
18 minute read
Dansteel: Manufacturing Plates Used in Shipbuilding and Offshore
Making Plates for Shipbuilding and Offshore Structures
Taking into consideration the existing general trends in the development of heavy plate market in the segments of shipbuilding and offshore constructions, new variants of chemical compositions and production technology for the manufacturing of steel heavy plates with a thickness of up to 55 mm from low-carbon microalloyed D36, D40 steel grades in normalized rolled delivery condition (+NR) were developed at 4200-mm rolling complex of NLMK DanSteel. Such types of steel heavy plates are commonly used for the manufacturing of cruise liners.
Advertisement
AUTHOR: E. Goli-Oglu (PhD), Z. Greisen (PhD), NLMK DanSteel A/S, Frederiksvaerk, Denmark
CONTACT: EGO@nlmk.com, ZIB@nlmk.com
Shipbuilding plays an important role in the development of international, regional tourism and passenger transportation. It remains one of the most metal-intensive segments of the transport industry and the foundation for the development of international trade. Trends in the design and construction of cruise liners (Fig. 1) may serve as a vivid example of the dynamic development of the industry. In the 1970s, the average maximum gross volume of typical cruise liners did not exceed 20,000 GT and the length did not exceed 180 m. With increased interest in this type of vessels, as well as the wish of ship owners to turn a cruise liner into a full-fledged leisure and entertainment centre, the net volume of cruise liners increased at least twice a decade over the past 50 years and as of 2018 the largest launched cruise liner is the 18-deck (70 m in height) Symphony of the Seas, produced by the French shipyard Chantiers de l’Atlantique. Its net volume is exceeding 228,000 GT and its length more than 360 m. According to 2018-2019 Cruise Industry News Annual Report (the major printed magazine of the industry), another 30 new cruise liners with a length over 300 m and a net volume of 130,000 to 230,000 GT will be manufactured in 2019 to 2024. An analysis of shipbuilding steel heavy plate markets shows that, first and foremost, the demand for heavy plates with higher thickness (above 40 mm) is increasing. The strength level requirements are increased by at least one class with respect
Figure 1. Evolution of cruise liners modern generation design in terms of net volume and dimensions over the past 50 years
to traditional materials. While the temperature requirements for toughness remain the same (0 and -20 °C), impact energy requirements are becoming more stringent with regard to sampling location together with higher demand in resistance to strain aging processes. Surface quality requirements of plates have also become increasingly important and the presence of surface imperfections/imprints, which are formed due to furnace scale, is not allowed in many cases. The above considerations have increased the economic feasibility for development of new chemical compositions and production technology for shipbuilding heavy plates with higher thickness and strength levels compared to those that have already been implemented at NLMK DanSteel.
Requirements of maritime standards
The main requirements of DNV-GL, RINA, LR, RMRS, ABS and BV international maritime classification societies for the manufacture of steel heavy plates for shipbuilding are similar, since they are based on the requirements of the General Rules of the International Association of Classification Societies (IACS), including acceptance requirements for certification tests in order to confirm the possibility of manufacture of heavy plates of studied steel grades. The existing minor differences are associated with the historical stages of development of regional shipbuilding procedures, as well as with the national or geographical features of each classification society.
Chemical composition
The chemical composition and production technology for the manufacturing of shipbuilding heavy plates in normalizing rolling delivery condition (+NR) previously implemented at NLMK DanSteel was based on microalloying of steel with Niobium and enabled the manufacture of heavy plates with a thickness of up to 35 mm
Steel variant
Mastered (Al+Nb) Steel A (AI+Nb+V) Steel B (AI+Nb+Ni) Quality
A32/A36 D32/D36
A36/A40 D36/D40
Maximum thickness, mm
35
55 C
0.17 Mn
1.5
1.6 Si Al Nb V Within, no more or presence*, %
0.2 0.02
0.4 0.04
0.04
* Actual content of mentioned chemical elements may vary depending on the thickness, strength grade and additional requirements for the weldability of heavy plates Ni
Table 1. Chemical composition of studied steel variants
and with a grade of up to D36 (Table 1). Based on the analysis of production results, it was determined that an increase in the strength level of heavy plates to D40 along with a simultaneous increase in the final thickness of heavy plates to 50-60 mm was possible through the adjustment of chemical composition in two ways. Steel A is based on additional microalloying of Al+Nb-steel with Vanadium in an amount of more than 0.030%; Steel B is based on additional alloying of Al+Nb-steel with Nickel (Table 1).
Production technology
Converter steel, which is continuously casted into 200-355 mm thick slabs at NLMK, is used for the manufacture of heavy plates with the studied quality grades in normalizing rolling condition (+NR). Slab rolling is carried out with the use of NLMK DanSteel 4200-mm four-high reversible rolling stand. Slabs are reheated in a 6-zone continuous walking beam furnace. Depending on slab thickness, reheating phase takes from 4 to 8 hours. In order to ensure the required level of strength and low-temperature toughness, heavy plates are subjected to intensive modes of 2-stage normalizing rolling.
Base metal microstructure
No significant qualitative or quantitative differences in the microstructure of Steel A and Steel B were revealed. Given the differences in chemical composition, a more detailed study, especially at nanolevel, enables the identification of certain differences in precipitations of Nb and V. The microstructure of the studied steel variants represents a mixture of ferrite and pearlite. Grain size assessment is performed in accordance with the requirements of ASTM E1382 and E112. The average matrix grain size (da) at the subsurface (1/8 of the thickness) in studied steel variants is within the range of 6.2-7.6 μm. At 1/4 of the thickness, da is increased to 9.7-10.2 μm, and at 1/2 of the thickness – to 14.5 μm.
Base metal mechanical test results
The complex of mechanical properties of D36 and D40 heavy plates manufactured from Steel A and Steel B is ensured by the selection of optimal rolling parameters taking into account the features of selected chemical composition and the productivity factor of the 4200mm rolling mill. As an example, Table 2 shows tensile properties of Steel B depending on the requested strength level. Tensile tests were performed in accordance with ISO 6892 and EN 10164. Steel A has an equivalent strength level. Optimal temperature and deformation parameters of the two-stage normalizing rolling process were selected for each strength level. Target yield strength ranges serve as the basis for the determination of technological parameters of rolling, namely: for D36 – 370-390 MPa; for D40 – 405-425 MPa.
The results of serial tests for the determination of impact energy curves for Steel A in the longitudinal (L) direction relative to the rolling direction (Fig. 2a) are characterized by a non-uniform distribution and are dependent on sampling location. At the subsurface, impact energy is maintained at the level of 220-190 J within the range of +20 °C to -20 °C. As the test temperature is decreased to -40 °C, a relatively abrupt transition from ductile fracture to brittle fracture mechanism is observed, which is accompanied by a significant decrease in the impact energy to 60-70 J, followed by a further decrease to 10-20 J at lower test temperatures. The reduction in the level of impact energy at 1/4 and 1/2 of the thickness of studied plates occurs more smoothly, however, it starts already from 0 °C. When tested at the target temperature of -20 °C, the impact energy at 1/4 and 1/2 of the thickness is staying on the level 100-120 J and 70-80 J, respectively. At lower test temperatures, the differences in impact energy throughout the thickness of tested heavy plates are minimal.
The level of impact energy (Fig. 2b) in the longitudinal direction of Steel B at the surface is not decreased below 70 J even at -80 °C, and the transition ductile-brittle temperature is within the range of -40 °C and -60 °C. At ¼ of the thickness, when tested at the guaranteed temperature of -20 °C, the impact energy is characterized by the average values of 140-150 J, which is more than 3 times higher than the requirements of the standard. At a test temperature of -60 °C, the level of impact energy has a minimum margin above the requirements of the DNV-GL standards for materials of level E (-40°C) and level F (-60°C) pertaining to steel intended for Northern and Arctic regions. The only reason why the level of low-temperature toughness of studied steel variants cannot qualified to level E (-40 °C) is the test results at ½ of the thickness, where impact energy values are above 46 J only at -20 °C. Low impact energy values at ½ of the thickness are primarily associated with the presence of central segregational heterogeneity and increased ferrite grain size.
It is possible to compare the quality of two studied steel variants by analyzing the level of impact energy with the use of the cumulative result. When summing up 32 reference points, Steel A shows a result of 85 J. Steel B shows a result of 121 J. With a certain degree of deviation, it is possible to conclude that in the framework of the study, the level of low-temperature toughness in terms of total absorbed energy of Steel B is higher than in Steel A by 42%.
Welded joints – Welding parameters Technological parameters of welding and the welding technique differ at various shipyards and for different structural elements, but the main ones include: submerged arc welding (SAW); flux-cored arc welding (FCAW) and gas metal arc welding (GMAW). In order to ensure good weldability of developed steel variants, which is determined by obtaining high results of mechanical testing of welded joints under the most varied welding conditions, various
welding techniques with heat inputs in the range from 15 ± 1 kJ/cm to 50 ± 2 kJ/cm were used during certification testing. The applied welding consumables are certified by the DNV-GL classification society.
Tensile and impact toughness
Studied welded joints with a thickness of 55 mm were tested for strength, static bending on both sides of the weld, low-temperature impact energy at the face, middle and root sides of the weld, the hardness of the weld and the HAZ, as well as a number of additional mechanical tests, the results of which allow evaluating the reliability, cold formability and crack resistance of welded joints obtained through the use of various welding techniques. Tensile tests in the transverse direction with respect to the weld showed positive results for both variants of the chemical composition. Elongation decreased to the average values of 20-21%, which is explained by an increase in volume fraction in a flat tensile specimen of the weld metal, which is characterized by lower plastic properties in comparison with the base metal. Low temperature toughness of welded joints at a temperature of -20 °C is deter-
Parameter
Tensile strength, Rm
Yield strength, ReH
Elongation, A200
RoA in the thickness direction (Z-test), cz UoM
MPa
MPa Strength level
D36 521-564 533 368-421 385 24-30 26
58-72 67
D40 545-593 562 405-450 428 25-32 27
Table 2. Mechanical properties of D36 and D40 heavy plates with a thickness of 55 mm made of Steel B (Al+Nb+Ni)
mined based on the results of impact test of the weld metal, fusion line (FL), and at a distance of FL + 2 mm, FL + 5 mm and FL + 20 mm. Fig. 3 shows the values of impact energy through-thethickness of welded joints (heat input 50 kJ/cm) of VL D40 with a thickness of 55 mm manufactured from studied steel B. The level of impact energy complies with the requirements of the standard.
Microhardness
Standard HV10 hardness measurements in accordance with the requirements of DNV-GL-CP-0243 standard revealed a hardness level of welded joints of studied steel variants not higher than 270 HV, while the maximum allowed value is 350 HV10. A Duramin Struers microhardness tester was used for the performance of additional measurements of microhardness of welded joints. The level of microhardness of the base metal of Steel A near the heat-affected zone (HAZ) is characterized by values in the range of 169-185 HV. After welding with a heat input of 50 kJ/cm (Fig. 4), the HV0.5 level is within the average values of 215 HV with maximum values

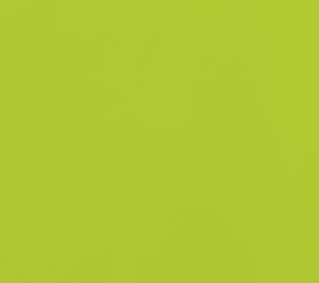

Digitalization
Enjoy the Sound of Silence with PSImetals Quality


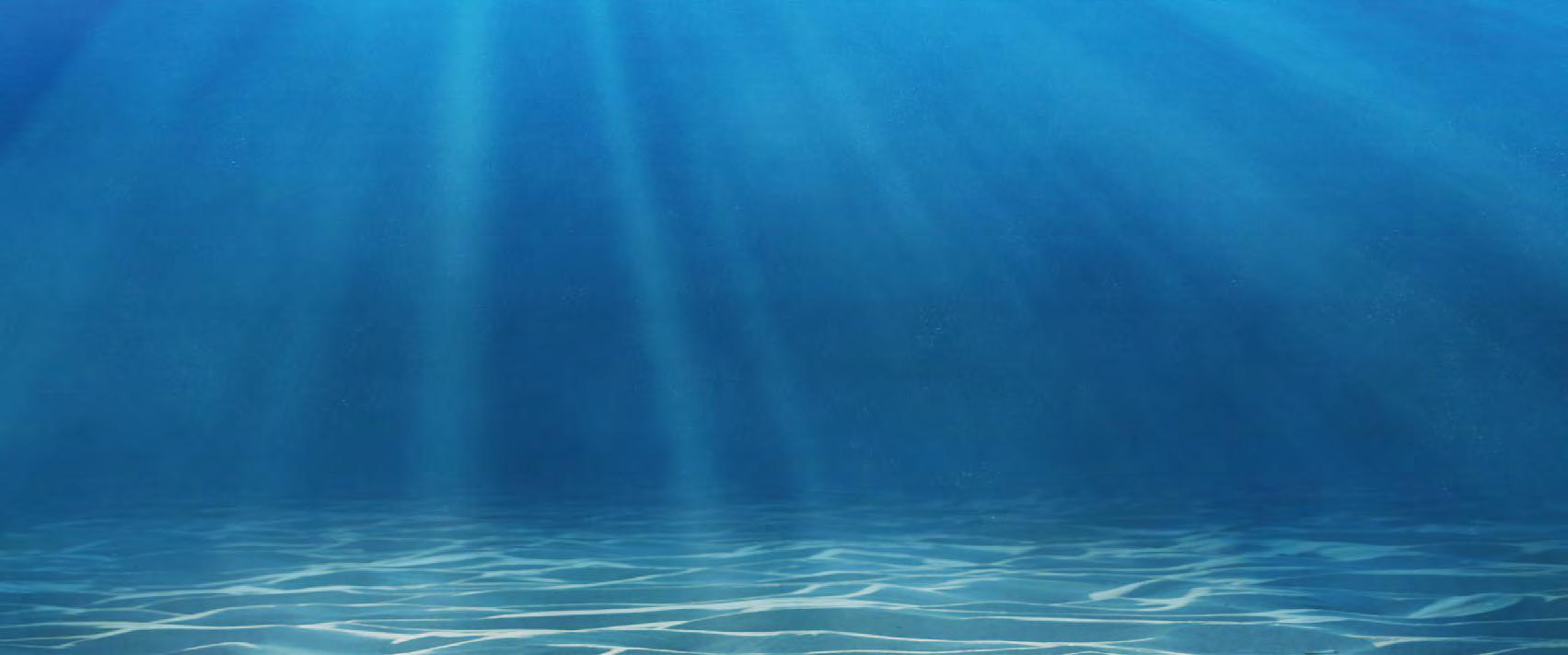
www.psimetals.com/quality


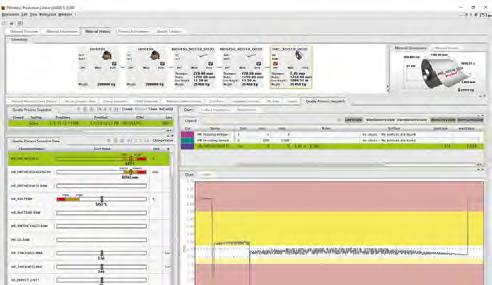
not higher than 250 HV. Separate zones with a microhardness of 230-250 HV can be distinguished, which are most likely caused by additional local hardening of weld metal and characterize the overlapping areas of welding passes. The microhardness level of the welded joint of Steel B does not significantly differ from Steel A. With a certain degree of inaccuracy, a narrower range of hardness of the HAZ can be noted. This could be explained by the absence of vanadium and, consequently, a smaller dispersion hardening effect in the intercritical part of HAZ.
Quasistatic fracture toughness
The quasistatic fracture toughness of welded joints is determined by crack tip opening displacement (CTOD) tests, whose methodology is standardized in ISO 15653 and ISO 12135. Tests are performed on the most brittle section of welded joints of studied steel variants, namely the grain-coarsened heat-affected zone (GCHAZ), along which an incision ending with a fatigue crack is made. Tests are performed on welded joints with a heat input of 50 kJ/cm. The standardized test temperature is -10 °C. According to the requirements of the offshore standard DNVGL-OS-B101, a welded joint is considered reliable in case when the average value of crack tip opening displacement dCTOD is not lower than 0.20 mm. Fig. 5 shows the curve characterizing the conditions for the development of a crack up to the moment of critical opening and the type of fracture of the specimen after the end of testing of the studied material. With regard to the above, crack opening displacement before the break of studied welded joints is different. Steel A specimens are characterized by maximum applied load values Fm CTOD = 126-130 kN, applied specific load value Aplastic = 64-99 kN.mm and crack opening value dCTOD = 0.22-0.30 mm. Steel B specimens demonstrated a comparable level of Fm CTOD = 124-131 kN (Fig. 5),
Figure 3. Impact energy of VL D40 welded joints obtained by SAW process with a heat input of 50 kJ/cm for Steel B a b
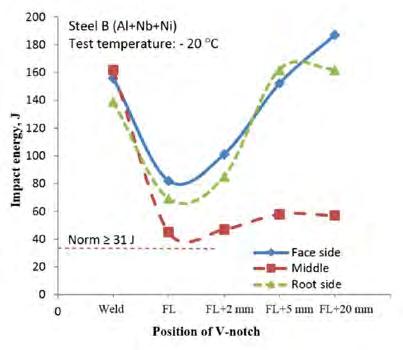

Figure 2. Impact energy in the longitudinal directions of VL D40 heavy plates with a thickness of 55 mm
Figure 4. Microhardness of Steel A after welding with a heat input of 50 kJ/cm

however, they are characterized by higher values of Aplastic = 110-151 kN.mm and dCTOD = 0.33-0.41 mm.
Cold cracking resistance
Cold cracking resistance is associated with the hardenability of steel and hardness increase under the influence of the thermal cycle of welding, as well as saturation of the weld metal and heat affected zone with hydrogen. The lower the Pcm and CEQ values, the lower the risk of cracking. In order to determine the resistance of weld joint of developed steel variants to cold cracking and to determine the need for preheating operations prior to welding, the procedure specified in JIS Z 3158 was used. ESAB AUTROD 12.51 wire was used for the performance of the test. Test results showed the absence of cold micro cracks of welded joints (Fig. 6) when performing the first pass in the workshop temperature conditions 11 ± 1 °C.
Conclusion
Two variants of chemical composition on the basis of Al + Nb + V / Al + Nb + Ni alloy systems and production technology for the manufacturing of VL D36, D40 shipbuilding/
Figure 5. Crack opening curves of Steel B welded joints
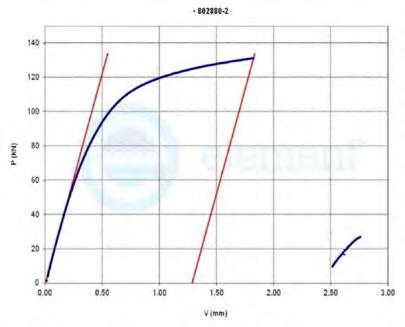
offshore steel heavy plates with a thicknesses of up to 55 mm were developed at NLMK DanSteel. Produced heavy plates meet the required level of strength and low-temperature toughness at -20 °C throughout the thickness. Heavy plates are characterized by a high level of mechanical properties of welded joints when welded with a heat input in the range of 15-50 kJ/cm and are recommended for warm (~580-600 °C) and hot (~ 900-940 °C) forming. The results of testing of base metal and welded joints of industrial batches were used for NLMK DanSteel certification under the general rules of IACS and the rules of DNV-GL, ABS, RINA and BV marine classification societies.
Figure 6. Cross section of welded joint acc. to JIS Z 3158 of steel B

Shipbuilding in Times of Covid-19: A Light in the Far East?
The interruptions of cruise ship tourism and in international transport chains caused by the Covid-19 pandemic brought shipyards to a hal t, with many projects now suspended. Some good news, though, have lately been heard from Russia, where the prospect of a new steel mill for the supply of a shipyard has come up.
BY CHRISTIAN KÖHL
Russian company Rosneft has plans to build a new steelworks on the Russian east coast to meet the needs of the Zvezda shipbuilding yard, Rosneft’s head Igor Sechin revealed during a meeting with Russian president Vladimir Putin on 26 November . Sukhodol Bay was chosen as the most appropriate location for the construction of the new plant with a projected production capacity of 1.5 million tonnes/year of hot rolled flat products and pipe.
According to Sechin, about 330,000-350,000 tonnes would be consumed by the shipyard itself, and new consumers in the region will also be able to use these capacities. Zvezda’s output includes drilling rigs that are designed for year-round work in the Arctic, as well as commercial vessels for transporting goods, and Aframax and Suezmax tankers operating on gas fuel.
But the project is not necessarily welcomed by the Russian Steel Association, which criticises the investment for being unprofitable. Such projects are questionable amid the conditions of steel oversupply not only in Russia but throughout the entire Pacific region, the association finds.
Cruise ships are crucibles for viruses
The one segment in the shipbuilding sector that has been hit worst by the brake on public life from the coronavirus is likely cruise vessels. Cruise tourism in recent years was enormously profitable, but on the downside, the palaces of mass tourism with up to 10,000 people aboard are crucibles for viruses. „There are 400 cruisers worldwide and none of them is at sea now,“ says a spokeswoman at the association of Germany’s maritime industry, VSM. „All of them are sitting at the ports, but parts of the operations need to keep going and create costs.“ In that respect, some parallels can be drawn from cruise liners to blast furnaces at steel mills, which cannot be shut down just like that.
This is fatal for the shipyards specialising in building such vessels. In recent years, these have been the most successful type of newbuildings. Meyer Werften group, for example, with three yards in Germany and Finland, by the end of 2019 had twenty cruise ships under construction, commissioned by companies like Royal Caribbean, Aida and Disney, most of them would have weights of 140,000 – 180,000 tonnes.
The biggest ships under construction are two identical versions of the „Global Dream“ for Silver Cruises with 201,000 tonnes each, at MV Werften, which is owned by Malaysia’s Genting group. Works here have been halted until the end of the year.
Rough times for shipbuilders

Most other shipyards in Germany can still keep up works within the limits of antivirus protection measures. This includes the production of submarines by Thyssenkrupp group, and that of luxury yachts at Lürssen and Abeking & Rasmussen. These are prime choices for the status symbols of billionaires, a customer group little harmed by the economic slowdown.
Shipbuilders insist on quarto plate
The plate typically used for ships is relatively thin, 10 to 15 mm for double-hull ships that are meant to travel fast, and up to 40mm for ships travelling frozen waters in Arctic zones.
However, plate for ships is not the favourite product for mills, the manager of a distribution company, a specialist in plate, points out. „Some mills try to avoid orders for plate grades that are much under 15mm. You need up to ten times the rolling time to get them appropriately thin, but you don’t get ten times the price,“ he explains. Shipbuilders insist on quarto plate and won’t accept plate from coil, which would make the process easier, the manager says. Another effort for the mills are widths of more than 2,000mm preferred by the yards so that they can pre-fabricate very large parts. Still, shipyards are a reliable customer sector for the domestic steelmakers. Imported material is not too popular because frequent reloading at ports makes the material prone to damages, the manager says.
At plate mill Dansteel NLMK, the overall situaion of shipyrads is seen „depressed and volatile“. „The only few segments in shipyards that are still running are middle-to-small size ferries, naval (frigates) ships and that’s more-less it at the moment, says the commercial director of Northern Europe, Eugene Sarkits. „Country-wise we do see some activity in the UK (frigates), Finland (ferry), Poland & Baltics (as subcontractors only) and Germany but in much smaller scope than it was before ,“ he adds.