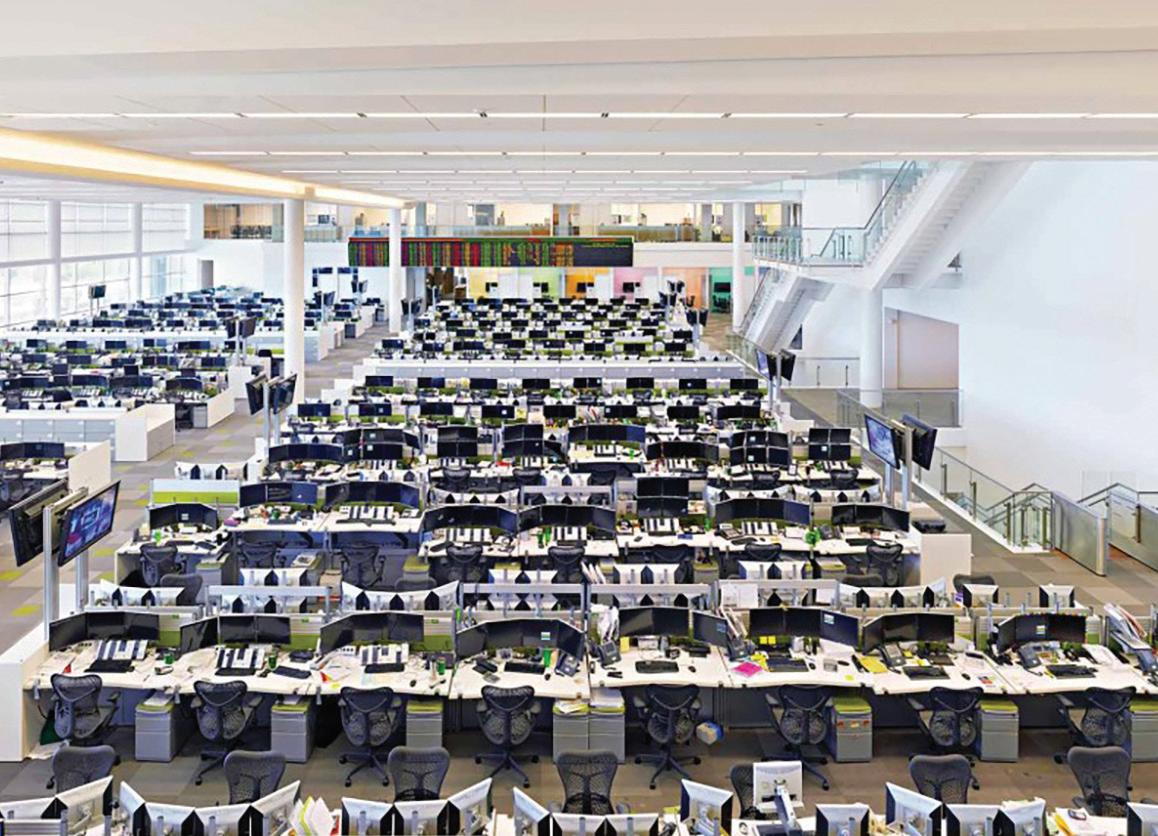
2 minute read
FLEXIBILITY AT BP
from TDSpirit 2019
by TDIndustries
FAST, EFFICIENT PROJECT AT BP
Collaboration helps renovation stay flexible
For TD’s Houston construction team, being part of the BP office design-build project helped solve problems and the decision-making process in a faster and more efficient manner.
The collaborative workspace project included two entire floor buildouts (16th and 17th floors at 22,000 sf per floor) on BP’s Westlake campus in Houston. From start to finish, TD ran an eight-man sheet metal crew, a two-man plumbing crew and a two-man piping crew on this 26-story building. Substantial completion was achieved in mid-June.
A project like this often involves constant changes, including the scope of what certain areas are intended to be and occupancy fluctuations. Design-build can help with those changes, offering an insider point of view and the ability to have instant, offline conversations with engineers. A standard project would require going through the typical chain of command and the general contractor, which could take 2-3 weeks.
“That is an advantage,” said Michelle Reyes, TD Project Manager. “We can strategically figure out items and conflicts prior to presenting them to the entire teams – including the owner and architectural teams.”
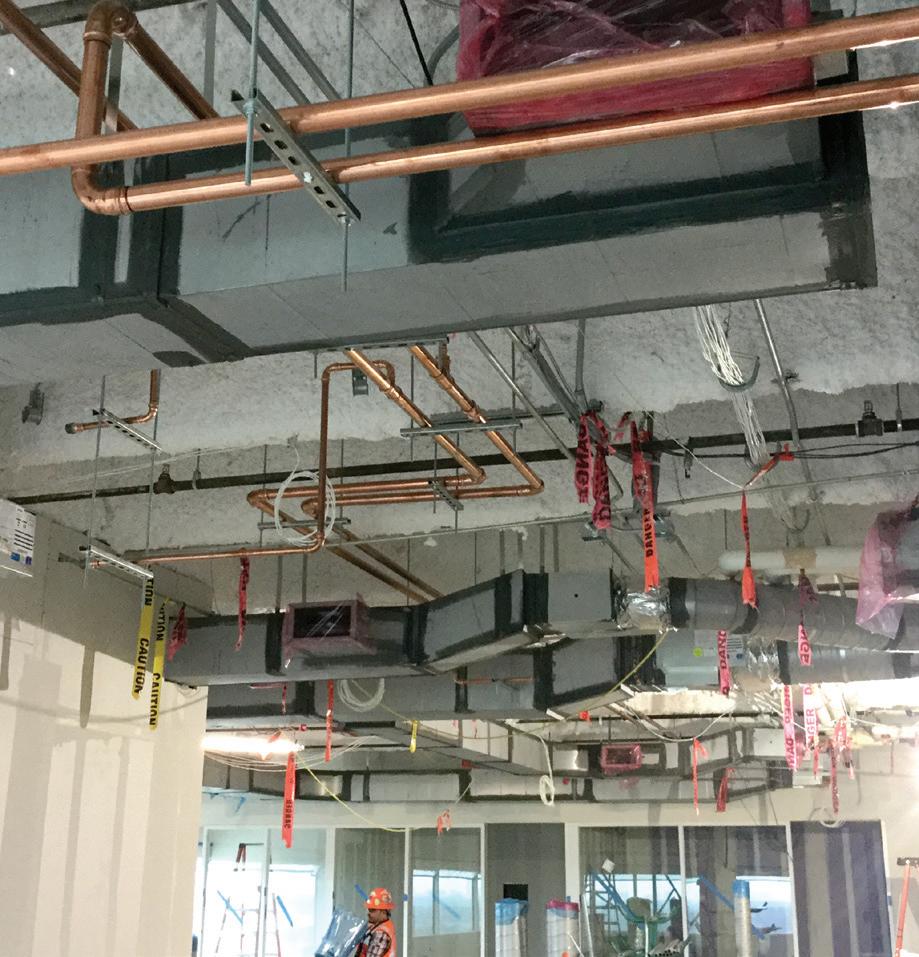
Work on the 16th floor of this building presented its own challenges: executives are using the 15th floor. Any construction noise often led to work shutdowns.
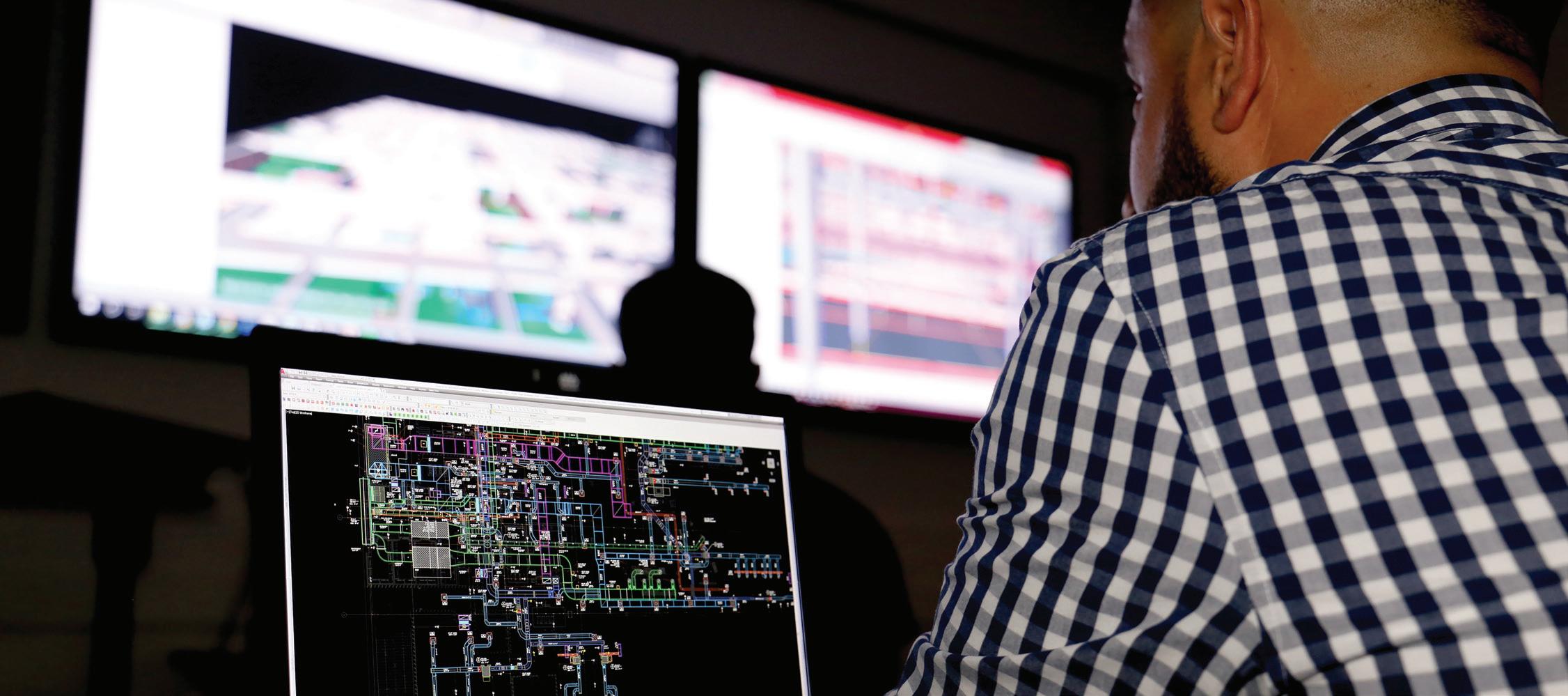
To avoid this issue, the TD crews switched operations to a nighttime schedule to achieve productive work. TD also assembled the ductwork offsite to reduce onsite noise. It was shipped flat from TD’s Dallas manufacturing operations to TD’s Houston assembly shop, and then shipped assembled to the job site. This eased delivery coordination, which normally required 48 hours’ notice to the owner, BP. Another challenge included lifting 38,500 lbs of duct work to the 16th and 17th floors from the loading dock, which is part of a basement-level area that has been under construction due to Hurricane Harvey flooding. TD had to coordinate deliveries of 18 wheelers of ductwork with all other contractors on site.
“Being that there are now two projects nearly complete with the same Rogers O’Brien (Houston) team, these designbuild projects have established an outline,” Reyes said. “Having that history, the only modifications are building owner-suggested or required. That is the best advantage, knowing the expectations and construction standards to be expected.”
Of course, this project wouldn’t have been possible without some key teams, including Phoenix Insulation, who was recently named TD’s Houston Hard Hat Award Recipient.
The general contractor for the project is Rogers – O’Brien and the architect is PGAL, both of whom have successfully worked with TD in the past, across different types of projects and in other branches.
Thank you to these valued teams.

Fast Facts
Size of project: 44,000 sf (two floors) and 496 occupants
TD’s scope: Mechanical and plumbing systems
Completion: Summer 2019
Project partners: Phoenix Insulation (TD’s Houston Hard Hat Award Recipient), Rogers-O’Brien, PGAL
Key TD leadership: Project Manager Michelle Reyes, Superintendent Chad Hubenak, SVP Ronell Peters; engineers Esmeralda Morales (P.E.) and Jeff Farley (P.E.)