
11 minute read
TECHNICAL SPOTLIGHT
DO BOLTS REQUIRE LUBRICATION?
Fastener lubrication is a specialist issue, requiring specialist knowledge. Microgleit – part of the Coventya Group – shares its specialist knowledge with Torque Magazine readers…
Millions of different screws are used to connect components every year. Yet often it is not known, or at least not sufficiently appreciated, that bolts and lubricants are indispensably linked. The function of a threaded connection is based on its ability to build up pretension‐ing force between parts to be connected. The applied tightening torque is translated via the thread pitch into the resulting preload force. Without lubrication, the fric‐tion losses of combined head‐ and thread‐friction reach values up to 90%. That means only 10% of the tightening torque is available to apply pretension force. A defined friction value with low variation is an absolutely mandatory product feature for all threaded connections. The mechani‐cal elements, used fastener and lubricant are parts of a tribological system. Preten‐sioning force, coefficient of friction and tightening torque are mathematically connected. Lubrication is the system’s central element. It is important to know that there are many parameters for the tribolog‐ical system of part and bolts. So, while one and only lubricant for all applications is not possible, the best solution can still be found based on a set of selection criteria.
STANDARD GUIDELINE 1 > NO THREADED CONNECTION WITHOUT LUBRICATION
Main issues regarding insufficient lubrication >
Pretension load out of spec. This problem may result in leakages (flanges or oil pans) when the used fasteners show different pretensioning force from screw to screw. Too low pretensioning force (as a result of too high friction) can trigger self‐loosening of screws. Too high pretensioning force in combination with dynamic loads could lead to the yield strength of screws being exceeded, with subsequent loss of elasticity leading to breakage.
Seizure of threads >
Seizure of threads can occur during tight‐ening of screws –for materials such as austenitic steels or zinc platings this is very likely, while other material combina‐tions show high friction values and high scatter. In the case of bolts made of high‐temperature steels, thermal expansion can lead to high specific surface pressures on thread flanks: the yield point is exceeded and welding occurs.
Corrosion >
Water and/or oxidizing gases penetrate the thread area –this causes the screw to seize up due to rust – so normal loosening of the connection becomes impossible. Rust formation blocks the thread and makes it impossible or much more difficult to dismantle the screw as intended.
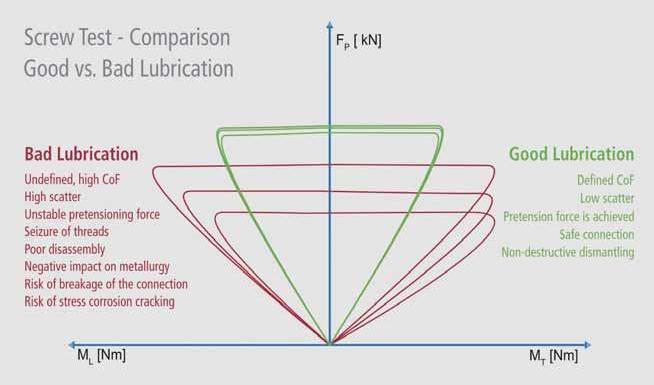
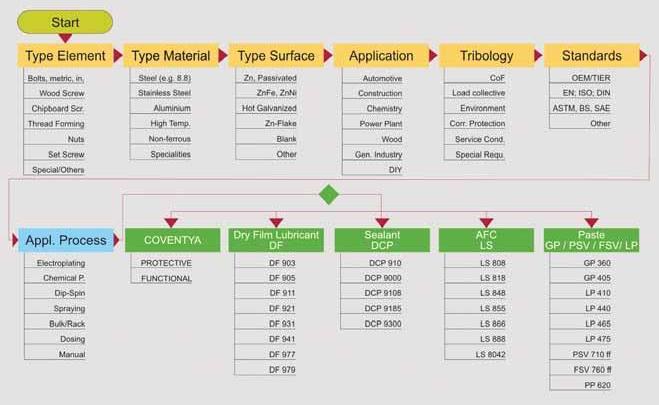
Cracks, Material Brittleness, Stress Corrosion Cracking, Fretting Corrosion >
High‐strength and heat‐resistant screws are susceptible to cracks or stress corrosion, cracking under certain conditions. The pres‐ence of elements such as chlorine, fluorine, sulphur, lead, or aluminium accelerate the effects. Lubricants have to be formulated with metallurgical compatibility in mind. Fretting corrosion is an extremely effec‐tive wear mechanism –parts must be protected with highly‐effective lubricants.
High Torsional Load During Tightening –Risk of Breakage >
High friction automatically generates high torsional stress, which can lead to premature screw breakage.
Selecting the right lubricant for a threaded connection
STANDARD GUIDELINE 2 > FASTENER LUBRICATION IS A SPECIALIST ISSUE
How to Select the Right Lubricant >
The graphic shows the parameters that are crucial to select the right lubricant for a given threaded connection. The selec‐tion guide is based on tribological system elements, combined with practical expe‐rience and knowledge of the specific market segment. Various fasteners, mate‐rials, application and service conditions, specifications etc. require specific lubri‐cant solutions. In conclusion, the COVENTYA and microGLEIT range offers everything to make it work and last. For more details visit the website:
www.microgleit.de
www.pasvahl.de
Up to 34 million special screws directly from stock!
Fit bolts, plugs, knurled thumb screws, square head bolts, flat headed screws, hexagon set screws, brass screws and specials.
FIT BOLTS according to DIN, 609, 610, ISO 7379, DIN 7968 Fon +49 (0) 40 532 852-0 Fax +49 (0) 40 532 852-52 info@pasvahl.de
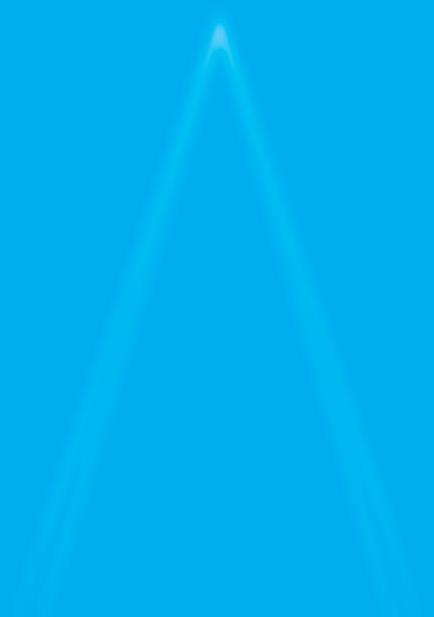







FIRST-CLASS CONNECTIONS
Right on schedule: Deutsche Bahn reported its highest punctuality rate in 15 years in 2020. The importance of being on time is well understood by long-term fastener supplier Ferdinand Gross, which is experienced in supplying crucial parts in good time to ensure the smooth running of Deutsche Bahn and other rail companies...
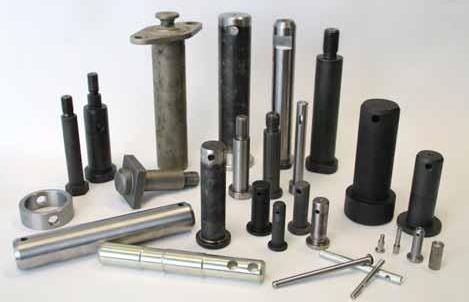
Continuity, experience and quality have been the watch‐words for Ferdinand Gross for more than 150 years, with the company among the largest suppliers of fastening technology in Germany. One speciality of the company is railway‐specific parts; for example bolts, double spring cotter pins, wheel set tape, expansion screws, locking rings and many more. Since 2012, Ferdinand Gross has been the exclusive supplier of Deutsche Bahn AG for fastening elements with the classification Q1. The company supplies Deutsche Bahn with over 60 million parts a year as part of a Kanban system. This Kanban system ensures that the roughly 10,000 customer‐specific parts kept constantly in stock are always available at the more than 400 Kanban storage locations of Deutsche Bahn. Thanks to the integrated Kanban system of Ferdinand Gross, Deutsche Bahn‘s procurement costs have been reportedly cut by 70%. With the FALCON visualisation software, Ferdinand Gross has put the Kanban system on a new level: Deutsche Bahn was one of the first companies to implement the future‐oriented tool. The browser‐based software FALCON gives the customer the visual access to all Kanban shelves within the company. Its virtual cockpit serves as a central control unit and presents the individual shelves and boxes in a visually appealing manner –also in 3D, including the contents of the boxes, the respective delivery quantity, the assembly – everything. With FALCON the storage location can be changed, the filling volume of a container can be altered or additional items can be ordered –all intuitively from a PC, smartphone or tablet. For Deutsche Bahn, it was above all this innovative system, which optimises the service for the production‐driven material consumption for around 120 production warehouses, which was the decisive factor to award Ferdinand Gross the "DB Supplier of the Year" in 2003 and 2016. Ferdinand Gross also supplies other rail companies that manufacture and main‐tain rail vehicles. Through years of coop‐eration, Ferdinand Gross is specialised in railway‐specific parts and offers its own stock programme for these items, which is deliverable on short notice.
www.schrauben-gross.com
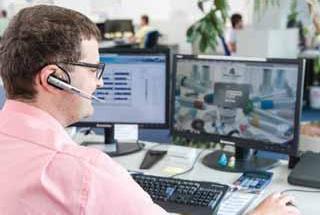
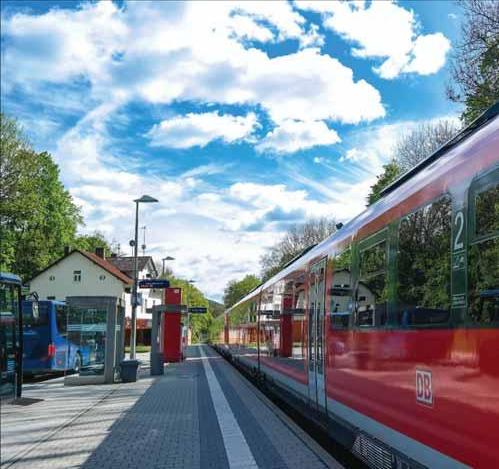

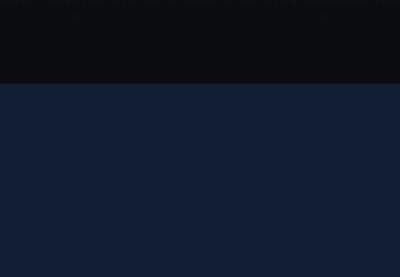

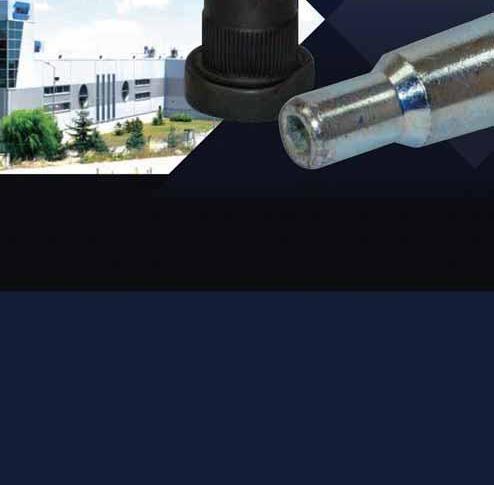
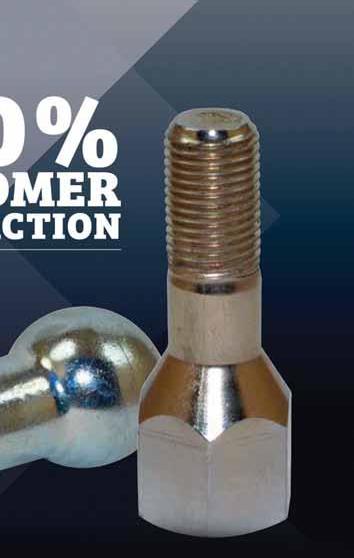
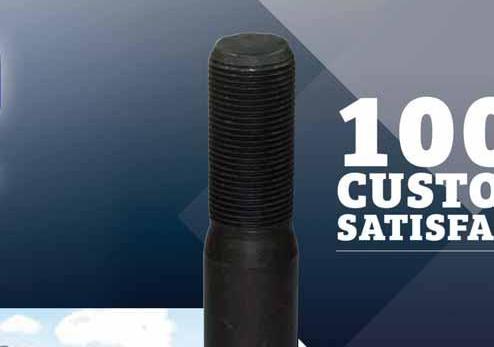

RAILWAY CUTTING
Dormer Pramet provides tools for the railway industry as standard. Here, the firm explains some of the challenges of the sector –and the tool solutions it provides…
Railway‐focused cutting tools can often be complex due to the specific requirement needed to machine a certain component in an efficient and highly reliable manner. Therefore, across many applications, the majority of cutting tools for the railway industry are classed as specials, designed with the customer and operation in mind. But not all products! There are several tools within Dormer Pramet’s standard assortment, which can be used to support the production of various railway components. The company’s Penta HD and Econ HN, for example, are milling tools from its Pramet index‐able range which can be used for various applications, includ‐ing machining switches, base plates and wagon parts, such as frames, wheel axles and bogies.
Machining Switches
Rail switches and crossings are the sections that guide trains from one track to another. Dormer Pramet’s assortment encompasses tools for machining switches in all major rail profiles. The 60E1 and 60E2 rail profiles, for example, are the most common, especially in Europe. The type T section rail (flat bottom rails) is suitable for medium and heavy load traffic. In the crossing part of the two rails, known as the frog, manganese steel, also known as Hadfield Steel, is used. An alloy steel, it is ideal for high impact environments. Manganese steel is not magnetic and has a very high abrasion resistance because the crossing must withstand the highest load on a rail‐way track. It is a very tough material, with a low hardness (200‐280HB), however, when it is machined, the hardness increases to more than 350HB. Another material used in the production of switches is Bainite steel, which is much easier to machine, even though it is a harder material at 450HB. It is ideally suited to this part of the track due to its high strength and wear resistance. Rail steel must be designed to be able to resist plastic deformation, rolling contact fatigue, bending and thermal stresses during the welding processes and renovations. When machining switches, the design is usually made from a single component and therefore one of the first operations is roughing the top and bottom sections of the rail. This requires a large diameter cutter, enabling the fewest number of passes possible. Both the Penta HD and Econ HN assortments have indexable cutters up to 315mm diameter.
Dormer Pramet’s range encompasses tools for machining switches in all major profiles
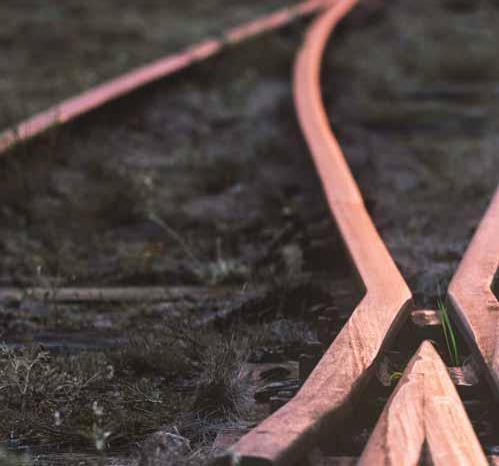
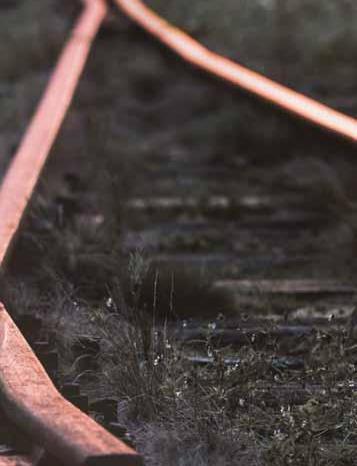

Railway switches during the production process.
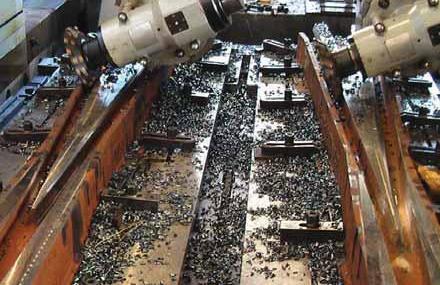
Penta HD
The Penta HD milling cutter was specifically developed with switches machining in mind. Allowing operators to utilise the full power of their machines, the Penta HD with PNMU insert is ideally suited to heavy roughing operations in a variety of material, including steels, stainless steels and cast iron. Offering up to 10mm depth of cut and a feed rate of 0.7mm per tooth, the range enables high metal removal rates and productivity. Its double‐sided insert design with ten cutting edges has an available length of 100mm, with each edge numbered for easier indexing. In a recent test example, the Penta HD with PNMU insets, M chipbreaker and M8345 grade was able to machine 4,600mm of track in 39 minutes, with a cutting speed of 70m/min, a feed rate 0.33mm/tooth and an axial depth of cut (ap) at 7mm. Another key feature of the Penta HD is the use of Dormer Pramet’s patented Sidelok technology system, which provides quick and easy clamping and release of the inserts.
Econ HN
Additional railway operations where standard tools can be used include the machining of base plates –the connecting element which ensures the rail is securely attached to the tie or sleeper. Also, wheel set axles, break‐pad connectors, beam bolsters and bogie frames all require machining into shape. For all these applications, customers demand high productivity, while at the same time, respecting specific production limitations and materials. In any initial machin‐ing, face milling cutters are usually the most suited tool. This allows for the removal of large amounts of metal and creates a smooth, flat surface and base, before specific shaping can be performed for connectivity with other components. When machining the bottom part of base plates, for example, face milling cutters with diameters up to 160mm are often used. The Pramet Econ HN assortment offers a 45° face milling cutter, which is available from 25 –315mm in diameter and includes the HNGX 06 and HNGX 09 inserts. Designed to generate improved surface quality, the indexable range can perform both roughing (up to 6mm depth of cut), through to finishing (up to 1mm depth of cut). Its inserts have 12 cutting edges, with a wiper option for higher surface finish and is ideally suited to machining cast iron, as well as steels. High insert density for high productivity and longer tool life, means lower cutting forces are required. Also, a differential tooth pitch and a unique geometry (F, M or R) for each operation, from finishing to roughing, along with an internal coolant supply, provides high tool accuracy and quiet running.
Spezialfabrik für Schrauben- und Wellensicherungen
Sperrkant spring washer A / Z DIN 6905 captive DIN 6796
conical washer
DIN 127 ASME B18.21.1 A / B
DIN 128 A / B convexed / corrugated
DIN 137 A / B curved / crinkled
Contact washer NF E 25-511
S / M / B / K slim / medium / wide / toothed
Railway washers
DIN 74361 limes type conical lockwasher C Centring ring
DIN 7993 A / B for shafts / for drillholes Sperrkant spring washer captive
Sperrkant washer S / M / B / K / Z slim / medium / wide / toothed
DIN 6797
A / I / V outside / inside / countersunk Doubled toothed lock washer
DIN 7967
row 1 / row 2 DIN 6798
A / I / V outside / inside / countersunk
Güde GmbH Dieselstraße 8 58840 Plettenberg Germany