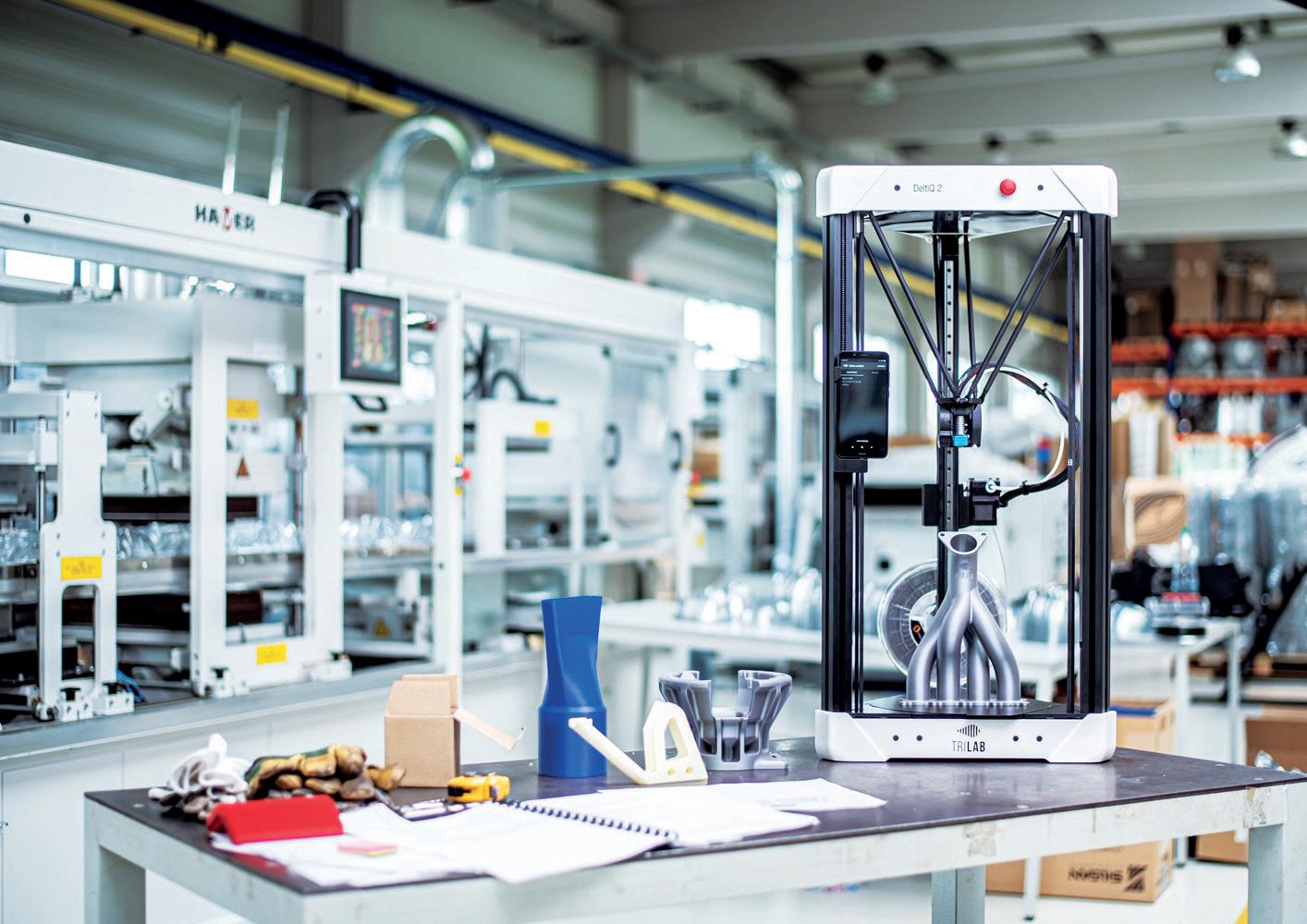
4 minute read
BEST OF BOTH WORLDS
from TCT EU 28.3
by TCT Magazine
BEST OF BOTH WORLDS When is additive manufacturing not 3D printing and vice-versa?
Sometimes it is difficult to draw the line at what is and what isn’t 3D printing. Take the LOM and then later Mcor technologies, both described themselves as 3D printing but if a common definition of that term is “a process that manufactures geometries by adding material layer by layer” those Sheet Lamination technologies may start by adding layers, but the geometry is created by subtracting material.
Definition and categorisation of technologies can be messy but in the grand scheme of things all that matters is that parts are fit for purpose. Ultima Forma is a metal forming company that spun out of Queen Mary University of London in 2017 with a novel electrodeposition process that it describes as metal additive manufacturing, but quite different to 3D printing.
Ultima Forma’s technology deposits metal atom by atom over a surface area to make light-weight, high performance, multifunctional, complex shaped components to net shape. Although that technology might not be 3D printing by the strictest definitions, Ultima Forma runs a wax-PLA mixture through a TRILAB DeltiQ 2 delta style FFF machine, for the majority of its tooling.
Unlike many manufacturing processes that use a wax like 3D print for tooling, Ultima Forma’s tooling is not always sacrificial, the Ultima Forma electrodeposition process grows parts in tanks resulting in low residual stresses. Surface finish is directly related to the tooling since the atom-by-atom process deposits directly onto the tooling’s surface. No large presses or heated tools are required and the whole part is produced at the same time – from the inside to the outside surface finish.
As a member of the European Space Agency business incubator at Harwell, an area of focus for Ultima Forma is replacing metal assemblies in satellites with an integrated multi-functional part, reducing weight and assembly time.
Typically, transition metals and noble metals are used to 'grow' parts, whereby controlling the micro-structure Ultima Forma can create enhanced properties which can be varied across a single part. Parts are not alloys, but laminates of dissimilar materials. By controlling the lay-up of dissimilar materials the properties of the materials formed can be varied across relatively large ranges when compared to conventional metallic alloys.
This innovation allows the material properties to be tuned to the specific mechanical design. The material properties can be varied within a component to produce multifunctional components as a single entity without the need to join or assemble dissimilar materials together. Increases in specific strength are often an advantage and by controlling local properties provide a major advantage for advanced engineering applications.
Athermal properties are possible since the microstructure does not break down until 600°C making parts suitable for high temperature applications. For each component Ultima Forma can tailor the chemical and electrical solution to each part design & user specification. The electroforming additive manufacturing process enables Ultima Forma to grow
5 ABOVE:
THE TRILAB DELTIQ 2
metal structures onto dissimilar materials so long as they can withstand acidic solutions. For example; ceramics, polymers, composites and pre-formed metal fittings, allowing hybrid components and assemblies to be formed into a single structure.
Other metals can be grown onto with separate pre-conditioning process trials underway and Ultima Forma is working with Queen Mary University of London to understand the limits of 3D printed polymers for tooling, particularly investigating the limits of tolerances and topological features to inform design guidelines.
Scott AM specialises in advanced manufacturing technologies to support product design and prototype development, low volume production and rapid prototyping. We work with a range of industries including automotive, healthcare, consumer goods and industrial products.
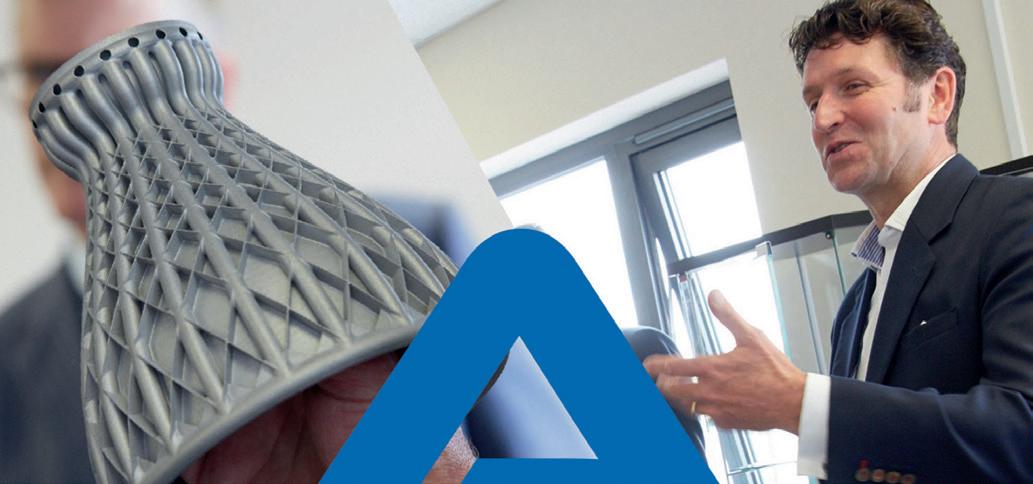

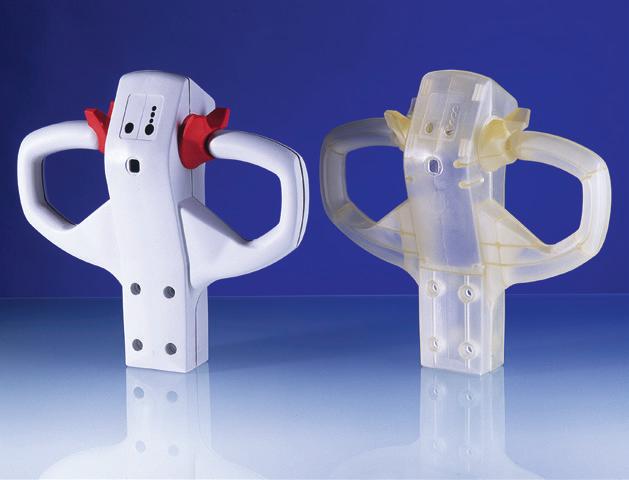
STOCK & SUPPLY:
• Extensive range of Polyurethane vacuum casting resins • Silicone tooling materials • Accessories and consumables
OFFER:
• Range of vacuum casting systems and ancillaries, including the
ScottAM 1000 and ScottAM 4000 vacuum casting machines • Fully qualified engineers, experienced in service, applications support and training for vacuum casting machines from MTT,
MCP, Renishaw and ScottAM.
With our expertise, qualified and experienced staff, we are here to support you. For more information, please contact us at sales@scott-am.com or visit
www.scott-am.com
ScottAM Ltd
Sutherland Works | Beaufort Road | Longton Stoke-on-Trent | Staffordshire | ST3 1RH Aerospace
Automotive Healthcare Motorsport
Official suppliers of Pelnox and H&K resins from Japan, regarded worldwide for their quality, performance, and safety.
Is your powder recovery process future-proofed?
Recover
Quick and safe transportation of AM powders
Re-qualify
Virgin and reclaimed powders qualified with maximum yield
Reuse
Compatible for use with all printers and powder vessels
Russell AMPro ® Range is a range of solutions for all powder transfer systems whether using powder containers, a fully integrated closed-loop powder recovery system or inert gas conveying and sieving.
Controllable & repeatable Maximum productivity Reduced manual handling Safeguard operators safety
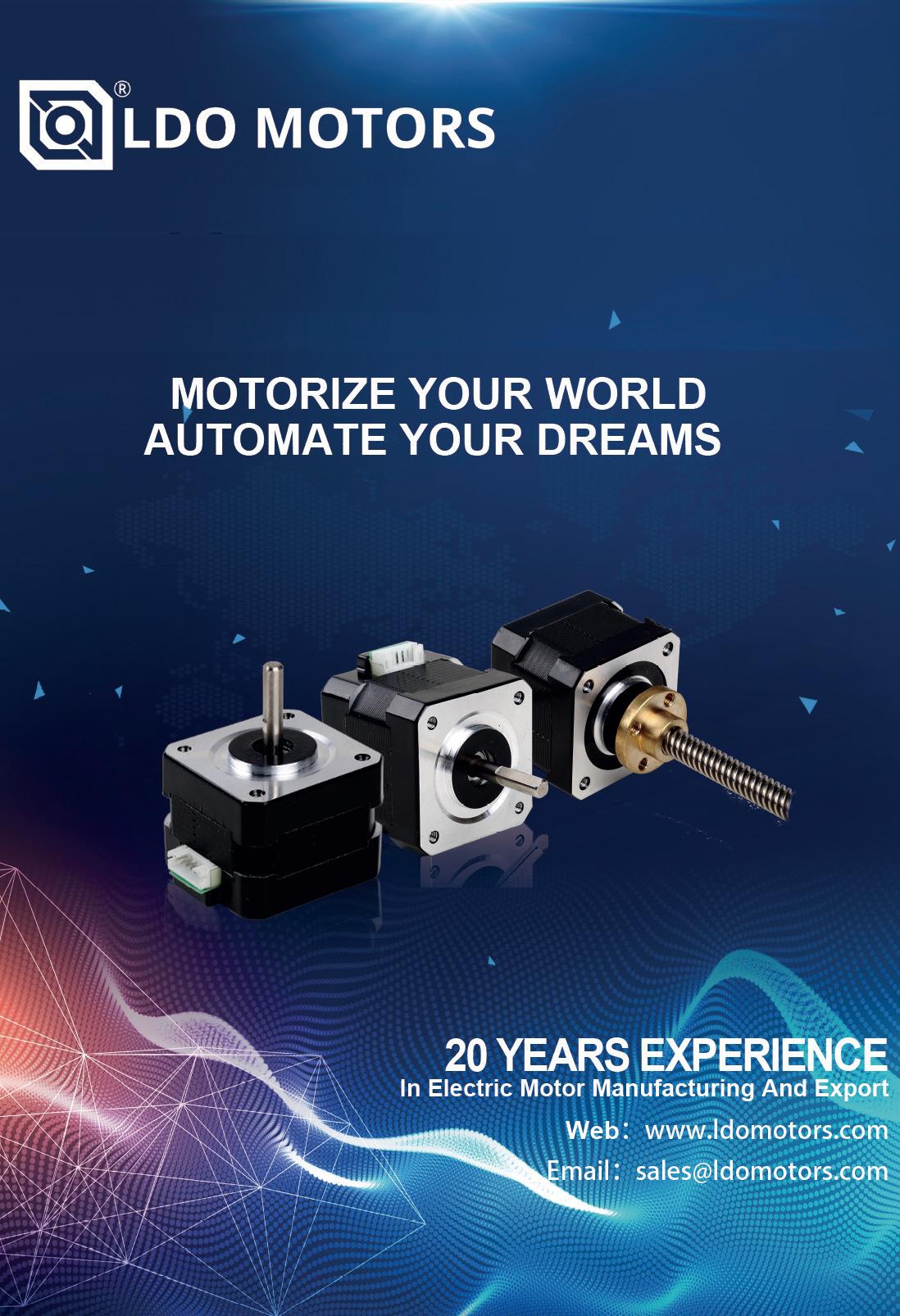