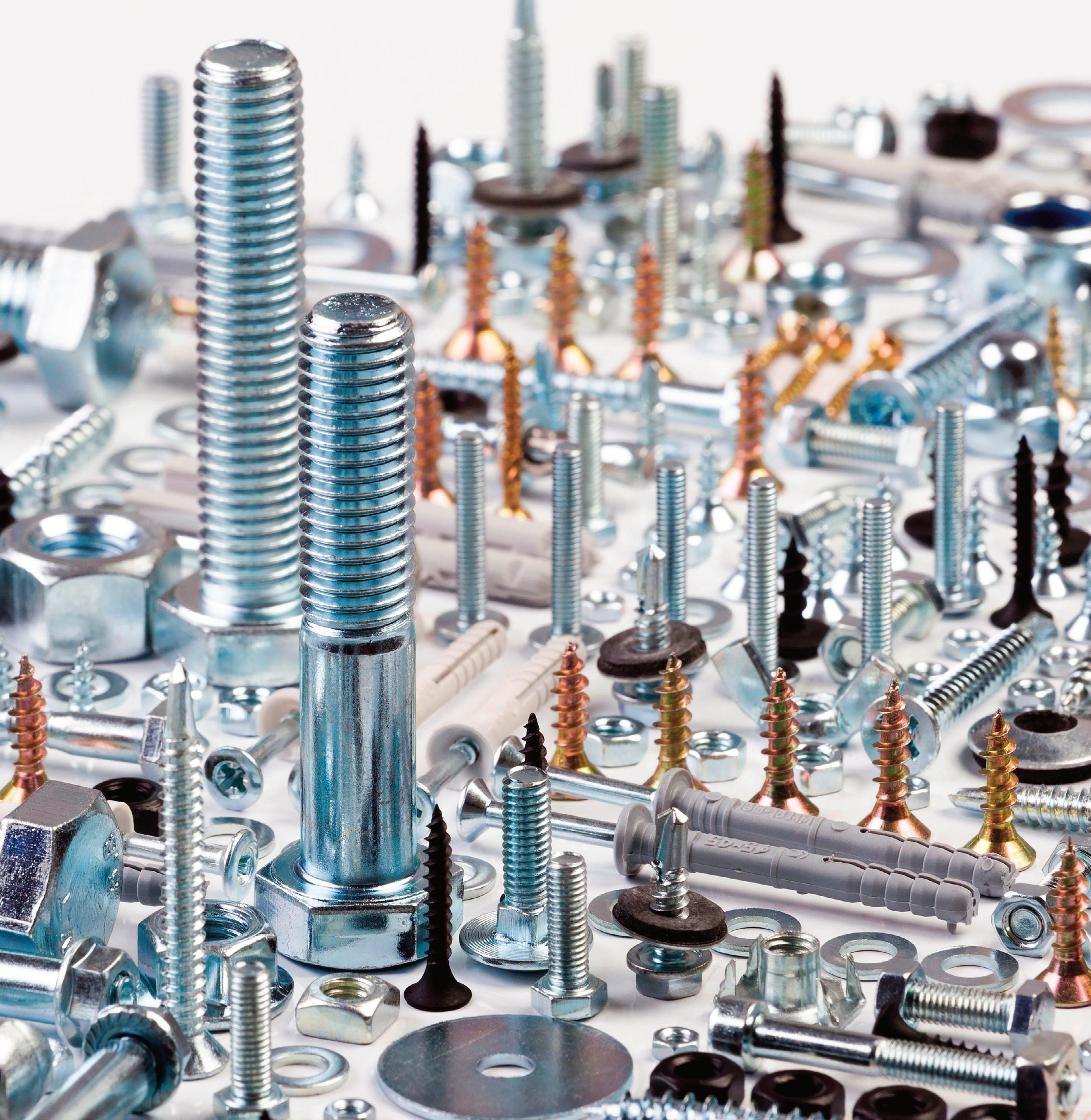

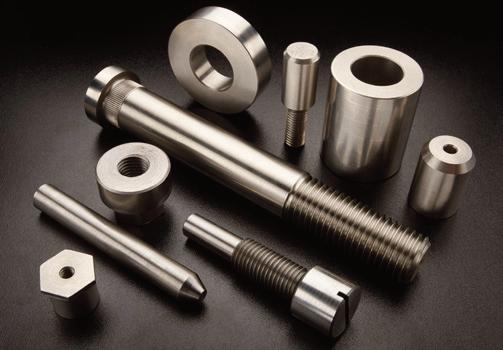



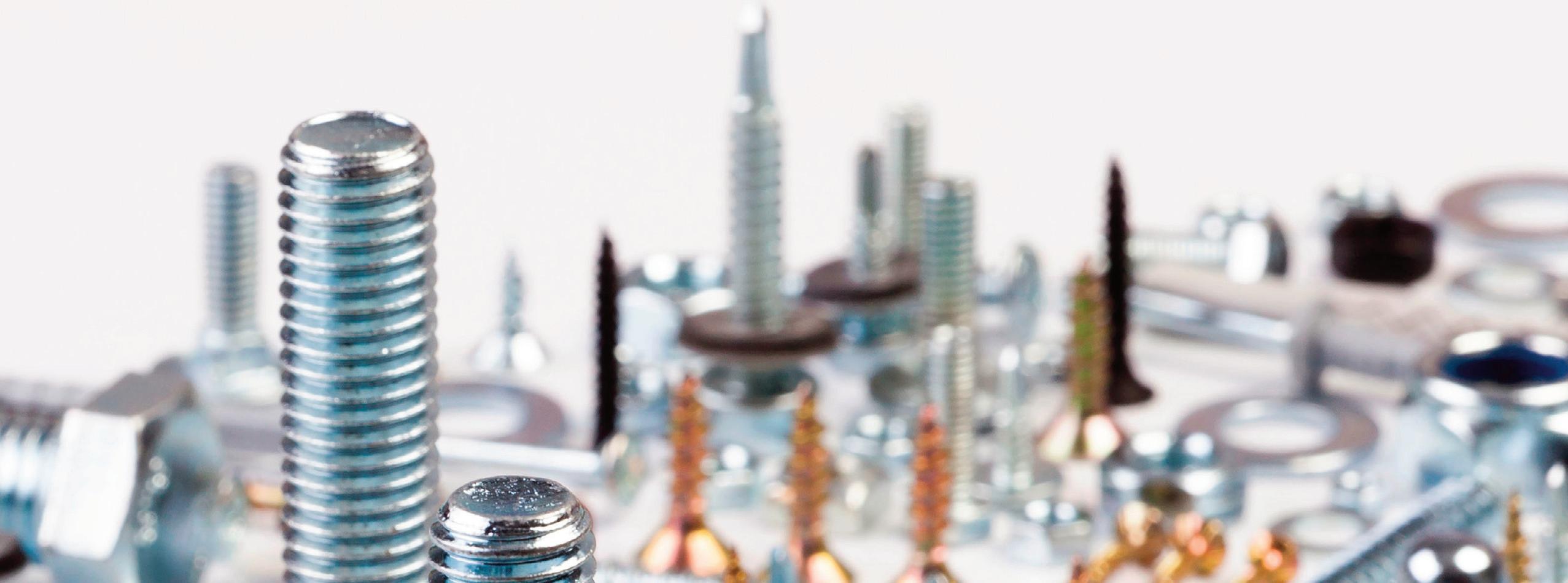
Since 1955 ND Industries has specialized in the development of innovative materials and processes which increase the safety and reliability of fastener assemblies.
ND serves a global market with divisions across the continental U.S., Taiwan, and licensees around the world. ND’s core business revolves around the application of a wide variety of materials onto fasteners and assemblies to aid in functions such as locking, sealing, masking, lubricating, and noise and vibration dampening. ND also manufactures a line of bottled products under the Vibra-Tite® brand name for MRO and retail use.
From two base products in 1965 to currently over two hundred twenty, ND continues its tradition of cutting edge research and development with the regular introduction of unique materials along with competitive brand offsets.
High strength encapsulated epoxy threadlocker for use in electrical systems where low halogen materials are necessary. Contains small micrometer microcaps which reduce material extrusion on installation.
A high temperature, high pressure thread sealant which withstands up to 40MPa. Offering thread locking breakaway torques greater than 20Nm and a maximum temperature of 428°F (220°C). Thermoseal is an extremely versatile product for challenging sealing conditions.
ND’s highest temperature chemical threadlocker. Initially performs like a vibration dampening compound. Once temperatures reach 750°F (400°C), a secondary activation begins, causing the fastener to be permanently locked in place. Tested to over 1500°F (850°C).
Did you know that ND is an approved 3M applicator? Further proof why ND should be your one stop shop for pre-applied fasteners.
Publisher
Jerry Ramsdale jerry@torque-expo.com
Editor Jonathon Harker jonathon@torque-expo.com
Deputy Editor
Rachel King rachel@torque-expo.com
Sales Manager – UK Claire Warman claire@torque-expo.co.uk
Sales Manager – International Harry Whyte harry.whyte@torque-expo.com
Sales Manager - USA & International Thomas A. Keenan tom@torque-expo.com
Circulation Tracy Howell tracy@torque-expo.com
Head of Production Luke Wikner luke@torque-expo.com
Designers
Dan Bennett dan.bennett@torque-expo.com Victoria Arellano victoria@torque-expo.com
Published by Stag Publications Ltd 18 Alban Park Hatfield Road St Albans Herts AL4 0JJ tel: +44 (0)1727 739160 fax: +44 (0)1727 739169 Email: info@torque-expo.com Web: www.torque-expo.com
Disclaimer
Although the utmost care is taken to ensure that information contained herein is accurate and up to date, the Publisher cannot be held responsible or in any way liable for errors or omissions during input or printing of any material supplied or contained herein. The Publisher also cannot be held liable for any claims made by advertisers or in contributions from individuals or companies submitted for inclusion within this publication. The opinions expressed are not necessarily those of the Editor or of Stag Publications Ltd.
IN THIS ISSUE we dedicate a few column inches to (one of) the industry’s current challenges – overstocks. It’s something referenced by our Guest Editor over the page and also by other top CEOs and MDs of leading fastener companies in our news pages.
Having cash tied up in the warehouse is not a predicament unique to the fastener industry. For example, take the cycling industry where the Covid lockdowns had a huge impact. They brought an explosion in demand for bicycles and all the accompanying gear, a demand that was virtually impossible to keep up with, not least with all those supply chain challenges.
Now, with inflation and other cost pressures hitting consumers in the pocket, demand for bicycles has predictably declined, leaving some distributors and bicycle retailers with much more stock than they’d like. The critical difference is that bicycle stock is often tied to model years, so if you don’t shift it before the new models are due then the value of the stock on your shelves declines irrevocably with absolutely no hope of return.
Other industries are more fortunate, with stock that could well regain value if you can afford to hold onto it. How long you have to wait for that to happen is the real head-scratcher.
Harker Editorjonathon@torque-expo.com
It is a Chinese proverb, or perhaps a curse, that you may live in interesting times. The past few years have been anything but boring! In fairly quick succession we have had Brexit, Covid, AntiDumping Duty, the war in Ukraine, slowing global demand and, in the UK, a political debacle which has devasted the UK’s financial credibility.
It would be fair to say that we had some notice of the Brexit finalisation and the introduction of Anti-Dumping Duty and whilst we may not have liked the implications of those, we could at least put plans in place to deal with the issues.
I suspect pandemics would have been on few risk registers historically, Covid and the scale of the impacts was a huge shock, now thankfully retreating. Last year the focus was firmly on the supply chain challenges of booming post-Covid demand characterised by stock shortages and sky-high shipping costs in the face of capacity constraints. Then along came the next unexpected shock, the war in Ukraine.
For most of us, the war will have had little direct impact, but the knock-on impacts on energy prices, inflation and global economic growth have been dramatic. Last year’s stock shortages have become overstocks and, with the exception of shipping costs, operating costs have risen markedly. In the UK we have managed to exacerbate these issues even further with our own political circus with the pound down 20% on the US Dollar from a year ago and interest rates spiking. Rishi Sunak has certainly got his work cut out for him!
Doherty Chief Executive of Owlett-Jaton www.owlett-jaton.comWhatever next? Well, China still considers Taiwan a breakaway province, if that tension turned into something more physical, the impact on our Far East supply chains would be unthinkable. But, perhaps that is the point, increasingly we have to think about the unthinkable risks and try and prepare for them.
Everyone I speak to says these are unprecedented times, perhaps living in interesting times is more of a curse than a blessing, some boring times might be nice for a change!
Now, I need to go and look at that risk register again, I wonder what we should do if space aliens invade…
// Increasingly we have to think about the unthinkable risks and try and prepare for them. //
www.torque-expo.com
Globally operating fastener businesses are aiming to cut stocks as availability has begun to normalise. Supply chain disruption had led to significant difficulties in getting hold of product over the last two years. However, with disrupting factors including inflation now denting demand, as well as some distribution challenges subsiding, many firms are focused on reducing busy warehouse shelves.
Quoted in its Q3 2022 financial statement, Bufab President and CEO Erik Lundén said: “[Our] strong organic growth in combination with the past two years’ longer lead times, has led to the need for us to increase our inventory. The lead times have been decreasing for some time and we have taken several measures to ensure that our inventory follows suit. We expect the trend in increasing inventory to reverse in the fourth quarter and that the cash flow will then gradually improve.”
Echoing that priority, Bulten President and CEO Anders Nyström, quoted in the firm’s Q3 report, said: “The focus moving forward will be on reducing stock levels and increasing margins.”
Global manufacturer of precision measuring tools and saw blades Starrett has unveiled a new partnership with OwlettJaton. The new distribution deal will bring a range of Starrett power tool accessories to OwlettJaton’s 4,000 customers, starting November.
The top selling and wellknown Fast Cut and Cordless Smooth Cut hole saws from Starrett’s Bimetal range will be available as well as their jigsaw and power hacksaw blades, both of which are produce of Starrett’s patented Bimetal Unique™ Technology.
Further saw blades offered include the 3x Power reciprocating blades. Launched in 2021, the Starrett 3X Power reciprocating saw blades set a new level for performance and value on the market with a line that includes blades for cutting wood, metal, multiple materials and heavyduty cutting.
Global firms have recorded another strong Q3. Bufab’s interim report (January to September 2022) saw net sales increased by 49% to SEK 6,358 million (4,279) with organic growth at 16%. The operating profit (EBITA) increased to SEK 748 million (526) for January to September and the operating margin was 11.8 % (12.3). Bulten saw net sales increase 12.9% in the period JanuarySept, to SEK 3,136 (2,777) million. Grafton Group revenue (excluding divestments) increased by 9.5% to £1.93 billion in the ten months to 31 October 2022 from £1.76 billion in the prior year, and by 39.2% from £1.39 billion in the same period in 2019.
Tom Pettit UK Sales Manager said: “I am really excited to have OwlettJaton onboard as a wholesale partner. They have the Sales team and customer base to support our aggressive growth plan in the UK.”
Tony Williams OwlettJaton Sales Director added: “Starrett is a great addition to our existing list of marketleading brands. OwlettJaton is recognised within the trade as offering a complete wholesale solution, with low minimum order levels and free nextday delivery. Customers can order multiple items, in small quantities, all from one supplier. The introduction of over 130 Starrett lines complements our existing cutting blade offering and will provide new opportunities and existing customer growth into 2023.”
www.starrett.co.uk www.owlett-jaton.com
Dee Ward has been appointed as the new Chief Executive Officer at Marine Fasteners and will transition to the new position over the coming months. With over 20 years’ experience in B2B and the construction industry, Ward is making the move from Brikksen, a Würth subsidiary, where he has been a branch manager and the Executive Vice President since 2021.
Marine Fasteners was acquired by the Würth Group in 2008 to function as its primary stainlesssteel supplier in North America. Since then, Marine has continued to use its expertise in stainlesssteel and the marine industry to grow into new markets, including servicing the solar, curtain wall, hydro industrial, food processing/production, and sporting equipment sectors.
Staffordshirebased Hydrajaws Limited has recruited a new Managing Director, Stephen Hynes. He joins the company with an extensive background in a diverse range of industries from automotive and chemicals to offhighway and logistics experience in B2B manufacturing and distribution.
“It’s a very exciting time to be joining Hydrajaws Limited,” he said. “We have an excellent established team and a trusted name within the pull testing industry. I am looking forward to leading and evolving the business during its next stage of significant development.”
Atlas Copco has appointed Anna Sjörén as its new Vice President Sustainability. Sjörén is currently at Dometic Group as the Compliance and Sustainability Officer. She previously worked at Atlas Copco between 2007 and 2019, where she last held the position as Global Sustainability Manager for the business area Industrial Technique. She will take on her new position in January 2023.
Optimas Solutions has announced the promotion of two Presidents to dual CEOs. By elevating Mike Tuffy (top) to CEO, International, and Daniel Harms (bottom) to CEO, Americas, the pair will be given more autonomy to continue the successful transformation of the company.
“The past year has been a great journey for Optimas,” said Harms and Tuffy. “We both share a deep belief in this dualCEO structure and the positive momentum Optimas has gained in the last year is real. Feedback from customers, prospects and teammates around the globe is positive and tells us we’re on the right track.”
EJOT SECURES UKTA >
EJOT UK has received UKTA (UK Technical Assessment) certification for its LEIBIG Superplus BLS range of selfundercutting heavy duty anchors to fully comply with the postBrexit standards protocol. EJOT UK has worked with the BBA (British Board of Agrément) to complete the independent assessment checking its performance data against British and European standards.
DEWALT has announced the DEWALT IMPACT CONNECT system, a new line of attachments to quickly convert select impact drivers into fast, powerful cutting tools. The system is rolling out with two attachments: a Copper Pipe Cutter Attachment and PVC/PEX Pipe Cutter Attachment that attach to select DEWALT 20V MAX and other prograde 18V Impact Drivers.
The BostwickBraun Company has announced the acquisition of Mill Supplies, Inc. (MSI) by the company’s Industrial Business Division. MSI is a contractor and industrial supply company operating out of Fort Wayne and Indianapolis, that has supported the OEM, construction, and metalworking industries for over 60 years.
NEW MD FOR AWI >
Alloy Wire International (AWI) has named a new Managing Director, Tom Mander. He has been promoted to the role after being with the company for more than 17 years. The move will see previous MD Mark Venables move to Chairman, remaining in the business to guide and advise for the foreseeable future.
Screwfix has opened its first physical store in Wattrelos, near Lille in France, following the opening of its French online site in 2021. The store follows the same model as the British counterparts, with plans for two other stores in the North of France in the coming months.
Crane Electronics has opened a new sales and service facility located in Plüderhausen, Germany. The new facility will form a key European centre for Crane Electronics Group, serving customers and distributors both in Germany and throughout Europe. The allnew onsite calibration laboratory also allows Crane to deliver a fast and efficient service, repair and calibration offering.
To subscribe to Torque Magazine and receive the newsletter visit: www.torque-expo.com/subscribe/ or scan this QR code...
REGISTRATION OPEN FOR THE BIG 5 > Registration is open to The Big 5 International Building and Construction Show to be held in Dubai in December. From new product launches to indepth netzero debates The Big 5 has a broad selection of products showcased for all kinds of construction projects. The event will be held at the Dubai World Trade Centre from 58 December 2022.
The sixth edition of The Taiwan International Fastener Show (Fastener Taiwan) will be launched over 35 May 2023 in Kaohsiung City, Taiwan. The event will feature allinclusive fastener products, including nuts, bolts and screws, fastener manufacturing equipment, fastener tools, meters & instruments and wire & raw materials.
There were no mega container ships blocking the Suez Canal in 2022, but there were plenty of other challenges in terms of supply and distribution. Join as us we select some of the big stories from the previous 12 months…
The European Commission’s timing was considered questionable but hopes that the trade levy would be postponed until after trade disruption of the time were dashed.
The duty rates reach up to 86.5% with reduced tariffs for a limited number of Chinese companies.
Jiangsu Yongyi Fastener Co., Ltd.: 22.1%
Ningbo Jinding Fastening Piece Co., Ltd.: 46.1%
Wenzhou Junhao Industry Co., Ltd: 48.8%
Other cooperating companies: 39.6%
All other companies: 86.5%
The true big story of the year has been, unfortunately, Russia’s invasion of Ukraine. The human cost of this conflict, like those of the other conflicts afflicting the world, outweighs everything else. Some enterprising citizens and businesses were moved to do their bit, including one fastener business driving over an ambulance and supplies for the conflict zone. Aside from those human costs, the knockon effects of energy prices and inflation in general are being felt throughout Europe and beyond.
Onto more fastenerspecific news and the implementation of Europe’s antidumping duties on certain iron and steel fasteners from China on 18 February 2022 was probably the biggest story of the year for the sector.
The prior November saw the first solid indication that antidumping levies were on their way, following a lengthy trade investigation instigated by EIFI (the European Institute of Fastener Industries), which provided evidence of “unfairly lowpriced imports” which “have caused material injury to the Union industry of the like product”. The European Commission has been investigating whether the imports from China were “dumped” and if so, whether to impose a levy to “restore fair trading conditions”.
In a previous financial crisis, back in 2009, the European Commission imposed antidumping duties on fasteners from China. The levies imposed were broadly similar to 2022’s levels, at around 80%. China fought back on that occasion, heading to the WTO to question the ruling. The WTO (eventually) found in favour of China and then, in 2016, the European Commission repealed the antidumping levies, with little warning.
So, can we expect the WTO to strike again? It’s unclear whether China has been in contact with the WTO’s Dispute body this time around, although even if there is an official dispute being investigated, it’s likely it will take some time to come to a resolution.
And what about the success of 2022’s antidumping duties? Anecdotal reports certainly indicate that more fastener production is being seen in countries such as Poland (see our last print issue), with factories in that country incredibly busy. Returning to a point made earlier, it’s hard to reasonably attribute this phenomenon solely to antidumping, or to any of the many other disruptions to trade we’ve seen in the last few months (and years).
Drewry’s World Container Index placed the cost of a 40ft container at $7,115, higher than the five-year average of $3,754 (numbers from early November).
Maersk’s Q3 2022 analysis said that freight and charter rates actually declined in Q3, relative to the previous quarter as the “expected normalisation” gained momentum throughout the quarter. Higher freight rates did, however help AP Moller-Maersk to an overall revenue increase of 37% (both EBITDA and EBIT increased around 60%), in Q3 2022.
£54 million was the sum paid by Swedenheadquartered Bufab for the UK and Ireland focused fastener wholesaler, TIMCO. Founded in 1972, the firm is continuing to be run by the founding Midwood family, current MD Simon Midwood is still heading the business with the senior TIMCO team, which leads a business with approx. 180 employees and a £60 million sales.
In fact you didn’t have to go far to find news of an acquisition in 2022, from fastener related deals that dwarfed the TIMCO deal like MKS completing a $4.4billion Atotech buyout to purchases of innovative startups.
Simpson Manufacturing spent €725 million on ETANCO while Fabory snapped up Fastto Nederland and the fastener division of Importinox.
One of the biggest acquisitions was SFS Group’s purchase of quality tool brand Hoffman SE. Hailed a “quantum leap” in expanding the market position and size of SFS Group, Hoffman is a heavy hitting firm, generating around €1 billion in sales (in 2021), with approximately 3,000 employees and on site in over 50 countries.
The World Bank predicted (in April 2022) that metal prices would increase by 16% in 2022, before easing in 2023 – albeit at elevated levels.
1.Keller Kalmbach and Mohindra Fasteners new joint venture: The two joined forces to establish KK Mohindra Fasteners, which will implement VMI, Kanban and other Cparts management tools to Indian and international industrial plants in India.
Strikes disrupt ports: Felixstowe, the UK’s largest port, saw strike action leading many importers to rearrange and reroute their goods. Further industrial action followed, with more looking possible, at time of print.
Milwaukee Tools owner buys C4 Carbides: Heavyweight power tool group TTI snapped up UKbased C4 Carbides, a firm making a name for itself with innovative cutting solutions.
Battery sharing platforms gather momentum: Bosch had a phenomenally busy 2022, not least in its promise to spend billions on producing semiconductors. The power tool market also eyed its expansion of its AMPShare multibrand shared battery system, which follows in the footsteps of the Metabo techled Cordless Alliance System, which has been adopted by some fastener brands.
Happily, 2022 has seen plenty of significant stories of fastener and tool businesses investing, not least in new facilities.
The start of the year saw Volt Industrial Plastics hold a groundbreaking ceremony for an allnew 36,000 ft² expansion. Plastic fastener manufacturer Volt is located outside of Yellville, Arkansas, and this expansion will now give the factory a total of 100,000 ft², allowing it to expand its current inventory of over 100 million parts to even more.
In Europe, Adolf Würth GmbH & Co. KG, parent company of the Würth Group, held its own ground breaking ceremony in June for a new transshipment centre directly on the A6/Kupferzell exit in the Hohenlohe industrial park.
The investment sum for the new warehouse and the associated redesign of the logistics process amounts to around €73 million and requires a corresponding freight volume. In the final phase, around 300 employees will work in two shifts in the new logistics complex.
While there was a trickle of trade shows taking place in 2021, 2022 saw a fullon programme of international trade fairs return, postCovid.
Fastener Poland, Cologne’s Eisenwarenmesse, Euroblech, Vegas’ International Fastener Expo, Innotrans... these were among the shows getting back to pulling in thousands of visitors from around the world. However, some shows were notable by their absence, with the likes of the Taiwan International Fastener Show now cautiously scheduled for 2023.
There are more thoughts on the year from our Guest Editor Ian Doherty, on page 6.
Make sure you stay up to date with the industry news by subscribing to Torque’s weekly newsletter here...
Under the UK Construction Products Regulation, from 1 January 2023, manufacturers of structural timber fasteners and fixings within the scope of the UK Designated Standard BS EN 14592 must successfully complete the UKCA testing process for any new product to be placed on the GB market.
With the deadline approaching, Fastener Testing Laboratory Warringtonfire is reminding manufacturers of that looming deadline, affecting new or even updated products planned for launch in 2023, to be able to be sold in the UK.
Having successfully achieved UKAS accreditation for its new Fastener Testing Laboratory, Warringtonfire is reminding manufacturers that the UKCA marking deadline is looming.
The UK is currently transitioning away from the EUrecognised CE Marking. Products undergoing a change in their specification, for instance, fasteners and fixings that have a change in design or coatings, will also need to be retested to gain the UKCA marking and confirm their stated performance.
For this reason, Warringtonfire has launched its stateoftheart Fastener Testing Laboratory, which is located in High Wycombe. One of only a select few UKASaccredited ‘Approved Laboratory’ facilities, the laboratory can undertake assessments of performance for structural timber fastener and fixing products, so that manufacturers can UKCA mark them to BS EN 14592.
The laboratory achieved the accreditation thanks to the expertise of its technicians as well significant investment into highcalibre testing equipment, which includes a universal testing machine for compression and tensile testing, a series of bespoke testing rigs, and conditioning rooms for structural timber samples.
The organisation will offer a range of geometric and mechanical testing procedures for dowel type fasteners from a particular group of structural timber fixings, comprising of nails, screws, staples, dowels and bolts with nuts. The laboratory will also test steel fixings used to create joints between timber components or to attach other materials to timber.
Ben Sharples, Commercial Lead at BM TRADA, comments: “While the testing process itself may not take too long, a lack of accredited laboratory space within the UK means manufacturers placing new or updated products on the GB market after the 1st January 2023 deadline should not delay with arranging testing.
“However, to further support our customer base within the construction products sphere, we have invested heavily into our High Wycombe Fastener Testing Laboratory to achieve UKAS accreditation and undertake UKCA testing.”
Alongside offering fastener and fixing testing, the laboratory can also offer thirdparty certification through its BM TRADA QMark certification scheme.
Sharples concludes: “We have already undertaken several UKCA assessments of performance for structural timber fastener and fixing manufacturers, and I would strongly urge those who need to secure testing time for new products to do so as soon as possible to avoid delays.” www.warringtonfire.com
Rapid Industrial Fasteners has been established since 1980, and lately the highly active company has been evolving at speed – or if you prefer, pretty rapidly. Most recently, the firm moved into a new office and larger warehousing unit.
Business growth got to a point where it was no longer possible to operate optimally in its old warehouse. As Managing Director Richard White says, the old facility was akin to a ‘Meccano’ set, with racking bolted on to squeeze ever more product in. Also restricted in terms of height, and with the business resorting to using secondary warehousing to house its growing stock holding, it was clear the old warehouse was no longer ticking all the boxes.
This summer, Rapid Industrial Fasteners moved the distri
bution part of its business to the new larger unit, closer to its machine shop – more on that later. With 720 pallet locations, the new distribution site is approximately 18,000 ft², a sizeable expansion on the old unit, which was closer to 10,000 ft².
Ambitiously, Rapid Industrial Fasteners opted to have as little downtime as possible for the move, with virtually no disruption for its customers, it says.
The new warehouse offers more space and, perhaps most importantly of all, a facility that is more suited to the growing business. “It works for us now. It allows us to pick product quicker and more accurately with carefully laid out stock locations.”
With increased space for Rapid’s steadily growing employee numbers, the new unit also includes a customerfriendly reception area.
The warehouse is particularly well situated as its very close to Rapid’s machine shop. “It’s almost the perfect location. It is as good as it could be,” White tells Torque Magazine
As important as the new warehouse is, Rapid Industrial Fasteners’ manufacturing facility is probably the biggest development the firm has undertaken in recent years. It was 2019 that Rapid opened its machine shop, putting it in a fairly rare position for a UK fastener business – a distributor with an inhouse manufacturing facility.
Starting from scratch, albeit with skilled personnel boasting extensive fastener manufacturing experience, the machine shop has come a long way in a short time. Counter intuitively, it was the Covid lockdowns that played a large part in speeding up its development.
“We didn’t close down for the lockdown and that’s when we picked up a lot of business. It was hard work. But we have clearly been doing something right.
“Our manufacturing workshop literally started from scratch, with four walls and a roof in an empty unit. Now we are a fullyfledged manufacturer and we are confident in our ability as a company.”
As the manufacturing side has grown for Rapid, the firm has been able to bring in more lead and key roles for the machine shop, largely to handle the increasing workload. Recently new machines have been acquired and further investments are planned, likely be made on more advanced machines, capable of performing multiple processes, the firm says.
Since Rapid Industrial Fasteners opened its manufacturing arm, it has kept it physically separate from its distribution hub. Moving the distribution business to a new unit in the summer, you might argue, could have been an opportunity to bring the two sides of the business under one roof, but the firm sees advantages in keeping them separate but close by.
“There’s a different work ethos in the distribution and manufacturing sides,” the firm tells Torque Magazine. “Distribution is by nature fast paced, there are goods coming in and out all the time, there is a lot of hustle and bustle.
“The machine shop is different – operators are constantly checking quality and can only go as fast as the machines allow… the nature of the two sides of the business is very different.”
Undoubtedly though, having manufacturing and distribution within the Rapid Industrial Fasteners business now allows the firm to offer an allround service for customers and have greater control over its supply and – ultimately – how well it can serve its clients.
“We used to use lots of subcontractors to turn around orders for special parts, but we were frequently let down and timescales drifted. That was disastrous for us,” explains White. “It meant we weren’t always able to get products to customers when we wanted to. It meant we couldn’t be as consistent as we aimed to be. Now we are a UK manufacturer, so we have more control.”
And on the distribution side, the firm is committed to high
// Our goal is to have happy customers that keep coming back. //Rapid opened its machine shop in 2019
volume stocking: “We offer a have regular import cycles of standard items, and we have solid relationships with key wholesalers in the UK.”
The many advantages of operating manufacturing and distributing hubs include a comprehensive approach to qual ity. Quality processes used in production can also be used for distribution products, says the firm.
“We have tools for Positive Material Inspection (PMI), we
routinely issue 3.1 and 3.2 material validation certificates, and our quality system is robust. We have ISO 9001 Quality Management System certification, tested by SGS, a higher end reputable testing agency. We offer complete traceability and tighter controls on material handling in accordance with ISO standards.”
Much of Rapid Industrial Fasteners’ successes have come down to quality relationships, with customers, within the business and with suppliers. The firm is fully invested in the notion that “people buy from people”: “Our goal is to have happy customers that will keep coming back. We’re willing to make it happen for them, whatever they want.”
The growing firm now has over 150 years cumulative experience in the fastener business, with ambitions to grow gradually. Rapid Industrial Fasteners prefers to develop business with customers, earning trust along the way: “It can be hard work, but business develops out of it and people begin to trust us to look after them.”
For the manufacturing side, Rapid plans to grow its share of the UK market and expand abroad. Investments in the aforementioned advanced machines will play its part in those ambitions, as will attracting more skilled manufacturing staff,
The first post-Covid Fastener Poland comes as the country’s fastener industry has been working flat out coping with boosted demand for shorter supply chains…
Over 1920 October 2022, representatives from a broad variety of industries met at the International Exhibition and Convention Centre EXPO Krakow. Attendees converged for the fifth International Trade Fair for Fastener and Fixing Technology, FASTENER POLAND®, and the 13th International Trade Fair for Powder & Bulk Solids Technologies as well as the 13th International Trade Fair for Suppliers of Maintenance Products and Services.
“This year’s FASTENER POLAND® Trade Fair was attended by 2,306 people, 24% of whom came from abroad, mostly from the Czech Republic, Germany and Romania,” explains Beata Snopkiewicz, Project Manager. “These were very specific visitors who, according to exhibitors, came for a specific purpose. As a result, lucrative contracts were being signed at the fair. In this respect, FASTENER POLAND always rises to the occasion and is appreciated by the industry community.”
Manufacturers and distributors of fasteners from the furthest corners of the world come to Krakow for two days. This year, as many as 65% of exhibitors came from abroad, including China, Czech Republic, Estonia, India, Malta, Germany, Sweden, Taiwan, Turkey, USA, Hungary and Italy.
“This year’s edition of FASTENER POLAND Fair has been very successful for me,” said Joel Alexandersson from the Swedish company REHOBOT ROTEX AB. “I gained a lot of valuable business contacts in Poland. We had a few customers from Poland before, but now we see that Poland is still a growing market for us, and we see that production that up to now took place in East Asia is now moving to this region, and our parts are as suitable as possible for this type of production process.”
Ayza Akmut from the Turkish company ISB FASTENERS
expressed a similar opinion: “We were very pleased to be at FASTENER POLAND. We had many meetings with visitors and I think we will meet them in the future. We gained a lot of knowledge and contacts at the fair. We often send emails presenting our services to other companies, but they don’t open them because they don’t know us at all. That’s why trade fairs are so important to us. Here they can see us, get to know us, see who we are. This makes us successful. We will definitely see you at the next edition, because this one was very fruitful for us.”
Domestic companies also used the fair to expand their contact base: Tomasz Karwowski of DROMET said: “Personal contacts have been significantly reduced over the past two years. We rarely met facetoface, whereas today, thanks to the fact that the restrictions have been reduced or removed altogether, we can meet and refresh our relations. With some clients we have the opportunity to get to know each other or meet for the first time, and I think this is very, very positive. Many of us have been waiting a long time for the opportunity to organise a trade fair and exhibit.”
The last two years, which have been difficult for many industries due to pandemics and broken supply chains, have, paradoxically, improved the situation for many Polish companies in the fastener industry. European manufacturers, faced with a lack of product availability from Asia, sought suppliers located closer to their plants. This benefitted Polish companies, which were able to offer highquality goods at affordable prices. According to Marek Łangalis of Olfor: “Over the past two years, the transportation system has shifted, breaking down completely from China and Taiwan, making the Polish market the biggest winner in Europe. We increased exports by
30% for two years. Theoretically the time of the Covid pandemic was when all Polish manufacturers had their machines set for three shifts, working so hard that products were sold that were still hot. A number of challenges lie ahead for the industry. In February, an antidumping duty was imposed on China; – on the one hand this is a very big challenge for importers to find new suppliers, and for manufacturers it is to fill a gap in the European market.”
exhibition included, among others: stateoftheart industrial fasteners and fixings (from bolts, to nuts, studs and wedges); construction fasteners (anchors, concrete bolts, facade and insulation fixing); advanced assembly and installation systems, as well as fastener manufacturing technologies and fastener storage and distribution equipment.
Conversations held at the fair indicated that the fastener industry is doing well – very well, even. The conference “The challenging world of manufacturing: from supply chains to distribution” turned out to be a hit. Knowledge and experience were shared by wellknown experts who spoke, among other things, about Poland’s prospects for 20222026 under the current market perturbations, flexibility in the context of the bidding process, antidumping and the associated threat to importers, and whether the crisis is an opportunity or a threat.
According to Maksymilian Krzyszton of EUROFIX Poland, the disturbance of supply chains is a problem on the one hand, and an opportunity for Polish companies to develop on the other: “The need and opportunity to produce here has emerged. The antidumping that the European Union has imposed on products from China has left Polish producers with their hands full, which means they can invest. The industry’s revival could be felt at FASTENER POLAND.”
From the first to the last hours of the fair, customers were busy chatting at the stands and taking full advantage of the event’s potential, so says the event organisers. Marek Łangalis added: “The pandemic has changed the thinking of customers, some are trying to move to the virtual world, but in the virtual world you can only do small business, while at the fair you do big business.”
FASTENER POLAND was a combination of a trade show exhibition and an extensive training programme. The scope of the
This year’s fair also included FASTENER POLAND B2B Meetings, cooperation meetings organised in a hybrid formula by the Krakow Chamber of Commerce and Industry and the Enterprise Europe Network centre. Over 1920 October, participants met in person in a comfortable exhibition space, and after the fair, until 28 October, on a dedicated electronic platform.
Rising prices and widespread uncertainty, the cost of raw materials, commodity availability, supply chain problems from Asia and the slowing economy were all topics dominating the 5th edition of FASTENER POLAND, said the organisers. According to Ayza Akmut: “One of the challenges is the cost of raw materials and the change in all other costs. But we also have an opportunity because of the current situation and the fact that manufacturers from China and Taiwan have higher expenses. We as manufacturers from Europe have a better chance to grow, because our delivery times are also much shorter.”
Reportedly, the Polish fastener industry has ambitions to not only maintain its position as a growth leader, but also to be among the top three importers of fasteners in Europe. Over the past 18 years, the market has grown sevenfold. Next year’s FASTENER POLAND will no doubt reveal what is to come for the market.
www.fastenerpoland.pl
// The anti-dumping that the European Union has imposed on products from China has left Polish producers with their hands full, which means they can invest. //
Bosch’s new pro level impact driver can tackle concrete bolts and screws and rusty bolts on small and medium commercial vehicles. And this smart tool has enhanced setting options and customisation thanks to connectivity features…
Bosch’s latest impact driver has a breakaway torque of 800 Newton metres, handy for loosening even rusty bolts and screws on commercial vehicles
T
Customisable screwdriving modes
he launch of the GDS 18V450 HC Professional has expanded Bosch’s Pro 18V System with a powerful cordless impact wrench with connectivity features. Designed to give professionals full control and flexibility when working with metal and wood, the impact driver has a breakaway torque of 800 Newton metres which enables it to loosen even rusty bolts and screws on commercial vehicles such as vans and SUVs. With a tightening torque of 450 Newton meters, the impact wrench is also touted as the first of its kind to be suitable for predrilled concrete screw connections measuring up to 8mm. Typical applications include fixing balcony or carport supports directly in concrete, or mounting supports for cable ducts or formwork elements.Your expert for efficient and durable bolt securing solutions HEICO-LOCK®
Mode A is preset for metal bolts and includes features such as ‘Shutoff after time’ and ‘ABR’ (Auto Bolt Release), which are activated when tightening or loosening bolts and nuts in order to avoid overtightening or loss during disassembly. Mode B for wood screws includes features such as ‘Auto Shutoff’ to prevent material from being damaged when tightening screws. Both modes can be customised via the Bosch Toolbox app and saved for subsequent applications. As a result, professionals save time when performing repetitive screwdriving tasks such as assembling facade components, cable ducts, or handrails – and can easily select the ideal setting for the respective application.
Battery advantages
The Professional 18V System covers all other major 18V applications – and even goes beyond the Bosch portfolio thanks to the multibrand AmpShare battery alliance, where many brands and tools share a battery system for user convenience.
Bosch Power Tools generated sales of approximately €5.8 billion in 2021, 80% of which was outside Germany. By end of 2022, this division of the Bosch Group will have launched more than 100 new products in the four business segments of power tools, garden tools, accessories and measuring tools.
www.bosch-professional.com
Scan code to find out more!
// It is also suitable for predrilled concrete screw connections up to 8mm. //
Heavy duty: Makita’s evolving cordless power tool range has been extended again, pushing the boundaries of what can be achieved with battery power
Makita gave independent dealers an exclusive first look at the new releases at the STAFDA trade show in San Diego. Memberdealers saw the new Makita products that span across platforms and applications, giving them more options for their pro customers seeking cordless products to replace equipment and tools traditionally powered by cords, gas and air.
“Makita is innovation driven and focused on the pro user,” says Brent Withey, Vice President, Brand, Makita USA. “STAFDA dealers reach the pro audience, so our membership is very important to our business.”
Makita has continued to expand batterypowered options with three cordless systems: The XGT 40V max | 80V max is Makita’s most powerful cordless system with tools engineered for applications that usually demand corded, gas or air power.
The recent release of the 80V max (40V X2) 14” Power Cutter (GEC01) is an example of the XGT System’s ability to replace petrolpowered equipment.
Meanwhile, ConnectX 36V | 40V max is pitched as a runtime and power solution for professional landscapers. The ConnectX 1,200 watt hour battery is compatible with ConnectX products, as well as 40V max XGT® and 36V (18V X2) LXT® products.
Finally, the LXT 18V | 36V is reportedly the world’s largest cordless tool system powered by 18V batteries (for over 300 products), with an expansive range of 18V and 36V solutions for construction, landscaping and lighting. The line includes Outdoor Adventure which is powered by LXT batteries, Outdoor Adventure products carry a distinctive camogreen colour and are ideal for the outdoor life.
GML01
CBU02
GCU04
GCU06
AC001GM1
Compressor
GSH05
GDT02
XGT Brushless 4-Speed Impact Driver
Combines power, torque and high speed for efficient fastening
Available Late 2022
XPH16 18V LXT Brushless Compact ½” Hammer Driver-Drill
More torque at high speed for efficient fastening 970 in.lbs. of Max Torque
Available Summer 2023
XT296 18V LXT Brushless Compact 2-Pc. Combo Kit
Includes New XPH16 and XDT14 3speed impact driver
Available Summer2023
XRJ08 18V LXT Brushless One-Handed Recip Saw
Onehanded grip is positioned to firmly transmit force to the workpiece
Loopshaped handle guard for added protection and improved tool rigidity
Up to 90 cuts in 2x10 lumber on a single charge (5.0Ah battery)
Available Late 2022
XCM01 18V LXT Brushless 3” Cut-Off Tool
Cutoff design with 20,000 RPM for fast cutting and designed for onehanded operation Forward and reverse operation
Available Q1 2023
XRT02 18V LXT Brushless Deep Capacity Rebar Tier
Deep capacity will tie #8 with a #7 rebar
Up to 5,300 ties of #3 x #3 diameter rebar on a single charge (5.0Ah battery) Available Late 2022
XCU11 18V LXT Brushless 14” Rear Handle Chain Saw Compact rear handle design for easy manoeuvrability Up to 73 cuts in 4x4 cedar on a single charge (4.0Ah battery) Available Q1 2023
All dates for USA market. Makita USA, Inc. is located in La Mirada, California, and operates an extensive distribution network throughout the USA. It’s been established for 50 years in the United States and over 100 years worldwide. www.makitatools.com
Howmet Fastening Systems (HFS), manufacturer of the Huck® range of vibrationproof fasteners and installation tools engineered for use in safetycritical applications, has responded to customer demand by launching two new “revolutionary” battery powered installation tools.
Developed in conjunction with Makita, they have been specifically designed by HFS for use in the installation of larger Huck lockbolts up to 14mm (BV17) and structural blind rivets up to 12.7mm (BV13). Like the Huck Range Force BV4500, they also feature a leading, electronically adjustable pulling force for the installation of pintailless lockbolts.
Aimed at a variety of industrial sectors from rail and agriculture to renewable energy the tools, which are equally as suitable for use on production line fastener installation, infield repair as well as insitu machinery assembly, have the power to deliver up to an impressive 1,000 installations per charge.
“Huck is a wellrespected brand of products with a strong reputation for engineering reliable, superior quality fasteners and tooling that work to meet the everevolving needs of our customers,” says Joël Melquiot, Huck product manager at HFS. “The new BV13 and BV17 tools are available to solve issues our customers were facing around the need to install large diameter fasteners in locations not suitable for bulky equipment or trailing hoses and cables.”
The Howmet Fastening Systems industrial product range offers what it says is the greatest breadth and depth of fastening solutions available including selflocking nuts, quickrelease fasteners, draw latches, threaded inserts, lockbolts, structural blind fasteners, heavyduty blind rivets and accompanying installation tooling for the brands: HuckSpin®, Camloc®, Recoil®, Keensert® and Simmonds®.
For more information about the Huck BV13 and BV17 tools, or to speak to an engineer, please email enquiries@hfsindustrial.com www.hfsindustrial.com
Owlett-Jaton, itself celebrating a business milestone, looks ahead to 2023 when the Unifix brand reaches its 60th anniversary…
Whilst 2022 may have been traumatic with the ongoing, but diminishing, challenges of Covid, the war in Ukraine, global economic slowdown and the UK political and economic debacle of the minibudget, at OwlettJaton we were celebrating our 75th birthday. We consider this milestone a great achievement and we are now looking forward to 2023 when our Unifix brand will reach 60, its diamond anniversary.
The Unifix brand launched in 1963, a year that saw the assassination of President John F Kennedy, the Great Train Robbery and the very first episode of Doctor Who. Over the years the range of products as grown and the brand has moved between a number of different owners, ending up with Wolseley in 2003. However, Wolseley later decided that the brand did not fit with their strategy and OwlettJaton acquired the brand ten years ago.
On top of the product changes, instore merchandising solutions have also moved forward and we are just in the process of launching our new merchandising solutions to the market which will take product presentation to a whole new level.
OwlettJaton has grown the brand extending the already broad range of products to include a comprehensive range of fasteners, woodscrews and the patented Kliplok® Pipe Clips. An important part of the growth has been in recognising the changing needs of customers and the need to merchandise products effectively. This has seen the introduction of a nearly 400strong range of resealable freestanding trade bags providing a core range in a convenient easily merchandisable format. The tub, clam and small retail bag ranges have all been extended to meet the changing needs of the market. There are now over 6,000 products in the Unifix range.
With the full implementation of UKCA upon us shortly, our currently CE marked products will move to have both CE and UKCA. It may take a few months for the new packaging to filter through, but all our products will be fully compliant. The Unifix heritage is backed up by OwlettJaton’s extensive stock holding, nextday delivery in the mainland UK and our ISO 9001:2015 quality and our ISO 14001:2015 environmental accreditations.
With 60 years under its belt, it truly is a brand steeped in history and trusted by professionals for its quality and reliability. We are looking forward to the next chapters in the Unifix story which will see continued investment in innovation to meet the everchanging needs of the market whilst staying true to its heritage.
www.owlett-jaton.com/unifix
// With 60 years under its belt, it truly is a brand steeped in history and trusted by professionals for its quality and reliability. //
The extensive Unifix range has developed over the years, as has its packaging and merchandising options to meet the changing needs of customers
Back in 2020, EISENWARENMESSE INTERNATIONAL HARDWARE FAIR was dealt a severe blow by the closures and travel restrictions imposed by the coronavirus pandemic, with the show cancelled just days before the scheduled event. Two years on and the disruption the lastminute cancellation caused was still a source of consternation with some exhibitors but for many they were ready to put it all in the past and get back to normal operations.
While event organisers everywhere are doing their best to overcome the ongoing travel restrictions and logistical issues that are still hounding the global economy, the team behind the show managed to attract strong visitor numbers who were keen to see what was on offer.
Around 25,000 people from 125 countries walked through the doors at Koelnmesse for the fourday event to see the nearly 1,400 exhibitors from all aspects of the Hardware industry. Yes, the numbers are down on previous shows but given the circumstances, there was still plenty to be positive about. “The sense of relief at finally being able to meet facetoface again after such a long time and do business in person could be clearly felt among all our exhibitors and trade visitors throughout the entire trade fair,” said Oliver Frese, Chief Operating Officer of Koelnmesse GmbH. “You had the feeling that a big family was getting together again after a long time apart. The trade fair was a success, especially in the context of the ongoing travel restrictions in Asia, the acute energy and raw materials crisis, and the geopolitical situation in many countries. The feedback from our
exhibitors about the business contacts they’ve made is positive across the board. Clearly, companies made a strategic decision to attend the EISENWARENMESSE – INTERNATIONAL HARDWARE FAIR – the decision makers were here.”
Despite the event being smaller than previous editions (opinions varied on the reduction of halls), the spectrum of products presented ranged from tools and accessories to building and DIY supplies all the way through to fasteners, fixings and fittings. It was also an appropriate time to launch new products as well, and the team from GESIPA were keen to capitalise on the situation.
“Despite the still ongoing Corona pandemic, the date of the International Hardware Fair in September 2022 was a stroke of luck for GESIPA, as it provided an ideal platform for the successful launch of the new Birdie riveting tool, and the team was particularly pleased to be nominated for EISEN 2022,”
explained Andrea Lawitschka, GESIPA Marketing Services Team Leader. “On the first three days of the fair, especially on Monday, you almost felt like you were back in the old trade fair days. The entire GESIPA stand staff had a lot to do the whole day, everyone was in top form, had a lot of fun and of course they were pleased about the numerous trade visitors from home and abroad. At the same time, there were also many good conversations with exhibiting CAS members and stand neighbours and despite the, let’s call it challenging times, most of the people we talked to were in a predominantly positive mood.”
GESIPA was one of the nominees for the coveted EISEN Award that was presented in cooperation with the Zentralverband Hartwarenhandel (ZHH). From the over 50 innovative products that were submitted, the jury selected this year’s three winners from Picard, SOLAMesswerkzeuge and ToughBuilt. Picard’s carpenter’s tool, the AluTec hammer, boasts a unique combination of aluminium and steel, which provides previously unattainable ergonomics. The second winning entry was the Go! SMART measuring tool by SOLAMesswerkzeuge which brings the analogue and digital worlds together and fulfils the functions of a spirit level, an inclinometer and a protractor in a piece that is just 8cm long. The final EISEN Award winner for 2022 was ToughBuilt with its Scraper Utility Knife. The patented knife allows users to switch between a utility knife and a scraper with the flick of a thumb, a true twoinone.
Innovation is a key thing for any exhibitor to display and Wolfgang J. Kirchhoff, Chairman of the Advisory Board of the EISEN
WARENMESSE – International Hardware Fair was pleased by how much was evident at the event. “The EISENWARENMESSE – International Hardware Fair Cologne is still the industry’s numberone event, where most of its innovations are presented. It’s the trade fair with the strongest international profile, even though many visitors and exhibitors from Asia have been unable to attend due to the pandemic,” explained Kirchhoff.
// The EISENWARENMESSE –International Hardware Fair Cologne is still the industry’s number-one event, where most of its innovations are presented. //
// On the first three days of the fair, especially on Monday, you almost felt like you were back in the old trade fair days. //
While economic uncertainty remains a concern for businesses across the globe, many people at the fair were optimistic about general trade conditions. Dr Peter Wüst, Managing Director of the German Retailers’ Association for Home Improvement, Building and Gardening (BHB e.V.) said, “I’m delighted to be at the International Hardware Fair. The event is absolutely vital for maintaining business relationships facetoface in this period of crisis. Despite the difficult times we find ourselves in, I’m picking up a sense of optimism about the future from the people I’ve been talking to.”
the product. Instead, we look at the bigger picture in terms of sustainability and the customer journey as well as our products,” said Stefan Weigel, Executive Director/CMO at Wolfcraft. “The EISENWARENMESSE – International Hardware Fair is a great opportunity for me to explain this wideranging approach to visitors, so I’m very happy to be able to take advantage of this platform. It’s a source of potential that we, as suppliers of branded products, will continue to draw on in the future.”
So, while businesses are planning ahead and looking to the future, people won’t have to look too far in advance for the next event. A new show, International Hardware Fair Italy – powered by EISENWARENMESSE, will be held on 56 May, 2023 at Fiera di Bergamo. A major international event for the hardware sector that will be held in Italy in odd years, alternating with International Hardware Fair Cologne. The first edition of International Hardware Fair Italy will be a great event for the Italian and European market, especially for those looking to capitalise on the off years in between Cologne shows. The international event is hoping to attract professionals from across the hardware sector for two days of meeting and discussion and has the support of the main Italian and European associations.
Of course, it isn’t just about innovations and the products at the show – although they are obviously a drawcard. Issues surrounding sustainability continue to be a prominent theme and many were keen to explain their credentials, including tool manufacturer Wolfcraft. “At Wolfcraft, we don’t just focus on
Cologne will continue to have its chance to shine and bring people from across the industry together when the next EISENWARENMESSE – International Hardware Fair Cologne returns again from 36 March, 2024.
www.eisenwarenmesse.com
With rising demand for power tools in the market, DK Tools has expanded its range of DK Tools to capitalise, together with a range of free POS for retailers and merchants…
Free POS for retailers as well as online videos are being used to drive custom for the extended range
DK Tools has extended its portfolio of Amtech power tools with 15 new additions to the range, including supporting accessories.
From a 600W quick blade release pendulum jigsaw and 200W 3in1 detail sander to an 18V 2Ah LiIon Cordless Combi Drill and a Cordless Impact Driver, the broad range of new products are competitively priced, says Amtech.
“Consumer adoption of power tools is on the increase and the market is set to grow over the next few years, as such, it makes complete sense for us to unlock this category growth opportunity for our trade customers,” says Product Manager Val Lu. “My rationale for the new range was to include very competitive features at a competitive price point – which is a winwin for both our trade customers and consumers.”
DK Tools has invested in supporting the launch with rich content that includes inuse photography and video. Retailers
buying into the range can also expect free POS when they place their orders via the dktools.com web portal.
Ricky Johal, Head of Marketing and eCommerce, adds: “This is a key launch for the company, so we have created a campaign with the objective of breaking down barriers to entry and using humour to highlight the emotion of feeling empowered. We have also used a lofi production technique for the videos so that they resonate with a wider audience on our Amtech DIY YouTube channel. Additionally, the free POS is automatically added to online baskets and includes QR codes to activate the productrelated content seamlessly between offline and online channels.”
A trade power tools brochure is available on request or when you register to become a stockist at online. You can also enquire via telephone or email.
www.dktools.com
When it comes to surface treatments and coatings it is all about protection, whether it’s from corrosion, the elements or other factors. These coatings and treatments can be done as part of the manufacturing process or onsite as we see from these examples from Dörken and Owlett-Jaton
OwlettJaton is renowned for offering a ‘onestopshop’ service for secondary processing, including surface treatments, coatings, threadpatching, and machining to bespoke drawings.
One of OwlettJaton’s largest customers – a global distributor that provides inventory management to some of the largest companies in the world, recently won a new contract to supply standard and nonstandard fasteners. The contract was to supply a new automotive/yellow goods venture. They immediately turned to OwlettJaton for support for several reasons.
The new contract included hexagon and flange bolting in various grades of steel with several types of plating requirements, including zinc flake (for example, Geomet or Delta Protekt) and Zinc Trivalent Heavy Passivation, along with a range of specially manufactured fasteners.
Zinc flake finishing was introduced into automotive and yellow goods manufacturing to eliminate Hydrogen embrittlement issues when plating highergrade steel fasteners. This treatment offers greater resistance to corrosion than standard bright zinc plating, necessary due to the harsh working environments the products would be subjected to.
The extensive range of stocked products from OwlettJaton fulfilled the majority of items; their dedicated Specials team were responsible for sourcing the balance of nonstocked fasteners.
OwlettJaton’s Subcon team was responsible for decanting the product from the manufacturer’s packaging into stillages, before
transporting the product to their relevant secondary process partners. Once the refinishing of the product was carried out, the product was repackaged inhouse, complete with data on the label containing product code and description, quantity, barcode, and batch reference. The stock is held at OwlettJaton’s warehouse facility and delivered as and when required by the customer on a calloff basis.
Special fasteners often end up in demanding applications, resulting in them potentially requiring additional certification, and this contract was no exception. The customer required Production Part Approval Process (PPAP) and Initial Sample Inspection Reports (ISIR) documentation; OwlettJaton was able to supply them accordingly.
OwlettJaton’s Specials team also provided Country of Origin and full batch traceability to the special products. This is supported by their ISO 9001:2015 quality systems and ISO 14001:2015 environmental management system.
This level of service all adds up to convenience, efficiency, and peace of mind for the customer, ensuring that their requirements are supplied right the first time.
Enquiries should be directed to OwlettJaton’s sales offices or the Field Sales Team. Contact details can be found at www.owlettjaton.com/contact www.owlett-jaton.com
No matter what kind of corrosion protection you need, we have the right tool for you. MKS' Atotech corrosion protection solutions meet and exceed all industry requirements and cover the full spectrum of coating technologies: from pretreatment, zinc and zinc alloy plating processes, as well as zinc flake coatings to a comprehensive range of post-treatment systems with suitable coefficients of friction. The various possible combinations of our exceptional product range ensure outstanding corrosion protection with an attractive appearance and durability. Our unique products, global availability, and unsurpassed service capabilities make us a trusted partner for the fastener industry worldwide.
Learn more about our products at: www.atotech.com
Zinc flake coatings impress with cathodic corrosion protection, in which base zinc sacrifices itself for the underlying material. A low coating thickness, high fitting accuracy as well as an attractive appearance are further advantages of this coating. After pretreatment of the surface, a component is coated. The application technique varies depending on the size and geometry of the component. Possible methods include spraying, dipspinning, rackdipspinning and dipdrawing. The material application is followed by predrying and curing in the oven, during which the coating hardens and becomes a uniform, hard layer.
However, it is not always possible to cure a coating in an oven. This can be for a variety of reasons. On the one hand, the component may be too large or too immobile. On the other hand, there are components which or whose parts must not be exposed to high temperatures. For these cases, Dörken has the ideal solution: The roomtemperature curing zinc flake dries within approximately 60 minutes at an ambient temperature of 20 to 25 degrees Celsius. Forced drying is also possible. Even without a curing process, this solution offers a high level of corrosion protection and, apart from zinc, does not contain any heavy metals such as chromium (IV). With the help of DeltaProtekt® Repair, the roomtemperaturecuring zinc flake coating in the practical spray can, individual defects can also be repaired, or small areas coated.
The roomtemperaturecuring zinc flake has already been able to show what it can do in a very special place. In 2018, the product was used on the Petersglocke in the Cologne Cathedral, which is steeped in history. As the clapper of the bell swung irregularly,
a new mount was developed, designed and produced. In order to safely protect this loadbearing element from corrosion, the experts at Dörken were contacted. The corrosion protection system from the Herdeckebased company is more than able to withstand external influences such as mechanical stress as well as strong temperature fluctuations. Thanks to the roomtemperature curing solution, the 800kilogram component could be coated on site in the bell tower. Now the Petersglocke rings again safely above the roofs of Cologne.
www.doerken.de
Sometimes it is what is on the outside that counts. Our zinc flake systems are suitable for all screws and bolts and hug every thread perfectly. Premium quality that protects against corrosion, sets defined coefficients of friction and withstands a range of mechanical stresses. However, we are not satisfied with the best and are constantly on the lookout for new solutions and innovations – for every problem, for every challenge.
Cross-linking
Harmonised studs and part numbers using the same stud design reduces complexity and contributes to lower TCO.
SEF's Lightweight Steel Studs were designed specifically for modern cars built from different grades and thicknesses of steel
In practical terms, lightweighting vehicles has led to mixing different types of metals. Traditional fastening methods have not proved suitable for bonding these dissimilar parts to each other, explains STANLEY® Engineered Fastening
As the shift from traditional internal combustion engine (ICE) vehicles to electric vehicles (EV) is rapidly occurring, the automotive industry is seeing its most significant transformation since the introduction of the assembly line in 1913. But with great change comes great complexity… and competition.
The EV revolution has opened the doors to new automotive OEMs and suppliers, as the market and component needs change alongside the industry shift. One key driver of the electric vehicle future is the need for more sustainable methods of transportation in terms of fuel economy and reduced CO2 emissions. Over the past several decades, automakers have
pursued vehicle lightweighting to meet the increased demand of standards and regulations placed on ICE vehicles – and that concern becomes even greater with electric vehicles.
Due to the extremely heavy battery pack, EVs must prioritise lightweighting across all facets of the vehicle to achieve key consumer benefits of extended range, better handling, increased lifetime of the battery and more. One way to implement lightweighting for EVs is by using a variety of different materials for the various parts of a vehicle’s subassemblies.
Mixing different types of metals with aluminium, magnesium, plastics and composites allows each component to be made of the material that best suits its purpose. Traditional
fastening methods are not suitable for bonding these dissimilar parts to each other. As a nohole fastening and mechanical joining technology leader, STANLEY Engineered Fastening’s Tucker® stud welding and selfpierce riveting solutions can be used to reliably connect these materials to each other with ease and efficiency. And with the new Tucker CleanJet, lightweight aluminium material can be prepped by spot cleaning the surface just prior to the welding process for superior weld results and joint strength.
At the stud level, SEF’s Lightweight Steel Studs were created specifically for modern cars built from various grades and thicknesses of steel. This revolutionary stud offers up to 70% less spatter, increased equipment life, longer maintenance cycles, better fit, and better appearance. Harmonised studs and part numbers using the same stud design reduces complexity on the studportfolio as well as equipment spare part needs, both contributing to lower TCO.
The more that can be done to reduce the weight of electric vehicles, the faster they will find consumer acceptance in today’s marketplace. Lightweighting can be a major contributor to reduced cost, improved range, increased performance and more efficient assembly of the current and upcoming generations of electric vehicles – and STANLEY Engineered Fastening is at the forefront of the EV lightweighting movement, continuing to develop and improve technologies to support this shift to a new mode of propulsion.
STANLEY® Engineered Fastening – a division of Stanley Black & Decker – is among the global leaders in precision fastening and assembly solutions, helping revolutionise the industry for nearly 100 years. Our industryleading brands, Avdel®, Integra™, Nelson®, Optia®, POP®, STANLEY® Assembly Technologies, and Tucker®, represent a diverse portfolio of fastening and assembly products and solutions and empower engineers who are changing the world.
//
REVOLUTIONARY STUD OFFERS UP TO 70% LESS SPATTER, INCREASED EQUIPMENT LIFE, LONGER MAINTENANCE CYCLES, BETTER FIT AND BETTER APPEARANCE.
Spurred on by developing government sustainability regulations and consumer demands to go green, many automotive manufacturers are investing in sustainable technologies. With the automotive sector contributing to a significant portion of global emissions, suppliers and engineers are working with EV innovators to boost their production and lessen the sector’s carbon footprint.
The EV industry is currently dominated by range anxiety and lightweighting issues, so manufacturers are prioritising parts that enhance conductivity, optimise insulation and reduce weight, including the smallest of parts. Knowing that each part contributes to a vehicle’s overall performance, manufacturers are now sourcing specialised, lightweight fasteners for EV, alongside components like cable glands, rivets and strain relief bushings.
EV manufacturers are acutely aware of the negative impact that external temperatures can have on vehicle performance. With excessive heat and cold damaging battery health, typical EV fasteners are comoulded with polymers to optimise insulation and prevent deterioration. Lightweight materials like aluminium, titanium and magnesium are often bolstered by materials like CuCrZr (chromium zirconium copper) to enhance conductivity, while connectors and components are required to cope with temperatures as extreme as –40 to 140 degrees Celsius.
Electric vehicles clearly pose new challenges for the automotive industry, and customers especially are concerned about range and charging capabilities. With the number of electric vehicles massively outweighing the number of charging points, there is a clear need for electric infrastructure, but the same conductivity and lightweighting requirements apply.
Formed over 100 years ago, manufacturer and distributor Optimas Solutions has supplied a diverse range of automotive manufacturers over their time, but is now witnessing a considerable uptick in the supply of fasteners and CClass components for EV manufacturers.
The automotive industry requires especially stringent quality standards, and suppliers are working not only to provide optimised parts for EV use, but ones that will stand up to durability
and safety checks. Committed to a zerodefect culture, Optimas work with its suppliers to continually improve their product performance and mitigate process or product risk, addressing both industry specific and customer requirements.
Director of UK Business Development at Optimas Solutions Simon Wright comments: “‘As a company that actively promotes sustainability in manufacturing and has worked closely with the EV industry, Optimas is providing premium fasteners and components to electric innovators. Our product expertise and engineering experience are helping these manufacturers to boost their productivity and meet demand.”
EV manufacturers also require complex and bespoke solutions for their vehicles, with many attempting to revolutionise the market as a way to address range and lightweighting concerns. Optimas’ team of global fastener engineers work with manufacturers from product development to assembly line to reassess their products, aiming to improve performance and cut costs through performance testing and prototyping.
Bolstered by decades of manufacturing experience, expert engineers and an indepth knowledge of industry standards, Optimas is wellsuited to working with increasingly complex EV requirements and is embracing the challenge.
international.optimas.com
EVs may seem revolutionary for consumers and businesses making the switch from petrol and diesel vehicles, but for many of the automotive industry’s long standing supply partners, the change has been far more gradual.
The construction methodology and assembly approaches for the raft of boldlydesigned and futuristiclooking electric vehicles that we see on the market today – as well as those which subtly disguise the fact that they are any different from their fossilfuel powered predecessors – are largely the result of an evolution which EJOT has been supporting since the 1970s.
The primary market for EJOT’s industrial engineering thread forming screws is historically automotive. The reason behind this relates to the features and benefits common in all EJOT fastening products – parts rationalisation, to reduce the numbers of fastening products needed in assemblies, allied to higher joint strength performance.
These dual benefits are as applicable to EVs as they are to combustiondriven vehicles, but there are some obvious mechanical differences which has meant supporting manufacturers to deploy proven fastening solutions to new assemblies throughout the vehicle.
A perfect example of this is in relation to the motor and electronic control unit (ECU) which EVs use instead of a conventional powertrain. This ‘command centre’ of the vehicle requires fasteners that will enable printed microcircuit boards to be secured into a light aluminium casting, which is an application EJOT’s micro screw range can comfortably accommodate.
These threadforming screws have actually been available for at least 25 years, originally used on Ericsson and Nokia mobile phones, providing performance at a miniaturised level that designers would normally expect to achieve with much larger screws. As a result, it represents an effective alternative to soldering, gluing, clipping or welding.
Other key EV technology applications that are benefitting from established EJOT fastening technology include the connector housing for DC adaptors, the HV/LV filter in the power electronics and for both the WR and PWR – DC/DC Units. One major German vehicle manufacturer is using the EJOT ALtracs Plus, a selftapping screw for light metals, for all
The development of electric vehicles continues at pace. One company that has been embedded in the evolving automotive sector for decades is EJOT, helping facilitate those changes. Steve Wynn, UK Sales Manager for Industrial Fastening Solutions at EJOT UK, explains more…
these applications, while another is using the EJOT Delta PT, a screw for direct use with thermoplastics, for fastening the battery pack and WR DC/DC unit.
Battery packs have been a particular application focus over recent years – for obvious reasons – and the strengths of the Delta PT are increasingly being realised. In fact, one prestige car manufacturer specifies this screw for several batteryrelated applications, including for fastening the lithium battery, the onboard charger circuit board securement and as a casing fastening for the battery.
Development of the power technology required to make EVs a realistic alternative to combustion engine vehicles has run in parallel with innovation in how the vehicle structure and body is built. The key reason for this – as with petrol and diesel powered vehicles – is to reduce weight so the vehicle range and fuel efficiency can be maximised.
For several decades climate change has been the driver for government policies around the world to reduce CO2 emissions and the development of electrification commercially has been part of that drive. In Germany, where the EJOT Group is based, our development teams have been working with vehicle manufacturers and academic institutions as part of that development process in recent decades.
Fastener development, product modifications and new joining systems allied to differing vehicle construction materials and methods have all evolved during this period and they are part of the electrification ‘revolution’ we are already seeing.
Engineering for the EV sector is about the need to ‘build lighter, build stronger’ which in turn has seen the advancement of many new engineering materials. Carbon fibre is the obvious example – light, versatile but high in strength.
EJOT’s product range has responded accordingly with the development of products such as EVO PT. This innovative selftapping threadforming screw is the latest generation of the PT which revolutionised fastening into thermoplastics in the 1970s. It has the benefit of an optimised locating point and depth independent installation torque, enabling a uniform tightening torque in production at different screw lengths.
Another technology with great EV potential – already used by the automotive sector for conventional vehicles – is EJOWELD. It is an example of how EJOT has worked to develop joining systems outside that of thread forming technology.
EJOWELD is a friction weld system that was developed in conjunction with a premium German vehicle manufacturer who sought to take weight out of traditional vehicle design. Its solu
tion was to deploy high strength boron steel as the core structure for bodyinwhite structures. It was a move that would offer extreme strength benefits in a much thinner material than those traditionally used, but it demanded a new approach to joining secondary alloys to the main vehicle body – hence EJOWELD, a unique friction weld system, was developed.
But it is not just the vehicle body where weight reduction is sought. The increased use of lightweight foam and composite materials with a good strengthtoweight ratio, which has been an ongoing process in vehicle manufacturing for decades, has also demanded new fastening solutions.
EJOT has responded with the TSSD, a thermal adhesive bonding boss which provides a secure boss for the EJOT DELTA PT screw or a direct fastening element, and EJOFORM bespoke cold formed fastening elements. The virtually unlimited application potential offered by EJOFORM means designers can consider lightweight materials in all kinds of assemblies where previously the ‘how do we attach it?’ question was a barrier – such as for the locking system on doors and the trunk lid or engine covers.
Through a continuous R&D programme and close partnerships with designers for many of the world’s major vehicle manufacturers, EJOT is at the forefront of fastening solutions that will enable ever lighter and more efficient EVs.
Designing mechanical joining systems for thinner and more lightweight materials requires solutions that can accommodate the increased flexibility that these materials bring. This requires EJOT to work years in advance of new vehicle assemblies to ensure the joining technology is tested and available for when the need arises.
As EVs become the norm, so too will the need for charging points in the home and in all appropriate public and commercial locations. Hence, suppliers will inevitably move into mass production of these units. Up to 50 fastening elements are used in home wall charging stations, which is one of the reasons we are seeing increased demand for EJOT’s EVO PT screws, which enable direct fastening capability in plastics. And this screw comes with the support of EVO CALC, a prognosis program that can be used in the development phase for advance computation of the screw joints saving time and costs.
Find out more about EJOT’s fastening solutions and technical support for the automotive sector at www.ejot.co.uk. www.ejot.co.uk
A typical application for EJOT fasteners is in the power electronics in EVs
Production lines are busy places to be and tools need to be powerful, efficient and easy to use to keep up with the fast pace and intensive demands. We look at some of the production line tools hitting the market.
From the advent of the wind industry, hydraulic torque applications have been paramount in delivering the high levels of torque required to ensure the structural integrity of the tower, nacelle and blades. More recently, construction firms have been reducing the number of hydraulic wrenches being used, in favour of electric and batteryoperated torque tooling, primarily due to cost, speed and ease of use.
However, with the latest offshore wind turbines being much larger, capable of generating up to 14MW of power each, much bigger bolts and higher torque values are necessary, so the need for hydraulic torque equipment has returned to the fore. With safety, performance, ease of maintenance, quality and costefficiency being key drivers for turbine operators, Atlas Copco, a world leader in continuous rotation tooling, has invested significantly in the development of its hydraulic wrench offering.
According to research by the International Association of Oil and Gas Producers in 2021, 35% of injuries sustained were caused by tool handling incidents or dropped objects. Over 80% of these were in environments where hydraulic torque was used.
Innovation within the hydraulic torque market has been limited. But challenging the status quo through customer driven innovation, Atlas Copco has launched a brandnew hydraulic torque wrench line, called TorcFlex™. Designed specifically to provide greater value in terms of ergonomic safety, accuracy, performance and costefficiency for multiple industry applications, TorcFlex™ models include the TF Square Drive Tool and TFX Direct Fit Tool. These are complemented by a marketfirst CoAxial single hose and coupling, that’s over four times faster in setup than previous generations, with better manoeuvrability and zero risk of hose tangling with free moving couplings.
Capable of delivering torque levels over 43,000Nm on the Direct Fit Tool and 35,000Nm on the Square Drive Tool, TorcFlex™ addresses both assembly and maintenance demands of major turbines, maintaining a tool accuracy of 3%, while focusing on the user’s experience and prioritising safety.
One of the most innovative features is the retained reaction arm. Other available wrenches have a reaction arm that needs to be fully disengaged before being repositioned on the application. This is time consuming but also a dangerous drop hazard. Working at height is an obvious risk, so having a retained reaction arm that can be easily transferred increases safety for everyone.
TorcFlex™ also features an integral square drive retainer. Instead of a separate drive retainer, which must be removed and reengaged when changing direction, Atlas Copco’s square drive assembly is now a single piece with a springloaded button mechanism, which allows the user to change direction easily.
All hydraulic wrenches are also supplied with a new innovative support handle. The handle can first be positioned in multiple positions on the wrench, but then the head can be indexed by the operator, without it being removed, like all other designs. As it’s supplied as standard and not an accessory, safety is again being prioritised.
To find out more about Atlas Copco’s safer, quicker and smarter high torque applications for the wind energy sector, visit: www.atlascopco.com/en-uk/itba/industrysolutions/energy/wind-energy www.atlascopco.com
//
Copco’s square drive assembly is now a single piece with a spring-loaded button mechanism, which allows the user to change direction easily.
The JRP battery rivet gun tooling is made for performance as it’s not only the lightest on the market but also offers the highest powertoweight ratio, it says.
In the last five years, the battery rivet gun tool market has seen considerable growth in the production line sector. Manufacturers are consistently looking for new technology that is fast and reliable to help improve efficiencies. When developing their riveting brand Jaton Riveting Products (JRP), OwlettJaton carried out months of rigorous testing in the UK to identify the best type of tooling to offer alongside their extensive range of rivets and rivet nuts.
Hand tools are small and easy to move around, but installation can be slow, and their use is limited when used repetitively in a production process due to labour impacts. Pneumatic tooling lacks portability and requires considerable investment. Dragging air hoses through manufacturing plants is cumbersome, and extensive maintenance is essential for stability of position and control of speed. While both hand tools and pneumatic tooling will continue to have a part to play in production, it’s easy to see why battery tooling is growing in popularity in production line assembly.
Initially, a small range of JRP hand tools was launched, aimed at smallerscale installers. To complement the hand tools, four battery tools were launched soon after. Tested by experienced window fitters, roofing and cladding contractors, automotive/rail metal fabricators and light/heavy commercial vehicle builders, the feedback received included the ease of
use, speed of use and lightness.
The ergonomic tool and battery design result in a fantastic weightsaving combination. The four battery tools are not only the lightest rivet gun tooling but also some of the most compact powertoweight ratio tools to be introduced to the marketplace. JRP’s most popular rivet gun, the RB65, weighs 33% less than its competitor equivalent, the brand says. The NB80A is 37% lighter than its likeforlike counterparts.
Fast and reliable, the JRP battery tooling range can help to speed up production in multiple industry sectors. Their portability makes them ideal for use on internal or external components in production line assemblies. The LED display settings on the tools allow manufacturers to set a tool up accordingly for the applications and thread diameters they are to be used on, that way they can ensure the tools are used correctly and optimise battery and shelf life. The uniform battery system for the JRP range allows the batteries to be used on all tool models, prolonging battery life and reducing recharge costs and tooling inventory.
The tools are powered by an 18V 2.0Ah Liion battery designed to give higher performance and increased runtimes of almost 120 minutes, depending on the tool model and fasteners being set. Unlike comparative tools on the market, JRP’s tools come with two batteries. With a recharge time of less than 30 minutes, manufacturers can rely on the tools for continuous use without purchasing additional inventory.
www.jrprivets.co.uk
// Fast and reliable, the JRP battery tooling range can help to speed up production in multiple industry sectors.
Panasonic’s nextgeneration transducerized mechanical pulse tool, the AccuPulse 4.0, was designed to help manufacturers improve quality control and accuracy, increase energy efficiency and safety, and collect data on the assembly line while reducing costs.
Built with four onboard microcomputers and a transducer to intelligently manage torque, motor control and wireless communication, the ultimate lightweight and high torque AccuPulse 4.0 meets the needs of manufacturers for an Industry 4.0compatible assembly solution. As an energyefficient and ecofriendly tool, the AccuPulse 4.0 reduces annual maintenance costs compared to competing pulse tools.
“Panasonic’s AccuPulse line of cordless mechanical pulse tools was specifically designed with worker safety in mind, to allow for freedom of movement and flexibility, and greater production efficiency in a compact, high quality solution,” said Aziz Lokhandwala, Senior Product Manager for assembly tools at Panasonic Eco Systems North America. “With the AccuPulse 4.0, we have enhanced features and expanded the bene fits to provide one of the most advanced cord less mechanical pulse tools in industries where high torque precision fastening is required, including but not limited to automotive, aviation, farming and construction equipment. The built intelligence and advanced program ming of the AccuPulse 4.0 will allow the quality engineer to monitor and control performance on site and remotely. The reactionless ergonomics and durability of the tool will foster a healthier and safer work environment.”
na.panasonic.com/us
mechanical pulse tools was specifically designed with worker safety in mind, to allow for freedom of movement and flexibility.
The demand for prefabricated homes has increased because it offers a lower carbonprint on the environment in light of rapid population growth. Everwin Pneumatic offers a full tool recommendation guide to equip the most efficient nailers and staplers to these busy production lines. Everwin tools are uniquely engineered for high volume industrial applications. Whether a manual production line or an automated assembly line with machinemounted operations, Everwin provides a solution at every stage of the manufactured construction process.
ing a bypass rapidloader cap magazine, a steel back cover, and an industrial tool free jam clearance. It ensures that these extra layers of air control will keep temperatures constant.
For further sheathing and plasterboard, the SN50 series heavy wire staplers is offered in multiple variations specific for a production line’s need. Designed with a long magazine kit to hold 480 fasteners, or a machinemounted version equipped with RCVA1 or RCVA2 remote control trigger valves, or even a full automatic version driving up to 20 staplers per second. The result is
The first stage of manufactured housing is framing assembly. This sees that the lumber is secured on the joists and also that OSB or plywood is securely fitted to the frames. Whether a line uses a gantry or manually, it requires a heavy duty framing nailer. This can be a FSN34100LM, a framing stick nailer with an extended magazine, open nose design, and singlepiece caste cap assembly that prolongs tool lifespan and minimise maintenance downtime. Another option can be a PN80/90 PAL machinemounted coil nailer. Bolstering a high flow driver guide, remote control valve, and a jumbo magazine holding fasteners dependent on the users’ need. It is designed for powerful high volume repetitive use.
The second stage will see insulation layers fitted as well as exterior sheathing secured. The FSN9240BC, an 18 gauge cap stapler ensures that more surface area is held in place. Featur
more loading capacity and less downtime on a production line.
For window press installation, the FN1850 brad nailer is engineered with a robust construction for the industrial environment. An aluminium extruded sideload magazine with a composite rear cover, as well featuring an industrial tool free jam clearance. The hybrid safety allows precision nail placement and a nomar pad which is 30% more compact than other models in its class. The result is a clean finish on intricate trim work.
While the manufacturing housing market has been predicted to grow, it requires an efficient production line to keep up. Everwin offers the industrial grade tools to keep up with the users demand and provides a solution guide that keep up with innovation.
www.everwinpneumatic.com
The woodworking industry has always been a dangerous place to work – the industry is second only to farming in terms of accident rates.
Each year, around 12,000 people in the UK die from workrelated lung diseases linked to past exposure to hazardous substances at work. That figure includes dust exposure. Back in February 2022, HSE (Health and Safety Executive) released a report that showed over 50% of the 200 woodworking businesses they visited in the last two quarters were breaching dust exposure regulations.
Whilst dust exposure doesn’t sound too threatening on the surface, it can actually lead to occupational asthma, lung disease, and even cancer.
“We’ve suspected for a long time that the LEV (Local Exhaust Ventilation) side of workshops could be improved generally throughout the UK,” says Alex Dalton, Director at Daltons Wadkin. “From my own experience as a salesperson in the early part of my career, going into different businesses to talk about different machine solutions, it would not be uncommon to walk in and see piles of wood chippings and high dust accumulations on work surfaces and window sills.
“Without making any excuses, it’s the way the industry has been for a long time. It’s very traditional – the methods followed now were also followed years ago. There’s been a real lack of progression given the modern data and findings we now have access to.”
Wooddust inhalation is included in the figure of 12,000 people dying yearly from workrelated lung diseases. But what is it about dust that causes these health issues?
Essentially, fine dust particles (known as respirable dust) can easily be inhaled into the nose and pharynx. In industries like manufacturing, avoiding inhaling these particles is practically impossible. Over time these particles will build up, and take up space in workers’ lungs which will eventually cause blockages in their chests.
These blockages may initially present themselves as breathing problems, but if nothing is done, these issues could turn into lifethreatening respiratory disease.
In fact, it’s not uncommon for inhalation to cause occupational asthma and in the case of hardwoods, sinonasal cancer.
Employers working with woodworking equipment know that they have to have their LEV systems checked every 14 months, but with deaths and safety breaches becoming more common, it has led the industry to wonder whether regulations are truly being followed.
“A lot of systems are designed and installed to service a certain number of machines but over time workshops evolve, equipment is added, and dust extraction systems modified inhouse along the way.
“When that happens you can lose efficiency very quickly and expose workers to excessive amounts of dust in the workplace. It’s a slippery slope.”
“It can be extremely obvious that large volumes of dust are being created, but in other situations, it isn’t quite so obvious. Regardless, it is still there, still airborne, still present and workers are breathing it in all day.”
It’s a law that all woodworking machinery should be LEV tested at least every 14 months, but Daltons Wadkin recommends that LEV systems should be tested every year.
Beyond that, they always encourage customers to opt for a fully integrated LEV system. These are standalone, purposedesigned, extraction systems with externally located collection bins complete with purposebuilt ducting and manifolds to suit each machine. Flow rate gauges can also be installed at each machine to give operators a quick visual indication of whether the system is working optimally.
The solutions are clear, but if the whole industry doesn’t make active improvements to deal with dust exposure and extraction, then the problem will only get worse.
There’s more information about dust exposure if you use the QR code below.
https://www.daltonswadkin.com/dust-exposure-weneed-to-stop-ignoring-this-silent-workplace-killer/
With reports that many woodworking businesses breach regulations in the UK, industrial woodworking manufacturer Daltons Wadkin highlights the dire consequences and advocates for improved precautions…
Dynamic markets, shorter production cycles and requirements from lean management are radically changing the procurement of C-parts. In demand are more efficient solutions in production supply in order to devise processes that are simpler and more cost-effective.
Our C-parts management makes your processes fit for the challenges of the future! Get in contact with us.
Magdrills are a staple in metal construction, required to drill larger bolt holes on the girders and RSJs, with most major industrial buildings using steel frame construction
Most trades would happily point out the major plus points of FEIN’s range of worldbeating oscillating tools – the MulitiMasters. And I would agree with them. My battle scarred MultiMaster Supercut is always included in the kit I take onto the jobsite because it is my number one getoutoftrouble tool that can do things other tools can’t, as well as a lot of things that other tools can – like detail sanding, for example.
Looking back over the last thirty years or so, users could have been forgiven for thinking that FEIN only focused on MultiMasters, helped by the company making a superb job of constant innovation that ensured that each generation of MultiMasters was better than the last. From the QuickIn system to Starlock (in cooperation with Bosch) FEIN has still got a nose ahead of the competition in my view, despite the patents for oscillating tools having run out.
But to take an even longer view, FEIN has actually been making tools for over 150 years, and has been credited with the invention of the world’s first power tool in 1895. Also, the company has traditionally had a focus of expertise in the metalworking industries, so in fact, the MultiMasters were a lucrative and innovative sideways step. Now that the market supports multitools from just about every major power tool manufacturer, FEIN has decided to refocus, using its vast metalworking knowledge and expertise.
Some quick stats: FEIN is a worldrenowned power tool manufacturer with 900 employees, 530 of which work at FEIN HQ in Germany. It has over 800 active property rights and 500 patents and applications and is well known for consulting customers about their needs and possible solutions.
Perhaps best known for its oscillating tools in recent years, Peter Brett examines the metalworking heritage of FEIN and its newly relaunched KBE 32 magdrill for work on-site…
// FEIN has been making tools for over 150 years, credited with the invention of the world’s first power tool in 1895. //
The current FEIN range covers grinding, polishing, drilling and cutting metals and we were sent one of its most recentlylaunched tools, the FEIN KBE 32 magdrill, to put through its paces. Magdrills are a staple in metal construction, required to drill the larger bolt holes on the girders and RSJs that even relatively modest kitchen extensions seem to need these days. And, of course, most major industrial buildings use steel frame construction.
By listening to customers and their needs, FEIN soon worked out that they wanted lightweight and compact to be part of the spec for a new magdrill. Add “easy to use and robust” into the equation and you have a set of competing priorities that would make designers scratch their heads.
‘Lightweight’ is a relative term when it comes to magdrills. Ferrous magnets are inherently heavy, and they need to be large enough to hold a drill firmly in place on a girder as it drills. I can’t imagine the damage a magdrill could cause if it fell from height for any reason. The KBE 32 has very efficient magnets and a compact cast alloy body for strength and lighter weight. I noticed how slim the body was when I operated the switchgear – my hand could come at the switches in three directions and was also easily able to operate them. This feature is important because there are many occasions when the drill will be used in tight spaces.
The three switches are also carefully designed to feel different from each other so that your fingers soon learn to differentiate between them. You really don’t want to switch off the magnets by accident…
The HSS cutter supplied with the KBE 32 proved to be very efficient. It routinely cut through 5 or 6mm steel in about 30 seconds
Hole in one: Our tester cut through 5 or 6mm steel in 30 seconds with the KBE 32
// The KBE 32 has very efficient magnets and a compact cast alloy body for strength and lighter weight. //
per hole. Users, I think, couldn’t complain about that rate of cut.
Although it seems like a bit of an afterthought, the system for delivering lubricant to the cutter is, in fact, a practical and efficient method wellsuited to the functions of the drill. A squeezy plastic bottle can be attached to the body with a flexible tube that connects to a nipple mounted directly above the cutter so that the lubricant flows straight onto it.
The operating handle has the usual refinements necessary, like the fact that it can be mounted on the left or right of the body and each individual handle can be unscrewed to allow access to tight spots.
A large plastic case with metal latches houses the drill, and it has enough space for the whole tool, handles, cable and all to be packed away easily at the end of the job.
I spent a very interesting hour down at my local steel fabricator playing with the KBE 32. As a very experienced and skilled steel man, he was initially keen to point out the KBE 32’s ‘faults’ like its lightweight and small size. But when he tried it out, some of the objections faded. He conceded that it worked very well and commented on how relatively quiet it was.
He liked the arrangement of the switches, even calling his apprentice over to test his reaction. When I explained that it was meant to be as lightweight and compact as possible he also agreed that there was definitely a place in the market for such a machine.
As I packed the KBE away he was looking over my shoulder, and commented on how good it was that the whole machine fitted into the case – accessories and all.
I think that is an example of victory going to the FEIN Orange corner. Its design brief criteria met and a justification for looking at “old” products in order to see how modern methods and materials can still produce improvements. www.fein.com
// A large case houses the drill, with enough space for the whole tool, handles and cable to be packed away easily at the end of the job. //
Based in Jiaxing City, between Shanghai and Hangzhou, Cavort is a manufacturer of fasteners and hardware. The firm produces standard fasteners as well as customised specials, according to customer requests.
Founded in 2008, the firm was originally known as Cixi Cavort Hardware, moving to Jiaxing in 2014 and changing its name. Now it produces bolts, nuts, selfdrilling screws, drywall screws, washers, thread rods, blind rivets and more, working mainly in carbon steel and stainless steel.
A trading company as well as a manufacturer, Jiaxing Cavort manufactures around 300 tonnes of screws per month via 50 sets of production machines, operated by circa 20 staff. “In total, we manufacture and trade a volume of about 1,000 tonnes a month in a stable, typical period,” the firm tells Torque Magazine. Much of that volume goes to the construction sector and for furniture hardware systems.
Since it set up in 2008, Jiaxing Cavort has been geared up solely for export, with the firm particularly busy serving South America, including Mexico and Brazil, as well as Europe, including Poland.
The firm can provide special packaging depending on customer requirements, with extensive QC facilities and partnerships to ensure consistent quality and timely deliveries.
We hear a lot about recent supply chain disruption from the perspective of Europe and North America, but how does a Chinese fastener producer and trader view the recent difficulties?
“Covid19, from the start of 2020, the war between Russia and Ukraine as well as USA raising interest rates, these have all made business soft and disrupted the supply chain,” the firm tells Torque Magazine
“From my view to fight the current situation, we should persist in improving our quality and keep on working through the difficulties. In the end, the world needs our products.”
www.nbcavort.com
Master Builders Solutions introduces a customisable, environmentallyfriendly concrete repair system designed to increase versatility, efficiency and ease of use on job sites – without separate, dedicated products that serve each need.
The first of its kind in the industry, MasterEmaco® OneMix™ Concrete Repair System consists of one universal bag of base material that can be used in horizontal, vertical and overhead applications by adjusting the water demand. Additionally, combining the base material with six specialised Power Paks™, creates 120 different products.
“We strive to lead the concrete repair industry, bringing our customers innovative and highquality solutions,” said Konrad Wernthaler, Senior Vice President of Construction Systems at Master Builders Solutions. “We're excited to introduce MasterEmaco OneMix because the system provides highperforming concrete repair products, reduces project complexity and optimises storage space.”
done.
Using the MasterEmaco OneMix system is simple and intuitive.
ADDITIONAL BENEFITS INCLUDE:
• SUPERIOR PERFORMANCE
MasterEmaco OneMix Concrete Repair System provides increased durability compared to other products.
•
Contractors can quickly and easily create a repair material suitable for many different applications, on the spot.
• QUALITY ASSURANCE
Each Power Pak has a unique visible tracer that is easily identifiable, even post application to ensure an appropriate installation.
• REDUCED STORAGE AND JOBSITE COMPLEXITY
Rather than storing multiple repair materials, contractors can use the same universal base material for many job types.
•
The small Power Pak size reduces waste. Additionally, because the Power Paks are smaller and customisable, contractors only use what they need.
MasterEmaco OneMix Concrete Repair System is available in the US and Canada.
www.master-builders-solutions.com/en-us
Waferthin or strong as Hercules, adhesive tapes are allrounders with unexpected superpowers.
The team at tesa have heroes who they love and celebrate – their tesa tape heroes: products with unique capabilities. The tesa FireGuard is one such hero, an unassuming patch that offers fire protection.
tesa® FireGuard is a fire containment sealing patch developed specifically with safety of electric vehicles in mind –withstanding flames of up to 500°C for more than five minutes, tesa® FireGuard protects the passenger compartment so that people in the car can exit the vehicle safely in the event of a battery fire in an electric car. The tape is part of the company’s series of special sealing solutions for the automotive industry that are used to seal holes in the vehicle body and will last as long as the vehicle itself.
The FireGuard tape was developed to permanently seal openings in the vehi cle body that are exposed to direct heat, helping auto manufacturers to meet stringent GTR 20 standards for electric cards.
With over 7,000 adhesive solu tions, tesa has products tailored to the automotive, electronics and construction industries as well as the paper and printing trades.
www.tesa.com/en-in
Sometimes the smallest things can cause the biggest headaches and whether its a much-needed repair or the finishing touch to complete a task, there will always be a need for some form of adhesive, sealant, tape or filler to get the job
Henkel has opened its new Inspiration Center Düsseldorf (ICD) following an investment of 130 million euros. The Adhesive Technologies business unit has built a stateoftheart and global innovation and customer centre with a floor area of 47,000 square metres. The ICD provides space for 30 laboratories, four technology centres and more than 650 Henkel experts. The new building also serves as a global customer centre for Adhesive Technologies to present its entire portfolio of adhesives, sealants and functional coatings and can work on new solutions together with customers from over 800 industry segments.
“The ICD marks the largest single investment in our company's history and is a key element of our strategic framework for purposeful growth. With this stateoftheart building, which is unique in the industry, we have created the infrastructure to take the innovation capabilities of Adhesive Technologies to the next level,” said Henkel CEO Carsten Knobel. “In 1922, Henkel started producing adhesives for its own use – today we are very proud to celebrate another milestone in the 100year success story of Adhesive Technologies, which will further expand our leading position in the adhesives business. As such, the ICD is a prime example that embodies both our pioneering spirit for sustainable action and our longterm entrepreneurial thinking.”
“The ICD reinforces our commitment to further strengthen our globally leading portfolio and knowhow in materials science and to create value for our customers,” added JanDirk Auris, Executive Vice President Henkel Adhesive Technologies. “The ICD brings our entire portfolio to life for our customers and enables close collaboration with them and with external partners on novel futureoriented solutions. Our focus is particularly on sustainable innovations that contribute, for example, to CO2 reduction for our customers or to new solutions for a circular economy.”
Within the new building’s seven levels are 30 laboratories with various research and testing facilities, as well as four technology centres with doubleheight rooms that house pilot production lines and equipment for largescale applications such as in the automotive industry or for engineered wood. The laboratories are modular and can be adapted quickly and flexibly depending on the research and development task and to support collaboration between teams.
The heart of the building is a large lightflooded atrium including a coffee bar, which promotes the exchange of ideas between employees and provides space for events with partners, suppliers, customers, universities and startups. The ICD is the most sustainable building at the company's site in Düsseldorf. It is designed to be resourceefficient, has a rainwater collection system, highly efficient refrigeration technology and meets the highest building insulation requirements.
Henkel Adhesive Technologies is globally leading with highimpact solutions in adhesives, sealants and functional coatings. The business unit supplies more than 100,000 customers in over 800 industry segments with customised products and technologies used in a wide range of consumer and industrial goods.
The central focus of Adhesive Technologies' innovation activities is on developing sustainable solutions for its customers. The business unit is consistently working on products that enable resource efficiency in production and during use throughout the entire life cycle and that are based on renewable or recycled raw materials. In addition, Henkel offers a growing portfolio for the recyclability of, for example, packaging or consumer goods and the repairability of everyday products and is working intensively on new debonding solutions to drive efficient debonding of a wide range of materials across industries, thereby increasing longevity and recyclability.
www.henkel.co.uk
// The ICD reinforces our commitment to further strengthen our globally leading portfolio and know-how in materials science. //
ENGEL GmbH has successfully launched its own timber construction screw E-Jet® X, the newest member of the well-established E-Jet family
ENGEL was founded in 1949 as a mediumsized family wholesaler, and prior to 2013 was providing over 100,000 items for the industrial and trade markets. Besides standard parts in fasteners and high quality special and drawing parts, innovative Cparts management was also a key reason to choose ENGEL as the reliable procurement partner for secure supplies.
Then, in 2013, the first EJet® was launched, the first of ENGEL’s own brands. This wood construction screw with ETA approval has a diameter range from 3 mm up to 6 mm with a maximum length of 300 mm, and a special designed Jetta bit.
“It was quite clear, also due to the fact that ENGEL was always well known for distributors focused on the timber construction, that the range of screws focused in this area had to be extended,” says Daniel Kamp, Head of Sales Trading at ENGEL. “So, the idea for the EJet® X timber construction screw was born.
“The market launch at the end of April 2022 came during the critical and dramatic situation in the Ukraine, the already longlasting difficult supply market situation and the energy crisis.”
The brandnew EJet® X timber construction screw combines useful properties, including for structural timber engineering and the fastening of onroof insulation systems, paired with the highest quality standards. The European Technical Assessment (ETA) with CE marking makes the EJet® X suitable for the most demanding design requirements.
The user benefits from fast, practical processing in combination with an outstanding surface appearance. Available in both countersunk and wafer head designs, a diameter range of 68 mm and a maximum length of 400 mm, the new EJet® X timber construction screw offers a great deal of flexibility.
“Despite the fact we did not have the ideal market situation for a new product launch we are very satisfied with the turnover results. But we also have to be vigilant to ensure the delivery performance in order to meet the current market demands,” emphasises Kamp.
And ENGEL also has many plans for the future: “We will expand our family of brands little by little, to be a reliable and strong partner for our worldwide distributors, especially with fasteners specialised for wood construction,” he concludes.
www.schrauben-engel.de
Wafer head High head pull-through values and a better contact pressure.
Countersunk head with milling ribs Clean, flush countersinking of the screw in the material.
Reamer shank
Reduces the effort required for screwing and battery life.
Coarse thread Easier screwing and minimising of splintering and bursting of the wood.
Cotting edge with serrated thread Better bite in the material, faster processing and a reduction in the slitting effect. Screwing in softwood is possible without pre-drilling.
was Engel’s first move into own brands, with recent iteration E-Jet X now available to the market
We are the reliable and sustainable partner of the distributors in the heart of Europe. With an attractive portfolio and a strong own brand for wood construction, we offer the highest quality for the assortment of our trade customers. Together with our various customer services, we master the challenges of the specialized trade with great passion.
All our actions focused towards creating benefit for our customers. To this end, we develop targeted, flexible solutions. Combined with our high level of service in performance and support, we create sustainable business relationships beyond the product. We live honest cooperation at eye level and are a fair and reliable partner.
With our experience and technical knowledge we are the reliable partner for direct container business with best possible conditions. Furthermore, we realize high-quality special and drawing parts, meeting the special requirements of our partners, we support our customers from development to series production. This is how we create tailor-made solutions for the tasks of our customers.
Our innovative C-parts management systems ensure security of supply for our industrial customers. We are the procurement service provider for medium-sized companies and develop dynamic solutions tailored to the customer. Competent handling, lean processes and high transparency ensure a long-term success.
Sorta-Case, a leading manufacturer of high-quality plastic and metal cases, has launched a brand-new case in a popular configuration. What’s more, it is being produced in the UK, with supply-chain-disruption-busting lead times…
SortaCase®’s brandnew GrabCase® is a robust case with compartments, ideal for use with kits, starter packs, introductory packs or similar. 100% made in Britain, it features a popular compartment layout, with six or nine removable compartments, in a range of layouts and colours.
So why has SortaCase® chosen now to launch the product?
Martin Jefferys, SortaCase® Director, tells Torque Magazine: “Every now and then we’d get requests for 4,000 cases of these type, for example, typically when people have been let down by their supplier. But we were never really in a position to help and turn something around for them quickly, as we never had the tooling.”
But now all that has changed.
“We took this basic product, altered it and I’d like to think improved it. Now we are able to offer something that caters to a demand and fills a gap in the market,” he adds.
The case for UK production
SortaCase® has been gradually expanding its range over the years, although the last two years has seen it simply get on with business amidst all the disruption seen in virtually all sectors. However: “Lately we have started to get out a bit more and it sparks ideas, it really is eye opening.”
The time was ripe for the firm to make good on its longheld plan to expand its UKmade product line, which so far has included a handful of lines.
Jefferys explains: “Having more Britishproduced product has been on our mind for the last few years, but there have been a lot of reasons to postpone it recently,” he says, alluding to the disruption of Covid.
“We produced two other cases in the UK and one smaller basic product, but not in great numbers. We anticipate a lot of volume for GrabCase®
“We want to make as much as we can in the UK, it makes sense and is simple economics. When you are shipping a product like this you are carrying a lot of air, due to the nature of the products. It’s not like a box of screws. So, there is not a lot of value in the container.”
And with the longdistance supply chain proving less reliable in recent years, having production nearby has proven to be increasingly popular, with turnaround times vastly improved.
Customisation, including silk screening, is something SortaCase® has offered for many years. The GrabCase® is no different, with vast colour options and room for branding on the handle. But why is branded product so popular?
// We are able to offer something that caters to a demand and fills a gap in the market. //
Businesses can brand up their Grab-Case® with company colours
When companies use branded products, for promotions, such as starter packs or introductory packs, not only does it get their brand name out in the market, but it can lead to repeat business.
“People see the branded cases on sites and they might ask, ‘where can we get one?’ Word spreads and then customers ask for more of the same, so then you see repeat business from customers. That’s the proof of the pudding.”
With customisable product a reliable and proven part of its business, the firm is beginning to ramp it up. Crucially, SortaCase® now has its own facility to customise product and has begun to promote the service in its catalogue. “We used to subcontract it, but now we have greater control over the process and the quantities required have been decreased.”
The customisation possibilities for GrabCases® are huge, explains Jefferys: “We can match to any Pantone or RAL colour, so the possibilities are almost infinite! Black is the most cost effective, but we can do anything, even luminous colours. Our minimum quantity for Own Branded grabcases® is 480 pieces, for smaller quantities we will be keeping stock of the popular colours.”
Customisation options continue: “We are offering compartments in two sizes, but we have another tool and will be offering a third compartment size by December.”
Case® handle offers eyecatching space for branding: “Once we have the logo the turnaround only takes four to six weeks. We have a lot of control as it’s our facility.”
For now, the aim will be to bring GrabCase® to as many customers as possible: “We’re fully focused on the product. We invested a lot in the tooling – it uses seven tools – and the tooling was made in Britain.
“It’s a good quality product, it’s customisable, it’s a good price, it’s made in Britain and we make it simple for customers.”
People see the branded cases on sites and they might ask 'where can we get one?' Word spreads and that's where you can see repeat business. //
Las Vegas lived up to its reputation as a great place to meet and have a good time –and to do business – as the location once again for the International Fastener Expo which proved in-person events are making a strong rebound.
Las Vegas has more casinos and convention centres than your average city and that experience was on display as the International Fastener Expo (IFE) once again returned to the halls of the Mandalay Bay Convention Centre. Held from 1719 October 2022, in addition to providing several new features, this year’s edition saw 450 exhibitors showcase their products, technologies and services to visitors on the tradeshow floor – including 30 new exhibitors making their debut at the event.
More than 3,500 visitors from 36 countries from across the globe gathered in Las Vegas for the threeday event, which Show Director Morgan Wilson says proves international events are making a strong comeback: “It was clear our industry was ready to be back in person and reconnect with each other.” Numbers were still down on prepandemic levels, but Wilson is optimistic that things are improving. “We are getting pretty close to preCOVID numbers, we may even exceed them here, which is pretty exciting!” he added.
Volt Industrial Plastics was once again in attendence at IFE 2022.
IFE’s annual golf tournament kicked off the event on the morning of 17 October, providing a fun way for participants to interact and learn. The tournament saw record breaking attendance with more than 145 players across 36 teams taking to the course at Bali Hai Golf Club for some goodnatured and friendly competition. Although it might be that the teams from B&D Cold Headed Products were competing among themselves as two teams took out first and second place, with the team from Williams Form Engineering and King Steel picking up third. The day’s events continued with a welcome reception at Mandalay Bay’s Daylight Pool, where over a thousand attendees came together for an evening of networking, music and dancing.
// We hope IFE brings everyone together to overcome challenges moving forward. //
Of course, the main event provided plenty of opportunities to network as well. There was a range of educational sessions presented on the Session Stage that offered attendees insight and knowledge on topics such as ecommerce, inflation, 3D printing, productivity and the nextgeneration workforce. Additionally, UnleashWD and Executive Producer of We Supply America Dirk Beveridge presented a keynote speech titled “Innovate! How to create relevancy in the age of disruption.”
Meanwhile in a sign of the times and continuous improvement with technology, the new IFE Match app helped to bring attendees and exhibitors together in a new ‘smart’ way to discover new business opportunities, explore educational sessions, and build a digital itinerary during the show. Over 350 meetings were arranged through the app, and attendees can watch back the educational settings for 30 days after the event.
As always, the Hall of Fame and Young Fastener Professional of the Year awards took place during the proceedings on day one. The new inductees into the Hall of Fame include Andy Cohn of Duncan Bolt, Tim Malone of Spring Bolt and Nut Manufacturing, Rick Rudolph of Rick Rudolph Associates, and Joseph Volltrauer of Volt Industrial Plastics. This year’s inductees continue the tradition of recognising those people who have made significant and enduring contributions to the industrial fastener industry on a national and global scale, joining previous members who include inventors, business leaders and educators.
The exhibition floor opened its doors to veteran exhibitors like BrightonBest International, Goebel Fasteners, Nucor, Star Stainless, Parker Fasteners and more, as well as some firsttime exhibitors including Alox and Optimas Solutions. Torque Magazine was represented along with new sister title Torque Direct. Our editorial and sales colleagues were keen to speak to visitors and exhibitors alike about key industry trends, new and upcoming product launches, and innovative technology advances. The majority of people we spoke to reported their experience of the show had been a positive one, both in terms of visitor numbers and the quality of the contacts and meetings held throughout the event.
Bryan Wheeler of Star Stainless was crowned Young Fastener Professional of the Year, receiving a special plaque. The award recognises a young professional who has made significant contributions to the fastener industry.
With the event over for another year, Show Director Morgan Wilson is pleased with how things went. “As always, we hope that attendees can come back from the show inspired, with new ideas, and new relationships. We hope IFE brings everyone together to overcome challenges moving forward.”
The International Fastener Expo will take place again next year at the Mandalay Bay in Las Vegas between 911 October, 2023. fastenershows.com
JANUARY issue 070
Online catalogues, brochures and webshops
IT services, software and e-business
Electric vehicle fasteners and tools, and supply chain
Battery pack technology & smart tools
Advanced battery pack technology
SHOW PREVIEW > Fastener Fair Global 2023
FEBRUARY-MARCH issue 071
Rivets, rivet tools and rivet technology
Hand tools and consumables
IT services, software and e-business
Building & Construction > Wood, chipboard and decking screws
TERRITORY FOCUS > North America
SHOW PREVIEW > Taiwan International
Fastener Show
SHOW PREVIEW > BAU
SHOW PREVIEW > Fastener Fair Global 2023
MARCH issue 072
Connected & smart tools
Margin makers > tapes, sprays, disposable gloves & more
SHOW PREVIEW> BAU
APRIL-MAY issue 073
Fastener distribution special Nylon and plastic fixings and fasteners
Drill & screwdriver bits
Building & Construction > High tensile (HT) and bolt assemblies
TERRITORY FOCUS > UK
TERRITORY FOCUS > ASEAN / ASIA
MAY issue 074
TERRITORY FOCUS > Nordic countries
Structural engineering & structural fasteners
New materials (graphene, hidrofugo, etc)
JUNE issue 075
Nuts, washers and locking systems
Tools > Made in Germany
Fastener machines, equipment & tooling
Rail
JULY-AUGUST issue 076
Women in fasteners special > North America
QC laboratory focus
Oils, sprays and lubricants
3D printing Building & Construction > Timber engineering SHOW PREVIEW > International Fastener Expo
Fastener Training - Academies
SEPTEMBER-OCTOBER issue 077 PRINT EDITION
Fastener manufacturing special Stainless steel fixings and fasteners
Torque tools, technology & bolting Workwear, PPE and safety Building & Construction > Anchors Wire & fastener cold heading
TERRITORY FOCUS > Eastern Europe SHOW PREVIEW > A+A 2023
OCTOBER issue 078
Rivets, rivet tools and rivet technology Plugs, plasterboard and cavity fixings
Janitorial supplies > Wipes, cleaners, sprays, etc Tool telematics
NOVEMBER-DECEMBER issue 079 PRINT EDITION
C-parts, logistics and Kanban
Production line tools (rivet guns, assembly tools, torque wrenches, etc)
Battery technology & smart tools Automotive fasteners & tools
Surface treatment and coatings Building & Construction > Adhesives, tapes, sealants and fillers
Turkish fastener manufacturing Torque Rising Stars
SUSTAINABILITY SPECIAL > A special magazine on sustainable practices in the fastener and tool industries, covering company initiatives, ISO 14001 certification, recyclable packaging, end of life & related topics.
Extended Producer Responsibility (EPR) is the Government’s proposed packaging sustainability legislation – currently in draft. It is set to be launched in 2024, with the new rules and the new reporting that will enable those rules likely to start appearing in 2023. As currently outlined, EPR will shift the burden of paying for recycling for the packaging of branded products from general taxation, retailers and suppliers predominantly to suppliers. The increase in packaging PRN costs for suppliers is forecast to be between eight and ten times compared to 2021.
As I have said, this is currently in draft form and if it goes ahead unchanged, it will be the most significant change to Packaging Regulations, indeed the whole PRN system, for a generation. The view at BHETA and among BHETA’s expert business service providers in the area of waste management is that the terms of the draft are fundamentally unfair for suppliers and that EPR should therefore be challenged. Based on this association’s experience of Government lobbying, unless the supply side is to bear these additional costs – up to ten times current exposure – we need to act collectively and now to make our views clear to MPs and the Minister.
To enable this BHETA is not only advising its members on the essential steps that every company needs to undertake in preparation for potential new rules, but it has also launched its latest lobbying campaign to challenge the whole principle of EPR. So it is here in Torque Magazine that I am appealing to all suppliers of tools, fixings and related products – whether members of BHETA or not – to join the BHETA campaign. If we fail to act ‘as one body’ now, there are two likely outcomes for suppliers and neither of them are good!
A) the proposed legislation stays as is and supplier cost for recycling increases tenfold B) suppliers attempt to share the burden with retail partners and are faced with the resulting inevitably tough negotiations
So what is BHETA’s EPR campaign?
Firstly, the BHETA EPR campaign and the advisory material for suppliers that goes with it is not about denying the need for packaging change. All moves to reduce packaging and to change packaging materials to those that cause least harm are welcome. But we need to spread the costs more equitably and in a fairer timescale. That way it is my belief that all suppliers and all retailers will be able to take genuinely positive steps towards the shared goal, rather than being bounced by an unfair cost burden into a place which consumers will have great difficulty accepting.
Let us start by understanding the detail. The principle underpinning EPR is that there will be a huge shift in financial responsibility for the treatment of waste packaging throughout its lifecycle, with producers picking up 100% of the bill. Currently, the costs for kerbside recycling / disposal of packaging from branded products is split roughly as follows:
10% by producers through PRNs ▪
10% by retailers ▪
80% by the taxpayer through Councils. ▪
Under EPR in 2023, for payment in 2024, this will change to 100% of the cost of collection and disposal met by producers and set to be charged on levels of 2023 packaging. Moreover, with reporting criteria set to be enhanced – possibly from 1 January 2023 – the minimum thresholds of turnover and packaging volume for small companies will be halved, so more small companies will have to pay.
By 2025 a ‘modulated fee system’ is expected to be introduced to provide discounts depending on the environmental impact of the packaging placed on the market. Packaging that can be easily recycled will attract lower EPR fees compared to hard to recycle packaging. This will therefore provide financial
// If we fail to act ‘as one body’ now, there are two likely outcomes for suppliers and neither of them are good! //
A new law aimed at protecting the environment looks to be placing the responsibility of packaging largely upon suppliers. Will Jones, Chief Operating Officer of BHETA, argues how the current plan is unfair for suppliers and that there is still time to ensure the costs are more equally shared…
incentives for producers to use more sustainable materials in their packaging.
While this is positive in theory, in the short term it will hike costs even further as suppliers will have to create even more reporting detail in 2024 in order to qualify for discounts if they are eligible.
So BHETA’s campaign centres on the whole way in which the forthcoming legislation has been drafted. Among the questions for the new Environment Minister are:
EPR as currently set out assumes that producers can make all ▪ the packaging decisions, while the reality is that the relative size of many producers and retailers means that the retailers frequently specify the packaging requirement, and the producer has a choice of meeting the specification or losing the business.
Secondly it assumes that only producers benefit from the pack ▪ aging, whereas the benefit is shared throughout the supply chain, from manufacturers to retailers to the consumer, through safe and secure transportation of goods, minimised waste due to breakage, clear communication of features and benefits, instructions on how to use products safely and efficiently, and so on.
The bottomline reality is that producers will be unable to absorb these additional costs on their own and as such they will be passed up the supply chain to the consumer, exacerbating the costofliving crisis. In a nutshell, BHETA is asking whether it would be sensible to review the draft guidance around Extended Producer Responsibility, in particular the huge cost burden this will place on suppliers.
As a fallback position, if what we hope will become a collective campaign cannot unpick the proposed legislation as it stands, then we will be asking for a delay of at least a year until the details of requirements and charges have been outlined in full. We will also be asking for a phased introduction of any legislation to allow producers time to adjust to the substantially increased costs.
FIRSTLY, please talk to BHETA about how as a supplier you can help support the EPR lobbying campaign. You can contact me on wj@bheta.co.uk or for more information on BHETA lobbying and legislative advice in general, contact BHETA Member Services on rk@bheta.co.uk or 0121 237 1130
SECONDLY, review all packaging and carefully consider every bag, box, and item to see if there is a way to remove, reduce or make it from more recycled and recyclable material. BHETA is also advising that as all suppliers will at some point be legally required to get a more detailed breakdown of the materials used in packaging, potentially in 2024, they look to putting methodology in place. If your company is not already part of a Compliance Scheme, I urge you to calculate the volume of packaging your business currently deals with, as the minimum threshold for being required to pay under EPR is likely to half to 25 tonnes.
BHETA’s own business service provider on this subject is Wastepack and for more information about joining a Compliance Scheme, contact: paul.vandanzig@wastepack.co.uk.
// The bottom-line reality is that producers will be unable to absorb these additional costs on their own and as such they will be passed up the supply chain to the consumer, exacerbating the cost-of-living crisis. //
Taiwan opened its doors to global visitors once again, at the 1st Taiwan International Tools & Hardware Expo...
The Central Epidemic Command Center (CECC) announced that Taiwan’s borders will be fully reopened from 13 October, paving the way for Taiwan’s largest international expo in the hardware industry, Taiwan International Tools & Hardware Expo (TiTE).
Running over 1214 October 2022 at the Taichung International Exhibition Centre, the first TiTE was introduced by the Taiwan Hand Tool Manufacturers’ Association (THTMA), showcasing Taiwan’s robust supply chain strength of the hand tool industry.
Over 250 exhibitors participated, largely hardware & tool manufacturers from Taiwan. TiTE provided an integrated service for not only visiting the exhibition, but also factory visits and procurement. Over 25,000 visitors and hundreds of international buyers from 42 countries worldwide visited the show.
Making Taiwan’s hand tool industry shine on the global stage
Over 20 significant industrial associations worked together to organise the event. The first TiTE was advised by the Bureau of Foreign Trade, Ministry of Economic Affairs and coorganised by the Strengthening Investment Services Project Office, NDF, Taiwan Institute of Economic Research, Taiwan Industrial Fasteners Institute, Taiwan Machine Tool & Accessory Builders’ Association, Taiwan Plastics Industry Association, Digital Transformation Association and Invest Kaohsiung.
“As countries all across the world are lifting their coronavirus lockdowns, global supply chains in a postpandemic world have been changed,” said Jack Lai, Chairman of Taiwan Hand Tool Manufacturers’ Association. “This is a great opportunity for Taiwanese manufacturers to rebrand the ‘Hand Tools Kingdom’. As the organiser, we are devoted to making Taiwan’s hand tool industry shine on the global stage. This expo just
made the first innovative move. As more ideas will be unlocked, a new chapter of Taiwan’s hand tools shall begin.”
Meanwhile, 2022 TiTE has reinforced its extensive network of domestic and international media partners for exhibition promotion. Working with TAITRA, 2022 TiTE served as an effective business matchmaking platform for participants, with hundreds of matchmakings from 18 countries occurring during the expo. What’s more, the online expo with a virtual exhibition hall was launched on 1 October, creating a conference system for international and domestic buyers ahead of the show. As for the global media, the major partners stretched across Asia, America and Europe.
Over 250 exhibitors included the likes of JONNESWAY, WHIRL POWER, PATTA, ALLPRO, KUANI, WOLF’s HEAD, MACHAN, PROXENE, AKRAFT, REDAI and Luckybrand, among many others.
TiTE Conf- INNOVATION OF INDUSTRIAL HARDWARE & TOOLS
The packed forum agenda tackled key topics, including Innovation, Transformation and Sustainable Development of Metal Industry and Digital Transformation of Traditional Industries. The opening sessions included statements from highlevel representatives from government and heads of industrial associations. The first thematic session on the opening day covered “Carbon Reduction Strategy and Profitability Control”, “Taiwan’s Pathway to NetZero Emissions” and “Digital Transformation in Manufacturing and Industrials”. Day two tackled “The future of Industry transformation”, while a closed session, “TaiwanUS Smart Home Industrial Networking Forum”, focused on the best solutions and AI application cases for smart homes.
hardwareexpo-taiwan.com
+49(0)7941 6094-0
JANUARY issue 070
Online catalogues, brochures and webshops
IT services, software and e-business
Electric vehicle fasteners and tools, and supply chain
Battery pack technology & smart tools
Advanced battery pack technology
SHOW PREVIEW > Fastener Fair Global 2023
FEBRUARY-MARCH issue 071
Rivets, rivet tools and rivet technology
Hand tools and consumables
IT services, software and e-business
Building & Construction > Wood, chipboard and decking screws
TERRITORY FOCUS > North America
SHOW PREVIEW > Taiwan International
Fastener Show
SHOW PREVIEW > BAU
SHOW PREVIEW > Fastener Fair Global 2023
MARCH issue 072
Connected & smart tools
Margin makers > tapes, sprays, disposable gloves & more
SHOW PREVIEW> BAU
APRIL-MAY issue 073
Fastener distribution special Nylon and plastic fixings and fasteners
Drill & screwdriver bits
Building & Construction > High tensile (HT) and bolt assemblies
TERRITORY FOCUS > UK
TERRITORY FOCUS > ASEAN / ASIA
MAY issue 074
TERRITORY FOCUS > Nordic countries
Structural engineering & structural fasteners
New materials (graphene, hidrofugo, etc)
JUNE issue 075
Nuts, washers and locking systems
Tools > Made in Germany
Fastener machines, equipment & tooling
Rail
JULY-AUGUST issue 076
Women in fasteners special > North America
QC laboratory focus
Oils, sprays and lubricants
3D printing Building & Construction > Timber engineering SHOW PREVIEW > International Fastener Expo
Fastener Training - Academies
SEPTEMBER-OCTOBER issue 077 PRINT EDITION
Fastener manufacturing special Stainless steel fixings and fasteners
Torque tools, technology & bolting Workwear, PPE and safety Building & Construction > Anchors Wire & fastener cold heading
TERRITORY FOCUS > Eastern Europe SHOW PREVIEW > A+A 2023
OCTOBER issue 078
Rivets, rivet tools and rivet technology Plugs, plasterboard and cavity fixings
Janitorial supplies > Wipes, cleaners, sprays, etc Tool telematics
NOVEMBER-DECEMBER issue 079 PRINT EDITION
C-parts, logistics and Kanban
Production line tools (rivet guns, assembly tools, torque wrenches, etc)
Battery technology & smart tools Automotive fasteners & tools
Surface treatment and coatings Building & Construction > Adhesives, tapes, sealants and fillers
Turkish fastener manufacturing Torque Rising Stars
SUSTAINABILITY SPECIAL > A special magazine on sustainable practices in the fastener and tool industries, covering company initiatives, ISO 14001 certification, recyclable packaging, end of life & related topics.
Rapierstar hosted a golf day to celebrate its 30th anniversary and support Hope House Children’s Hospices, via GM Fundraising.
The golf day – a practice session ahead of GM’s big fundraising golf event in Quinta do Lago, Portugal next year – took place at Astbury Golf Club in South Cheshire in October, with representatives from all areas of the window and door industry.
Many of those who played at Astbury will participate in GM Fundraising’s Ryder Cup style challenge in Portugal, which mimics the Ryder Cup while at the same time raising vital funds for Hope House Children’s Hospices. The last GMF Cup in 2021 raised over £41,000 for the charity and GM Fundraising is hoping for even more in 2023.
justgiving.com/fundraising/gm-fundraising
44 Jewson team members have walked 26.2 miles to raise cash for charity partners, Band of Brothers and Barnardo’s.
Staff from the UK builders merchant put on their trainers at the Jewson Staines branch on Gresham Road at 7am, and ended at London’s O2 Arena later that day. The route snaked along the Thames, calling at Jewson Acton (Horn Lane) and Jewson Lambeth along the way for wellneeded rests and supplies.
Band of Builders has been a Jewson charity partner since 2016, raising money to help people working in the construction industry who are dealing with challenging emotional or financial circumstances. Jewson has been partnered with Barnardo’s since 2017 and helped to codevelop the ‘Futurebuild’ YouthBuild Training Academy, which donates money, equipment, construction materials and expertise to help the academy teach trade skills to young people leaving care.
For more details visit: https://gofund.me/64987ffd. To donate to Barnardo’s, visit: https://gofund.me/2afcd248.