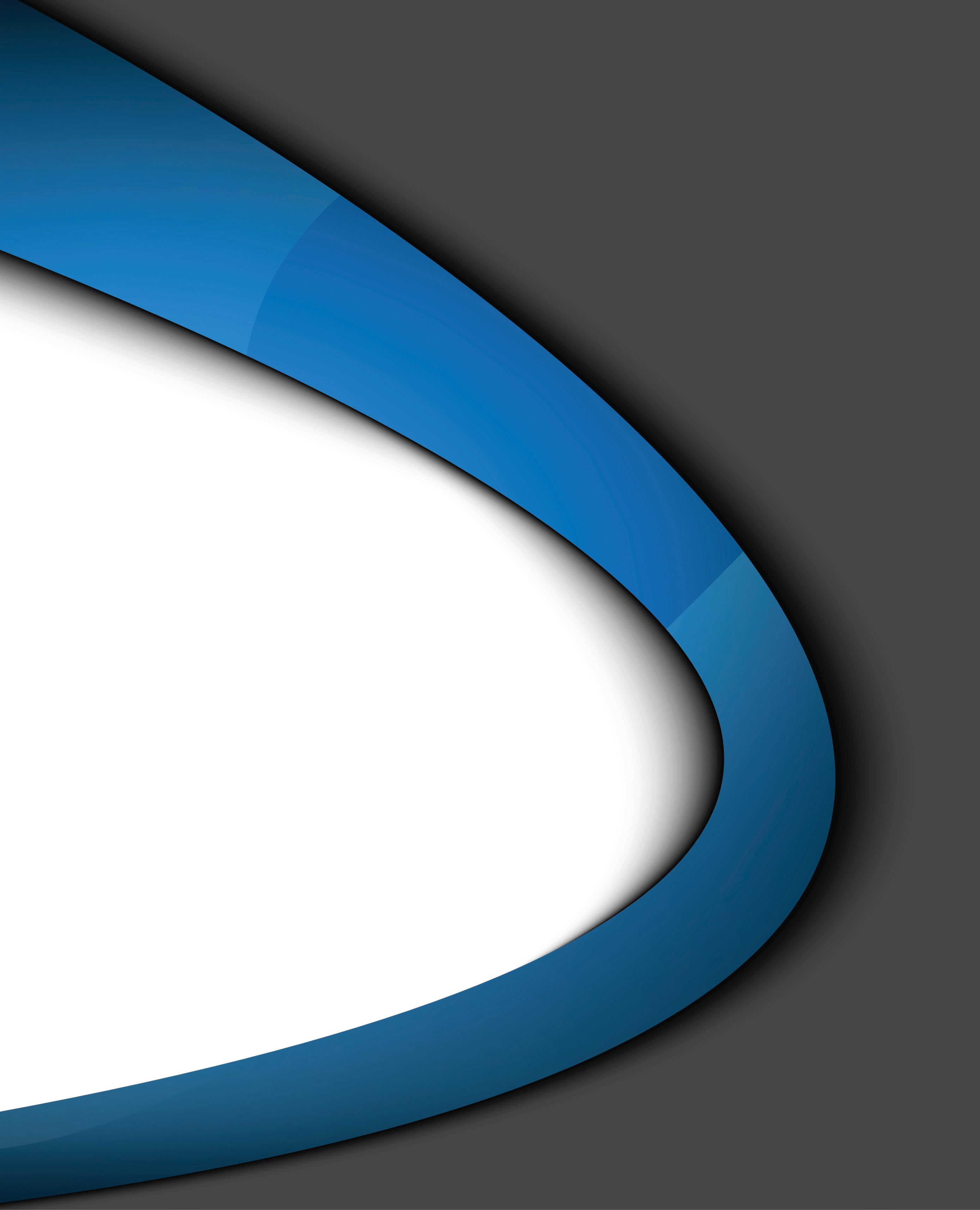
3 minute read
SMALL STEPS AFTER THE
from TCT EU 28.3
by TCT Magazine
WORDS: DANIEL O'CONNOR
Acriticism I often level at additive manufacturing (AM) presentations is their reliance on the GE Aviation LEAP fuel nozzle as an example of series production. My career in AM is roughly the same age as that of the LEAP fuel nozzles, and in the sum 50 conferences I've attended, I genuinely believe I've seen it mentioned in every single one.
In two whole days at the Additive Manufacturing for Aerospace & Space Conference 2020 (hosted a month before lockdown hit), I didn't see a single slide with the application that is to 3D printing presentations what traffic is to my commute home, ubiquitous.
If there was a theme from the proceedings, it was for the need for aerospace supply chain to get with the programme. The requirement for supply chains to print qualified parts was present in the talks of Boeing, Airbus, and Leonardo Helicopters. In his opening remarks, the chair for day one, Sebastien Messé of Safran Landing Systems, set the tone by posing the question, "is supply chain ready to produce parts at the right quality and safety?'
Steven Catt, the AM Technical lead at Thales, said that the industry needed to work together to establish some businessas-usual standards so Thales isn't applying the same qualification levels to a coat hook as a flight-critical component. Steven is currently working to form a cross-industry collaboration involving the sharing of data for parts not considered to have significant intellectual property, to agree on an approach for supply chain standards.
One of the event's main sponsors was Siemens and its VP of AM for the Gas & Power division, Markus Seibold, was keen to point out how Materials Solutions was founded on the very proposition on being an aerospace accredited AM service provider. The Siemens-owned business was the first UK company to receive the important Nadcap accreditation for the aerospace industry. However, even though Materials Solutions has over 50 machines, the problem appears to be that companies like Materials Solutions are few and far between.
It's not just the qualification of parts that needs addressing; the qualification of machinery is a major pain-point. Melissa Orme VP of Additive Manufacturing at The Boeing Company responded to a question from the floor with a comment that once a machine is qualified at Boeing, they prohibit software updates as each update would require requalification of the machine. Steven Catt suggested the following day that machine requalification is one of the costliest endeavours in AM. He stated that in many cases, machine requalification is more expensive than recreating a mould.
Because, specifically with metal AM, we've been forging new ground for the last decade, the question of machine longevity also came up; it's, for this reason, the frequency of machine requalification in aerospace is high.
The rate-limiting steps of AM were discussed in great length during the panel sessions and networking breakouts; it could be enough to suppress one's AM appetite; that was if it wasn't for the abundance of AM in action throughout the remainder of the conference.
Of particular interest was a talk from Dr David Wragg of Leonardo Helicopters, whose evaluation of were AM fits for them was both pragmatic and enlightening. Leonardo's approach to AM is to ask the question, where does it add value, and where does it create problems?
David and the team consider additive manufacturing 'normal' in low critical uses such as jigs, fixtures, and prototyping. However, Leonardo is now exploring materials like ULTEM and carbon fibrefilled polymers for applications like spare parts and maintenance repair and overhaul.
One particularly impressive example David shared was of an exhaust component. The traditionally manufactured version was notoriously tricky to fit onto the aircraft. However, the titanium AM version is not only designed for perfect fit but included part consolidation, reducing joins, which in turn reduces the risk of leakages.
Overall, it's clear that although we've not seen a giant leap for AM in aerospace since the fuel nozzles, the small steps that everyone else is taking are charting the right course.