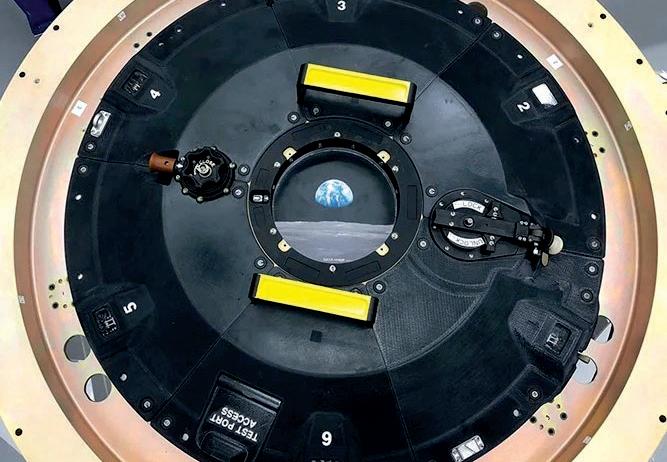
2 minute read
JUMP TO LIGHTSPEED
from TCT Europe 31.1
by TCT Magazine
Oli Johnson speaks to Foster Ferguson, Aerospace Business Segment Leader at Stratasys, about the company's use of Hexagon simulation software for lightweighting aerospace components.
the print, that the tolerances have been met for the designs for the very unique spacecraft.”
Multi-scale models of Stratasys Antero 840CN03 and Antero 800NA have been added to Hexagon’s Digimat materials exchange ecosystem, with associated print parameters from Stratasys’ aerospace-ready 3D printers. The models allow engineers to create digital twins that accurately predict how parts printed with the chosen material and approved aerospace-ready Stratasys printer will perform. According to Hexagon, the parts can be digitally simulated with real-world use-cases and certification tests before any physical prototypes are manufactured. The materials are already being used in aerospace engineering, with Lockheed Martin using Antero 840CN03 to create NASA’s Orion spacecraft docking hatch cover.
The lightweighting of components is key to introducing new sustainable aircraft and spacecraft faster. 3D printed plastic parts can offer benefits in this area, reducing energy use and increasing the range of new aircraft. In November 2022, Stratasys announced that it applied simulation technology from Hexagon’s Manufacturing Intelligence division to capture the behaviour of its ultra-lightweight Antero reinforced polyetherketoneketone (PEKK) and its additive manufacturing processes.
According to Stratasys, the adoption of AM for structural components has remained slow due to the safety-critical nature of the aerospace industry and the regulations imposed on parts. In the original press release announcing their partnership, Hexagon and Stratasys said that by providing engineering teams the simulation tools to validate the materials that will achieve the required part performance, they are supplying the ‘missing link’ which will enable designers to make breakthroughs.
Foster Ferguson, Aerospace Business Segment Leader at Stratasys told TCT: “When you start to talk about the dimensional accuracy and printing to what the standards are looking for, hitting those specifications is really important. Whatever we’re testing, longevity, UV, heat, fatigue, whatever, characterising that data and giving it to the engineer is critical. That’s why the Hexagon Digimat software is so important to the entire process. We want to able to give confidence with the technical proof on the back end of
Speaking about the importance of lightweighted components, such as the ones designed using the simulation software, Ferguson said: “The lightweighting is very important, obviously to engineers who are always looking for ways to save pounds, every pound that you save in spaceflight is very significant in terms of fuel costs. Great aspects of the materials are that they are very fatigue resistant, very strong, and it has electrostatic dissipative properties.”
Ferguson told TCT about the benefits of using simulation software: “Meeting specific requirements and regulations is certainly one of the benefits. There are different regulations in commercial travel and space travel. With space travel you’re more concerned about overall safety issues and making sure that when this thing goes out there it’s going to meet the original design specifications and requirements a customer is asking for. In the past we’ve gone through extensive testing on our