
10 minute read
OPINION
CUT THE CORD >
THE BENEFITS OF GOING CORDLESS
Writing for Torque Magazine, Kevin Brannigan, Marketing Manager at Makita UK, explains the key features and technology of the latest cordless power tools and how these help distributors to meet the needs of their customers…

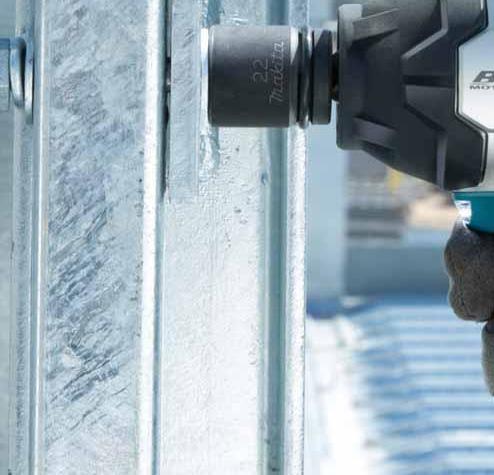
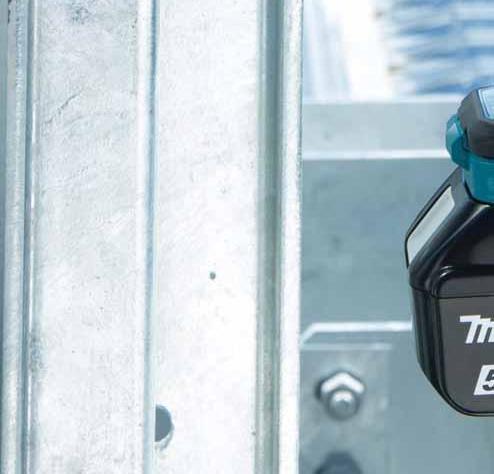

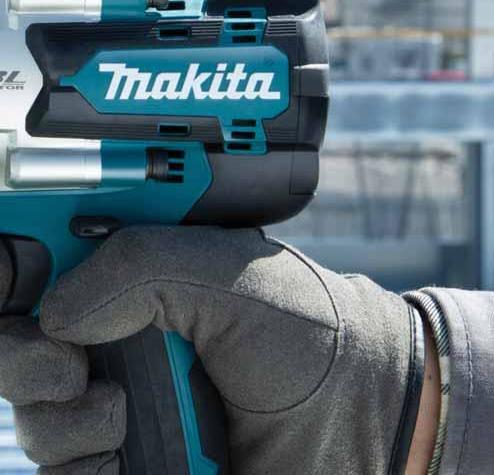


Tools featuring brushless motors offer reduced fatigue for users too
All Makita cordless power tools are driven by one of three battery platforms
Cordless tools have become the product of choice for many customers and for a range of applications due to the benefits they offer. Cordless tools allow users to work safer, quicker and more flexibly. By removing the need to carry transformers or locate a power source and get that power to the work area, cordless reduces the amount of set up time. Also, if not managed correctly, the cables can become a trip hazard so this risk is eliminated with battery powered tools along with the time required to plan and manage the safe placement of the cables. There was traditionally a trade‐off with cordless tools as they were generally less powerful than petrol or corded alter‐natives. However, advances in battery and motor technology in recent years has meant that these tools now offer compa‐rable power and performance, with a growing number being suitable for high‐demand applications. One of the key innovations has been brushless motors. Due to their design, brushless motors do not create friction, limit‐ing wear and tear and reducing the energy wasted through heat production. As a result, they have greater efficiency and produce more torque per weight. This means that less power is required to achieve the same result and extends run times by up to 50% on each battery charge. Brushless motors also have reduced maintenance requirements, saving time and on‐going expenditure. Tools that feature brushless motors can also be lighter and more compact compared with their brushed motor equivalents. This can make a significant difference to those operating the machines as they will be more comfortable to use and muscle fatigue will be reduced. Another factor that is worth advising customers on when they are investing in new tools is the battery platform. Choosing a brand that has a wide range of tools that use the same batteries can be a significant advantage. It improves the user’s productivity as it is easy to swap batteries between various tools as required. It also simplifies the equipment needed on site as one type of battery and charger can be used. It also makes buying new tools simpler with customers invested into one family system of tools. For example, all Makita cordless power tools are driven by one of three battery platforms: the 12VMax CXT, 18V LXT or 40VMax XGT. The LXT batteries can be used on more than 270 different products, including the Twin 18V machines that use any two LXT batteries to produce 36V power, representing huge sales poten‐tial for distributors. For distributors, understanding the benefits of the latest cord‐less tools is important. By helping customers to choose the right products on a versatile battery platform can help them work more efficiently and use their capital more effectively. To find out more about the Makita range of cordless tools visit
www.makitauk.com

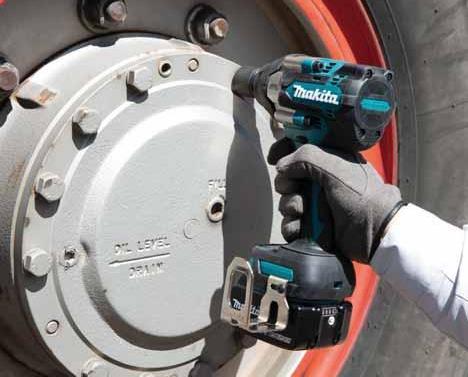
// Brushless motors have been one of the key innovations, limiting wear and tear while reducing wasted energy through friction. //
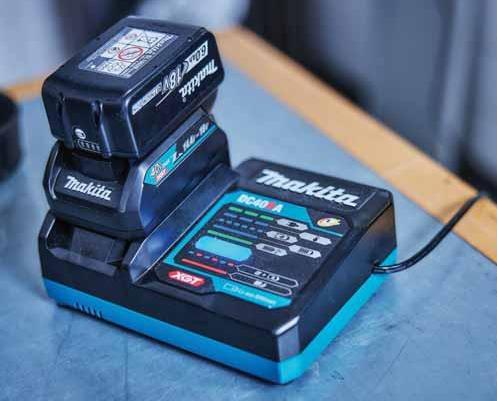
A fresh set of fixings
From new products to fresh services: Torque Magazine rounds up a flurry of new year announcements from the fixings giant…
FIS V PLUS –LASTING SAFETY FOR GENERATIONS
fischer has launched what it believes is the market’s first universal injection mortar with an evaluated service life (ETA) of 100 years in concrete, the FIS V Plus. In addition to a long service life, the latest generation of fischer’s universal mortar increases the composite strength in concrete by up to 45% with an expanded range of applications. FIS V Plus applications include fastenings in concrete and masonry, post‐installed rebar connections, water‐filled drill holes as well as seismic applications in performance categories C1 and C2 or A and B according to the ICC‐ESR. The universal mortar can also be used with low edge and axial spacing. Numerous system components allow specialist applications with a general technical approval.
fischer FIS V Plus is a universal injection mortar with an evaluated service life of 100 years in concrete
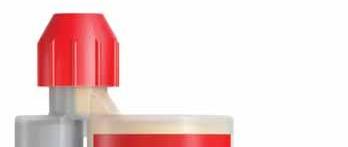
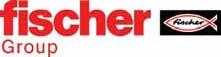
fischer’s revamped ‘Fixperience’ design software DUOSEAL – SECURE FASTENINGS WHILE RELIABLY DRILLING HOLES IN WET AREAS
The DuoSeal plug is also among fischer’s product launches. Together with the accompanying stainless‐steel screw, the DuoSeal guarantees watertightness in accordance with ETAG 022 and the DIN 18534 standard up to the W3‐I water expo‐sure class (for the German market the DuoSeal is only recom‐mended up to water exposure class W1‐I). The plug is also suitable for tiled surfaces and can be securely installed in solid, perforated and panel construction materials.
DIGITAL FISCHER SERVICES FOR TRADESPEOPLE
And it’s not just new products; fischer has been hard at work developing new digital services for tradespeople on the construction site. The fischer Professional App provides access to information and advice on fischer’s fixing technology from anywhere, at any time. Offering a product advisor (and options to complete a purchase online or in‐store with an associated retailer), users can intuitively find any information needed on the world of fischer fixings and even chat directly with application engineers. Tradespeople effectively get a mobile fixings consultant with them at all times on site and can manage fixings tasks through their smartphone. The new installation protocol function within the fischer Professional App makes it faster and easier to correctly document fastenings with just one touch. The free and practical tool allows post‐installed rebar connections and all other fastenings to be captured digitally before being sent via PDF function. This signif‐icantly increases the level of safety and efficiency when docu‐menting fastenings compared to manually filling in protocols.
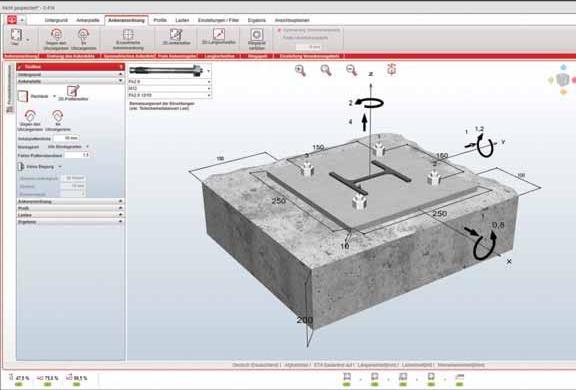
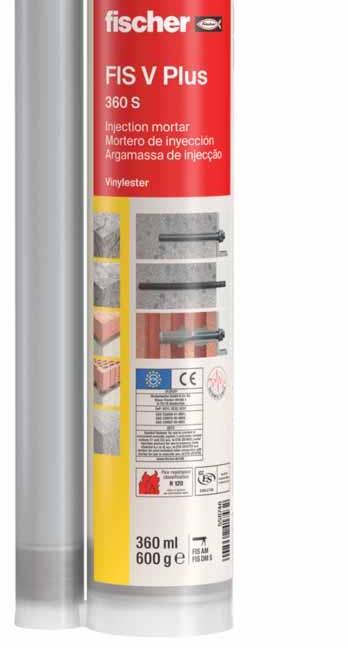
fischer has significantly upgraded its digital support for those on-site
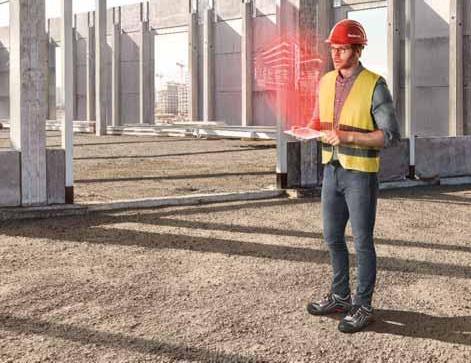
Users must register for a myfischer account in order to access the installation protocol function, which is easy to do through the app. Data that has been entered can be synchro‐nised across various devices. Speaking of the myfischer portal, the brand has been dili‐gently pooling everything worth knowing about products, services, deliveries and much more in the revamped myfischer portal, available free of charge. The password‐protected area of the fischer website is available after successfully registering target group‐specific information and provides essential day‐to‐day information, says fischer. It ranges from individual content to the Fixperience design software and additional services, available 24/7. fischer is also providing its customers with additional digital contact and order options through the portal. The user‐friendly self‐service allows the company’s partners to work with fischer in an even more efficient, flexible and time‐saving manner, says the group. What’s more, the fischer Fixperience design software also helps tradespeople plan fastening solutions for entire projects and individual applications in a targeted and cost‐optimised manner. fischer also offers BIM services such as digital twins of rele‐vant products and predefined smart components as well as custom BIM engineering solutions and services.
REALISTIC ANCHOR DESIGNS IN CONCRETE AT BAU ONLINE
BAU was online this year and saw fischer introduce an inno‐vative design method: The non‐linear spring model, which allows the resistance of anchor groups to be calculated realis‐tically based on individual anchors within a group while taking into account the base plate geometry and anchor layout as well as the existing stiffness of base plates and individual anchors. The approach therefore goes beyond the limits of the previ‐ous concrete capacity method (CC‐method) on the design of tension loaded fastenings in concrete, says fischer. The perfor‐mance‐based concept allows the realistic force distribution between the group anchors and the displacement of the base plate to be taken into account. This enables a better assess‐ment of the overall system than calculations based solely on load‐bearing capacity. There’s more on all those announcements and products on fischers website.

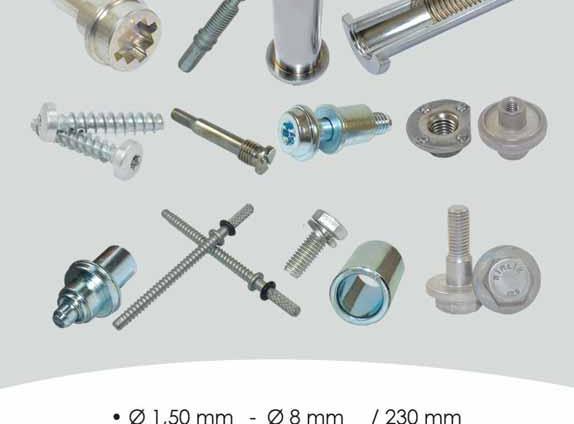
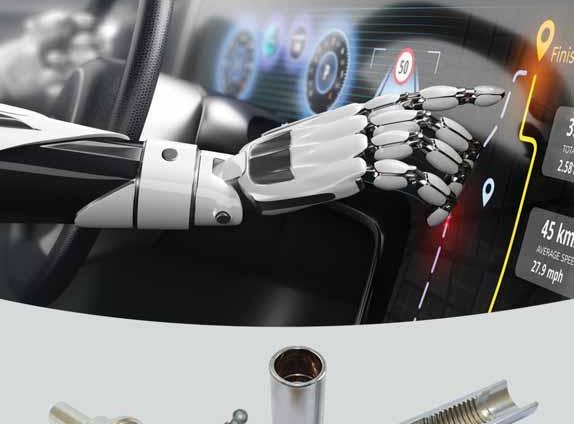
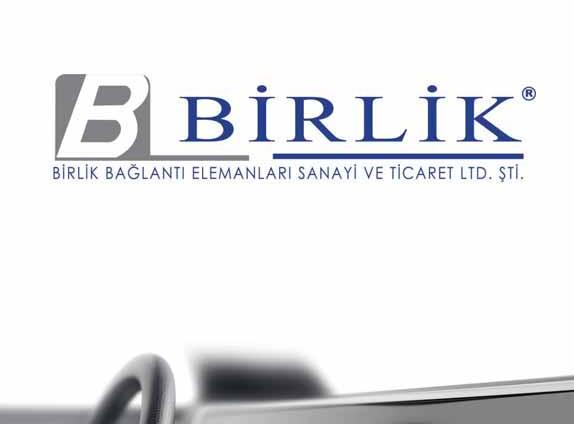
IT’S ALL ABOUT THE BASE > ATOTECH REVEALS NEW BASE COAT, ZINTEK 200 SL F
Prime protection and controlled friction with a two base coat layer system, courtesy of Atotech’s new base coat Zintek® 200 SL F. Atotech explains all…
Many industries rely on the multi‐functional properties of coatings with lamellar zinc particles when it comes to the optimal coating of their fasteners. Zinc flake systems provide high and durable corrosion protection with an attractive appearance with a very low coating thickness. Lubricants that are generally integrated into the top coat allow a controlled ability to control friction when applied to two base coat layers as part of standard coating sequences.
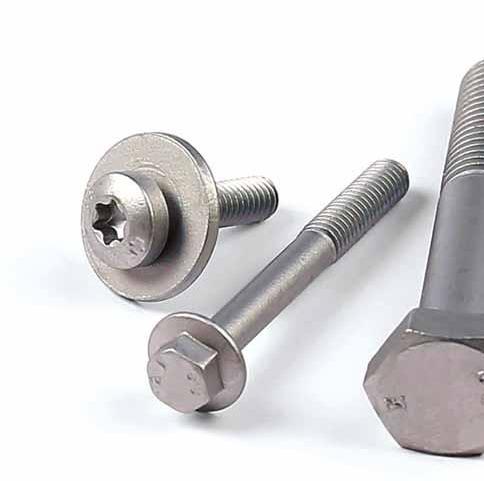
“A two base coat layer system with incorporated lubricant significantly increases production capacity”
Atotech’s solvent‐based Zintek® 200 SL F base coat features an incorporated lubri‐cant. By eliminating the need for a top coat, this cost‐effective system provides excel‐lent adhesion, highest corrosion protection and precise friction coefficient properties in a centered CoF range of 0.12 to 0.18 with only two base coat layers. At the same time, the system shows no stick‐slip effect, which is a problem with several alternative solu‐tions available on the market. The elimina‐tion of the top coat application leads to a higher throughput (up to 30%) and thus significantly increases the capacity of the dip‐spin coating system.
Pre-eminent cathodic corrosion protection
Besides its excellent adhesion and friction properties, Zintek 200 SL F boasts excel‐lent cathodic corrosion protection proper‐ties. Many OEM standards require that a coating must exhibit corrosion resistance for at least 600 hours in neutral salt spray tests with no evidence of base metal corro‐sion. Zintek 200 SL F lasts for more than 1,000 hours, far exceeding standard OEM requirements. These outstanding corro‐sion protection properties also apply to complex part geometries, and Zintek 200 SL F shows high corrosion resistance (720 hours) when subjected to stone chipping.
// By eliminating the need for a top coat, this cost-effective system provides excellent adhesion and high corrosion protection. //
Less sensitivity against humidity
Another crucial requirement of solvent‐based coatings is humidity stability. High sensitivity to humidity can lead to devia‐tions in friction behaviour and corrosion protection, as well as severe paint destruc‐tion within the tank during lead times. Unlike other comparable products in the market claiming to possess commensurate properties but showing inconsistent CoF behavior after being exposed to humidity, Zintek 200 SL F, a reliable, production‐proven process, clearly exhibits less sensi‐tivity against humidity, leading to a prolonged lifetime for the ready‐to‐use paint inside the dip spin tank. In addition, Zintek 200 SL F requires a curing temperature of just 230°C. This moderate curing temperature does not weaken the hardened steel structures typi‐cally found in modern fasteners. This char‐acteristic makes Zintek 200 SL F perfectly suitable for application on safety‐labelled parts for the automotive industry. Due to its economic benefits as a two‐coat system, its effective corrosion protec‐tion, high bath stability, and reliable controlled friction properties – all outstanding features – Zintek 200 SL F has claimed accreditation and approval from two major French automotive OEMs.”
www.atotech.com

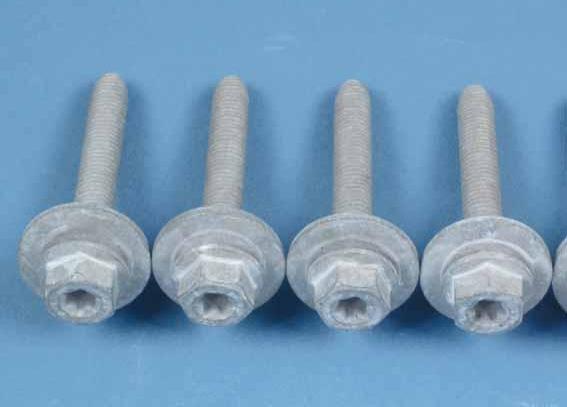
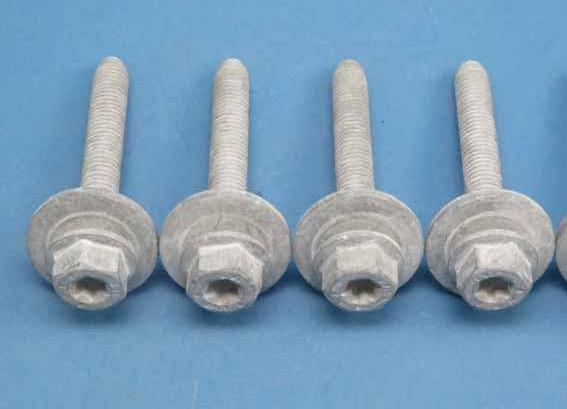
Zintek® 200 SL F
CORROSION PERFORMANCE > Before testing
Zintek® 200 SL F
CORROSION PERFORMANCE > After 1,008 h NSST acc. ISO 9227
Zintek® 200 SL F