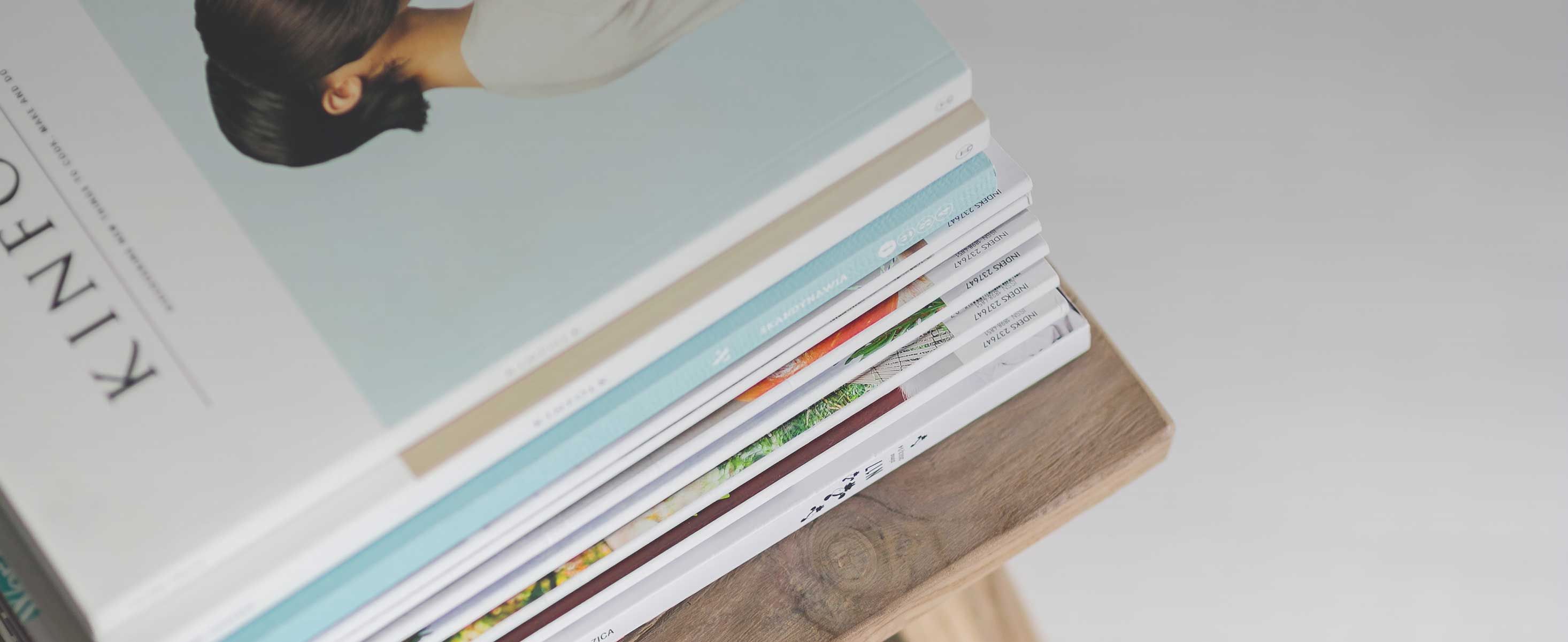
6 minute read
WHAT’S DRIVING AM ADOPTION?
from TCT Europe 30.2
by TCT Magazine
WORDS: Laura Griffiths
WHAT’S DRIVING AM ADOPTION?
The medley of machines, applications, materials, software tools – and confusing acronyms for good measure – can make the task of building a business case for additive manufacturing (AM) feel daunting. It’s why we created TCT 3Sixty’s Evaluation, Adoption and Optimisation framework to help our community identify their place on the AM adoption curve and access the relevant information.
Recent reports from market intelligence specialist CONTEXT and 3D printer manufacturers MakerBot and Formlabs each suggest renewed interest in AM technology, meaning there are likely more users than ever before locating themselves somewhere on the middle of that curve. So how did they get there?
In a survey published by desktop 3D printer manufacturer MakerBot, over the last year, prototyping and concept modeling were, as perhaps expected, still found to represent the majority of use cases for respondents. Yet, one of the most signifi cant takeaways was the number of users who are utilising machines, in some cases multiple, in-house. Over three-quarters of respondents stated that they have at least one 3D printer in-house, with 29% using them daily. What’s more, the report found that 84% of respondents who invested in 2021 also plan to purchase more equipment, materials, and accessories throughout this year.
“Respondents see the benefi ts of using 3D printing to accelerate their design and production processes,” MakerBot’s CEO and President Nadav Goshen told TCT. “As a result, they are citing continued interest in adding more printers to their collection, exploring new materials, and expanding their applications with 3D printing - whether that's for prototyping, tooling, or production parts.”
While just 5% of those asked claimed to be using 3D printing for mass production, applications in R&D, tooling, and replacement parts were said to be on the rise. Throughout the pandemic CONTEXT reported a rise in desktop machine sales as a result of work-from-home scenarios, which MakerBot reacted to with the launch of its CloudPrint software to enable more streamlined remote working and the increase in capabilities for its industrial yet accessible METHOD printer. While offi ces were closed and supply chains were down, 3D printing came to the fore.
“The pandemic highlighted some of the fl aws of traditional supply chains,” Goshen said, refl ecting on the increase. “Shortages in healthcare products led to a surge in on-demand production using 3D printing. By integrating 3D printing, companies gained greater fl exibility to minimise potential supply chain delays by increasing local production. With immediate access to a digital inventory of part designs, replacement or custom components can be produced or iterated upon as often or quickly as needed with little to no additional cost. On-demand 3D printing for prototyping and part production enables manufacturing fl exibility and reduces reliance on traditional supply channels.”
EARLY ADOPTERS VS. RECENT ADOPTERS As detailed in our last issue, the pandemic brought more attention to 3D printing’s unique advantages: the ability to reduce inventory with localised on-demand manufacture, create tooling to mitigate long lead times and augment manufacturing lines with rapidly produced jigs and fi xtures. Formlabs’ report emphasises that AM’s sweet spot remains in rapid prototyping and model making but the company, which
manufactures desktop SLA systems and launched its fi rst benchtop SLS machine last year, also claimed that it’s seeing a trend from more recent adopters who are using the technology for small-batch production and end-use parts.
“Beyond prototyping, 3D printing enables the on-demand creation of custom, on-demand parts to add fl exibility to manufacturing processes,” Juliette Combe, Applications Engineer, Formlabs, told TCT. “For example, 3D printed manufacturing aids, like jigs and fi xtures, are very easy to adopt and already one of the most common applications in the industry. 3D printed rapid tooling, like injection moulds and forming dies, are also a quickly growing use case but one that requires slightly more education for companies that still rely on traditional manufacturing methods for these applications.”
In fact, Formlabs’ results show that recent adopters are moving into these kinds of applications much faster. New adopters were found to be almost twice as likely to frequently print end-use parts compared to early adopters, and 60% are deploying its technology for rapid tooling compared to just 30% of early adopters. “As manufacturers continue to see the durability, variety, and fl exibility of 3D printed manufacturing tools, they will gain confi dence in more advanced applications like end parts for consumers," Combe continued. "In fact, we’re already seeing that recent adopters of 3D printing are using technology diff erently, for diff erent reasons, and are planning relatively large investments moving forward. Of those who have already deployed 3D printing, 76% agree that 3D printing will change product design, 72% agree 3D printing will allow for custom manufacturing tools, and 71% predict 3D printing will become a staple in manufacturing and engineering departments. The pace of investment in 3D printing is growing and manufacturing tools remain a strong initial use case for incorporating 3D printing into manufacturing processes.”
IN-HOUSE OR OUTSOURCE? Another route to AM adoption is through use of a service bureau. New York-based MakeLab, which operates a fl eet of machines including Formlabs Form 3s, has worked with brands from Quip to Silvercup Studios, and MakeLab co-founder Christina Perla believes positive AM application stories in the media are inspiring potential adopters to “take another peak at AM.”
“We’ve seen an increase in interest evolve as the conversations evolve in the mainstream about AM production use cases,” Perla told TCT. “I still see use case validation being the most grey area. There’s an interest, but not the most trust when it comes to production.”
Perla notes heightened conversation around challenges such as standardisation, which will help to build that trust for newcomers,and adds that the introduction of “more industrial equipment and materials” at MakeLab will ultimately open up more opportunities for functional prototyping and production use cases.
While prototyping remains king and ‘low hanging fruit’ applications on the manufacturing line have proven to be an ideal, low-risk introduction to the technology, Formlabs’ report also cites an all too familiar hurdle that new adopters face: fi nding
the right application. Of current nonusers, half claim “lack of use cases” as their biggest adoption challenge, while just under a third of recent adopters cited the same reason for why they may not invest further in the technology. More education is needed around where additive makes sense and the advantages it can aff ord over traditional means. Figures from Formlabs’ report show 57% responders agreed or strongly agreed that their internal 3D printing capabilities are helping to solve supply chain issues, while further global challenges, such as sustainability, which 70% of recent adopters cite as a signifi cant or very signifi cant benefi t of AM, so that understanding is certainly coming through. For those newcomers, Perla adds the following advice.
“The one thing we did from the very beginning of MakeLab - without realising we really wanted to do the scalable tech thing - was build for profi tability and scalability. We inherently built systems surrounding those concepts from the get-go, allowing for easy growth and scalability at this point in time. It started as a simple mind shift to simple workplace workarounds, and then now is digitising into an IP-enabled solution.
“No matter whether you’re building a business revolving around the tech, or you’re utilising the tech for prototyping or production use cases, you really want to be conscious of the cost factors as well as workfl ow. Workfl ow bleeds into supply chain, and you most defi nitely want to make sure that is reliable and scalable.”