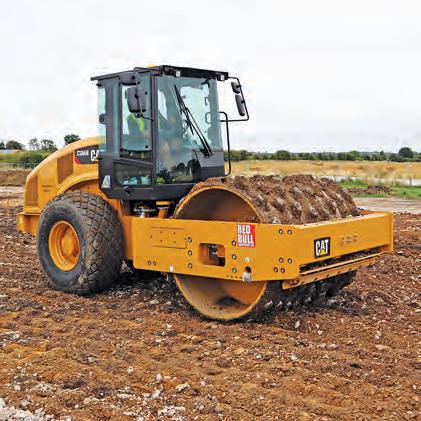
10 minute read
SITE VISIT
PROVING AUTONOMOUS VEHICLES
Peter Haddock visits a fully connected site in Buckinghamshire, which is going to be the first UK proving ground for autonomous vehicles
Advertisement
he challenges of introducing
Tfully autonomous electric vehicles on to our roads are not under-estimated, as the latest development is the construction of the UK’s first dedicated proving ground for such vehicles. It is based on a former World War Two airfield at Oakley, near Aylesbury in Buckinghamshire, where the main phase of the track is due to be opened in spring next year.
The groundworks, on behalf of the Spanish-based client IDIADA Automotive Technology, are being undertaken by local earthworks contractor LF Pearce & Son. Founded in 1937, the business is now run by grandson Derek and is based just a mile from the site. Following the successful completion of some enabling works, including establishing access roads and forming a 2.2km bridleway, Pearce obtained the contract for the three-year project.
FULLY CONNECTED
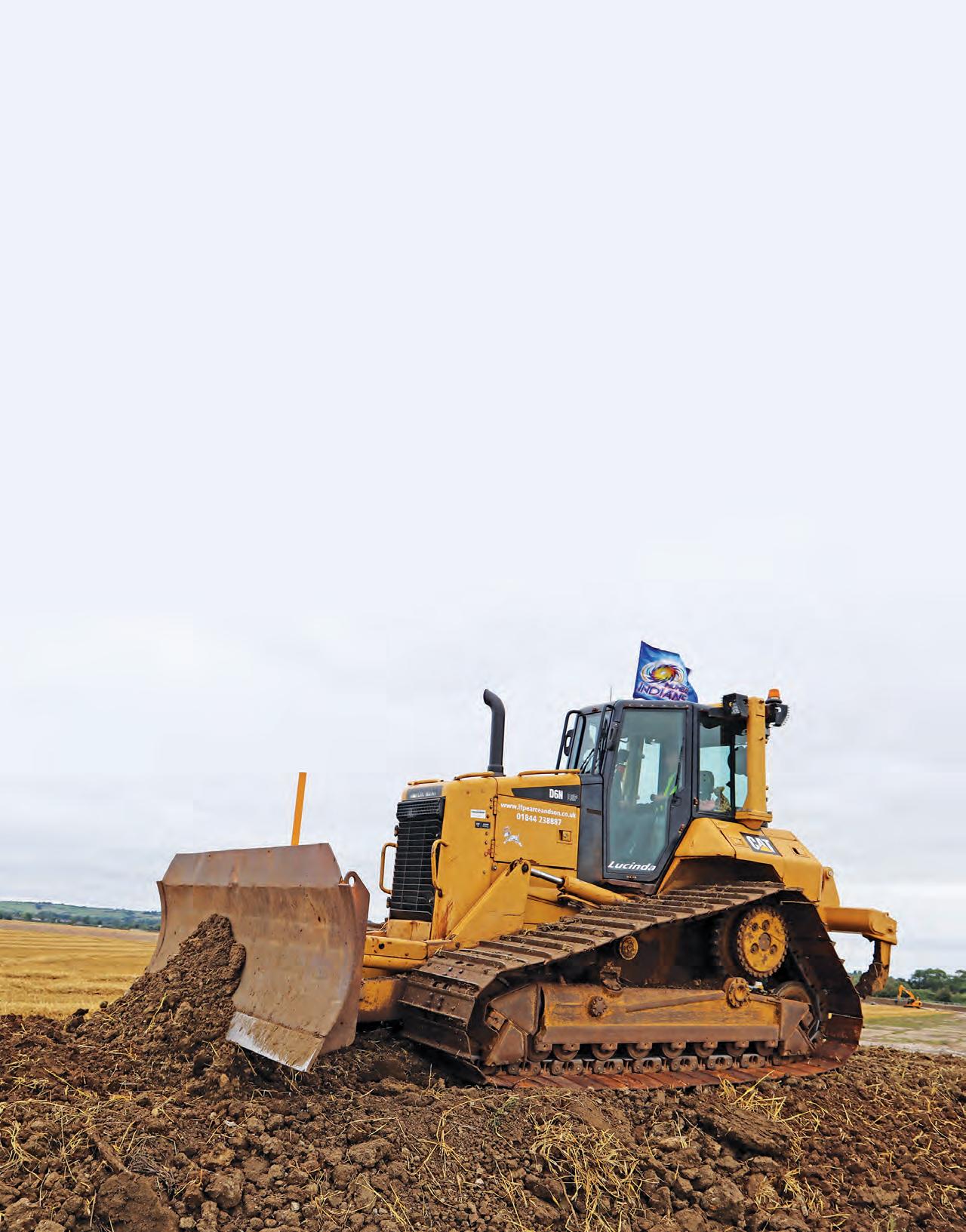
For many, the concept of autonomous road vehicles is something from sci-fi movies. A decade ago, the same would have been said about how this complex project is being managed, particularly as the client’s detailed requirements evolve over time. Derek said, “The project itself is being delivered by our fleet of Trimble 3D-enabled equipment, including JCB excavators and Caterpillar dozers. We are using a complete 3D site model to create the road layouts that a vehicle will have to navigate, reflecting what drivers would experience in the UK.
“This means we are preparing the site to create everything from alternating cambers, roundabouts, flyovers, straights and a spaghetti junction-
Below and inset: As much material as possible will be re-used on site, building up the levels of a former wartime airfi eld to a vehicle test track.
style road layout. These different road set-ups will be used to test the performance of a range of different autonomous EVs from cars to trucks. The challenge on-site is the ever-changing design of the project, as the team picks up on new requirements for testing, which are being asked for by the authorities and car manufacturers alike. This is why it is being constructed in


phases. The outer track will be completed first, and the inner sections comprising a spaghetti junction design, roundabouts and flyover following.”
To create the wartime airfield on this 200-acre site, which has been farmed for the past 80 years, the earth was simply pushed to one side and thick concrete used to form the runways. To reduce or remove these robust concrete runways, a specialised motor breaker was used – further details in panel overleaf.
Derek continued, “When you look at the site itself, you have a variety of materials to move, remediate and reuse. For example, the farmland is quite easy to soil strip, cut and fill. But around the runway itself is a challenge, with some really horrible clay mixed with all sorts of bricks and bits of concrete. If we were to remove and remediate this, it would blow the budget and take too long to complete. This is why we have used 3D design to support the best use of material movement, labour and the reuse of the existing base layers of the concrete runway.
“As the first proving ground to be built in the UK in 50 years, the design team have gone all out to make this a world-class facility. This creates its construction challenges, which can only be delivered using 3D machine control. For example, we are dealing with cross falls of up to 8% and down to 1%. There are banks into corners where we see material fill of up to about 1.2 metres, which is proving very interesting. To keep costs down, we have engineered a number of ponds, extracting the right grade of material to create the surfaces, drastically reducing the need for imports.
“Using 3D to guide our operators, we are not over grading or digging and moving material to the shortest whole route. And because we have a whole site model, our operators are able to work autonomously, as there is no setting out required.
SITE WALK-ABOUT
The west section of the project has been completed. Tarmac has carried out the surfacing works using the same 3D site model to lay the pavement. As part of this collaborative process, the Pearce team constructed a network of fixed mounting points for Trimble base stations, to enable the Tarmac machines to work to millimetre accuracy.
Derek continued, “We deliver a graded surface that is 330 millimetres off the finish level. Tarmac then comes in and lays a 100mm of type one with a paver, adding a base and then surface asphalt finish level on top. For key track areas, there is a need for very high accuracy, which they are able to achieve using the 3D model.”
On part of the east section of the site a GPS-equipped JCB 150X excavator, complete with a Steelwrist tilt-rotator, was being used to shape the trickier sections of
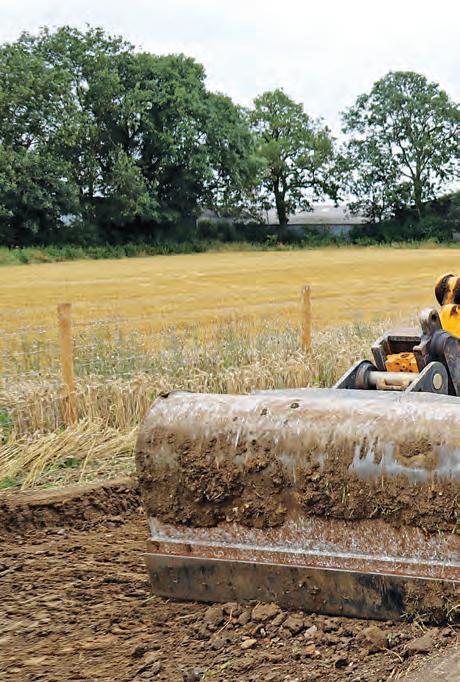
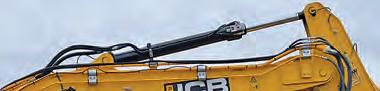
Left, far left and inset: A GPS-equipped JCB 150X excavator with a tilt-rotator is used to form the more complex shapes and to prepare the sub-base of the former runways.
Above and below: A pair of GPS-equipped JCB 220X excavators have been added to the fl eet to deal with the more intensive work on site.
cambers and bunds. Every piece of plant on the fleet is named and this one, called Poppy, was being operated by Will Squire, assisted by his dog Maisie.
Will was unfamiliar with Trimble machine control before being fitted at the beginning of this year, but has clearly mastered the system, adding, “You just can’t deliver this project without the model in the machine, as every section is different and demands high levels of accuracy. Even though we are working on a big site, we also have to work closely within the boundaries to ensure we make the most of the space for the client, so having a tilt-rotator makes the job very simple.”
In addition to bunds and shaping sections of the track, Will also uses the 3D model to level off the base layers of the runways, using a riddle bucket to remove the oversize material. This makes it easier for the roller team to compact the surface, for which a Cat CS66B has been hired in from Red Bull Equipment.
For the larger sections of the project, Derek has invested in a pair of new JCB 22-tonne excavators, named Penelope and Louise, as he continued, “The 220Xs are much more suited to grading large areas of the site, ripping out vegetation and managing the ponds and water runoffs. They are also tasked with loading the ADT fleet, which we have sub-contracted to Moore Transport. We work with Moore because it’s a fellow family-run business and they provide a really good service with some great back-up. For this project, they are using their Bell ADTs to help us move material around the site, which we are then grading with our new-to-us Cat D6N, which we call Lucinda.
“Because we look after all of our own kit and know the Cat dozers very well, we look to purchase second-hand machines,
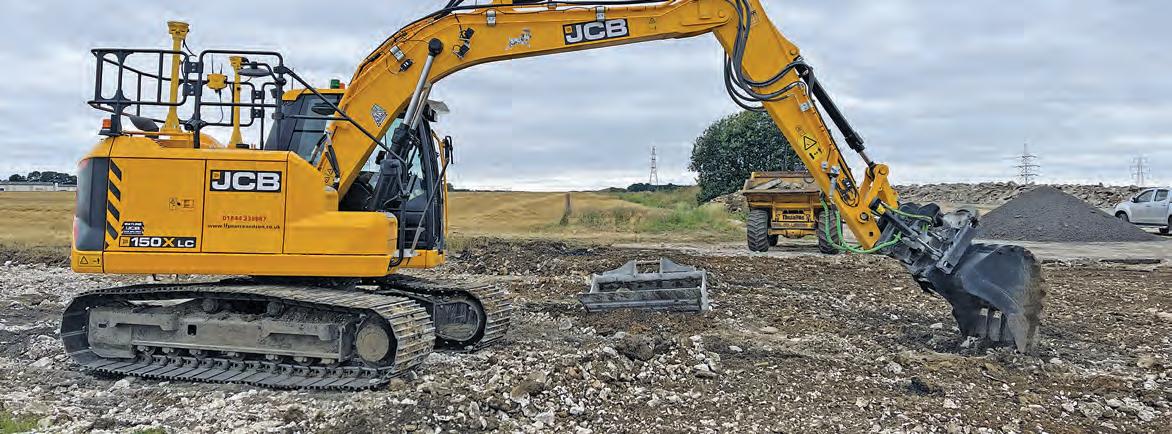



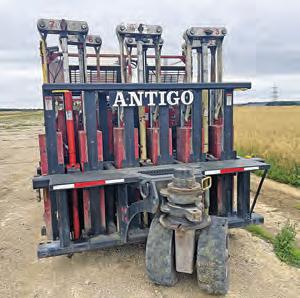
as they are very expensive to buy new and the waiting times are also prohibitive. We recently purchased Lucinda, having sold our previous dozer named Lucy through Ritchie Bros, as we felt we had got the most out of this particular machine. We were fortunate to drop one dozer off and pick the other one up on the way back, which was very cost-effective transport-wise.”
At the time of our visit Lucinda and Laura, another of the firm’s D6N dozers, were roughly building up the next section of the works to be tackled. Both are plug-and-play ready to use Derek’s existing Trimble GPS receivers and in-cab control monitors. He commented, “I tend not to keep the kit on the machine as it is a remote site, so we lock these items away when not needed. As we are growing the connected fleet, we can hire in or buy new systems as and when we need them.”
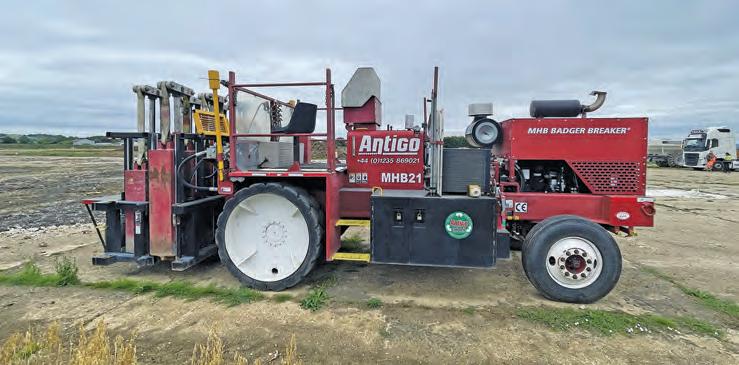
CONCLUSION
Perhaps one of the most surprising aspects of this site visit was the assumption that Derek and his team had many years experience of using cutting-edge earthworks systems, which is not the case. Derek largely taught himself how to manage the 3D model changes and workflow on the Trimble Business Centre cloud-based software.
He continued, “Using online tutorials and other videos I came across on the web, I learned how to do all the changes myself, along with our office manager Olivia. To ensure we were using the system properly, we also got some on-site training from dealer Sitech and we haven’t looked back since. I probably go back to the model and make changes on average every two to three weeks.” This family-run business clearly impressed the client during the enabling works for this project. Their can-do attitude and a willingness to learn new skills have helped them win this prestigious contract, which is being managed internationally in real time, thanks to the use of digital 3D site models.
Derek concluded by saying, “What is really great is how we have been able to work as a team to make even more from the software. For example, the dozer and excavator operators now know how to take and record measurements of work carried out, like marking the bottom of a trench by saving a reading of the bucket position on the tablet. Having this information allows us to update the client team at IDIADA Automotive Technology with as-built models. This has proved to be very useful, as the team is actually based in Spain and they can see the progress of the job and understand what has been achieved in the project’s programme. It also adds an important layer of transparency, as with all jobs that change over time, there are always going to be cost and time variables associated with delivery.”
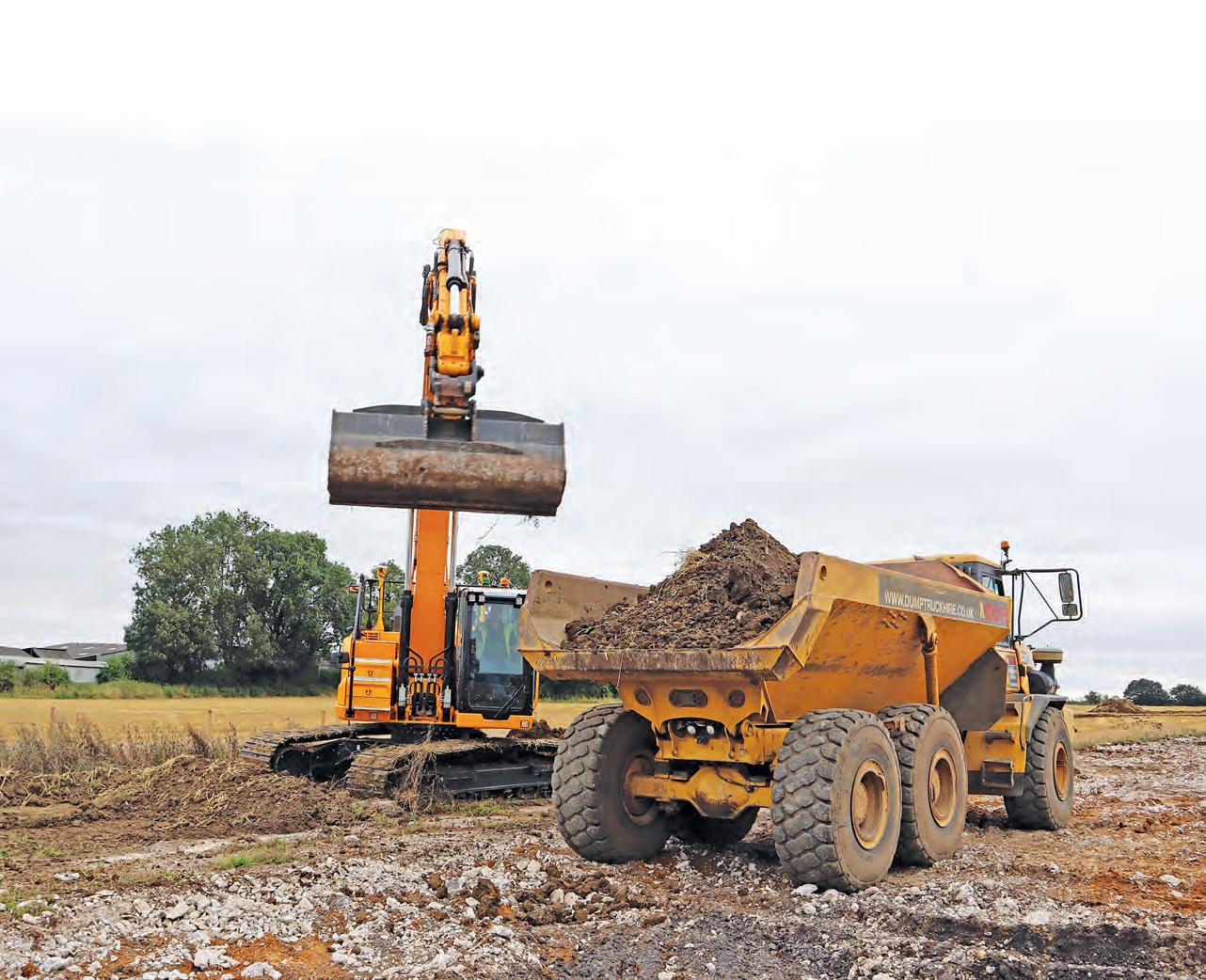
Below and inset: A self-propelled, rubber-tyred MHB21 Badger Breaker was used to reduce or remove the concrete runways.
MOTOR BREAKER
A key part of this project was turning wartime runways into rubble as cost eff ectively and quickly as possible. Antigo Breakers was brought in to deal with material using its MHB21 Badger Breaker, a self-propelled, rubber-tyred multi-head concrete pavement breaker.
Derek commented, “The unit itself carries 1200 to 1750lb hammers, mounted laterally in pairs. Half the hammers are in a forward row and the remainder diagonally off set in a rear row. Each pair of hammers is attached to a hydraulic lift cylinder, which operates as an independent unit. It develops between 1000 and 8000ft.lb of breaking energy, depending upon the lift height selected, and cycles at a rate of 30 to 35 impacts per minute. This allows for continuous breakage of concrete from side to side, as it travels up and down the airfi eld.”