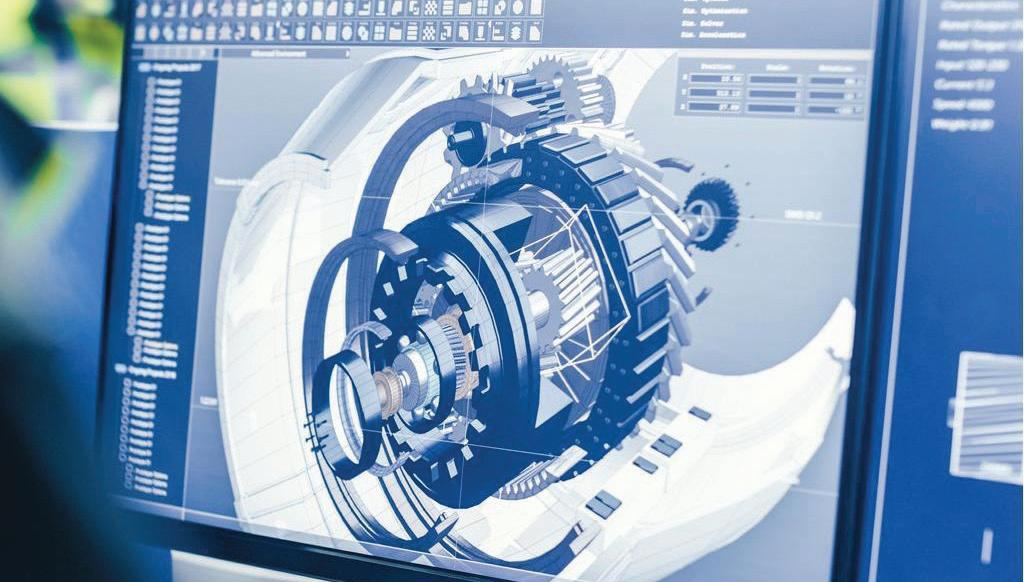
7 minute read
INTRODUCING HAUTE
from TCT EU 28.3
by TCT Magazine
INTRODUCING HAUTE FABRICATION WORDS: Sam Davies
Somewhere between Iowa and Texas, there is a suite of metal additive manufacturing machines in transit, a host of automation technology pieces as well, and a team of people who make up the latest contract additive manufacturing outfit on the market.
Haute Fabrication is in the process of bringing online four variants of its Hybrid Direct Laser Sintering (HDLS) machines, with build volumes ranging from 600 x 600 x 600 mm to 5200 x 5200 x 5200 mm, the number of lasers spanning between 1-4 and 64-144, and each with the capacity to learn from previous builds through artificial intelligence (AI) and heat treat components up to 2,400F, as they are manufactured, through built-in autoclaves.
It has taken to the road to situate itself within a region steeped in additive manufacturing expertise. In Austin, Haute will join Structured Polymers, the additive manufacturing powder company set up by Vikram Devarajan, James Mikulak and the late Carl Deckard, as well as put itself in close proximity to Deckard’s former supervisor, Dr. Joe Beaman at the University of Texas, all of whom have been the source of much guidance as appointed advisors in Haute’s early years.
“We can help you spend millions of dollars and build a printer just like what’s out there,” Haute’s Chief Science Officer and co-founder Kevin Friesth remembers the Structured Polymers cohort saying, “but what you need to do is develop the next generation. If [3D printing] is going to be accepted as a mass manufacturing [technology], it has to be automated because one, you don’t want people around powder and two, the quality of life damages, such as carpal tunnel because of repeated motions. You need to go automated and robotic to eliminate those two and then reduce the cost down to where it’s acceptable.”
AUTOMATION
Back when Deckard developed Selective Laser Sintering (SLS) technology in the 1980s, to automate the technology so humans never came into contact with powder wasn’t possible. It was barely possible in 2013. For Friesth, who had this vision of taking the foundations of laser sintering technology and supplementing it with AI-powered control systems and robotic devices, and scaling it up to sizes not seen before, it was more than a little frustrating that this was to be a steady development process, with much time waiting on other pieces of technology to get up to speed. HAUTE FABRICATION’S HDLS PLATFORMS:
HDLS 250 Minotaur:
1-4 1100W lasers; 600 x 600 x 600 mm build volume
HDLS 500 Tiamut: 4-9 1100W lasers; 1250 x 1250 x 1250 mm build volume
HDLS 1000 Kraken: 9-25 1100W lasers; 2500 x 2500 x 2500 mm build volume
HDLS 5000 Karathen: 64-144 1100W lasers; 5200 x 5200 x 5200 mm build volume
“Until about five years ago, the controller technology hadn’t developed to the point we needed it, you didn’t have a lot of the sensors that we do today. And when you had the sensors, you didn’t have the micro controllers, so it’s been chicken and egg,” Friesth tells TCT. “It’s been frustrating trying to fight through that, but now we’re getting to the point that artificial intelligence, data buses, networking capabilities, the storage tech has finally caught up.”
With Haute’s 2020 take on laser sintering technology, its robotic system is responsible for loading powder into an argon-filled melting system, which ensures no change of oxidation or moisture contamination, and later taking build cakes out of the machines for part removal and polishing. Job scheduling has been automated to help prioritise orders, while Haute’s set-up also includes an active feedback loop and AI-driven learned response from previous builds across its entire fleet of HDLS machines. Here, a patent-pending system of visual, thermal and ultrasonic imaging technology analyses the fabrication of every part layer by layer, detecting and recording defects and anomalies throughout.
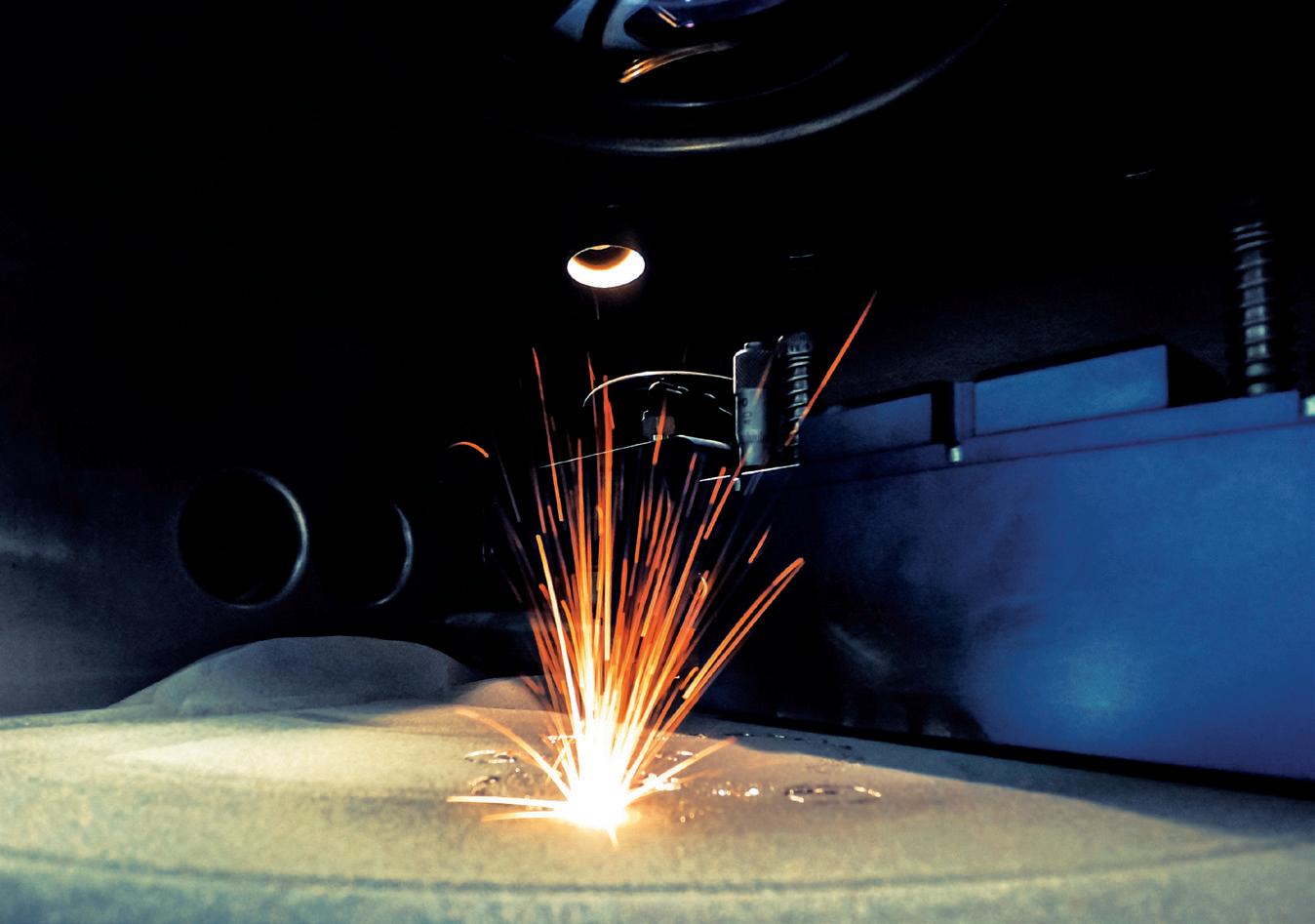
APPLICATION
This infrastructure has been put in place to ensure Haute has a running start once operational later this summer. The roadmap has already been laid out; the company knows which industries and applications it will target from the get-go, what comes further down the line in a few years, and how the company grows in response.
“We’re going to go after the markets we know we can get into,” Freisth outlines.
This means that, although Haute has designed its HDLS systems to deliver the quality and volumes required by the aviation industry and be robust enough to achieve certification, it doesn’t want to wait around. The company will start by serving lower tech markets, manufacturing components like heat exchangers for ground source pumps and coolers for graphics processing units.
“Some of the other printer companies are still working on getting certified with [commercial aviation] three and four years later. It’s one of the hardest industries to get into,” says Friesth. “Why would we want to spend 200 million on a product that we might only be able to sell in three to five years?”
While commercial aviation is on the back burner for now, Haute will get to work right away on rocket engines, with an order to build several rocket engines for Odyssey Aerospace already placed. With its Karathen 5000 machine, which might not be operation until next year, applications like this will be produced in one primary piece, with just the turbo pump component and piping added after.
When Haute does tackle the aviation space, it looks likely that the company will set up a separate business unit, catering for what it anticipates being large demand and moving through the regulatory processes as the main Haute business focuses on low-tech components and rocket engines. This way, Haute believes it can solidify its base and allow the aviation business ‘the time to grow as it needs it’.
That growth will rely on a collaboration of innovation and guidance. Friesth, while the business was located in Iowa, made the trip down to Texas frequently in the last seven years, regularly being turned around to do more work on the thermal control inside the machines or the AI around them.
Advice like this, Friesth and his team have been more than happy to take on board. It was encouragement from the Structured Polymers team that set Friesth on this endeavour, their standards that raised his, and guidance like the titbit from Deckard that follows that went a long way to deciding how to bring HDLS technology to market.
“One of the first things Carl said to me,” Friesth recalls, “he said, ‘you can make a lot of printers, but you won’t make money on them. If you’re going to make money, you’re going to make it on the materials or you’re going to make it on the fabrications. I’ve got 30 years’ experience, I can tell you first-hand, if you try to go into the market selling printers, you’re going to be like all the rest and barely make a dime.’
“[Carl and Structured Polymers] have been very valuable mentors. They’ve ‘been there, done that’ with multiple machines, and we were able to [benefit] from their 100-plus years of knowledge. Unfortunately, we lost Carl early because I really wanted him to see the next generation machine, born from his original technology.”
Make the future with proven powders created by Praxair

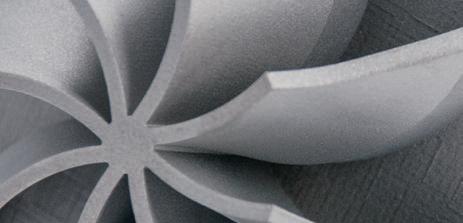
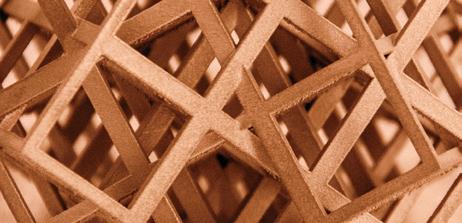
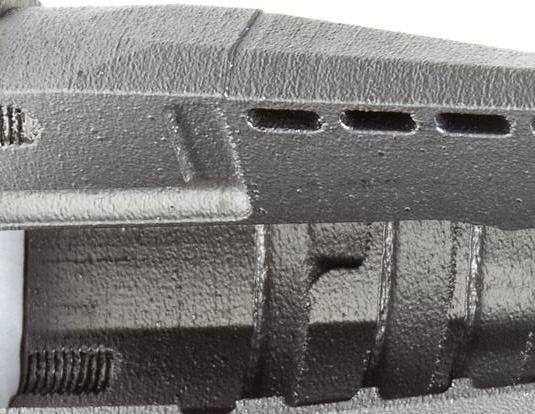
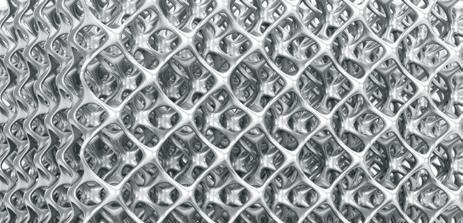
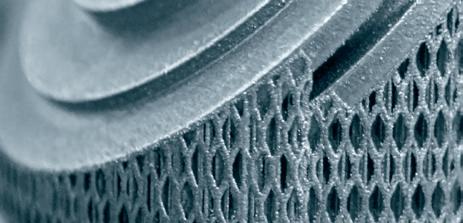
TruForm ™ metal powders support every part you make with capacity, quality and experience. • Used by leading OEMs across AM industry • Custom alloys and particle sizing available
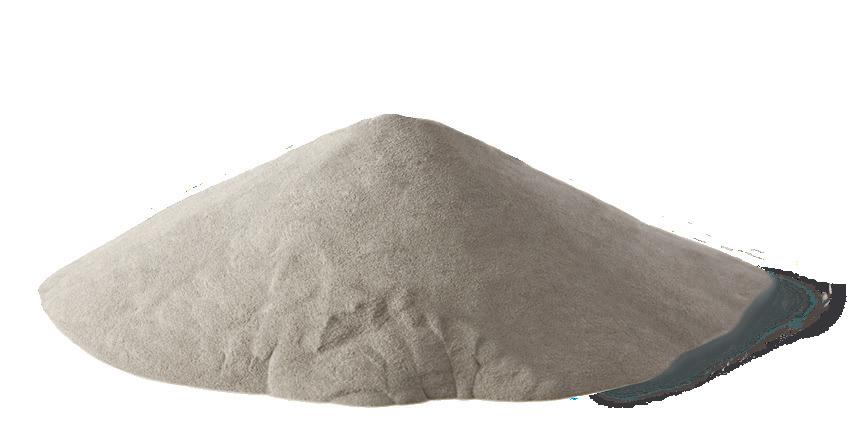
• Aerospace-grade
Learn more: To order: praxairsurfacetechnologies.com/am Praxair Surface Technologies GmbH Am Mühlbach 13, 87487 Wiggensbach Germany Tel: +49 (0) 837 0 9207 0 Fax: +49 (0) 837 0 9207 20 Email: AME_Europe@praxair.com
It’s Tru:
Tru2Spec ™ is the leading custom alloy formulation process for OEMs looking to go beyond conventional powders.
© Copyright 2019 Praxair S.T. Technology, Inc. All rights reserved.
Creative:Clients:Praxair:5701-25931 Updated Half Page TruForm Print Ad for Germany:5701-25931 Updated Half Page TruForm Print Ad for Germany - 192mm x 136mm_v02.indd
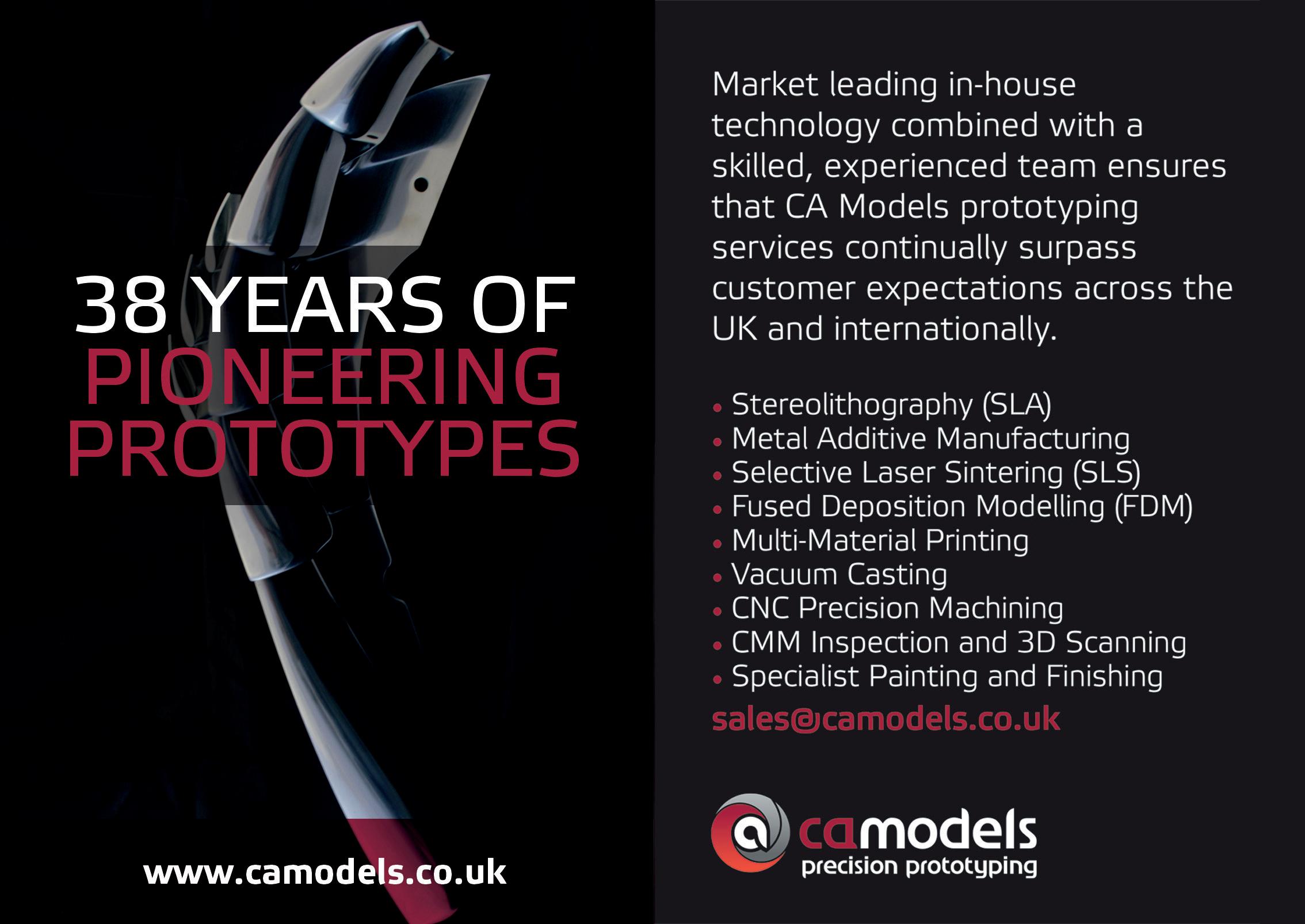
December 19, 2019 11:45 AM