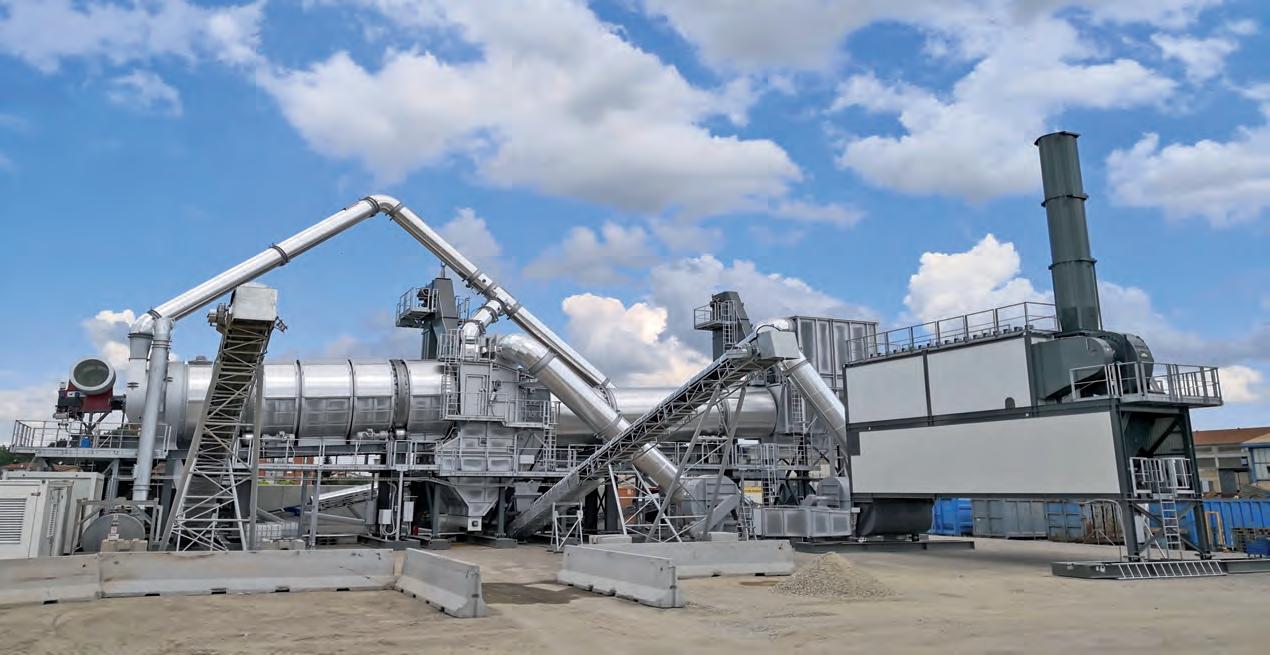
14 minute read
Studiato su misura per le Aziende
asfalti&bitumi
Matteo Ferrario
Advertisement
STUDIATO SU MISURA PER LE AZIENDE
LO SCORSO NOVEMBRE, PRESSO LA SEDE DI ALFONSINE (RA), MARINI HA MOSTRATO IN ANTEPRIMA A “S&A” IL MASTER TOWER, INNOVATIVO IMPIANTO DI PRODUZIONE DEL CONGLOMERATO BITUMINOSO A DOPPIO TAMBURO PRESENTATO AL BAUMA MEDIA DIALOG 2019, CHE CONSENTE UN UTILIZZO DEL 100% DI RAP, ED È STATO REALIZZATO SECONDO UN CRITERIO “TAILOR MADE” PER CLIENTI SENSIBILI A TEMI COME IL RICICLO E L’ABBATTIMENTO DELLE EMISSIONI. DOPO LA VISITA AGLI STABILIMENTI, ABBIAMO FATTO ALCUNE DOMANDE A MARZIO FERRINI E AD ANDREA PIRAZZINI, RISPETTIVAMENTE RESPONSABILE MARKETING E RESPONSABILE RICERCA & SVILUPPO DI MARINI
Negli ultimi anni Marini ha lavorato molto sulla diversificazione dell’offerta, sulla base del principio che ogni prodotto abbia il suo Cliente. Dall’edizione 2016 del BAUMA a quella del 2019 si registra così un aumento delle macchine presentate sia per la gamma Xpress (da 1 a 6), per la gamma di impianti containerizzati Be Tower (ad oggi composta da sette modelli) che per la famiglia Top Tower. Nella sede di Alfonsine ci è stato presentato in anteprima il nuovo impianto Master Tower, un prodotto completamente nuovo. La configurazione presentata è quella classica a torre con sviluppo verticale, ma si tratta di una macchina estremamente flessibile, come prova il fatto che il primo esemplare venduto in Italia nel 2018, e in consegna all’inizio di quest’anno, sia stato scelto in sostituzione di una macchina esistente.
IL FRESATO D’ASFALTO
La presentazione del Master Tower da parte di Marzio Ferrini si è aperta con una riflessione su questo tema, ancor più centrale dopo l’entrata in vigore del D.M. Ambiente 28 Marzo 2018, n° 69, che disciplina la cessazione della qualifica di rifiuto per il conglomerato bituminoso proveniente da fresatura a freddo o demolizione delle pavimentazioni stradali, stabilendo i criteri per trattamento, qualificazione e conferimento all’impianto. Il primo messaggio che viene trasmesso dal criterio “end of waste” è che il fresato d’asfalto rientra fra i pochissimi materiali riciclabili al 100%. Il conglomerato bituminoso si può dunque recuperare, e le possibilità di impiego sono molteplici: pavimentazioni a freddo, caldo o tiepido, consolidamento del sottofondo e opere di ingegneria civile come il riempimento di fondazioni. In mercati maturi come quello europeo si tenderà dunque sempre più a recuperare pavimentazioni esistenti, e il materiale nuovo sarà via via meno utilizzato, anche in considerazione della grande quantità di fresato che viene generato ogni anno e delle conseguenti difficoltà di smaltimento da parte dei grossi produttori: un problema che può trasformarsi in una risorsa, grazie ai vantaggi che questo materiale presenta. Il primo è nella sua ecosostenibilità: minor impatto su tutto il sistema, minor necessità di asportare materiale nuovo dalle cave, a maggior ragione considerando che non si riesce a smaltire il fresato che arriva in stabilimento con cadenza quotidiana, e che il materiale recuperato nel fresato può essere correttamente impiegato se riadditivato.
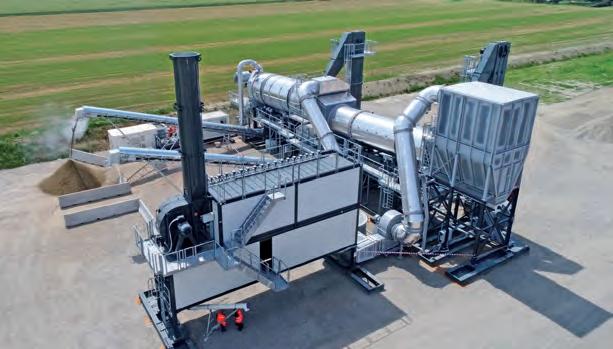
1. Il nuovo Master Tower
IMPIANTI PER CONGLOMERATI BITUMINOSI
Il secondo vantaggio è quello di natura economica, sia per le Aziende produttrici che per la collettività, attraverso la potenziale riduzione dei costi di opere pubbliche: attraverso il reimpiego del fresato d’asfalto, un produttore che investe in tecnologie e ricerca, riuscendo al contempo a contenere i costi, può essere competitivo nelle gare d’appalto. Il terzo è un vantaggio prestazionale, poiché è stato ormai smentito da molti studi il pregiudizio iniziale secondo cui il mix ottenuto con impiego di fresato sarebbe una miscela “vecchia”: al contrario, non si pone un problema tecnico o di prestazioni, e l’applicabilità sul mercato italiano nel rispetto delle norme e delle prescrizioni dei Capitolati non è in discussione.
LO STUDIO SUL MATERIALE PER AUMENTARE LE PRESTAZIONI
In un’apposita area test presso la sede Marini è stata ricreata una sorta di cantiere sperimentale in cui condurre verifiche e indagini conoscitive su come il materiale reagisce a un diverso impiego dell’impianto. Forte di un’esperienza di produzione dei macchinari di quasi 120 anni, l’Azienda si sta concentrando ora sull’obiettivo di colmare il divario fra le esigenze dei Clienti e l’esperienza dei laboratori. Come sottolineato da Ferrini nel corso della sua presentazione, non si consegna più soltanto il prodotto, ma un pacchetto di esperienza di cui la macchina costituisce solo una parte. Allo scopo di far rendere l’impianto al massimo delle sue prestazioni, il team di lavoro ha eseguito una campionatura del materiale, riqualificato il bitume all’interno, rideterminato il fuso e condotto prove di laboratorio per capire come il riscaldamento di alte percentuali di fresato impattasse sulle caratteristiche prestazionali del conglomerato. In questo ambito è risultata fondamentale la collaborazione tra Marini e le singole Aziende del territorio, che si erano poste il problema di come ottenere una miscela prestazionale impiegando molto fresato, e sono risultate fondamentali con la loro esperienza. Queste potenzialità sono state confermate dall’esperienza con una pavimentazione stradale in cui i tre strati sono stati realizzati da un impianto del Gruppo Fayat in Francia, a Nord di Bordeaux, con impiego del 100% di fresato, ottenendo un risultato soddisfacente sul piano prestazionale.
L’INFLUENZA DELLA TEMPERATURA E DELLA SCELTA TECNOLOGICA SULLE EMISSIONI
La presenza di impianti nel territorio è spesso causa di disagio da un punto di vista olfattivo per i residenti in aree limitrofe, oltre che di inquinamento. In generale, l’impatto viene controllato attraverso i limiti di emissioni in atmosfera prescritti dalla Legge: l’Italia ha i suoi, che purtroppo non sono armonizzati da un Ente locale a un altro. Alcuni parametri sono molto influenzati sia dalla scelta tecnologica che dalla temperatura: i loro valori tendono a crescere di pari passo con l’impiego di granulato d’asfalto nella produzione della miscela, e con l’aumento della temperatura a cui viene riscaldato il bitume. Allo scopo di conciliare con tali limiti le possibilità di impiego del riciclato, è stata quindi condotta da Marini un’indagine volta a comprendere come le emissioni varino in funzione della temperatura del conglomerato, soprattutto quello contenente fresato: oltre i 240 °C circa, quest’ultimo perde una certa quantità di peso, corrispondente a una quota parte di un idrocarburo, che dopo aver subito un processo di invecchiamento oltre questa temperatura viene ulteriormente danneggiato. Tra le tecnologie disponibili sul mercato per l’impiego di fresato in impianto, Ferrini ha evidenziato come quella a freddo, che offre il vantaggio di poter produrre una miscela vagliata, sia indicata per piccole percentuali di fresato, ma oltre il 15-20% presenti un limite: introducendo una elevata quantità di fresato, viene immessa anche una quantità considerevole di acqua che deve essere rilasciata in pochi secondi, tramite evaporazione. Si ha quindi una quantità enorme di vapore da evacuare con il problema del surriscaldamento di aggregati vergini a 300-400 °C, temperature a cui il bitume si danneggia.
LA SOLUZIONE DEL DOPPIO TAMBURO
Per l’essiccazione, il Master Tower impiega un’innovativa soluzione integrata, con bruciatore unico, che consente l’impiego di percentuali rilevanti di riciclato con basse emissioni. A differenza delle tradizionali tecnologie che prevedono la generazione di elevate temperature - che inevitabilmente vanno a danneggiare il materiale fresato -, nel Master Tower l’aria calda è veicolata in un processo controcorrente all’interno di un doppio tamburo: il materiale fresato entra da un lato e incontra il flusso d’aria calda prodotto in direzione opposta. L’energia termica viene ricevuta da aggregati che contengono umidità, fino al raggiungimento della temperatura di 160 °C, analoga a quella richiesta all’uscita dall’impianto: ciò rende possibile un impiego di RAP pari al 100%. Il cuore dell’impianto consiste nel controllo della temperatura prodotta nel primo cilindro e trasferita in volumi d’aria calda al secondo: esso avviene attraverso un sistema di ricircolo dell’aria, e un insieme di strumenti che permettono di tenere monitorato in tempo reale lo scambio termico nel primo cilindro, nel secondo e nel condotto centrale, per poter gestire le temperature. I due tamburi posti in linea presentano l’enorme vantaggio di un minor consumo, in quanto alimentati da un solo bruciatore.
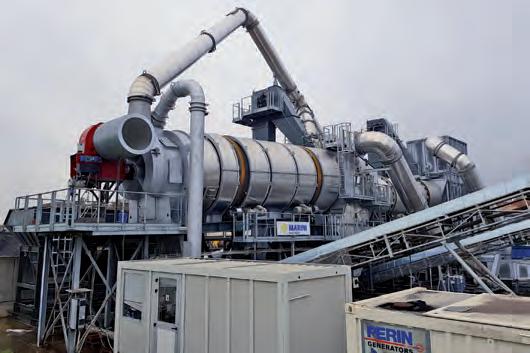
2. Grazie alla soluzione innovativa del bruciatore unico, il Master Tower consente di impiegare alte percentuali di riciclato con emissioni contenute
asfalti &bitumi
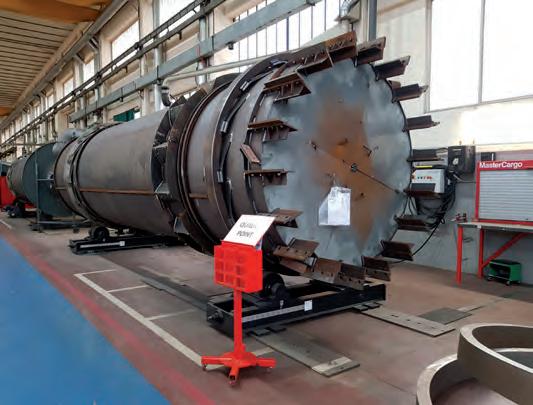
3. Il doppio tamburo
Nel caso del nuovo Master Tower, il materiale viene scaldato in cima e poi scaricato nelle rispettive tramogge a seconda che sia vergine o RAP. I tamponi permettono di variare le percentuali di fresato, evitando limitazioni nella produzione. La capacità di stoccaggio è di circa 130 t di fresato riscaldato a 160 °C (oltre il doppio della capacità massima di circa 60 t attualmente offerta dal mercato). Per il materiale vergine la proposta Marini è di 200 t, ma è possibile arrivare a capacità superiori. Oltre all’utilizzo con 100% di fresato e a quello con 100% di materiale vergine, è possibile quello con miscele variabili. L’obiettivo era quello di creare un impianto dotato di estrema flessibilità, e poteva essere raggiunto solo con una macchina basata su questa concezione, ma anche supportata da una torre completamente nuova: si tratta quindi di un unicum nella produzione Marini, non paragonabile ad altre macchine più seriali, perché studiata secondo un criterio “tailor made”.
UN PERCORSO SPERIMENTALE DI TRE ANNI
La tecnologia sviluppata per il Master Tower è il risultato di tre anni di lavoro che hanno visto Marini affiancata da Enti di ricerca autonomi. Un Bando di gara con fondi europei ha aiutato a sostenere parte dei costi di sviluppo della macchina. Un aspetto di particolare interesse di questa fase riguarda il fatto che, per ridurre il “time to market”, Marini si è affidata a processi di sviluppo del progetto basati su simulazioni ad elementi finiti del processo di fluidodinamica a livello di scambio termico, progettazione macchina a livello virtuale, simulazione funzionamento e correzioni sul modello. Entrambi i cilindri del doppio tamburo sono pieni di sensori e strumenti di diagnostica al fine di inviare le informazioni necessarie affinché il nuovo software, sviluppato per questo tipo di impianto, possa gestire la macchina in modo semplice per gli operatori. La soluzione tecnica più efficiente per i volumi d’aria calda destinati a riscaldare aggregati bagnati, con un bruciatore unico che consente di arrivare fino al 100% di RAP risparmiando fino al 30% di energia, è stata sviluppata prima attraverso simulazioni e successivamente con verifiche in cantiere, e ha richiesto uno sforzo notevole prima del deposito del brevetto. Quest’ultimo guarda a nuovi standard di impiego di granulato d’asfalto - con un’elevata flessibilità produttiva, e una perfetta verticalità tra il punto di uscita del fresato riscaldato a 160 °C e l’ingresso nel mescolatore allo scopo di prevenire fenomeni di impaccamento dovuti a cambi di direzione - ma anche alle tecnologie costruttive di un tamburo essiccatore: questa soluzione è volta infatti a preservare il più a lungo possibile l’acciaio del tamburo dagli effetti inevitabili del calore. Un altro brevetto Marini è quello che riguarda la ricombustione del particolato, e che permette ad oggi di bruciare parte dei fumi e degli odori prodotti dal processo di produzione miscele a caldo in un processo efficace.
Di seguito riportiamo quanto è emerso dalla nostra conversazione con Marzio Ferrini e Andrea Pirazzini.
“Strade & Autostrade”: “A quale tipo di Clientela si rivolge il nuovo impianto Master Tower?”. “Marzio Ferrini”: “Il nuovo impianto Master Tower è nato per rispondere a tre ben chiare esigenze: 1) confinare e trattare tutte le emissioni di natura sia gassosa che odorigena, prodotte negli impianti per conglomerato bituminoso a caldo; 2) permettere il riutilizzo di materiale proveniente dalle pavimentazioni stradali esistenti, offrendo la più totale flessibilità in termini di percentuale di impiego, fino anche al 100% di fresato; 3) abbattere significativamente i consumi energetici, generando sia un reale beneficio per i produttori sia un altrettanto reale beneficio per l’intera collettività in termini di minori emissioni di CO2. In definitiva, ogni Cliente che guarda al futuro ed all’innovazione tecnologica per la propria attività produttiva, non può che essere interessato a confrontarsi con questo nuovo tipo di impianto”.
“S&A”: “Ad oggi la soluzione del doppio tamburo con riscaldamento del fresato tramite volumi d’aria calda e funzionamento in contro corrente rappresenta lo stato dell’arte e, come da lei sottolineato nella presentazione, una sorta di vestito su misura per il Cliente. Crede che in futuro sia destinata a un impiego sempre più esteso, fino a soppiantare definitivamente la soluzione tradizionale dei due tamburi separati con altrettanti bruciatori?”. “MF”: “Il Master Tower segna uno spartiacque negli impianti per CB a caldo con soluzioni tecniche brevettate e tecnologie innovative, che permettono di utilizzare in maniera efficiente un solo bruciatore invece di due. Per rispondere alla sua domanda, sono convinto che chi dovrà affrontare l’acquisto di un nuovo impianto equipaggiato con un tamburo dedicato al riscaldamento del fresato, valuterà l’acquisto del Master Tower ed il mercato si popolerà progressivamente di nuove unità. Se poi arrivasse a soppiantare definitivamente i due tamburi con due bruciatori, ne saremmo molto felici”.
IMPIANTI PER CONGLOMERATI BITUMINOSI
“S&A”: “Il Master Tower sarà la novità principale presentata da Marini al BAUMA 2019: in considerazione delle dimensioni dell’impianto, e dell’esigenza di mostrarlo al pubblico sia nel dettaglio delle sue componenti che nell’insieme, che soluzione adotterete a livello espositivo?”. “MF”: “Questi impianti hanno dimensioni molto importanti e dall’esperienza già maturata in molte precedenti fiere internazionali è evidente questo: un impianto alto 45 m impressiona per la sua mole ma non permette di apprezzarne le caratteristiche, né tantomeno di poter ricevere una spiegazione da parte degli specialisti di prodotto. A BAUMA 2019 abbiamo deciso di presentare un prodotto più a misura del visitatore, sia che si tratti dello specialista di settore sia del semplice visitatore, attraverso un modello in scala 1:5 del Master Tower nella configurazione completa. Si andrà dai predosatori per gli aggregati vergini e il fresato alle cisterne del bitume, dal silo del filler verticale alla torre di nuova concezione, che sarà alta ben 7 m! A corredo del modello in scala saranno disponibili innovative soluzioni digitali per poter raccontare l’intero processo in modo nuovo ed efficace”.
“S&A”: “Vuole parlarci del percorso sperimentale di tre anni che ha portato alla realizzazione del Master Tower?”. “Andrea Pirazzini”: “Marini è da sempre attenta alle esigenze dei Clienti, all’innovazione e al rispetto dell’ambiente: ad esempio introdusse e brevettò a suo tempo l’anello di riciclaggio all’essiccatore, poi il riciclaggio “combinato” e riciclaggio in situ, solo per citare alcuni esempi. Tre anni fa abbiamo avvertito una forte richiesta da parte del mercato di soluzioni innovative ed alternative a quanto già disponibile, che consentissero l’utilizzo di alte percentuali di fresato nel rispetto delle emissioni in atmosfera, riducendo i consumi energetici. L’idea della macchina è nata da un brainstorming collettivo, partito dalle esperienze maturate dall’Azienda per andare su una prospettiva diversa di macchina, che mirasse al cuore del “problema”. Al contempo c’è stata la possibilità di intraprendere un percorso per il finanziamento europeo per progetti di rilevante innovazione tecnologica. Durante lo sviluppo della macchina ci siamo avvalsi dei migliori software disponibili per simulare i processi più innovativi e complessi, dalla distribuzione delle temperature e delle velocità dei gas con il CFD, alla simulazione del comportamento del materiale all’interno degli essiccatori con il DEM. Il progetto ha riguardato anche un’indagine sul materiale RAP, attraverso simulazioni in laboratorio per verificare come ridurre il processo di impaccamento. Per essere all’avanguardia abbiamo anche pensato che il software di gestione dovesse essere di nuova generazione, con un controllo automatico e predittivo dei processi fisici che si sviluppano all’interno della macchina, al fine di semplificare e ridurre l’attività dell’operatore. Il passo conclusivo del progetto è consistito nella costruzione e installazione di un prototipo funzionante all’interno della Marini, che ci ha permesso di eseguire tutti i test di validazione della macchina prima di immetterla sul mercato”.
“S&A”: “Quali sono gli Enti autonomi con cui avete collaborato, e qual è stato il loro ruolo?”. “AP”: “Abbiamo collaborato con Aziende e laboratori facenti parte della rete dell’alta tecnologia della Romagna per la parte di simulazione CFD e DEM (Romagnatech) e per le analisi sui materiali (Certimac). Per lo sviluppo del software ci siamo invece rivolti al dipartimento di Automazione dell’Università di Bologna”.
“S&A”: “Il brevetto riguardante il processo di ricombustione delle sostanze nocive come i COV (Composti Organici Volatili) è stato ottenuto con un lavoro “sul campo” anziché attraverso la simulazione. Vuole parlarcene più nel dettaglio?”. “AP”: “Le basi del nuovo progetto nascono qualche anno fa con lo sviluppo di un’applicazione particolare richiesta da un Cliente. In quell’occasione abbiamo sviluppato un essiccatore in grado di ridurre, attraverso un processo di ossidazione, il quantitativo di sostanze inquinanti come i COV emesse dal processo di produzione del conglomerato bituminoso. Questo essiccatore è stato utilizzato per una campagna di acquisizione dati, per la validazione dei modelli matematici alla base del progetto del Master Tower”. n
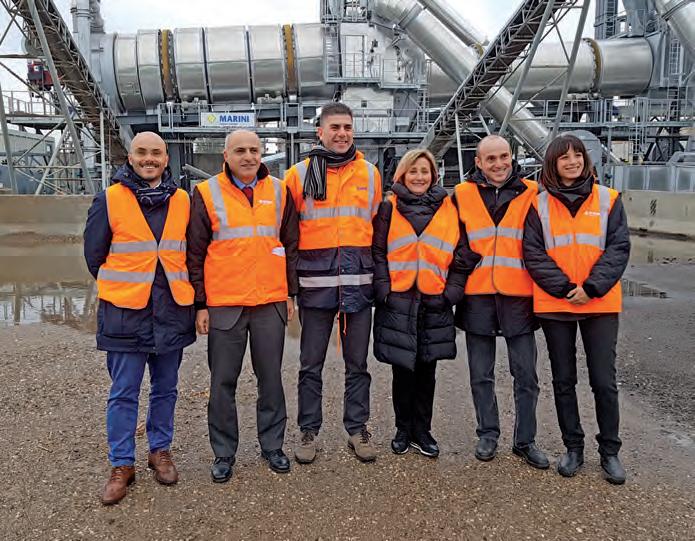
4. Il team che ci ha accompagnato nella visita al cantiere sperimentale del Master Tower. Da sinistra: Marzio Ferrini, Responsabile Marketing di Marini, Paolo Monduzzi, Responsabile Operativo di Bomag Alfonsine, Daniele Rambelli, Responsabile Operativo di Marini, Gian Paola Pezzi, Responsabile Comunicazione di Marini, Andrea Pirazzini, Responsabile Ricerca & Sviluppo di Marini, e Delia Forte, Addetta Comunicazione di Marini