
6 minute read
Fuelled by data
Construction Worx correspondent Peter Haddock talks to Flannery Plant Hire’s Strategic Manager, Chris Matthew about positive training and carbon reduction impacts – all fuelled by data.
For some time, I have been following the journey of Flannery Plant Hire as it embraces technologies like 3D machine control, from the likes of Leica Geosystems and Trimble, and invests in advanced laser safety solutions from Xwatch Safety Solutions.
Advertisement
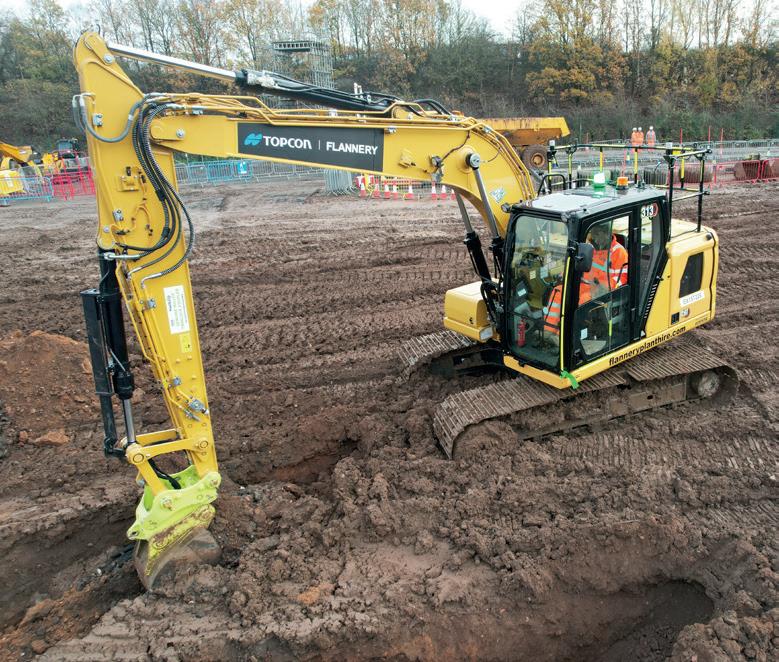
More recently on a visit to its Operator Skills Hub, near Birmingham, I discovered just how much the business has been able to integrate everything it does, thanks to another long-term industry partnership with global telemetry specialist MachineMax launched in June 2020.
The partnership has seen Flannery connecting all of its mobile plant equipment to the MachineMax integrated dashboard. And nearly three years later, the business has transformed its approach to plant hire, thanks to all the data it can now draw upon, as Chris Matthew explained to me:
Chris: "Since the business was formed in 1972, we have always looked forward. And having celebrated our 50th year last year, we haven't changed the fundamental five pillars the business has operated on, namely, People, Safety, Innovation, Sustainability and Value.
"Having one of the UK's largest mixed fleets, we have always recognised the importance of understanding how each machine operates and, ultimately, how to get the best productivity out of each asset in the safest and most efficient way possible.
"There are numerous challenges to tackle to achieve this, but as we recognised in 2020, we needed first to know what each machine was doing, where it was and how much fuel it was burning. MachineMax gave us a simple way of doing this with its easy to install hardware and intuitive dashboards. The impact has been significant, and impact has become an important word in our business ever since as we have recognised its every small impact that ultimately makes a big difference to our overall performance.
“The first major impact however on the back of our partnership with MachineMax, was the ability to also launch our Eco Operator Training Course in 2020, supported by the new dashboard. This in-turn saw us sign up for the Sustainability Supply Chain School Plant Charter in the same year.
“The Eco Operator Training Course has now been delivered numerous times to operators across the country, with every person taking the course making a positive impact on reducing our idle time and carbon missions.
“We have also added to our overall training programme with the opening of our first Operator Skills Hub in a joint venture with Balfour Beatty in February 2021. Through the combination of Tenstar Simulators linked to machine control, we are able to train teams of operators on the latest technologies like 3D machine control. And the individuals can literally walk into the dig area next to the classroom to try the latest machine using the relevant technology, in a safe job site scenario.
“This is particularly impactful when it comes to delivering our Trailblazer Apprenticeship Programme, which has been a big success and allowed us to more recently work with Government to offer boot camp training to potential new recruits. In 2022 we even started taking training 'On the Road' with our specially designed mobile HGV classrooms with simulators and, more recently, our investment in single simulator vans.
“This is all about making an impact on site by training staff where they work and reducing the need for them to travel, as it's not just the fuel savings related to the usage of a machine that we are trying to reduce."
Over the last three years, Flannery has also worked with the wider industry and key organisations like the Connected and Autonomous Plant (CAP) Group and National Highways Plant & Earthworks Community (PEC) to support better industry collaboration.
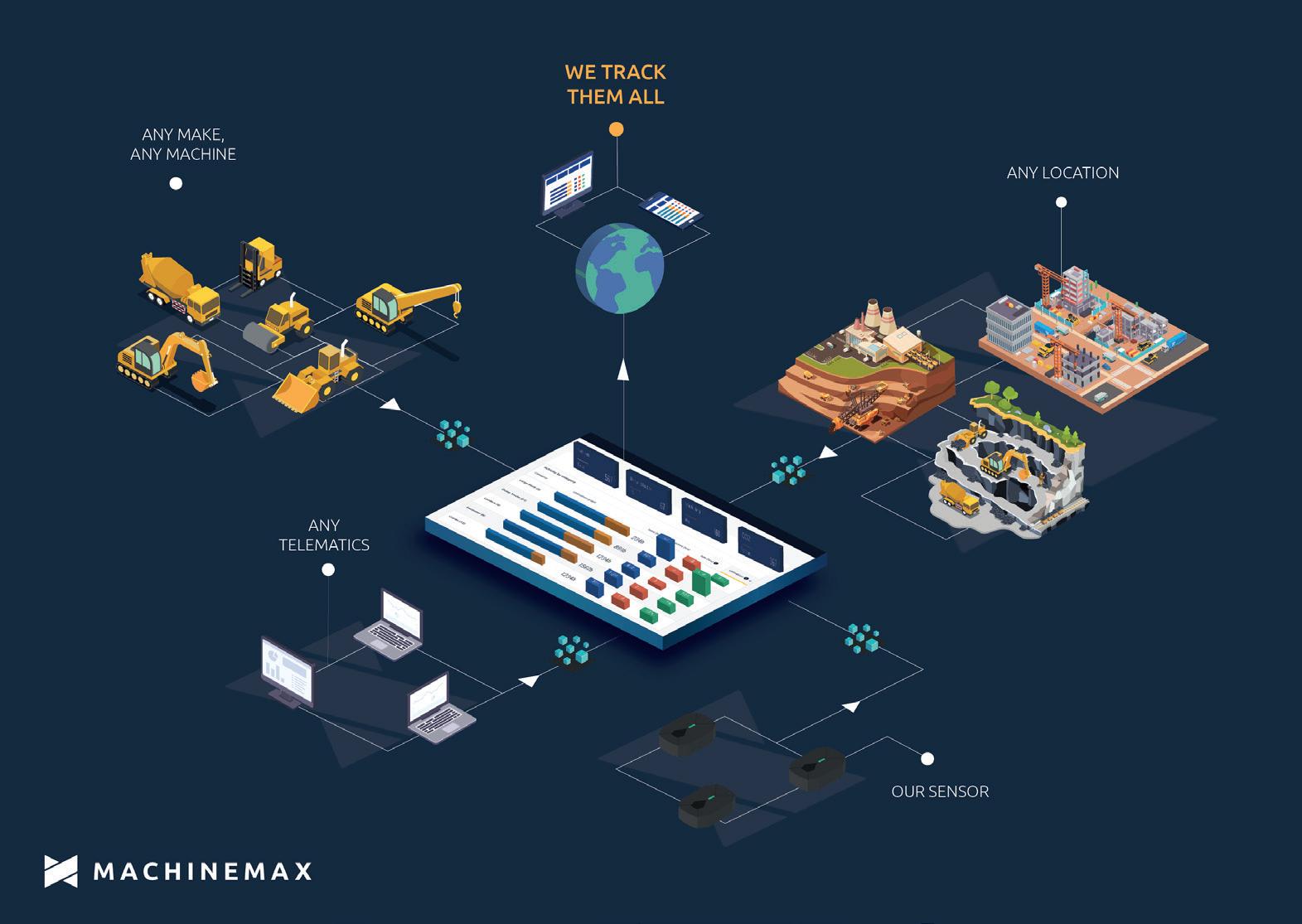
Chris continues: "CAP and PEC represent really important opportunities where we can share our experience with key clients, Tier 1 contractors and fellow hirers to support wider industry strategies and goals.
“Two of those key areas are safety and the use of new innovations, including advances in machine control. By working together, we can develop standardised approaches that positively impact the safe operation of equipment, productivity and efficiency. We can also raise important issues like designing earthworks models for the equipment we use to deliver them.
“Equally, with our MachineMax historical data sets collected over the last three years and our general documenting of projects we have delivered, we can now provide important benchmark data for future projects. This is already helping to set up and manage sites more effectively, removing bottlenecks whilst realising incremental improvements from day one.
Culturally we haven't changed as a business, but I think we are now much more aware of everyone's individual impact on the overall success of a project. And this is all about making small improvements, recognising trends and supporting each other as roles transition and new roles are required. For example, in the future, we will have more digital plant managers, data analysts and digitally enabled site managers, all with expertise that can support each other.
“So, when we think about how we cost a job, we will take information on potential fuel burn, payloads to be carried, haul routes and material movements before a machine lands on the site or the job is even at design, let alone tendered stage.
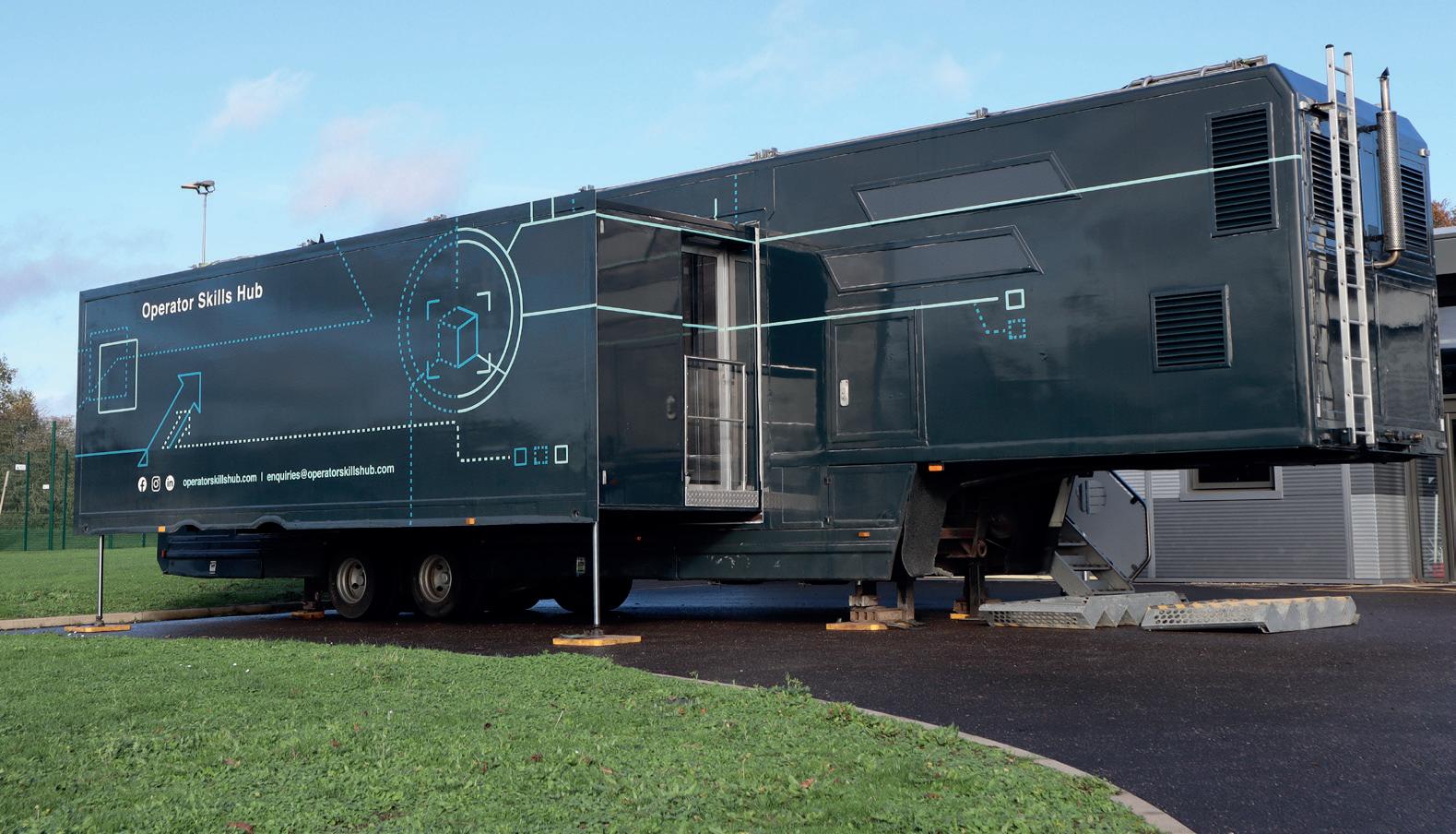
And in the future, this will also be about using real-time information that supports and informs actions onsite from black hats to operators and clients. Ultimately, we need to move material as short a distance as possible, handle it preferably once or twice but certainly not three times, whilst maximising payload and minimising carry-back.
And if we can show client procurement teams how this works and can deliver safer, more effective sites with minimal people plant interface and logistics, then we can add more value to each project.
This, in turn, will make the biggest impact by reducing the associated carbon emissions of operating and maintaining plant and equipment. And with Net Zero targets already published by clients like National Highways, every positive impact we can make adds up to a more sustainable future.
Since working with MachineMax Flannery has:
● Collected over 8 million hours of machine data to date.
● Connected and supported over 1,000 sites.
● Reduced idle time by 20% per month over a three month project with Amery Construction in 2022.
● Delivered 700+ training courses.
● Carried out 131 bootcamp completions with 59% successful bootcamp outcomes (Attendees securing employment).
● Delivered 20+ Eco-Operator training sessions.
● Trained 40+ apprentices to date.