
11 minute read
CLASSIC PLANT
Above: A Ruston-Bucyrus 22-RB dragline with 7/8-yard bucket loads 15 tons into an AEC 690 dump truck on the M9 project. Inset above: An NCK 605 dragline with 1½-yard bucket excavates unsuitable material, too soft to be traversed by mobile equipment.
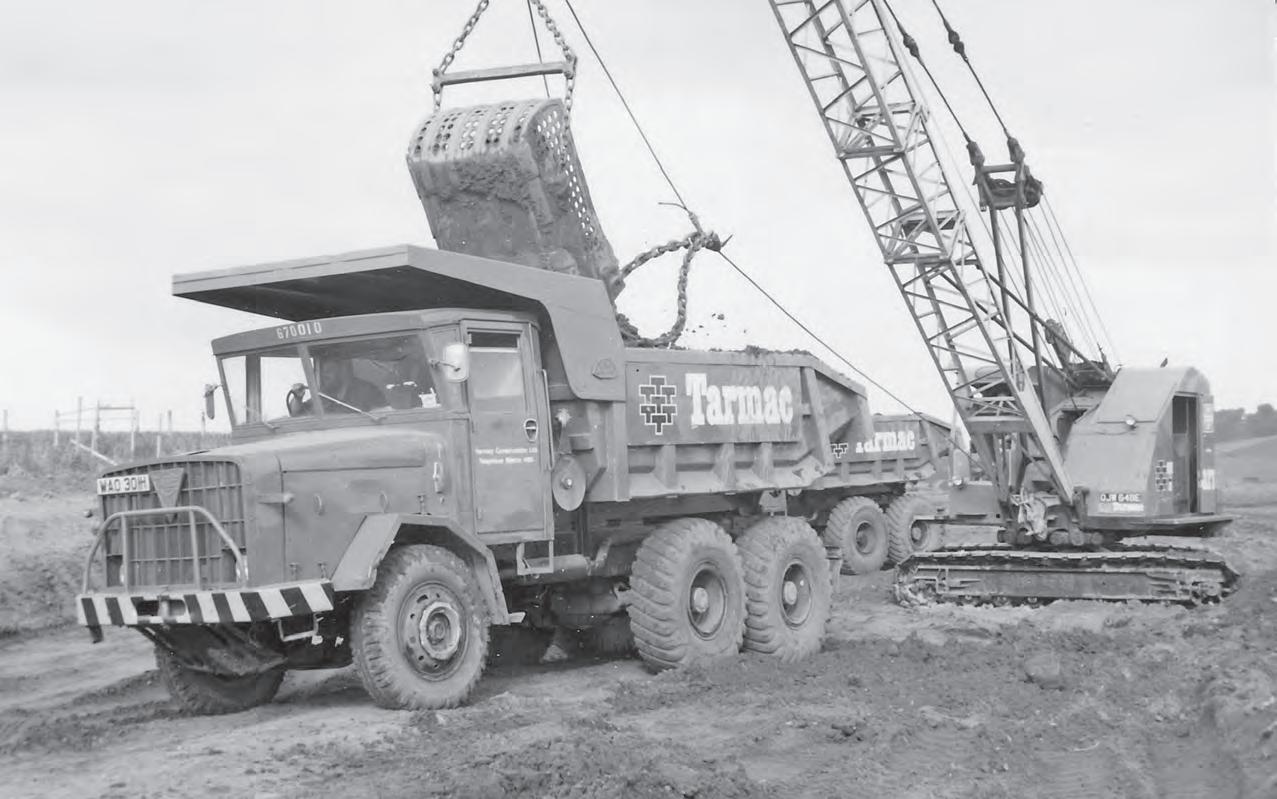
Advertisement
FAST FROM FORTH TO FALKIRK
Keith Haddock recalls the Tarmac contract to build sections of the M9, where the use of hydraulic backhoe excavators for mass muck shifting was pioneered
n 1971 Tarmac Construction was awarded contracts to build two consecutive sections of the M9 motorway, running 10 miles from the start of the Falkirk bypass to the approach to the Forth Road Bridge. Although not a particularly diffi cult road to construct, the contracts were awarded on the basis of an accelerated build schedule lasting just 18 months from start to fi nish. This two-lane stretch of motorway was duly opened in December 1972, the fi rst feather in the cap of Tarmac’s newly-formed Earthmoving Division.
Just before the M9 contracts were awarded, Tarmac had acquired the Scottish earthmoving and civil engineering contractor, AM Carmichael. Well-versed in opencast mining and general earthmoving, although none of Carmichael’s plant came to Tarmac, a signifi cant number of their experienced drivers and foremen formed the core of Tarmac’s new Earthmoving Division. I joined them in May 1971, after I was transferred from Tarmac’s Roads Division, to be their Earthmoving Sub-Agent on the M9 contracts.
Tarmac’s newly-formed Earthmoving Division had amassed a fl eet of Terex TS-24 motor scrapers and Caterpillar tracked tractors with pull scraper boxes for this job. Several areas along the route required the bulk removal of soft material, which was excavated by draglines hired in from local plant hire companies. However, this was at a time when hydraulic excavators were just starting to take over from cable-operated machines, graduating from a service or trenching machine to production earthmovers. For this job, we pioneered
Below: An excavation of a typical motorway cutting: four Terex TS-24 motor scrapers and three Cat D8s with 435 scrapers in action. Inset below: Rated at just nine cubic yards capacity, the Wabco 101F was the smallest motor scraper on site.
the concept of performing bulk excavation work using hydraulic excavators confi gured as backhoes.
Liebherr backhoe excavators, with short booms and maximum-size buckets, sat on top of the excavation and, where the ground was dry enough to support them, loaded a fl eet of AEC dump trucks on the bench below. Because each dump truck parked next to where the excavator was digging, it was just a matter of hoisting the heaped bucket high enough to clear the truck’s body, a short swing over its side and then dump the material.
This working method is still recognised today as being the most effi cient and is commonly employed in bulk excavation works. The angle of slew required during such a loading cycle is minimised, as is the need to hoist the bucket, as the excavator is sitting above the truck. Even better, the excavator drivers had an excellent view of the working area – pioneering times indeed.

CLASSIC FLEET
W.A. Fairhurst & Partners were the design and consulting engineers for this £7.7m contract, the route of which passed close to the ancient town of Linlithgow with its picturesque lake and preserved ruins of Linlithgow Palace. The works required the removal and placement of large volumes of soft material unsuitable for use as structural fi ll, and some long hauls were required. Coupled with the M9’s accelerated construction schedule, a large and diverse fl eet or earthmoving machines was deployed to this job.
Three main fl eets of machines carried out the majority of the earthworks, plus many ancillary machines for the smaller work. Short-haul dry material was moved by a fl eet of Cat D8s pulling 435G scrapers rated at 17 cubic yards heaped. For longer hauls in good material, four Terex TS-24 motor scrapers rated at 32 yards heaped did their duty, aided by a Cat D9G rigged strictly as a push tractor.
The third fl eet handled unsuitable material, which probably amounted to more than half the volume of this job. This fl eet consisted of crawler draglines and hydraulic excavators equipped as backhoes loading into a variety of haul units. Draglines included a one-yard Smith 26, a ¾-yard NCK 305, a 1½-yard NCK 605 and a 7/8-yard 22-RB.
Hydraulic excavators included three Liebherr 941s with 1½-yard buckets, a two-yard Liebherr 961 and Priestman 220, together with a one-yard Hymac 880. The Tarmac haul fl eet boasted a dozen brandnew AEC 690 dump trucks rated at 15 tons
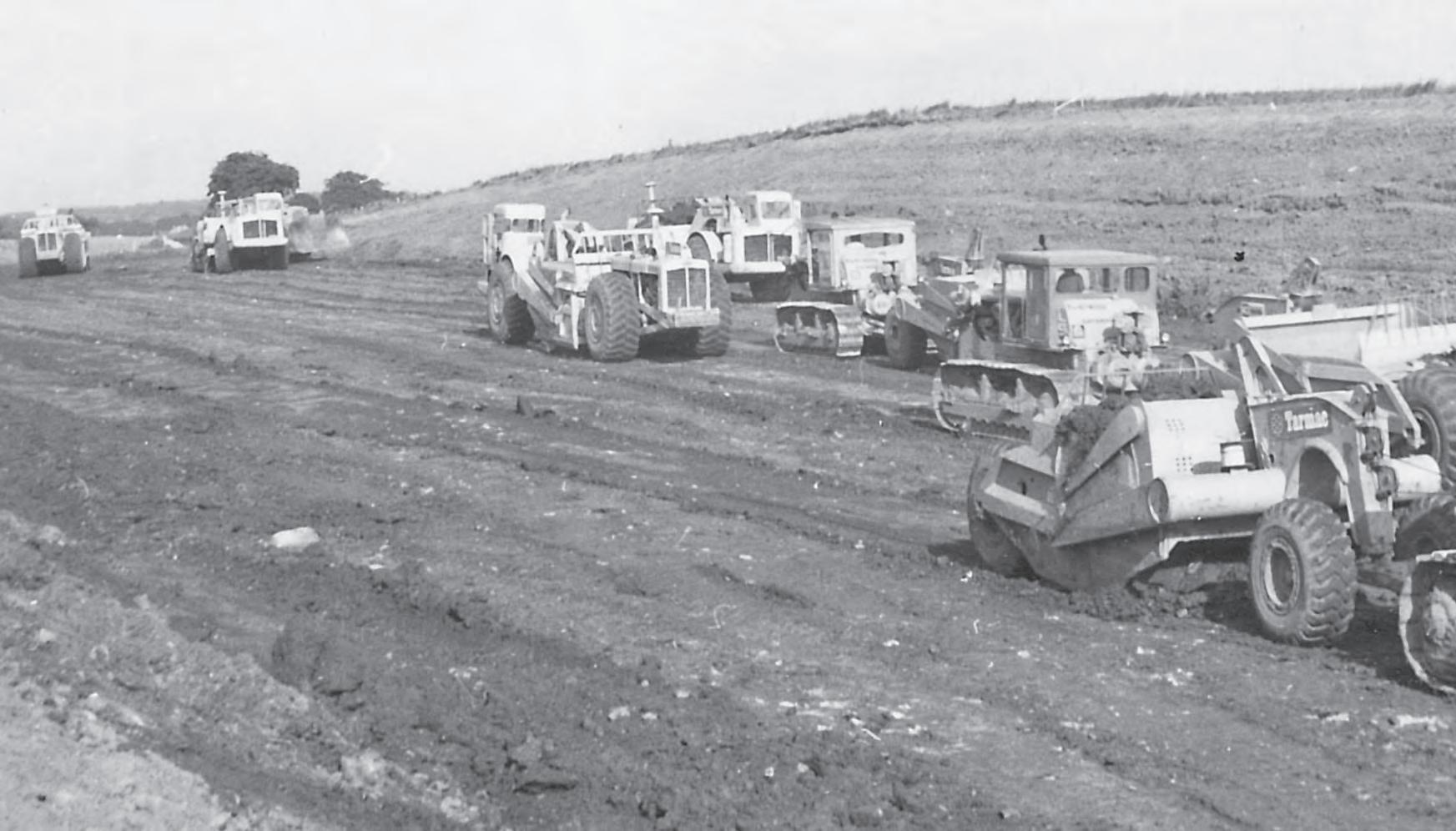
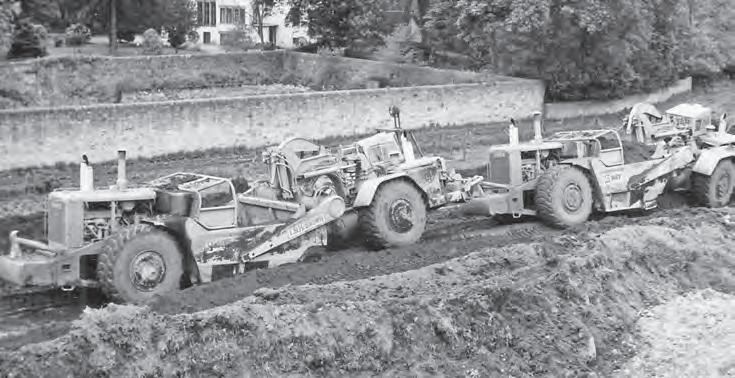
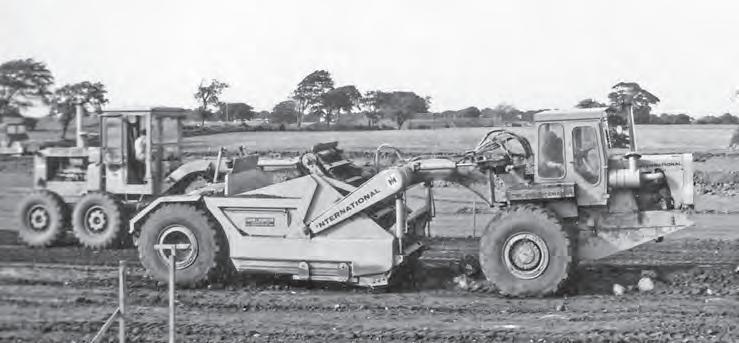
Below: An International E200 elevating scraper was employed on fi nal landscaping duties.
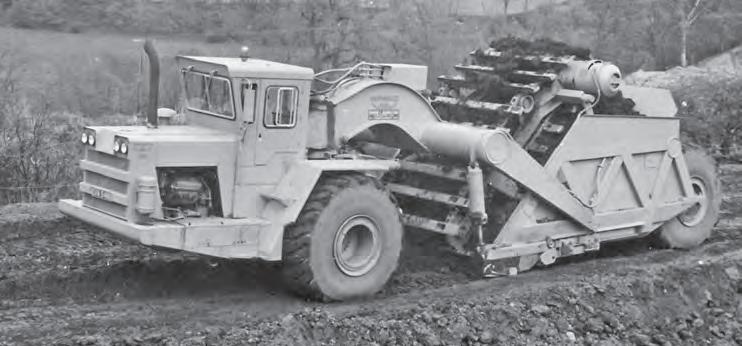
capacity, which on this job were supplemented by a number of hired-in haulers, including Volvo DR860 articulated dump trucks.
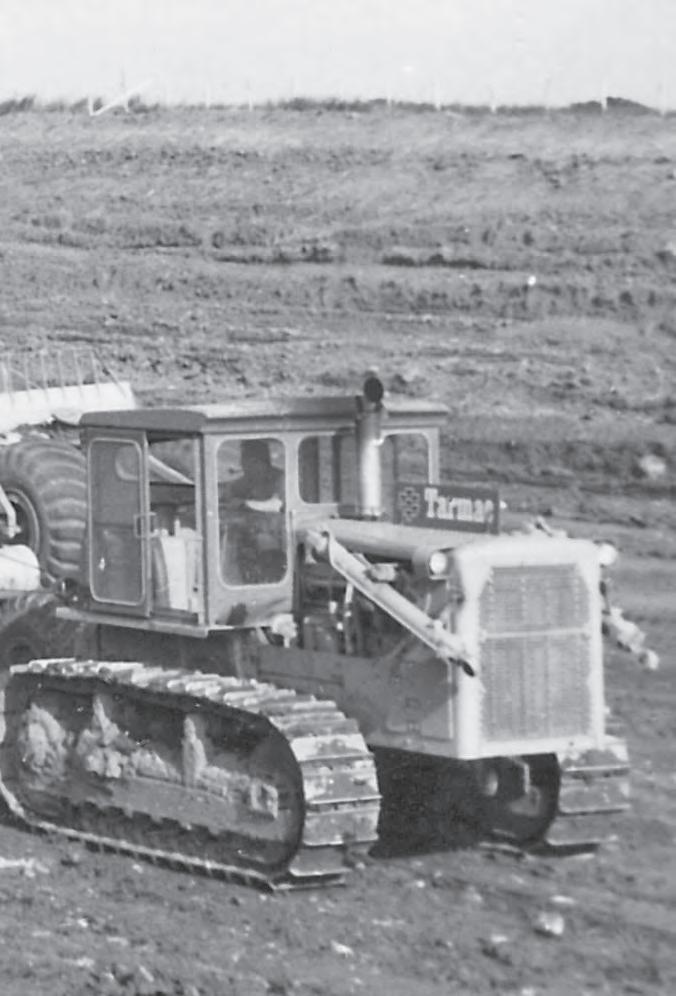
MATERIALS MANAGEMENT
After the surveying, staking and placement of the batter rails had been undertaken, excavation works began. First to move on to the site were the D8 pulled scrapers, to salvage all suitable topsoil. After a stretch of the site was stripped, teams of Terex motor scrapers or hydraulic excavators and dump trucks would haul any suitable fi ll material to the site of an embankment, sometimes over a mile away, or to the nearest tip area on site if it was unsuitable. The topsoil was stored in mounds alongside the motorway easement or on adjacent land rented from local farmers. It would eventually be placed on the fi nal profi les of the cuttings and embankments along the route.
None of the soft wet clay could be used as fi ll on the motorway so several permanent dump sites were negotiated with local landowners. Most farmers were generally co-operative and reasonable, as we could use the material to level an unproductive ravine, or re-landscape part of the farm. In some cases, a borrow pit would be established on land adjacent to an embankment, again these areas were reclaimed and reprofi led to the landowner’s preference.
Profi ling the dump areas for the soft clay material often needed special attention,
Below: Three of AF Budge’s Cat 637s supplemented Tarmac’s scraper fl eet on the M9 contract. The mid-size Wabco C222F elevating scraper was hired in from Gavin Hamilton.

Above: Probably the biggest elevating scraper ever to reach UK shores, this Wabco 333FT could self-load 36 cubic yards in about a minute.
as it could not support the weight of a loaded dump truck. A fl eet of low ground pressure dozers, four Cat D4LGPs and a pair of Komatsu D50Ps, were used to push the dumped soft material into place, often over considerable distances. These dozers were later used for spreading topsoil in the fi nal landscaping stages of the motorway, including on the steep side slopes.
As the job opened up and the schedule intensifi ed, additional equipment was
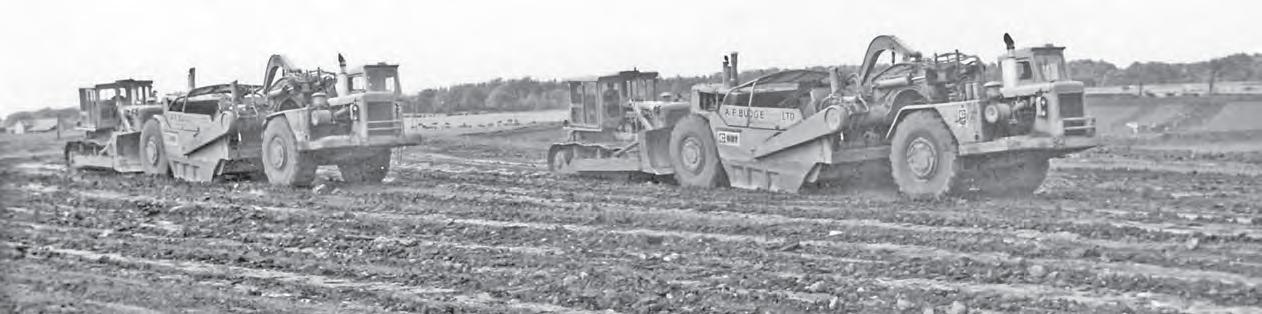

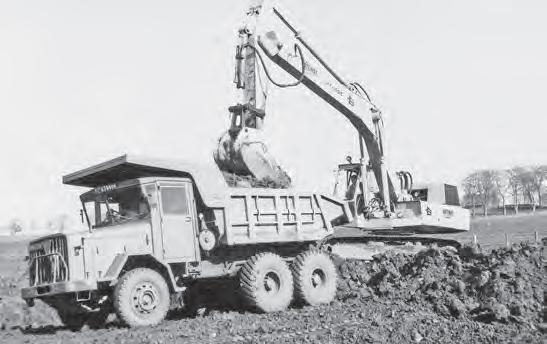
brought-in to supplement Tarmac’s own fl eets. A trio of Cat 637 twin-engine motor scrapers, rated at 30 yards heaped, were hired in from AF Budge, together with a D8 push dozer. In addition, a pair of 20-yard Cat 627 motor scrapers were hired from I&H Brown.
Three sizes of Wabco elevating scraper also joined the team. A motor scraper brand rarely seen in the UK, a 36-yard Wabco 333FT was hired from Stewart Plant, followed by 21-yard C222F and a 9-yard 101F models from Gavin L. Hamilton. Unlike the Terex and Caterpillar scrapers, with the driver’s cab positioned on the left-hand side of the tractor unit, the Wabco cabs were centrally mounted. Although this provided a smoother ride for the driver, its position was not liked, as the machine’s gooseneck blocked rear visibility.
Two small elevating scrapers, an 11-yard Cat 613 and a 9.5-yard International E200 were also hired in from Hamilton, used for utility earthmoving and landscaping works.
MAN MANAGEMENT
General foreman Jimmy Coull kept the earthmoving pace in top gear. He continually patrolled the length of the motorway in his Land Rover, keeping the foremen informed of the constantly changing activities, in addition to keeping an eye on the operators for any signs of equipment abuse, and planning the next day’s activities. A foreman was positioned in the cut to ensure excavated material was removed in an
Above far left: A busy scene near the B903 junction east of Linlithgow. Liebherr 941 excavators and a Cat 977H crawler loader keep the AEC 690 dump trucks on the move. Above: A Hymac 880 and an AEC 690 help with long-haul excavation uneconomical to move by scrapers.
Left: A Cat 14D grader maintained the haul roads and shaped the fi ll areas on the M9 contract.
orderly fashion. He also ensured the side slope batters and excavation depth were formed in accordance with the surveyor’s stakes and profi les.
At each of the embankment dump areas, a foreman was positioned to supervise the fi ll operation, using hand signals to direct each incoming dump truck or scraper to where to dump its load. With a team of D6 and D8 dozers, he also ensured the depth of each layer was placed according to the road specifi cation, and the specifi ed number of passes from the rollers was achieved (see panel). Haul roads and fi ll areas were

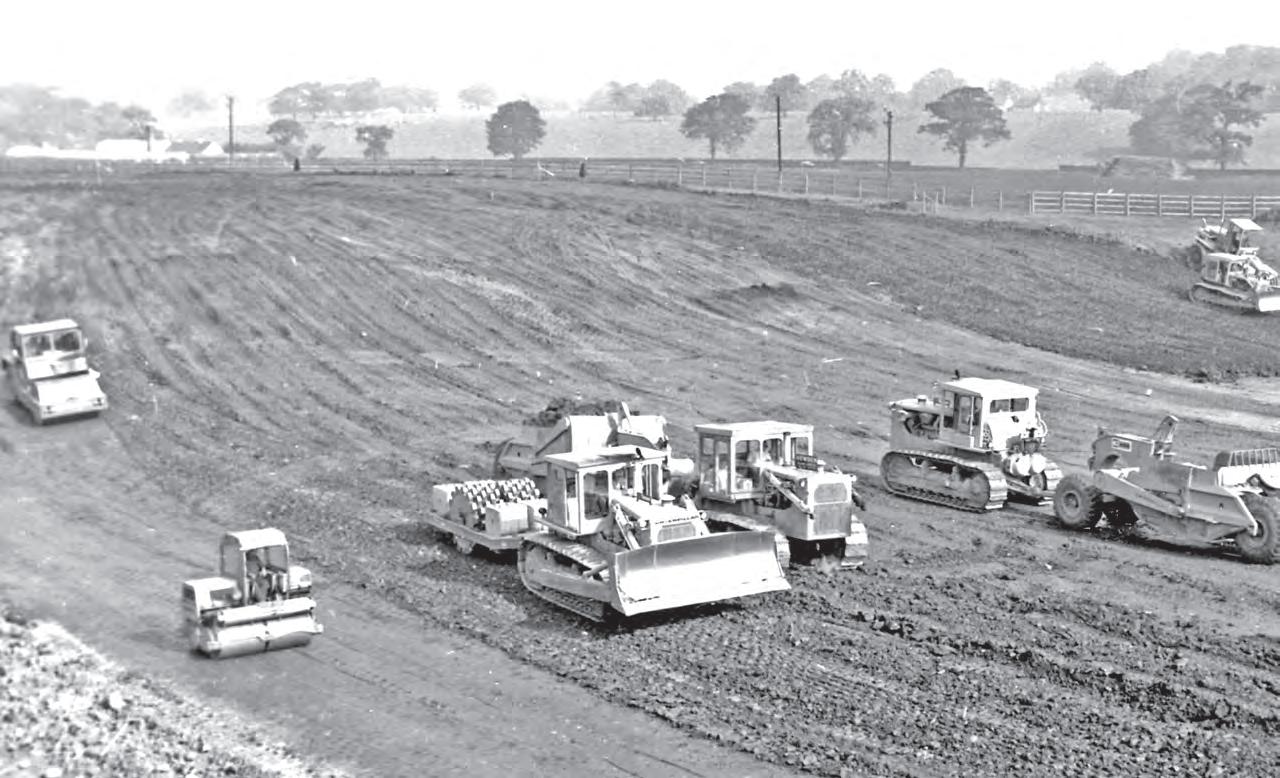
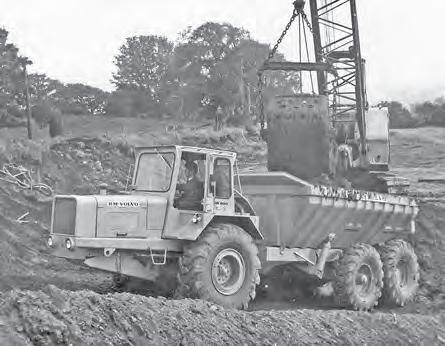
Above: An early Volvo entrant into the UK was this DR860 articulated dump truck, shown on trial on the M9 motorway.
maintained by Cat 14D and Aveling-Barford Super 500 motor graders.
As the route contained a number of new bridges, access along its length was not continuous. The earthmoving fl eet was therefore moved to the next section on public roads, the motor scrapers travelling under their own power, escorted by Jimmy with a Wide Load board on the front of his Land Rover.
In fi ne weather, our working hours were 7am to 8pm Monday to Friday, 7am to 4pm on Saturday, and 8am to 6pm on Sunday, with half-hour meal breaks taken at 11am and 3.30pm. The generous ‘early’ fi nish at 4pm on Saturday and the equally lavish ‘late’ 8am start on Sunday provided those operators that lived within striking distance
“THIS WAS AT A TIME WHEN HYDRAULIC EXCAVATORS WERE JUST STARTING TO TAKE OVER FROM CABLE-OPERATED MACHINES” COMPACTING FLEETS
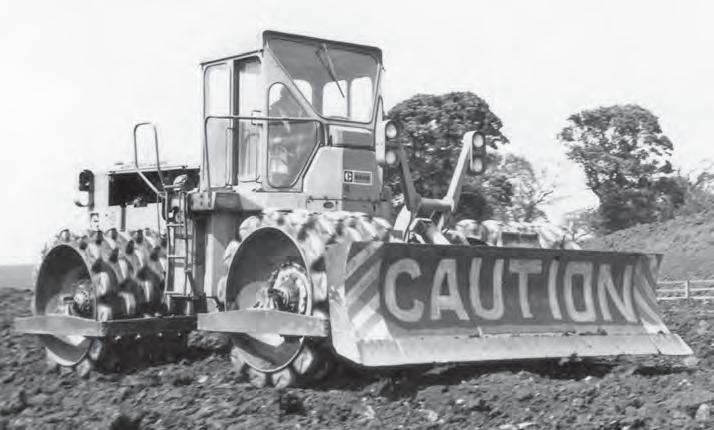
Compaction of the incoming material to form embankments was assigned to a variety of compactors and rollers. The largest was a Cat 824B with tamping drums (as illustrated). Other types included several Bomag BW200 vibratory smooth-wheel rollers, a Bomag KB300 tamping roller, a number of Hyster towed grid and vibrating rollers, together with Aveling-Barford VP single drum vibrating rollers.
A prototype of a Hamm GRW20 roller, complete with its nine rubber tyres, was also tested on site. Equipped with a pendulum device for keeping it level, unfortunately it did not work properly, as it had a habit of frightening the driver by leaning toward the down side of the hill.
At the end of each day, embankments were left with a cambered profi le and the roller drivers paid an extra hour to compact and seal off the surface with smooth-wheel rollers. This paid off in the event of rain, as the surface would drain and dry quickly, resulting in an earlier start when the rain ceased.
to have a night with their families. Most lived in mobile homes, which Tarmac moved from job to job, and connected to a sewer and a water supply, and each provided with Calor Gas heating.
CONCLUSION
Once the earthworks phase was completed, Tarmac’s Roads Division moved in to install drainage pipes along the centre and sides of the carriageways and on the top and bottom of the cuttings and embankments. The motorway was completed by fi nal grading to formation level, placement of sub-base and fi nal asphalt paving.
A striking aspect of this section of the M9 was the soil embankments, which were designed to minimise the motorway’s intrusion into the landscape of the historic Linlithgow Palace. As these baffl e mounds grew, the sights and sounds of construction activity were soon obscured, and quickgrowing grass seed gradually blended the works into the scenery. Visitors to the palace grounds now barely notice the passage of a motorway in such close proximity.
Below: A pair of Bomag BW200 double-drum vibrating rollers and a Bomag KB300 model compact the next layer of an embankment.

Left: From right to left on the fi ll area: dumped material spread by small dozers; dumped material by scrapers; initial compaction by grid rollers; fi nal compaction by smooth-wheel vibrating rollers.
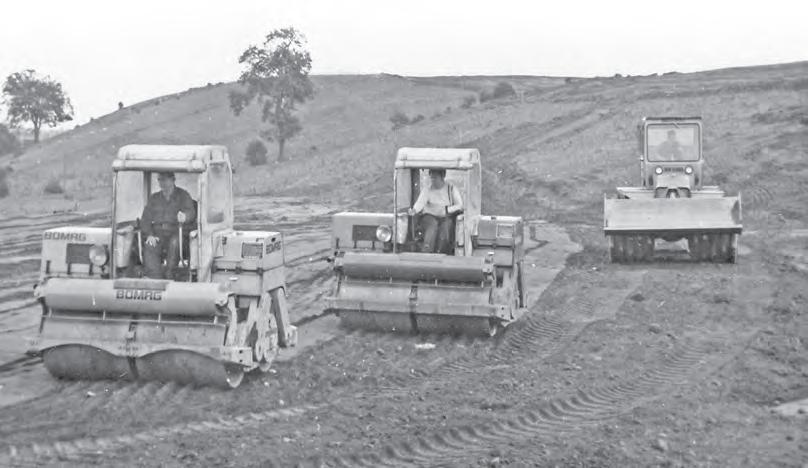