
9 minute read
SITE VISIT
GEARING UP FOR THE FUTURE
David Wylie visits the Grange Quarry Group to see how its new prime mover, the fi rst Hitachi ZX530-7 to be sold in Scotland, is settling in
Advertisement
s we have reported over the years,
ALockerbie-based Grange Quarry has a network of quarries, concrete batching plants and local operating centres, together with fl eets of both tipper and mixer trucks, supplying aggregates and ready-mixed concrete across Dumfriesshire and northern Cumbria.
Since our last visit to Kelhead quarry near Annan, a new market has been developed for the limestone deposit on site, in the form of an agricultural lime. Last year 70,000 tonnes of this high calcium material were distributed by Grange Quarry to farmers throughout Scotland.
A key product on site is a Breccia stone, known as Kelhead Red, which has many applications and is used extensively by Grange Quarry’s Lockerbie and Dalbeattie batching plants. Once the distinctive red rock has been through the primary crusher at the face, new Liebherr wheel loaders feed a fl eet of articulated dump trucks, which haul the material to the top of the quarry. Much of it is tipped directly into the washing plant’s in-feed hopper, which produces various fi nished products, including 10/20/40mm stone, together with grit and sand.
NEW PRIME MOVER
Every few weeks a team from contractor RJ Blasting carry out their trade at the Kelhead quarry. Depending upon demand, the blast releases 20,000 to 60,000 tonnes of material at a time. Around 350,000 tonnes a year are extracted from this site, using a 50-plus tonne excavator as the prime mover at the main face. These duties have recently been entrusted
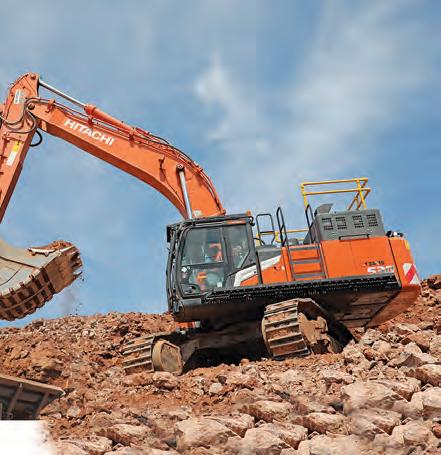
Grange Quarry has replaced a 50-tonne class mass excavation spec machine at its Kelhead quarry with a standard reach Hitachi, which weighs closer to 60 tonnes.

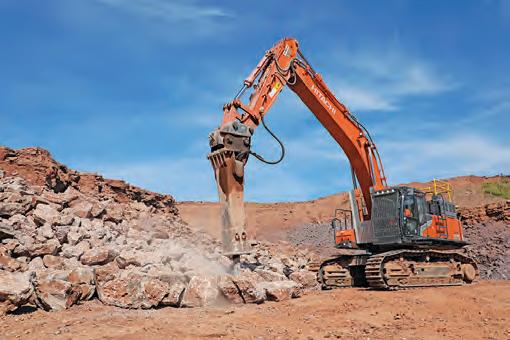
to a Hitachi ZX530-7, the fi rst example of this model to be sold in Scotland.
It represents a minor, but important change in the working method at the face. The previous excavators were confi gured with mass excavation working equipment, while the new Hitachi – weighing closer to 60 than 50 tonnes – swings a larger threecubic-metre bucket on a longer, standardlength dipper arm. The extra reach this excavator provides will come in handy when loading material into a tracked crusher and for descaling the rock faces.
The standard-length working equipment is robust enough to regularly host a 4.7-tonne Rammer 5011 hydraulic hammer. Despite trying various blasting confi gurations over the years, this formation of Kelhead Red always seems to produce a lot of oversize material. The new ZX530-7 will typically spend the fi rst few days after a blast reducing the larger rocks to a size suitable for the tracked crusher. However, appropriately-shaped large lumps are increasingly being diverted out of the production chain at this point, to help fulfi l the growing demand for rock armour – more about this later.
Above and below: Providing almost 12m of reach, the ZX530-7 works with a 3cu.m MST rock bucket, a Rammer 5011 hammer and a heavy-duty Eurofab ripper. OPERATOR FEEDBACK
At the time of our visit the new Hitachi was using its 3cu.m MST rock bucket to feed the Kelhead Red stone into a Kleemann 122 impact crusher, which has a rated throughput of 475 tonnes per hour. At the controls of the ZX530-7 excavator was Denny Duff who, over the last seven years, has operated every new prime mover at the quarry. He said, “Compared to my previous 50-tonne mass excavation machine, this new ZX530-7, with its standard stick and boom and bigger bucket, has lots of digging performance. And has the added advantage of much better reach, to effectively load the mobile crusher from one position.
“The heavy-duty undercarriage and 600mm-wide double grouser track pads make for a very stable machine and the full-length track guards offer good rock protection for the bottom rollers. The cab is nice and comfortable as it comes with all the very latest creature comforts. I particularly like that the levers and seat slide independently from each other to get the most comfortable operating position.”
Denny was also enthusiastic about a number of those all-important minor design details, which make his life easier. They not only include an automatic greasing system, but also a grease gun reel with a long enough reach to maintain the quick-hitch. In addition, the hydraulic connections to feed the hammer line are easily reached from ground level.
With much experience gained over the years of breaking this tough material, the front of the new Hitachi has been provided with additional protection. Collaboration between the site’s fi tters and local company DK Engineering has resulted in a large hoist cylinder guard, which also provides protection for the cab’s offside window. The team have also designed and built a dismountable fi ne screen to stop fragments coming through the standard quarry-spec front screen rock guard.
Quarry supervisor George Lowther explained, “We suffered from a few minor cracks
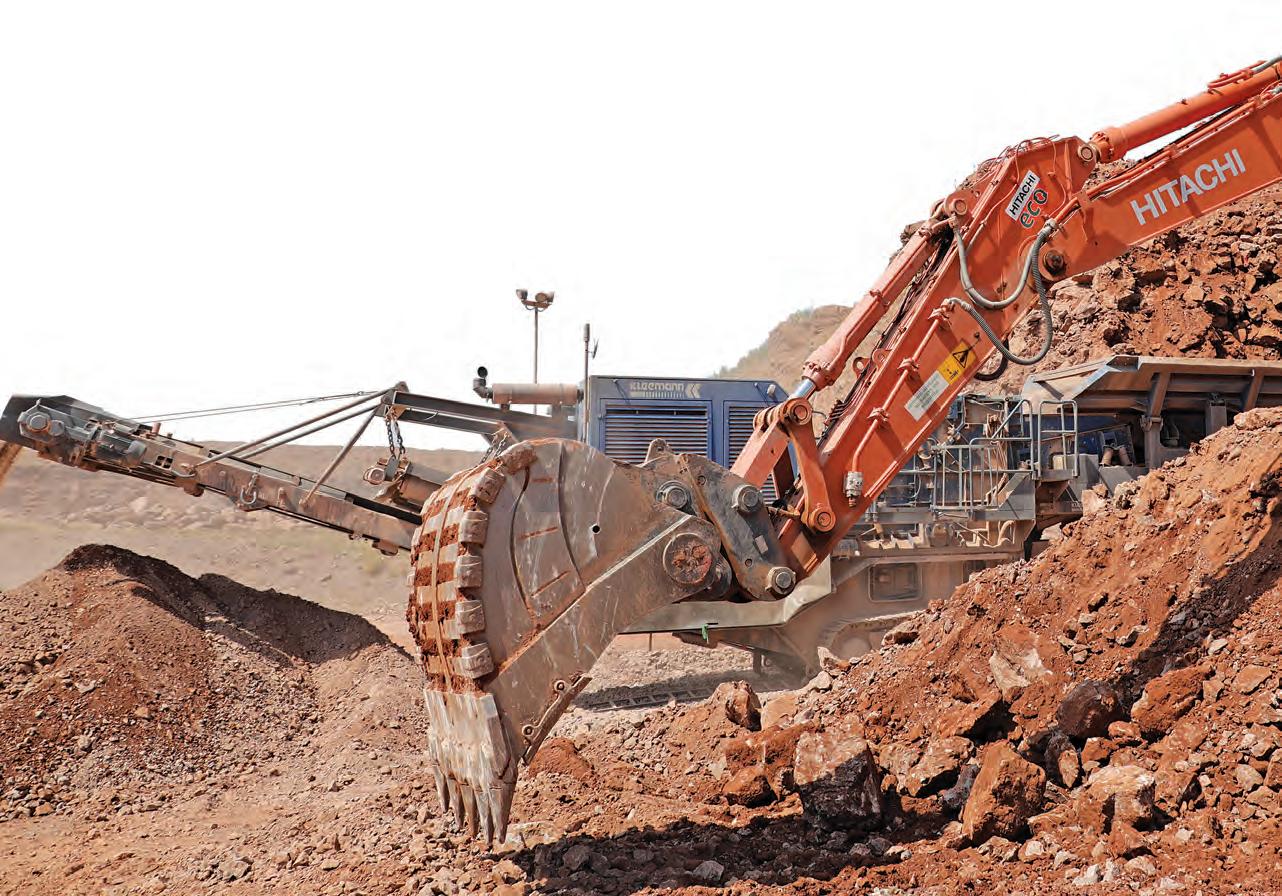
in the front and side windows of our last machine. The team decided to do something different and came up with an effective side guard and detachable mesh screen to protect the front window when breaking the oversize rocks.”
The new Hitachi is subject to a full fi ve-year/10,000-hour service and repair package from the manufacturer, as George continued, “We’re delighted with the new machine’s performance and the service back-up has been fantastic from our local Hitachi engineer. From arrival to its recent fi rst 500-hour service, the machine has not missed a beat. We’re also delighted with the new Hitachi’s fuel economy. It’s burning less diesel than the previous machine and AdBlue consumption is also low, as it’s only using about 10 litres every few days.”
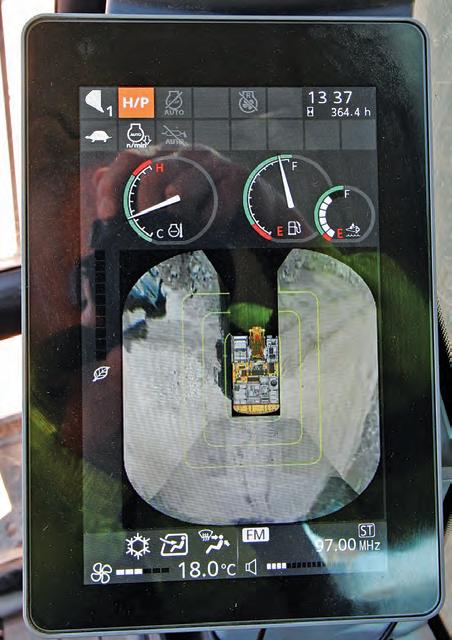
THE BIG PICTURE
The improved fuel consumption from this ultra-low emissions excavator (see spec panel) is only one part of the equation, as it is also more productive than its predecessor. Grange Quarry’s founder,

Right, below right and inset: In addition to a large guard protecting the main hoist cylinders, an easily mountable mesh screen is used to protect the front screen when using the hydraulic hammer.
MD Stuart Dodd, said, “With the big threecubic metre MST bucket it will be tipping the scales at nearly 60 tonnes, loading the primary crusher with fast cycle times with its bigger bucket and longer reach stick than the
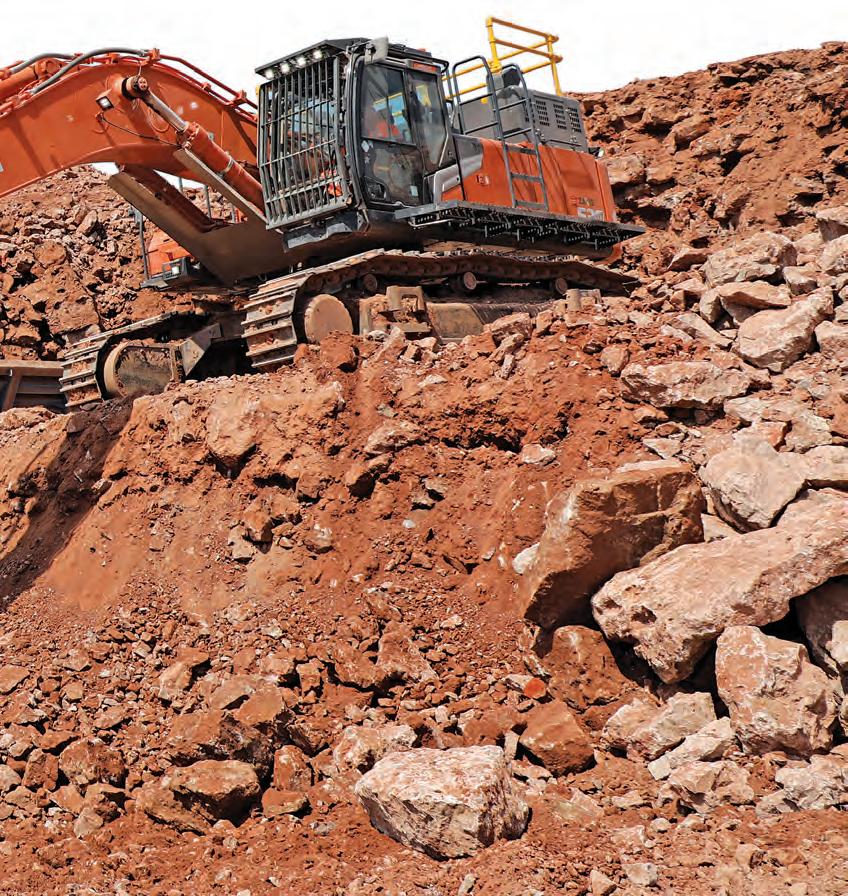
At the heart of the ZX530-7 is a Stage 5 ultra-low emissions six-cylinder Isuzu engine, mated to the latest in cutting-edge Japanese hydraulic systems. Hitachi claims that this combination results in fuel savings of up to 11% compared with the previous model, together with faster cycle times.
The driveline features Hitachi’s unique ConSite Oil system, which continuously monitors the quality of the engine and hydraulic oils. The data are available remotely in real time from Hitachi’s telematics system and its various portals. Periodic oil sampling is a widespread maintenance technique in the quarry sector, and ConSite Oil helps to provide a highly accurate estimation of component health, plus the ability to react immediately to any indication of an imminent component failure.
The ZX530-7 comes with wide full-length catwalks to provide safe access to the engine and hydraulic bays on the nearside of the upper-structure. This example also features full boxing-ring handrail structures round the upper-structure, in addition to quarry-spec flashing rear strobe lights and chevrons. An interesting feature in the cab is the fitment of Hitachi’s aerial angle camera system, which provides a 360-degree view round the machine, displayed on a large LCD control monitor.
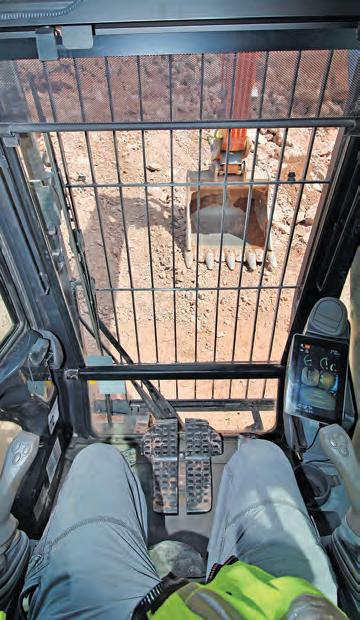
Below and inset: The Hitachi feeds a Kleemann impact crusher, following which the material is hauled to the processing plant. Elsewhere on site progressive restoration is underway.
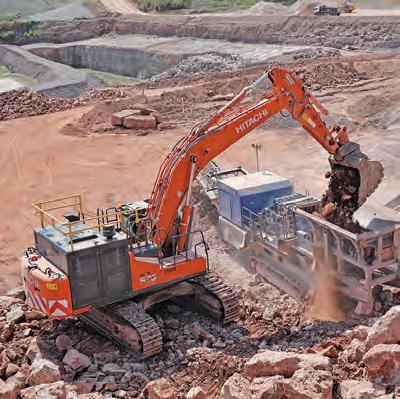
previous machine. Hitachi is a well-respected brand for reliability and durability.
“When we looked at the market for a heavy-duty excavator that would fi t the needs of Kelhead quarry, I spoke to Oliver Halligan at Hitachi about the ZX530-7. We have a long-standing relationship with Oliver, who understood our needs and put together a competitive package for a high specifi cation machine and service contract to suit our needs. Since service support is very important to us, we were impressed to hear of Hitachi’s plans to support Scottish customers, with more service support staff and a larger depot situated in central Scotland.”
With the changing climate there is an increasing demand from various local authorities for rock armour as part of fl ood defence projects. Although a limited amount of suitable material can be diverted from the main blast heave, Stuart ordered a heavy-duty ripper tooth for the new Hitachi to prise out large square-shaped rocks from the face. It was designed and built by local attachment manufacturer Eurofab, which is featured elsewhere in this issue.
CONCLUSION
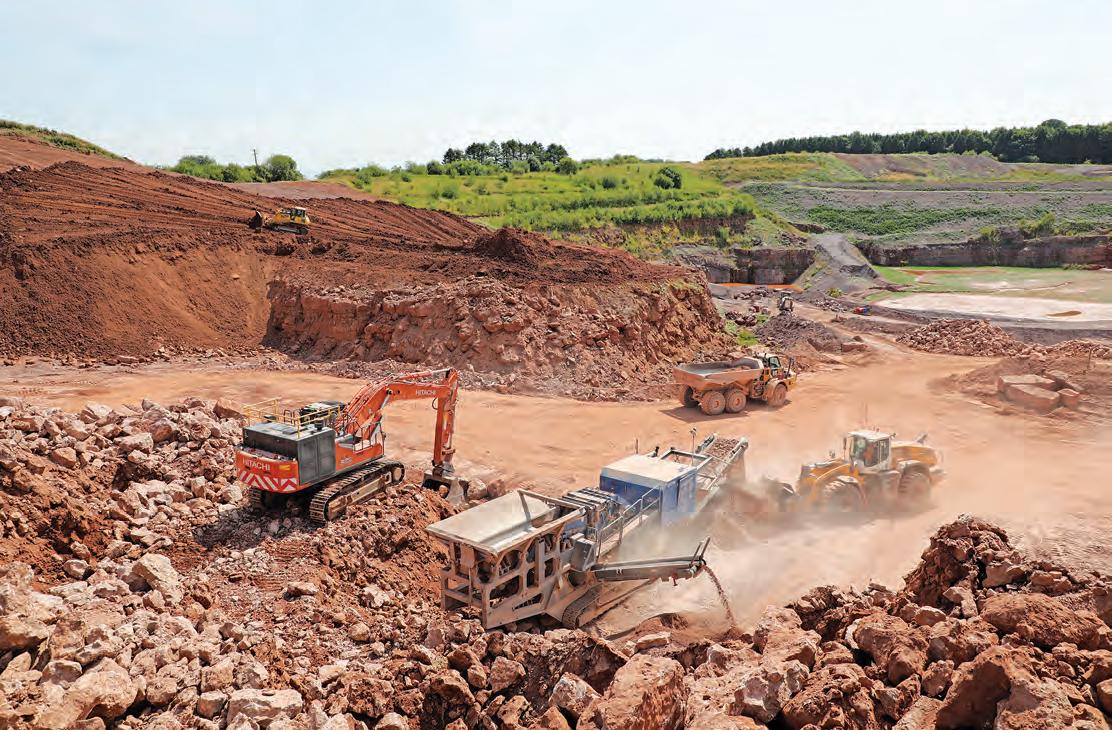
The Kelhead quarry currently has planning permission for another 15 or so years. The site is being progressively restored, and at the time of our visit a Komatsu PX65 dozer was spreading sub- and topsoil to reinstate a worked-out section. Elsewhere on site there is a state-of-the-art CDE M2500 E4 mobile washing plant with an AggMax 83 portable logwasher. It produces a range of saleable products manufactured from inert waste materials accepted into the site’s recycling station.
Without rebated red diesel from next spring, off-road machinery businesses such as Grange Quarry are facing a signifi cant increase in their fuel bill. One way to mitigate this is by bulking up a number of marginal gains. The new Hitachi is proving to be more economical than its predecessor, but also delivers more productivity, while its fl exibility has been increased with the provision of specialist attachments.
Stuart concluded, “While it is still early days operating the ZX530-7, everyone is really impressed with its performance.”
HITACHI CUMBERNAULD
In what is rapidly becoming a local centre of excellence for the off-road machinery trade, Hitachi has relocated its presence in Scotland to Cumbernauld near Glasgow. No longer operating from a small parts depot at Bellshill, Hitachi now supports its Scottish customers from a 12,500sq.ft facility, complete with a parts warehouse and a trade counter. There are also workshop facilities together with a large concrete yard to accommodate the stock of new and used machines. Eight full-time members of staff will be based at the depot, which has created a number of job opportunities, as Hitachi UK’s Stephen Creaser explained, “By investing in bigger premises, employing new sales staff, additional service engineers and a dedicated product support manager, we can ensure that customer uptime will be maximised throughout the region. “There is massive scope for growth here in Scotland. We have already gained the trust of many new customers since the announcement of the new depot, and we look forward to driving their businesses forward over the coming months and years.”