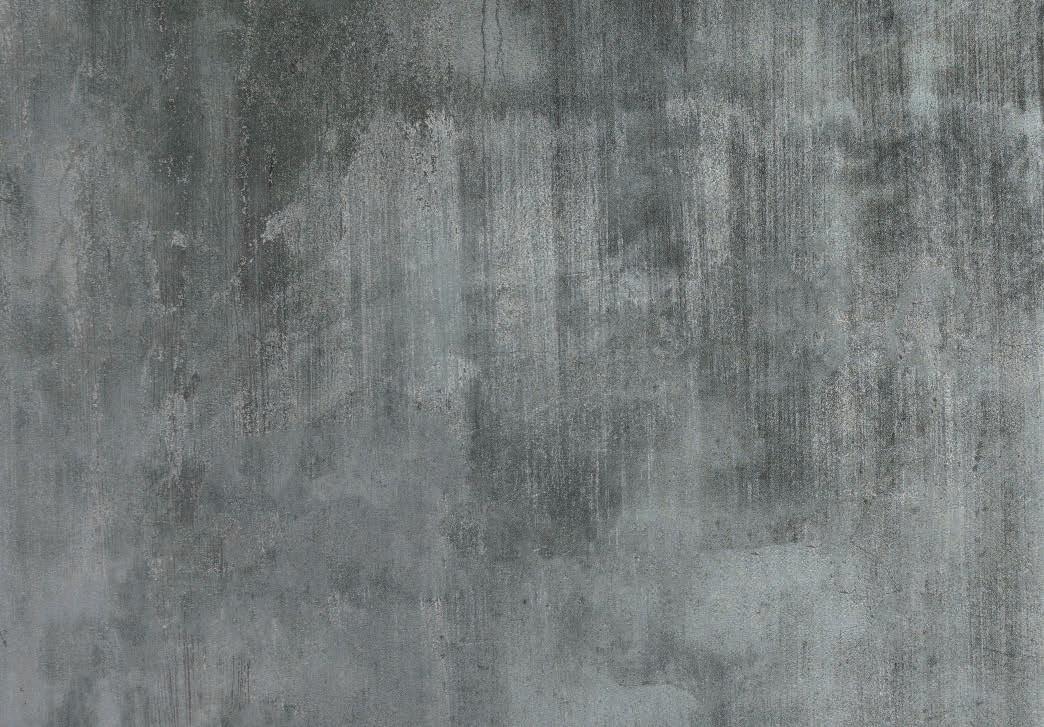
8 minute read
A concrete commitment
As the US embarks on a drive to improve its infrastructure, various companies equip themselves with enclosed Siwertell ship unloaders to assist with the growing demand for cement
TEXT Ken Upchurch PHOTOS Bruks Siwertell, Shutterstock
IN NORTH AMERICA, INFRASTRUCTURE IS A BIG DEAL. While there are enormous cities throughout the United States (US), the population, in general, is far more spread-out across suburbs and rural communities. Of the top ten biggest cities in America, just four have over two million people. Compare this with Paris, Europe’s tenth biggest city, with 2.1 million; or Wuhan, China’s tenth largest, with 7.9 million.
This ‘sprawl,’ as it is known, places an outsize importance on infrastructure for getting people from one place to another. There is a reason that the Pacific Coast Highway and Route 66 are so iconic; in the US, the open road is the main way of getting around, and trucking is the main method of getting goods around, as well.
In the 1950s and 1960s, building new roads was considered a national defense matter; the 1956 National Interstate and Defense Highways Act enshrined into law the importance of highways for evacuating cities and deploying troops, and set off the largest public works project in the history of the country. Those highways and bridges were built to last, and last they have; today, most of a century later, they are still standing. But in many places, American infrastructure is reaching or has even exceeded the end of its life; and to make matters more complicated, it is now having to contend with extreme weather events its builders could not have known about or planned for.
In recognition of this, announced in July 2021, the US’ Bipartisan Infrastructure Law allocated USD 110 billion for repairing and upgrading roads and bridges, USD 50 billion in ‘weatherization’, and interestingly, also invests USD 66 billion for building and upgrading rail lines.
There is one thing that is needed to support all this work: concrete. The US uses a great deal of cement every year; around 103 million metric tons of it as of 2019. The vast majority of this material is provided by domestic
producers; in 2019, 89 million metric tons of concrete was produced domestically, with around 15 million metric tons, or 14 percent, imported. According to a 2021 report authored by PEC Consulting Group and PENTA Engineering Corp, many domestic plants have been closed due to lower costs for imported cement combined with concerns over pollution, but those that are open are now reaching capacity.
If the US is to embark on a massive spree of infrastructure renewal, then, it will need more cement than domestic producers can provide. If America’s ports are to make intelligent decisions about what sort of additional capacity to provide, they must examine the global stateof-the-art in handling of cement and clinker. Fortunately for them, they will not have to look far.
A high bar
Siwertell screw-type technology has a worldwide reputation for high-capacity, environment-friendly cement handling. Almost since the very beginning of the Siwertell brand, the cement handling industry has taken advantage of the totally enclosed conveying lines that Siwertell screw-type ship unloaders offer.
The first Siwertell ship unloader was delivered to the cement industry in 1975, with today’s unloaders able to reach continuous rated capacities in excess of 2,000t/h. The US has numerous, long-standing references for Siwertell unloaders, including a pioneering delivery in 2006 to Houston Cement Company, in Houston, Texas. The operator could sell more cement than it could

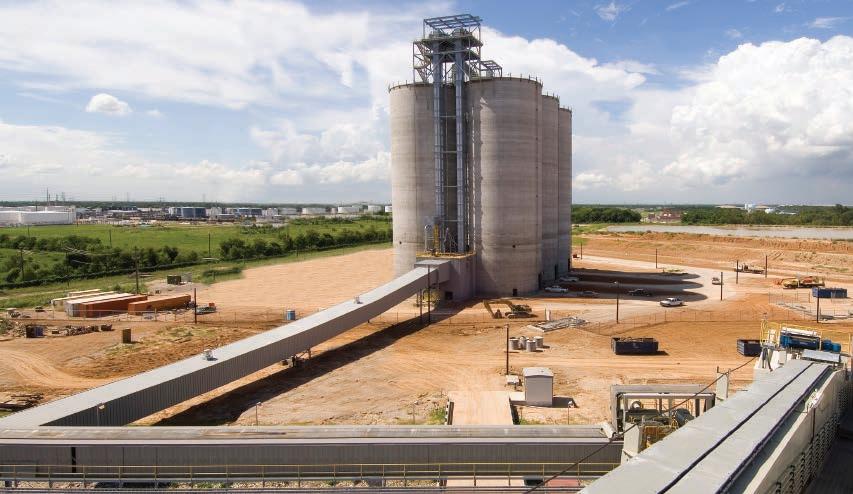
Enclosed dry bulk material conveying ensures no dust emissions or spillage
import and needed to replace an existing pneumatic ship unloading system. It ordered a rail-mounted Siwertell ST 640-D unloader, which delivered cement unloading rates of up to 1,500t/h, setting a new world record at the time.
Its high-capacity capabilities meant a reduction in unloading days of 50 percent, translating into a 50 percent reduction in berth occupancy and the possibility of higher annual intakes; return on investment was achieved in less than two years. The unloader has now handled more than 10 million metric tons of cement.
Now standard, the unloader was also one of the first to feature an auto level mode, which ensures peak efficiency by keeping the vertical conveyor’s counterrotating inlet feeder at an optimum level; not digging too deep, or too shallow.
The Houston Cement Company order was a catalyst for many more Siwertell cement handling ship unloader orders in the US, most recently received is a new Siwertell 490 M-type ship unloader contract for the cement and ready-mix concrete producer, ARGOS USA. It offers a continuous rated capacity of 800t/h and is designed to accommodate vessels up to 65,000 dwt. The unloader will be assembled on site and is planned for delivery in February 2024.
Cleaner, higher capacities
Also in Houston, Sesco Cement elected to make a transition under consideration by a number of operators to boost import volumes; switching from bagged to bulk cement. Sesco Cement chose a Siwertell ST 640-M ship unloader for the task at its new import terminal.
Commissioned in 2020, the unloader handles cement at around 1,500t/h, discharging vessels of up to 80,000 dwt. “In performance tests after installation, the ST 640 M-type unloader handled cement at a throughput of up to 1,650t/h,” says Ken Upchurch, SVP Sales and Marketing, Bruks Siwertell. “Since making the switch from bagged to bulk material, the port has experienced a complete step-change in efficiency.”
Other US facilities to benefit include Colonial Group’s Georgia Kaolin Terminals, in Savannah, Georgia, with the completion of a new high-capacity Siwertell ship unloader installation.
Ordered to support the company’s strategy for sustainable cement import growth, the Siwertell 490 F-type ship unloader offers high through-ship efficiencies and a rated cement handling capacity of 800t/h, discharging vessels up to 55,000 dwt.
This was another company that was looking to transition from bagged to bulk deliveries of cement, significantly increasing the terminal’s unloading capacity, which in turn delivers faster vessel turnarounds on the jetty, and with that, cost-savings.
Environmental considerations were also a key factor in Colonial’s choice of equipment, and because the Siwertell unloader has an enclosed dry bulk material conveying line, ensuring no dust emissions or spillage, it is permitted to operate within this historic port and complies with its strict environmental regulations.
Containing the clouds
These units serve as effective showcases of all the features that make Siwertell unloaders ideal for handling cement. One of the most important is the mitigation of dust emissions, which is a serious issue for many powdery cargoes, but particularly for cement. Cement is formulated to react with water, cure and solidify, making it detrimental to health when breathed in and negatively impacting the environment.
“People who have worked on a building site, or lived or worked near one, will likely be familiar with yellowish clouds of cement dust; the reason why construction workers wear masks when handling it,” explains Upchurch. “Moving cement is only a part of the operation in these places.
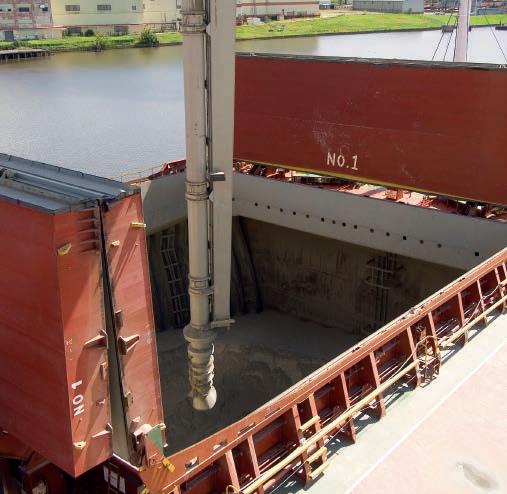
Houston Cement Company’s Siwertell ST 640-D unloader delivers unloading rates of up to 1,500t/h
“Now imagine a facility where unloading, storing, and moving cement around is the entire point, and you can see why we must place such an emphasis on protecting the environment from the effects of dust.
“In this context, it is not difficult to see why the continuous, enclosed handling offered by Siwertell technology is preferable to open handling,” he notes. “Once the rotating inlet feeder is submerged beneath the material’s surface, the system is fully enclosed, with cement only moving inside the unloader’s conveyor system.”
KEN UPCHURCH, SVP SALES AND MARKETING, BRUKS SIWERTELL
Opportunities galore
It is not only large-scale systems that are needed. In 2020, Bruks Siwertell delivered a Siwertell 5000 S road-mobile ship unloader to US operator Ozinga, following an investigation by the company into the best cement handling technologies available.
Ozinga needed a piece of equipment that would help it answer vessel calls with high throughput, but also be able to redeploy and move to where it was needed. As well as being able to deploy and repack within an hour, the system can handle large volumes of cement for its compact size. The dust filters on the Bruks Siwertell unloader add an extra layer of certainty against dust emissions.
Ozinga specializes in concrete, dry bulk materials, and natural gas energy solutions, and has an extensive network of truck, rail, barge, and ship terminals. Its operations are predominantly focused in the US Midwest, where the new ship unloader is making its mark, delivering a continuous rated unloading capacity of 300t/h for vessels up to 5,000 dwt.
The trailer-based, diesel-powered system is fitted with dust filters and a double-bellows discharge arrange-
In the US, the cement market is huge right now
KEN UPCHURCH, SVP SALES AND MARKETING, BRUKS SIWERTELL
ment with an automatic shifting function. It features advanced digital technology for diagnostics and troubleshooting as well.
Advanced digital capabilities are also included on a pair of new 5000 S Siwertell road-mobile ship unloaders destined for an undisclosed US operator. They will provide a flexible, environmentally friendly solution for unloading cement at planned future sites in the US Midwest and Southeast, enabling better access to barges and port facilities.

Siwertell road-mobile ship unloaders are offering a flexible solution to cement handlers in the US Their commissioning is due for completion later this year, and to reduce environmental impact even further, will have electric as opposed to diesel-drives.
These and many others offer clear signs that the US’ infrastructure renewal drive is already stimulating demand. “In the US, the cement market is huge right now,” Upchurch says. “We have systems operating all across North America, so it is not surprising that terminal operators have heard of our technology’s capabilities. But to be able to help terminal operators bring online the most efficient, clean, and high-capacity systems, at a time when this is sorely needed – and ultimately, to be part of helping America to rebuild itself – what an opportunity!”