
6 minute read
DEMOLITION
CANADA DRY DOCK DEMO
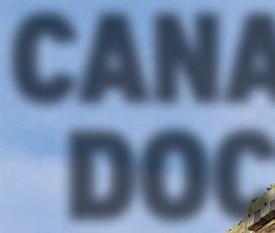
Advertisement
Paul Argent reports on a tricky demolition job on a former warehouse in the Port of Liverpool
he Port of Liverpool extends for
T7.5 miles from the Brunswick Dock in Liverpool to the Seaforth Dock just to the north of the city. The first dock structure was built in 1715, and the site has expanding and developed ever since. Today it is the UK’s busiest west coast port, handling over 35m tonnes of cargo a year.
The businesses located within the port are constantly evolving, and a major project is currently underway on the Canada Dock, adjacent to the new oil terminal. It involves the demolition of an imposing dockside dry goods warehouse, a two-storey reinforced concrete structure 300m long x 40m deep. The arisings from this building are to be processed and used as infill for an old dock, to provide additional land for a recycling business.
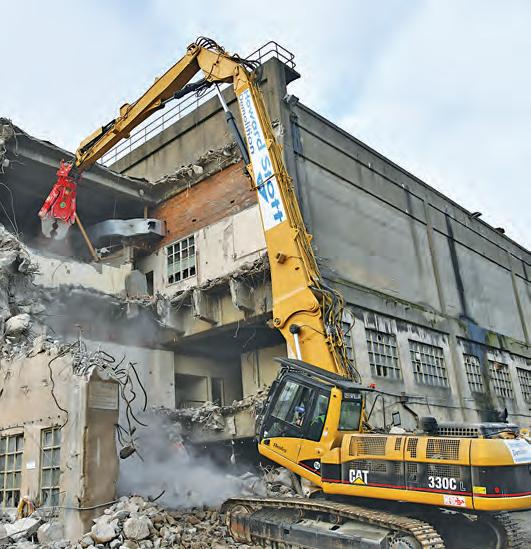
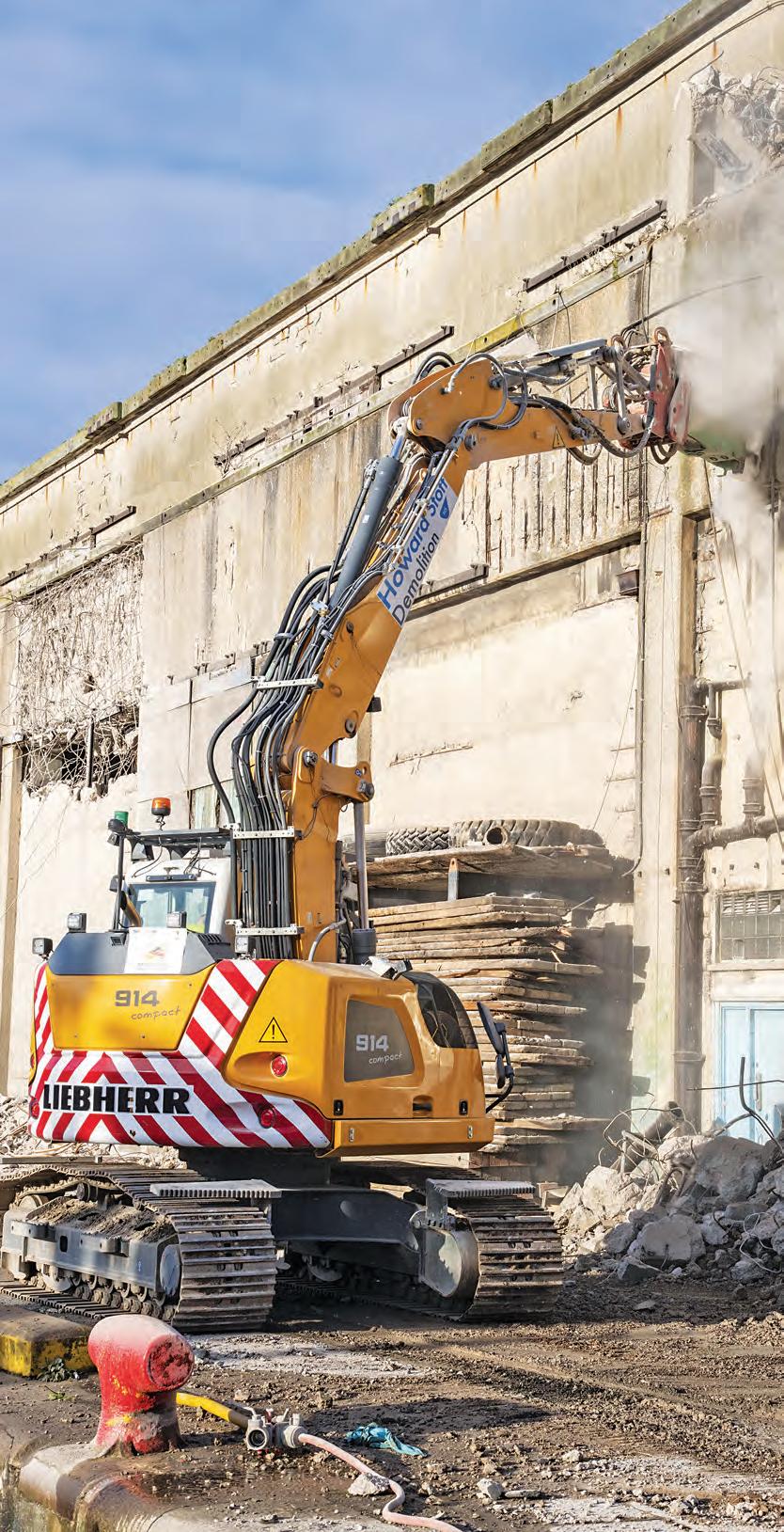
Left and above: The fi rst phase of the project was to undertake protection works for a live substation within the structure, then remove the adjoining three-storey offi ce block.
SITE CHALLENGES
Undertaking the demolition of such a large concrete structure may sound like an inviting project, but working within this dockside environment has presented a number of challenges for Lancashire-based Howard Stott Demolition, which is undertaking this work in a short 12-week programme.
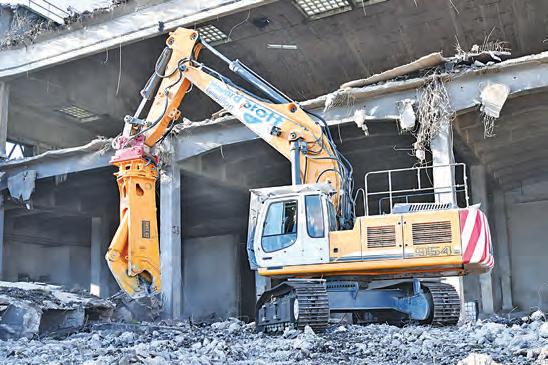
Above and below: The pair of 55-tonne Liebherr demo rigs had a variety of attachments at their disposal, while quick and safe changes were undertaken thanks to their Lehnhoff couplers.

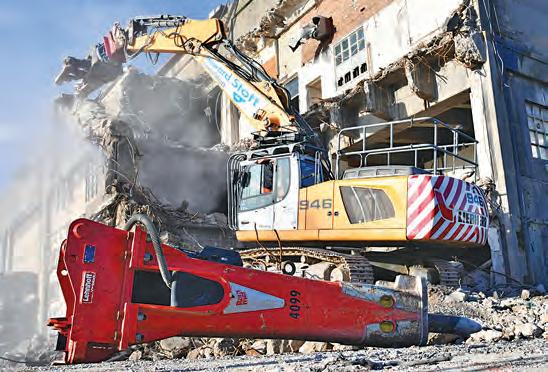
Stott’s operations director Ryan Noon explained, “We have to work around the busy road leading to other port businesses on one end of the building, the new structures being built along one long elevation, and a berth for tugs within 4m of the other long elevation. Oh, and did we mention the electrical substation situated within the building, which stays live throughout the project?
“We do have various issues, these days it just seems to be something that the modern-day demolition contractor has to deal with. We are in the lucky position to have a small and very experienced team who are more than capable of dealing with any such issues promptly and effectively.”
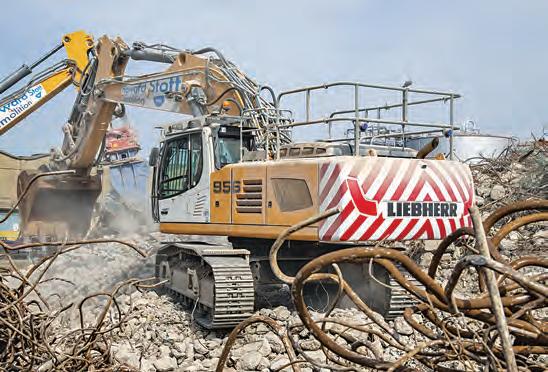
DEMOLITION PLAN
The project is under the supervision of experienced demolition man Keith Healey, and the way in which he calmly approaches the step-by-step demolition of the large structure is a joy to behold. Starting a large demolition project at the tightest point of the site may seem a little strange, but Keith wanted to tackle the live electrical substation first, as it would make the rest of the demolition process safer and simpler.
As the only access is along the dockside towpath, the largest excavator that could be used was Stott’s 17-tonne Liebherr R914 Compact, its triple boom equipped with a Montabert breaker. While this excavator was on the small side for attacking such heavily reinforced concrete, operator Lance Miller soon formed holes in the structure above the substation to allow the installation of temporary works to cover the equipment inside.
Once the substantial protection works were installed, the adjacent three-storey office block was taken down by Stott’s three heavyweights: a high-reach Caterpillar 330C and a pair of 55-tonne Liebherr demo rigs, a 2019 R956 and a 2011 R954. With this removed and this corner of the site opened up, the team could turn their full attention to the 400m-long, two-story warehouse itself.
The main structure comprises 17 cast-in- situ arched roof sections sitting on large post-tensioned concrete beams running the full 40m width of the building. Each of the beams is supported by two external columns, which run through the heavily reinforced first floor. After decades of exposure to salt-laden sea air, Mother Nature should have given the demolition team a head start on this old structure.
Keith said, “We were hoping that the steel reinforcement would have corroded and blown the concrete. Unfortunately, this isn’t the case and we are finding that it is probably some of the hardest material we have dealt with.”
The operator of the high-reach Cat rig has a Montabert breaker and Verachtert concrete muncher at his disposal. The first task is to remove a section of the arched gables of the cast-in-situ roof, leaving the end of the roof unsupported. The first-floor walls are then removed, exposing the column and beam structure. They are cut to allow the roof to collapse on to the concrete first floor structure below.

PROCESSING CHALLENGES
Once the main structure is down, the pair of 55t Liebherrs are called back in to process the concrete and steel into lengths
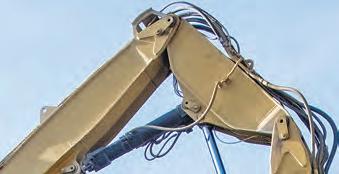
The main warehouse is 300m long x 40m deep; its beams and columns are constructed from heavily reinforced tough concrete.
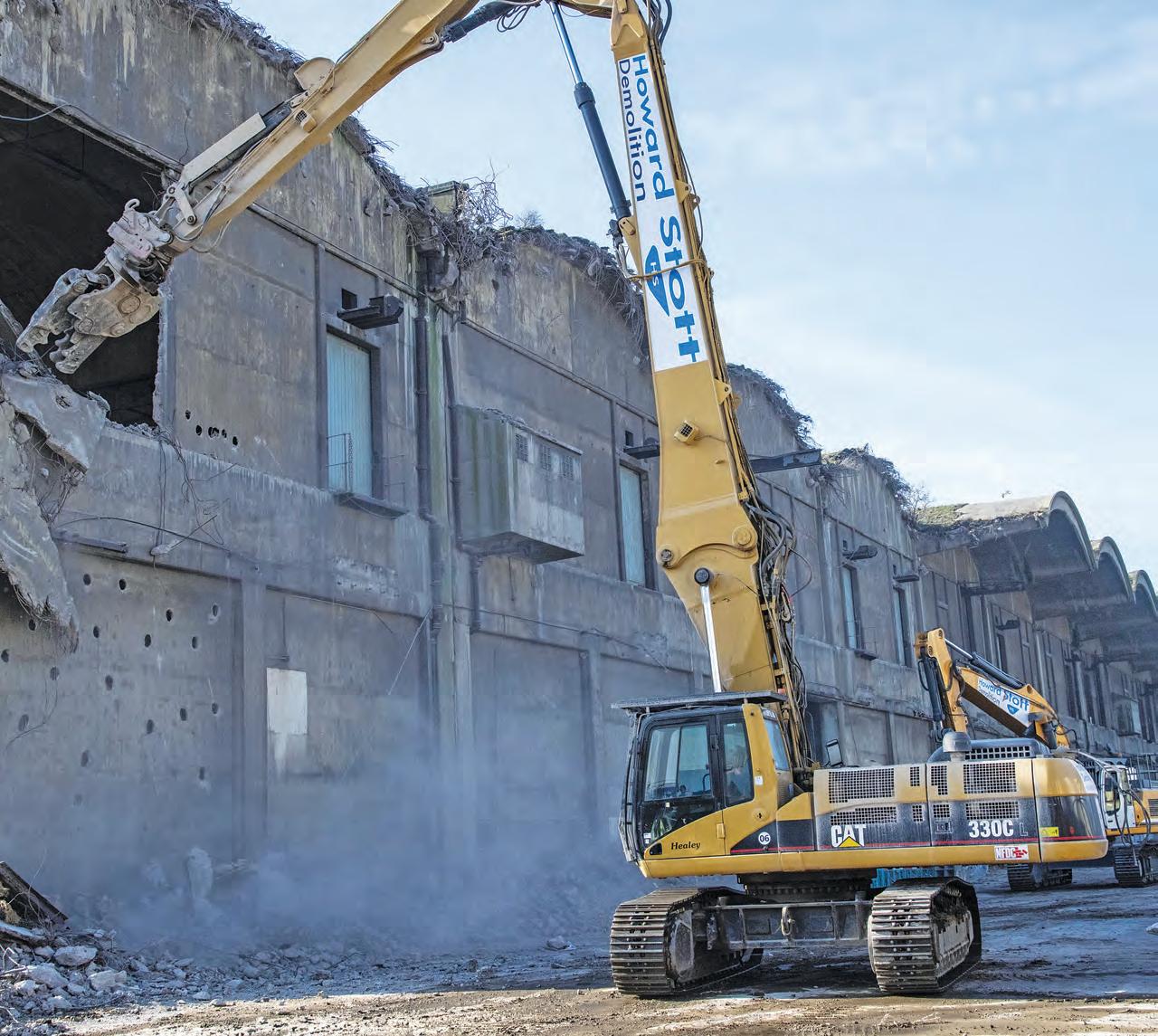
no longer than 10m. Keith explained, “Our client is processing the material down to their specification. It makes for a quicker job for us, but means we have to drag some very heavy beams out of our way for us to carry on working.”
In addition to being made from extremely tough material, the scale of the beams – both their dimensions and weight – proved to be an issue. Even Stott’s largest concrete cracker attachments could not despatch some of the structural elements without them being pre-weakened.
The working method adopted was to use large Rammer hydraulic hammers to reduce such over-sized elements to allow the crackers and munchers to get a grip of the concrete structure. While the rebar cutters in these attachments are more than capable in normal circumstances, the team found rebar almost 50mm in diameter within the beams.
To tackle this Keith brought in a veteran Trevi Benne shear and mounted it on the R954, commenting, “We may end up using a set of blades, or even two, on the job, but the speed at which we can cut the rebar will be increased massively. There certainly wasn’t a shortage of concrete or rebar when this building was put up.”
All the larger machines on the Stott fleet feature Lehnhoff automatic hydraulic couplers, allowing the operators to quickly change attachments from the safety of their cab, as Keith commented, “They are a godsend, but you have to make sure the mating faces are kept clean. We try and keep everything looking and running well. The kit is all looked after and wants for nothing and, despite the age of the high-reach and the R954, they look as if they have only done a minimal amount of work over the years.”
This warehouse is one of the last old storage structures within the Port of Liverpool. Its removal will signal the start of a new life for this part of the massive site.