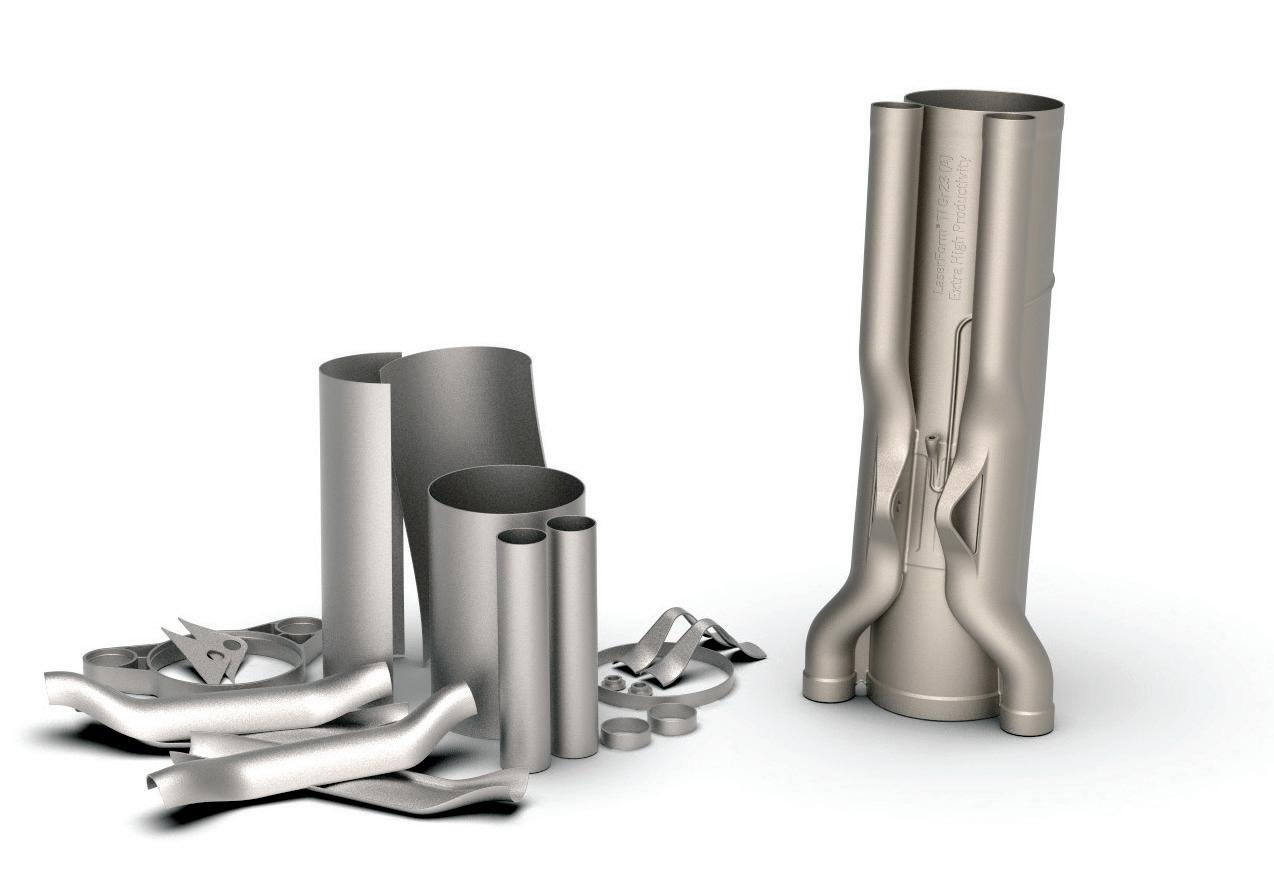
10 minute read
INNOVATING FOR EFFICIENCY
from TCT EU 28.3
by TCT Magazine
INNOVATING FOR EFFICIENCY WITH AM IN THE AEROSPACE INDUSTRY Patrick Dunne, Vice President, Advanced Application Development at 3D Systems explores the advantages the aerospace industry can gain by embracing DFAM/AM.
As green credentials supply chain – it ultimately contained a However, nowhere is this improvement increasingly gain QC step where nearly 10 metres of weld realised more than space systems. importance for lines had to be meticulously CT inspected Design-driven structural optimisation, many businesses, for defects. When AM was applied, 12 both manual and automatic, yields step manufacturers are looking for new parts became one – and jigs and fixtures, changes in strength-to-weight ratios. ways to create products that deliver assembly and slow QC inspection of weld Recent examples include Thales brackets performance efficiencies. The lines were no longer required. The resultant for satellite antenna. Utilising advanced aerospace industry is at the forefront, part was lighter, had fewer points of failure, structural algorithms, Thales was able looking for opportunities to innovate was more cost-effective and efficient to to generate a bracket design that, when with novel designs that ultimately help source and produce, and yielded better expressed in Direct Titanium printing, improve fuel efficiency. performance. was 25% lighter – while maintaining the
Additive manufacturing (AM) is performance of a traditionally manufactured a revolutionary technology that is THERMAL TRANSFER bracket. Further opportunities for changing the way many companies The fuel efficiency of jet engines is a optimisation were identified based on are designing and producing function of multiple factors. One of these transitioning to tubular structures, as we see products. In aerospace, this rapid, factors is system temperature. Typically, the in bicycle frames. minimally constrained design hotter you can run the system, the more environment allows for step changes fuel-efficient it becomes. A 100-200°C AM, THE EFFICIENCY in design optimisation. At a practical increase in temperature can account for a BREAK-THROUGH level this is now enabling aerospace 1-2% efficiency increase. When you combine thermal transfer, companies to design better, faster While that does not sound like much, it component consolidation, and weight and more efficient platforms. can equate to hundreds of millions of dollars reduction, you can see how AM has a large in fuel savings for an airline when you part to play in improving energy usage DESIGN SIMPLIFICATION, look at thousands of engines flying many figures for the aerospace market. There CONSOLIDATION AND PART thousands of hours. AM allows engineers are other benefits too such as more costCOUNT REDUCTION to integrate the design of exotic/conformal effective R&D,
Historically, complexity, cost, cooling structures into sub-components reduced time-to-market as well as end system that ultimately allow the parts to maintain time to first reliability hold a close correlation to functional and structural integrity at these part, and the number of subcomponents within elevated temperatures. the ability an assembly. The fewer parts you Similar principals of thermal transfer exist to create have, the less assembly required and within rocket combustion systems, where bespoke ultimately, the fewer points of failure. temperature drives pressure. This, in turn, parts,
While a reduction in the number yields performance, as well as the rate of furthering of parts as a design philosophy is wear and tear/ablation, feeding the trend innovation. not new, nor even exclusive to AM, it towards system reuse economics. allows engineers to take it to a AM is whole new level. WEIGHT REDUCTION transforming
My favourite recent AM holds huge potential how industryexample was a direct benefits for the efficiency leaders are metal component that was of spacecraft and satellites. creating new, traditionally made from Reducing the weight of improved 12 separate castings and parts that fly always products tubes, all welded into a yields improved while gaining single part. Aside from fuel efficiency efficiencies that assembly labour, tools, jigs and performance. place them well and fixtures – as well as ahead of their a complex multi-vendor competitors.
Protolabs CEO & President Vicki Holt talks embracing digital manufacturing and sustainability with Deputy Group Editor Laura Griffiths.
Five million and counting. That’s digital manufacturing means end-toIf there is a positive to be found in the midst how many parts Protolabs end digitisation of the digital thread of this health pandemic, the reliance on speedy had produced by mid-May, of information that starts right at the and distributed manufacturing has allowed that purely for COVID- 19-related beginning when our customers interface digital model to shine. Amongst those millions of applications. The company was one of with us on e-commerce and they upload parts produced, Protolabs has supplied 10,000 countless manufacturers and service a computer aided design or CAD sterilisable and reusable face shield components providers that quickly switched up their file. That data is what our proprietary for Michelin to support medics production lines software analyses in detail with parallel at two of France's largest university hospitals for masks, swabs and ventilator computing in order to understand how before altering the design and switching to components to produce vital parts we're going to make that part, turnaround injection moulding to supply a further 20,000 on-demand. It’s a world away from a quote for that part and then once the in a matter of days. It has also worked with those Met Gala ball gowns, 3D printed customer finalises their order, that same Mercedes-AMG F1 team and UCL to help in collaboration with GE Additive, that digital thread moves all the way through manufacture an urgent CPAP device, and with featured in this very magazine just 12 our manufacturing process and allows Brescia-based engineers at Isinnova to supply 100 months earlier. us to manufacture custom parts in as 3D printed valves that turn snorkelling equipment little as a day in very low volumes and into non-invasive ventilator masks. On the day of
But Protolabs, a manufacturer of very economically. That speed and the our conversation alone, the company had over 20 custom prototypes and production parts, scalability around which we can produce active COVID-19 related projects in production. has always known the value of digital custom parts is fully enabled with the manufacturing in responding to diverse digital model.” “I think this whole thing has shone a light on the challenges ever since its founding in very, very important role that manufacturing plays a garage in Long Lake, Minnesota in in innovation and solving problems,” Holt explains. 1999 with a vision to drastically reduce lead times for plastic and metal parts 6 BELOW: VICKI HOLT, PROTOLABS PRESIDENT AND CEO “I think people are realising the importance that manufacturing has for us through digitisation. For Holt, who joined to be able to be the society that we are and Protolabs in 2014 with already 35 years sometimes we take that for granted. I think this of experience in the sector, that vision has shone a light, that no, we cannot take that for remains the same. granted. We're very essential businesses.”
“It [digital manufacturing] does mean different things to different companies,” Holt tells TCT. “At Protolabs,

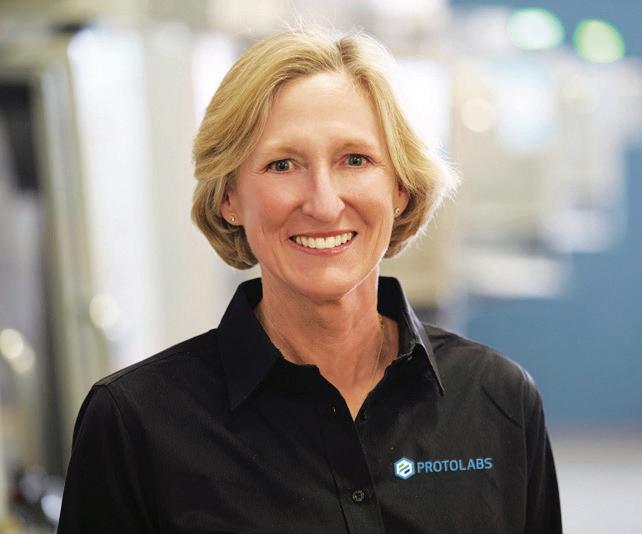
SHOWN:
PROTOLABS CURRENTLY HOUSES MORE THAN 170 3D PRINTERS
ADDING ADDITIVE
With facilities across Europe, the U.S. and Japan, Protolabs specialises in 3D printing, CNC machining, sheet metal fabrication and injection moulding services for prototypes and low volume production runs, all connected by a sophisticated software platform. Holt says it’s in the company’s DNA to “always think about a process from end to end” which is becoming increasingly important as the so-called digital thread becomes “part of how we think as companies and how we exchange with each other.”
To that, Holt says 3D printing was a logical addition to Protolabs’ toolset, which materialised in 2014 with the acquisition of Fineline Prototyping. Now, the company has over 170 additive manufacturing systems worldwide, 120 in North America alone, including machines from Carbon, HP and EOS. The most recent addition was the GE Additive Concept Laser X Line 2000R metal laser melting system that’s already serving largevolume metal projects across aerospace and industrial equipment applications. Although 3D printing currently only represents around 13% of Protolabs’ sales revenue, Holt believes we’re still in the early stages of tapping into its potential and
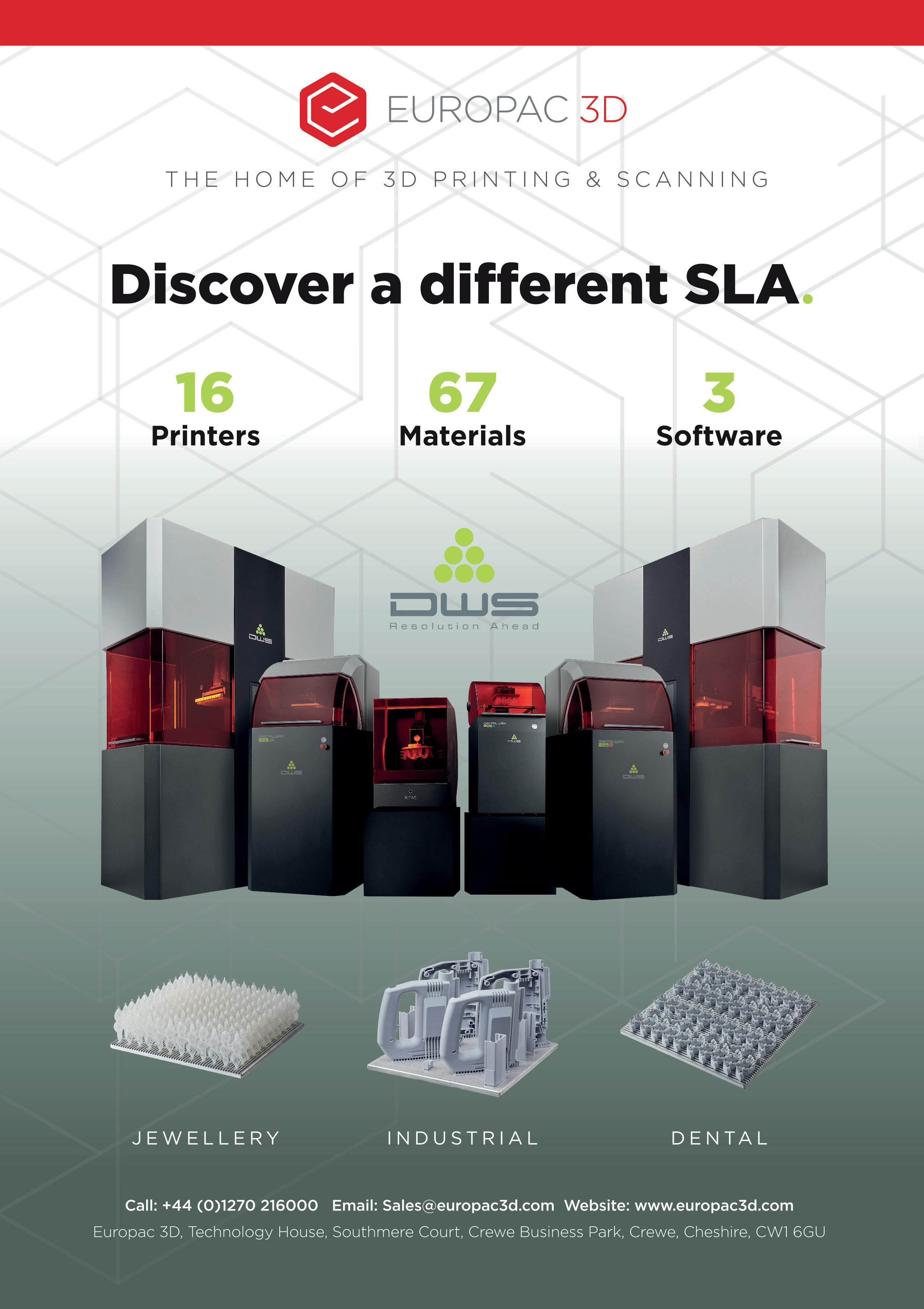
as more product developers learn how and when they need to use the technology, those AM capabilities will continue to grow.
“We see the technology [3D printing] bringing value in a couple of areas. It certainly, in its roots, was around prototyping and we still see an awful lot of prototyping solutions where a designer designs something, they just need something in their hand to see what it's going to look like and how it's going to fit. But more and more we're seeing manufacturers look at the actual structure of the product, and how could I design that product in a way that gives me another major business advantage whether it be lightweighting, whether it be energy efficiency, and when you have 3D printing, you have complete design flexibility."
On being a one-stop shop for multiple processes, Holt adds: “The great thing about our business model is we're not wedded to a single technology and the technologies play different roles, depending on what the customers part geometry is and what problem they're trying to solve."
THE BUSINESS OF SUSTAINABILITY
While the pandemic has emphasised how technology can be used to solve immediate challenges, there’s another long-term challenge that Holt believes technology could have a real influence on: sustainability. The term has become a bit of a buzzword, particularly in additive manufacturing where the technology is often considered sustainable by nature; in theory, you only use the material you need rather than removing material from a solid block, in reality, it’s not so simple. Protolabs is taking an active role by investing in initiatives that reduce waste, recycling materials like CNC machining shavings, water from the injection moulding process and AM powders, and taking advantage of renewable resources.
“I am passionate about sustainability,” Holt says. “I believe that the answers to problems we've got around climate change are going to come from technologies and it's going to become from companies collaborating together to find these solutions. I’ve been very inspired by how companies have come together in this pandemic
6 BELOW:
CHARLOTTE VALVES 3D PRINTED
WITH HP MULTI JET FUSION
and it tells me we can solve the problems around climate change and focus on sustainability.”
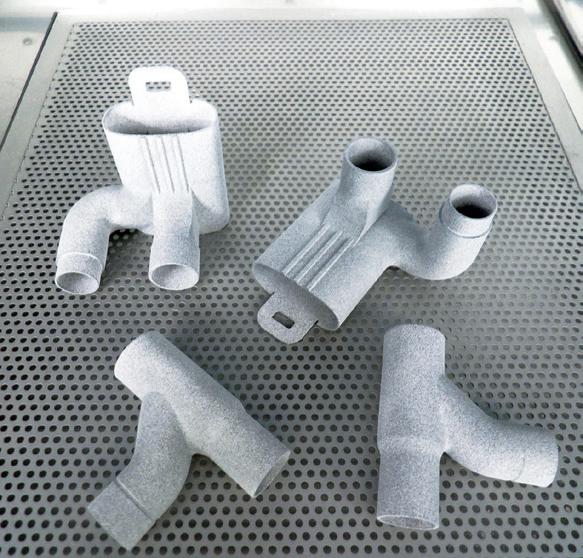
Holt argues sustainability is embedded in Protolabs’ business model. Customers can order the exact number of parts they need, whether that be 25 or 10,000 injection moulded parts or a single 3D printed prototype, there’s no need to order in large quantities to justify the cost of a mould tool or account for future demand.
“One of the core things about our business model is we don't have minimum order quantities for customers. If you need one part, we'll make you one. If you need 52, we'll make you 52. A lot of companies and manufacturers require you to buy 10,000 of something or 100,000 of something. Well, that quantity might be a 10- year supply and you might have a bunch of obsolescence and throw it away. For us, you just have to take what you need for your product at this point in time and eliminate the waste. That business model itself, I think drives for sustainability.”
Listen to the interview in full: mytct.co/VickiHolt
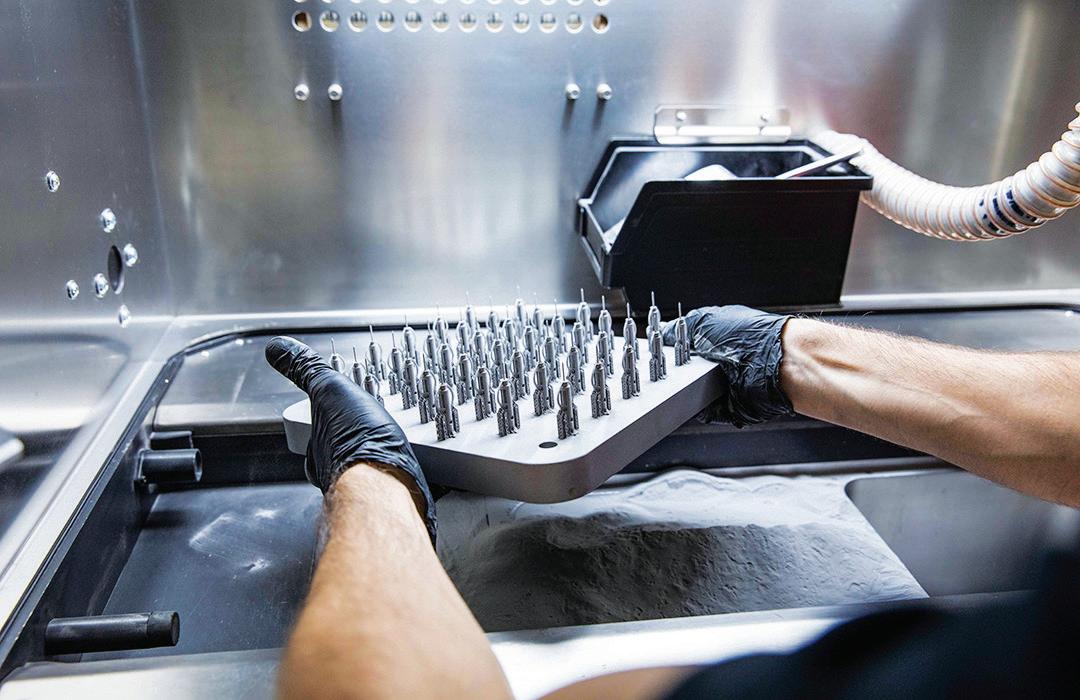
RAPID PROTOTYPING
We are dedicated to providing an excellent service
– from rapid quote to on-time delivery – producing high-quality components at the right price.
· Stereolithography · Selective Laser Sintering · Vacuum Casting · Two Shot and Over-moulding · Silicone Components
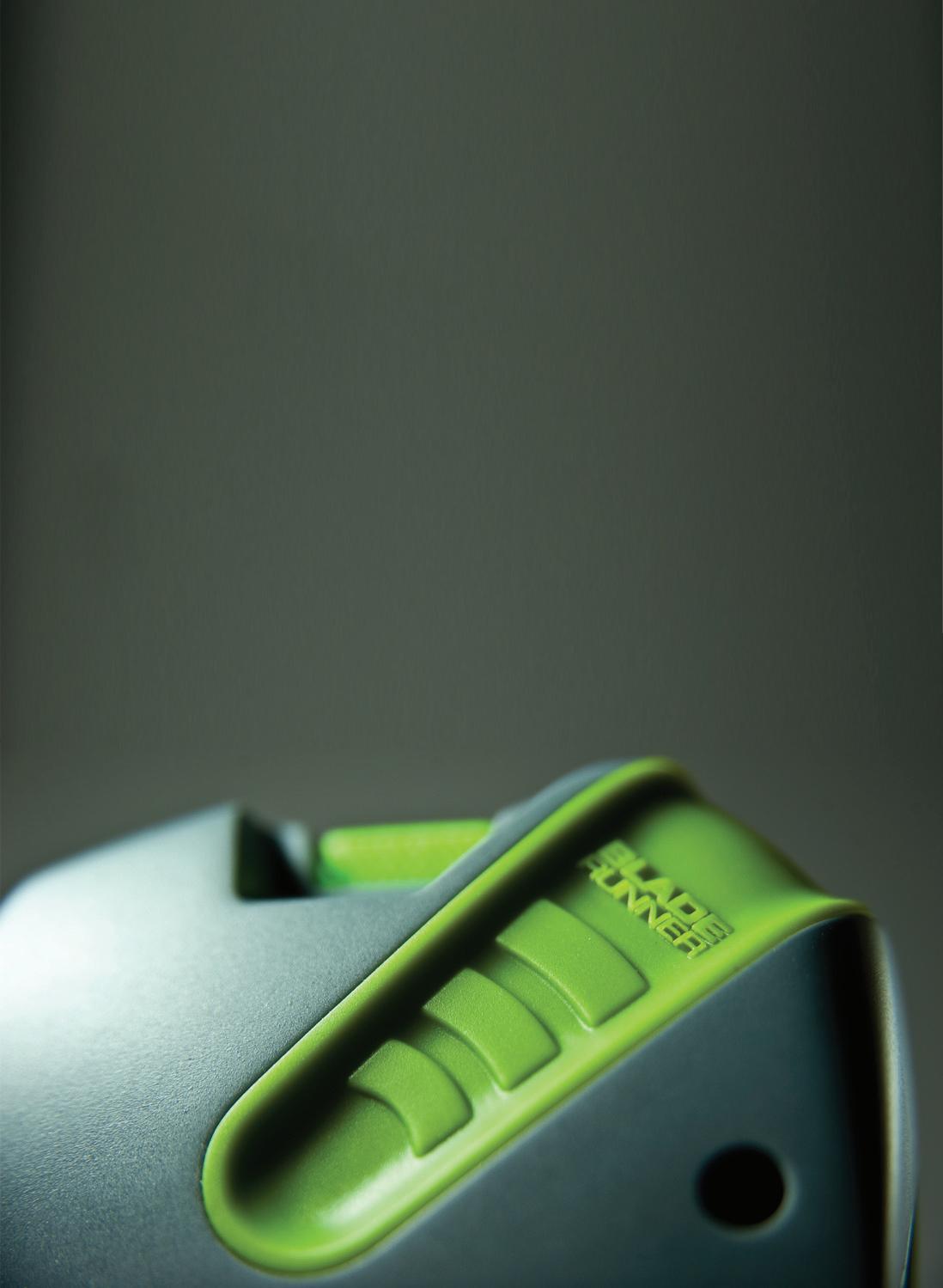