
16 minute read
Netherlands open recycling plant for contaminated steel scrap
Special Coating Protects Steel from Hydrogen ‘Attack’
Regeneratively produced hydrogen is an ideal energy carrier, which will be used in future applications as fuel cells and in cars; it will supplement natural gas as an energy source. But atomic hydrogen often induces brittle behaviour in metals at high temperatures. Fraunhofer IWM, MikroTribologie Centrum mTC, has now developed a robust coating that effectively protects steel from the penetration of hydrogen. The barrier effect of this so-called MAX-phase layer is 3500 times greater than that of untreated steel.
Advertisement
CONTACT: Lukas Gröner, lukas.groener@iwm.fraunhofer.de Telephone +49 761 5142-488
The wind blows when it wants to. This is a real problem for the production of wind energy, because wind turbines do not always generate electricity when it is needed. In addition, there can be more electricity available in the power grid on windy days than is actually needed. That’s why it makes sense to use the excess supply of wind and also solar power in a different way - for example to produce hydrogen. Hydrogen is an environmentally friendly energy carrier that can be stored very well. When burned, the only waste product is water. It can be mixed with natural gas and used in gas-fired power plants to generate energy. It can be used as fuel in cars or to generate electricity and heat in fuel cells. All of this makes hydrogen a beacon of hope for the energy revolution. But there are still a few hurdles to be overcome before hydrogen can be used on a large scale. One challenge is that atomic hydrogen makes metals brittle, which can lead to component failure. Atomic hydrogen accumulates in the parts of a component that are subject to particular stresses, such as at welding seams or in areas under tension. Hydrogen embrittlement then becomes a problem, espe-
Fig. 1: REM image of the fracture edge of a Ti2AlN coating with platelet-like shaped grains.
cially in components that are exposed to high operating temperatures.
The hydrogen barrier combines the strengths of ceramics and metals
In his doctoral thesis at the Fraunhofer Institute for Mechanics of Materials IWM, MicroTribology Centrum µTC, and at the Institute for Microsystems Technology at the University of Freiburg im Breisgau, physicist Lukas Gröner developed and tested special coatings for steel components that virtually prevent the penetration of atomic hydrogen. These are so-called MAX-phase materials, which have been the subject of international research for over ten years. ‘MAX-phases have amazing properties because they combine characteristics of both ceramics and metals’ says Gröner, scientist in the Tribological and Functional Coatings Group at the Fraunhofer IWM. MAX-phases, like ceramics, are insensitive to attack by oxygen and very heat-resistant. At the same time, they are electrically conductive like metals. Unlike pure ceramics, they are not brittle, so they do not break. Lukas Gröner has now succeeded in producing thin MAX-phase coatings that protect steel very well against corrosion and hydrogen embrittlement. In a vacuum chamber, he first deposited very precisely alternating layers of aluminium nitride, an aluminium-nitrogen compound, and titanium on a steel surface using physical vapor deposition (PVD). This sandwich structure, which is only about three micrometers thick, was then heated to form a very thin MAXphase layer of titanium, aluminium and nitrogen (Ti2AlN). The challenge for Gröner was to control the deposition of titanium and aluminium nitride in such a way that parallel Ti2AlN platelets were formed during subsequent heating. He succeeded: ‘The platelets are close-packed like bricks in a wall’ is how Lukas Gröner describes the success.
In his doctoral thesis, Lukas Gröner also investigated how the MAX-phase coating behaves when it is intensively heated - as could be the case in future gas turbines or fuel cells. To simulate normal operating conditions, he heated the material to 700 degrees and left it in the furnace for up to 1,000 hours. This created a thin layer of a special
Fig. 2: REM images of a Ti-AlN multilayer stack of the surface (a) and the fracture edge (b), as well as the surface (c) and fracture edge (d) of a resulting MAX-phase Ti2AlN layer.

aluminium oxide on the top side of the coating – a-Al2O3. As was shown in the further course of the investigations, this thin aluminium oxide coating considerably increases the barrier effect of the protective layer against hydrogen.
New testing measures barrier effect against hydrogen
To test how well the MAX-phase layer prevents hydrogen from penetrating the metal, Lukas Gröner first developed a new test rig for thin metal sheets. In this test he compared uncoated steels with MAX-phase coated steels. This was the first time that it was possible at the Fraunhofer IWM to precisely quantify the penetration of hydrogen and to determine the so-called permeation reduction factor (PRF) as a measure for the barrier effect.
The results are impressive: steels with a MAX-phase layer that were not heated withheld hydrogen 50 times better (PRF 50) than untreated steels. But the results were particularly impressive for the coated steels that had been heated and formed an a-Al2O3 layer. These blocked the hydrogen from entering the metal roughly 3500 times better than with the untreated steel. ‘These are values that absolutely meet the requirements of the industry,’ emphasises Gröner.
Almost no evidence of brittleness
Lukas Gröner is currently testing how well the MAX-phase layers work when applied in collaboration with cooperation partners such as the Forschungszentrum Jülich - for example on high-temperature fuel cells (SOFC) that operate at temperatures of approximately 600 degrees Celsius. Says Gröner: ‘The MAX-phase coatings are ideal for these types of applications because they protect the metallic components from heat and at the same time can dissipate the electric current that is generated inside the fuel cell’. The coating is also suitable for gas turbines. In the future, more and more regeneratively produced hydrogen will be added to natural gas, which means that the gas will burn at a higher temperature. However, more hydrogen and higher temperatures increase the risk of hydrogen embrittlement, which is why a component coating with a-Al2O3 can be very advantageous. Gröner cannot say whether in the future, the new coating process will be offered by the industry as a service or if it will find its way into the market in another form. The individual PVD coating process steps also still need to be optimised. However, Lukas Gröner has at any rate proven that MAX-phase coatings can provide excellent protection against hydrogen.
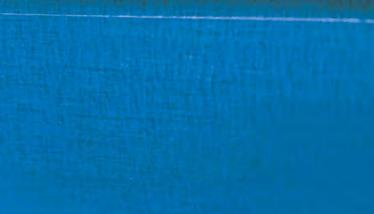

Diode lasers improve gap bridgeability
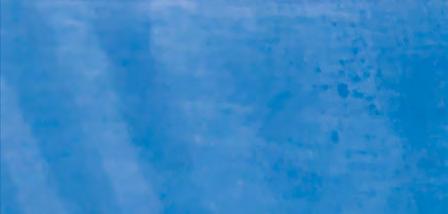

Laser joining with multi-spot module replaces GMAW welding
Bridging wide gaps is a classic challenge in metal welding. It may arise in car body construction as well as in machine building, pipeline construction or shipbuilding. The primary solution has long been gas shielded metal arc welding (GMAW) – a classic joining technology that uses an electric arc to melt the workpieces. This welding solution is inexpensive to purchase and has certainly proven itself for bridging wide gaps. However, there are weaknesses in terms of seam optics and process effi ciency: in addition to comparatively slow welding speeds, users often struggle with considerable distortion due to the high heat input. Often, time-consuming and costly straightening is required. Added to this are cost-intensive rework operations to repair unclean seams.

Overall, joining processes can be realized more effectively by diode laserbased cold wire welding with multi-spot optics from Laserline. For this purpose, a multi-spot module splits the collimated laser beam and generates in this way a smaller inner spot, superimposed by a larger, rectangular outer spot. In the welding process, the inner spot melts the joints of the workpieces and the supplied cold wire, which serves as an additional fi ller material for the seam. The wide outer spot improves gap bridgeability and, due to its low penetration depth, produces a calm weld pool without spatter formation. Compared to pure laser beam welding, the multi-spot optics and cold wire insert allow gaps of one millimeter instead of the usual 0.1 to 0.3 millimeters to be bridged. The result of the welding process is smooth seams without edge notches, which no longer require any post-processing. The seam cross-section can also be optimized by specifi cally adjusting the spot size and power distribution. The spot-in-spot confi guration opens up interesting processing possibilities, especially when joining asymmetrical seams: the outer spot can be continuously shifted, thus enabling dynamic adaptation to changing seam geometries while the process is running. This supports onesided melting in the case of thickness jumps, which is desirable for example for tailored blanks.

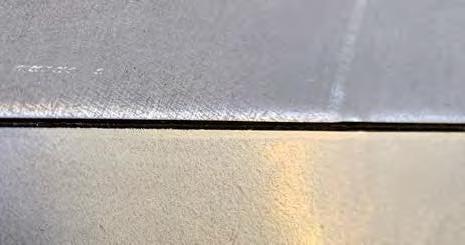
High process speeds, very low distortion
With the spot-in-spot design, the desired seams can also be realized signifi cantly faster: Laser powers in the multi-kilowatt range allow the process speed to be tripled compared to GMAW welding, thus ensuring higher output in industrial series production. In addition, the increased feed rate reduces heat input into the workpiece, effectively preventing material distortion. Overall, laser systems with spot-in-spot focus from Laserline are thus a real alternative to GMAW welding that not only achieves better results in terms of seam quality, speed and cost-effectiveness, but also offers new processing options when joining asymmetrical seams. The multi-spot modules can be easily integrated into processing optics of a Laserline LDF series laser system. When selecting individual application confi gurations, the diode laser manufacturer from Mülheim-Kärlich is happy to provide everything from detailed advice to test runs in the company‘s own application laboratory.
Laserline GmbH
Fraunhofer Straße 5 56218 Mülheim-Kärlich Johannes Schäfer Technical distribution Phone +49 2630 964 4000 | Johannes.Schaefer@laserline.com
DB Cargo secures major order from ArcelorMittal Eisenhüttenstadt
The railway is considered an indispensable mode of transport for steel producers. This is now illustrated by a new cooperation between ArcelorMittal and DB Cargo, which is to create one of the most modern raw materials logistics in Europe in summer 2021.
ArcelorMittal and DB Cargo have signed a ten-year-contract for the transport and handling of raw materials at the steelmaker’s Eisenhüttenstadt site in Eastern Germany. To this end, DB Cargo plans to invest in more than 350 new wagons and 1,400 special containers. As a further innovation the transport and logistics company intends to build two semi-automated unloading facilities including dust removal and operate them itself. This will be done in cooperation with forwarder Innofreight which – according to its own information – specialises in logistics solutions in the field of rail technology. Completion and commissioning is scheduled for summer 2021.
Most of the transport carried out by rail
As a result, ArcelorMittal plans to have one of the most modern raw materials logistics in Europa at its Eisenhüttenstadt site. “By using special container types optimised for the different properties of ore, coke and limestone, we can increase the net load per train by around 20 per cent and thus need significantly fewer trains,” says Sybille Klipstein, Lead Buyer Rail at ArcelorMittal. This protects the environment and reduces the shunting effort in the plant. In addition, the automated unloading offers employees a low-dust and noise-protected workplace.
For ArcelorMittal Eisenhüttenstadt, trains are the most important mode of transport. 95 per cent of the raw material transports to the site are currently carried out by rail. Every day there are six trains with about 200 wagons, of which up to four trains cross the German-Polish border. However, the steel-
DB Cargo will modernise the logistics processes at ArcelorMittal Eisenhüttenstadt, i.a. the unloading of ore.

First look at ArcelorMittal’s future ore containers
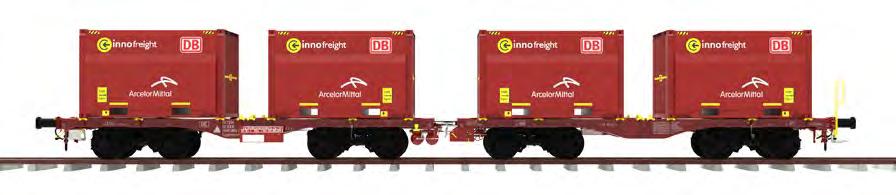
maker is only one suitable example to illustrate DB Cargo’s influence in this industry. Transporting steel is also one of the core competencies of its national company in Italy (DB Cargo Italia) that operates a high performance network in the country consisting of four hubs and more than 60 transshipment facilities. Thus, DB Cargo has had operations in Italy for many years and is increasingly experiencing success there. Thyssenkrupp’s subsidiary Acciai Special Termin (AST) for example imports its main ingredient Inox steel scrap from Germany to its Terni site in special wagons. Once the scrap has been transformed into stainless steel, is is exported to different destinations in Germany in various forms including steel coils. “With its Italian network, efficient transit times and high level of wagon availability, DB Cargo Italia is an indispensable partner for AST when it comes to providing raw materials,” says Emanuele Sinibaldi, an employee at AST. Four times a week, DB Cargo Italia delivers 3,400 net tonnes of steel scrap to Terni from Munich and Karlsruhe.
REVOLUTIONARY DANIELI MIDA HYBRID MINIMILL
Scrap shredding and cleaning; smart handling (automated scrap yard).
SCRAP MANAGEMENT
20 kWh/ton saving Lateral and top continuous charging system (ECS).
ENDLESS SCRAP CHARGE
30 kWh/ton saving
DR+DDM PRODUCTION ROUTE
C02 reduction: 800 kgCO2/tls DR+DDM route vs. 1,800 kgCO2/tls BF+BOF.
DRI PRODUCTION USING HYDROGEN
324 kgCO2/tls using up to 70% hydrogen instead of 100% natural gas (without compromising DRI quality).
DRI HOT CHARGE
100 kWh/ton saving
Unique performances using patented DIGIMELTER® OCTOCASTER® DYSENCASTER® DUE®
11% lower electrode consumption; Zero power grid disturbances.
DDM - DANIELI DIGIMELTER: THE EVOLUTION OF THE EAF
30 kWh/ton saving
HYBRID VIA Q-JENIUS
50 kWh/ton saving
Use of alternative power sources at site to Q-One via patented Q-Jenius DC link and Q3-Jenius energy management.
Note: energy savings expressed in kWh/ton (1 kWh/ton = 3.6 MJ/ton)
— Green Steel technologies for quality products at competive OpEx
Up to 260 kWh/ton saving.
DYSENCASTER® UP TO 6.5 M/MIN CASTING SPEED Q-HEAT FLAT INDUCTIONTEMPERATURE CONTROL
DUE@ Three rolling modes. Coil-to-coil, semi-endless, and endless for no steel-grade production limits.
OCTOCASTER® UP TO 10 M/MIN CASTING SPEED Q-HEAT LONG INDUCTIONTEMPERATURE CONTROL WIDE RANGE OF QUALITY HOT-ROLLED STRIP
BARS, WIREROD, MERCHANT SECTIONS
DIGISAVER 20 kWh/ton saving
Additional digital overall plant optimization
Up to 330 kWh/ton saving.
DAN IELI G REEN MET A L Please visit www.danieli.com to learn about the orders for the first MIDA Hybrid minimill received from CMC Steel in the USA, and a new 2.5-Mtpy direct reduction plant that allows the use of hydrogen and natural gas, for OMK in Russia.
danieli.com
Netherlands open recycling plant for contaminated steel scrap
A large scale processing plant to recycle contaminated steel scrap was recently taken into operation in Delfzijl, the Netherlands. The auguration took place in the presence of Dutch King Willem Alexander.
Builder and operator of the plant is Purified Metal Company (PMC), founded by Jan Henk Wijma, Nathalie van de Poel and Bert Buel, all with previous experience in the steel industry. Together with Jansen Recycling Group as a shareholder, they developed a method of cleaning steel scrap contaminated from other hazardous components like asbestos, mercury, PCB‘s or chrome VI.
PMC is a „circular process that makes it possible possible to convert hazardous steel waste in a clean premium raw material in an economically sound way,“ the company says.
UK-based waste-to-product company Renewi plc, will exclusively collect and transport contaminated steel directly to PMC’s facility in Delfzijl. According to PMC, the end product of its circular process is a clean, premium raw material for steel mills. Purified metal blocks are produced in a batch of 20 tonnes with a chemical composition, and can be delivered to the customer per container. The blocks are free of dirt, and have a high density. PMC aims to roll out the patented process in other countries in Europe and beyond.
The PMC process combines different proven technologies are combined such as sub-atmospheric pressure units, a steel scrap shear, induction furnaces and casting machines. Moreover, the process has been investigated technologically and proven by the University of Aachen, a renowned institution in the field of steel technology. The factory has been engineered and build by Küttner, Visser Smit Bouw and Royal Haskoning DHV.
How the process works
In a first step, the material handling, the contaminated steel scrap is loaded
PMC’s processing plant to recycle contaminated steel scrap in Delfzijl, the Netherlands

into standard disposal containers. The containers are then placed on the transport trolley and brought in via a lock. The container is transported to the storage bunker in the factory via two locks that are pressurised. An overhead crane feeds the scrap into a shear where it is cut and pressed. The material is then loaded into a loading vehicle.
Secondly, in the melting area, the loading vehicle transports the steel scrap to two electric furnaces. The material is then slowly fed into a melting bath of more than 1,500 degrees Celsius. During the melting process, contaminants are separated from the steel in a 100 % safe manner. The asbestos fibre structure is completely destroyed and converted into the harmless components H2O, SiO2 and MgO which float like slag on the melt and are later removed. Other hazardous substances are collected or neutralised by an advanced flue gas cleaning system. Once the steel has completely melted, it is transported to the casting machine via special channels. There, a batch of 20 tonnes of liquid steel is transformed into purified metal blocks. In order to determine the chemical composition of the melt, chemical analyses are made of the liquid melting bath.
The last step consists of cleaning the flue gas. During smelting, this is continuously extracted via the flue gas duct and transported to the flue gas purification system. This step includes the post combustion, in which flammable components are burned at 1,200 degrees Celsius. Any residual asbestos particles are then completely destroyed. Within a so-called “DeNoX” installation also NOx components are captured. What follows is a very rapid cooling of the flue gases in order to be able to carry out the rest of the flue gas cleaning. Ultimately, the system adds different additives in two steps to remove and capture (heavy) metals and other contaminants. The flat-bag filter then ensures that the dust particles are captured.
Our Tube products
Our service for you: Permanent availability of 20,000 tons of steel tubes. We saw cut lengths with tightes tolerances according to your requests. Shot-blasting and corrosion protection in various colours are also part of our range of services. Further processing on request.
Hollow Sections

Wall thickness: 30 × 30 mm - 500 × 500 mm 40 × 20 mm - 500 × 300 mm 2.0 - 20 mm Seamless steel tubes

Hot formed, longitudinally welded steel tubes
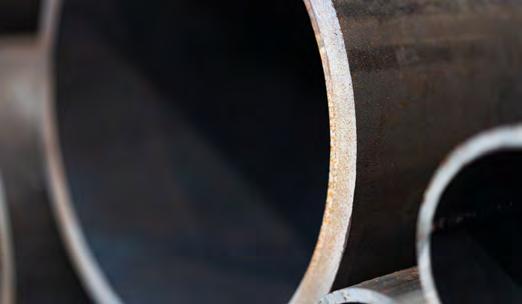
EN 10210, quality S355 J2H Outer diameter: Wall thickness: 219.1 mm - 610.0 mm 5.6 mm - 25 mm Longitudinally welded steel tubes
