
3 minute read
VALUE THROUGH ANALYSIS
from TDSpirit 2019
by TDIndustries
CHANDLER REGIONAL
Advantages Of Early Design-Build MEP Involvement
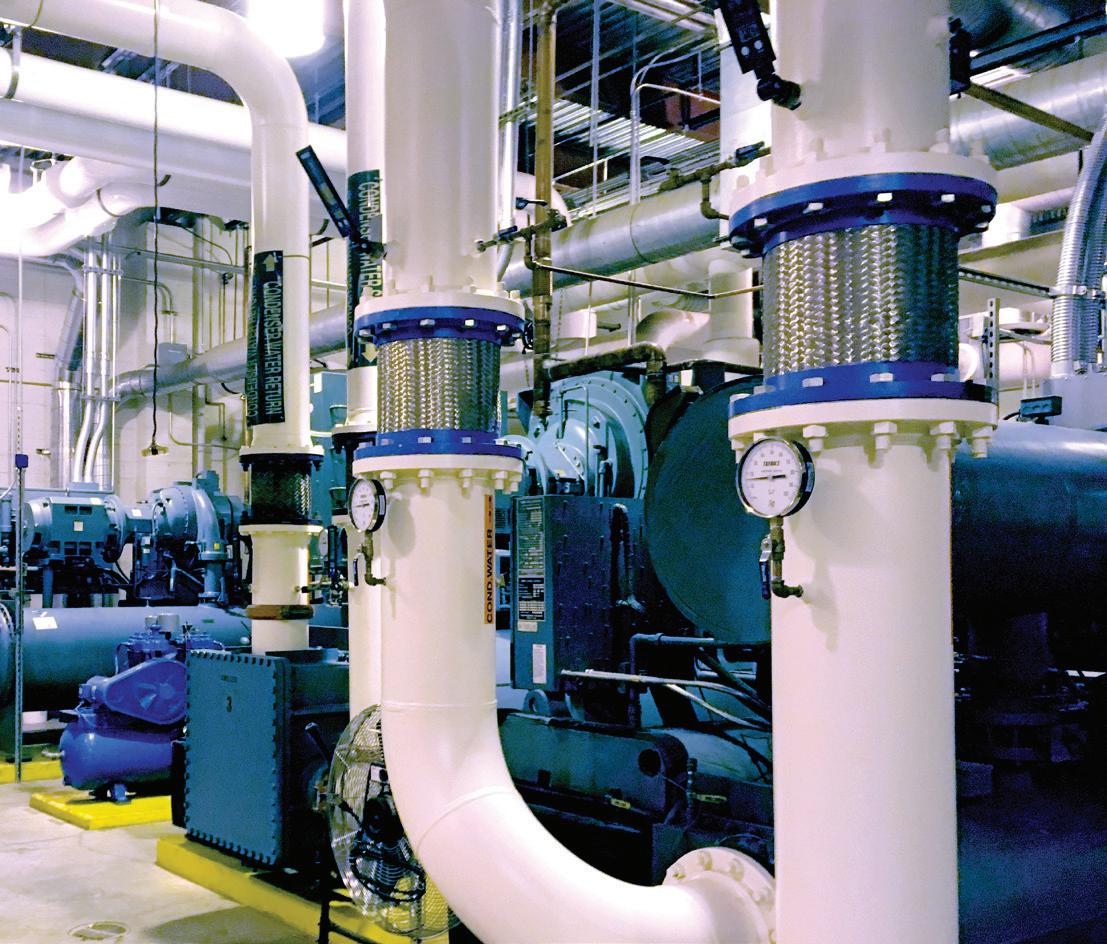
Experience is invaluable when tackling a multimilliondollar project. As with all similar ventures, the earlier those voices can be heard, the better. It only makes sense to include the contractors who will be doing the physical installation during that phase. Dignity Health did just that at Chandler Regional Medical Center in Arizona, which is in the midst of an expansion. “It is a spatially tight MEP project, and requires a high level of expertise,” said Engineer Ardas Sabuncuyan. “We have the HVAC and plumbing design and installation knowledge that traditional design teams often do not own, so we’re all working together to accommodate compressed schedules.”
TD is producing advanced coordinated models prior to permitting, which allows fabrication and construction to begin faster and speeds up the entire project. With an aggressive
design schedule, engineering firm WSP partnered with TD on engineering efforts. WSP knew that TD had the experience to ensure the schedule and constructability remained at the forefront. TD is working with Devenney Architects and the rest of the design team to pull-plan the entire design effort from schematic designs through permitting. To streamline the design process, TD’s engineering and VDC coordinators work in the same Revit model with the design team, allowing simultaneous design and coordination.
The result is a design at construction documentation level that is spatially coordinated and constructible. This allows the design schedule requirements to be met, while also producing a model that could go straight into shop drawing and fabrication drawing production.
That kind of work product would not have been possible without the early involvement and collaboration of the trade partners.
TD’s experience in design-build hospital construction is helping with:
Helping owner make smarter decisions:
TD submitted several A3s to encourage collaboration with multiple trades, allowing for smart decisions on chiller selection, shower-valve configuration, and pharmacy ceiling system.
Coordinating construction documents:
Working with a design engineer, TD created the conceptual design and virtual, coordinated documents for permit. This eliminates the traditional double work of completing these separately, while saving money and reducing time.
Solving space crunch with constructible
plans: Functional plans for floors with multiple architectural challenges were designed, while keeping installation in mind. The design, VDC, and field teams created typical MEP strategies for each floor to ensure consistency and installation ease.
Saving costs through prefabrication:
Knowing its manufacturing capabilities, TD has designed the mechanical and plumbing systems to fully use prefabrication and equipment skid options.
Finding additional value through
coordinating design: A plan to standardize the plumbing in patient restrooms, as well as med-gas and dialysis ports on the headwalls was recommended to the customer, which improved installation schedules.
Mitigating future risk: TD is modeling the future underfloor sanitary piping on the shell level 5 to ensure that the level 4 overhead will accommodate future expansion.
Reducing RFIs: Design-build projects shift work-order changes from expensive end-stage costs to the design team, reducing project cost and duration. This process reduces the number of 2-3 week RFIs and replaces them with 3-day model revisions.
Perhaps the greatest advantage is having this input up front with cost in mind.
“Before the first shovel hits the ground, we have an open-cost model, submittals, and buyout packages ready,” shared Engineer Doug Rohrer. “With the designbuild model, we can work with vendors to kit typical rooms, identify and prefab typical components, and schedule labor more accurately. The owner knows what they’re getting and when they’re going to get it.”
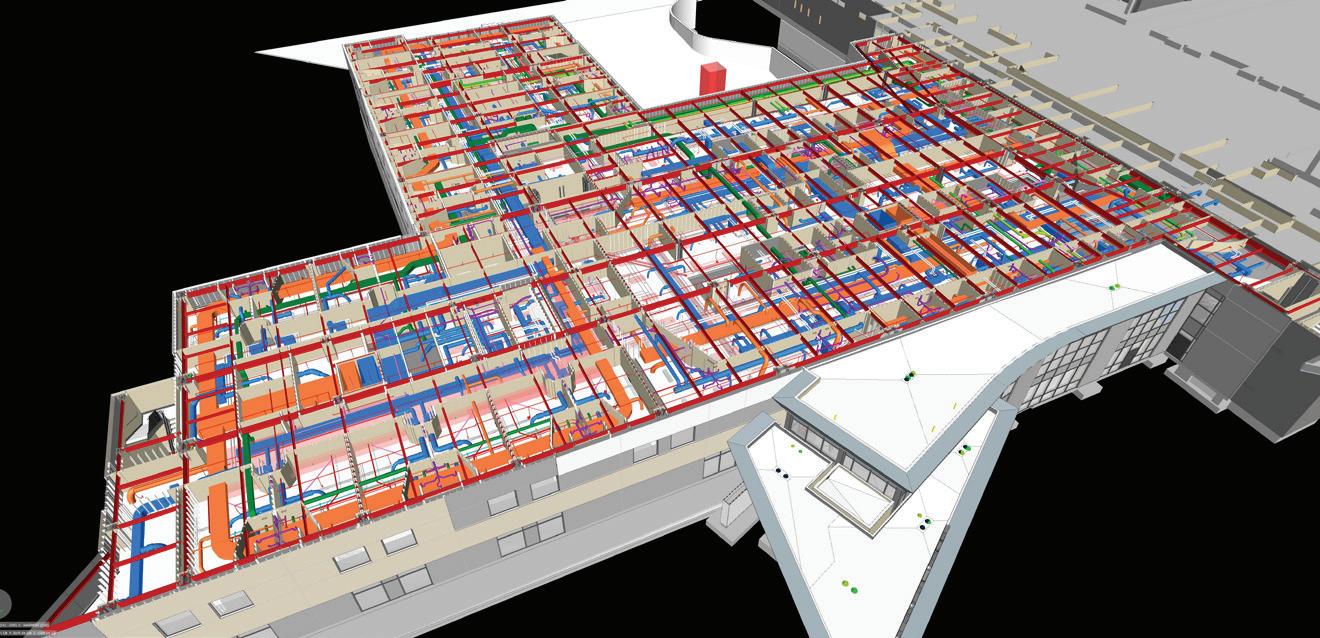
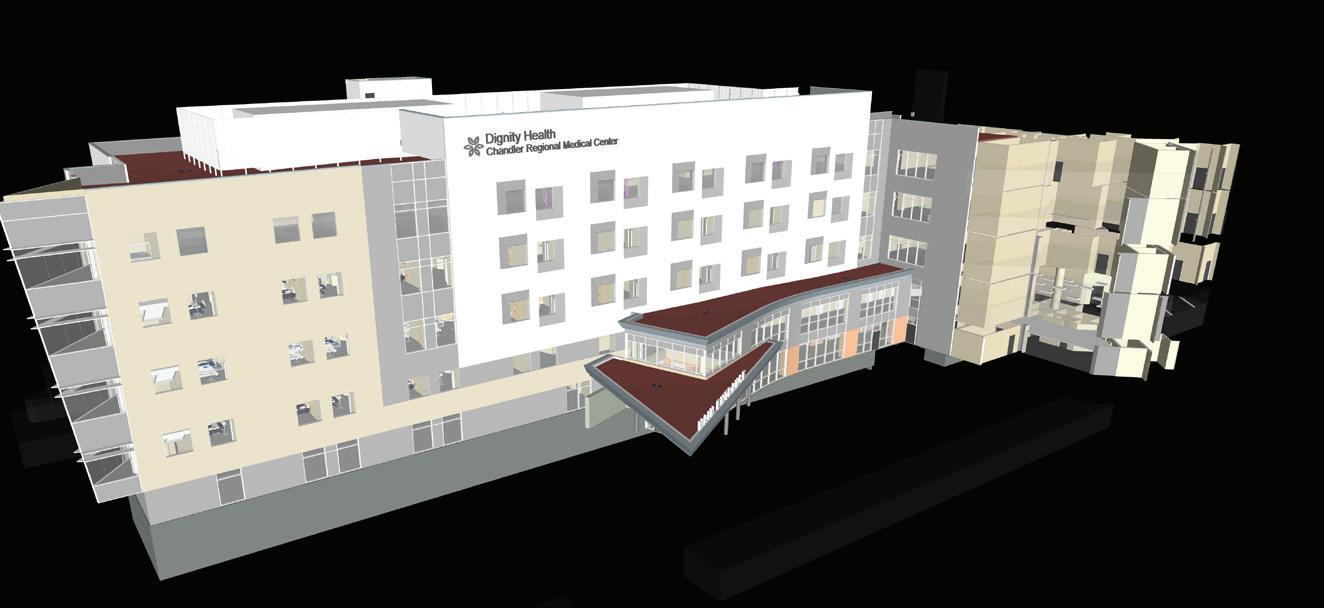
Fast Facts
Size of project: 220,000 sf
TD’s scope: Mechanical, plumbing, and med-gas systems
Anticipated completion date:
Early 2021 Amenities: Cardiac rehab rooms, PACU (post-acute care) and Thoracic patient rooms, ORs, central sterile, pharmacy, shell space Project partners: Dignity Health, McCarthy Building Companies, engineer WSP, Devenney Architects Key TD leadership: Engineers Ardas
Sabuncuyan (P.E.), Doug Rohrer (P.E.), and Fred Henke (P.E.); Superintendent Doug Wallace; SVP of Operations Jay Layton