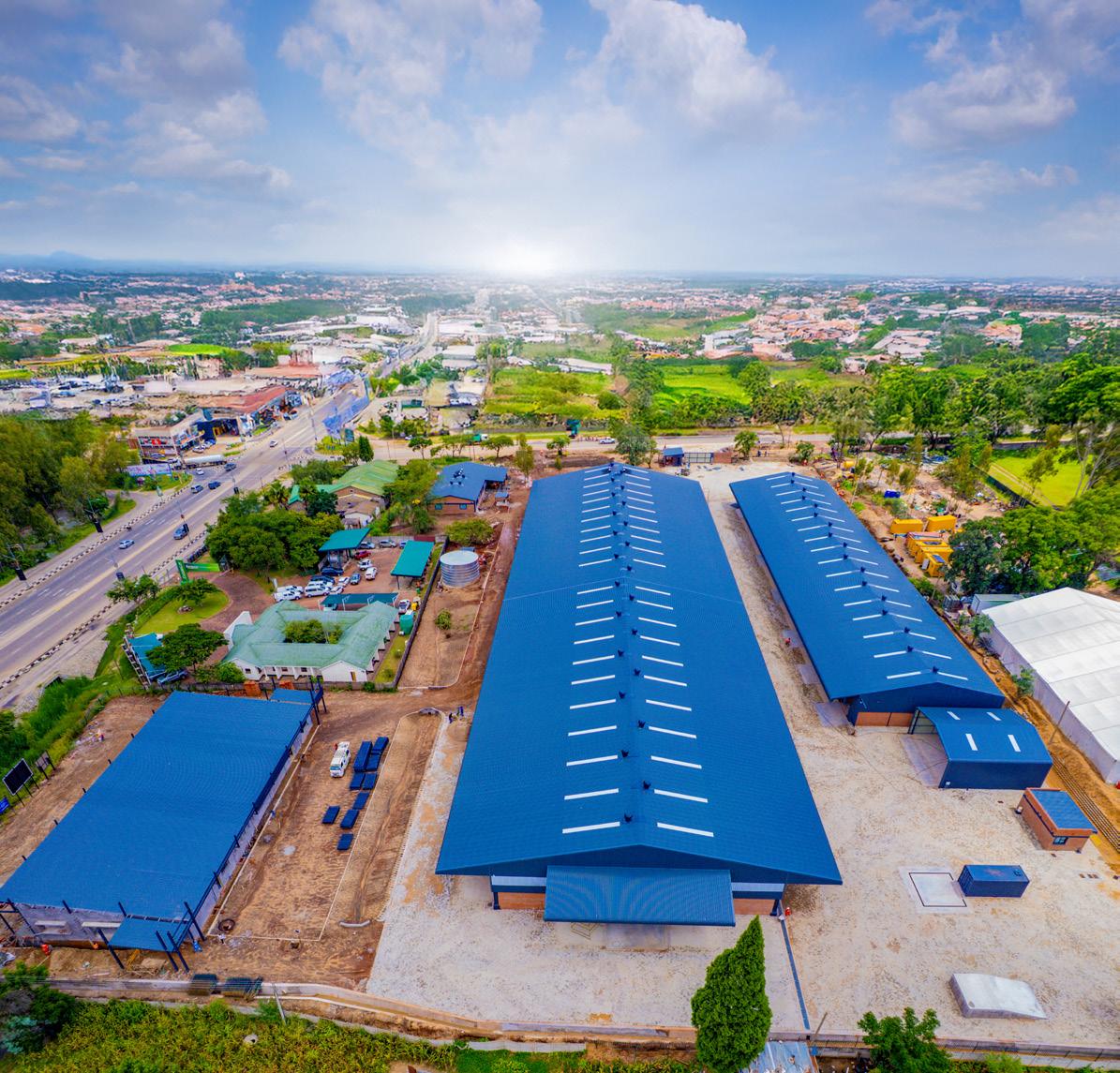

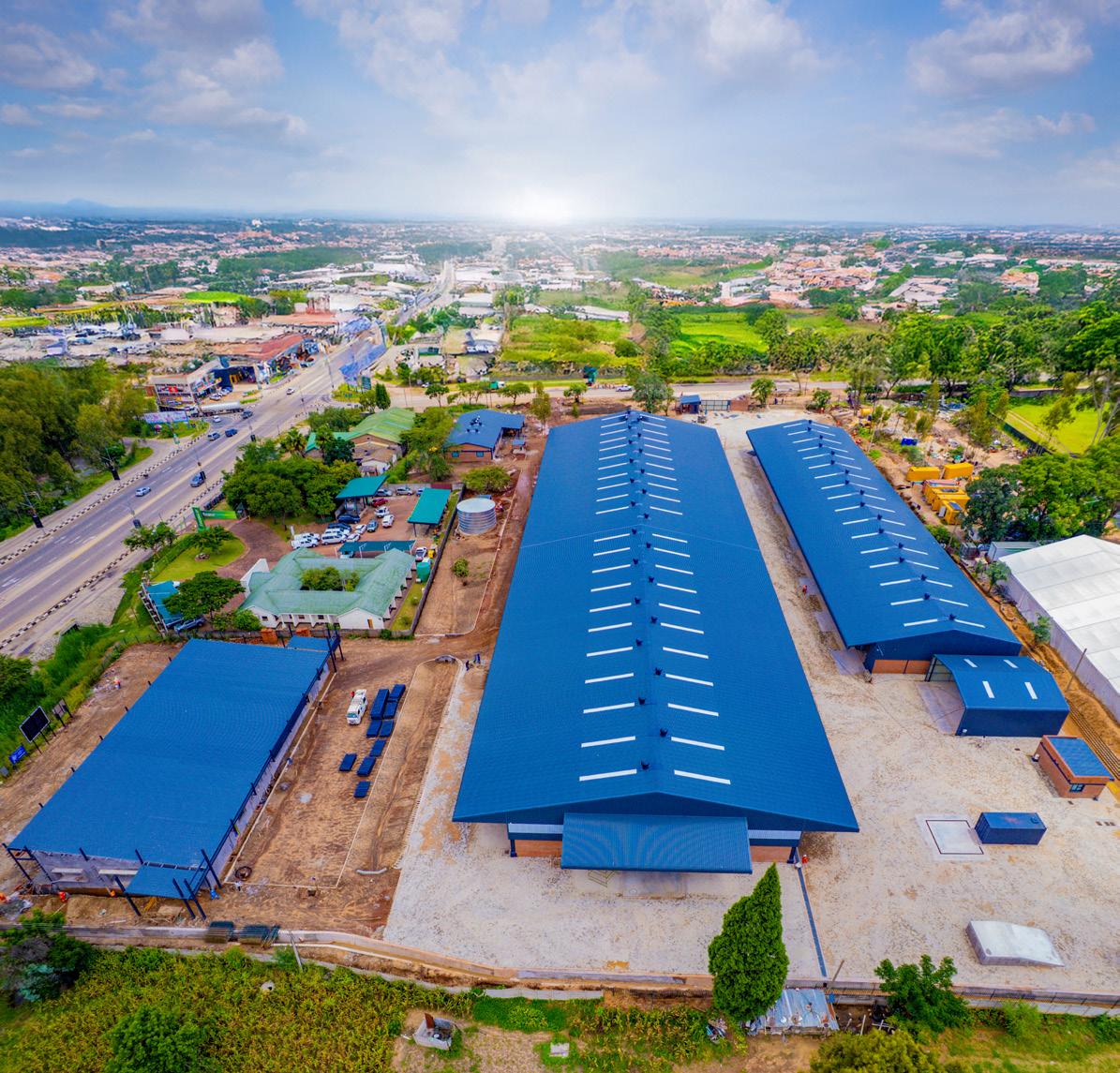
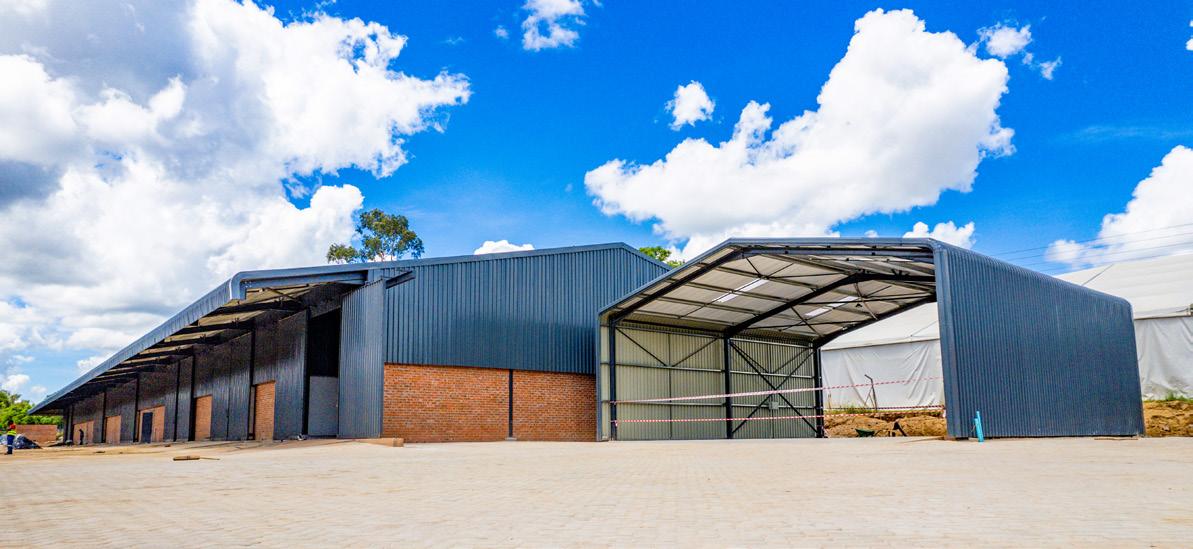
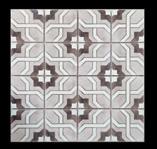

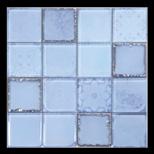
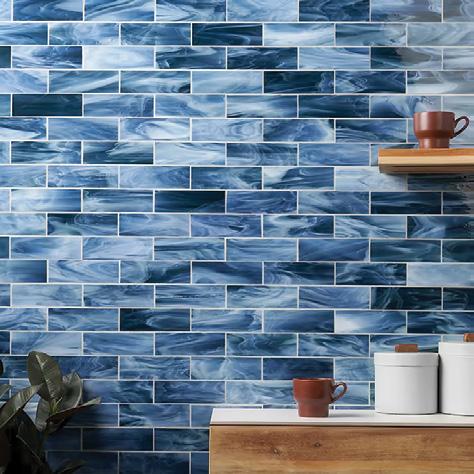
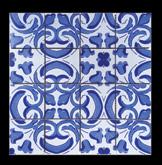
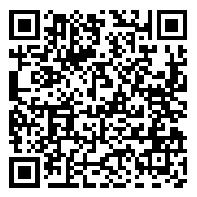
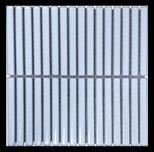

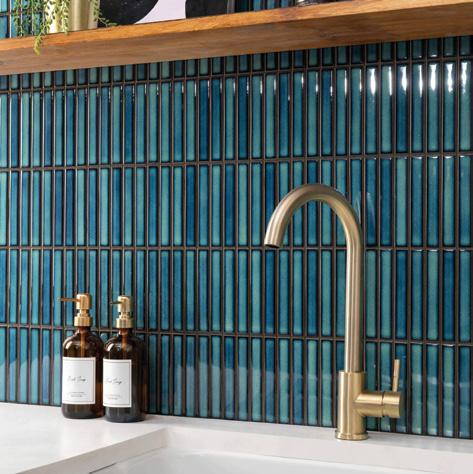
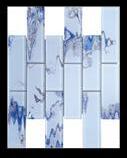


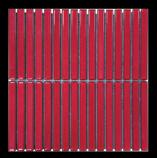
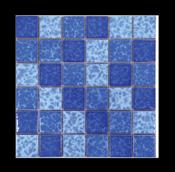
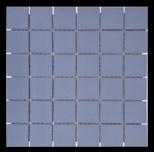
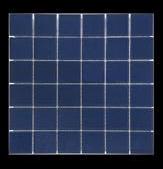
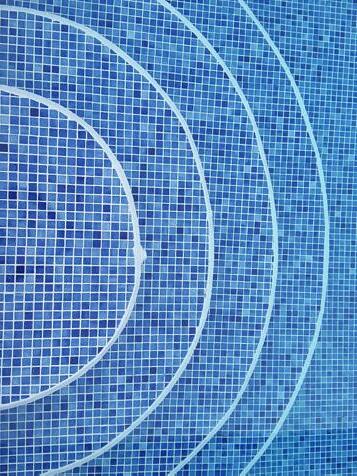
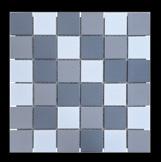
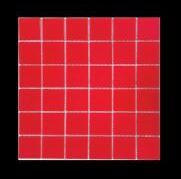
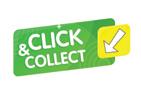
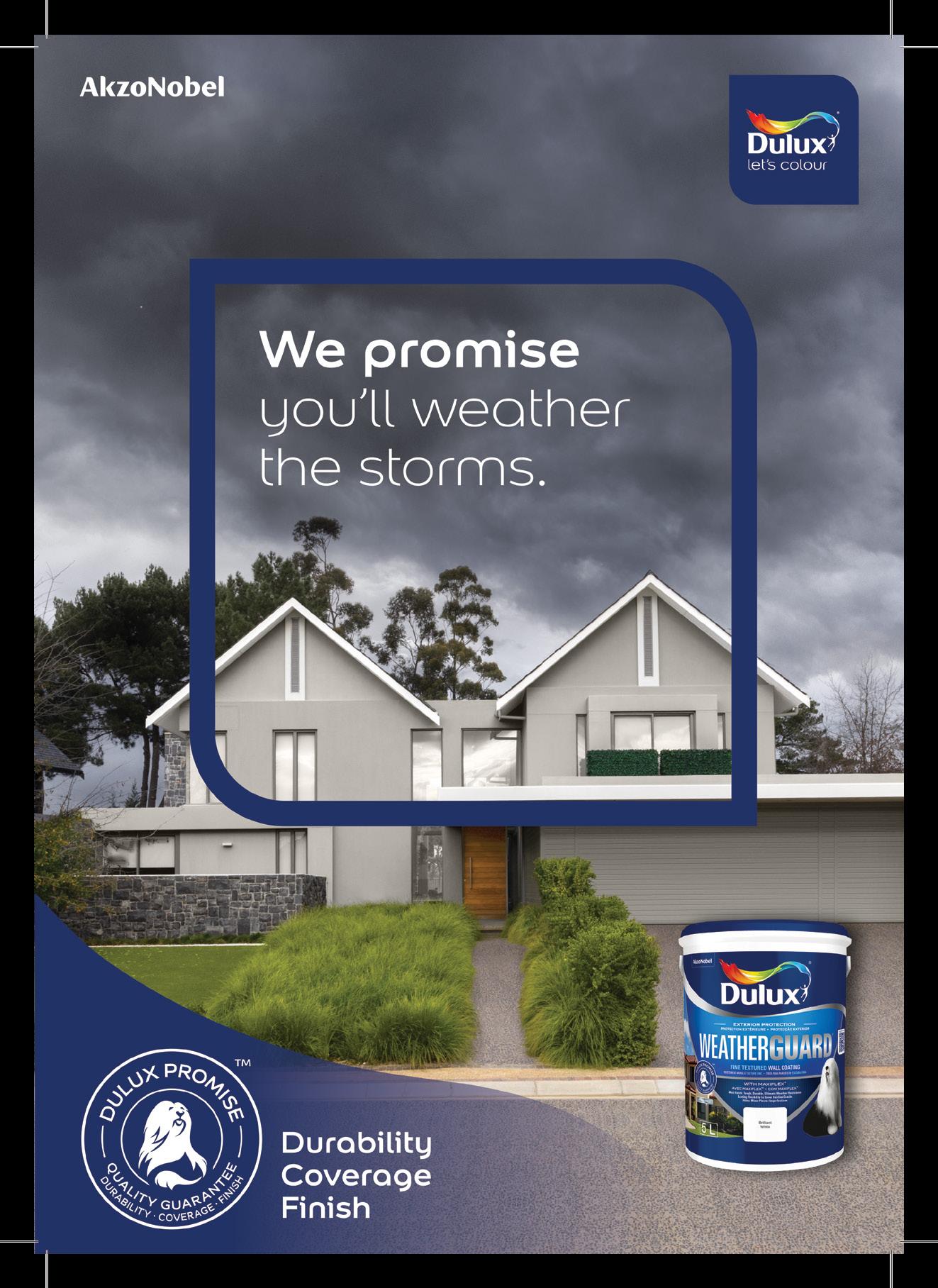
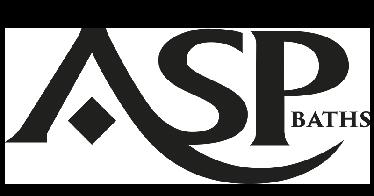
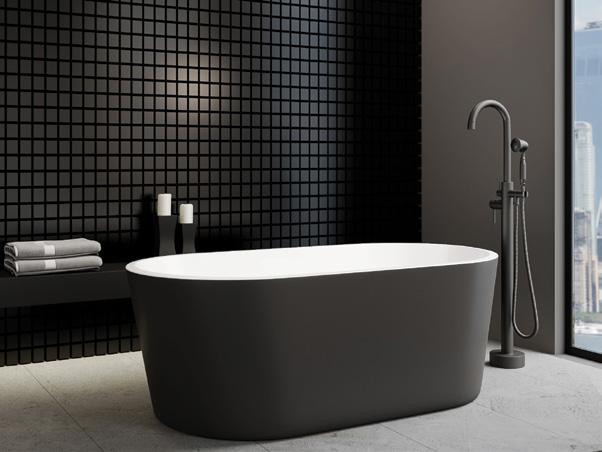
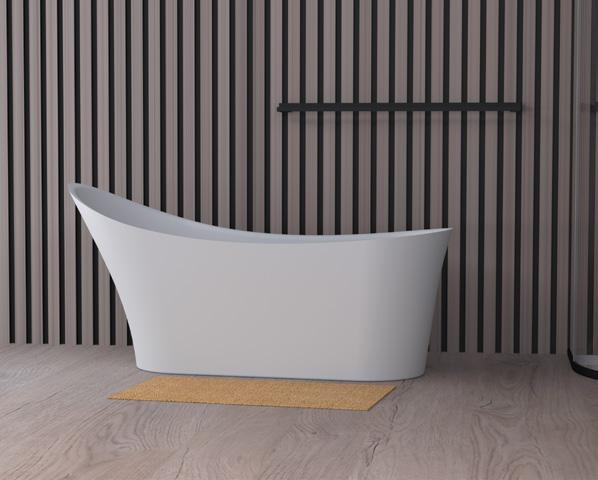
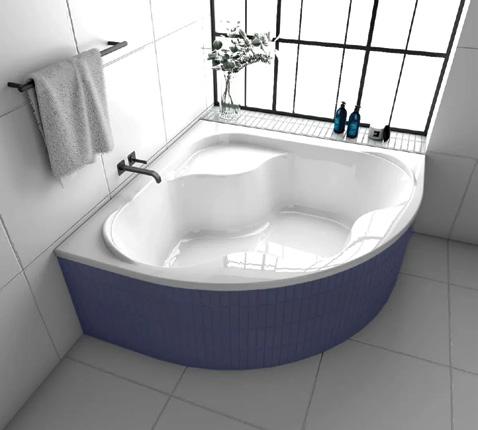
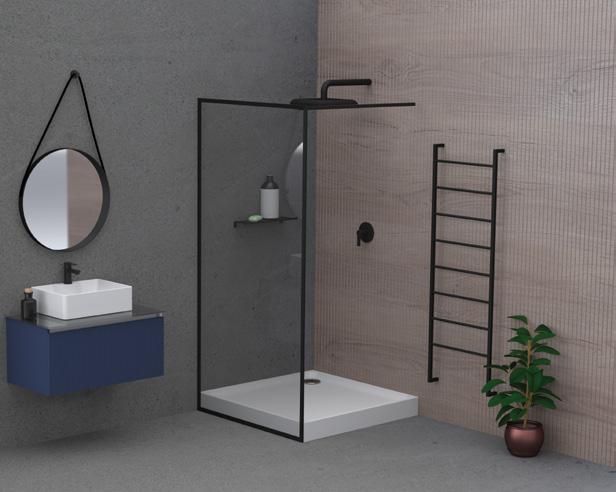


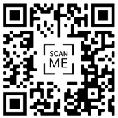
We begin with an update on Kalamain’s impressive redevelopment of the Rooneys Headquarters in Hatfield. The project, nearing its March deadline, stands as a testament to Kalamain’s expertise in handling complex commercial undertakings. Building on our previous coverage of the structural phase, we highlight the meticulous attention to detail in the installation of the drainage system. Recognizing the potential for significant disruption without effective water management, the team ensured a flawless execution, marking one of the final major tasks. With the structural framework largely complete, the focus has shifted to refining the buildings’ aesthetic and functional interiors. Construction teams are now concentrating on crucial wet trades, including flooring, concrete finishing, and skimming, across the three primary buildings designated for events, administration, and the canteen. Construction resumed on January 12th, underscores Kalamain’s commitment to delivering a high-quality finished product. The Rooneys Headquarters transformation is poised to become a showcase of Kalamain’s expertise and dedication.
DripTech Irrigation has opened a new facility in Pomona, Borrowdale, adding to their steadily expanding branches across Zimbabwe. Originally focused on micro-irrigation, it has broadened its offerings to include a comprehensive array of water-related products, including borehole pumps, tanks, pressure tanks, booster pumps, and an extensive range
The Hive 25 is a vibrant business hub where professionals can work, connect and grow in an environment infused with natural beauty and community spirit. The place is not only a sanctuary for productivity, creativity and collaboration, but one aimed at building a community.
Coastal Construction, a leading and trusted name in construction, offers a comprehensive range of services to bring your vision to life. Based in Harare, they specialize in all aspects of brickwork, substructure foundations, and related works.
The mining town of Mazowe is poised for a of a state-of-the-art shopping mall, known as Mazowe Walk Shopping Mall. This ambitious project is being spear headed by Gateway Construction.
Simultaneously, the construction of Rooney’s Hire Services’ new headquarters along Harare’s Airport Road is surging toward completion. Managing Director Niall Rooney’s enthusiastic pronouncements underscore the project’s pivotal role in the company’s strategic growth. Since the August 2024 groundbreaking, the site has witnessed remarkable progress, with two primary warehouses now fully constructed and poised for handover. The expansive yard, crucial for operational efficiency, is already 50% paved, equating to approximately 6,000 square meters of completed surface. Furthermore, the canteens and change rooms are finished, and comprehensive installations of warehouse lighting, electrical systems, and water infrastructure have been successfully completed, all within a compressed six-month timeframe. Rooney commended Kalamain for adhering to the project’s stringent schedule. The headquarters’ design philosophy, centering on “Simplicity and Efficiency,” reflects Rooney’s brand ethos, with every facet of the site meticulously planned to optimize operational efficiency and enhance the client experience.
touches, they are committed to delivering excellence in every project.
The iconic Harare Showgrounds is set to undergo a dramatic transformation following Terrace Several leading construction companies have been roped in to spearhead the project and among them is steel infrastructural experts Brown Engineering Group.
Our piece on 258 Hotel, looks at a hospitality player positioned on the fringes of Harare’s Central Business District, and offering a contemporary retreat that successfully blends modern luxury with rich cultural heritage. An in-
its unassuming elegance, providing a tranquil haven for both business and leisure travellers alike.
In the dynamic arena of modern business, rebranding is a strategic imperative. Soltam, specializing in the manufacture of steel products, is embracing this transformative journey. The firm recently changed its name from Soltam Steel to Soltam, recognizing the need to broaden its market perception beyond steelworks. This strategic move reflects the company’s commitment to diversifying its offerings and capturing a wider market share.
Founded in 2016, Bellington Riggers (Pvt) Ltd is one of the foremost construcexpertise in steel fabrication, electrical engineering and of course, rigging, the tractor of choice in the rapidly advancing construction sector.
Construction of bridges in Zimbabwe is facing a critical juncture, as the realities of climate change and the imperative for sustainability reshape traditional construction practices. The increasing frequency and intensity of extreme weather events necessitate a paradigm shift in how bridges are designed, constructed, and maintained.
In our attempt to support women in construction we feature several women doing wonders in the in the broader building construction space. These are Padsor Scaffolding and Construction, a company at the forefront of providing innovative scaffolding solutions and construction services; MajorCon, a leading civil engineering company specializing in precast concrete products and services and Elegance Ivy Construction and Interior Design, renowned for crafting luxurious, functional, and elegant spaces.
It keeps getting exciting with every paje. Enjoy the read.
follow us at SDMagzim While every effort has been made to ensure the accuracy of its content, neither editor nor publisher can be held responsible for any omissions or errors: or for any misfortune, injury, or damages which may arise there-of.
As we celebrate 14 successful years in business, we reflect with gratitude on the journey that has brought us here.
As we celebrate 14 successful years in business, we reflect with gratitude on the journey that has brought us here.
We wish you and your loved ones a joyful holiday season and look forward to continuing our journey together in the new year
We wish you and your loved ones a joyful holiday season and look forward to continuing our journey together in the new year
PUBLISHER
Caast
Tinashe
DESIGN,
Takudzwa Matienga
Saul Chidakwa
Kudakwashe Gakaka
WEBSITE &
JOURNALISTS
Martin Chemhere Farai Chaka
DISTRIBUTION
Joshua Govati Gift Sepi
PHOTOGRAPHY Fotohaus
CONTRIBUTORS
marketing1@caastmedia.org markerting@structureanddesign.co.zw
FIND US AT 31 Alexander Rd, Highlands, Harare
Text by Martin Chemhere
Images by Caast Media Group
Kalamain’s ambitious project at the Rooneys Headquarters in Hatfield is progressing smoothly, with the construction firm on track to meet its March completion deadline.
The transformation of the site, reflecting significant investment, stands as one of Kalamain’s most substantial commercial undertakings to date.
Following up from a previous report on the structural phase, the site has witnessed remarkable progress. Taurai Chinyemba, Kalamain’s Site Manager, highlighted the advancements made since the initial groundwork. “The last time you were here, we were working on the engineering part of the structures. We were mainly doing foundations, subcolumns, steel structure, framework in general.
So, from there, things have been going on quite well so far,” he explained. The team did a great job working on the drainage, recognizing the potential for chaos without a proper system in place. All drainage is now perfect and it’s among some of the very last work activities they have been doing of late.
With the structural phase largely completed, the focus shifted to the aesthetic aspects of the buildings. “We were on schedule in terms of the structural part of it. What was left was mainly the aesthetic part of the building, which included starting with the brickwork and you move on to wet trades, which are almost complete.
It’s to do with the aesthetics of the building. Sort of like final touches,” Chinyemba noted. During the last week of February, the construction teams concentrated on wet trades, including flooring, concrete, and skimming, across the three main buildings designated for events, administration, and the canteen.
This work has been ongoing since the resumption of construction on January 12th. The two large warehouses, intended for main storage and maintenance, are nearing completion and are slated for handover to the client by the end of February 2025. The remaining tasks involve meticulous finishing touches, such as wall perfection, sanding, and touch-ups on painting.
Most of the work on these warehouses, along with three smaller buildings, has been finalized and is ready for handover. As of now, the project is estimated to be around 85 percent complete.
With March marking the final month of construction, the team is intensifying its efforts, including weekend work, to meet the deadline. The goal is to finalize the major works, including wet trades, within the first two weeks of March, leaving the remaining two weeks for final snags, touch-ups, and external works.The external works are a significant focus for the final phase, encompassing paving, cabins, staff car parks, and other landscaping elements.
The paving is particularly crucial due to the heavy traffic expected on the site, including heavy load trucks. The team has implemented a robust paving solution to ensure durability.
“The paving is special due the site being a heavily trafficable area, using heavy load trucks, and the like. They had to stabilize the road, as seen in the two layers done on the roads around the headquarters,” Chinyemba explained.
The paving process involved a two-layer system, with the top layer stabilized to withstand heavy traffic. Interlocking block pavers, specifically 80-millimeter pavers for enhanced strength, are being used to complete the surface.
These pavers offer both durability and aesthetic appeal, allowing for the integration of greenery and preventing erosion. Heavy-duty industrial capstones, weighing 88 kg each and supplied by PMB, are being used for the external works.
Additional external improvements include the construction of main entrance cow beds and culverts to prevent curving. “We had to extend a bit, Saint Patrick’s Road, because this site has so much traffic coming in and out of the site. We had to actually modify the smooth movement of traffic that’s going either way.
To ensure that there is smooth movement of traffic,” Chinyemba stated. This involved extending entrances and applying asphalt to ensure smooth traffic flow.The project so far has been going on well. If all goes well, all work should be done by the end of March, which is the target.
Harare's Airport Road is rapidly nearing completion, with the company on track to meet its projected timeline. Niall Rooney, Managing Director, expressed immense satisfaction with the progress, highlighting the project's significance for the company's future.
"A lot!!!" Rooney exclaimed when asked about the milestones achieved since the August 2024 groundbreaking. "To date, the two main warehouses are complete and ready for handover. The yard is 50% paved, which is approximately 6000m2 complete. The canteens and change rooms are complete. All the warehouse lighting, electrics, and water have been installed, which is very impressive considering we only broke ground six months ago."
He further confirmed that Kalamain, the construction firm, is maintaining the project's schedule. "Kalamain are right on time, with everything, all target dates have been met, and construction is going smoothly," Rooney stated.
The new headquarters' design is deeply rooted in Rooney's brand identity. "The whole site is focused on two aspects – 'Simplicity and Efficiency,'" Rooney explained. "The design of all the warehouses, sales office, yard, and traffic flow will help improve the efficiency at which we operate, which will result in a better experience for our clients and a better working environment for the Rooney’s team. Rooney’s is all about finding the best way to offer the best in service for our clients, and the new premises will definitely allow us to take our service up a notch."
a central focus of the design process. "The Sales area is a key area for our operation – we have made this area as open as possible to incorporate meeting areas, product displays, reception, and the Special Event Consultants workstations," Rooney detailed. "This area will allow consultants to communicate with each other easily and will allow clients to feel a part of our full experience.
Again, we have focused on simplicity and efficiency, with all main departments like Accounts and Distribution being part of this building. Being close to the sales team for these departments is very important to ensure clear and efficient communication, which will all result in our clients having a world-class experience with Rooney’s."
Sustainability has also been a key consideration. "The whole site has been designed with water capture and solar power integration at a later stage," Rooney revealed. "We hope to be fully off the grid and waterwise within two years of moving in."
The building's infrastructure is designed to accommodate the company's expanding range of services. "We have ensured that space is maximized to its best by using height where we can," Rooney said. "With a shelving system imported from South Africa, we will be able to store vertically. With the use of forklifts and pallets, we will be able to store goods at multi-levels and at greater heights, which will make access to our products and handling of our products more efficient."
The architectural impact of the new headquarters is intended to be significant. "The Sales Office will be the main standout building," Rooney emphasized. "Positioned right on the Airport Road, we want this building to be noticed. We want it to be viewed as almost like a steel sculpture with a unique steel facia. The building will definitely be different from any other structure in Harare. It will be noticed!"
Employee comfort and well-being have also been prioritized. "We have ensured that we have made the most of natural light in all the warehouses with skylights and in the sales office with high vertical floor-to-ceiling glass windows," Rooney explained. "During the day, all areas should be able to operate without any additional lighting. We want our warehouses and sales office to feel open to the outside with fresh air able to flow freely through all the warehouses and sales office."
Operational efficiency is a primary driver behind the new headquarters. "The main goal of this project is to ensure Rooney’s is able to operate at its best efficiency as possible," Rooney stated. "Great thought has gone into all aspects of our operation: loading and off-loading of goods, cleaning and washing, maintenance, storage, fleet flow, customer flow – every aspect has been thought out to ensure we offer our team the best possible working environment."
The location along Airport Road offers significant advantages. "Everyone knows Airport Road, everyone knows their route to the airport – just mentioning to clients that we are located on Airport Road makes the commute to our offices not so intimidating," Rooney said. "The visibility that Airport Road will offer us is a big plus – we will ensure our brand is well represented to all that pass us on their way to or from the Airport."
The investment in the new headquarters reflects Rooney's long-term vision. "Rooney’s is a family-owned and operated company, with the third generation currently running the company," Rooney explained. "The long-term hope is that there will be a fourth and fifth generation who will keep looking after this great brand and great company.
Our goal is to ensure we are here to help create amazing events for future generations of Zimbabweans. Our new location will allow us to make Harare home for many more years to come."
The company is also ensuring a smooth transition for its team. "Over the past month, all staff have been taken on familiarization tours of our new home," Rooney said. "Each department head has been tasked with designing and implementing their new workspace. It’s going to be a very big undertaking to move all our equipment, and we plan to do this in stages so it won’t affect our daily operations."
With its focus on efficiency, sustainability, and customer experience, the new Rooney's Hire Services headquarters is poised to become a landmark in Harare, solidifying the company's position as a leader in the Zimbabwean market.
In the dynamic arena of modern business, rebranding is more than a mere aesthetic change; it's a strategic pivot, a declaration of renewed purpose, and a calculated move to capture market dominance.
One firm, Soltam, specializing in the manufacture of steel products, is embracing this transformative journey. The firm recently changed its name from Soltam Steel to Soltam as its owners felt that they were sending the wrong message. The market associated the name Soltam Steel to work involving steel only.
So, they wanted to correct that confusion since they are more than a steelworks firm. “Our name change was due to the need to accommodate all the products that we manufacture. Also in Zimbabwe, if you mention the word "steel", people think you are talking about metal only. Therefore, we have evolved from Soltam Steel to just Soltam,” said Lot Musara, Managing Director.
Through their manufacturing section, pre-fabricated products as well as clent-specific needs-designed products are manufactured. This involves manfacturing of industrial box gutters, seamless gutters (industrial and home), palisade fencing, window frames, door frames, metal cabinets and burglar screens.
Also manufactured are gate panels, sliding and butterfly gates, garage doors, steel doors, substation or transformer doors, birds laying nests, tobacco curing pipes, plus other customer purpose made products. Soltam has unveiled a fresh vision and mission, while simultaneously demonstrating its capabilities through the successful completion of critical infrastructure—the new Mbare Traders Temporary Market.
This structural landmark has transformed the look and feel of the regeneration-starved greater Mbare Traders Hub, attracting enthusiastic looks from passersby along the Ardbennie Road.
"Rebranding is about seizing the moment," declares Lot Musara, Managing Director. "It's about solidifying our position, showcasing our commitment to innovation, and ultimately, delivering unparalleled value to our customers."
The company's recent work at the Mbare traders market serves as a tangible testament to this commitment. Installing industrial box gutters, seamless gutters, domestic palisade fencing, and substation/ transformer doors, they tackled complex challenges with precision and efficiency.
"We understand the importance of robust infrastructure," states Musara. "The Mbare market project was an opportunity to showcase our expertise and contribute to the development of vital community hub."
Beyond project execution, the company's rebranding is anchored by a revised vision: "To be the premier manufacturer and supplier of high-quality, innovative, and durable steel products in Africa, delivering exceptional value to our customers, while driving economic growth and development in the community."
The ambitious vision is supported by a clear mission: "To design, manufacture, and deliver a comprehensive range of high-quality steel products that meet the evolving needs of our customers, while contributing to the growth and development of Africa's construction and manufacturing industries."
Soltam's commitment to excellence is further solidified by its core values of quality excellence, customer centricity, innovation, sustainability, and teamwork.
From door frames and steel doors to roller shutters, gutters, gate panels, and palisade fencing, the company's product portfolio reflects its versatility and commitment to meeting diverse customer needs.
The rebranding initiative, coupled with its proven track record, positions Soltam as a formidable player in the Zimbabwean steel industry, ready to forge a new legacy of excellence and innovation.
WestProp Holdings Limited is offering a novel approach to dividend payments, giving shareholders the choice between cash and new "10% non-redeemable participating preference shares."
This innovative strategy aims to retain cash within the company to fuel its ambitious development projects, according to property consultant Kura Chihota.
The dividend, amounting to 83.33 US cents per ordinary share, can be received as a cash payment or in the form of these new shares, each with a nominal value of US$5. This decision follows the company's 2023 IPO, which listed 30 million ordinary shares and 6 million preference shares.
The board's decision aligns with the company's constitution and the Companies and Other Businesses Act, empowering them to offer scrip dividends. Shareholders approved this scrip dividend option at the Annual General Meeting held on May 3, 2024. The total value of reserves to be capitalized for this dividend is a substantial USD 25 million.
Shareholders must choose either the cash or the scrip option; partial selection is not available. The dividend payment, whether in cash or shares, is expected around February 28, 2025. Shareholders should be aware that applicable shareholders' tax will be deducted from gross dividends.
Detailed information regarding the scrip dividend offer will be sent to shareholders on February 10, 2025. The company has advised shareholders to ensure their mailing details are up-to-date with Corpserve Registrars.
This strategic move by WestProp allows shareholders to participate further in the company's growth while simultaneously bolstering WestProp's financial capacity for development.
The construction industry demands durable, functional, and safe workwear. From scorching summers to frigid winters, and from dusty job sites to hazardous environments, construction workers need clothing that can withstand the elements and protect them from harm.
High-visibility clothing is crucial for ensuring worker safety. Bright colors and reflective materials make workers easily visible to vehicles and machinery, reducing the risk of accidents. Safety footwear is another essential component, providing protection against punctures, slips, and falling objects. Steel-toed boots are a common choice, offering robust protection for the feet.
Beyond safety, comfort and practicality are key. Loose-fitting clothing can get caught in machinery, posing a serious risk. Comfortable and breathable fabrics help workers stay cool in hot weather and warm in cold conditions. Durable materials like reinforced knees and elbows are essential for withstanding the rigors of the job.
Investing in quality workwear is not just about comfort and safety; it's also a matter of productivity. When workers are comfortable and protected, they can focus on their tasks and work more efficiently.
Ultimately, the right workwear is an investment in the safety, comfort, and productivity of the construction workforce. By providing workers with the appropriate gear, companies can create a safer and more efficient work environment.
The building and construction sector, while vital for development, presents significant respiratory health risks to its workers. Exposure to dust, fumes, and other airborne particles can lead to a range of respiratory illnesses, from asthma and bronchitis to more serious conditions like lung cancer and silicosis. Addressing these risks is crucial for protecting the health and well-being of construction workers.
One of the primary culprits is dust. Activities like cutting concrete, sanding wood, and demolishing structures generate substantial amounts of dust containing hazardous substances like silica, asbestos, and wood dust. These particles, when inhaled, can irritate and damage the respiratory system. Fumes from welding, painting, and using solvents also pose a threat, as they contain volatile organic compounds and other harmful chemicals.
Implementing effective control measures is essential to minimize these risks. Engineering controls, such as using dust suppression systems, local exhaust ventilation, and substituting hazardous materials with safer alternatives, should be prioritized. These measures aim to reduce the generation and spread of airborne contaminants at the source.
Where engineering controls are not sufficient, respiratory protective equipment (RPE) should be provided and used correctly. This includes respirators, masks, and other devices designed to filter out harmful particles and fumes. Proper training on the use and maintenance of RPE is crucial to ensure its effectiveness.
Regular health surveillance of workers is also necessary to detect early signs of respiratory problems. This includes lung function tests, chest X-rays, and other assessments to monitor workers' respiratory health and identify any potential issues. Early detection allows for timely intervention and can prevent the progression of respiratory diseases.
Beyond these measures, promoting a culture of respiratory health awareness within the construction sector is vital. Workers need to be educated about the risks they face and empowered to take proactive steps to protect their health. Employers, meanwhile, have a responsibility to create a safe working environment and enforce safety regulations.
By prioritizing prevention, implementing effective controls, and fostering a culture of health and safety, the building and construction sector can significantly reduce the burden of respiratory diseases and ensure a healthier workforce.
By Martin Chemhere
In a significant stride towards bolstering national infrastructure, the Ministry of Transport and Infrastructural Development recently announced the commencement of site establishment for the highly anticipated Murambinda-Birchenough Road construction project.
This development marks a crucial step in improving connectivity and accessibility within the region, promising to unlock economic potential and enhance the quality of life for local communities. The project underscores the Ministry's ongoing commitment to upgrading Zimbabwe's transport network, adding to a growing portfolio of road construction and infrastructure development projects across the nation.
The Murambinda-Birchenough Road, a vital artery connecting these two key areas, has long been in need of significant improvement. The existing road has presented numerous challenges for travelers and transporters, hindering efficient movement of goods and people. Its current state likely contributes to increased travel times, higher vehicle maintenance costs, and limited access to essential services for communities along the route. The upgrade promises to alleviate these issues, fostering smoother and safer journeys for all.
The commencement of site establishment signifies the initial phase of the project, involving critical preparatory work. This includes setting up construction camps, mobilizing equipment and materials, and conducting necessary surveys and assessments. This foundational stage is crucial for ensuring the smooth execution of the subsequent construction phases, laying the groundwork for a successful and timely project completion. The Ministry's proactive approach to this preparatory phase demonstrates its commitment to efficient project management and minimizing potential delays.
This initiative is not an isolated undertaking. It forms part of a broader national strategy to modernize Zimbabwe's infrastructure. The Ministry of Transport and Infrastructural Development has been actively pursuing multiple road construction projects throughout the country, recognizing the vital role of a well-developed transport network in driving economic growth and social development. These projects are designed to improve connectivity between urban centers and rural areas, facilitate trade and commerce, and enhance access to essential services such as healthcare and education.
The Murambinda-Birchenough Road project is expected to bring a multitude of benefits to the region. Improved road conditions will significantly reduce travel times, making it easier for people to access markets, healthcare facilities, and educational institutions.
This enhanced connectivity will also stimulate economic activity, attracting investment and creating new opportunities for local businesses.
Furthermore, the improved road infrastructure will facilitate the efficient movement of agricultural produce and other goods, boosting trade and contributing to regional economic development.
The project also holds significant social benefits. Improved accessibility will connect previously isolated communities, fostering greater social integration and improving access to essential services. This will contribute to an improved quality of life for residents in the region, promoting social equity and inclusivity.
The Ministry's commitment to infrastructure development demonstrates a clear understanding of the crucial link between transport networks and overall national progress. As the Murambinda-Birchenough Road project progresses, it promises to not only connect two important centers, but also pave the way for a brighter future for the communities it serves.
By Martin Chemhere
Engineering surveyors often express a fondness for their profession, citing the opportunity to work with heavy machinery as a major draw. These machines, often likened to impressive toys, have indeed transformed road construction, making the process more innovative and less laborious, particularly with the advent of the GNSS grader.
Historically, road construction relied heavily on traditional methods like profiles, a process that was not only excruciatingly time-consuming and exhausting but also prone to inaccuracies. The introduction of GNSS graders has revolutionized this aspect of the industry, offering a more engaging and cost-effective approach. These technologically advanced machines utilize Global Navigation Satellite Systems (GNSS) to precisely control the grading process, leading to smoother surfaces and more efficient construction.
Like any technological advancement, GNSS graders have created opportunities for continuous professional development for engineering surveyors.
Operating these sophisticated machines requires a blend of skills, including proficiency in specialized software for surface creation and a strong technical understanding of their management and ongoing operation.
This need for specialized knowledge has elevated the role of the engineering surveyor, demanding a higher level of expertise and creating new career paths.
The limitless potential presented by GNSS graders, in both field and office work, has made engineering surveying an increasingly attractive career choice.
This technological shift has also opened doors for greater inclusivity within the profession.
Women passionate about construction can now excel as engineering surveyors, leveraging their interest in design and software without necessarily needing extensive experience with heavy machinery.
The focus has shifted towards technical skills and data analysis, making it a more accessible field for a diverse range of individuals.
The integration of technology like GNSS graders has not only streamlined road construction but also improved the quality and longevity of roads.
The precision offered by these machines ensures that roads are built to exact specifications, reducing the need for rework and minimizing material waste. This translates to cost savings for construction companies and ultimately benefits the public through better infrastructure.
As technology continues to advance, the field of engineering surveying is poised for further innovation, promising even more efficient and sustainable road construction practices in the future.
By Martin Chemhere
Bridge building in Zimbabwe is facing a critical juncture, as the realities of climate change and the imperative for sustainability reshape traditional construction practices.
The increasing frequency and intensity of extreme weather events, such as floods and droughts, pose significant challenges to the longevity and safety of bridge infrastructure. These environmental shifts necessitate a paradigm shift in how bridges are designed, constructed, and maintained. One of the primary concerns is the increased risk of flooding. Zimbabwe's river systems are experiencing more erratic flow patterns, leading to heightened erosion and scouring around bridge foundations.
In addition to material selection, bridge designs must incorporate climate resilience. This involves considering future climate projections and designing bridges that can withstand anticipated changes in temperature, precipitation, and wind patterns.
This demands the implementation of more robust foundation designs and the use of materials that can withstand prolonged exposure to water and debris. Furthermore, the selection of construction materials is becoming increasingly scrutinized.
There is a growing emphasis on utilising sustainable and locally sourced materials to reduce the carbon footprint of bridge projects. This includes exploring the potential of recycled materials and innovative concrete mixes that minimize environmental impact.
This may necessitate the adoption of new engineering techniques and technologies, such as advanced modeling and simulation tools, to assess the vulnerability of bridge structures to climate change.
The need for sustainable bridge building extends beyond the construction phase. Ongoing maintenance and monitoring are crucial to ensure the long-term performance and safety of bridges in a changing climate. This includes regular inspections to detect early signs of damage and the implementation of proactive maintenance measures to prevent costly repairs and replacements.
Ultimately, bridge building in Zimbabwe must embrace a holistic approach that integrates climate resilience and sustainability into every stage of the project lifecycle. This requires collaboration between government agencies, engineering firms, and local communities to develop and implement innovative solutions that address the unique challenges of the region.
By prioritizing sustainability and climate resilience, Zimbabwe can ensure that its bridge infrastructure remains safe, reliable, and environmentally responsible for generations to come.