertell unloader movements are well-balanced, smooth and controlled. The vertical conveyor arm moves into and around the ship’s holds with minimal risk of collision with the ship’s sides.
The number of personnel needed to operate unloading equipment further influences OpEx. A Siwertell unloader can be operated by one person, either from an operator’s cabin or using a remote radio control on deck. Grab cranes are typically operated by a crane driver in the driver’s cabin, plus additional personnel at the hatch and sometimes one in the hold. A bucket chain-type unloader is often operated by two personnel, one in the cabin and one providing directions from the hold.
OpEx is improved by operational flexibility, including the ability to handle a variety of different materials, even compacted ones. The inlet feeder on a Siwertell unloader can exert digging forces and therefore
The inlet feeder on a Siwertell ship unloader increases the filling factor of the screw by around 80 percent
discharge compacted materials, such as salt. They can also handle virtually any dry bulk cargo. This flexibility opens up opportunities for operators, enabling them to efficiently compete in commercially intensive markets.
Siwertell screw-type ship unloaders have few moving parts, continuous torque loads, and are extremely reliable. They deliver fundamental operational advantages in terms of energy demand, through-ship efficiency, reliability and service longevity and offer an impressive return on investment.
Big impact of small parts
Siwertell unloaders have hundreds of references worldwide and their industry progression and wide installation base enables Bruks Siwertell to have a robust and well-resourced research and development strategy. This ensures that the company leads the market when it comes to the guaranteed lifetime of wear parts, such as screws and tubes for the vertical conveyor. Quality original equipment manufacturer (OEM) components improve OpEx, along with a commitment to continuous development. OEM spare parts benefit from decades of continuous development and are perfectly suited to the equipment.
Screw-type conveyors already provide excellent through-life efficiencies, but securing even lower maintenance costs, and therefore significantly improving OpEx through another technical route, is part of Bruks Siwertell’s service commitment. A recent R&D program, specifically designed to see if it was possible to extend the lifetime of the screw conveyor, concluded in early 2022.
Grain is the third largest cargo that Bruks Siwertell machines handle and this sector was taken as the program’s core segment for analysis. This was for several reasons, dry bulk handling equipment in this industry is operated very intensively, handling huge surges in demand as a result of the seasonality of crop harvests. Operations are often
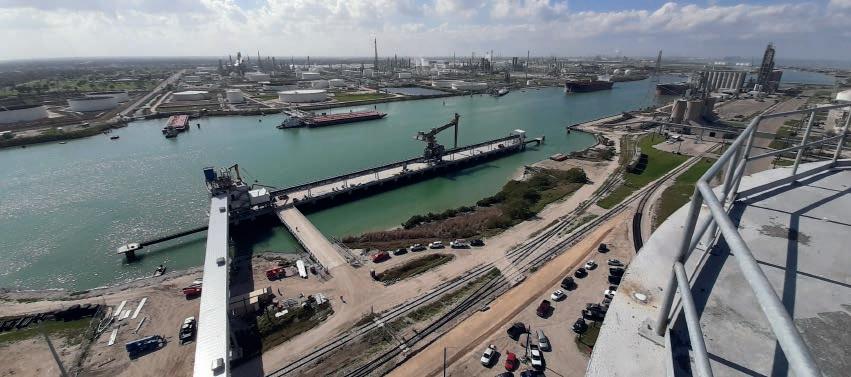
Siwertell ship unloaders are low in weight, so huge cost savings can be made on the jetty
located in remote terminals so maintenance and spare parts availability are critical, and unplanned downtime is unacceptable. It is also an extremely competitive market that places substantial expectations on component lifetimes and through-life costs.
For this industry, Bruks Siwertell has Siwertell screw-type ship unloader references that discharge grain and other agri-bulk commodities at rated capacities of up to 1,800t/h and ship loaders that offer continuous rated capacities in excess of 3,000t/h.
With a lot of experience in this sector, and many customers that could benefit from through-life cost savings, the program, therefore, researched if it was possible to stretch component lifetimes while maintaining cost awareness, along with increasing maintenance intervals, decreasing supply lead times and the need to replace spare parts. It also included analyzing component materials and the production methods of vertical transport screw components.
Drive best practice
The results reveal that permitting a five to ten percent increase in component cost can triple the service life of vertical screws, and that the improvement of lifetimes of vertical screws contribute to around a 30 percent lower total operational cost per 1,000 metric tons or per hour over five to ten years.
These positive results are applicable to Bruks Siwertell’s entire portfolio of new and existing screw-type equipment including all transport screws on Siwertell ship unloaders, loaders and conveyors. The findings are so convincing that Bruks Siwertell will also implement them as best practice in future product development projects.
When all factors are combined it is clear to see how technology, design and ongoing research deliver routes to improved OpEx, which, collectively, can have a significant impact on the profitability of a terminal. As operators expect decades of service from their dry bulk handling equipment, the projected OpEx of any investment should be considered from the outset.
Our research and development strategy ensures that Bruks Siwertell leads the market when it comes to the guaranteed lifetime of wear parts
DAVID INGVARSSON, SALES MANAGER, BRUKS SIWERTELL