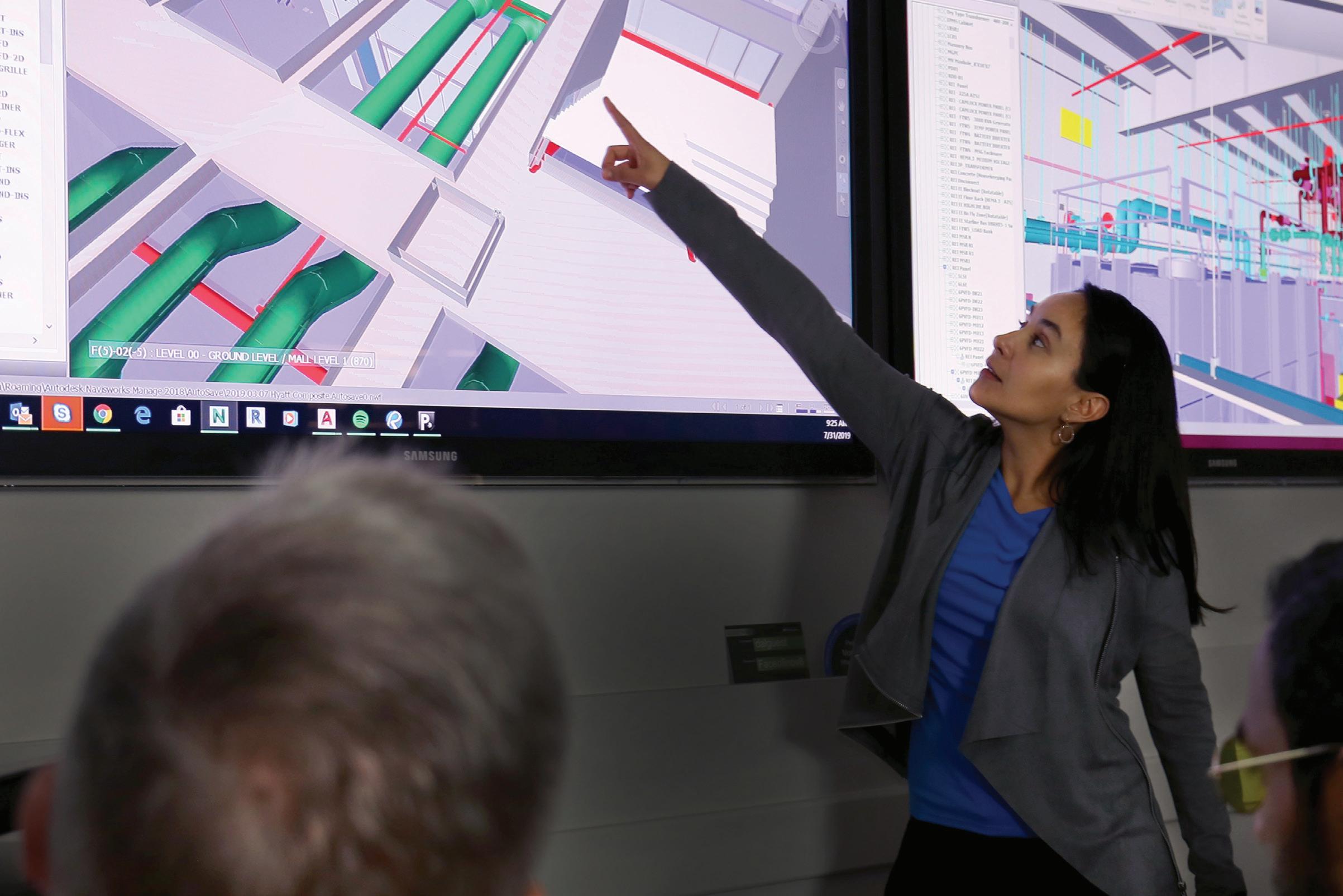
2 minute read
EARLY TRADE INVOLVEMENT
from TDSpirit 2019
by TDIndustries
SPEAKING THEIR LANGUAGE
Why cross-party communication is crucial on today’s projects
Your last project was a headache. You selected the best architect and contractors, but the schedule ran long, costs grew throughout the project, and now your annual maintenance expenses are more than you expected.
What went wrong? The answer is simple: a failure to effectively negotiate between design intent and installation/ constructability issues. That’s why early collaboration is critical.
In traditional builds, team members are sometimes unable to step outside their responsibility zones to increase value for the project. For example, consider an executive and architect looking at floor plans. The executive might decide he wants to swap his corner office for a meeting room closer to the rest of his employees. It’s a simple change for the architect, but it will require additional changes in ductwork, diffusers, and controls on each conditioning zone for the MEP contractor. That has a cost, and without early, detailed discussion between design and contractor segments in a design-build group, the costs may be significantly higher than necessary.
Including contractors in the design process can be advantageous in avoiding unintended consequences.
That’s why early collaboration between engineers and construction teams is critical to avoid a scope gap, to maintain a budget, and to streamline the schedule. “The combination of engineering knowledge and construction experience applied to problem solving simply generates better outcomes than either team working in isolation,” said Engineering Vice President Justin Bowker. “Challenges must be approached addressing all of the owner’s project requirements including quality, budget, and schedule.”
Here are a few ways a contractor can enhance projects through early involvement:
Apply field experience: Historically, architects do a great job solving the big design issues for owners; however, small cost and efficiency gains sometimes aren’t discovered until construction teams join the project. Large-scale

rooftop installations which require helicopter lifts have a cost and schedule impact during the summer because those crews are fighting wildfires.
VDC/BIM management: When all phases are discussing changes to the building model, the contractors can identify the impact on their upcoming tasks immediately. Construction teams can reroute labor until the issue is solved, holding off rework and driving down overruns.
Full life-cycle thinking: The construction process is just the front end of decades spent in your building. TDIndustries has business units dedicated to service, maintenance (120 million sf under contract), and renovation, including one arm that monitors data from more than 70,000 tons of central plants.
Broader options: Contractors coordinate directly with vendors and, when included in decision-making, can provide solutions adapted to specific equipment capabilities, find savings, and use in-house experience to install systems as the manufacturer intended. Many contractors also use prefabrication, assembly systems, and modularization to lower costs and increase quality. In most cases, these strategies are more cost effective – especially when tailored specifically for unique pieces on the jobsite.
Better decision-making: Traditional builds can sometimes leave coordination and implementation until late in the construction schedule. By that time, deadline urgency eliminates many options. Concise and transparent decisionmaking process documentation allows all stakeholders to understand the factors to consider resulting in better decisions with fewer changes later in the process.
“In today’s fast-paced construction environment, it’s imperative that we communicate quickly and effectively,” states Bowker. “The complexity of today’s construction projects requires teams to be structured in a way that encourages collaboration.
“Design-build is the best structure at delivering predictable outcomes and reducing risk to the owner.”