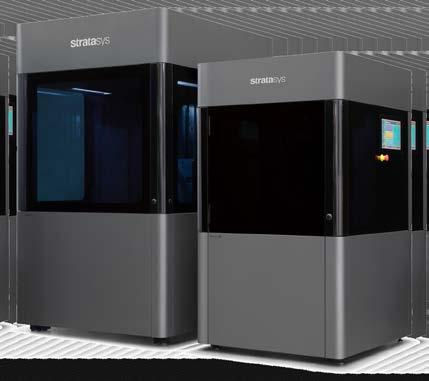
3 minute read
EDGE
from TCT Europe 31.3
by TCT Magazine
smaller printed assemblies of the rocket motor are HIPed in the Quintus Application Center, applying a soak with a temperature of 1,120°C, pressure at 100MPa, while being held for four hours. The cycle is also leveraging the URC functionality to rapidly cool the HIP unit to minimise process time for improved productivity.
The 3D printed liquid rocket engine is then passed onto Avonix Imaging to undergo computed tomography scanning. This project requires both 3D cone beam scanning and 2D linear array scanning, with the former being leveraged to capture several thousand radiographic images to produce a large three-dimensional volumetric datasheet in a single scan, and the latter being used to overcome any image degradation from the cone beam CT scan which might prevent defect detection.
Deploying the cone beam scanning approach, Avonix scans the rocket motor with a 450KV microfocus source, 61.5-micorn voxel size and 4mm copper filtration to capture 3,000 projection images in a 45-minute process. No indication of porosity in the printed parts has been found, with Avonix then deploying its linear approach to validate the findings. For this second scan procedure a 450KV microfocus source is used at a 100-micron voxel size with 2mm copper filtration. More than 1,600 Z-slices are captured in a process time of 45-seconds per slice, amounting to 19 hours in total.
By the end of the process, SLM Solutions, Quintus and Avonix are returning a rocket engine to the students that has a reduced part count, heightened complexity, increased fatigue strength and less variability in its mechanical properties. The partners have also highlighted a problem with current HIP standards for 3D printed Inconel 718, which have been developed for castings and transferred over to additive manufacturing, despite AM materials having different microstructures. And with the help of quality assurance tests, they have reinforced that metal additive manufacturing, in conjunction with HIP, can be used to make high-grade applications for space and aviation without sacrificing quality.

It is now over to the SDSU students to get its 3D printed liquid rocket engine over the line.
Second to none.
Designed by engineers, for engineers. The reliable and proven Neo series of 3D p r i n t e r s b u i l d h i g h - q u a l i t y p a r t s w i t h superior surface quality, accuracy and detail.
Open resin system
An open material system means users are not restricted by the usual parameter constraints, this offers the ability to utilize any 355 nm hybrid resin chemistry
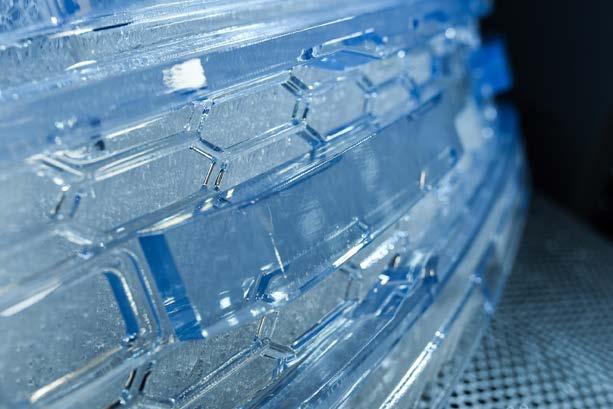
Proven reliability and quality assurance
D e s i g n e d b y e n g i n e e r s f o r e n g i n e e r s , t h e N e o i s c a r e f u l l y engineered throughout using state-of-the-art technology, proven components and aesthetic finishes.
Reduce finishing time by up to 50%
The Neo produces highly accurate parts with unparalleled industry quality Optimising the machine design and utilising the latest cuttingedge technology available for laser and scanners, our beam delivery system produces exceptional layer-to-layer alignment repeatability
The printed parts are dimensionally accurate, with exceptional sidewalls and crisp feature resolution.
Find out more, visit Stand No. D51 at TCT 3SIXTY 2023
As he extols the virtues of the technology facilitating a satellite weighing less than 100kg, Tony Boschi shows the depth of his experience with the repeated use of two words: rapid prototyping.
Boschi has been working with 3D printing technology for so long, that he not only refers to the processes using that phrase, but he also has the war stories. When he first used the technology, for example, he and his colleagues took to squirting hairspray on stereolithography (SLA) parts to prevent the sticky texture they were left with when coming out of the printer, and in turn allowing any paint applied to the components to dry faster.
“It was one of the greatest things in the world,” he recalls thinking. But such glee is relative. These days, as Lead Design Checker at Sidus Space, he has printed sample holder parts in Markforged’s Onyx carbon fiber-filled nylon material that formed part of a flight test platform installed on the outside of the International Space Station (ISS) for a year. That the parts survived on the ISS with next to no degradation emboldened Sidus Space to push forward with the idea of producing the structure of its LizzieSat satellites with 3D printing.
Sidus Space was founded by Carol Craig, a former US Navy officer who became the first woman eligible to fly combat aircraft in the US Navy, to carry customer sensors and collect data for a multitude of different customers at the same time.
The partially printed LizzieSat constellation will launch for the first time later this year on the SpaceX Transporter-9, if it weighs less 100kg.
This has represented a significant challenge for Boschi and the Sidus team, especially since integral