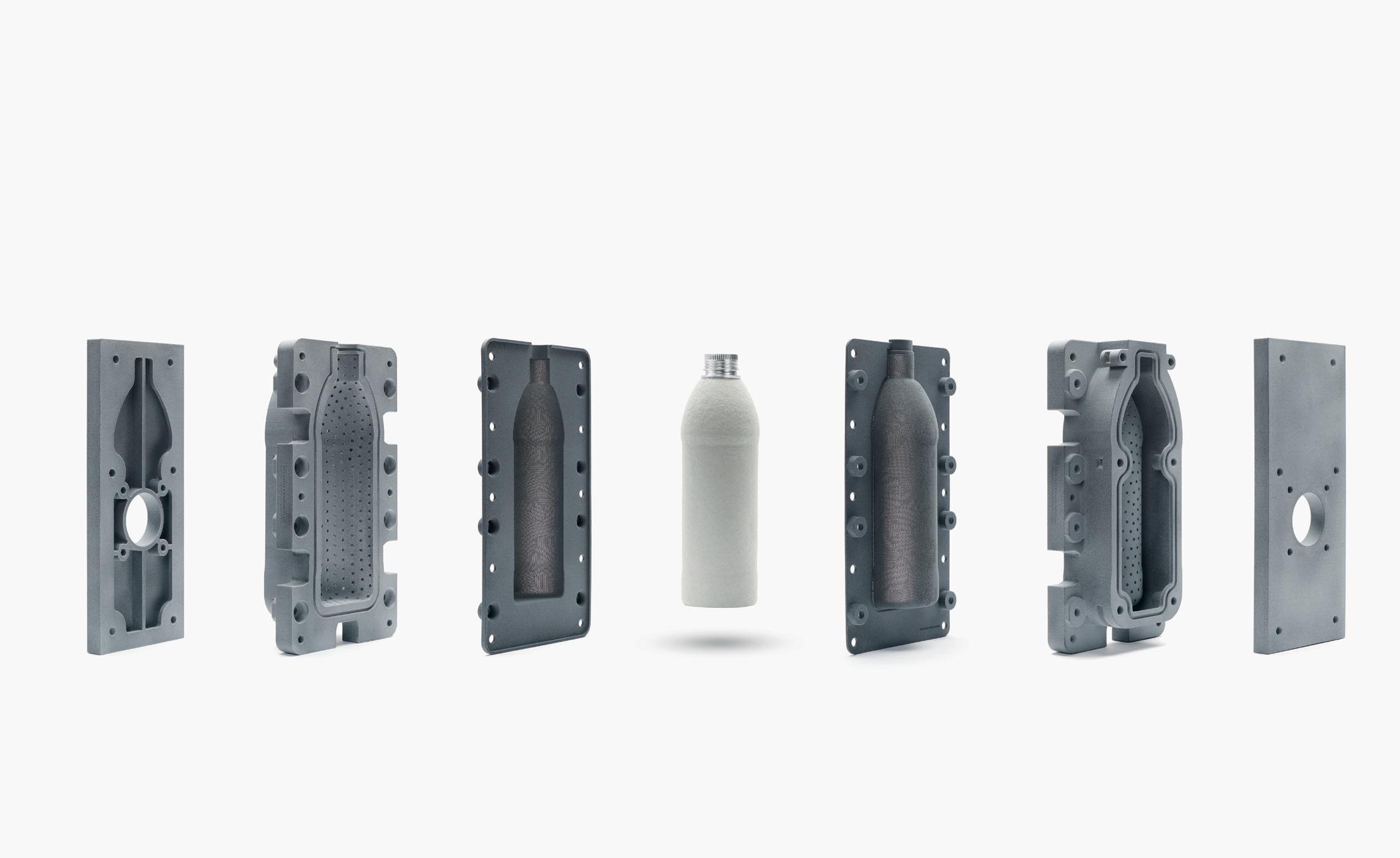
7 minute read
PACKS A PUNCH
from TCT Europe 30.2
by TCT Magazine
WORDS: SAM davies
No matter the industry and no matter the application, for every product that is conceptualised, designed, manufactured, sold and dispatched there is packaging to protect it.
In many respects, it means a separate product has to be developed for every product that is developed. And with that comes considerations around design, cost, time and waste. Yet, too often, packaging is an afterthought.
“The way every single NPI (New Product Introduction) works,” Mariona Company starts, “and it’s the case for HP and the case for any other company, packaging is always the last thing that we decide.”
Mariona speaks as the Global Head of HP’s Molded Fiber endeavours, an advanced tooling business set up to facilitate more sustainable packaging, with a keen focus on the food and beverage sectors. It was born out of HP’s commitment to eliminating 75% of single-use plastic packaging by 2025; single-use plastic packaging – of which more than 150 million tonnes is produced per year – contributes to greenhouse gas emissions all the way through its lifecycle and typically ends up in landfi ll. Having set up the Molded Fiber business, HP is aiming to ‘disrupt’ the packaging market with fi bre-based, 100% plastic-free packaging. The tooling for these packaging solutions leans on the capability of HP’s Multi Jet Fusion 3D printing technology, while Choose Packaging – a zero-plastic paper bottle manufacturer – was acquired by HP and integrated into its Personalization & 3D Printing business earlier this year. HP has applied this solution in-house for products such as its HP Desktop Mini, and is also now working with external customers.
It suggests that more thought is going into packaging and indicates a growing interest from the market in 3D printingenabled solutions.
AHEAD OF THE PACK One packaging company to invest in and integrate 3D printing technology is Quadpack, who purchased a Stratasys J750 in 2018 and a Stratasys J850 in 2019, after starting out with an Objet 30 machine.
Quadpack is a designer and manufacturer of packaging for skin care, makeup and fragrance companies, delivering bottles, jars, product dispensing systems and airless componentry. For at least 90% of the projects it works on, Quadpack turns to this 3D printing capability to help its clients move through the design iteration phase. With its full-colour 3D printing systems, the company can produce multiple prototypes at the same time to explore diff erent design options, while resembling something close to the fi nal packaging product.
“It’s helped package designers to test out new ideas quickly and try out what is likely to work and what isn’t,” Quadpack Senior Designer Oliver Drew tells TCT. “But, in addition, it’s helped to allow the customer to accelerate that development stage of design. Whether it’s for bespoke [products], or for a new catalogue item, it’s helped to avoid the need of having to create a pilot mould sample, which in a lot of cases can take four to six weeks to create the tool. Then, you’ve got to wait to receive the samples [and] if you want them decorated, that’s a separate process in itself. So, being able to 3D print in full-colour, to then also apply the decoration with the right opacities and mixing those two together from an early stage, really helps the customer to visualise what that design could look like in that colour with that artwork.”
SHOWN:
HP MOLDED FIBER PACKAGING MOULDS FOR CHOOSE PACKAGING'S ZERO PLASTIC PAPER BOTTLE
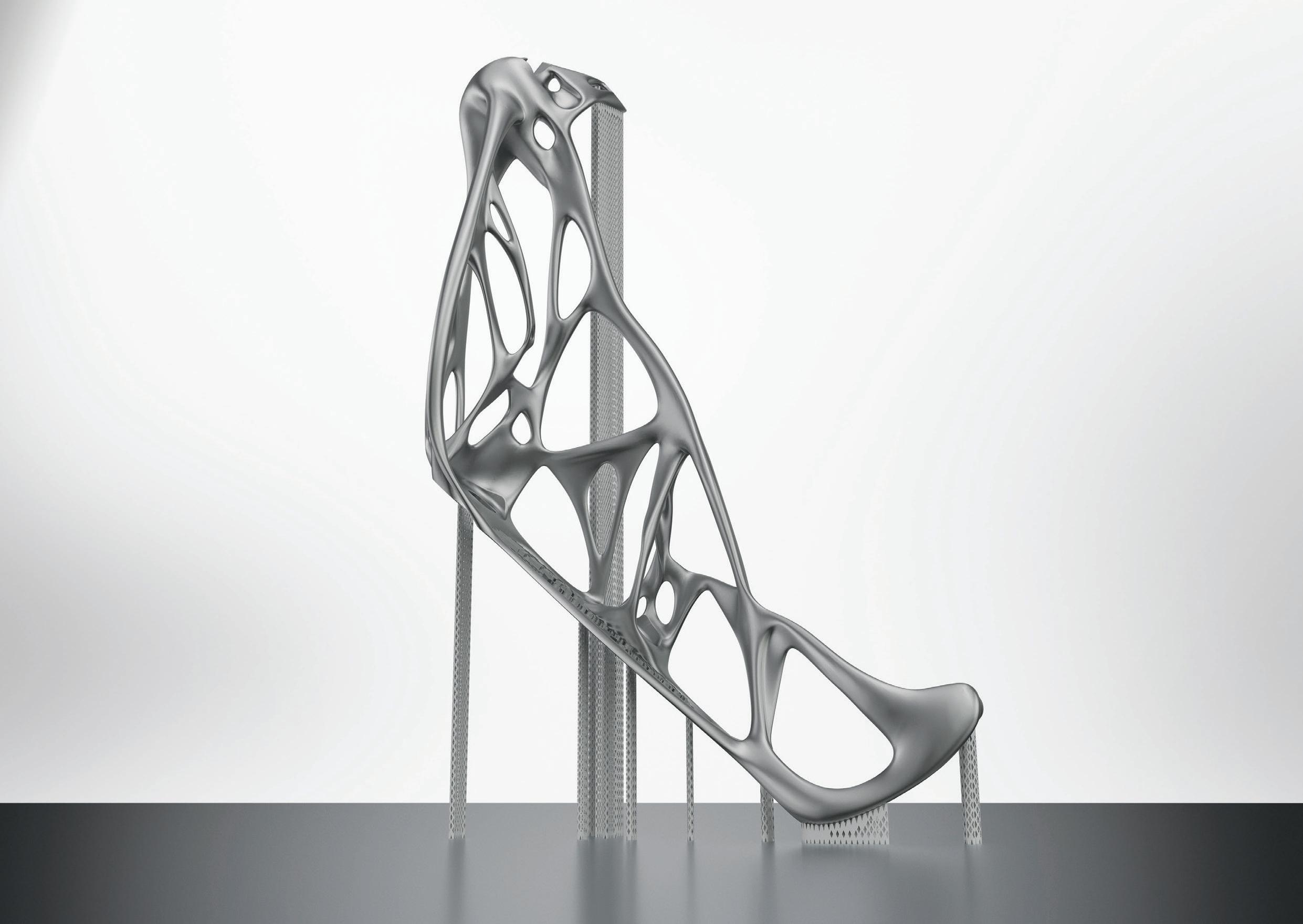
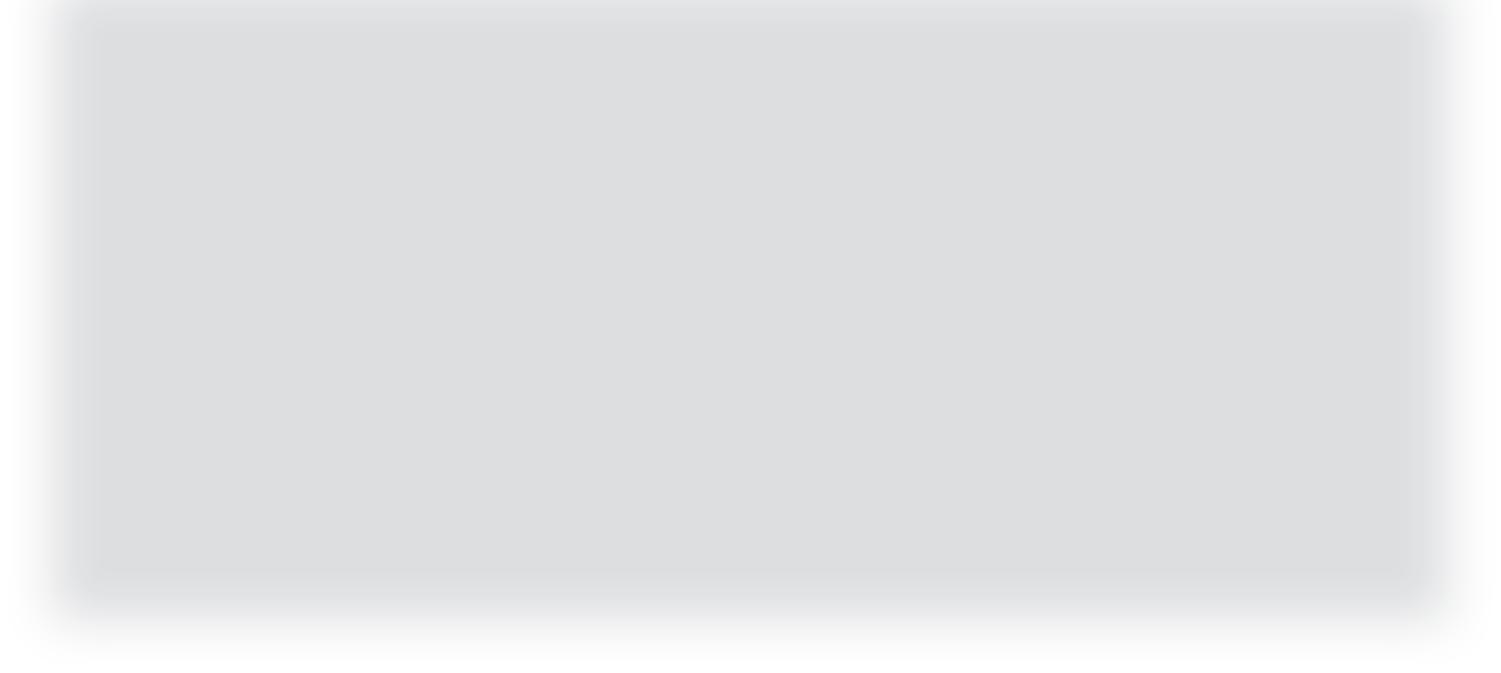
While 3D printing has obvious benefi ts for prototyping applications, the full- colour capabilities of Stratasys’ J Series, for example, make the technology an increasingly attractive option for packaging companies, particularly those working in the beauty and food stuff industries. Mimaki is another company off ering colour 3D printing technology through its 3DUJ-553 and 3DUJ-2207 systems, with the latter available at a list price of 35,000 EUR. Though the company sees its biggest opportunities in the medical, art and fi gurine markets, there is some interest regarding packaging from the perfume industry.
“What we see is that people can have a much faster time to market if they have a 3D object,” says Mark Sollman, Mimaki’s Product Manager EMEA, “because then they can touch it and the process will go [quicker].”
Though Mimaki is seeing some interest from customers wanting to enhance their packaging prototyping procedures, there is some doubt as to whether end- use product applications will emerge in packaging - as they have in other markets - particularly when volume and economics are considered.
HP, though, is confi dent it has found an application primed for additive manufacturing.
TOOLING UP When HP fi rst embarked on its Molded Fiber venture, it took two months for the company to get a design ready and processable on a HP 3D printing system in a Mexico facility. Once it had rode those software issues, however, the mould was successfully 3D printed fi rst time. At this point, the company decided to invest in a cross functional team of engineers, as well as a proprietary workfl ow and design software. This software is said to be capable of automatically creating optimised moulds based on the product’s CAD design, as well as organising a pipeline of job intake to the 3D printers.
What comes out of the printers are three diff erent types of tooling componentry. The HP Advanced Mold Body and the HP Advanced Transfer Tool both reduce the need for sectioning and drilling, while the HP hot swap SmartScreen integrated key features such as wash-walls, block-outs and hold-downs. All are made with an ‘engineering polyamide that is not subject to corrosion or calcifi cation in water,’ and are said to help enable quicker time to market, design fl exibility and effi ciency gains, per Mariona. now it’s getting to this stage of industrialisation. So, for the initial design stages we’ve never really needed to depend on the sustainability of the material because you’re only producing a few components. Whereas, when you start going into the thousands of pieces, you then need to obviously start thinking about the sustainability of the material.”
With that said, and while Oliver acknowledges the design freedom, fl exibility and personalisation profi ciencies of 3D printing, he notes that there are still limitations in material quality and volume capacity. Despite that, HP has teams ‘working with major brands on primary packaging’ products, in which the only way they can be manufactured is with 3D printing. Concerning sustainability, Mariona reminds us of 3D printing’s ability to produce parts locally and on-demand, but maintains that right now the big opportunities for the technology lie in tooling and prototyping.
“I can talk about what I know, which is 3D printing is the future in fi brebased products,” Mariona fi nishes. “This industry has been looking at 3D printing for a long time, it’s just that until now there haven’t been any 3D printing technologies that could address the requirements of such a tough application. If you talk about the rest of packaging, I believe that if you look at the trends on how packaging and the products are being created – less short runs, more customised, sustainability, new products – 3D printing will play a critical role. And it will do because of prototyping for sure, but [also] the bridge to manufacturing.”
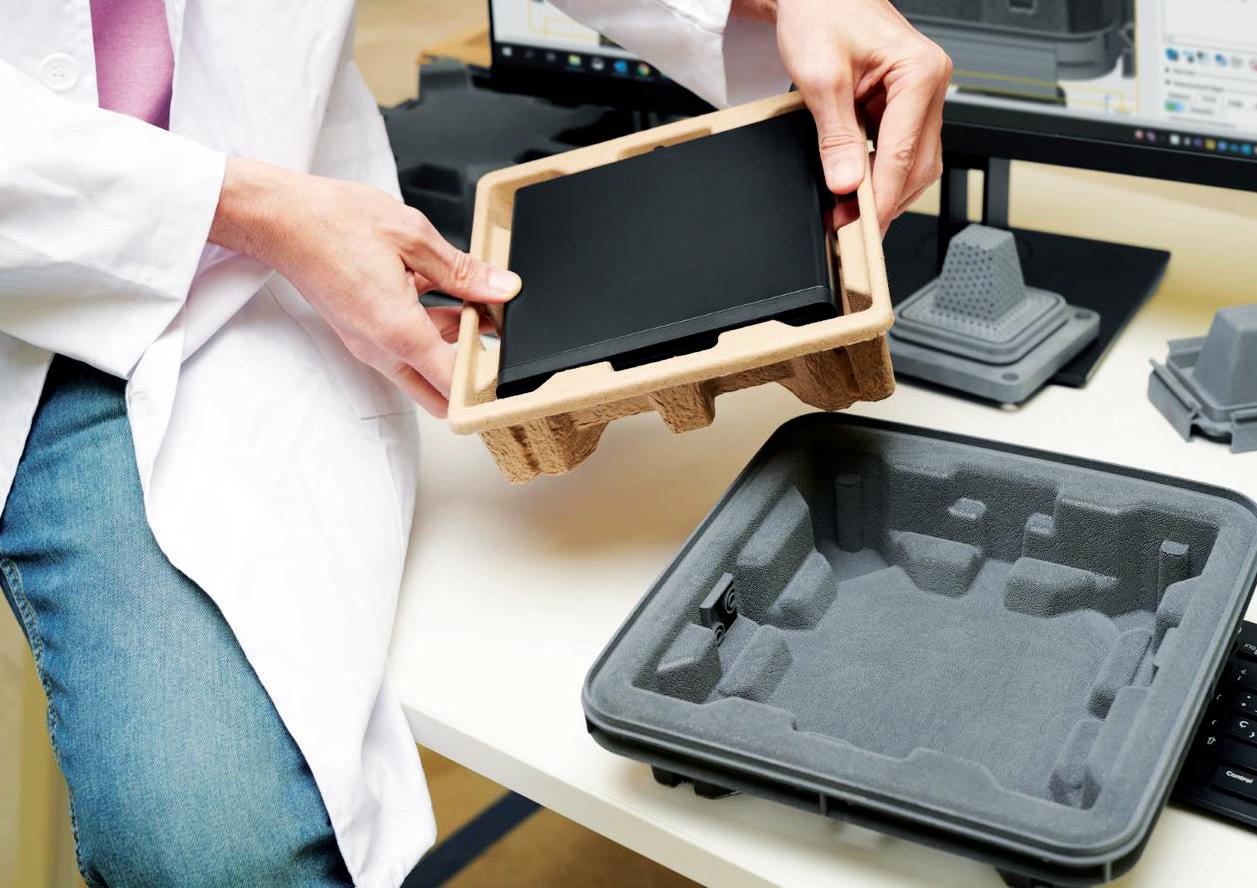
SHOWN:
HP'S MOLDED FIBER PACKAGING MOULDS FOR ITS DESKTOP MINI PC PRODUCT
HP’s internal divisions are said to be lining up to utilise the Molded Fiber solutions, with the company looking to prioritise the products that will represent a transition from plastic foam type packaging to moulded fi bre.
“When you are designing with tooling and fi bre, if you start from the beginning when you design the product, you get better outcomes,” Mariona says. “What we are doing with the diff erent divisions with HP is identifying the roadmap of products that we want to move into sustainable packaging and then working with our engineers in packaging on moving this technology.”
ARRIVING ON THE SCENE HP’s approach to the roll out of Molded Fiber within its own business is in line with that 2025 target, which falls under its sustainability strategy umbrella. Of course, while the end result of HP’s moulded fi bre packaging process might be more ideal than plastics, the sustainability profi ciencies of energyintensive 3D printing technologies have been the subject of much debate over the years. Oliver suggests that 3D printing has been ‘a little bit late to the scene in terms of sustainability’ making a direct reference to materials, though it only becomes a serious consideration when the 3D printing volumes increase.
“We’re determined to make those advances,” Oliver says of sustainability. “We’ve used 3D printing as a way to reduce development time, whereas