Haulier NEWSLETTER
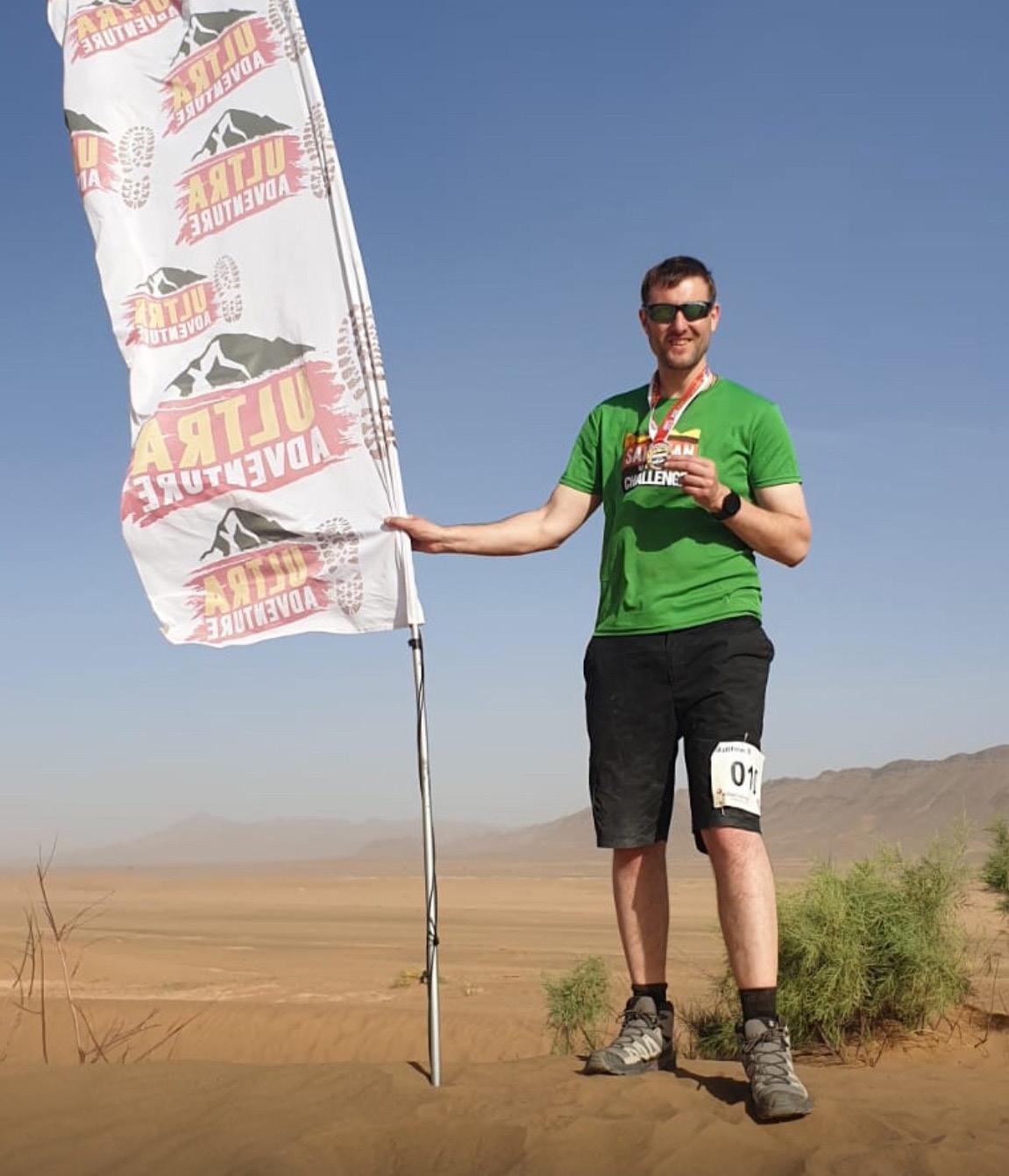
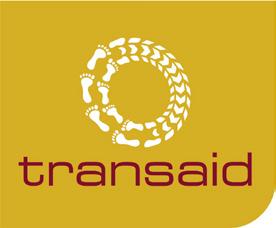
Bayston have had lots of changes over the past few months and site management have been keeping a close eye on the road conditions around the quarry.
The Quarry access road pass the new asphalt plant has now been asphalted giving a very good surface for trucks going to the Type 1/6F5 piles and towards the washed chippings plant.
Further changes to the VPMP will occur over the coming weeks.
Thank you to those drivers who have raised safety observations and site management for controlling the situation during a difficult time.
A concerned haulier stepped in with regards to 2 external 3rd party wagons tandem tipping in Coxhoe stockyard.
It was the understanding that the wagons were instructed to go to the stockyard and report to the shovel driver; they were told not to tip until this has been done.
The shovel was refuelling at the plant and the wagons tipped without the shovel being in the area and rightly so, one of our ICH flagged this as an unsafe act.
This is an excellent example of how our hauliers can be an extra set of eyes within our operations and help us operate safely.
The team at the plant have been given a refresher of the potential consequences of tandem tipping and other safe tipping protocols and will brief this out to all hauliers entering site with particular focus on 3rd party.
One of the Scottish hauliers submitted an observation to let us know there were no maps issued for a nightshift job. Tracy our Transport Account Manager reacted immediately to send the maps over to the hauliers for that night and we then followed up with the distribution team in Birtley.
The maps had been issued on Monday for the full week, they needed to be issued every night to account for changes in hauliers/drivers. So this has now been amended in process.
RMX driver delivering to a customer site in Sheffield reported an unsafe condition on a customer site where adequate exclusions hadn’t been put in place around a manhole cover. This was reported and resolved with the customer.
SOURCE Logistics N&S
DISTRIBUTION All Hauliers
DATE – October 2024
Detail:
A Contract Haulier was delivering to a customer site and instructed to reverse towards the paver by a member of the customer’s gang. Working near to the paver but not in the path of the reversing truck was a gang operative who was using a pedestrian single d rum roller on a strip of asphalt laid earlier in the day. The Haulier reversed towards the paver as instructed . As the truck reversed adjacent to the operative, the operative, unaware of the reversing tru ck, stepped backwards directly into the path of the truck and his left leg became trapped under the rear wheels. Following the incident, the operative was air lifted to hospital and underwent surgery for injuries to the leg and remains in hospital.
While the investigation continues the following facts can be confirmed at this stage:
Key Factors:
▪ The haulier was instructed to reverse towards the paver by a member of the gang
▪ No banksman was provided to control the reversing movement of approximately 100m.
▪ The haulier did not use the guidance when no banksman was provided in either the STOP/GO Card or MPA Haulier Handbook.
▪ The operative was working adjacent to and with his back to the path of the oncoming truck.
▪ The haulier had not carried out the required pre-start checks on the truck and did not detect that the audible reverse alarm was switched off from a previous shift
▪ The operative stepped backwards directly into the path of the truck.
▪ All Hauliers are to brief their drivers, face to face, on the incident using this alert and remind their drivers of their obligations to ensure their vehicles are operating safely and meeting Tarmac’s minimum standards at all times.
▪ Hauliers are to ensure that the required pre-start vehicle checks are being carried out and recorded with any defects being recorded and actioned.
▪ Particular attention should be made to ensure that the truck’s audible reverse alarm is working.
▪ All Hauliers are to remind their drivers to use the STOP/GO Card if they have any concerns about site conditions or controls, do not proceed onsite and contact the Transport Team for support
Safety is Tarmacs Number 1 priority.
We want to ensure everyone working with us goes home safe, as no one should get hurt whilst being at work.
Your observations are vital to safety improvements, and we have many ways these can be reported by:
• ePOD
• Apps
• What’s App
• Phone Call
• Near Hit Pads
• Speaking to site management
These are ways that are still available, but we have listened to Haulier and drivers feedback on these processes and have developed a QR code where you can report incident along with photos and this goes directly onto Tarmac safety system, and you will receive feedback.
Unsafe act/ condition
This shows an unsafe conditionno brick-guard and bricks unstable near the edge.
Note: the bricks were poorly stacked by someone in the first place and/or the brick-guard was removed (unsafe act).
Near miss
incident
This shows a near miss - the falling bricks didn’t cause any harm as they didn’t hit the person or cause any damage, but they did fall so they could.
Here the bricks hit the worker causing harm (in this case an injury). They could equally have caused other types of harm e.g. damage to equipment, loss of product (including the bricks).
Minimum course length halved from seven to three and a half hours.
The revised DCPC still requires 35 hours of training but now that the minimum course length has been reduced from seven hours down to three and a half hours, it will make scheduling training less burdensome for drivers and operators, while ensuring training material is focused and relevant.
Thank you to everyone for your support with the tablet switch over. Everything went relatively smoothly 1 or 2 small issues, but these have now been resolved. Thank you again logistics team.
Below are some of the issues we seeing through our Haulage Help desk and via our Transport Account managers with ePOD. We will continue to monitor and resolve any issues that are raised.
• Leaving bridge before receiving a ticket
• Multiple log ins - Will cause tickets to autocomplete as picks up two locations
• Not logging out at end of shift - Will stop any updates coming through
• Do not use back button (will reset any times recorded)
• No location turned on device - Unable to track and may result in non-payment of any time on site.
Vision Techniques are the innovative driving force in vehicle safety and security systems, protecting not only vehicles but also the lives of employees, the public and the environments they operate in.
The company has evolved into one of the UK’s largest vehicle safety and security equipment providers, supplying across a wide range of industries including construction, waste management, quarrying and mining, agriculture and blue light.
Loved by some of the largest fleets in the UK, Vision Techniques’ products are influencing and changing safety and security standards across industries daily.
Vision Techniques award-winning system, Brakesafe, is just one of their products helping to keep both drivers and vulnerable road users safe whilst on the roads.
The system is a fail-safe automatic braking system. Should the driver exit the cab without applying the vehicle park brake, the system will automatically apply the brake on their behalf, eliminating the risk of a vehicle runaway.
It offers instant protection, an audible alarm, is failsafe and is also VCA approved.
It is also autonomous so there is no need for driver interaction.
The system has won a range of awards since it came to the market including the Motor Transport Award, the CIWM Award and the Commercial Fleet Award.
Don’t risk a runaway, get the VT Brakesafe System installed now.
The challenge was a double Marathon in the Sahara, and was completed as a combination of personal challenge, and fundraising challenge. The fundraising was on behalf of Transaid - a Tarmac logistics nominated charity that Matt and several others are attempting to raise money for over the course of this year. Gareth Banks - who recently did a challenge cycling across Kenya - is part of the fundraising team and did that for the same reason.
Matt was part of a team of 30 people (plus support staff) all taking part for various reasons. They were initially flown into Marrakech, where everyone spent their first evening getting to know each other, before then travelling 8hrs by minibus’s to base camp the next day. Everyone stayed in this camp for 3 days and nights.
For the first marathon everyone was dropped off 26 miles away from the base camp, and then had to make their way back to it. The next day they completed the second marathon - starting at base camp and moving 26 miles away from it to another temporary camp, where everyone was collected by minibus and driven back.
Matt and the group moved through a combination of dry scrubland, local villages, main roads, and then finally, the desert itself (with a brief, but very strong sandstorm). Temperatures were in the high 30’s the whole time, with little shade anywhere. The whole challenge was extremely demanding, but immensely rewarding, and the whole group looked out for one another and bonded really well - a fantastic example of “one team”.
Matt and the group finished the challenge on the last night back in Marrakech, where they got to explore the city a little before heading home.
The link for the GoFundMe page set up is below. The link is still open, as Matt is looking to raising money for the year, so even though he has finished the challenge, people can still donate. Rather than purchasing a coffee, why not donate this to Matts go fund page for a challenge that deserves to raise as much as possible.
To donate, click on Matt’s GoFundMe page.
Leading up to Christmas it is very important that we remember the following Tarmac Policy
Tarmac has a zero tolerance policy when it comes to both drugs and alcohol, and we are continuing to increase random D&A testing across the country following an increase in the number of failures.
210 deaths caused each year from drink driving
80 deaths caused each year from drug driving
x2 increase in the number of deaths and serious accidents due to drug driving in the last 5 years
13% of all road related deaths are as a result of drink driving
It is vital that everyone is aware of the risks of driving under the influence and the importance of making the DVLA and your employer aware of any prescription drugs you may be taking that could affect driving.
5% of people failed a breath test following an accident
85,000 people are convicted of drink related driving offences every year
40 days - the length of time some drugs could remain in your body and be detected by our testing process
The Progressive Safe System furore over conformity and arguing over ‘fit for purpose’ technology has died down now. And so too has the rush to apply for the grace period which was open to London Road users up until October 28th 2024. This date has now passed, and the grace period can no longer be applied for.
Now, it’s all about making sure any outstanding vehicles are fitted with the necessary technology by
midnight May 3rd 2025.
TrafficAngel has a YouTube video explaining all the TfL intricacies, headed up by Odri (right) who also has her own desk and busy telephone dealing with the many customer queries and fleet managers confused about the exact procedure to continue to drive without being fined.
Full PSS requires a left turn alarm, AI camera or radar system, a minimum 7 inch screen giving an uninterrupted nearside side view and the correct rear signage for rigid vehicles. The upgrade PSS fitment presumes the vehicle has the original DVS system already installed which is then supplemented by the latest AI technology.
TrafficAngel spent a great deal of time researching and developing the best PSS technology to fit, deciding on AI cameras. That decision was based on the following logical processes: 1) ease of use for the customer, 2) ease and speed of fitment, 3) ignition and earth the only connections required (thereby avoiding CAN and other sensitive electronics in the vehicle), 4) overall reliability of the system, 5) factory-fit looks.
And TrafficAngel is delighted to report customers are already telling us how our system has avoided serious pedestrian collisions and has even saved lives. Another key benefit of the TrafficAngel PSS when driving in London is the sound of silence! Drivers are telling us how much quieter their day is now the constant unnecessary bleeping has been removed from the cab!
And it was this constant aggravating audio distraction that was the ultimate driving force behind the TfL drive to upgrade these safety systems. The old-style sensors would bleep at anything within a certain distance of the vehicle leading to driver complacency and ignoring the audio warning when the bleeping really mattered!
To enquire about our fully-certified TrafficAngel PSS and staged payment scheme, do call us any time and visit our brand new website at www. trafficangel.co.uk We also offer full HD recording, live drive 360 degree vehicle monitoring, 3-8 cameras, light bars and beacons, audible external warnings, audio-visual reversing sensor systems, and all our kit fully protected from the harshest of conditions, particularly the concrete and tarmac environment. And if you want any recommends from satisfied customers, we can offer that too. Call TrafficAngel today on 01825 768555 and let us take your PSS headache from you!
GETTING FROM JOB TO JOB IS A CHALLENGE. MICHELIN CONNECTED FLEET HAS A RANGE OF TOOLS TO HELP YOU KEEP COSTS DOWN AND MAXIMISE YOUR PRODUCTIVITY.
Whether you want advanced alerts of tyre related problems with our TPMS solution or route optimisation to get you to your next job quicker, MICHELIN Connected Fleet helps you keep your vehicle running. Keep your costs un der control by reacting to tyre alerts before they become a breakdown or access HGV optimised route mapping via our partnership with CoPilot.
Find out how MICHELIN Connected Fleet can help your business.
Do you own other trucks for clients that Aon haven’t arranged insurance for?
As well as arranging your Hauliers insurance for your Tarmac contracted trucks, did you know that Aon can also arrange the same cover for your non-Tarmac contracted trucks, company owned vans and cars?
As specialists in arranging Hauliers Insurance, trust us to arrange cover that’s right for you. Whether you have a single truck or multiple, whether you’re an experienced Haulier or a new firm, our Haulier Insurance experts will help you choose the right cover for you.
Let Aon give you the confidence that you meet the minimum standards as set out in your Tarmac Independent Contract Haulier Agreement. Cover includes Motor, Combined Liability and Goods in Transit. In addition, we can also arrange cover for Vehicle Breakdown, Management Liability, Property and/or Business Interruption.
To discuss a quote for your additional trucks or if you have any queries about your cover, please contact the dedicated Aon Hauliers Team:
Tel: 0333 0603 412 Email: enterprise@aon.co.uk Visit: https://bit.ly/aon-hauliers