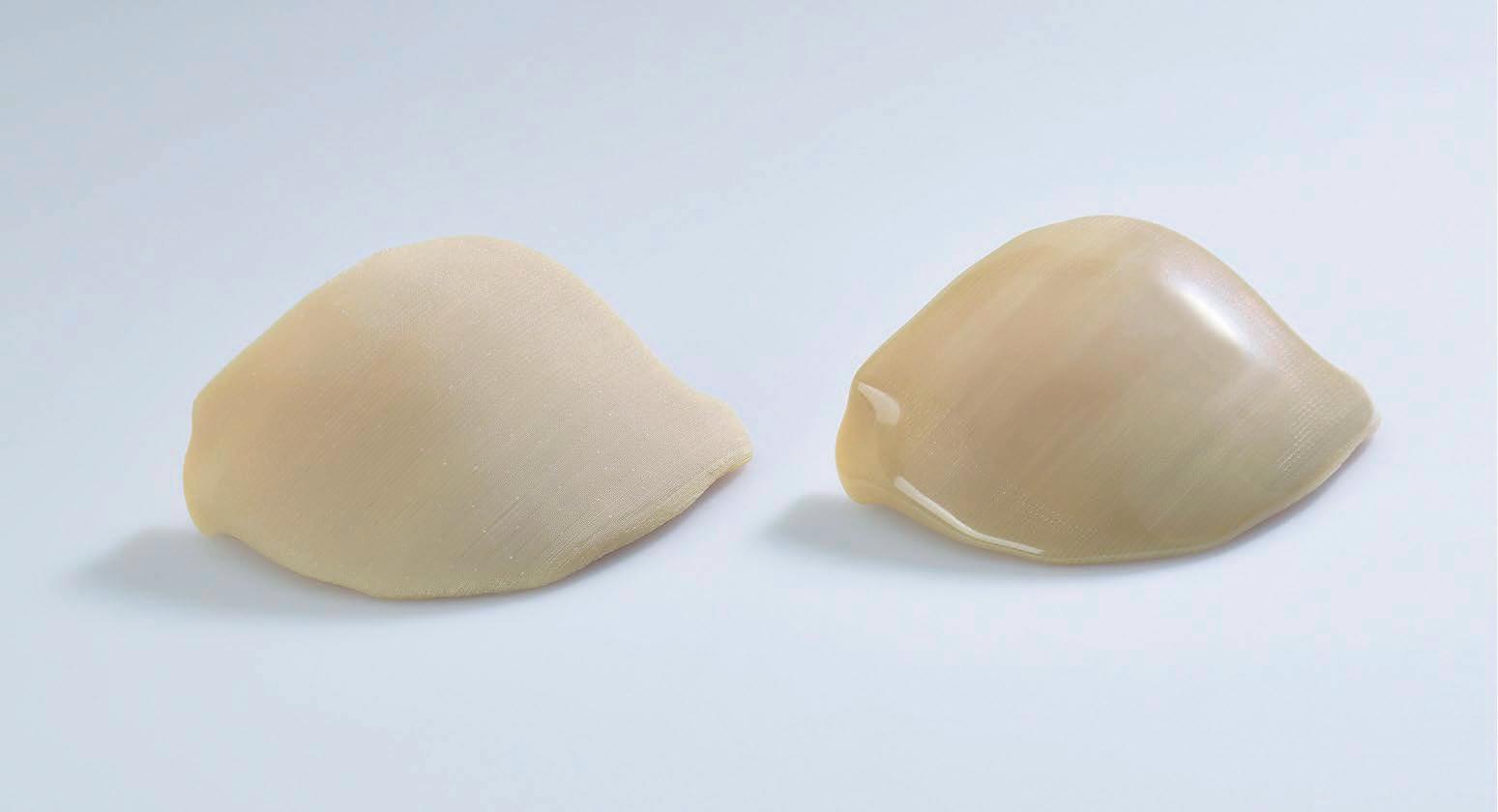
9 minute read
RIGHT TO RE-PRINT
from TCT Europe 30.2
by TCT Magazine
WORDS: LAURA GRIFFITHS
RIGHT TO RE-PRINT
In just the last six months, my washing machine has broken down twice. It’s over ten years old so the length of time taken to source and install parts meant several weeks of handing over a laundry bag to my parents like I was an 18-year-old student going home for the weekend again.
It got me thinking about a presentation by industry consultant Phil Reeves back at CES in 2015: the teardown of a Bosch washing machine to see which components could and couldn't be 3D printed. While the technologies referenced have evolved in the intervening years, its message, that the economics don’t always add up to AM, continues to off er a relevant dose of pragmatism whenever the topic of spare parts is raised.
“I think if we did this study now, we'd fi nd a lot more viable components that are either economically viable to 3D print or materials that are more suited,” Reeves recounted in a recent call with TCT. “Personally, I still think the whole spare part debate comes down to material properties. Do we have an available additive material that is fi t for purpose to replace the spare part? The right to repair thing is going to be really interesting in that, yes, we have a right to repair but where does the liability sit if you take the choice of repair? Because unless the part was initially designed to be made by 3D printing, it's always going to be kind of a Band-Aid.”
While recent conversations around supply chain have put AM and digital inventories under the spotlight, 3D printing replacement parts is nothing new. Back in 2012, Swedish consumer electronics manufacturer Teenage Engineering made some of its components available via online 3D printing provider Shapeways to combat high shipping costs associated with replacement parts for its OP-1 Synthesizer.
“Companies like Teenage Engineering highlight one of the greatest benefi ts in 3D printing, allowing anyone to take control of creating spare parts, and pushing back against the ongoing issue with products that can be impossible to repair,” Christopher Angi, Director of Sales at Shapeways, told TCT. “On the larger scale, we see the ability to 3D print spare parts and eliminate enormous amounts of warehouse space – along with the long-winded chain of communication it can take just to get one or a few parts – replaced by digital inventories. We are working with companies in several verticals who are already doing this, or considering the transition. We also see a trend in companies who want to focus on sharpening their own specialties while outsourcing 3D printing services for functional parts related to maintenance, repair, and operations (MRO).”
Where the volumes are right or a redesign benefi cial, the case for AM can be made but for many parts, traditional methods of manufacture are still the way to go. Reeves recalls a visit to the warehouse of one of Europe’s largest white goods spare parts suppliers almost a decade ago. An analysis of the millions of SKUs on-hand was conducted but Reeves concluded “you could literally count on one hand the ones that were viable 3D prints.”
“Some of those were viable for printing but the vast majority of parts that fail are not the mechanical principal parts,” Reeves continued, noting cast metal parts such as metal hob burners which might otherwise prove costly to reproduce with traditional tooling. “The vast majority of white goods parts that fail are electrical parts systems, interlock switches because they wear out, motors, bearings, it's all things that are actually not particularly printable.”
For those parts where 3D printing does make sense, 3D printer manufacturer and service provider Ricoh 3D has been deploying AM for spare parts both internally and for customers. The company has adopted a ‘one-on-theshelf’ model for its own spare parts, with engineers at Ricoh UK's Products Limited site swapping out critical factory jigs and automation tooling for AM alternatives. In one customer example, domestic equipment consortium Groupe SEB worked with Ricoh 3D to redesign an obsolete drip collector for an espresso machine. The company already off ers 3D printed spare parts for several products as part of a 10-year repair scheme guarantee, and was able to successfully perform 1,000 coff ee cycles with this SLS spare.
Mark Dickin, Additive Manufacturing & Molding Engineering Manager at Ricoh 3D, told TCT: “The project demonstrates how 3D printing allows small intricate products to be
produced quickly; whether this is in the repair of fi nished consumer products or production line equipment. When volumes are relatively small or parts are out of production, 3D printing is often the only profi table solution.”
While Dickin believes AM can play a huge role in application stories such as this, he cautions there are still challenges in disrupting established spare part models.
“The ‘right to repair’ legislation is likely to cause logistical headaches for manufacturers globally who face having to stock hundreds of thousands of spare parts.” Dickin said. “However, the law could also fi nally move the dial in reversing the “throwaway society” trend of the last 60 years by creating goods that last longer - producing savings for both the consumer and environment.
“Some parts will be frequently required and it makes sense for manufacturers to hold these in physical form, but 3D printing means the parts which are less in demand can be held digitally as CAD data. With only a data fi le needed, why stop at a 10year guarantee?”
Paul Ruscoe, New Business Development Director at LCD-based 3D printer developer Photocentric, which has worked with a number of manufacturers in the consumer electronics and durables space to produce spare parts, agrees.
“The legislation is likely to cause signifi cant logistical problems for manufacturers who face having to stock thousands of spare parts,” Ruscoe told TCT. “The fl exibility of AM provides a solution to this problem. It’s likely that parts that are often required will be held in stock, but 3D printing means the parts which are required less frequently can be held digitally – with small production runs printed on-demand.”
With right to repair legislation now requiring manufacturers across Europe to supply replacement parts for select white goods and easily yourself, you no longer depend on the manufacturer to supply you with the things you need to make a repair. You would then really have the means to make repairs. Of course, you still need repair information, which the manufacturer is not keen to supply. But being able to create spare parts yourself would be a huge step which would stimulate self-repair. It would also be better for the environment if spare parts could be produced locally instead of having to come from the other side of the world.”
In the UK, Manchester Metropolitan University’s PrintCity is part of a 7.84M EUR Interreg North-West Europe project called ShaRepair, which aims to decrease WEEE (Waste Electronic and Electrical Equipment) from consumer products through citizen repair initiatives leveraging digital tools like 3D printing.
“There are thousands of citizens out there with varying degrees of expertise in repair, but they are diff use and some don’t have access to the parts they need,” Gary Buller, Technical Offi cer at PrintCity commented. “The digital tools of ShaRepair will hopefully bring these citizens together, closing the gap between intent and behaviour. 3D Print is one of the tools in closing those gaps, enabling citizens to manage their parts inventories better, bringing an agility to the supply chain of spare parts and also optimising the repair process.”
Working with partners across Belgium, the Netherlands, UK, Ireland and Denmark, ShaRepair provides online tools, a digital library of printable parts, professional repair service information and free product repair workshops throughout the year. PrintCity has even repaired its own 3D printers using recycled fi lament made from coff ee cups.
Rhiannon Hunt, Circular Economy Project Manager at MMU, added: “It's not necessarily things you think about off the top of your head. We've had a radio housing that was cracked so they printed out a new housing for it, attachments for vacuum cleaners and buttons, all sorts of things. I think that's one of the key benefi ts of additive, it’s so fl exible so you can tackle a lot of diff erent types of products easily.”
electricals over ten years, Ruscoe says this creates a challenge for manufacturers who will be required to stock parts they may not need, and the company is actively inviting consumer goods manufacturers to collaborate and digitise their spare parts lists.
“3D printing can easily unlock this problem by being able to print quantities on demand,” Ruscoe said. “This gives manufacturers the opportunity to support the right to repair initiative whilst saving costs on stock and warehousing, and at the same time minimising risk of producing parts that are not required.”
In some cases, consumers are taking repair into their own hands. Repair Café has created a network of 2,200 free spaces where visitors can bring in their broken items and learn to repair for free. The initiative was started in 2009 by environmentalist Martine Postma in Amsterdam. Now, with locations all over the world, equipped with all the tools and materials needed to repair items from electrical appliances to toys, might 3D printing have a place?
“The Repair Café community across the world is enthusiastic about 3D printing and sees its potential,” Postma told TCT. “We see some Repair Cafés experimenting with 3D printing, but not on a large scale. Designing spare parts is still rather diffi cult. If this should become easier, more Repair Cafés would feel more confi dent about 3D printing and then it could be a real revolution for the repair movement.”
While Postma notes the increase in students learning 3D design and manufacturing skills in schools, which the founder believes are “much needed in a repair society,” there are other challenges to contend with.
“It could be a revolution,” Postma added. “When you can print a spare part pretty
SMOOTH 3D PRINTED ULTEM COMPONENTS
AM component from PEI (Ultem 9085), re-worked to injection moulding finish
FINISHING OF PRINTED COMPONENTS
The ARBURG freeformer 300-3X is specially designed for processing high-temperature thermoplastics. This enables the use of pure pelletised materials including polyetherimides (PEI). Materials such as Ultem 1010 for medical applications and Ultem 9085 for the aerospace sector can be processed additively using the ARBURG Plastic Freeforming (APF) process.
The PEI/PC blend Ultem 9085 is a high-strength, flame-retardant material that is approved for aerospace applications. It also meets the fire protection requirements for rail transportation (UL94 V-0 flammability rating). With a build chamber capable of consistent heating at 200 degrees Celsius, the freeformer can reliably process high-temperature materials. Functional prototypes such as gears, ventilation ducts, and other complex geometries can be created using Ultem along with a break- away structure. Optimised temperature management, active component cooling, and high precision axis drives, allow the freeformer to create parts with extreme accuracy and fine detail. The APF process allows for a high level of detail. Thanks to the open material platform, users can process a wide spectrum of thermoplastic granules alongside their own original materials and optimise the process controls themselves. The freeformer can also additively manufacture very small functional components and delicate structures without any problem.
Recently at formnext 2021, ARBURG and its partner OTEC demonstrated the post-processing of APF functional components using vibratory finishing, for example. This additional process makes it possible to achieve surface qualities comparable to those of injection moulded parts. For freeformer printed components, the roughness can be reduced from an Ra of 19.42 to one of 0.46.
i
Further information: www.arburg.com