
24 minute read
International Industry
ArcelorMittal and Italian state agree on plan for Ilva
ArcelorMittal has signed a binding agreement with Invitalia, the Italian state-owned company investing in former steelmaker Ilva in Taranto. The two will form a public-private partnership. The updated industrial plan agreed between ArcelorMittal’s unit AM InvestCo and Invitalia involves investment in lower-carbon steelmaking technologies, including the construction of a 2.5 million tonne Electric Arc Furnace. The industrial plan, which targets reaching 8 million tonnes of production in 2025, involves a series of public support measures including ongoing government funded employment support. This year Taranto’s output will reach slightly over 3m tonnes, impacted by the pandemic as well as the uncertainty over the future of the company. The conditions precedent to closing include: the amendment of the existing environmental plan to account for changes in the new industrial plan; the lifting of all criminal seizures on the Taranto plant; and the absence of restrictive measures – in the context of criminal proceedings where Ilva is a defendant – being imposed against AM InvestCo.
Advertisement
Tata unveils €300 million ‘Roadmap+’ for IJmuiden
Tata Steel on 8 December launched ‘Roadmap+’, a €300 million environmental-improvement plan to reduce emissions at its IJmuiden plant in The Netherlands. Roadmap+ means to combat industrial odors and dust pollution at IJmuiden. Its announcement coincides with the publication of a progress report on Tata Steel’s Roadmap 2030 sustainability programme involving 25 projects to enhance the company’s environmental performance. As part of the Roadmap+ programme , Tata Steel Netherlands will work closely with local authority and government leaders in the Province of Noord Holland to ensure the measures exceed environmental laws. The measures include the planned €150 million construction of a DeNOx facility at IJmuiden’s Pellet plant, which will reduce emissions significantly by cutting output of nitrogen oxides (NOx) and heavy metal particulates by more than 90%. The project will also include an investment of
Seaside view of Tata Steel Europe’s Ijmuiden works
€50 million in improvements to the Coke and Gas Plant 2 (CGP2), helping to cut odors and emission of particulates.
U.S. Steel buys outstanding shares in Big River Steel
U.S. Steel has exercised its call option to acquire the remaining equity of Big River Steel for approximately $774 million from cash on hand. The group had previously acquired a 49.9% stake in Big River Steel for $700m. “For months, I’ve said that we can’t get to the future fast enough. Today, I can say the future is now. We are acquiring Big River Steel, the cornerstone of our ‘Best of Both’ strategy,” said David B. Burritt, president and chief executive officer of U. S. Steel. Big River Steel operates a LEED-certified Flex Mill in northeast Arkansas that is believed to be the newest and most advanced flat-rolled mill in North America. Big River Steel produces eleven advanced U. S. Steel grades, including substrate for its XG3grade of Genera-
Liberty Steel and Thyssenkrupp get serious
Liberty Steel and Thyssenkrupp in early December confirmed they that will be entering the due diligence process which could eventually lead to a takeover of Thyssenkrupp Steel Europe by Liberty. “Thyssenkrupp and Liberty Steel Group have agreed to enter a further process phase,” the UK-based group writes in a statement, noting that it will shortly begin a detailed due diligence and thus gain insight into key business data of Thyssenkrupp’s steel business. The economy minister of the state of North Rhine Westphalia, Andreas Pinkwart, was quoted in the local press as saying that Liberty’s offer “is a reasonable basis for discussion,” after talking to Liberty chief Sanjeev Gupta. Pinkwart said Liberty’s concept is substantial, and he welcomed the group’s apparent willingness to push the transformation towards green steel. tion 3 advanced high-strength steels (AHSS). Big River recently started up and commissioned its Phase II expansion, which brings the Osceola, Arkansas-based mill’s capacity to 3.3 million short tons/year.
SSAB confirms interest in Tata Steel Ijmuiden
SSAB has confirmed that it is in discussions with Tata Steel Group concerning a potential acquisition of Tata Steel Europe’s IJmuiden steel mill and related downstream assets. The Swedish company says that discussions with Tata are on-going but no decisions have been made. There can be no certainty that any transaction will materialise, nor as to the terms of any such potential transaction. Further announcement will be made in due course, it says. Source: Tata Steel Europe
CSN’s ladle furnace during the first treatment

Americas
BRAZIL
Primetals Technologies has re-
vamped electrics and automation
systems at the Presidente Vargas
Steelworks of Companhia Siderúr-
gica Nacional (CSN) in Volta Redonda, Rio de Janeiro State, Brazil. In this context, the electrics and automation systems of a RH degassing plant, a ladle furnace and the common alloy system were replaced with new versions. Primetals‘ scope included the engineering for electrics and automation, HVAC (heating, ventilation, air conditioning)-systems, fire-fighting systems and the installation of all equipment supplied.
CANADA
Tenova was awarded a contract by Valbruna ASW for the supply of a new electric arc furnace (EAF) at the steelmaker’s facility located in Welland, Ontario. The scope of the supply includes the latest generation of the EAF unit which will replace the existing one. Tenova will also provide the associated auxiliary equipment, the material handling system, including bins batteries, hoppers and conveyor belts, for the charging of the ladle and of the EAF and the complete automation system. The complete management of this plant will be fully automatised and integrated in the new the EAF process control system.
USA
US steel producer Big River Steel has commissioned the second construc-
tion stage of its steel plant in Osce-
ola, Arkansas, supplied by SMS group. Also for the mill expansion, which doubles the mill’s annual production capacity to approximately 3 million short tons of steel, SMS group supplied the mechanical equipment, the electrical and automation systems, and the digitali sation technology. Now, with the second construction stage completed, Big River Steel operates two electric arc furnaces and two twin-ladle furnaces. The steelworks has also been equipped with a further gas cleaning

No. 2 CSP casting strand with pendulum shear at Big River Steel in Osceola, Arkansas

system as part of the project. The CSP plant (compact strip production) has seen the addition of a second casting strand, a second tunnel furnace and another downcoiler. Big River Steel’s CSP plant produces up to 1,930 mm wide coil, making it one of the widest CSP plants in the world.
Asia
AZERBAIJAN
Automazioni Industriali Capitanio
(AIC) has completed the upgrade of
dividing shear and cut line automation at Baki Inshaat Senaye
OJSC in Baku, Azerbaijan. This project included the new electric and automation control system for the cooling bed entry line. The team of AIC was also involved in site installation and commissioning phases, start-up support and the remote assistance.
BANGLADESH
The Danieli Service Small Revamp-
ing Team has commissioned a bar mill upgrade at BSRM Steel Mills in Chittagong, Bangladesh. The target of the revamping was to improve the productivity for the smallest bar sizes by implementing 5-strand slitting and producing 5x8- and 5x10-mm-dia finished products. The intervention was completed two days ahead of schedule, Danieli says, and involved installing the slitting guides, modifying the existing ratios on the stand gearboxes and upgrading shears and QTB along the mill. Furthermore, for the same plant, Danieli is supplying a new offline cutting area. There, angle bars will be automatically cut in submultiple commercial lengths at a productivity of 36 tonnes per hour, whilst allowing the main rolling mill to continue producing longer sections of the entire range of profiles at a high-performance rate.
CHINA
The world’s first DRI (direct reduced iron) production plant powered by hydrogen enriched gas will be implemented in China by the HBIS Group with the Energiron technology. Tenova has signed a contract with the group for the implementation of the so-called “Paradigm Project”, a high tech hydrogen and energy development and utilisation plant. The project includes a 600,000 ktpy Energiron DRI plant using technology jointly developed by Tenova HYL and Danieli. “This is an important breakthrough for the Chinese steel industry as it will be the first gas-based DRI plant in China”, stated Stefano Maggiolino, President and CEO of Tenova HYL. The HBIS DRI plant will use make-up gas with approximately a 70 % hydrogen concentration. Due to the high amount of H2 the HBIS plant will be the “greenest DRI plant in the world”, Tenova says, by producing “only 250 kg of CO2 per tonne of DRI. The carbon dioxide will be selectively recovered and part of it will be reutilised in downstream processes, with a final net emission of about 125kg of CO2 per tonne. The plant is scheduled to begin production by the end of 2021.
The new Andritz S6-high cold-rolling mill delivered to Shougang Jingtang United Iron & Steel Co., Ltd, China, has rolled its first strip. Shougang Jingtang commissioned Andritz to supply a cold-rolling mill with an annual capacity of 280,000 tonnes for the production of high-strength and ultra-highstrength steel strip for the automotive industry in the summer of 2018. According to Andritz, its S6-high solution provides a means of rolling thinner strip thicknesses, even at yield points of 1,000 MPa or more.
Schade Lagertechnik GmbH will be supplying eight semi-portal reclaimers, each with a capacity of 1,800 tph of iron ore, for Zhongtian Steel Works in Nantong, China. Schade is a member of the Aumund group and represented in China through group unit Aumund Machinery Technology (Beijing) Ltd. In Nantong, Zhongtian Steel is currently building a greenfield
Concept of the new Energiron DRI plant designed for HBIS group

steel plant which is due to commence operations at the end of 2021. Zhongtian Steel belongs to the Zhongtian Group with activities in metallurgy, ports, power plants, logistics and hotel construction.
PHILIPPINES
Capitol Steel contracted Automazioni Industriali Capitanio (AIC) to
update and digitalise the existing
stand drives in the Philippines from the company’s workshop in Torbole Casaglia (BS), Italy. Amongst others, the scope of supply includes the engineering and electrical drawings for digitalisation of the drives, a digitalisation kit the existing stand drives as well as ABB components including a communication card to connect the PLC and the encoder card. At the present time, AIC says, two out of ten stand drives have been commissioned online through video communication platforms and conference calls.
SOUTH KOREA
Paul Wurth has announced the signing of a contract with the South Korean steelmaking group Posco for the new coke oven plant #6 at Pohang steelworks. It includes the supply of refractories and key equipment as well as supervision services to erection and commissioning for two new coke oven batteries and a complete new coke oven gas treatment plant. Equipped with an under-jet heating system, the topcharged batteries will feature 48 ovens each with an oven chamber dimension of 7.6 m height and 20 m length. The batteries are designed to reach a total annual production of 1.5 million tonnes of coke, while the Coke Oven Gas treatment and by-products plant is designed to treat a coke oven gas flow of 100,000 Nm3/h. A particular focus is given to the environmental aspect, Paul Wurth says. For this purpose the company integrates its in-house developed Sopreco system single oven pressure control) for emission control and the “Cokexpert” level- 2-automation system for coke oven plants. The start of the new plant is expected in 2023.
TURKEY
Turkish steel producer Tosyali Demir Celik Sanayi has placed an order with Primetals Technologies to supply a
150-ton EAF Quantum electric arc furnace, a 150-ton twin vacuum-degassing plant with oxygen blowing and a two-strand slab
caster for a flat steel greenfield project in Iskenderun, Turkey. The scope encompasses the complete mechanical and electrical process equipment and the automation technology. This includes the automated scrap yard management, the automated charging process, automation of the oxygen injection and sand refilling, as well as the Level 2 automation. The EAF Quantum is designed to handle metallic scrap and virgin materials such as HBI, pig iron in different composition and quality. The electrical energy requirement of the electric arc furnace is extremely low, Primetals says – mainly thanks to the scrap preheating system, but also due to many other features of EAF Quantum technology, such as FAST Tapping system, continuous foaming slag and continuous submerged electric arc (flat bath operation).

Europe

FINLAND
Primetals Technologies completed the online commissioning of the new software for optimizing the Level 2 process automation for the CCM1 continuous caster at Outokumpu’s plant in Tornio, Finland. The remote commissioning used empirical values gained from commissioning the similar CCM2 continuous caster at the same location in December 2019. As well as upgrading the process optimisation software for the CCM2, Primetals Technologies also installed a TPQC (Through-Process Quality Control) caster system, which records all the quality data of the entire production process in a long-term archive.
ITALY
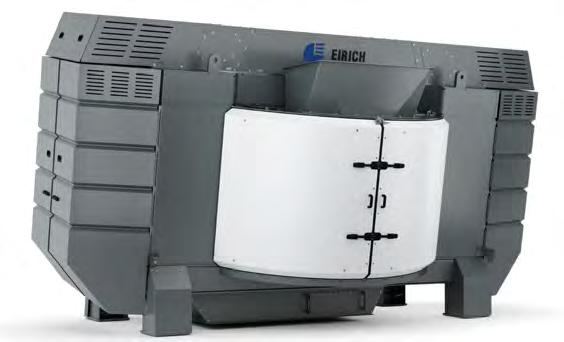
The Arvedi ESP (endless strip production) line at Acciaieria Arvedi in Cremona, Italy was restarted after a major upgrade. The modernization performed by Primetals Technologies include changes to the continuous casting machine, resulting in an increase of mass flow and – consequently – production capacity. Against this backdrop, the upgrade is the first step to raise the overall production capacity of the ESP line
Arvedi ESP line at Acciaieria Arvedi in Cremona, Italy

to 3 million metric tons per year. All modernization work was carried out during planned shutdowns in December 2019 and August 2020, with the ESP line starting up 3 days ahead of schedule. In the first month of operation, production exceeded previous levels, Primetals says. The electric arc furnace (EAF) of the ESP melt shop also received an upgrade and a ladle size increase. Accordingly, the ladle turret was replaced with a larger unit including new software features.
SPAIN
Sidenor Aceros Especiales has commissioned a Reducing and Sizing Block (RSB) 435++/5 in 5.0 design by Friedrich Kocks. The new machine is one of the highlights of the modernisation project at Basauri Works executed by Saralle Group in Spain. The five stand RSB 435++ is based on the newest 5.0 generation and contains a number of modern features. It covers Sidenor‘s size range of rounds from 20 mm up to 120 mm. The remote control (RC) ensures fast size changes and provides flexibility. The Size Control System (SCS) works in a closed loop with the new light section profile gauge, the 4D Eagle, to ensure closest and constant tolerances. Beyond that, the RSB is equipped with a quick stand changing system but also a quick roll changing concept which is installed in the new roll shop area where the setup of the new 3-roll stands and guides takes place off-line during production.
SMS group eyes restructuring and further acquisitions in tough 2021
SMS group believes that 2021 will be another tough year marked by the COVID-19 pandemic, but is optimistic that key performance figures will rebound by 2022. In the meantime, it will be stepping up its services and digitalisation activities.
Family-owned German plant-builder SMS group normally reveals its annual figures in the summer but postponed its annual press conference until the end of November this year. - The conference was held as an online event, with presentations by each member of the management board. In 2019, the company still recorded an increase in its key figures, with revenue up 4.6% on-year to €2.9 billion, order intake up 2.2% to €3.2 billion, and pre-tax profit up 127% to €64 million. The order book at the end of the year stood at €3.85 billion, 6.3% higher than in late 2018.
Mainly due to the coronavirus pandemic, SMS expects order intake to be around one third lower than originally planned for all of 2020. In his address in the annual report 2019, owner and former CEO Heinrich Weiss notes that “SMS is going through a difficult period, the most challenging I have experienced in nearly fifty years since I took charge of the company. Initially, the decline in new orders triggered by global over-capacities in steel production forced us to restructure and downsize our organisation. Now, the impacts of the COVID-19 pandemic have once again dramatically reduced our order intake and, in turn, our workload.”
Apart from a drop in investment spending among mills, the pandemic
CEO Burkhard Dahmen
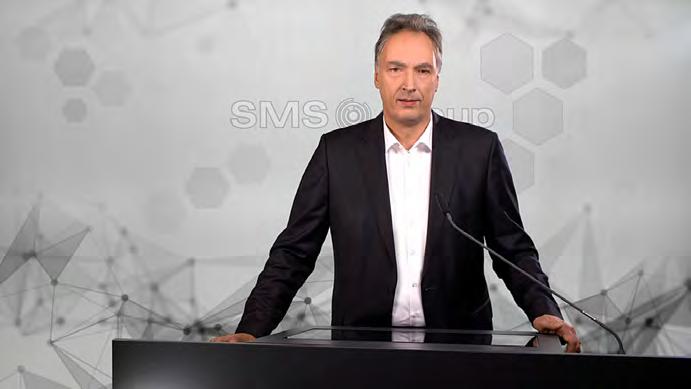
has caused other practical challenges. During the conference, COO Michael Rzepczyk noted that “…the actual construction site remains our main working place, and here we had to cope with massive hygienic regulations, and also with employees infected with the virus.” Thanks to augmented reality and video conferences that seemed to last all year through, the firm managed to finish the projects despite the hurdles. In fact, this year has seen the number of employees in the SMS Digital division more than triple, according to digitalisation officer
Graphic of the The future SMS Campus, under construction in Mönchengladbach, High-speed casting in eight strands on an SMS Concast casting machine North Rhine Westphalia Katja Windt. She predicted that services and maintenance, powered by digitalisation, will make up 50% of the company’s revenue by 2030.

Acting local
Chief executive Burkhard Dahmen emphasised that the company will act more regionally, with representatives that speak the local language at different locations. These “generalists” will be the initial contact for the customer, while the technical sales agent with the appropriate specialisation will come in at the next step.
This shift comes partly as a consequence of plant operators being less willing to make investments this year. “Previously, customers would come to us with some idea of the problem they wanted us to solve. In the future, we will be approaching them more actively, and working together to develop things like software solutions to improve plant availability,” Dahmen said. The lull in investment is mainly affecting the company’s Plant Construction business,
At the 3D Competence Center in Mönchengladbach - Metal Powder and Additive Manufacturing

where a long-term decline in order intake is expected. Against that, the Service and Digitalisation business “…is more continuous and less volatile,” and will, therefore, increase its share in the company’s revenues.
Dahmen highlighted a combination of big data technologies and new business models such as Equipment-as-aService. This new field allows customers to turn their capital expenses into operating expenses, as the plant builder is paid for continuous operation as opposed to just the supply of equipment.
As well as establishing new technologies in the metals industry, such as 3D metal printing and the recovery of precious metals from electronic scrap, SMS group is increasingly transferring its expertise to other industries. Examples of this “New Horizon” strategy include generating environmentally friendly synthetic gases from sewage sludge, which have numerous uses including fuel and energy production. The most recent example is the commissioning of a high-bay storage system for shipping containers in Dubai. This facility owned by SMS joint venture Boxbay offers three times the capacity of a typical container storage facility on the same area. It also boasts a far higher handling speed, improved worker safety and a carbon-neutral footprint, the company says.
The group also announced a change to its corporate structure. Key components
Three fundamental challenges
CEO Burkhard Dahmen identifies three fundamental challenges facing the materials industry today and in the future: *Decarbonisation of the entire industrial value chain, from raw material conversion to recycling. For example, iron ore reduced directly by hydrogen is turned into truly green steel with SMS technology. Our projects not only cut CO2, but they also turn it into new raw material for many branches of industry. *More effective use of plants and equipment across the entire production process. Our rapidly growing service unit offers comprehensive, integrated solutions worldwide, from mechanical optimisation using state-of-the-art automation, to digital, autonomous solutions using “learning” processes. *Technological innovations for the materials of the future. Our recent technology push supports our customers in reducing investment costs, enabling “low-cost” solutions for products and advancing the development of lightweight construction and materials. By combining long-term service contracts and financing models such as Equipment-as-a-Service (EaaS), we create flexible partnerships aimed at increasing investment value in the long term. of the planned new organisation are a cross-divisional, international focus on customer projects. In contrast to the present structure, six regions will assume project responsibility for sales and execution. In place of the current business units, Centres of Excellence (CoEs) will be created that will deliver their services and technologies to the projects. The new organisation will be implemented worldwide from spring 2021.
Expansion outside Europe
SMS will continue to supplement its organic growth with the acquisition of suitable start-ups and established specialists, primarily outside Europe. This year, it acquired shares in Viridis and Vetta, two companies based in Belo Horizonte, Brazil, to create a competency centre for industrial digitalisation. With the acquisition of OMAV and Hydromec, in Italy, SMS expanded its product range in the extrusion plant and forging press sectors.
Major projects in 2019
Steel Dynamics Inc. (SDI) selected SMS to supply a complete steel production line for its Sinton location in Texas, USA, with an annual capacity of over 2.7 million tonnes of steel per year.
Shandong Iron and Steel Riz-
hao gave the final acceptance certificate (FAC) for the pickling line/tandem cold mill, the hot-dip galvanising line and the continuous annealing line SMS supplied to the Chinese steelmaker. The product focus is on demanding cold-strip grades for the automotive industry. The lines are part of a new flat steel complex erected by SMS group in the Shandong Province on China’s east coast.
Turkey’s largest steel producer, Erdemir Group, placed orders with subsidiary Paul Wurth for the supply of two new blast furnaces, replacing existing furnaces at Erdemir’s integrated steelworks in Ereğli and Iskenderun.
On the Virtual Floor: Kallanish’s European Steel Markets 2020
One such event is European Steel Markets by daily information service Kallanish Steel. Originally intended to be staged in Milan, Italy, in spring this year, it was postponed to November and eventually took place virtually on 9 and 10 December. Most speakers originally invited to speak in Milan had since grown accustomed to the idea of delivering their presentation to a camera at home, with one hand on the mouse to navigate their slides and graphics.
The companies that participated actively were large European mills and distributors, including ArcelorMittal, Marcegaglia, Stemcor, SSAB, along with speakers from Kallanish’s own rank of experts on the markets in China and the USA. The timeline was similar to the physical events in previous years in places like Antwerp or Düsseldorf, with six sessions of three to four speakers, and the possibility for all listeners to ask questions in subsequent discussion rounds.

Mills need flexibility
Eurofer, the association of European steelmakers, stressed that extraordinary periods like the current COVID-19 crisis urge steel mills to develop even more flexibility. “The matching of steel production to volatile demand is a key issue, especially given the high volatility we see in the market now,” said Karl Techelet, Eurofer’s director of trade and external relations. He noted that such preparedness takes extra effort to manage capacity, especially with less-flexible blast furnaces. One session was dedicated entirely to the continent’s on-going transition to green steel. Carl Orrling, vice president of technical development at SSAB said the critical question “we should ask ourselves is, can we afford a fossil-free product in the future?” He stated that affordability will be developed synergistically For regular visitors of trade shows and conferences, 2020 has essentially been a year of cancelled events. It is particularly painful for those looking to exchange views and make contacts. By now, many event organisers have adjusted their model to the circumstances, moving the physical meeting to a virtual platform.
through rising carbon costs and improved hydrogen and electricity technology.
However, the future supply of both hydrogen and electricity remains an open question, said German analyst Andreas Schneider of StahlmarktConsult. “I think it’s not a matter of individual European countries—it’s a task for the whole European Union,” he observed. “You will need so much energy and hydrogen, and a lot of countries all over the world will compete for this, and it’s not a question of prices, but availability.”

A message to the world
The sense of a common fate for European steelmakers will ultimately be shared

Beware the Brexit: Gareth Stace of British association UK Steel
by steel producers and consumers worldwide, said Christian Dohr of Feralpi Stahl in Germany. “I think we all find ourselves in a world where we are not isolated anymore,” he commented. “We are all interconnected. These trends will become relevant to everyone very quickly. It matters—to consumers as well. They may not be interested in what steel is in their car or fridge today, but they might be in the future. I think it will become very relevant.”
Along the same lines, Eurofer’s Karl Tachelet emphasised that the proposed EU carbon border adjustment is not only about reducing CO2 emissions, but it is also a message to other countries’ steel
Carl Orrling of Scandinavia’s SSAB explains the group’s path to hydrogen-based steelmaking
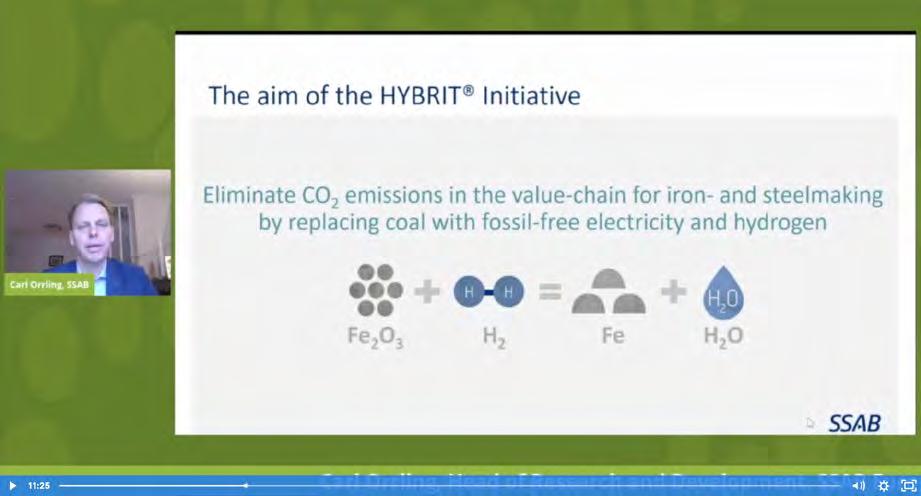
industries of the importance of such action. If this plan works, there will be a global impact on emissions reduction and intensification of investments.
Beware the Brexit
The conference also addressed a crucial issue specific to the continent, namely the exit of the United Kingdom from the European Union, and its effect on steel trade. The EU is the biggest market for British steel exports, accounting for some 2.5 million tonnes/year, or 30% of the UK’s total steel production. Following Brexit, exporters and importers on both sides of the Channel will have to return to standard customs border checks from January, which is likely to cause huge delays and additional paperwork on both sides. “We anticipate that it will result in a 4-5% increase to the cost of supplying steel to our clients in Europe,” said Gareth Stace, director-general of steel federation UK Steel.
He expressed hope that the UK and EU would exempt each other from safeguards, saying that “it would be a win-win situation for both sides.” Karl Tachelet of Eurofer was not quite convinced that this will work. “The EU’s treatment of the UK as a third country is, in fact, the same, as for any country outside the European Union,” he said. “The UK has received a country-specific quota, but on the condition that the total volume does not change. The EU cannot discriminate other states and give Great Britain preferential treatment, which countries such as China, Russia and others do not have.”
Advantages of online events
While online events will never fully replace the feeling of a physical gathering, they do provide some advantages unavailable to face-to-face events, such as watching or re-watching programme sessions on-demand, and the opportunity to connect with many more attendees from around the world that may not have been able to travel to Milan. It also allows for interactive networking, personalised agendas and the ability to engage with speakers via live Q&As and polls.
“Like everyone else, we look forward to the day that the steel industry can gather in person once again. Until then, we are excited to show you what our new virtual event platform can do,” says Kallanish’s event organiser, Bijan Farhangi.
Blast Furnaces in Europe
Sweden
• SSAB Oxelosund
idled
Germany
• ArcelorMittal Bremen • HKM Duisburg • Salzgitter
restarted restarted idled
Belgium
• ArcelorMittal Gent
relining
France
• ArcelorMittal Dunkirk restarted • ArcelorMittal Dunkirk idled (unclear if restarted in December) • ArcelorMittal Fos-Sur-Mer restarted
Spain
• ArcelorMittal Gijón
restarted Finland
• SSAB Raahe
idled
Poland
• ArcelorMittal Krakow
idled permanently
Czech Republic
• Liberty Ostrava
restarted
Slovakia
• USSK Kosice • USSK Kosice
restarted idled
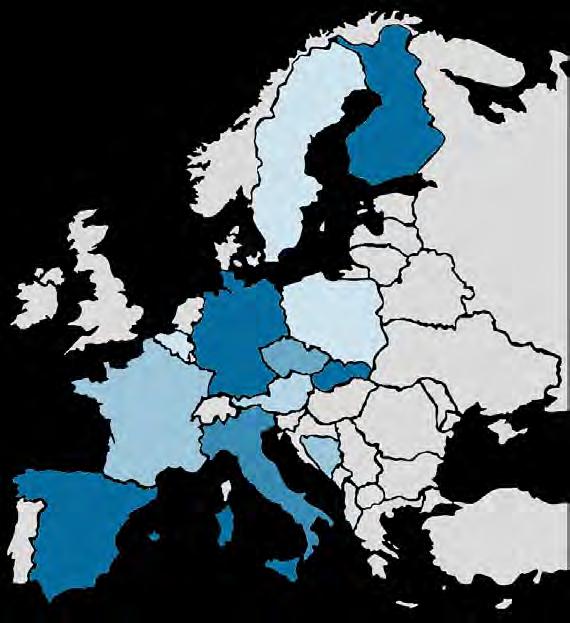
Austria
• Voestalpine Linz • Voestalpine Donawitz
restarted relining
Bosnia
• ArcelorMittal Zenica
Italy
• ArcelorMittal Taranto (clould be restarted in 2021)
idled restarted
An overview of the status quo of activity of blast furnaces which were temporarily idled this year, as compiled by Kallanish editor Emanuele Norsa