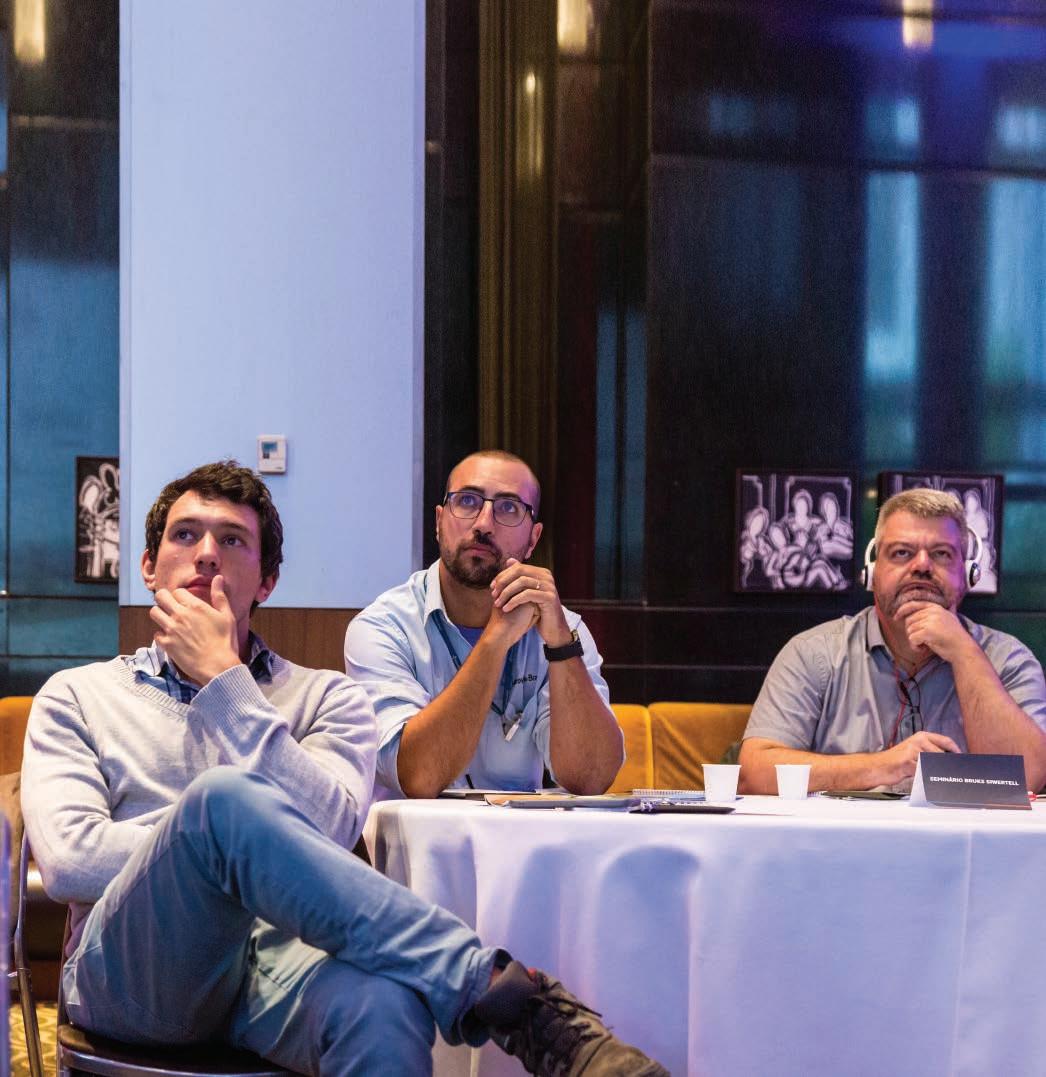
8 minute read
Bulk Days: connect, share, repeat
It is vitally important that we regularly reach out to operators to share developments, listen to feedback and provide a platform for face-to-face connection; the pandemic stalled these interactions, but now they are back
TEXT Patrik Henryson PHOTOS Bruks Siwertell
‘BULK DAY’, AS IT HAS BECOME AFFEC-
TIONATELY NAMED, is now a regular knowledge-sharing and networking event, held at least once a year in different countries. Organized by Bruks Siwertell and repeated twice last year as a result of popular demand, it is designed to set aside dedicated time to meet operators, port representatives and engineering companies from all over the world, and provide a platform for connection. With plans underway to repeat the event in Mexico this year, last year’s two Bulk Days were held in South America. The first in May in Rosario, Argentina, and the second in October in São Paulo, Brazil.
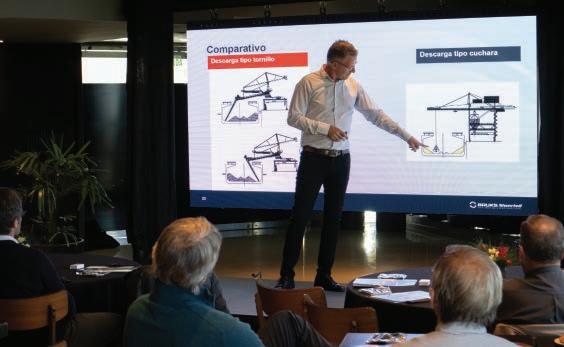
Presentations showed how Siwertell ship unloaders can deliver operational advantages Jönsson, Key Account Manager, who discussed aftersales and service, and Björn Ohlsson, Senior Contract Manager, was invited to present a fertilizer handling project.
“Bulk Days are a good way to deliver regional insight,” Henryson continues. “Not only does Bruks Siwertell get to understand more about local markets and operations, operators get to take advantage of regional expertise and connections.”
Tough seasonal schedules
Encouraging industry dialogues
“Our customers know their operations best, and events such as Bulk Day allow for the free exchange of ideas and technology updates. The information shared is beneficial to all parties,” explains Patrik Henryson, Sales Manager Latin America and Caribbean, Bruks Siwertell. “Operators can use the platform to feed back, not just about the equipment, but about the industry as a whole, right down to discussing niche site- or material-specific issues and challenges with our dry bulk handling experts. We are also able to update operators with any technology advances or simply be there to facilitate industry dialogues between stakeholders.
“The formula for connecting with stakeholders, sharing information, and making a commitment to continue to do so is a simple, but effective one. Both events generated lively discussions about specific case studies and equipment capabilities. Stakeholders were engaged, we were able to share insight and we even received several inquiries, including further interest in our air-cushion conveyors,” Henryson notes. “We could not have asked for more; they were great.”
In both Argentina and Brazil, each event was attended by around 30 invited participants. In Rosario, Argentina, the day was hosted by Patrik Henryson, along with Bruks Siwertell representatives, Julian Luna from South Point Engineering, Argentina, and Leonardo Lemgruber from Brazil, who was invited as a special guest to discuss barge unloading operations in northern Brazil, on the banks of the Amazon River. South America sees some of Bruks Siwertell’s busiest customers. “We have Siwertell ship unloaders that operate to incredibly tight schedules on a year-round basis,” Henryson explains. “For example, in Brazil, Siwertell installations regularly operate up to 4,000 hours/year handling grain, soya bean and soya meal. These systems work under very high use conditions and meet extremely tough seasonal schedules.”
In São Paulo, Brazil, the event was organized by Leonardo Lembgruber, and Per Hansson, Sales Director, Bruks Siwertell, took the helm. Other Bruks Siwertell personnel were on hand, including Mats
Mats Jönsson, Key Account Manager, Bruks Siwertell
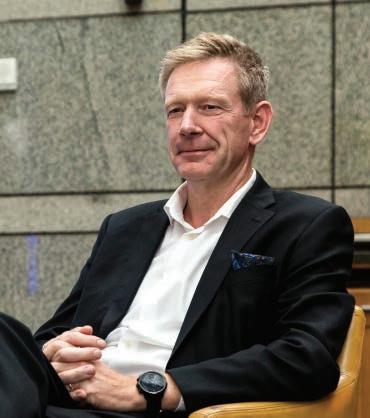
Siwertell screw-type ship unloaders can discharge grain and other agribulk commodities from vessels up to 230,00dwt at rated capacities up to 2,400t/h, and loaders deliver the market’s highest continuous rated capacities, which are in excess of 3,000t/h. For other dry bulk materials, unloading rates can be as high as 3,000t/h and loading up to 12,000t/h for iron ore, discharging vessels up to 300,000 dwt.
Like Brazil, Argentina is also a significant agricultural hub, and ranks as one of the top five wheat producers in the world. Exports are big business for Argentina, with the South American country exporting over half of the crops that it produces, and in addition to wheat, these include soya beans, corn, barley, rice, flaxseed, sugarcane, and cotton.
A resonating theme for both events was the importance of servicing machinery and reliability. In Brazil, Mats Jönsson was able to present customer case studies that highlight how the timely, regular service of Siwertell ship unloaders in Brazil, for example, enable them to remain competitive and also be relied upon to handle one year’s full intake of grain.
It was also noted that many Siwertell operators do not have any other equipment to unload incoming material, so planned maintenance stops are critical.
Both sides of the coin
The other side to handling grain, is handling the fertilizers needed to grow it. The Bulk Days allowed for Bruks Siwertell to demonstrate its capabilities in this arena as well, explaining that Siwertell unloaders can do this very efficiently and safely, given the volatile nature of fertilizers as a cargo.
One example of a fertilizer handler in Glomfjord, Norway, was presented. This particular operator was

Björn Ohlsson, Senior Contract Manager, Bruks Siwertell
replacing a Siwertell ship unloader that had been in service for more than forty years with a new one. The operator needed an environmentfriendly solution, which minimized dust, spillage and material degradation when handling various types of fertilizer, at a capacity of 600t/h.
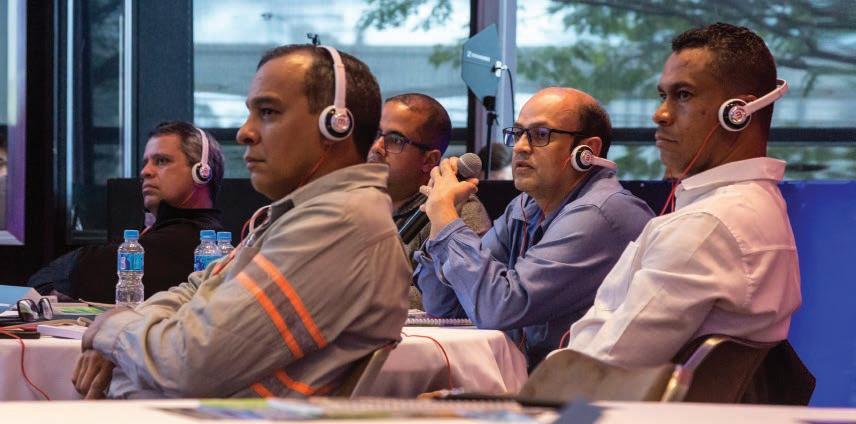
The events generated discussions about specific case studies and equipment capabilities
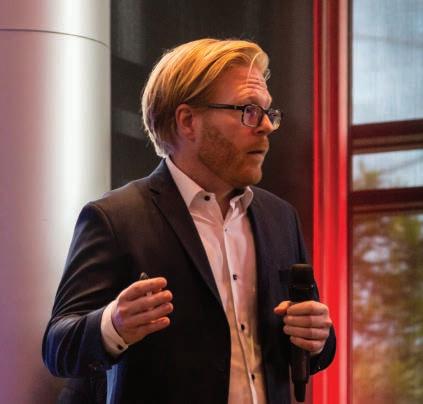
Per Hansson, Sales Director, Bruks Siwertell
PATRIK HENRYSON, SALES MANAGER, BRUKS SIWERTELL
Other presentations included information about the significant benefits Siwertell technology can deliver to the alumina market from a steady conveying velocity that minimizes any material degradation. This highlighted just some of the advantages that Siwertell technology can deliver to specific dry bulks.
Continuous improvements
Another key message that Jönsson was able to share was the significant advances delivered by an innovative research and development (R&D) program, which was completed in 2021. It targeted improving the lifetime of the vertical screw conveyor and its component parts.
The grain handling market was taken as the program’s core segment because, as an industry, it has to meet some of the most challenging conditions, with dry bulk equipment exposed to huge surges in demand. Ship unloaders have to consistently deliver high capacities for maximum profitability, but also maintain the quality of shipments through sensitive handling. It is also an extremely competitive market that places substantial expectations on component lifetimes and through-life costs.
Jönsson noted that by significantly improving the service life of wear parts, customers save money on through-life maintenance, without increased investment costs. Parts last longer between wear intervals, which saves money and benefits the environment.
The continuous development of the Siwertell ship unloader’s unique inlet feeder was also discussed. When introduced, the counter-rotating device increased the fill factor of the screw conveyor by at least 30 percent. It continues to undergo incremental design improvements to increase the utilization of the screw conveyor even further in the most energy-efficient way.
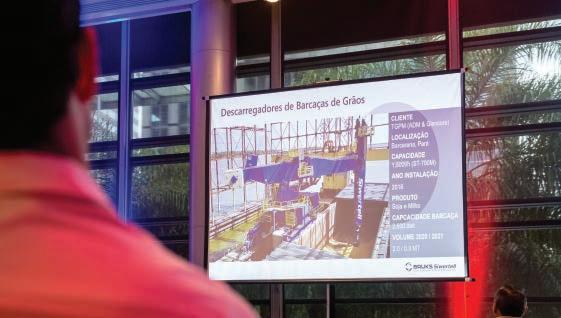
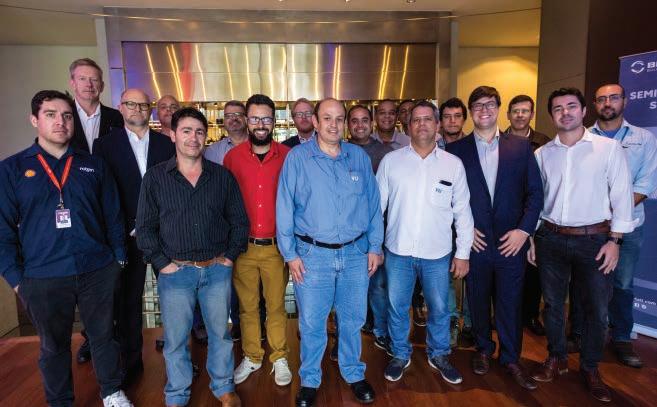
In both Argentina and Brazil, Bulk Days were attended by around 30 invited participants
Unloaders have automatic regulation to ensure that unloading is being carried out at the right capacity and not overfilling the jetty belt. “The screw transports the material, but the inlet feeder sets the capacity,” explains Henryson. “The whole system is designed to achieve a steady, reliable discharge rate, regardless if at 20 or 100 percent speed.”
Several different inlet feeder solutions are available, depending on the commodity handled. These can include different drive technologies such as hydraulic or electric, which are all adjustable so that the operator can optimize capacity control. Also, different designs are available for handling compacted materials. For example, high humidity and lengthy transportation times, mean that some commodities, such as salt and fertilizers, form a hard crust in the hold, which requires equipment to withstand digging forces.
The imminent phased introduction of the new digital tool, Siwertell Smartview, was also revealed. It is the latest industrial Internet of things (IIoT) system planned for integration into Siwertell technology. Developed as part of an ongoing research and development (R&D) project, it is designed to optimize the productivity and profitability of dry bulk handling operations, and deliver a better understanding of components through enhanced data analysis.
Like the longer-life screw, Siwertell Smartview will be applicable to Bruks Siwertell’s entire portfolio of screw-type equipment including Siwertell ship unloaders, loaders and conveyors.
Practical solutions explained
Anti-collision systems were also discussed. Siwertell unloaders minimize dust in the hold because of their layer-by-layer unloading principle, optimizing unloading efficiency, and avoiding deep trenches in the hold and therefore the potential for material avalanches. However, limited visibility, as a result of dust, particularly in windy conditions with powdery materials, is sometimes problematic.
Dust makes it impossible to use traditional lasers for anti-collision systems. Furthermore, some operators use a water mist over the hatch, due to a zero-emission tolerance, which also makes lasers impossible to use.
To overcome these issues, the Siwertell anti-collision system uses specialist software integrated into the unloader’s programmable logic controller and human machine interface, along with features such as 3D-scanners that analyze the material surface, 2D sensors for anti-collision data, and GPS sensors as well. The whole system can be integrated into traditional close circuit television screens.
The anti-collision system will prevent the Siwertell unloader’s vertical arm and the horizontal arm colliding with the ships hatch coaming. It is manually activated and deactivated through the radio remote control or from the cabin, and will start to reduce the speed of the motion when the operator is getting close to the hatch coaming, or stop completely if too near.
“Every presentation delivered a valuable opportunity for discussion, showing that events like Bulk Days are some of the most important platforms for networking between customers, representatives and industry experts. We value and appreciate the time that operators spare to attend them, and very much hope that they gain as much from them as we do,” Henryson concludes.