
8 minute read
DESIGN-BUILD ON DFW AIRPORT
from TDSpirit 2019
by TDIndustries
FLYING HIGH AT DFW
See why Khaled Naja chose design-build for DFW Airport’s new DPS office
Khaled Naja, Executive Vice President for Infrastructure & Development at Dallas Fort Worth International Airport, answers how designbuild is helping create the best possible product. 01 What circumstances made this the right project to utilize design-build at DFW Airport?
We used a design-build methodology for Terminal D. What makes this delivery method attractive was that the general building requirements were known. Design-build projects are delivered quicker than the traditional approach of design-bid-build, which was important to us since the officers and staff have been working out of the first building ever built on the airport. It was time to bring a modern, efficient facility to meet the needs of the department, as well as prepare for the future. 02 What are some key features of the new building? How will they help improve officers’ daily routines, and how will they improve safety at DFW?
I heard an interesting anecdotes from Alan Black (DFW Director of Public Safety). If you think back to the 1970s, females in the work force were traditionally in the secretarial pool. The current building was designed and built for the workforce at the time. There isn’t sufficient locker space for female officers and even restrooms are a challenge in the current building. The DPS workforce today is nearly one-third female. The new DPS Headquarters building was planned and designed for the entire expected workforce over the next 25 years.
In June 2017 representatives from DPS, corporate communications, the designbuild team, and our design, code and construction team held a workshop to understand what was important for
the end user. What was surprising was that the main theme was to provide a building that was functional for their operations. They weren’t asking for crazy things, they wanted restrooms and lockers for women, men, and unisex staff. They asked to consider officers’ load; they carry a lot of equipment on their bodies daily, so they would like wider, sturdier chairs, and hooks in restroom stalls that could hold their belts. They wanted a space that they could work safely, collaboratively, and efficiently.
The single most important theme was a space they could be proud to come to work in daily. We believe we’ve delivered on these goals and more. The building was designed and built for future growth. There are several areas for meeting, training, briefing, and just quickly grabbing a cup of coffee. The building has a fitness area that can also hold defensive tactics training and quiet rooms.
03 How did DFW Airport benefit from utilizing design-build on this project?
I think the single most important benefit was schedule. We could design and build this building in about a year. We also benefited from using a model that allowed the design and construction team to bring opportunities for better solutions.
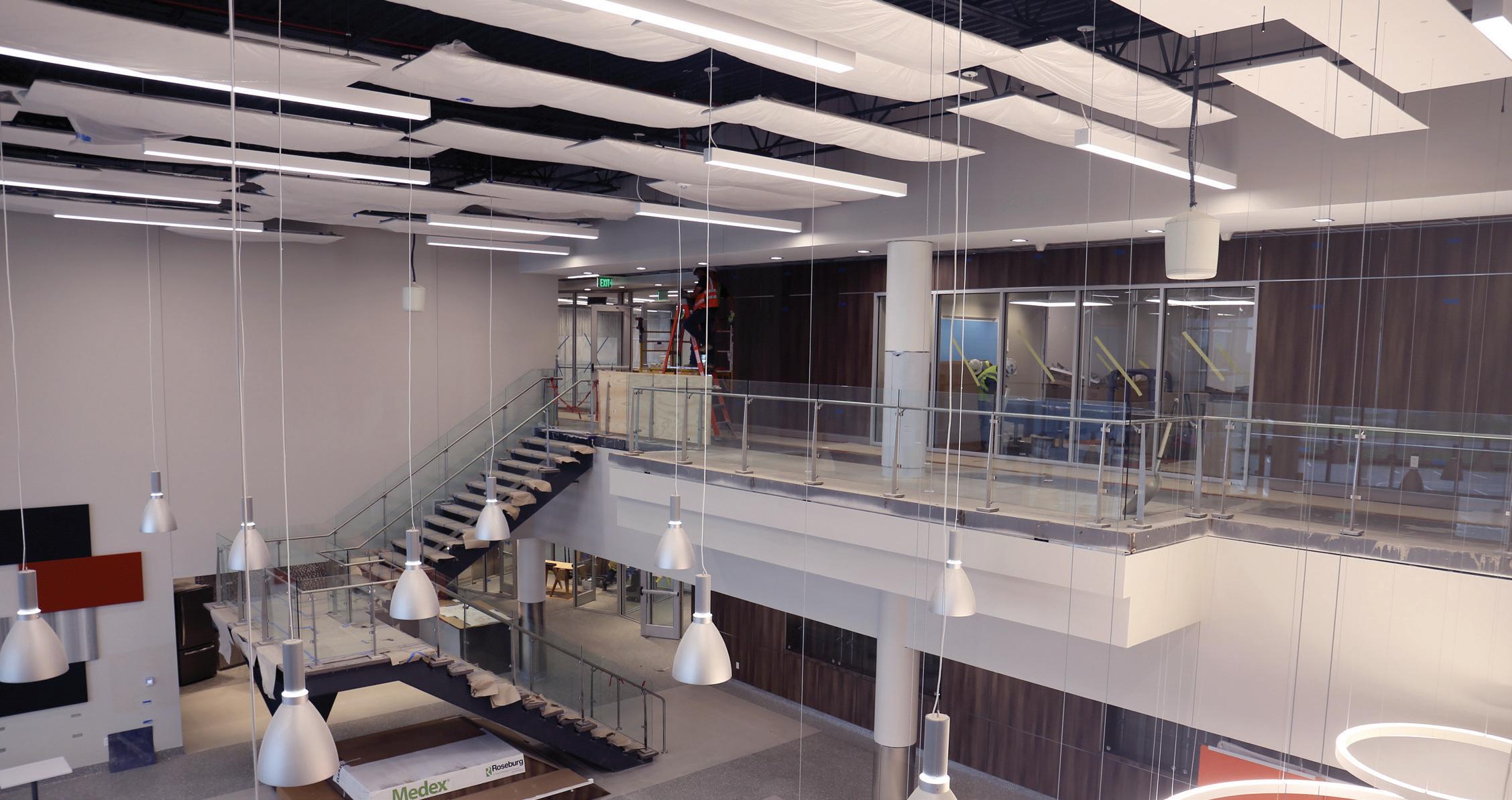
04 Is having a single point of contact for both design and construction an advantage for an owner during a design-build project?
As an owner, you have a single point of contact and mitigate the potential for the finger pointing that can sometimes occur once design is complete and construction is underway. It’s now the responsibility of the contractor and designer to work through solutions together. 05 Design-build projects often boast faster schedules and less variance from the original budget. Did the design-build approach on the DPS Headquarters affect schedule and cost?
The schedule was one of the primary reasons the airport chose to use this delivery method and it proved to be successful. We are tracking on budget. I think one of the reasons the budget and schedule are trending positively is because DPS leadership really took to heart the need to make decisions quickly and while there were some concessions that were made, they also made sure to prioritize their desires and needs. Their responsiveness and diligence was critical to the design build team being able to proceed as quickly as they could on the project. 06 Do you anticipate utilizing the design-build process on future projects at DFW Airport?
We never rule out any delivery approach. We are considering how this approach can be used on civil projects, like TxDOT. 07 What would you say is the best design-build advantage over designassist or plan-spec projects?
I think the collaboration is up there. Having a single point of contact is critical. Having a clear understanding of the need, a stakeholder willing and able to make decisions, and a designbuild team who communicates often is critical to the success of the project.
NEW ROLES, NEW VALUE
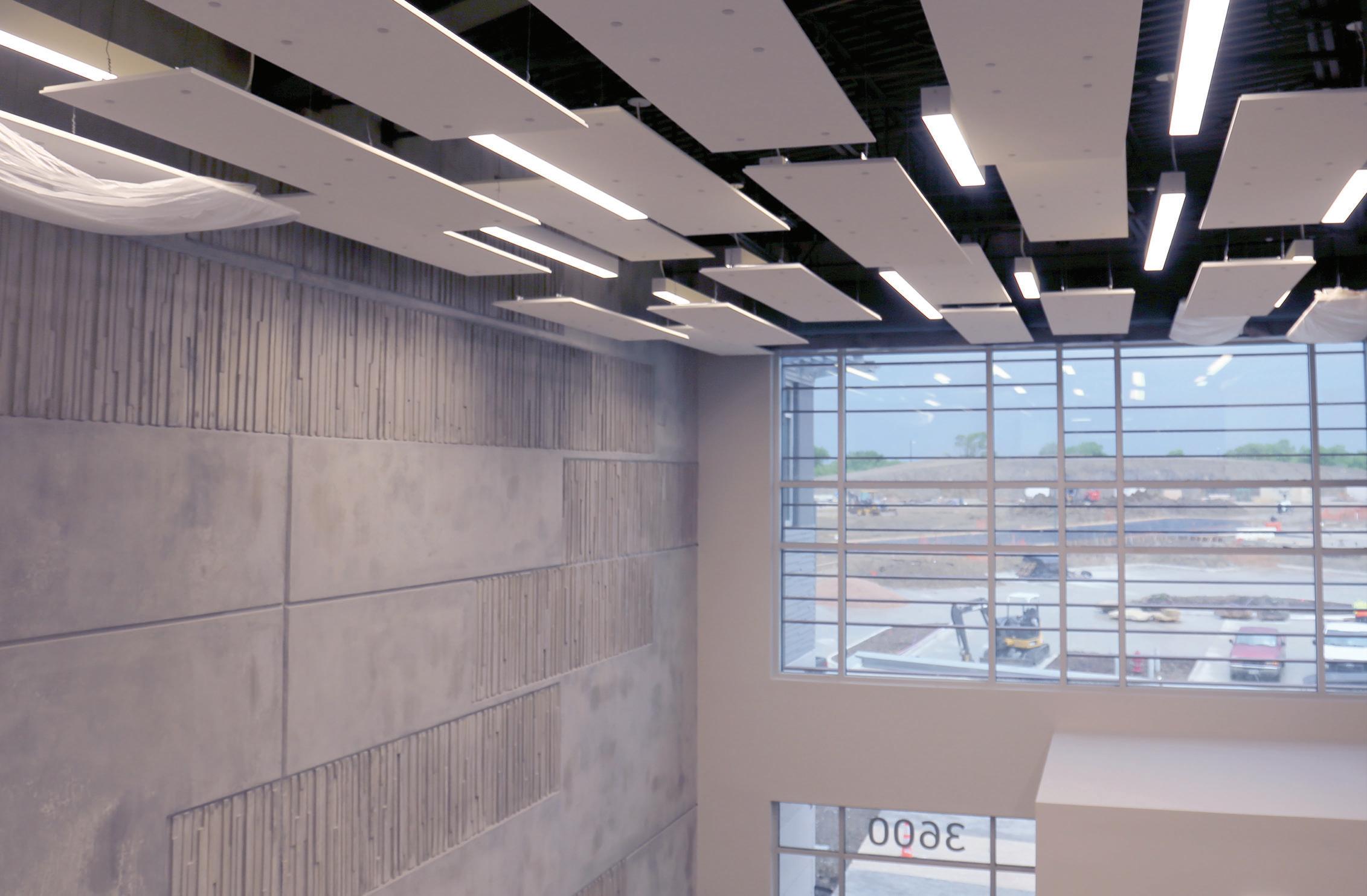
General contractor JE Dunn talks teamwork, value of design-build at DFW’s DPS project
Chris Peck, Senior Vice President of JE Dunn’s Dallas branch, discusses the general contractor’s role in a design-build team. 01 Does JE Dunn have a prior history of utilizing the design-build approach? If so, on what types of projects?
JE Dunn has a long history in completing design-build projects. We have successfully completed projects of all types from Department of Public Safety buildings such as the DFW project to office buildings, warehouses, manufacturing facilities, medical office buildings, dental clinics, parking garages and many others.
Our clients have included public entities such as DFW Airport, the U.S. Army Corps of Engineers, multiple universities, the General Service Administration, along with numerous private clients. 02 Design-build projects, by their very nature, are collaborative and innovative endeavors. What were some examples of contractors (GCs and subs) and the design team providing added value through discussion and innovation?
The biggest advantage in the designbuild collaborative delivery is the ability to deliver the design in a more efficient manner. Rather than taking the normal phased approach to design with concept, schematic design, design development and construction documents our team identified what information was truly required to support construction starting early and allowing material procurement to begin.
We developed what we called a “super schematic” set of documents that allowed the team to guarantee the project GMP 10 weeks after the initial kick-off meeting. This approach of not being constrained by industry standard milestones proved to be very successful.
The other advantage to having trade partners on board in a design-assist role with our team was the ability to make early decisions about mechanical system choices. The TD team was able to provide cost information that we could include in a total cost of ownership model that allowed DFW Airport to make a valuebased decision about the use of variable refrigerant flow HVAC system that will ultimately save the airport significant operating cost. 03 How does the role of a general contractor change on a design-build project?
The biggest change in design-build for the general contractor is the management of the design. On Construction-Manager-atRisk (CMAR) or traditional bid projects, we are working together with our design partners but we are not in control of the schedule or coordination.
With design-build you need to be in tune with all team members, whether it is the architect or one of their consultants or the trade partners installing the work, as the design-builder you are ultimately responsible and accountable for all members of your team. 04 Building Information Modeling (BIM) and Virtual Design and Construction (VDC) techniques are essential to designbuild projects. How did these tools help move the DPS project forward?
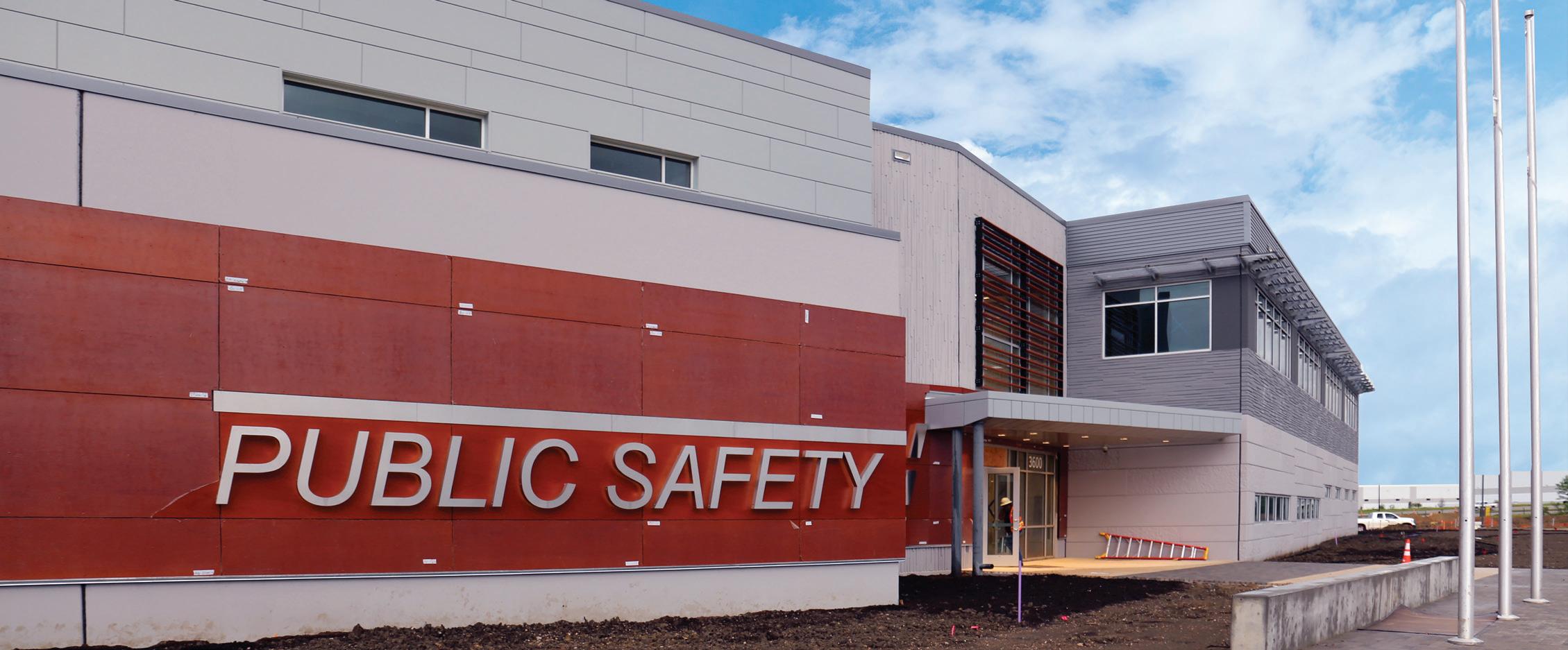
The use of BIM and VDC continue to make the construction of our projects more efficient in the installation. The ability for team members to have coordinated things virtually allowed the work to flow extremely smoothly.
05 Can you discuss the natural tension that may exist between the contractors and design professionals on a design-build project? Is this tension productive and how do you manage it?
This natural tension is a good thing; we are all working hard to ensure that the client is provided with the best possible project through a painless process. The only way that we know how to manage the process is through constant open communication. The issues that arise and create tension are normally from a lack of trust or understanding of the financial aspects of the project. We provide complete transparency with our budgets and estimates, which allow our design partners to understand how they can provide the best possible solution for the dollars allowed.
06 What advice would you give to other general contractors considering the pursuit of design-build projects at DFW Airport?
I would tell them that it is way too difficult and they should probably avoid it at all cost – just kidding!
Design-build delivery requires certain skill sets and behaviors from project participants that are different from designbid-build or CMAR delivery. The designbuild team leader must understand the design process and have the ability to manage the overall design-build team.
Additionally, a successful design-build contractor needs to have experience with early engagement of trade partners to maximize the target value design approach. Understanding that pro-active engagement of the various DFW Airport stakeholders is a must. To be successful, a designbuilder must make sure that they are communicating with all stakeholders for the project. DFW airport includes many entities that have a stake in the project.
Each of these groups needs to be engaged to understand how the project will be executed and how the process may be different from the normal process, and that the overall outcome is to provide the best possible product for them, the end client. 07 For a general contractor, what are the advantages of pursuing a designbuild project?
Design-build delivery offers cost and schedule advantages over traditional delivery methods, such as design-bidbuild and CMAR. Design-build allows the reduction of design schedules through better alignment of design and preconstruction activities without compromising the iterative process of design.
From our perspective, design-build is a more collaborative process resulting in better budget control that can foster fasttrack delivery of the construction phase. Being able to offer solutions that are faster, more cost effective with better cost certainty is a differentiator for a contractor with a design-build acumen.
08 Are there any other thoughts regarding design-build which you would like to share?
The architecture, engineering and contractor community is moving rapidly toward project delivery solutions that will deliver buildings faster and cheaper. The design-build process, due to its collaborative nature, leveraging technology and prefabrication for instance, makes this goal more attainable than traditional delivery methods.