
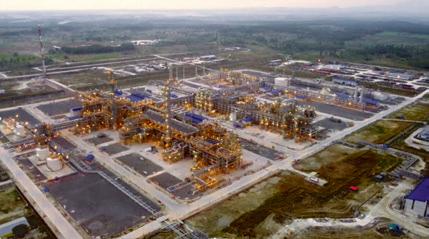

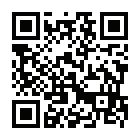
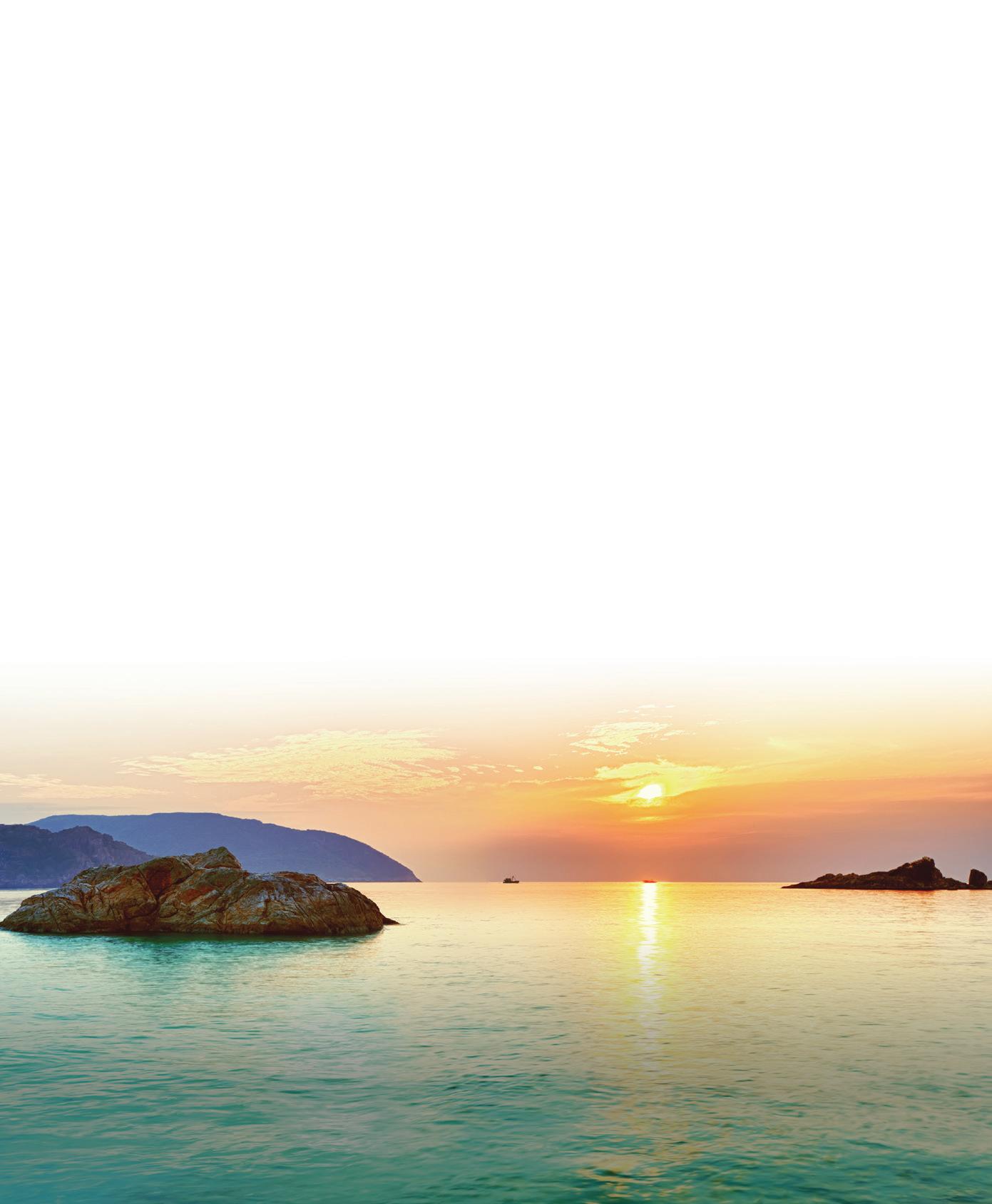
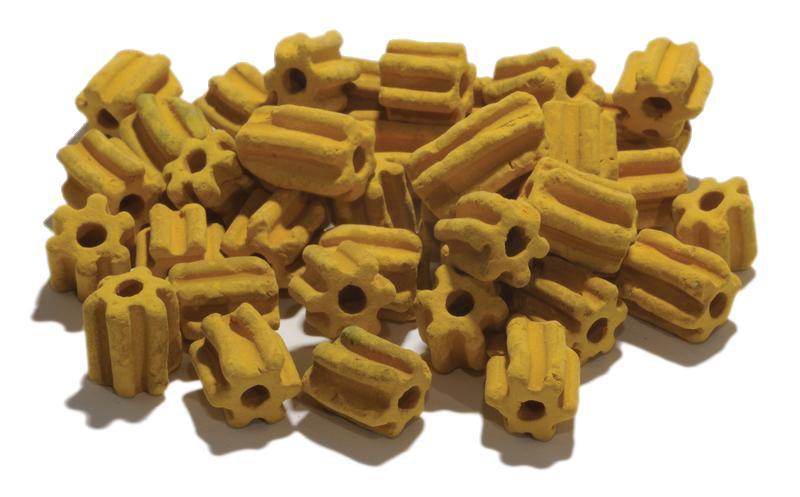
7 In a major advancement in Indonesia’s energy sector, stateowned PT Pertamina EP Cepu (PEPC), a subsidiary of Pertamina Hulu Energi, has successfully integrated a sulfuric acid plant within its acid gas processing facility at the Jambaran-Tiung Biru (JTB) gas field in Java.
Dear Friends,
Welcome to the Spring/Summer 2025 issue of Sulfuric Acid Today magazine. We have dedicated ourselves to covering the latest products and technology for those in the industry, and hope you find this issue both helpful and informative.
In this issue, we have several informative articles regarding state-of-the-art technology and projects. Our cover story focuses on a major advancement in Indonesia’s energy sector, state-owned PT Pertamina EP Cepu (PEPC), a subsidiary of Pertamina Hulu Energi, has successfully integrated a sulfuric acid plant within its acid gas processing facility at the Jambaran-Tiung Biru (JTB) gas field in Java (page 7), Acuity Commodities explains how factors outside of the sulfuric acid market have potential knock-on effects that could change the supply and demand outlook as well as trade flows for sulfuric acid (page 10), Weir shares how pump failures can devastate the bottom line and explains the key to solving chronic pump issues often lies in understanding the specific demands of a facility’s application (page 16), Academia.Holtec has launched its first Basic and Advanced asynchronous online courses tailored specifically to metallurgical sulfuric acid plant operations (page 18), MECS® sulfuric acid catalyst celebrates 100 years of innovation (page 20), NORAM announces a triple offset butterfly valve manufactured using NORAM SX®, a high
silicon, austenitic stainless steel (page 24), Worley Chemetics recently celebrated its 60th anniversary as a technology leader and service provider to the sulfuric acid industry (page 26), Beltran Technologies shares its WESP technology—a key to producing pure sulfuric acid (page 28), INTEREP explains the most common alloys used for metal expansion joints, why they matter, and where they should (and shouldn’t) be used (page 30), Topsoe shares its expertise in designing a good catalyst involves a compromise between achieving good strength, low pressure drop, and high activity (page 32).
I would like to welcome our new and returning Sulfuric Acid Today advertisers and contributors, including: Academia. Holtec, Acid Piping Technology Inc., Acuity Commodities, Alphatherm, BASF, Beltran Technologies, Central Maintenance & Welding, CG Thermal, Chemetics, Christy Catalytics, Clark Solutions, Elessent MECS Technologies, INTEREP, NORAM Engineering & Constructors, Southwest Refractory of Texas, SmartScope, Sulphurnet, Topsoe, VIP International, and Weir.
We are currently compiling information for our Fall/Winter 2025 issue. If you have any suggestions for articles or other information you would like included, please feel free to contact me via email at kathy@h2so4today.com. I look forward to hearing from you.
Sincerely,
Kathy Hayward
MA’AN, Jordan—Prime Minister Jaafar Hassan laid the foundation stone for the second phase of the Sulfuric and Phosphoric Acid plants in the Al-Shidiya area, Al-Jafr District, Ma’an, Jordan. The project, owned by the Phosphate Mines Company, is estimated to cost JOD250 million and is expected to create around 300 direct job opportunities and 500 indirect jobs.
Hassan emphasized the importance of the Phosphate Mines Company implementing training and retraining programs for the local community, including university graduates and vocational training graduates, in line with the project’s various stages. The programs will help locals benefit from the job opportunities the project will generate. He was briefed by Abdul Wahab Ruwad, CEO of the Jordan Phosphate Mines Company, on the project, which has been awarded and is set to be completed over 18 months with an investment value of $250 million..
Ruwad explained that the project’s second phase aims to increase the sulfuric acid plant’s production capacity from 2,200 metric tons daily to 4,450 metric tons (equivalent to 1.5 million metric tons annually). The phase will generate an additional 20 megawatts of energy per hour, with the potential to export 9 megawatts.
The project will boost the production capacity of the phosphoric acid plant from 900 metric tons per day to 1,600 metric tons daily (equivalent to 550,000 metric tons of P 2O5 per year).
Ruwad discussed the company’s parallel work on the phosphate flotation project, valued at $125 million. The project will produce approximately 2 million tons of high-quality floated phosphate annually and is expected to be completed by the end of March. It will provide 250 direct job opportunities and 2,000 indirect jobs, mainly in the shipping sector, with daily transportation of 20,000 tons of phosphate to the factory.
He mentioned the ongoing phosphate washing water treatment project, with a financial cost of $25 million. This project aims to treat the muddy water from washing phosphate ore at the Shidiya mine, producing approximately 7,000 cubic meters of pure water daily for the company’s factories. The construction is expected to be completed, and operations will begin by September of this year.
Ruwad noted that the project would significantly increase phosphate consumption. With the expansion of the industrial complex in Aqaba and future projects involving potash and partnerships in the phosphoric acid industry, the Phosphate Mines Company plans to increase its local consumption to 70%, while reducing external exports by 30%.
The Prime Minister, accompanied by the Ministers of Local Administration and
Energy and Mineral Resources, inspected the work progress at the sulfuric and phosphoric acid plants.
For more information, please visit www.jpmc.com.jo.
MALVERN, Pa.—Ecovyst Inc., a leading integrated and innovative global provider of advanced materials, specialty catalysts, virgin sulfuric acid and sulfuric acid regeneration services, announced today that it has reached an agreement to acquire the sulfuric acid production assets of Cornerstone Chemical Company located in Waggaman, Louisiana. The acquisition is expected to expand Ecoservices’ capacity to serve regeneration and virgin sulfuric acid customers and provide for enhanced flexibility within the company’s existing plant network in the Gulf Coast. Ecovyst plans to fund the acquisition with cash on hand, and the transaction is targeted to close in the second quarter of 2025, subject to customary closing conditions.
“The acquisition of Cornerstone’s sulfuric acid assets represents a unique opportunity for Ecoservices to strengthen its network of facilities and expand its ability to support the future growth needs of our customers, on a cost-efficient basis,” said George L. Vann, President of Ecoservices. “We look forward to serving the Waggaman plant’s existing customers and strategically incorporate the acquired assets to support the future growth needs of Ecoservices’ customers.”
“Given its proximity to our existing Baton Rouge site and alignment with our broader Gulf Coast operations, the acquisition of Cornerstone’s sulfuric acid assets not only complements Ecoservices’ current footprint but is also expected to bolster the resilience of its overall plant network. We are acquiring the assets at a cost below replacement value, aligning with our plan for executing on our high-return organic growth initiatives and targeting strategic bolt-on investments in Ecoservices. Additionally, the assets are being acquired at a transaction multiple basis that is favorable compared to Ecovyst’s current trading multiple, considering the expected pro forma EBITDA postintegration,” said Kurt J. Bitting, Ecovyst’s Chief Executive Officer. “We believe this acquisition is well-aligned with the company’s strategy of prioritizing and pursuing actions that will maximize Ecoservices’ value creation potential for shareholders.”
Ecovyst Inc. and subsidiaries is a leading integrated and innovative global provider of advanced materials, specialty catalysts, virgin sulfuric acid and sulfuric acid regeneration services.
Ecovyst has two uniquely positioned specialty businesses: Ecoservices provides sulfuric acid recycling to the North American refining industry for the production of alkylate and provides high
quality and high strength virgin sulfuric acid for industrial and mining applications. Ecoservices also provides chemical waste handling and treatment services, as well as ex-situ catalyst activation services for the refining and petrochemical industry.
Advanced Materials & Catalysts, through its Advanced Silicas business, provides finished silica catalysts, catalyst supports and functionalized silicas necessary to produce high performing plastics and to enable sustainable chemistry; and through its Zeolyst Joint Venture, innovates and supplies specialty zeolites used in catalysts that support the production of sustainable fuels, remove nitrogen oxides from diesel engine emissions, and that are broadly applied in refining and petrochemical process.
For more information, visit www. ecovyst.com. q
KWINANA, Australia—Australian manufacturer CSBP has shut down its 90,000100,000 t/yr superphosphate (SSP) manufacturing plant in Kwinana, and will switch to an import model going forward.
The company said the plant is going into “care and maintenance,” and the facility will be repurposed to increase CSBP’s storage capacity. CSBP is the fertilizer division of WesCEF, a subsidiary of Western Australia (WA)-based conglomerate Wesfarmers subsidiary.
CSBP said the decision was made because of a “long-term decline in market demand for SSP as growers continue to reduce livestock numbers, combined with increasing competition from overseas suppliers and rising operational and raw material costs, including sulfuric acid.”
Sulfuric acid has become increasingly expensive because of production curtailments in the WA nickel industry, which meant it needs to be imported. A market participant estimated the closure of the SSP plant will result in sulfuric acid imports falling by 50,000-60,000 t/yr.
“Choosing the care and maintenance option gave the business the flexibility to recommence operations in the future, if market conditions change,” said CSBP Fertilisers’ general manager Ryan Lamp. But market participants think a reopening of the plant is highly unlikely, considering much cheaper SSP imports are available, principally from China.
CSBP’s fertilizer sales rose by 31pc to 396,000t in the first half of the July 2024June 2025 financial year compared with a year earlier, according to the company’s half-year presentation.
Australian chemicals and fertilizer producer Incitec Pivot also recently announced it would cease manufacturing SSP at its 350,000-400,000 t/yr plant at Geelong by the end of this year.
This will leave Ameropa’s 150,000200,000t/yr facility in Hobart, Tasmania as the last operational SSP plant across the Oceania region. Market participants think the closure of CSBP’s and IPL’s plants will spell trouble for Ameropa’s plant, which likely makes SSP swaps with IPL from time to time.
For more information, please visit www. csbp.com.au.
Life still left in Mount Isa copper smelter, Glencore confirms
QUEENSLAND—Glencore says it is working with the Crisafulli government to extend the life of the Mount Isa Mines copper smelter in Queensland.
Chief executive officer Gary Nagle gave the clearest indication yet that the smelter could continue beyond the current 2030 scheduled closure. Speaking to national media last week, Mr. Nagle said the LNP government was offering its assistance to keep the smelter operating.
“They (LNP government) are aware of these challenges and are looking for ways to assist us in ensuring we can keep that smelter running longer term and hopefully be able to invest in a re-brick if the operating and cost conditions are right,” he said.
As a lynchpin piece of infrastructure for the North West resource sector, the future of the MIM smelter is considered a pivotal issue to the region’s future that was also identified as a threat to future project rollout under Mount Isa City Council’s economic diversification plans released last week.
The smelter currently treats more than one million tonnes per annum of copper concentrate, which includes accepting ongoing contracts from surrounding operations in the region.
Looming projects, such as the proposed Harmony Gold Eva Copper project at Cloncurry is also expected to use the smelter and could offer significant new throughput once its mine is operational.
Any potential closure of the smelter would cause significant disruptions to the supply of sulfuric acid at a time when demand for the smelter by-product is also expected to surge as a host of new projects, which are reliant on the acid, are scheduled
to become operational across the North West over the coming decade.
With more than half of the state’s total supply off acid coming from Mount Isa Mines, there is expected to be significant international competition for the acid as countries boost both food production and critical mineral extraction.
Speaking at a media briefing in Mount Isa last week, Glencore officials warned that overseas competitors were already receiving significant financial assistance from governments to maintain smelting operations amid falling treatment charges and declining profit margins.
There has also been a spate of new smelters under construction in countries such as China, India, Indonesia and parts of Africa as nations attempt to provide security over their domestic copper demand.
For more information, please visit www. glencore.com.
TAMPA, Florida—Tampa-based fertilizer company Mosaic, the world’s fourth-largest potash producer, agreed earlier this year to sell a phosphate mine and tailings dams in Brazil to local company Fosfatados Centro for $125 million in cash.
The deal for the Patos de Minas site located in the country’s Minas Gerais state aligns with Mosaic’s strategy to review and monetize non-core assets while reallocating capital to higher-return investments, the company said.
“This agreement represents an important step for the phosphate supply to the Brazilian fertilizer market and demonstrates our commitment to advancing the National Fertilizer Plan,” Rodolfo Galvani Júnior, owner of Fosfatados Centro, said in the statement.
Mosaic’s move comes as global potash prices have started to fall and supply levels return to those seen before Russia’s invasion of Ukraine. Top producers Russia and Belarus have circumvented Western sanctions by increasing shipments to Asia and South America, contributing to the market’s recovery.
The company’s South American operations include 26 potash and phosphate facilities across Brazil, Paraguay, and Peru. They comprise production and blending facilities, offices, and infrastructure.
Its São Paulo-based subsidiary, Mosaic Fertilizantes, manages regional commercial and production facilities, as well as port and storage units. The company operates 11 blending facilities, eight toll units, one port terminal, and has a blending capacity of 8.6 million tonnes annually.
For more information, please visit www. mosaicco.com. q
Strike the balance between regulatory, economic and environmental requirements when dealing with sulfurous off-gasses. Whether you’re managing sulfurous emissions from a new facility or an existing plant, our solution allows you to keep your operation compliant and running smoothly.
Visit topsoe.com to learn more.
By: April Smith, Editor
In a major advancement in Indonesia’s energy sector, state-owned PT Pertamina EP Cepu (PEPC), a subsidiary of Pertamina Hulu Energi, has successfully integrated a sulfuric acid plant within its acid gas processing facility at the JambaranTiung Biru (JTB) gas field in Java. The multi-component facility, completed amid the challenges of the COVID-19 pandemic, uses the latest technologies from Worley Chemetics and Shell to improve operational efficiency and environmental sustainability. The facility converts hydrogen sulfide extracted from raw natural gas into marketable sulfuric acid, aligning with PEPC’s goal of maximizing resource utilization while minimizing environmental impact.
Founded by Pertamina in 2005, PEPC got its start in oil production, operating the
Cepu Block, a region encompassing the central and eastern Java province. In 2007, the company started building early production facilities and two years later began producing 20 million barrels of oil per day.
In 2011, PEPC was appointed operator of the JTB gas field and in 2013 began designing a gas processing facility with a design capacity of 330 MMSCFD.
Following the official transfer of JTB management to PEPC in 2017, the company signed an engineering, procurement, and construction contract with PT Rekayasa Industri (Rekind) and PT JGC Indonesia for further development of the gas field. In 2019, PEPC secured $1.8 billion in funding from a banking consortium to advance the project. Today, JTB consists of an onshore gas field with up to three production wells and a downstream gas facility that processes natural gas before its distribution into Indonesia’s energy grid.
PEPC’s new acid gas processing facility consists of a series of components that remove SO2 from upstream flue gas. The components include the acid gas incinerator (licensed by Zeeco®), the regenerative Cansolv® scrubber (licensed by Shell), and
Shell acted as the overall licensor for the acid gas unit supplying its Cansolv® SO2 scrubbing system, which captures byproduct value from the SO2 emitted from flue gas streams and achieves SO2 emis-
sions of 200 ppm or less. The Cansolv® system is particularly suited for treating flue gas streams with relatively high (up to 5 vol%) SO2 concentrations.
cation.” said Herbert Lee, Senior Business Development Manager, Worley Chemetics.
“The technology is a good fit for JTB, as PEPC needs to remove sulfur species from the natural gas and the salable sulfuric acid product provides a positive payback for PEPC. The CORE™ technology requires significantly reduced dilution of the incoming gas as it can operate at high SO2 concentrations. This makes the plant significantly more compact compared to conventional sulfuric acid technologies,” Lee said.
Cansolv® is a regenerative process, using a proprietary amine technology to capture and release a pure stream of SO2 Because the SO2 is released as a product gas stream, the process generates a fraction of the waste created by alternative alkaline scrubbing processes and consumes virtually no reagent. High-cost, consumable, absorbents are also not required and effluents are reduced to a minimum.
Worley Chemetics, headquartered in Vancouver, Canada, supplied the first of its kind CORE-FGD™ sulfuric acid plant to convert high-concentration SO2 into saleable sulfuric acid. The facility produces commercial grade 98.5% H2SO4
“The sulfuric plant receives concentrated feed gas (about 94% SO2, 6% water) from the upstream acid gas incinerator and Cansolv® regenerative SO2 scrubbing system. After adding ambient air to supply the required oxygen for the reaction, the CORE™ reactor processes an SO2 gas concentration of 18.7 vol % for JTB’s appli-
Worley Chemetics’ services spanned two contracts. The first supplied the process design package and the CORE™ reactor system, including internals and catalyst. The second contract provided detail design, procurement, and the balance of the CORE™ system materials, along with technical advisory services for construction and commissioning as well as operator training.
The plant is designed for turndown to 20%, but has operated as low as 15%, Lee explained. Energy is recovered to produce LP steam (50 psig / 3.5 barg) for use in the gas processing facility. The plant is fitted with an electric preheater, so there are no direct CO2 emissions from the acid plant during preheating. This preheater also allows the plant to remain in hot stand-by mode
indefinitely if the need arises. To reduce water consumption, the plant incorporates an air-cooled closed loop cooling water system (including the product cooler) instead of the more traditional evaporative cooling.
The CORE-FGD™ reactor and all the SARAMET® equipment was fabricated at the Worley Chemetics shop in Pickering, Ontario, which was recently expanded by 60% to further enhance its ability to deliver sulfuric acid equipment. The compact plant design allowed all equipment to be delivered to the JTB site fully fabricated.
PT Enviromate Technology International (ETI) provided wrap-around detailed design services for the sulfuric acid plant, including civil and electrical design, structural steel fabrication and supply of utility piping, ducting, manual valves, and insulation. PT Rekayasa Industri (Rekind) was responsible for executing the EPC contract for the entire project. This included detailed design and supply of the remaining portions of the acid gas unit (incinerator, Cansolv, utilities), site construction, and coordination between PEPC and various technology providers to bring the project to fruition.
“The project took place during the Covid-19 pandemic, causing obstacles,” ETI’s Alex Yang said. “And there was the time difference between Indonesia and the manufacturer that we had to manage,” he added. “However, with good coordination carried out during the project, we were able to complete the work on time.”
Worley Chemetics worked closely with PEPC, Rekind, ETI and all the vendors and suppliers to adjust delivery schedules around work-from-home restrictions and other health measures. COVID safety protocols were implemented to allow site support while international travel was still restricted. This allowed the project to
continue construction and commissioning prior to the end of the pandemic and reach production in Summer 2022.
Despite the obstacles, the project was completed with no safety incidents and the sulfuric acid plant has been producing high quality sulfuric acid since 2022. The acid is supplied to a nearby copper leaching facility, further supporting the local Indonesian economy.
Regarding future CORE™ implementations, a CORE-SO2™ sulfuric acid plant is in the works for a facility in Australia. “This will be the fourth CORE™ reactor worldwide and the first CORE-SO2™ sulfuric acid plant to be built,” Lee explained. “This project is currently awaiting final investment decision (FID) after basic engineering was completed in late 2023. FID is expected in Q2 this year.” q
By: Fiona Boyd and Freda Gordon, Directors of Acuity Commodities
Factors outside of the sulfuric acid market itself have potential knock-on effects that could change the supply and demand outlook as well as trade flows for what is widely described as the most-used chemical globally. Developments such as tight base metal concentrate supply and U.S. tariffs are contributing to uncertainty overhanging the sulfuric acid market while also highlighting regional differences that could intensify in the years to come.
First, with respect to tariffs, at the time of writing, 25% tariffs on imports to the U.S. from Canada and Mexico were expected. Given the fast-moving developments under the new U.S. administration, it is hard to say if this will be the case when this issue of Sulfuric Acid Today is published. Nevertheless, any U.S.-imposed tariffs on sulfuric acid from these two countries would be notable, as the U.S. is a deficit market relying on imports to help cover demand from the merchant acid market. Canada is a critical supplier of sulfuric acid to the U.S. due to a concentration of base metals smelters in the eastern region as well as one in British Columbia. These smelters supply the U.S. with around 1.8 million t/yr of acid, largely by rail. Meanwhile, Mexico supplied around 800,000t to the U.S. in 2024, also largely by rail. The supply from Canada accounted for around 50% of the U.S. import total and Mexico around 20% of the annual import total for last year. The balance is supplied from offshore countries in the Asia and European regions. Options for sulfuric acid exports from both Canada and Mexico are limited, further highlighting the dependency on trade between the countries to help balance the respective markets.
Most of the acid traded in the global market is produced as a by-product from base metals smelting, resulting in inelasticity on the supply side. The current tightness in base metal concentrates, namely copper and zinc, is constraining smelter run rates in some cases, impacting acid output accordingly. When concentrate availability is tight, smelters reduce treatment charges (TC) and refining charges (RC) to attract feedstock. While historically TCs and RCs have been revenue sources for smelters, they are expected to stay low throughout 2025, limiting revenue. As a result, smelters are under more pressure to make up revenue in other ways, such as through sulfuric acid sales, which is evident in China. As an indication, Acuity’s China spot export price assessment was in the range of $10-20/t freight-on-board (FOB) in January 2024 compared with $48-55/t FOB in January 2025. The impact of constrained output due to a lack of concentrates and other supply issues also provides acid price support.
ance for this year, citing the tight zinc concentrate market as a primary factor. This, of course, will impact by-product acid output accordingly, further increasing the need for acid supply to help balance the U.S. market.
Shifting to Asia, while plenty of newly developed base metal smelting capacity is not being used due to the tight concentrate situation, some short-term relief could be seen. This is because Indonesia’s trade ministry has signaled support for extending PT Freeport Indonesia’s copper concentrate export permit until 2025, pending a cost-benefit analysis and alignment with the country’s downstream policy. This comes as Freeport was due to commission its new Gresik smelter, with those efforts thwarted by an October 2024 fire, requiring it to export concentrates until the new smelter commences operations, expected around mid year. At the same time, the start up of new smelting capacity in India is expected, also within a few months. But once again, when this new smelting capacity starts, acid output could be limited by concentrate availability.
On the demand side in Asia, Indonesia’s appetite for acid to support nickel leach operations has increased, resulting in both sulfur imports increasing to feed newly developed burners as well as incremental sulfuric acid. As a reflection, Indonesia’s sulfuric acid imports were reported as around 300,000t during the first 11 months of 2022 before increasing to around 1.1 million t in the comparable time period in 2023 and 2024.
The development of nickel capacity in Indonesia has had other consequences for the sulfuric acid market, namely impacting operations in Australia. BHP announced in July 2024 it was suspending its Nickel West operations beginning October 2024 and intends to review the decision by February 2027. The decision was driven by nickel oversupply in the global market, particularly with increasing capacity in Indonesia. The suspension includes the Kalgoorlie nickel smelter, with some of the acid used by BHP internally with the balance sold to the local market and occasional exports out of Kwinana. With the smelter no longer running as a result of nickel market conditions, there are now higher import needs in Australia to cover local consumption. We should also note that BHP had been considering expanding smelting capacity in the coming years given its West Musgrave project that includes mining of copper and nickel sulfide ore. That project is now suspended alongside the Nickel West operations. West of Suez, regionality is being seen in part due to a loss of sulfur supply due to refinery closures and crude slate changes. In Europe, a key exporter of smelterproduced sulfuric acid to countries such as Morocco and the United States, a reduction in molten sulfur supply there is creating increased demand for incremental sulfuric
Boyd, Acuity Commodities
Acuity Commodities
acid. We noted in our last article in the Fall 2024 issue of Sulfuric Acid Today that it remained to be seen if demand from sulfur-based acid producers seeking incremental smelter acid supply was sustainable, which it has since proven to be.
The increased regional demand is also as smelters there face operational challenges, in part due to prevailing concentrate market conditions described above. As such, availability of smelter acid has been impacted and we have seen more demand for sulfur-based acid for export, which is often opportunistic based on price. As an indication, Acuity’s northwest Europe spot export price in January 2024 was in the range of $40-50/t FOB compared with $100-110/t FOB in January 2025.
While sulfur production is also declining in the United States, we have yet to see a notable impact on the merchant sulfuric acid market. This is in part due to loss of demand from the pulp and paper sector because of several mill closures while emerging demand for new applications tied to the electric vehicle (EV) evolution is awaited. At the same time, the southeast United States saw an uplift in capacity with the restart of a burner in Georgia as discussed in our last article of Sulfuric Acid Today. Market conditions have not changed much thus far in 2025 as the evident slowdown in the upstream EV sector continues to delay downstream demand.
Looking forward in North America, there remains much focus on the western North American region as demand to support various mining applications is pursued. While several of these projects include plans for sulfurbased acid plants on site, consumption for others is not large enough to warrant such an investment, putting more dependency on the merchant sulfuric acid market accordingly.
The future landscape of the domestic North American market continues to hinge on if and when these projects proceed and the corresponding impact they will have on needed raw materials, including sulfur and sulfuric acid.
Globally both today and looking forward, it is clear smelter acid supply trends will impact availability for consumers of sulfuric acid. It remains to be seen how emerging new smelter capacity in India and Indonesia and the battle for concentrates could shift the top export countries. For demand, metals will become increasingly important as they are critical for needs in many countries including Australia, Chile, Indonesia, and the United States. Meanwhile, to support mainly fertilizer production, demand from import countries such as Brazil, Morocco, and Saudi Arabia should remain stable amid ongoing efforts to feed the growing population.
Acuity Commodities provides insight into the sulfur and sulfuric acid markets through price assessments, data, and supporting analysis. Offerings include weekly reports on the global sulfur and sulfuric acid markets. For North America, we offer a bi-weekly report on sulfur and sulfuric acid as well as a monthly report on industrial chemicals, including caustic soda and hydrochloric. We also have developed a database detailing battery and mining projects under development in North America that could consume products such as sulfuric acid. In addition, Acuity does bespoke consulting work. Please visit www. acuitycommodities.com for detailed information. q
In recent years, advancement in artificial intelligence (AI) technology has developed at an exceptional rate. The current state of AI is already showing promising results, even though it is still in the early stages of widespread integration. It is beginning to transform industries, driving unprecedented efficiency, innovation, and sustainability. In the chemical industry, AI is being used to revolutionize everything from process optimization and predictive maintenance to hazard prevention and reduction of environmental impacts. By embracing AI’s ability to analyze vast amounts of data in real time, chemical manufacturers have been improving performance, enhancing safety, and creating more personalized and cost-effective products. AI is shaping the future and has a myriad of opportunities to offer the chemical industry.
In the chemical industry today,
By: Nicolas “Cooper” Richards, GSP, International Safety Coordinator, VIP
AI is primarily being used to optimize existing processes, improve predictive maintenance, and enhance supply chain efficiency. Machine learning algorithms analyze vast amounts of data from sensors, production logs, and historical performance to predict equipment failure. This allows companies to intervene in a timely manner while reducing downtime and maintenance costs, and enhancing safety. AI is also playing a role in process control, where real-time data helps adjust parameters to maximize yield, minimize waste, and ensure consistent product quality.
Machine learning and real-time monitoring through AI have proven to be vital tools for improving efficiency and minimizing process downtime. Machine learning algorithms can analyze massive amounts of information and data from sensors embedded in manufacturing equipment. These sensors receive
data like temperature, pressure, and flow rate while machine learning algorithms can predict potential issues before they can escalate. Monitoring complex chemical processes using AI provides opera-
chemical manufacturing marks a big step, offering opportunities for improved process efficiency and safety of workers. “ ”
The integration of
tion, more accurate risk assessment, and proactive interventions enhance safety of plant personnel, contract workers, and the surrounding environment by reducing the likelihood of accidents and improving overall reliability. AI does not replace the human element of safety, but embracing this technology and utilizing its advantages can help improve the overall health and safety of workers.
tors with actionable insights that can prevent malfunctions. Embracing this technology allows companies to implement proactive maintenance strategies, shifting from reactive to predictive ones. Reactive strategies, like responding to equipment failure, can be costly and disruptive. However, anticipating equipment issues ahead of time using a proactive approach with AI allows chemical manufacturers to achieve higher uptime.
With these new technological advancements, AI is also revolutionizing safety and hazard prevention in the industry. With real-time monitoring, predictive analytics, and autonomous response systems, AI can help mitigate hazards before they escalate. Using machine learning algorithms and sensors, potential hazards like leaks, pressure buildups, or temperature fluctuations can be detected earlier and mitigated appropriately. Predicting these equipment failures or malfunctions will equip operators to take preventative actions long before incidents occur. Additionally, AI-powered technologies like computer vision can monitor plant equipment and infrastructure for signs of wear, corrosion, etc., identifying safety risks that might go unnoticed. This can help detect areas that need attention, making manual audits more efficient and effective. AI can also be used to enhance the communication of safety information and see that the information is efficiently disseminated, allowing for quicker response times to potential hazards and emergencies. Faster detec-
As AI becomes more deeply integrated into industries, ethical considerations and regulations will be essential. One primary concern is accountability and transparency. It is crucial for companies to maintain clear and understandable processes on how AI models make decisions, especially in high-risk/ high stake scenarios like safety and process optimization. Transparency can help prevent biases in decision making and ensure that AI systems are operated as intended. Data privacy and cybersecurity are also significant concerns, since AI systems require vast data accessibility of sensitive operational and personal data. Protecting data from breaches and ensuring compliance with privacy laws are essential. AI’s increasing integration raises questions about the impact on an individual’s job safety and income inequality. While AI can improve efficiency and innovation, it also has the potential to displace workers. Policy makers need to craft fair and inclusive policies that address the support of displaced workers while balancing AI’s economic benefits with social equity. The responsible integration of AI in any industry hinges on creating framework that promotes innovation but also ensures fairness and privacy.
The integration of AI into chemical manufacturing marks a big step, offering opportunities for improved process efficiency and safety of workers. From optimizing processes, predictive maintenance, enhancing safety protocols, and developing sustainability, AI is transforming how the chemical industry operates and competes in a dynamic market. The ethical and regulatory responsibilities must be carefully managed to ensure transparency, accountability, and fairness. By addressing these challenges and leveraging the responsibility of AI, the chemical industry can unlock its full potential and contribute to a safer, more sustainable future.
For more information, please visit www.vipinc.com. q
By: Douglas Azwell, Technical Manager, and Katie Gallucci, Process Engineer, MECS® Brink® Mist Eliminators, Elessent Clean Technologies
Proper tower performance is crucial to the efficiency and reliability of a sulfuric acid plant. Well-designed absorption towers maximize uptime, enhance production, reduce emissions, and lower maintenance costs. Conversely, poor tower design can lead to increased emissions, operational inefficiencies, and costly repairs.
Mist eliminators play a vital role in capturing acid mist from the gas stream before it exits absorption towers. However, the effectiveness of the mist eliminators depends not just on their raw mist-collecting capability but also on their ability to prevent reentrainment—the process in which previously collected mist is regenerated into particles at the exit of the mist eliminator and carried back into the gas stream. This phenomenon can lead to higher stack emissions for final absorption tower operations and potential damage to downstream equipment in the case of intraprocess locations.
One of the key factors influencing mist eliminator performance is the design of the drainage media. Some mist eliminators lack drainage media altogether, making them more susceptible to re-entrainment. Both the configuration and type of drainage layer play
ULSAN, South Korea—POSCO Group’s plans for domestic production of nickel, a key raw material for secondary batteries, have been shelved, leading to observations that Korea Zinc’s role in establishing a domestic secondary battery raw material supply chain will be greater. POSCO and Korea Zinc had both embarked on establishing nickel plants with production capacities ranging from 40,000 to 50,000 tons annually, but with POSCO abandoning its construction plans, only Korea Zinc remains.
Korea Zinc will have the second largest nickel sulfate production base in the world, following China, once its all-in-one nickel refinery, which began construction in November
critical roles in preventing re-entrainment by providing clear pathways for liquid drainage, thereby reducing the formation of liquid films that can burst and regenerate mist particles.
Performance variations can be illustrated with efficiency curves (see Fig. 1). The efficiency of a fiber bed with either an ineffective drainage layer, or no drainage layer, will drop off at large particle sizes. Emissions associated with a fiber bed that either has no drainage layer or an ineffective one as shown in Fig. 1 will have a higher mass mean particle size. These are tell-tale signs of acid mist reentrainment.
The fundamental function of a welldesigned mist eliminator is two-fold:
1. Capture mist: The fiber bed collects fine mist particles from the gas stream.
2. Drain collected liquid: The drainage media provides open pathways for the liquid to flow downward, preventing the formation of liquid films that can burst and regenerate mist particles.
By providing clear drainage pathways, a
2023, is completed. In a situation where dependence on Chinese key raw materials for batteries is high, Korea Zinc’s nickel refinery is expected to play a significant role in the country’s goal of self-reliance in the secondary battery supply chain.
According to the business community on the 14th, POSCO Holdings is in the process of liquidating its nickel production joint venture (POSCO CNGR Nickel Solutions) established in partnership with China’s largest precursor company, CNGR Advanced Material. POSCO Holdings had set up the joint venture last year as part of its efforts to establish a supply chain for secondary battery raw materials and materials. The plant being built in the Pohang Yeongilman 4 Industrial Complex was planned to produce up to 50,000 tons of high-purity nickel annually. Although a groundbreaking ceremony was held in May of last year, the decision was made to pull out about nine months later. This is observed as a move to readjust investments due to the prolonged slowdown in secondary battery demand resulting from
properly designed drainage layer minimizes re-entrainment, leading to lower emissions and improved tower performance.
Controlled lab tests have demonstrated that the effectiveness of a drainage layer is influenced by several factors, including fiber diameter, density, permeability, and orientation. Results show that different drainage layer designs can produce vastly different outcomes.
• Optimal design matters: Some drainage layers significantly reduce re-entrainment, improving overall efficiency.
• Poor designs can be worse than no drainage layer: Surprisingly, some drainage layers perform so poorly that they allow more re-entrainment than having no drainage layer at all.
Fig. 4 shows laboratory test results for different drainage layer options. As shown in the diagram, Drainage Layer A (blue line) is a good choice for minimizing re-entrainment because its overall efficiency (as shown on the Y axis) is higher than many other designs, particularly for larger particle sizes (as shown on the X axis); this is indicative
the contraction of the electric vehicle market.
Korea Zinc is currently constructing an all-in-one nickel refinery at the Onsan Industrial Complex in Ulsan through its nickel sulfate production subsidiary, Chemco. The facility can produce 42,600 tons of nickel sulfate annually. Nickel sulfate is an inorganic compound created by dissolving nickel in sulfuric acid and evaporating it, mainly used as a raw material for precursors needed for ternary battery cathodes.
The difference with the all-in-one nickel refinery compared to conventional nickel refineries is that it can produce nickel sulfate from various types of nickel-containing raw materials (intermediates) such as nickel matte, mixed hydroxide precipitate (MHP), black mass (processed waste batteries), and concentrate all within one facility. Foreign nickel refineries usually process only one type of raw material to produce nickel.
Korea Zinc plans to invest approximately 500 billion won in the construction of its allin-one nickel refinery. It aims to begin commercial production by the end of next year.
of low re-entrainment. By contrast, Drainage Layer C (green line) would be a poor choice for minimizing re-entrainment, as its overall efficiency for larger particle sizes is worse than using no drainage layer at all (red line).
MECS® Brink® mist eliminators incorporate advanced bicomponent drainage technology using effective materials specifically designed for fiber bed operation both in sulfuric acid and a variety of other processes. The bicomponent design has been widely demonstrated in the industry for over four decades to minimize re-entrainment, resulting in lower exit mist emissions and improved overall process efficiency.
By investing in superior mist eliminator technology, sulfuric acid plants can optimize tower performance, reduce maintenance costs, and ensure regulatory compliance while maintaining high production standards.
For more information, please contact Doug Azwell (douglas.azwell@elessentct. com) or Katie Gallucci (katie.gallucci@elessentct.com) of Elessent Clean Technologies or visit www.ElessentCT.com. q
Choi Yoon-beom, chairman of Korea Zinc, visited the construction site at the end of last month to check on the progress.
Chemco currently has a production capacity of about 90,000 tons of nickel sulfate. After the completion of the all-in-one nickel refinery, combining Chemco’s current production capacity will give Korea Zinc more than 130,000 tons of nickel sulfate production capacity, making it one of the largest in the world, excluding China.
Korea Zinc is expected to receive a tax credit for 15% of its investment in the all-inone nickel refinery. This is because the government is promoting a plan that designates nickel sulfate, cobalt sulfate, manganese sulfate, and lithium hydroxide production technologies as national strategic technologies and provides a 15% tax credit on the related facility investment. The government envisions fostering a domestic supply chain ecosystem to reduce dependence on overseas sources for secondary battery raw materials and materials.
For more information, please visit www. koreazinc.co.kr. q
MONDI™ Pipe and fittings
- MONDI™
- Teflon Lined Piping
- Pipe Hangers
- Bolts
- Gaskets
Tower & Converter Internals
- MONDI™ Distribution Systems
- MEEHANITE Converter Internals
- Ceramic Packing Saddles
- Ceramic Packing Support
- Quartz Rock
Flow Control
- Engineered Dampers & Valves for S02/S03 Applications
- PTFE/PFA Lined Valves
- 316SS, Alloy 20, 310SS Valves
- MONDI™ Thermowells
- PTFE Spargers
- Orifice Plates
- Pressure & Temperature Gauges
Pump failures devastate the bottom line. At one leading phosphate facility, each day of downtime costs $2 million in lost revenue. This plant is in Morocco, which controls over 70% of global phosphate reserves. Operators learned expensive lessons about running pumps in corrosive environments. Their experience shows how to boost reliability and minimize downtime across similar operations.
“The situation had become unsustainable,” recalls the site’s maintenance supervisor. The facility’s existing axial flow pumps, which move large volumes of phosphoric acid at low head conditions, failed an average of every nine months. Each failure meant not just the cost of new parts but 72 hours of maintenance time and, most critically, lost production.
The stakes were exceptionally high at this facility. As a long-term partner since the early 1980s, Weir’s team understood the site’s operations and challenges. This relationship proved crucial in developing an effective solution for the plant’s flash cooler application, where maintaining precise temperature control directly impacts product quality and plant efficiency.
For plant operators reading this, these symptoms might sound familiar:
• Frequent impeller replacements drained maintenance budgets.
• Persistent casing leaks required constant monitoring.
• Vibration issues never fully resolved.
• A constant juggling act between production demands and necessary maintenance.
The key to solving chronic pump issues often lies in understanding the specific demands of your application. In this case, several factors were at play:
1. The combination of high flow rates with a very low head (approximately 1m) created challenging hydraulic conditions.
2. Corrosive phosphoric acid media demanded specialized materials.
3. The continuous operation left little margin for the maintenance windows.
4. The existing pump’s materials and design weren’t optimized for the service.
Engineered for performance
Standard pump designs couldn’t meet these extreme demands. The solution centered on the LEWIS® 36 LHV vertical axial flow pump—purpose-built for corrosive, high-flow, low-head applications.
Competing pumps failed within two years despite lower upfront costs. LEWIS® pumps deliver 8-10 years of reliable service in the same conditions. The difference lies in
superior engineering and metallurgy:
• Vertical mounting ensures fast maintenance access.
• Heavy-duty shaft eliminates vibration.
• 24/7 local support backs this advanced technology.
That latter point is a critical one. On-site parts and technical experts ensure immediate response to any operational need; rigorous manufacturing controls—from casting to final assembly—guarantee consistent performance in these punishing conditions.
The proof of any solution lies in the numbers. In this case, the data proves immense value:
• Impeller life improved by 300%, extending from 9 months to 36 months.
• Maintenance hours per replacement cut from 72 to 12.
• Total cost of ownership reduced by 83%. The maintenance team reports:
• Zero casing leaks since installation.
• Complete elimination of vibration issues.
• Significantly reduced monitoring requirements.
• More predictable maintenance scheduling.
Technological advances in pump design and materials science are actively reshaping our industry. However, success in phosphoric acid processing ultimately depends on how effectively these innovations are implemented within a sophisticated operational strategy.
Performance monitoring and analysis
Rigorous performance tracking catches minor problems before they become expensive failures. Basic measurements like flow rates and pressures tell only part of the story. True performance insights come from watching how equipment responds to changing environmental conditions, day-to-day operational shifts, and variations in acid chemistry and concentration.
Smart monitoring helps maintenance teams predict issues and time repairs perfectly. Top facilities track both equipment and process data systematically, spotting warning signs early and scheduling maintenance before failures occur.
Downtime is one financial consideration. When equipment reliability directly impacts production capability, the actual cost equation must also consider multiple factors of total operational impact. The assessment of total operational impact includes:
• Direct maintenance costs, including labor and materials.
• Production impact of scheduled and unscheduled maintenance.
• Energy cost implications of equipment selection.
• Impact on connected processes and overall system reliability.
• Long-term reliability and performance consistency.
Choosing the right materials determines pump success or failure in corrosive services. Poor material selection triggers endless maintenance cycles, while optimal choices deliver stable, reliable operation.
Choosing the right materials determines pump success or failure in corrosive services. Poor material selection triggers endless maintenance cycles, while optimal choices deliver stable, reliable operation.
Flash cooler service illustrates this. High flow rates combine with corrosive media to
By: Anour El Amrani and Vinay Veluri, Weir
create brutal pumping conditions. Precise temperature control demands unwavering pump performance—and material compromises made to cut initial costs lead directly to accelerated wear, constant maintenance, and production stops.
LEWMET® alloys redefine performance in aggressive applications. These specialized nickel-chrome materials thrive in the industry’s most demanding services, from sulfuric and phosphoric acids to molten salt at up to 240°C.
Premium materials cost more upfront but reduce maintenance costs and boost reliability in the long term. This proves especially valuable where access challenges make repairs difficult or equipment failures halt production.
Maintenance teams face a clear challenge: keep production running while maintaining equipment and controlling costs. Premium pump technology transforms this equation by doubling or tripling time between services.
Strategic pump placement and smart design features allow operators to anticipate and plan for repair time. Every installation detail, from access points to maintenance clearances, impacts repair speed and uptime.
Acid pumping demands precise control while battling corrosion and erosion. The lessons from phosphoric acid service—where LEWIS® pumps extended impeller life by 300%—apply directly to sulfuric acid operations, where pump reliability determines plant success.
Decades of field experience in sulfuric acid applications prove that success comes from integrating advanced materials, precision engineering, and proactive maintenance. LEWIS® pumps command a considerable share of the global sulfuric acid market for good reason—they deliver 12-15 years of reliable service while competing units fail within two to three years.
Chemical processors face ever-tougher demands for reliability and output. Success in modern acid service comes from the fundamentals: advanced materials that resist corrosion, precision engineering that anticipates real-world conditions, and systematic monitoring that prevents failures. Cutting corners or up-front costs in critical acid service almost always costs more in the long run. As the industry pushes into new territory with higher temperatures and more aggressive chemistries, following proven material science and engineering principles is even more critical to operational success.
For more information, visit www.global. weir/brands/lewis. q
Effective operator education is crucial for environmental sustainability, asset management, and personnel safety in sulfuric acid plant operations. Continuous learning strengthens job security, career growth, and overall plant performance.
However, metallurgical sulfuric acid plants face severe challenges in planning education, adapting to shift work, replacing retiring experts, evolving workforce expectations, and integrating digital technologies. To address these challenges, online asynchronous technical-professional education methods offer a flexible and efficient solution, allowing operators to access high-quality learning materials at their convenience and allowing them to progress at their own pace.
Drawing on 25 years of expertise in sulfuric acid plant technologies and operations, and 20 years of experience in technical-professional learning, Academia. Holtec has launched its first Basic and
By:
Advanced asynchronous online courses tailored specifically to metallurgical sulfuric acid plant operations. Currently, they are available in English and Spanish.
For new operators, the courses provide a structured introduction to sulfuric acid plant operations. For experienced operators and junior engineers, they bridge knowledge gaps, standardize skills, reinforce safety procedures, and reduce operational errors—enhancing efficiency and safety.
The Basic Course covers chemistry, physics, adiabatic cooling, water balance, equilibrium curves, and catalysts, applying these concepts to key plant equipment. The Advanced Course explores process control, materials and corrosion, plant control systems, and troubleshooting. By integrating disciplines, operators better understand plant functions, recognize inefficiencies and unsafe conditions, and optimize performance.
Jukka Tähkä, Manager, Sulfuric Acid Plants at Boliden Harjavalta, highlights the impact of structured education:
“Acid plant training is a good package, and this increases operators understanding of the different stages of acid production. As operators understanding improves, it also affects general personal safety at the acid plant.”
CUSTOM TOWER DESIGNS TO MATCH YOUR PLANT NEEDS
• Achieves performance requirements in all plant operating modes
• Customized SARAMET® metallurgy is selected for each application (Dry, Inter, Final, ALPHA™ or Oleum Towers)
• Proprietary gas inlet nozzle designs engineered to eliminate localized corrosion
• Designed for retrofit or new tower installations
• Allows use of existing or new tower foundations minimizing installation time
• Scope of supply ranges from detailed engineering and manufacturing drawings with material supply, to complete EPC
• Full tower life cycle support is available from Worley Chemetics, including technical and inspection services
LEARN MORE chemetics.info@worley.com chemetics.equipment@worley.com
WORLEY.COM/CHEMETICS
As the sulfuric acid industry evolves, investing in employee development and prioritizing human talent as a strategic asset is crucial for ensuring long-term sustainability and operational excellence.
For more information, please contact Dirk van der Werff at dirk.vdwerff@holtec.cl or visit www.academia.holtec.cl. q
From our strategic location in Houston, TX, we are able to supply a variety of brick shapes (straights, arches, wedges, keys) and sizes from stock for immediate purchase.
Please reach out to us for technical data and pricing. Samples available upon request.
Meeting ASTM C279 standards for use in new construction and refurbishment of existing structures in sulphuric acid plants including towers, process vessels, floors, sumps, pits, etc.
Industrial Linings for Sulphuric Acid Plants. Absorption Towers, Pump Tanks, Sulphur Pits, Secondary Containment, Acid Resistant Linings.
Acid Brick, Acid Resistant Mortar, Membranes, Carbon Brick, Polymer Concrete, Refractories, Teflon, Ceramic Paper and Blanket, Ceramic Rope, Borosilicate Block
A-103 Mastic® is Still Available and in Stock in warehouses in USA and Canada. Madefromtheoriginalrecipe.
When your plant has a product that has proven successful for over forty years, why change? With this in mind, Alphatherm Inc. purchased the recipe of Pecora A-103 Mastic® to keep this integral piece of the Sulphuric Acid Tower lining system intact. Made from the same ingredients with A DECADES OLD RECIPE, A-103 continues to be the workhorse membrane in Acid Plants worldwide.
This is THE ONLY A-103 Mastic ® made with the original Pecora recipe.
A-103 MASTIC is a registered trademark of Alphatherm Inc.
By: Helen M. Cardwell and Timothy R. Felthouse, Elessent Clean Technologies
Over the past century, the number of sulfuric acid plants operating globally has expanded exponentially. Throughout the 20th century, rapid industrial growth in combination with increasing demand for superphosphate fertilizers led to high demand for the “king of chemicals,” sulfuric acid. Today, sulfuric acid is one of the most utilized commodity chemicals in the world with widespread applications in the phosphate fertilizer, non-ferrous metals, chemicals, and oil refining industries. In the early 1900s, the contact process for sulfuric acid production was improved greatly with the development of vanadium-based sulfuric acid catalysts. Previous sulfuric acid manufacturing using lead chamber units or contact processes utilizing platinum catalysts was expensive, unreliable, and produced lower strength acids.
To support its first sulfuric acid plant built in 1917, MECS, Inc. (MECS), then Monsanto, quickly advanced research and development on contact sulfuric acid processes, including the use of vanadiumbased catalysts. The research and production facilities for the vanadium-based catalyst were established at the Commercial Acid Company site, then designated as Monsanto Plant “B.” In 1925, Plant B produced what was known as the “Monsanto Mass” catalyst, which eventually led
to the “Type 210A” (T-210A) commercial product. Fig. 1 shows an example of an indoor acid plant constructed in 1930 by Leonard Construction Co. at the then newly acquired Monsanto Chemical Company plant site in Everett, Mass. The converters at this plant site contained the original T210A catalyst. Fig. 2 provides an example, ten years later, of a larger outside contact sulfuric acid plant.
Over the next two decades, MECS and Leonard Construction Co. designed, constructed, and provided operations for more than 250 sulfuric acid plants in 30 countries creating a global business with customers for catalyst and acid plant equipment and services. During this time, acid plant sizes grew, and converter designs started to employ a single vessel with ducts connecting the incoming SO2-containing gas stream and heat exchangers as separate unit operations.
The following decades were marked by rapid growth for MECS. By 1945, MECS had designed 40% of the world’s contact sulfuric acid capacity. By the late 1960s, the Plant B site was producing over 1MM liters of catalyst per year. In contrast, today
there are plants operating with over 1MM liters in a single converter. This growth in demand led to the eventual move of the Illinois MECS® catalyst production facilities to the Avon site in Martinez, Calif., which started up in 1970. Today, MECS has more than 1,000 sulfuric acid plant licenses and projects worldwide.
In addition to growth in demand for catalysts, the science and technology behind the catalyst also grew substantially in the years following the construction of Monsanto’s first sulfuric acid plant. The active catalyst formulation was recognized to be in molten salt that melted at reaction temperatures. The key elements comprise
alkali metals, vanadium, and sulfate anions in both sulfate and pyrosulfate states. These alkali-vanadium-sulfate molten salts (now often referred to as ionic liquids) were found to function as catalysts for sulfur dioxide oxidation in both bulk and supported forms. The active phase was on predominantly silica-based supports. Supported catalysts soon evolved from pellet to larger ring-shaped catalysts that adapted to the needs of converter designs having higher gas flow rates and sulfuric acid production capacities.
R&D into more energy-efficient catalysts increased starting in the 1970s. In that decade, the energy crisis drove the need
for lower pressure drop style catalysts that led to the MECS® “low pressure” drop LP smooth ring style catalyst products. Unlike the traditional pellet-style catalysts, LP catalysts drastically reduced the pressure drop buildup across the old low-velocity converters. LP catalysts were formulated to minimize screening losses and when combined with higher activity, LP catalysts met the needs of acid plant customers in the early 1980s.
“The MECS® catalysts we use have proven outstanding with their long lifespan and low screening loss. These characteristics ensure efficient and reliable performance in our operations.”
- Mr. Chen Ziling, Production Director, Two Lions
Over the next decade, MECS continued to optimize the shape of catalysts to minimize energy costs and extend production cycles. A computer-aided ribbed ring
catalyst shape was designed in the late 1990s through variations on the outside and inside (die pin) diameter, rib thickness, and rib depth. The resulting “XLP” shape produced a catalyst with significantly better reactor performance than the LP catalysts with higher activity, improved extrudate hardness, and lower pressure drop enabling operation at high gas velocities used in larger acid plants. In the early 2000s, the XLP product line was officially introduced, including MECS® XLP-110, which is now the industry standard with installations in over 450 plants globally.
The development of GEAR® shaped catalysts required a longer development path with parallel field and laboratory testing activities. A prototype of the GR-330 catalyst called “Bigfoot” was produced and installed in the first pass of a sulfurburning acid plant. The 13-mm Bigfoot catalyst exhibited very good activity over a 27-month testing period with measured pressure drop rising from the fresh value of 4 inches of water column to 12 inches of water column at the end of the test. The results demonstrated that Bigfoot extended operating time by 40% or 8 months more than a typical ribbed ring catalyst. During the field-testing period, laboratory tests compared the hexa-lobed shape to ribbed ring aluminum shapes. Equal volumes of the hexa-lobed and XLP shapes having the same outer diameter were settled in a pressure drop tube, and the pressure drop was measured and fit to the Ergun equation. The combined field and lab testing results led to the emergence of the GEAR® hexalobed design as a premium shape. These results justified the commercialization of the GR-330 catalyst, and after a slight formulation enhancement, sales of the new GEAR®
catalyst shape began in early 2012.
As shown in Fig. 3, GEAR® catalysts demonstrate a marked improvement over ribbed ring catalysts in the ability to let dust filter through the bed. Dust buildup on the top of a catalyst bed leads to a more rapid increase in pressure drop over time, but the specially designed structure of the GEAR® lobes encourages dust to move deeper into the catalyst bed thus slowing pressure drop buildup.
Alongside the push for more energyefficient catalysts, increasing regulations on clean air, double absorption plant designs, and SO2 emissions have driven improvements in conversion performance and operational flexibility. Sulfuric acid plants today require ultralow emissions and the ability to start up quickly. Beginning in the 1980s, MECS began developing cesiumpromoted catalysts for improved low-temperature performance. Cesium forms alka-
li-vanadium sulfate salt mixtures that lower the molten salt melting point below 400°C. Cesium-promoted catalysts such as XCs120 enable sulfuric acid plants to heat converters faster during startup saving critical downtime and reducing the emissions over the dynamic startup period. With lower temperature performance, cesium-promoted catalysts also provide the opportunity for increased conversion in individual beds before reaching the equilibrium conversion limit.
In 1989, MECS introduced its first cesium-promoted product: Cs-110. The catalyst had excellent SO2 conversion for its time, allowing for acid plant designs with dramatically reduced emissions. As new shapes were developed in later years, improved cesium products XCs-120 and eventually GR-Cs were brought to market. As shown in Fig. 4, using reduced inlet temperatures, cesium-promoted catalysts afford higher conversion performance that continues in the following catalyst beds and ultimately leads to lower SO2 emissions. For acid plants seeking ultra-low
emissions, MECS introduced the “super cesium” product SCX-2000 during its namesake year. SCX-2000 was specifically formulated for the final pass of a sulfuric acid plant converter operating with low SO2 inlet gas concentrations. Under these conditions, highly active catalysts are required to achieve significant conversion of SO2 to SO3. Additionally, because of the low gas strength, catalysts capable of low temperature performance are needed. These benefits are displayed in Fig. 5. By reducing the inlet temperature into the final bed from 425°C to 390°C and upgrading to SCX-2000, this customer was able to
Since its introduction in 2019, XLP310 has been installed in over 30 plants worldwide and data has been collected confirming its performance capabilities. Using MECS® PeGASyS™ (Portable Gas Analysis System) testing, highly accurate metrics can be collected around the acid plant converters. PeGASyS™ testing incorporates a gas chromatograph diagnostic system and proprietary simulation software to sample, analyze, and optimize converter performance.
Case 1: A study of two existing sulfur burning plants
the installation of XLP-310 in two beds of the converters.
Case 2: A new 4x1 metallurgical plant
reduce emissions by 35%.
Development of SCX-2000 enabled MECS to offer impressive designs for ultra-low emissions performance. However, with the limited availability of cesium raw materials, the market price of cesium started to rise significantly over the next several years. To provide another option for acid plants, particularly for those with less stringent emissions requirements, MECS began work on a series of high-performance catalysts that did not need the high-cost cesium promoter.
Along with the development of GR330, MECS also produced the GR-310 catalyst. This 12mm diameter option was designed for intermediate passes of the converter to provide continued low pressure drop across the operations, as well as boosting the overall conversion performance. The GR-310 catalyst proprietary formulation took advantage of optimized potassium levels to boost the volume-based activity of the catalyst.
In 2019, MECS went further with the announcement of two new product offerings: XLP-310 and Super GEAR® catalysts. The development of these catalysts demonstrated a significant advance in conversion capabilities with sulfuric acid catalysts. The proprietary formulations provide the most active non-cesium conversion performance in the MECS® catalyst product line.
Initial field trials of XLP-310 included a 4-year study in a sulfur burning plant as shown in Table 1. PeGASyS™ testing was used to monitor the conversion across each bed over each year of the study. In combination with GR-330 in Pass 1, the use of XLP-310 catalyst enabled this acid plant to achieve 99.8% conversion without the use of cesiumpromoted catalysts. In a similar application years later, another client upgraded their converter to improve reliability and reduce energy costs. PeGASyS™ testing was used to evaluate the performance before and after the installation of the new converter and upgraded catalyst. The emissions results were confirmed to drop significantly with the installation of XLP-310 catalyst as seen in Table 2. When testing 1 year later, the acid plant was operating at 18% higher capacity with less than 10% additional volume of catalyst. As shown in Tables 1 and 2, both sulfur burning plants reduced emissions by more than half with
XLP-310 is a valuable tool for reducing emissions in an existing plant, as well as minimizing the capital costs for new acid plants. In a recent startup of a 5-pass metallurgical sulfuric acid plant, the plant achieved emissions of less than 120 ppm while using XLP-310 in Pass 3 as shown in Fig. 6. The emissions resulted in 99.9% overall conversion which was achieved without the use of cesium in the final beds. Due to the high SO2 inlet, a cesium cap was used in the first bed to prevent the outlet temperature from exceeding the converter’s recommended temperature limits. The performance of the new plant was confirmed through PeGASyS™ testing in addition to standard stack monitoring.
pass. The boost in this difficult application led to the potential for significant reductions in loading to achieve similar performance. Expanded testing also revealed that the XLP-310 catalyst shows improvements even at sub-optimal temperatures in Pass 3. Typically, for Pass 3 operations without cesium, it is recommended to stay above 430°C inlet to ensure a good “light off” (activation) of the catalyst bed. However, even at temperatures as low as 420-425°C inlet, XLP-310 provides significant enough performance for good operation without the need for a cesium promoter. The comparative performance of XLP-310 and a standard ribbed ring catalyst in Pass 3 at 425°C is shown in Fig. 7.
What began 100 years ago as a vanadium catalyst formulation trial to qualify its use in Monsanto sulfuric acid plants quickly grew to a worldwide catalyst and sulfuric acid plant business. As sulfuric acid plant designs and capacities increased, the catalyst adapted through more energy-efficient shapes and higher performance formulations. With over a century of development, MECS has built a varied product line to address specific acid plant requirements:
• Low-pressure drop GEAR® catalysts to minimize operating costs
• Cesium-promoted catalysts for faster startups and ultra-low emissions
• High-performance catalysts for expanded capacity and high conversion
Customized catalyst design and support are key to meeting the ever-increasing needs of acid plants to improve output, reduce costs, and operate sustainably.
Case 3: Low temperature third bed conversion in a pilot plant
In addition to PeGASyS™ testing in the field, MECS uses an in-house pilot plant to assess catalysts across a variety of conditions. Testing showed that XLP310 demonstrated superior performance in a high SO3 environment typical of a 3rd
The sulfuric acid catalyst product portfolio from MECS, Inc. is built on a century of research and development. The newest line of products is designed to reduce emissions, minimize pressure drop, and provide operational flexibility across the acid plant production cycle.
For more information, please visit elessentct.com/technologies/mecs/. q
By: R Sarrazin, W Vorster, NORAM
Acid plant operators will be familiar with the large variety of valve types in a typical acid plant ranging from small sampling valves to large gas dampers and everything in between. Many different types of valves are commonly used in acid plants such as plug, ball, gate, check, and butterfly. This article focuses on the typical valves used in the strong acid circulation loop and present a novel solution.
Valve selection depends on several factors, including, but not limited to, its function (control or isolation), the fluid type (liquid, gas, presence of suspended solids etc.), as well as fluid properties (corrosiveness, etc.).
Typically, in an acid circulation loop, i.e. between the pump tank and tower inlet, one would find some large diameter butterfly valves used to: control the temperature of the return acid, modulate flow, and control acid strength and levels between pump tanks.
“So what?” you ask. A butterfly valve is a butterfly valve is a butterfly valve. Well, to borrow a metaphor from George Orwell’s Animal Farm: “All valves are created equal, but some are more equal than others.”
Allow us to introduce you to a valve that could be characterized as the “more equal” valve: a triple offset butterfly valve manufactured using NORAM SX®, a high silicon, austenitic stainless
steel specifically suitable for service in strong acid circuits in sulfuric acid plants.
Many plants are moving away from conventional materials of construction (brick lined, carbon steel vessels and ductile, cast-iron piping) in the strong acid loops, opting instead for high-silicon steel vessels and piping. This leads to the question of whether there are options available to produce high silicon stainless steel valves to suit the rest of the piping system. As it turns out, yes there is a solution!
NORAM has partnered with Somas, a leading, world-class valve design and manufacturing company in Sweden, to develop and fabricate triple offset butterfly valves in NORAM SX® for service in the sulfuric acid industry. The first SX valve was installed in 2014 and NORAM has
The triple offset valve adds another dimension where the disc seating surface is cone-shaped providing superior performance, especially in terms of leakage and shut-off capability and is more suited to demanding applications such as hot, sulfuric acid.
”
been working with various clients around the world to replace their “old” conventional butterfly valves (either bare metal or lined) with NORAM’s SX valves.
To understand one of the key differentiators between a NORAM SX® butterfly valve and other offerings in the marketplace, an understanding of typical butterfly valve configurations is required. Butterfly valves are
characterized by the “offset” of the shaft relative to the pipe and valve body centers, as demonstrated in Fig. 1.
The concentric butterfly valve is common and low cost, but has disadvantages in that some parts of the disc may contact the valve body, increasing friction. Eccentric designs such as the single, double, and triple offset valves overcomes this. In
a single offset valve, the shaft/ stem is on the center line of the pipe but behind the disc, whereas in a double offset valve, the shaft/ stem is offset from both the pipe and valve disc center lines, which decreases wear and improves the longevity of the valve.
The triple offset valve adds another dimension where the disc seating surface is cone-shaped providing superior performance, especially in terms of leakage and shut-off capability and is more suited to demanding applications such as hot, sulfuric acid.
NORAM’s SX butterfly valves have an advanced triple eccentric design with a unique disc shape, as demonstrated in Fig. 2.
The design is ideally suited for control and shutoff applications in sulfuric acid plants and has a standard tightness class
in accordance with EN 605344 Class V or ASME B16-104 Class V.
In addition, NORAM’s SX butterfly valves offer:
• Superb corrosion resistance as all wetted parts, except for the seat, are high silicon, NORAM SX®. The solid seat is made of glass filled, PTFE, suitable for concentrated acid service and proven at temperatures up to 250°C / 480 °F; and is fully replaceable (if required).
• The seat remains unaffected by high flow velocities and temperatures. The front retaining ring can be removed to replace the valve seat on inspection cycles.
• The valve bodies and all associated parts such as the butterfly disc, shaft, and stuffing box housing are robust, fabricated to Somas’ quality program and rigorously tested prior to shipping.
• The valve stem packing is specifically designed to prevent sulfuric acid from flowing up the valve shaft and leaking out or creating sulfate, which can cause the valve shaft to seize resulting in damage to the shaft and valve body.
• Any brand of actuators or hand operator can be fitted to the valves.
• Valve seat and stem packing replacement kits are available for all valves.
Apart from the materials of construction suitable for the harsh operating conditions in acid plants and the sealing capability, lead time for critical valves is a key consideration for operating plants. Lead times of 30 weeks or longer for replacement acid valves is not unheard of in the industry. To address this, NORAM has committed to stocking 3” to 20” valves in the United States as well as in Canada. (Larger valves are available but subject to special order.)
NORAM partnered with a well-established company, Control Southern, to distribute and stock NORAM SX® valves. Control Southern is an industrial automation and process solution company based in Suwanee, GA, with valve repair shops in Chattanooga TN, Decatur AL, Macon GA, Jacksonville FL, and Lakeland FL. Control Southern stocks multiple quantities of NORAM SX valves up to 20
inches in size. Their expertise in valve automation provides for customized NORAM SX valve solutions to meet any customer need.
In addition, NORAM is working with Somas to stock unmachined parts for common valve sizes to enable valve assembly times of fewer than 4 to 6 weeks and delivery of complete valves, start to finish, within 10 to 14 weeks.
Some may ask what this arrangement looks like in practice? How do these valves perform? Let’s look at some case studies.
A sulfuric acid producer in the southern United States experienced routine failures of their standard 20” butterfly valves installed in a hot acid circulation loop. The valves required replacement and/ or repair every 9 to 12 months due to acid leaking through the shaft packing and subsequent shaft seizure from sulfate build-up in the shaft packing. This resulted in unnecessary downtime to remove and replace the valves as well as the expense of re-building or replacing the valve.
The producer requested a valve that would last a minimum of three years to match their turnaround schedule and eliminating interim shutdowns. They installed a 20” NORAM SX® valve with its uniquely designed shaft packing and EN 60534-4 class V shutoff in October 2020 during a standard plant maintenance turnaround.
This valve operated flawlessly for three years in continuous hot acid service (up to 250°C / 480°F) after which the valve was removed for inspection during a standard turnaround in 2023. The valve was inspected at the Control Southern repair facility in Lakeland where it was bench tested, stroked fully open and closed without any issues. The valve shaft packing and seat were replaced, and the valve was put back into service. As of February 2025, the valve is still operating without any reported issues.
This plant went from replacing its valve every 9 to 12 months to operating 50 months (and counting) without any issues.
A sulfuric acid producer in the Southern United States had a
standard 6” butterfly valve which required replacement every 1 to 2 months. These failures were believed to be caused by excessive vibration in the piping system where the valve was installed resulting in a failure of its internals.
Control Southern supplied a new NORAM SX® 6” valve to this location in March 2024.
Since installation, the valve is being closely monitored for performance and as of February 2025 (11 months and counting), there have been no reported issues.
This plant went from replacing its valve every 1 to 2 months to operating 11 months (and counting) without any concerns!
A sulfuric acid producer in the western United States was planning a major plant turnaround in May 2024. Just before the turnaround, in February 2024, it became apparent they needed to replace a 20” valve, with actuator, in their strong acid circulation system. The typical lead time for a replacement valve would exceed their shutdown planning.
They knew about NORAM’s approach to stocking valves and
asked if a new valve and actuator could be provided in time.
NORAM and Control Southern had the valve in stock; the longest delivery item was the new actuator. The assembled valve and actuator were delivered to the client’s site on April 11th 2024, just six weeks after receipt of the purchase order. The installed 20” valve is shown in Fig. 4. During their May 2024 turnaround, it appeared they also needed emergency replacements of two other valves: 10” and 16” acid circulating valves. These valves were available in NORAM’s stock and could have been delivered to the site within a week (without actuator). Although the existing valves ended up not being replaced, the end user was very happy that NORAM could have shipped them immediately, providing a critical option within the shutdown schedule.
Contact NORAM if you have an emergency and require a replacement valve. Along with a range of butterfly valves, NORAM also supplies pipe and fittings in NORAM SX with components fabricated in the USA. For more information, visit www. sulfur.noram-eng.com. q
Worley Chemetics recently celebrated its 60th anniversary as a technology leader and service provider to the sulfuric acid industry. Since its inception, Worley Chemetics has strived to develop and patent new processes, equipment, and materials to make sulfuric acid production safer, more efficient, and environmentally more sustainable. Today its innovative equipment designs can be found in acid plants all over the world. The 2020s have already proven to be a decade of rapid technology development and growth.
With successful startup in 2022, Worley Chemetics’ first CORE-FGD™ acid plant was implemented in Indonesia at the PT Pertamina EP Cepu Jambaran-Tiung Biru site. CORE-FGD™ (Cooled Oxidation Reactor—Flue Gas Desulfurization) utilizes regenerative scrubbing to remove dilute SO2 from flue gas and produce a concentrated (~90% SO2) gas that is sent to the CORE™ acid plant for conversion to sulfuric acid.
technology by designing and supplying equipment for two of the largest sulfur burning acid plants in the world at the OCP Jorf Lasfar site in Morocco. Both plants commenced production in 2024. In the same year, OCP awarded an additional three plants of the same capacity for installation at their M’Zinda Phosphate Hub.
a third fabrication bay to meet the growing demand for specialized process equipment.
Worley Chemetics continues to design and fabricate the world’s best anodically protected and SARAMET® acid coolers in Pickering. The company has fabricated over 3,000 acid coolers since 1970 and today, the Worley Chemetics acid cooler is still the gold standard.
Further advancement of the CORE™ technology has resulted in the commercialization of the CORE-SO2™ process offering significant reductions in: plant footprint, CAPEX (through reduced equipment size and installation costs), and SO2 emissions (through sulfur combustion and SO2 oxidation using high-purity oxygen). In 2023, Worley Chemetics was awarded a contract by Arafura Rare Earths Ltd. for a CORE-SO2™ sulfuric acid plant for the Nolans NdPr project in Australia.
In addition to CORE™, Worley Chemetics continues to advance the conventional double contact double absorption (DCDA)
The company’s fabrication facility in Pickering, Canada designs and fabricates custom process equipment for the sulfuric acid, chemical, oil and gas, refining, petrochemical, nuclear, nitric acid, ammonia, urea, and fertilizer industries worldwide. In 2024, the Pickering shop was expanded to include
Worley Chemetics’ fabrication knowhow not only allows it to build proprietary and non-proprietary equipment in-house, but that capability extends across the globe allowing it to out-source and manage other fabrication shops. By leveraging geographical proximity to the customer, costs are minimized, schedules are accelerated, and the highest quality equipment is supplied to the customer.
In the 1980s, the company’s technical team developed and patented the high silicon stainless steel SARAMET® (Sulfuric Acid Resistant Alloy Metal) enhancing the construction of equipment and piping in hot sulfuric acid service. SARAMET® 23 was commercialized and brought to the industry in 1982. Since then, new metallurgies have been formulated to address the precise operating ranges of sulfuric acid applications: SARAMET® 25 (1990), SARAMET® 35 (1998) and SARAMET® HT (2018). Most recently, SARAMET® HT+ was developed in 2020 for service in strong acid at elevated temperatures.
Worley Chemetics is headquartered in Vancouver, Canada and employs over 300 personnel across the globe. Together with the Pickering fabrication shop, projects are delivered ranging from concept studies to full project execution involving detailed engineering, procurement, and fabrication. Performance guarantees are provided to customers looking to safeguard the production, reliability, and environmental sustainability of their investment.
Worley Chemetics offers site advisory services to ensure equipment is installed, commissioned, and started up correctly. Following successful completion of projects, Worley Chemetics can also provide technical services for ongoing operational support and/or inspections during major shutdowns and maintenance work.
As a world leader in sulfuric acid technology, Worley Chemetics continues to innovate and service applications in sulfur-burning, spent acid concentration/regeneration, and metallurgical off-gas treatment to meet the most stringent environmental and performance requirements for its customers. For more information, please visit www.worley.com. q
Looking for EBIT improvements without sacrificing SO2 emissions?
BASF’s Quattro catalysts can take you there!
Increase your plant capacity by up to 10% without the need to install additional catalyst volume!
BASF’s Quattro catalysts are designed to increase your EBIT!
30% Increased geometrical surface area
50% Increased knife edge hardness
60% lower attrition
No pressure drop increase
When compared to leading Star Ring catalysts
Leave your competition in the past by stepping into the future of Sulfuric Acid catalysts!
Purified sulfuric acid is still the number one chemical worldwide for phosphate fertilizer manufacturing; mineral processing; petroleum refining; wastewater processing; the manufacture of paints, dyes, detergents, lead and lithium batteries, explosives; and the synthesis of other chemicals, as in the alkylation of gasoline additives.
For industries that generate sulfur oxides and sulfuric acid, including metallurgical and mining operations, petroleum refineries, natural gas processing facilities, electric generating units, spent acid regeneration plants, and municipal waste incinerators, the answer is downstream sulfuric acid manufacturing plants. Operators of these facilities can take advantage of the high industrial market value of purified sulfuric acid.
An efficient sulfuric acid manufacturing process requires strict removal of contaminants from the input gas streams, especially fine and submicron particulates and acid mists such as those emitted from metal ore roasters and smelters, petroleum refineries and coal-fired industrial boilers. This is necessary for protecting downstream components such as catalyst beds from corrosion, fouling, and plugging, as well as for preventing the formation of a “black” or contaminated acid end-product. Proper gas cleaning also results in lower maintenance and operating costs for the manufacturing plants.
To reduce contaminants before entering the sulfuric acid plant, plant engineers have relied on several gas cleaning techniques, such as cyclones, scrubbers, and mist eliminators. These systems can control large particulates, but are usually inefficient at capturing fine and submicron particulates, submicron acid mists, and condensed organic compounds. For those reasons plant engineers and consulting engineering firms continue to specify advanced wet electrostatic precipitators (WESPs), which can clean complex gaseous emissions of particulates and acid mists down to submicron scale (PM 2.5) with up to 99.9% efficiency.
Beltran Wet Electrostatic Precipitators (WESPs) are an advanced technology designed around a multistage system of ionizing rods with star-shaped discharge points. These are encased within square or hexagonal tubes that are lined with grounded collection surfaces. Beltran WESPs are engineered using advanced materials of construction that utilize the advantages of collector tubes, such as the hexagonal and square tube.
The most efficient design when considering collection efficiency, compactness, and cost is the square tube collector configuration. The square tube collector utilizes the entire cross-section of a square or rectangular vessel and can also be effectively used in round and hexagonal vessels. Due to the
square tube’s high utilization of the vessel cross-section, it can be operated at a lower velocity, which reduces the required tube length, thus making the unit more efficient and easier to wash, since the wash sprays penetrate the collector. The high voltage frame is also more rigid, does not swing, and stays more accurately aligned, resulting in more efficient and reliable performance. Because of the shorter tube length, lower stabilizing insulators are not required, and the insulators can be mounted on the clean gas side of the WESP, reducing the requirement for heated purge air and resulting in more reliable WESP operation.
The unique electrode geometry generates a corona field 4-5 times stronger than that of conventional wet or dry electrostatic precipitators, propelling even submicron-size particulates and sulfuric acid droplets toward the collection surfaces, where they adhere as cleaned gas is passed through. The surfaces are intermittently cleansed of residues by recirculating water sprays.
The cool, saturated environment in the WESP makes the system highly effective on condensable or oily compounds, while the continuous aqueous flushing process prevents re-entrainment of particles, sticky residue build-ups, and unfavorable particle resistivity. By eliminating the need for mechanical or acoustical rappers common to dry ESPs, the wet cleansing process also minimizes energy and maintenance costs.
With virtually no physical or mechanical obstruction of gas streams, there is very little pressure drop through the WESP and gas velocities can be extremely high. This enables plant engineers to use smaller-scale, less costly equipment for specific gas volumes and still achieve superior collection efficiencies. The use of smaller, simpler equipment also means lower maintenance and energy.
Beltran WESP systems are built with sophisticated electronic controls linked to a close-coupled gas flow management system. These can optimize operating parameters such as gas velocity, saturation, temperature, and corona intensity, to achieve maximum efficiency. Also, to prevent premature deterioration, critical surfaces should be constructed with advanced protective materials such as fiber-reinforced plastics (FRP) or high nickelchromium alloys. The high-voltage insulators should be continuously purge-air cleaned to further reduce maintenance costs.
Mopani Copper Mines Plc, a unit of Switzerland-based Glencore Xstrata, operates sulfuric acid production facilities at their copper smelter plants in Mufulira and Kitwe in Zambia. The plants currently have 10
By: Gary Siegel, Marketing Director, Beltran Technologies, Inc
WESPs designed and engineered by Beltran Technologies for sulfuric acid gas cleaning. The Mopani smelter and refinery plants utilize both pyrometallurgical and solvent extraction/electrowinning (SX-EW) processes, which produce high levels of toxic sulfur dioxide, sulfuric acid mists, particulates, and other emissions originating from the metallic concentrate. Zambia’s Ministry of Mines and Minerals Development has required the facility reduce acid mists by 94% and particulates by 99.5%. The sulfuric acid plants operating with Beltran’s advanced WESP technology have surpassed the government guidelines.
AngloGold Ashanti Brazil Mineracao, a leading gold producer, operates a sulfuric acid plant that converts the sulfur oxide SOx produced as a byproduct of gold mining into sulfuric acid for sale in the worldwide marketplace while also preventing its release as a harmful gas in the atmosphere. For optimum gas-cleaning, the facility selected a WESP system from Beltran Technologies to clean the gas stream of impurities before they enter the sulfuric acid plant. These impurities include: As, Hg, Cu, Fe, Zn, Cd, Pb, Mn, Ti, Cr, SO3 and sulfuric acid mist.
At Hindustan Zinc, in Udaipur, India, Beltran executed a number of projects with a total of 16 WESPs in a 10 x 10 configuration. The WESPs clean gas emissions coming out of a zinc smelter. The gas emissions generated during the smelter operation contain dust and sulphur dioxide (SO2) as well as other gases. The gases first pass through a dry ESP to remove most of the dust particles. Then the gas passes through a Quencher/Venturi Scrubber where the gases are quenched and removed.
The result of this process is the formation of SO3 mists or sulfuric acid mist H2SO4 Following the Quencher/Venturi Scrubber sequence, the gases then pass through the WESP for final removal of sub-micron particulate and H2SO4 acid mists. Once the gases have passed through the WESP there is virtually no remaining dust particulates and the dirty gases have been cleaned to produce 99.98% pure SO2 gases. These gases are then sent to a sulfuric acid plant where they can be converted into pure sulfuric acid.
WESPs are being built of metal alloys, thermoplastic materials, thermosetting materials, and conductive graphite composite materials. However, some of these materials have disadvantages, such as metal alloys, are expensive to produce and have extended delivery time. But their biggest disadvantage is the unreliable performance with regard to corrosion. The sulfuric acid WESP operates in highly corrosive environments, including sulfuric, hydrochloric, and hydrofluoric acid and other impurities, as well as high temperature. Because of the high cost of more robust chrome-nickelmolybdenum alloys, like C-276, C-22, and C-2000, designers are attempting to utilize less corrosion resistant alloys like AL6XN and SMO 254, with resulting corrosion problems in some applications.
Beltran WESPs manufactured with conductive graphite composite materials have the advantage of being excellent in the following areas:
• Highly corrosion resistant
• Have good mechanical properties
• Electrically conductive
• Homogenous
• Do not require water/acid film to ground the WESP
• Fire retardant and thermally robust
• Cost effective For more information, contact Beltran Technologies, Inc., at (718) 3383311 or info@beltrantechnologies.com; or visit the company website at www. beltrantechnologies.com. q
• PROX-SVERS® Ceramic Balls
• Christy® Pak Ceramic Saddles
• Christy® Pak Cross Partition Rings
• Christy® Pak Low Pressure Drop Saddles
• Thermoplastic Tower Packing
If you’ve ever ordered a metal expansion joint and had a vendor throw a bunch of alloy names, H/L designations, and trade names at you, you’re not alone. There’s a lot of confusion about what different metal types actually mean, which ones you need, and which ones are a waste of money in a sulfuric acid plant.
This article aims to cut through the noise and break down the most common alloys used for metal expansion joints, why they matter, and where they should (and shouldn’t) be used.
Carbon steel remains a widely used material in sulfuric acid plants, especially in flanged and flued or heavywall expansion joints found on converter ducting. The reasoning is simple:
• The SO2 and SO3 gases are dry thanks to your drying tower (unless you have air infiltration due to leaks).
• Condensate formation is minimal when the plant shuts down.
• Stainless steel at >3/16” thickness is prohibitively expensive.
For these reasons, many sulfuric acid plants use carbon steel for large-diameter expansion joints, as well as for ductwork and converters themselves. However, carbon steel does not offer corrosion resistance when exposed to prolonged wet or acidic conditions, so its use is strictly limited to dry applications when used for gas-handling. (Obviously, the storage of cold liquid acid is a different story.)
Best applications:
• Heavy-wall or flanged and flued designs exclusively
• Converter ducting expansion joints
• Low-condensate environments
Avoid if:
• You need thin-wall metal bellows to achieve desired movements. Carbon lacks ductility for forming reliable convolutions.
• The expansion joint will be exposed to prolonged condensate.
By: CJ Horecky, Executive Director, INTEREP
• There is frequent cycling that could lead to stress cracking.
For most flue-gas handling expansion joints where some degree of condensate exposure is present, 300-series stainless steels provide a good balance of corrosion resistance, strength, and cost-effectiveness.
304L and 304H are both commonly used in sulfuric acid applications, but they serve different purposes.
304L is preferable for welding-intensive applications because its low carbon content prevents carbide precipitation, which can lead to intergranular corrosion.
304H is used in high-temperature applications where additional creep strength is needed, but it comes with a higher risk of sensitization if improperly welded.
Best applications:
• General flue-gas ducting where minor condensate exposure is expected
• Applications requiring significant repeat welding
• High-temperature service (304H)
Avoid if:
• The gas stream contains chlorides. 300-series stainless is highly susceptible to chloride stress corrosion cracking, especially 304L.
• Wet acid exposure is continuous. In such an environment, higher alloys may be needed.
Note: INTEREP does not recommend writing a specification for either 304L or 304H. Rather, specify the carbon content range that’s acceptable to you, which allows your fabricators to use “dual certified” materials and save you a lot of headaches during procurement. 304 Stainless with >.04 carbon content is notoriously hard to procure, and often requires mill-run purchase quantities.
321 stainless steel takes the benefits of 304H but adds titanium, which ties up carbon and prevents carbide precipitation entirely. This makes it one of the best stainless steel options for high-temperature service where welding is required. This is the most frequently used alloy for INTEREP metal bellows expansion joints.
Choosing the right alloy for sulfuric acid expansion joints isn’t about finding the “best” material—it’s about finding the right balance of corrosion resistance, strength, and cost for your specific application.
Best applications:
“ ”
• Flue-gas ducting with mild-to-moderate condensate exposure
• Expansion joints that require frequent welding during installation
• High-temperature applications where corrosion resistance is still necessary
Avoid if:
• Corrosion resistance is a primary concern in wet-acid environments. In such environments, higher alloys may be required.
• Your gas stream is high in chlorides.
When sulfuric acid condensate is a serious issue—especially in wet-gas handling systems, absorbers, or weak acid streams—304 and 321 stainless steels often don’t cut it. This is where nickel-based alloys like Inconel 625 come into play.
Unlike stainless steels, which rely on chromium oxide to provide corrosion resistance, Inconel 625 forms a protective nickel oxide layer, making it:
• Highly resistant to chloride stress corrosion cracking
• Exceptional in high-temperature environments
• Highly resistant to sulfuric acid exposure
Grade
Inconel 625 Nickel (58% min) + Molybdenum Exceptional High Acid condensate environments, high-temp flue-gas applications
In sulfuric acid plants, Inconel 625 is often overkill for converter ducting, but it becomes necessary in expansion joints where wet acid condensation, chlorides, or high cycling are concerns.
Best applications:
• Scrubbers or absorbers with hot gas exposure and mixed media
• Expansion joints in weak acid or wet-gas handling
• High-temperature and corrosive environments
• High chloride content in gas stream
Avoid if:
• The application is strictly dry-gas. In this environment, carbon steel or 321 may be more cost-effective.
• Operating within the Inconel 625 sensitization range.
(More to come on this in a subsequent issue of Sulfuric Acid Today.)
For quick reference, here’s a breakdown of the most common materials used for expansion joints in sulfuric acid plants:
Material Key Properties
304L SS Good corrosion resistance, easy to weld Flue-gas applications with occasional condensate High-temp or extreme corrosion
304H SS Higher strength at high temp Hightemperature flue-gas applications Frequent welding
321 SS Best for hightemp welding High-temp, mild acid exposure
Inconel 625 Outstanding corrosion resistance Wet acid, chlorides, absorber towers
Extreme acid resistance needed
Cost-prohibitive for dry-gas service or in sensitization temp range
Choosing the right alloy for sulfuric acid expansion joints isn’t about finding the “best” material—it’s about
finding the right balance of corrosion resistance, strength, and cost for your specific application. That said, there are plenty of other alloys and metals that we’ve made expansion joints from, including INCOLOY® Alloy 800, RA 253 MA®, Titanium, Bronze, and Copper. This article simply covers the most common metals that you’ll encounter in the expansion joint world.
• If cost is the main concern and the gas stream is dry, carbon steel is a solid choice.
• If carbon steel won’t cut it and significant repeat welding is required, 304L or 321 offers good performance with minimal sensitization risks.
• If high-temperature service is the priority, 321 or 304H provides increased strength.
• If wet-acid exposure is unavoidable or chlorides are present, Inconel 625 is the safest bet.
INTEREP has been designing and supplying sulfuric acid metal expansion joints for over 40 years, and we know that every plant is different. If you’re unsure about what alloy is best for your application, give us a call. We’ll give you straight answers and practical solutions, because when it comes to rebuilding the American sulfuric acid industry, getting it right the first time is the only option.
For more information, contact CJ Horecky at (480) 500-9161 or CJ@INTEREP.us or visit the company’s website at www.interep.us. q
By: Martin Ariel Alvarez, Anders Theilgaard Madsen, and Mårten Nils Rickard Granroth
The sulfuric acid industry is relentlessly striving for higher production capacity, better energy efficiency, and lower SO2 emissions. While there are many unique ways to achieve this, having access to better catalysts is an important enabler for all three. There is no such thing as a perfect sulfuric acid catalyst that can maximize all performance parameters simultaneously. Designing a good catalyst involves a compromise between achieving good strength, low pressure drop, and, most importantly, high activity. An important starting point for designing any catalyst is, therefore, to understand the relative importance of parameters such as intrinsic activity, pellet wall thickness, and voids in the catalyst bed.
The theory behind evaluating effectiveness factors for heterogeneous catalysts explains how these parameters are interrelated and is well known. When this model is combined with extensive experimental data and detailed kinetic modeling, it provides an understanding of the relative importance of the different resistances under the relevant conditions of industrial SO2 converters and where different catalysts are best employed for optimal performance in the industrial plant.
As shown in Fig. 1, the reactants and products diffuse through the external gas film to/from the catalyst exterior surface, and they diffuse inside the particle pore system where they also react in the surface-distributed melt.
The overall catalytic rate (-robs) for the catalyst layer should be for the entire layer including the void between pellets, while pellet rates could be called (-rint); the “-“ sign serves to remind that SO2, the key reactant, disappears with the reaction. Diffusion limitations must be calculated for pelletized catalysts because the diffusion in the catalyst pores cannot be decoupled from the catalytic reaction on the catalyst active surface (in this case the catalytically active melt) distributed on the carrier interior surface.
Assuming the case of a reversible (pseudo-)1st-order reaction, A(g) B(g), where there is no initial concentra-
tion of B present, the overall reaction rate can be written as equation [1], where the three resistances described before can be seen in series.
Equation variables: k1, the intrinsic constant rate; L C , the length of diffusion, or the inverse of the external surface area per unit of volume; kG , the external film mass-transfer coefficient; ηs , the effectiveness factor as a function of the surface conditions; C 0 A,G , the initial concentration of the key reactant A, and X and X EQ the conversion and the equilibrium conversion, respectively.
It shall be noted that the use of a pseudo-1st-order rate kinetic law is an approximation, as some difference in effectiveness factor compared with reaction order can be expected. However, when used together with a proprietary model derived from thousands of experimentally determined reaction rates by in-house measurements, the result will be accurate enough to give the right overall conclusions about the catalytic performance.
As a first example of how this model can be applied to understand the contributions of the different resistances to the overall reaction rate, Fig. 2 shows the relative importance of the different resistances along the first bed of an S-burner plant that operates with 11% SO2
The size and shape selected by a catalyst manufacturer are a compromise between pressure drop and strength on the one hand, and activity on the other. Shape and size define two geometric parameters:
• the bed void fraction (ε)
• the effective length of pore diffusion (L C) defined as the inverse of the external surface area per unit of pellet volume.
Low pressure drop is favored by larger catalyst sizes and shapes with higher void fractions. However, larger catalysts (high (L C) values) increase pore diffusion resistance, reducing reactant accessibility to the active melt. This results in low effectiveness and performance when pore resistance is significant. Additionally, shapes with very high void fractions contain less catalyst mass in the same volume, limiting performance.
Conversely, smaller sizes or shapes with lower L C and void fractions enhance activity but increase pressure drop. An example of how to deal with this compromise can be illustrated by comparing a 3+1 double absorption plant with a typical S-burner gas, using a converter filled entirely with 12 mm daisy-shaped catalyst in one case and 10 mm ring-shaped catalyst in another case.
At the top of the bed, where the inlet temperature is low, there is a significant kinetic resistance. However, as we move towards the bottom of the bed, where the temperature is the highest in the converter, the kinetic resistance decreases, and pore diffusion becomes more important. The influence of film resistance along the bed is negligible, and it only slightly increases at the very bottom. This example serves as an illustration of how the overall reaction rate is governed by different phenomena even within the same converter pass. At the top of the bed, the reaction is primarily limited by the kinetics. However, as one moves towards the bottom of the bed, the reaction becomes pore diffusionlimited.
Table 1: Geometric properties for 10 mm rings and 12 mm daisy-shaped catalyst.
Thanks to the higher void fraction, the daisy-shaped catalyst offers a considerably lower rate of pressure drop build-up and better dust capacity compared to an equivalent volume of 10 mm rings. This is achieved without sacrificing activity due to the shorter pore diffusion length of the daisy shape. The shorter pore diffusion length results in an average 10% higher effectiveness factor along the entire converter (Fig. 3). Therefore, even though a bed filled with 12 mm daisy-shaped pellets contains more void and less catalyst mass per unit of bulk volume of the reactor than a bed filled with 10 mm rings, the mass is used more effectively, and the conversion is maintained.
Table 2 shows the impact on catalyst loading and pressure drop for both cases. The same bed filled with 12 mm daisyshaped catalyst will have a much lower pressure drop than a 10 mm ring-shaped catalyst, without sacrificing conversion.
Table 2: Loading and pressure-drop for a converter filled with 12 mm daisy and 10 mm ring catalyst.
This example shows that for a given intrinsic material, an increase in the external surface area per unit of volume (a reduction in L C) leads to an optimized or better shape if it is also accompanied by an increase in the void fraction to counteract, at least, a major part of the pressure drop increase caused by the reduction in L C. In general, if the void fraction is not increased enough to balance this, then the extra activity gained by the increase in the external surface area per unit of volume is at the expense of higher pressure drop, which is generally not preferred in the industry due to its negative effects on plant capacity and energy consumption.
Having looked at the behavior in a first bed in the previous section, let’s look at how the resistance changes for the other beds in a double absorption plant. Fig. 4 shows the relative value of the different resistances along the four beds of a 3+1 S-burner with 11% SO2
At the top of bed 2, the kinetic resistance is high due to the lower inlet temperature. However, as we move along the bed and the temperature increases, the kinetic resistance decreases. It is important to note that the temperatures in the second pass are not as high as they were at the bottom of the first pass. As a result, the kinetic resistance remains high (>50%) throughout the entire bed. Since the reaction is reversible, an increase in the partial pressure of SO3 slows down the reaction, contributing to an increase in the kinetic resistance. The film resistance contribution is also negligible (<5%) in this pass.
In bed 3, the trend is similar, but the temperatures are even lower and the amount of SO3 is higher. As a result, the kinetic resistance remains very high and explains 6575% of the total resistance along the bed. Film resistance remains minimal (<5%) along the third pass as well.
The gas entering bed 4 is very lean and almost free of SO3. The low concentration of SO2 in the process gas causes all mass transfer phenomena to occur at a slower rate compared to the upper beds. Pore diffusion becomes significant, explaining more than 55% of the contribution at the bottom of bed 4. The film resistance also increases, although it remains very low.
In a standard SO2 converter, the kinetic resistance remains consistently high, except for the bottom of the first pass where temperatures are very high, or in the last pass
where internal pore diffusion resistance is significant. This suggests that other than for bed 4, improving the intrinsic activity will be the most effective way to improve the bulk activity. This can be achieved, for example, by developing superior carrier systems with optimized chemical composition that allow a better utilization of the active metals within the catalyst.
On the other hand, changes that only impact the pore diffusion resistance, such as using a catalyst with a shorter length of diffusion L C (e.g., smaller sizes or shapes with greater external surface area per unit of volume) will have a limited effect. These changes may be meaningful at conditions where the bulk activity is pore diffusion-limited, such as: lean gas conditions, regions with very high temperatures, or when the catalyst already is made of a very active intrinsic material and the kinetic resistance has been already minimized (example: special Cs-promoted catalyst such as VK69).
Factors influencing the film resistance (such as superficial velocity) will have no impact on the overall rate.
Let’s now consider the same case as in the previous section except with a converter filled entirely with a catalyst that has a higher intrinsic activity but with the same size and shape. To exemplify, this could be the VK38+ compared with the regular VK38. The contribution of the different resistances to the overall reaction rate can be seen in Fig. 5.
The kinetic resistance is reduced in all beds when a catalyst of higher intrinsic activity is used. The reaction rate is accelerated and increases the diffusion requirement. The table below compares the overall effect of using a catalyst with higher intrinsic activity in an industrial converter. The higher intrinsic activity, under the same inlet conditions and with the same shape and size, reduces the volume of catalyst required to achieve a given conversion of 99.86% by 28%, demonstrating the impact of addressing one of the most significant resistances. The reduction in pressure drop is also 28%; simply a consequence of the reduced catalyst bed height.
Finally, one may wonder if the weight of the relative resistances changes drastically with changes to the composition (and the O2/SO2 ratio). To answer that question, the relative contribution of the different resistances has been mapped for two additional cases with a gas composition typical of copper smelters and zinc roasters.
Overall, the distribution of resistances is quite similar among the three typical process gas conditions. However, there are some differences observed in the upper beds of a Cu-smelter gas. In this case, the stronger gas and higher temperatures contribute to a lower kinetic resistance.
Understanding which resistance (kinetic, pore-diffusion, or film) is rate-limiting in each part of the converter is a complex task and highly dependent on specific conditions. The distribution of resistances changes not only from bed to bed but also within the same bed. Consequently, a modification that benefits one bed or part of the bed may not be suitable for the rest. However, having a catalyst with higher intrinsic activity is generally by far the most efficient way to improve the bulk activity.
Changes in size or shape that result in a shorter diffusion length (L C) or a higher external surface area per unit of volume are in general advantageous if they are accompanied by an increase in the void fraction ε, and the new shape or size can reduce pressure drop without compromising activity. If the void is not changed, the higher activity comes at the expense of higher pressure drop.
The relative importance of resistances does not change significantly with three typical feedstocks used (Cu Smelter, Zn roaster, S burner). The only noticeable change is a decrease in kinetic resistance for Cu-smelter gases due to the high temperatures associated with higher SO2 strength.
Finally, no example of an industrial SO2 converter has been found where film resistances are important. Therefore, changes in superficial velocity or specific external surface area oriented to minimize this resistance are not expected to have a significant impact on performance. q
References
[1] Levenspiel, O.: Chemical reaction engineering, 3rd ed., 1999. Published by John Wiley & Sons, Inc.
[2] Froment, G.F.; Bischoff, K. B.: Chemical reactor analysis and design, 2nd ed., 1990. Published by John Wiley & Sons, Inc.
[3] Scott Fogler, H.: Elements of chemical reaction engineering, 3rd ed., 1999. Published by Prentice Hall PTR, Inc.
[4] Topsøe, H.F.A.; Nielsen, A.: The activity of Vanadium catalysts in the sulfur trioxide synthesis. Trans. Dan. Acad. Techn. Sci., 1948, vol. 1, iss. 3, pp. 18-24.
SOUTHWEST REFRACTORY DELIVERS THE HIGHEST QUALITY ACID PROOFING, REFRACTORY, INDUSTRIAL MASONRY AND FIREPROOFING WORK.
With in-depth engineering support, meticulous craftsmanship and extensive planning down to the finest details, we’re turning industry into artistry.
Sulfur is one of the most important feedstocks for all sulfuric acid plants and in most cases is supplied from a sulfur melting and purification plant. The process of liquifying sulfur seems like a relatively simple step in the production of sulfuric acid, but if done in a non-optimal way, the process could significantly impact operational reliability and maintenance in both the sulfur and sulfuric acid plants. This article provides an overview of the important considerations in designing a sulfur melting tank.
Many believe that the melting tank performs the single task of changing the phase of sulfur from solid to liquid. But in reality, the sulfur melting tank also removes water, neutralizes acid, and ensures the liquid sulfur is a homogenic suspension.
The sulfur tank’s major purpose is of course to melt sulfur and elevate its temperature to the required process temperature. The energy (heat) to do this is delivered to the melting tank by steam, which then cools and condenses inside heat exchangers. While the sulfur is heated from ambient temperature to 135°C, it surpasses the evaporation temperature of water. Therefore, the water present in the solid sulfur evaporates and leaves the melting tank via the stack into the atmosphere.
It is often thought that most of the heating energy is used for melting the sulfur itself, but when the latent heat of fusion for sulfur (39 kJ/kg) is compared to the latent heat for water evaporation (2258 kJ/kg) it is the water content of the material that has the most significant impact on the heat consumption of the melting tank. Fig. 1 shows an example heating curve for a melting tank. Section A represents heating the feed material from ambient temperature until 100°C, followed by section B, which represents the evaporation of water. Once the water has completely evaporated, the material is heated in section C from the evaporation point until the melting point of sulfur, which melts in section D. The last bit of energy is used in section E to elevate the temperature until the desired process temperature.
The melting tank also consumes energy in the form of electrical energy. The electrical energy is mostly consumed by the motor of the agitator and in much smaller amounts by the instrumentation installed on and around the tank.
There are various styles of commercially available heat exchangers that can be used inside the melting tank. The most common heat exchanger shapes are complex geometric and helical shapes (Fig. 2). What all heat exchangers have in common is that they should be designed in a way that allows the entirety of the heating surface to be installed underneath the liquid level. To extend the lifetime of the heat exchang-
ers, it is important to protect the steam and condensate pipes leading to and from the coil using a cladding material such as 316L stainless steel or a more acid resistant material to protect the coil from corrosion from acid present in the tank.
The more complex geometric shapes have the advantage of maximizing the surface area of the heat exchangers in the smallest possible space. Unfortunately, the space saving characteristics of this type of heat exchanger has several downsides. First, the complex shape requires a lot of manual welding to produce, which makes it time-consuming and expensive to manufacture. Also, the design offers very limited accessibility for maintenance, often requiring the removal of several layers of piping to access a leak in the inner part of the heat exchanger. Finally, due to its dense construction, larger particles such as stones can easily get trapped in between the exchanger tubes which impacts the liquid flow around the heat exchanger. Maintaining heat exchangers often requires removing them from the melting tank. And because of their complex shape and support structure, they typically need to be disassembled by major sections of piping which requires draining the contents of the tank to remove the heat exchanger.
The alternative to this more complex shape is the spiral heating coil, which has the advantage of being constructed from one or several pipes that are bent into a specific radius. This reduces the welding and labor involved in making the heat exchanger. The downside is that it is not as space efficient as the more complex heat exchanger types, but in general this is not an issue since the tank already has a minimum volume due to the acid neutralization reaction. Removal for maintenance of these exchangers is also simpler compared to the complex geometric shapes since the spiral types are often designed to hang from a flange in the roof and thus only need to be disconnected from the steam and condensate supply. Once disconnected, the coils can be lifted straight up out of the tank without requiring the tank be drained.
Sometimes heat exchangers are designed to include finned tubes to increase the surface area of the exchanger. Often this results in good heat transfer during the initial operation of a melting tank, but over time performance starts to deteriorate due to solid material such as ash building up in between the fins. For this reason, installing fins is not recommended unless there’s absolutely no other option.
An additional function of the melting tank is to neutralize sulfuric acid present in the solid material. To do this, lime (CaOH2) is dosed on the conveyor belt and the powerful agitator used in the melting process mixes the lime with the sulfuric acid to produce water and gypsum (CaSO4) in accordance with reaction formula 1 below. An important feature of a properly designed melting tank is that it provides sufficient holdup time to allow the lime to react with the sulfuric acid and neutralize the output of the tank.
(1) Ca(OH)2+H2SO4
Historically, melting tanks are designed as rectangular brick lined concrete pits that are positioned in the ground to provide strength and to simplify the construction process. This design has several issues, the most common being maintenance. Since the tank is installed in the ground it can’t be completely drained. Typically, the tank is emptied as much as possible using filtration pumps. The remaining content is cooled until the sulfur solidifies and then operators remove the solid material using pneumatic hammers. During this last step it is common to damage the brick lining and melter internals such as the heating coils, resulting in often costly and unnecessary additional maintenance work.
Modern melting tanks, on the other hand, are designed above ground and are circular with brick lining. They have a large drainage connection on the bottom (Fig. 3) through which sulfur is drained. By draining from the bottom of the tank, most of the sulfur is removed without requiring operator intervention inside the tank. In the most advanced systems, the bottom drain is connected directly to the inlet of the pump tank, where a strainer is installed in the pipe, and the entire or part of the content of the tank can be drained while retaining the larger settled parts in the strainer. This greatly reduces the amount of waste material produced during the cleaning process.
The rectangular tank design’s sharp corners also become dead spots in agitation where sedimentation of the solids collect. This further increases the maintenance requirements of the tank in comparison to alternative solutions. In the modern melting tank this issue is solved by making the walls of the tank round and by installing a strong agitator in the center of the tank, which keeps all solids in suspension until they are removed in the filtration section of the plant.
To minimize costs and have efficient and reliable melting tank operations, good design choices need to be taken into consideration. These include heat exchanger selection, acid neutralization, and tank shape. When overlooked, these can lead to increased energy consumption, equipment failures and costly downtime.
Sulphurnet offers an all-in-one design package that covers every stage of your project for sulfur processing plants. We are dedicated to more than just filtration systems; our mission is to help customers worldwide reduce production costs, enhance product quality and yields, and improve HSE performance. For more information, contact info@sulphurnet.com or visit www.sulphurnet.com. q
The Central Florida Section of the AIChE will host its annual Phosphate Fertilizer and Sulfuric Acid Technology Conference from June 6-7, 2025 at a new location, the TradeWinds Resort in St. Petersburg Beach, Florida.
Each year for the last 47 years, members of the AIChE Central Florida Section and colleagues from all over the world have gathered to share their ideas concerning chemical process technology, specifically the production of phosphoric acid, phosphate fertilizers, sulfuric acid and other related topics. The convention provides ample opportunity to relax with friends and family, enjoy good food, and have fun.
This year there will be several workshops held on Friday, June 6, including the Bi-Annual PE Laws, Rules, and Ethic Workshop as well as a session relating to sulfuric acid. Participants can also earn up to 8 PDH for attending both Friday and Saturday sessions.
If you have any other questions or would like more information regarding
the conference, please contact Convention Chair Michelle Navar at vicechair@aichecf.org or Section Chair Robert Andrew at chair@aiche-cf.org.
For more information, please visit https://aiche-cf.org/annual-conference.
Holtec will host its 2025 Round Table Meeting for Smelters, Roasters and Refineries from August 21-22, 2025 in Viña del Mar, Chile at the Hotel Novotel.
Operators and maintenance experts; technology providers; smelter-, roaster-, and refinery owners; consultants; and specialized engineering firms will discuss the latest developments in technology, projects, operations, and markets. The conference welcomes delegates from many of the Spanish speaking countries in Central and South America, and the rest of the world, to present projects and discuss operational and maintenance topics during this twoday seminar. Technology providers will have a unique opportunity to talk directly with their clients and present their latest
products and developments.
Registration is complimentary for operators. Deadline for registration: August 1, 2025.
For more information, please visit www.mesaredondachile.com.
Since 1993, the Brazilian Sulphuric Acid Congress (COBRAS) hosted by Clark Solutions has established itself as the southern hemisphere’s main forum for debate and presentation of new technologies in the sulfuric acid industry.
The 13th edition of COBRAS will be held from September 29 to October 2, 2025 in Serra Gaúcha, Gramado, RS. Leaders and experts from companies in various countries will meet to exchange experiences, share knowledge, present innovations, and discuss the main market trends.
For more information, please visit www.cobras2025.com.br.
The Sulphur + Sulphuric Acid conference continues to be an essential annual
forum for the global sulphur and acid community to learn, connect, and do business. Knowledge sharing is at the event’s core, via the respected dual-streamed technical program and connections between the attending industry experts and solution providers. The conference takes place November 3-5, 2025 at The Woodlands, Texas.
This year you can expect an expanded market outlooks agenda, including expert insights from CRU’s analysis teams on major supply and demand markets, including sulphur and sulphuric acid, plus additional industry updates from key players from across the supply chain.
Covering technical updates on the production and processing of sulphur and sulphuric acid, the event will feature industry-leading presentations covering new innovations in process, technology, materials and equipment developments, as well as practical case studies highlighting operational experience and improvement.
Running alongside the agenda will be an exhibition of world-class solution providers serving the sulphur and sulphuric acid industries.
For more information, visit events. crugroup.com/sulphur/home. q
With our expertise in process design, process optimization and numerical process simulation, we provide you with tailor-made solutions for your project.
With over 130 years experience, LEWIS ® pumps and valves are engineered with genuine LEWMET alloys, meaning they provide better corrosive resistance than anyone else. Our team is focused on one thing, and one thing only, creating the most durable products in the world. It’s no surprise we’re market leaders, there’s just nothing as strong as Lewis pumps and valves.
Learn more at onlylewis.weir