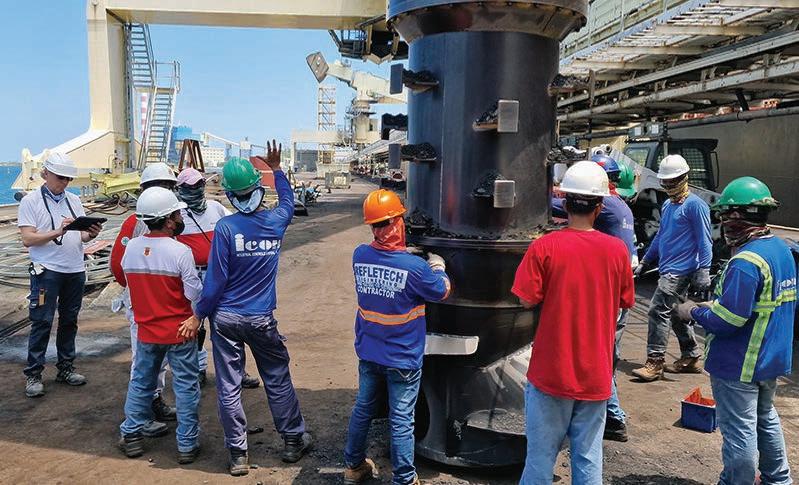
4 minute read
News in brief
NEWSIN BRIEF
Digital advances enhance service support
In a collaboration with Swedish information technology specialists, Pulsen Integration, part of Pulsen Group, Bruks Siwertell has adopted an app-based system called digital report tool (DRT). It streamlines service reporting across Bruks Siwertell’s market-leading range of dry bulk handling equipment and ensures that customers receive expert knowledge quickly and efficiently.
With the new app, Bruks Siwertell’s service teams have access to the most efficient, comprehensive and consistent method of report creation. “The incorporation of this digital advance creates a fully accessible platform that promotes rapid knowledge transfer and even better customer service,” says Daniel Frostberg, Service Director, Bruks Siwertell.
A new digital report tool ensures that customers receive rapid, consistent reports
“We have an extensive equipment inspection portfolio, where each machine is meticulously checked on a regular basis. This work is carried out at installations all over the world and by many different surveyors. Streamlining this process delivers a cohesive quality and saves our service teams an enormous amount of time,” explains Frostberg.
Previously, inspectors used a variety of reporting methods, which could prove time-consuming to produce the final report. Inspectors now fill in all the applicable fields, take pictures and then create the report with one click.
US mill modernization underpinned by Bruks technology
A leading American paper and packaging supplier will shortly take delivery of a new woodyard designed to modernize its southern USA mill.
The new complete woodyard includes a package of Bruks technology such as a back-on truck dumper, a 127,425m3 (4.5 million ft3) fully automated circular blending bed stacker reclaimer (CBBSR), a bark screening and processing system, and a complete conveyor package feeding from the chipping line to the existing screen building.
It has a capacity to deliver 800t/h of wood chips from the chipping line and truck dumper to the stacker reclaimer, and wood chips at 400t/h from the stacker reclaimer to the processing plant.
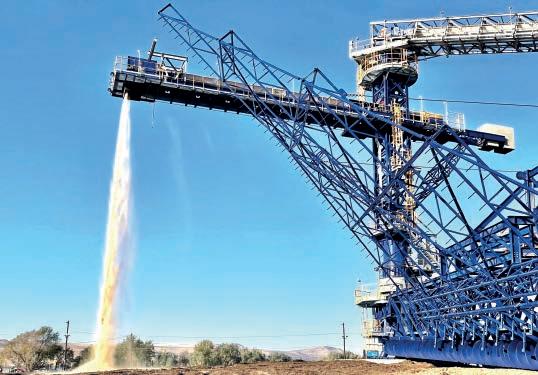
A fully automated Bruks circular blending bed stacker reclaimer (CBBSR) is included in the order
“The new storage and reclaiming system is fully automated, replacing mobile equipment with a safe, highly efficient, and environmentally friendly solution,” says Christopher Duffy, Sales Manager, Bruks Siwertell. “Our automated stacker reclaimers have a fraction of the carbon footprint of a manually managed pile, and offer much improved dust mitigation.”
Enclosed cement handling system ordered for Adelaide
Hallet Capital Pty Ltd has placed an order for a gantrymounted Siwertell 490 F-type ship unloader. It will provide environment-friendly cement handling in the South Australian port of Adelaide. The unit has been ordered along with a jetty screw-conveyor system feeding a dome silo and individual screw conveyors for installation inside the dome.
“Hallet Capital is a new customer for us, and part of its decision to choose Siwertell technology was based on Bruks Siwertell’s extensive experience with other cement import terminals,” says Jan Karlsson, Sales Director APAC, Bruks Siwertell. “There were two main considerations for this contract,” notes Karlsson. “The first was environmental protection and the second was designing a system that could be moved away from the jetty when not discharging vessels, as the port of Adelaide does not allow any fixed installations to hinder other operations within the port. We were able to meet both.
“The ship unloader will be fitted with a rubber-tire wheelbase ensuring in-port mobility,” he explains. “Furthermore, the jetty conveyor system will be installed in a recess so that the jetty remains clear for other activities. The entire system, from material pick-up in the vessel’s hold to the dome silo, will be totally enclosed, providing a virtually dust-free operation in the port, with no spillage.”
The new Siwertell ship unloader will be suitable for discharging bulkers up to 40,000 dwt at a rated cement handling capacity of 500t/h. It is planned for delivery later this year and will be assembled on site.
Siwertell Smartview delivers expert knowledge direct to operators
This year, Bruks Siwertell will start rolling out the introduction of an advanced digital tool, Siwertell Smartview. Designed to optimize the productivity and profitability of dry bulk handling operations, and deliver a better understanding of components through enhanced data analysis, the cloud-based tool is the latest industrial Internet of things (IIoT) system planned for integration into Siwertell technology.
Siwertell Smartview is suitable for all Siwertell ship unloaders, including port-mobile and road-mobile units, and ship loaders. For more information see page 12.
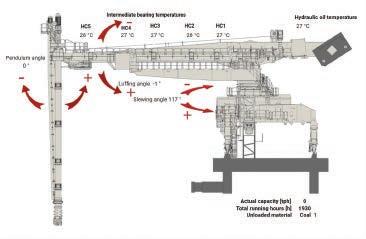
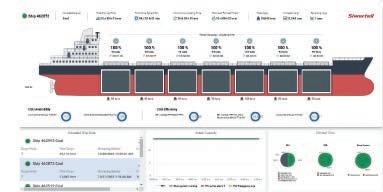
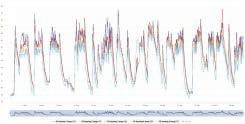
Siwertell Smartview delivers a better understanding of an operation through enhanced data analysis
Siwertell loader secures cement capacity growth for Indonesian operator
A Siwertell screw-type ship loader has been ordered by engineering, procurement, and construction (EPC) contractor, PT Hutama Karya (Persero), for cement handling operations in Tuban, on the Indonesian island of Java. It will secure dust-free material transfers for the state-run operator, PT Solusi Bangun Indonesia. “Environmental protection was a key concern for all parties, and one of the main reasons why this loader, with a totally enclosed screw-type conveying system, was chosen,” says Pierre Öhrwall, Sales Manager, Bruks Siwertell. “It will ensure efficient, high-capacity cement handling free from dust and spillage.”

PT Solusi Bangun Indonesia specializes in cement, ready mix concrete, and aggregate production. The Tuban terminal is a strategic new expansion, close to Indonesia’s limestone mines, and established maritime routes. It is also the operator’s first completely new terminal construction.
The HST 1000 1B-type ship loader has a continuous cement handling capacity of 1,000t/h and can load either open-hatched or conventional bulk carriers up to 50,000 dwt. It will be assembled on site and is planned for delivery at the end of 2023.