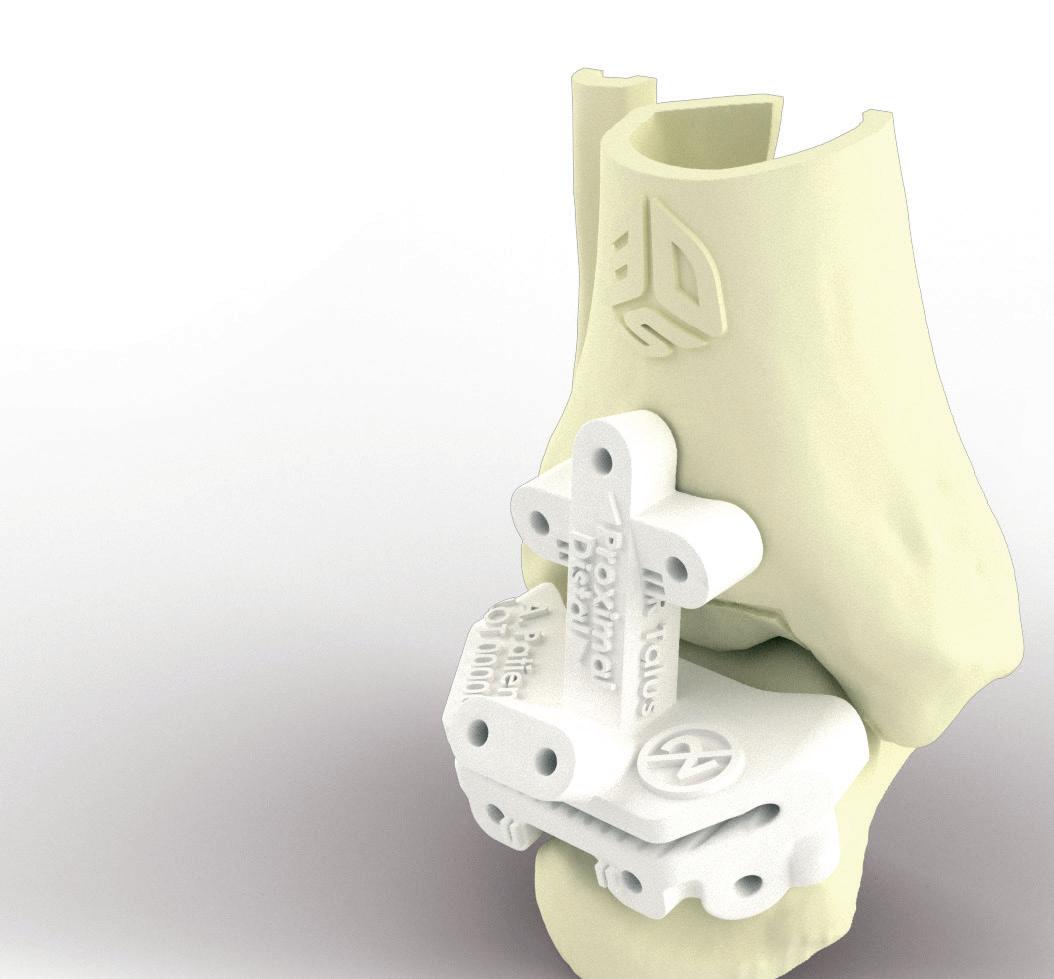
4 minute read
HEALTHY GROWTH
from TCT Europe 30.2
by TCT Magazine
HEALTHY GROWTH WORDS: LAURA GRIFFITHS
Whenever healthcare is spotlighted as one of the most interesting application areas for additive manufacturing (AM), the reasoning, whether coming from industry experts or the public, is typically as simple as this: “At the end of the day, all of us are patients at some point.”
That sentiment was shared by Menno Ellis, Executive Vice President, Healthcare Solutions at 3D Systems in a recent conversation with TCT. The AM leader has been a pioneer in the medical space for almost three decades, with more than two million medical devices produced out of its dedicated FDA-registered and ISO 13485-certifi ed facility in Colorado, and applications that span the gamut from dental devices to planning solutions and regenerative medicine.
Refl ecting on the progress 3D Systems has made in the healthcare space in the last decade alone – a decade that’s seen custom 3D printed spinal cages become an established solution and the total number of delivered patient-specifi c cases and devices reach more than 140,000 – Ellis said: “Initially, there were a number of companies and physicians that looked at [AM] and said, this makes sense, this gets better results, so we're going to adopt but they didn't really have a lot of data to back it up. What's really changed over the course of the last decade is there have been studies that validate the benefi ts of using, for example, surgical planning to plan surgeries and personalised solutions that now validate some of that initial thinking people had. That has obviously helped drive the adoption.”
We speak following a year of expansion and change for the company which included a number of acquisitions, namely bioprinting solutions developer Allevi and most recently, PEEK specialist Kumovis, alongside a change in leadership which saw company founder Chuck Hull taking on the role of Chief Technology Offi cer for Regenerative Medicine. The company also earmarked an additional 50,000 square feet for its Denver facility, scheduled to break ground this year, to accelerate its growth trajectory for patient-specifi c craniomaxillofacial applications and facilitate the development of new joint replacement solutions. “It is back to that theme of personalised medicine,” Ellis said of the expansion. “That’s the part of the business that is growing. Not just within the traditional indications where we started primarily in the craniomaxillofacial space, and continues to grow [...] but now we’ve started to take those capabilities and are talking to the orthopaedic companies around applying that to other parts of the body and are getting very good acceptance as well.”
Developments have been happening across various joint solutions, many still under wraps, but the most recent public advances have been in ankle devices. In 2020, the company received FDA 510(k) clearance for its Vantage Ankle PSI patient-specifi c total ankle surgical planning and 3D printed instruments
SHOWN:
VANTAGE ANKLE PSI VANTAGE ANKLE PSI PATIENT-SPECIFI GUIDE PATIENT-SPECIFI GUIDE in collaboration with Exactech. It’s in personalised solutions such as this, which aff ord better surgeries and patient outcomes, where Ellis says AM truly shines.
“One of the benefi ts additive manufacturing off ers is being able to produce in lot sizes of one [...]. As it becomes more practical, more economical to produce implantable devices for diff erent body types, as well as more complex surgical instruments for point of care systems, that enables practising physicians to think more creatively and more holistically about how healthcare is being applied. It really starts with that ability to personalise by way of additive manufacturing but then goes all the way upstream to the practitioner, really rethinking the way they practice medicine.”
This knock-on eff ect can also be seen in the way the technology is being adopted at the point of care. 3D Systems already has one of the largest publicly known initiatives within the VA hospital system in the U.S., and with the introduction of machines like its Figure 4 technology and a more accessible ecosystem of accompanying software and materials products, the barriers for healthcare professionals have been signifi cantly lowered.
“What we've seen is quite a few groups that dip their toe in the water and are using 3D printers on site to make anatomical models or surgery planning and communications, and maybe to a lesser degree, also some surgical tools, cutting guides, drill guides, things of that nature," Ellis concluded. "But what we've also seen is some occasional reactive moves like, for example, in the past two years, diff erent groups coming up with the ability to print nasopharyngeal [swabs] for COVID testing.
“I really think that we're standing on the threshold of adoption right now. The improved economics, and more environmentally-friendly machines that are easier to operate, promote manufacturing in a distributed environment, combine that with the ease of use of software that really ties everything together to make that happen. [...] We’ve observed some early steps, but that big adoption is really something that we’re right on the cusp of seeing.”
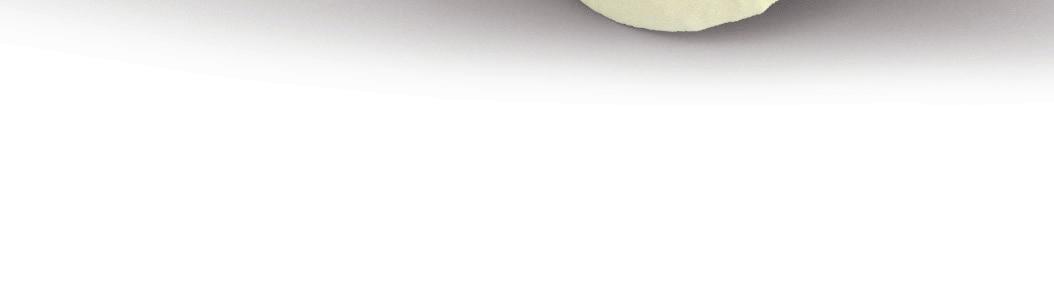