
16 minute read
Figure 4-7 – Gross margin of Poultry VC
Gross margin
The gross margin for the VC is estimated at around 26% of turnover (see Figure 4-7)
Figure 4-7 - Gross margin of Poultry VC
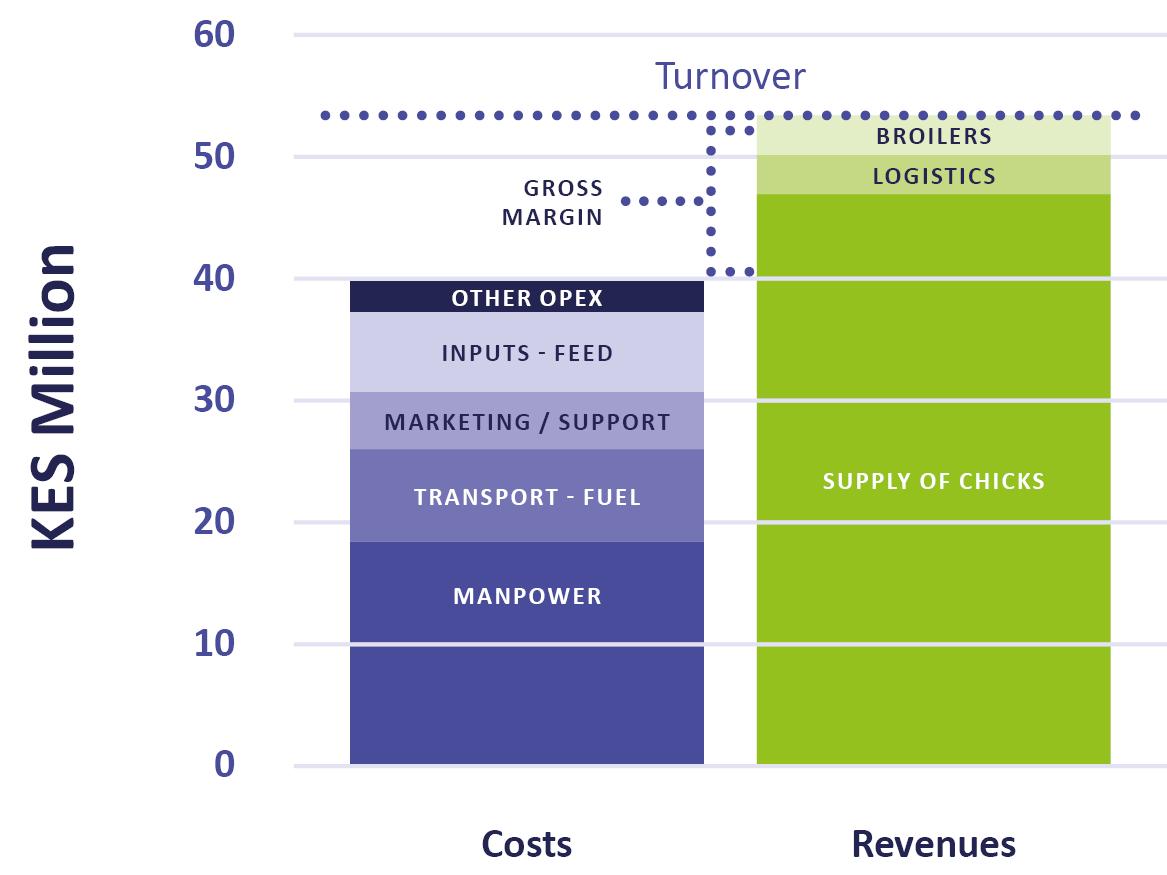
Source: Atkins, 2022
4.2.2.4 Recommendations and Need Assessment
Enabling Business Environment and/or Other Catalysts
The key to this VC is to support poultry farmers in raising production and productivity, and improving logistics across the sector between hatcheries, farms, feed mills and slaughterhouses. The VC then needs to cooperate closely with all significant players in the sector, including farming cooperatives, feed suppliers, hatcheries, aggregators, and slaughterhouses. The recommended approach to facilitating this cooperation is detailed in section 4.2.1.
In particular, the VC could partner with Shiffa Chicks, working with them to expand poultry farming and increase broiler supplies to the Chwele slaughterhouse.
Infrastructure Assessment
Water and wastewater infrastructure
Water is needed for watering and washing of livestock, washing of trucks, cleaning of processing equipment, and staff hygiene. Water consumption varies depending on the level of automation and the cleaning practices. Around 0.35 litres of water will be required per day-old chick35 . For a hatchery producing 1,000 day-old chicks per day this would equate to a water consumption of 0.35 m3/ day. Additional water is required during the slaughtering process, this is around 20 litres per chicken36. Therefore, the abattoir at Chwele currently uses around 100 m3/ day of water to process 5,000 chickens per day.
The hatchery will employ 60 people who are estimated to use 50 litres per person per day (double the volume for administrative workers37 as additional water is needed for hygiene practices associated with working with food products). Water requirements for employees is estimated at 3 m3/day.
35 The Poultry site, Designing a hatchery’s water system (2017),
Available at: https://www.thepoultrysite.com/articles/designinga-hatcherys-water-system, (Accessed: 20/01/2022). 36 The Poultry site, Poultry processing: measuring true water use (2014), Available at: https://www.thepoultrysite.com/articles/poultryprocessing-measuring-true-water-use, (Accessed: 11/01/2022). 37 Ministry of Water and Irrigation, Practice Manual for Small Dams, Pans and
Other Water Conservation Structures in Kenya (2005) Available at: http:// smalldamsguidelines.water.go.ke/technical_reports/ (Accessed: 22/10/2021).
This gives a total water requirement of around 3.35 m3/day.
Demand for water across the County currently exceeds supply and is unreliable due to high electricity costs, therefore it is unlikely that this water will be available from the public water supply, so there is a need to develop a water source for the hatchery. This is likely to be a borehole and a treatment plant. The use of renewable energy should be investigated to power the borehole pump. There will be a need for water storage in the system to cover interruptions in supply to ensure the value chain can continue to operate. The size of this will depend on space and costs. However, we recommend a reserve capacity of five days’ water supply. This equates to a reserve capacity of approximately 16.75 m3 and would build resilience into the system.
It is assumed that a maximum of 85% of the water used (2.85 m3/day) will be discharged as wastewater from the hatchery. At the Chwele abattoir, approximately eight litres of wastewater are produced per bird during slaughtering and packing38. It is therefore estimated that a total of 40 m3/ day of wastewater would be produced when slaughtering 5,000 chickens. Wastewater from the abattoir would be high in biochemical oxygen demand (BOD), chemical oxygen demand (COD), total organic carbon (TOC), total nitrogen (TN), total phosphorus (TP) and total suspended solids (TSS). There is a potential to use the wastewater from the hatchery in a micro AD facility, organic matter and the wastewater would be mixed to create a slurry. The final wastewater will need to be treated using tertiary methods before it is discharged into the environment. Effluent from staff toilets should be discharged into a septic tank and later transported to the Bungoma STW for further treatment. Sludge from the septic tank could be incorporated with the organic material used in the micro AD facility on site.
38 FAO, Management of waste from animal product processing (1996). Solid waste management
Assume all organic waste can go to animal feed or micro AD onsite. Guano, eggshells, feathers etc. could be processed by AD to generate gas/power which could be used by the facility.
Waste from staff and any other waste should be segregated into recyclable, organic and non-recyclable. Recyclable waste to go to local/national/international processors, organic waste to AD and non-recyclable to a local landfill.
Energy infrastructure
Based on the anticipated size of the facility, the general power and lighting demand for the buildings and process load could be in the region of 400-450 kW (including a heat demand of around 120 kW) depending on the type and efficiency of equipment installed.
The energy demand would mainly be for cold storage, operating the automatic slaughter line, water pumps, and cooling fans. Energy may also be needed in the poultry houses for warming up the flock, depending on weather.
The production chain features processes that require a significant amount of process heat and steam. Electric equipment should initially be considered for this (i.e. high voltage electrode steam boilers), as other fuels, such as natural gas, LPG, oil or wood, have significant issues around supply chain logistics, including sourcing, cost and stability, as well as environmental issues around deforestation and greenhouse gas emissions. There is an opportunity to utilise waste streams from this project in an anaerobic digestion (AD) plant that could provide both heat and power to meet some of the site’s energy demands, but this proposition would need to be developed further in a subsequent stage to check whether there is enough waste volume to make these options a feasible proposition. If a biogas plant is considered to be feasible and will be implemented, then the design and installation should comply with all relevant safety guidelines to minimise risks associated with gas storage39 .
In the urban centre of Bungoma the grid is fairly limited and not very reliable, however, in Webuye there is a major 132 kV substation that feeds the local region. The final location of the facility is yet to be determined, but if located close to the Webuye 33/11 kV substation there should be enough spare capacity and a suitable 11 kV grid supply should be available which can be extended to the site to provide the facility with a dedicated connection, however, this needs to be confirmed by KPLC. The processing facility will have an 11/0.4 kV distribution transformer on site (1 x 500 or 630 kVA capacity depending on the energy solution for the thermal demand).
Grid unreliability and power costs are major issues with respect to the successful operation of the plant. A well-implemented power resilience solution will allow the continued operation of the plant regardless of events on the local power grid.
39 German Agricultural Occupational Health and Safety Agency, Safety rules for biogas systems (2008) Available at: http://www.build-a-biogas-plant.com/
PDF/safety-rules-for-biogas-systems-2008.pdf (Accessed: 19/05/2021).
The solution here would consist of the following:
1. On-site energy generation. Solar PV should be installed on the site to reduce reliance on the grid and reduce electricity bills. An appropriate installed capacity would be around 110 kW. This would require an area of about 725 m2. This could be located on building roofs and possibly some standalone solar arrays if needed. This output will be reduced during cloud cover and at night, so the grid supply will still be sized to cover the peak demand, however, PV could reduce the cost of grid electricity by up to KES 58,000 per week. 2. Voltage regulation. Spikes, sags or fluctuations in voltage supply can cause damage to equipment and disrupt operations. Regulation equipment integrated into the distribution transformer at the incoming voltage will protect the manufacturing equipment. 3. Battery storage. This should be included to help with any extended power cuts. Lead-acid batteries are appropriate technology for this environment. An appropriate storage capacity of around 760 kWh would provide a suitable level of business continuity. 4. Uninterruptible power supply (UPS) would be needed to instantaneously bridge between any power cuts and the battery storage. The battery storage, voltage regulation and UPS equipment would require a dedicated building on site of roughly 13 x 5 m (65m2).
As the process has very limited general waste output (aside from that for the AD plant) waste to energy is not a viable proposition. High efficiency motors and drives and other low-energy equipment such as LED lamps should be installed throughout to ensure the demand is at the lower end of projections. The plant operation should also ensure it has budgeted maintenance programmes to cover items like regular cleaning of PV panels, servicing of motors, fans and coils and replacing equipment when its performance begins to degrade. Transport infrastructure
Transport services would need to be offered between the hatcheries, farmers, and end markets and slaughterhouses. Agrovets can also potentially act as aggregation centres where farmers can place their orders for day old chicks and the agrovet places bulk orders with the hatchery and collects the chicks on behalf of the farmers. Vaccination of the chicks can also be bundled in the service. Once mature, the birds or the laid eggs can be collected by rural aggregators directly from farmers who assemble them in bulk before transporting in large consignments. All-weather access roads will be required to these farms to facilitate access. For offtake of old layers and broilers from non-contract farmers, the livestock markets can serve as natural aggregation points by tapping into their pre-existing network of suppliers.
An alternative system is being developed by Shiffa Chicks, under which chicks, feed, and other inputs would be provided through dedicated aggregation centres to out growers, collecting mature birds on the back haul. This system would reduce overall transport costs, while allowing Shiffa’s extension officers to monitor the operations of the farmers, providing additional inputs and advice where required.
The government regulates the means of transportation used for DOC and also the movement of spent parent and grandparent stock. Current practice amongst farmers usually involves the use of public transport and taxis to deliver their poultry to market, however, this goes against regulations. Specialized pick-up trucks designed for poultry transportation with an upper and lower carrier should be considered. Transporters of poultry are also required to obtain a certificate of transport (COT) issued by the veterinary officer to the owner of the carcass as well as movement permits.
The output from the farm is expected to generate one refrigerated truckload per day. A paved road access to the plant well linked to the national transport corridor, A8 will be essential. Environmental Assessment
The VC involves the development of a fully-integrated chicken, egg and meat processing industry in the County. Total space required, based on a new hatchery and supporting services, is estimated at some 2,900 m2. An EIA is hence required to ensure the development does not cause detrimental effects40. The following issues should be considered during the decision-making process:
> The spatial requirements for poultry rearing are minimal, hence offering no significant land use competition to other VC projects. Minimal land requirement reduces pressure of limited land and therefore pressure on environmentally-sensitive assets. > Disregarding the slaughter process, the VC would require a low volume of water, around 0.35 litres of water will be required per day old chick. Low water demand for production is beneficial to the environment as it reduces pressure and potential overexploitation of water resources. > Given the level of energy demand (450-500 kW), on-site renewable energy systems shall be installed to provide a proportion of the energy need and supplement the grid supply. > The VC will lead to centralized production of organics (especially from the slaughterhouse) like guano, eggshells, feathers etc. which could be processed by AD to generate gas/power which could be used by the facility. > There is a potential to use the wastewater from the hatchery in the micro AD facility. The final wastewater will need to be treated using tertiary methods before it is discharged into the environment.
40 Natural Environment Management Authority, Environment Impact Assessment (EIA) (2022). Available at: https://www.nema.go.ke/index.php?option=com_ content&view=article&id=119&Itemid=144, (Accessed: 17/02/2022).
> The significant increase in traffic flows that would result from the integrated chicken farm would increase the carbon footprint of the local farmers’ community. > There is a potential for the landscape surrounding the integrated chicken farm to degenerate as a result of odours, flies, and rodents. > The site selected should not be in proximity to noise and air-sensitive receptors. This is due to noise produced as a result of operating the machines and potential odour from the flock and chicken waste (guano) if not managed properly.
Climate Resilience
This VC has an initial target input of 0.5 million total flock, 22.5 tonnes per day chicken feed (8,250 tonnes/year) and 5,000 chickens to be slaughtered per day (scope to increase to 8,000 per day). This is 20% of the total number of chickens in the County (around 2.5 million41, although discussions with Shiffa Chicks indicate that the actual number may be significantly lower than this). Around 80-100% of the County’s population is involved in poultry production, mostly at a small-scale42 which provides a strong base, however, issues surrounding high supply costs, high transport costs and dependence on unimproved varieties cause difficulties in maintaining the supply of chickens. This VC is rated as medium sensitivity to climate change, however, there is potential to strengthen the poultry sector and supply of chickens in the County, for example through improved delivery and collection services, which would reduce the sensitivity of this VC. Key climate risks for poultry production are high temperatures and increased rainfall. High temperatures and heat stress reduces the potency and shelf life of vaccines and antibiotics and can reduce growth rates and increase mortality rates. More space is needed when transporting chicks during high temperatures to avoid mortalities during transportation and the quality of meat is reduced. High rainfall impacts transportation by inundating roads, and can lead to an increase in the prevalence of diseases such as coccidiosis and mild hypothermia, requiring treatment and thereby increasing the cost of production. Waterproof packaging is also required during periods of heavy rainfall to reduce transport losses43. Rainfall is projected to increase during the short rains (late July – December) and mean annual temperatures are projected to continue to increase, as well as the total number of hot days with maximum temperatures equal to or above 35°C and night-time temperatures which could impact poultry production in the County. This VC is rated as having medium exposure to climate change. Adaptation strategies44:
> Commercial hatcheries and use of incubators for hatching chicks; > Use of commercial feeds; > Use of solar heaters for incubation; > Increased availability of deep freezers to store vaccines; > Construct modern poultry structures or upgrade existing structures; > Education and training on available technology, administering vaccines, application of social media as a means of selling; > Increased cold storage; > Installing temperature regulators on trucks and vans; > Improvements to road networks; and > Use of drone transport.
Overall, this VC has a low vulnerability to climate change. Providing suitable adaptation measures are included during inception, it is not expected that climate change will negatively impact this VC.
41 Ministry of Agriculture, Livestock and Fisheries, agricultural datasets. Available at http://kilimodata.developlocal.org 42 MoALFC. (2021). Climate Risk Profile for Bungoma County. Kenya County
Climate Risk Profile Series. The Ministry of Agriculture, Livestock,
Fisheries and Co-operatives (MoALFC), Nairobi, Kenya. 43 MoALFC. (2021). Climate Risk Profile for Bungoma County. Kenya County
Climate Risk Profile Series. The Ministry of Agriculture, Livestock,
Fisheries and Co-operatives (MoALFC), Nairobi, Kenya. 44 MoALFC. (2021). Climate Risk Profile for Bungoma County. Kenya County
Climate Risk Profile Series. The Ministry of Agriculture, Livestock,
Fisheries and Co-operatives (MoALFC), Nairobi, Kenya.
Gender and Social Inclusion Assessment Case study
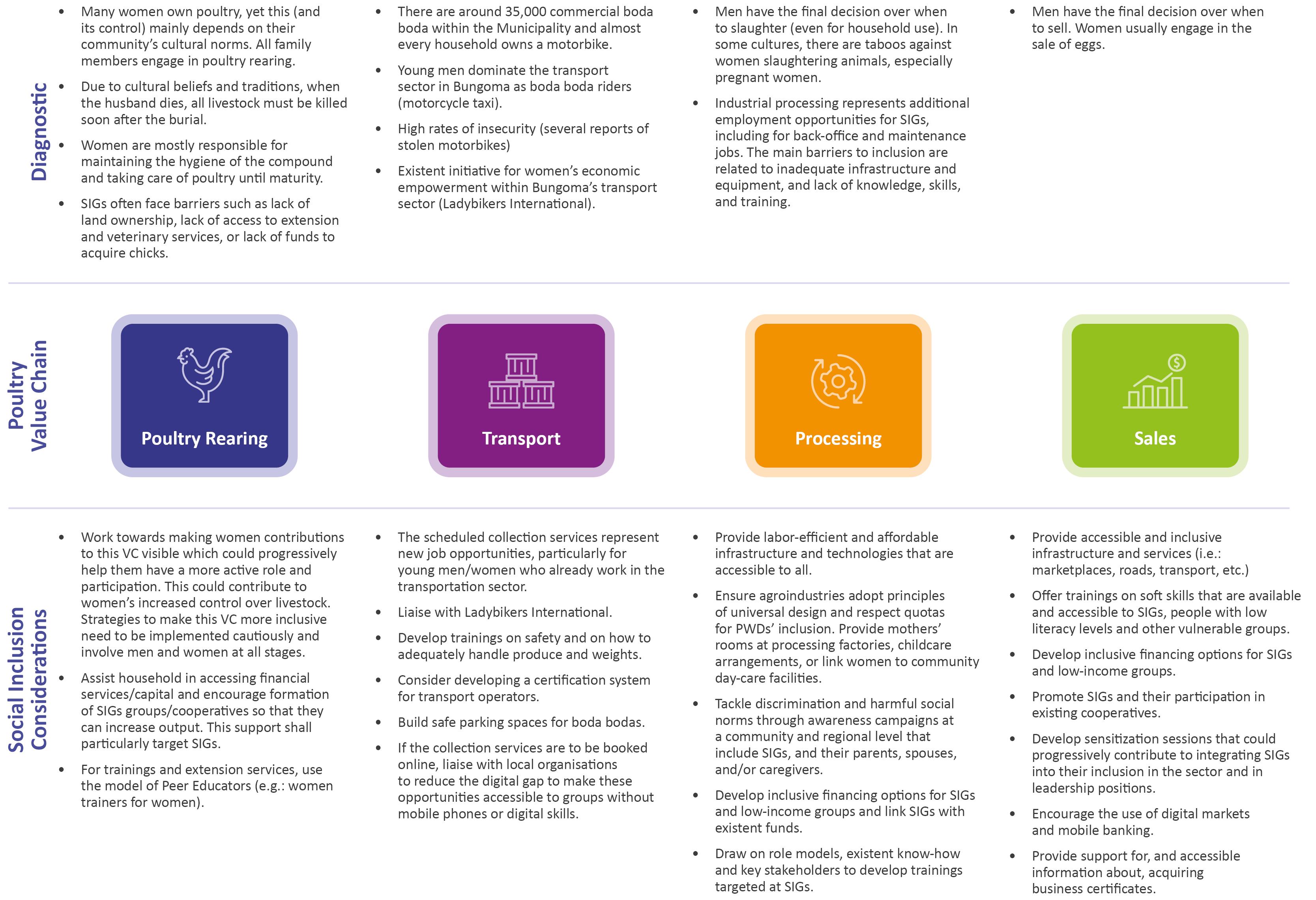
Case Study
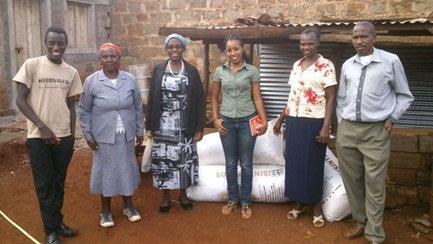
KEDOVO project: Kamamunda Poultry Farming
Kamamunda started as an informal self-help group in which women met every two weeks to contribute 500 KES in a money pool. These savings, however, only allowed them to cover household costs and needs, e.g. food, cooking utensils, school fees, etc., and were not enough to support any income-generating activity.
KEDOVO partnered with the group and facilitated their registration with the Kenyan Ministry of Gender and Social Development as a self-help group. Currently, the KEDOVO project works with 13 women and three young persons in poultry farming and egg production. The group receives training on poultry rearing and management as well as training on bookkeeping, marketing and entrepreneurship.
With this new knowledge and skills, the project not only created employment but also sustainable economic activity. KEDOVO does not depend on any donors, and operates with a revolving fund system where the group returns the initial capital over an agreed period of time. These funds can be used again to expand the project.
Source: KEDOVO for Sustainable Livelihoods45
45 Knedovo e.V., Kamamunda poultry farming project (2016). Available at: https://www. kedovo.org/english/our-projects/kamamunda-poultry-farming/, (Accessed: 18/02/2022).
4.2.3 Priority VC 2 – Dairy Processing
This VC covers the development of a milk processing plant and wide-ranging integration and improvements in the operations of the dairy sector in Bungoma, under the umbrella of the Bungoma Dairy Development Company (BDDC).
The key outcomes of this VC include:
> Providing a secure offtake and secure prices for milk; > Reducing losses and raising quality of milk for consumers; > Reducing production costs through improvements in logistics; > Providing an outlet for surplus product, helping to reduce wastage; > Supporting investment in improved dairy breeds, and fodder crops/irrigation; > Supporting improvements in the skills sets of farmers focusing on livestock management techniques and business skills, through technical support services; and > Creating direct employment for around 76 full-time employees, with high potential for employing special interest groups (SIGs) and people with disabilities (PWDs).
The dairy sector is a key activity across Bungoma, with most of the County’s 172,000 smallholders having at least one dairy cow.
There has been significant investment in the sector in recent years, focusing on supplying some improved stock, developing cooling centres and supporting the establishment of cooperative societies, and as a result overall production has been increasing, and now averages 265,000 litres per day. However, the sector is beset by a number of interrelated problems, in particular:
> Low productivity: traditional zebu cows dominate the County herd resulting in an average yield of less than 2,000 litres per cow per year, compared with a potential of over 10,0000 litres; > Skills shortfall: gaps in animal husbandry techniques and business skills prohibits investment in improved stock and feed; > No local processing: apart from some small-scale production of mala and yoghurt, all milk produced in the County is either consumed fresh or trucked outside of the region for processing. With no flexible local offtake for shelf-stable products (UHT), market surpluses result in wastage and price volatility; > High logistics costs: no overall coordination of collection services results in missed pick-ups and high delivery costs; and > High input cost: resulting from no substantial local production of feed or supplements, and high transport costs.
The result is that dairy farmers can face low margins and difficulties in securing investment to improve productivity.
To address these issues, the Ministry of Agriculture, Livestock, Fisheries and Irrigation commissioned the Bungoma County Dairy Development Feasibility Study (2018) and supporting investment proposal. The study identified a range of initiatives, with the first step being the formation of the Bungoma Dairy Development Company (BDDC). The BDDC has been established and this VC supports the development of the dairy sector across the County, under the umbrella of the BDDC.
Central to the development of the dairy sector is the establishment of a milk processing facility to provide an outlet for surplus production, and to support the stabilisation of milk prices paid to farmers. The facility would focus on producing long-life, UHT milk products which require good quality fresh milk, and therefore benefit from local in-County processing.