
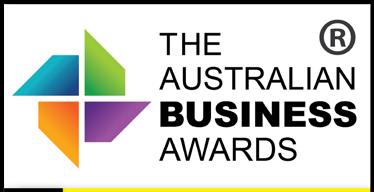
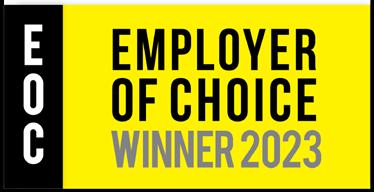
After an eight-year hiatus, the print industry’s largest trade exhibition was held in May, featuring 1643 exhibitors from 52 countries and drawing 170,000 visitors over 11 days.
The international share of the visitors was 80 per cent, with attendees coming from 174 countries – a record figure, according to the event’s organiser, Messe Düsseldorf.
Around 96 per cent of all visitors confirmed they had fully achieved the objectives associated with their visit. At over 50 per cent, most of them came from the printing industry, followed by the packaging industry, whose share has increased significantly, and which was the focus of many exhibitors as a growth driver.
Automation took centre stage from both exhibitors and attendees this year, with a strong focus on AI and smart workflows. In this special edition of Australian Printer, we wrap up the biggest news stories of the event as well as examine the key trends and learnings set to shape the industry’s future. Read our comprehensive drupa 2024 coverage from page 28.
Durst Oceania has confirmed Cactus Imaging will rollout the largest implementation of Durst Lift ERP software and Durst Workflow Plus software outside of North America.
Durst Lift ERP is a cloud-based ERP/MIS software which provides a single integrated platform to run every aspect of a print business. Durst Workflow Plus is a fully featured RIP and pre-press software production suite.
“Cactus is one of our most esteemed customers in the world and we’re very happy that they have chosen to work with Lift ERP,” Durst Group CEO and co-owner Christoph Gamper told Australian Printer
Nigel Spicer, general manager of Cactus Imaging, said he was looking forward to showcasing the technology to Cactus’ customers as well as the wider industry.
“This means the world to us. To be able to bring the technology to Australia and show our clients and the industry exactly what it can do, we’re really looking forward to it.
“We’ve looked at a number of different software solutions and there are some great ones out there, but nothing ticks the box like Lift for what we want to achieve for the future of our business” Spicer said.
“We don’t just have Durst machines. We have other machines on our floor, and this will integrate entirely with all the machines from workflow right through to finishing and dispatch. It’s across all different machines and across all different platforms. That’s the beauty of Lift
ERP – while it may be branded by Durst it runs independently and is going to be very successful for our business,” Spicer said.
“We’re thrilled to have Cactus on board with Lift ERP,” said Matt Ashman, managing director of Durst Oceania.
“This will be the largest installation in terms of the production volume and the number of supported printers and finishing devices.
“Lift is the leading ERP solution across North America and is now rolling out across Oceania. We already have an established customer base in Oceania and to now be able to add Cactus to that is a testament to the power of Lift and Workflow Plus to integrate a full production suite within Catus’ Durst printers and also their third-party printers,” Ashman said.
“Lift ERP and Workflow Plus is a completely agnostic software. It works with all the manufacturers‘ machines and all manufacturers‘ finishing devices, and all of the available business invoicing software that customers may have. Lift ERP brings all of these facets together in one solution.
“Both Lift ERP and Workflow Plus integrate seamlessly to facilitate the most efficient workflow for any print business, regardless of whether they are a Durst customer or not.”
Managing Director
James Wells / 02 8586 6101 james@intermedia.com.au
Subscriptions / (02) 9660 2113 subscriptions@intermedia.com.au
Subscription rate (5 issues) Australia $79
Managing Editor Claire Hibbit / 0432 796 384 chibbit@intermedia.com.au
Printed by Hero Print Alexandria, NSW, 2015
National Sales Manager
Carmen Ciappara / 0410 582 450 carmen@proprint.com.au
Mailed by D&D Mailing Services Wetherill Park, NSW, 2164
Design and Production Manager
Sarah Vella / 0406 967 559 svella@intermedia.com.au
Following the recent passing of IVE Group Limited’s executive chairman, Geoff Selig, IVE has advised that the group‘s non-executive director, James Todd, has been appointed chair of the IVE board.
According to IVE Group, Todd is an experienced company director, corporate adviser, and investor and has worked with IVE Group since prior to the company‘s initial public offering in December 2015. He brings extensive knowledge of the group to the role.
At the same time, the group’s chief executive officer Matt Aitken, will join the board as managing director.
Ricoh has unveiled its inaugural Reconciliation Action Plan (RAP), reinforcing the company’s ongoing commitment to sustainably and strategically taking meaningful action to advance reconciliation.
Over the next 12 months, Ricoh Australia will implement several milestone actions outlined in its RAP, contributing to a more equitable and inclusive society.
These include actions to help increase awareness of Aboriginal and Torres Strait Islander cultures, create direct employment opportunities for First Nations peoples, and support First Nations suppliers and companies to improve economic and social outcomes.
Yasu Takahashi, managing director of Ricoh Australia, said the company‘s inaugural RAP signifies its commitment to developing meaningful and respectful partnerships with the Aboriginal and Torres Strait Islander peoples.
Todd commenced his career in investment banking and has taken active roles in a range of private and public companies. He was until recently managing director of Wolseley Private Equity, an independent private equity firm he co-founded in 1999.
Todd is also a non-executive director of two other ASX listed companies, Coventry Group Limited and Bapcor Limited.
IVE Group’s new chair, James Todd said, “After a long career with IVE, the last five
“Implementing our Reconciliation Action Plan will create new learnings for many of our team members to better understand the importance of First Nations cultures and being on Country,“ said Takahashi.
“We also aim to create a proud culture for our organisation’s people and recognise the importance of the First
years as the group’s chief executive officer, we welcome Matt onto the board, and I’m very much looking forward to working closely with Matt and the rest of the Board to help the Group execute against its strategic priorities”.
Founding family member Paul Selig has reaffirmed his ongoing commitment to the group and will remain an executive director for the foreseeable future. Selig passed away suddenly in May while on holiday in Europe.
Nations history of Australia. We look forward to meaningfully impacting reconciliation in Australia and contributing to a more inclusive and equitable society.”
The creation of a sustainable RAP is also a key component of Ricoh’s Diversity Policy and supports its commitment to the employment of Aboriginal and Torres Strait Islander peoples through the provision of pathways to employment, professional development, and retention strategies.
At the same time, Ricoh is also committed to ensuring that the individual career goals and personal aims of Aboriginal and Torres Strait Islander staff are identified, promoted, and achieved.
As a result, the RAP has a strong focus on governance with built-in accountability and transparency, reporting on achievements, challenges and learnings both internally and externally, as well as providing appropriate support for the effective implementation of RAP commitments.
Karen Mundine, CEO of Reconciliation Australia, said, “Ricoh Australia joins a network of more than 2200 corporate, government, and not-for-profit organisations that have made a formal commitment to reconciliation through the RAP program. I look forward to following their reconciliation journey.”
Graphic Art Mart has consolidated Amari Visual Solutions into the Graphic Art Mart brand, creating a company with more than 120 staff members and 13 locations nationally.
Under this new structure, Graphic Art Mart will now stock what the company describes as an “unmatched portfolio of signage products,” including a wide range of rigid substrates, including acrylic, aluminium composite panel, flute, foam board, and polycarbonate.
Graphic Art Mart will also expand its hardware offering with the addition of HP alongside its existing brands – Roland DG, Mimaki, CWT Worktools, Keencut and Forte.
The company says its range of pressuresensitive materials will be enriched with many of Amari’s existing products that will complement several of the industry’s favourite brands: Avery Dennison, Arlon, Aslan, Siser, Chemica,
Insane Signs & Print has confirmed it has purchased the Mesh Direct business from the company’s administrators.
Mesh Direct went into voluntary administration in April with a total debt of $1.92 million, including over $875,000 to the Australian Tax Office.
Rodney James from Insane Signs & Print, based in Cardiff near Newcastle on the New South Wales Central Coast, has confirmed the purchase of the company’s intellectual property, staff, and property lease but has not disclosed any further details about the deal, including the amount paid for the business.
James said that as a creditor to Mesh Direct, he and his wife Sharon made a decision
R-Tape, TransferRite, 3M Reflective and many more.
The Siser heat transfer brand was the most recent Graphic Art Mart business acquisition in 2023.
Graphic Art Mart marketing and vendor relations manager Mark Canavan told Australian Printer this is an exciting evolution for the business.
“We can now offer a variety of consumable products as well as a comprehensive equipment portfolio through our alignment with a number of major global brands.
“We are excited to extend our reach and expand the business to provide better servicing solutions for our customers.
to recoup some of the losses incurred following the business going into administration.
“It is our intention for the business to run as normal as much as possible. We have a number of staff who have not been working for a month –but I am pleased to say they are able to start work again,” James said.
The business has grown from three to 13 locations over the last decade, and this has been an exciting evolution.
“From a customer perspective, we are a service-based organisation now offering a comprehensive range of consumable, rigid and hardware solutions. The feedback we have received so far has demonstrated that this is the right move, as our customers can clearly see the benefits of bringing these businesses together,” he said.
“We continue to assess the market for product and service solutions that are the right fit for our customers and business” Canavan said.
Graphic Art Mart is a subsidiary of MM
Epson has ranked fifth in Clarivate’s Top 100 Global Innovators 2024 list, announced by the global information services firm Clarivate Plc. This is the 11th time Epson has been named on the list since its inception in 2012.
Toshihiko Kobayashi, general administrative manager of the Intellectual Property Division at Epson, said, “It’s an honour to be selected as one of the Top 100 Global Innovators. In 2022, on Epson’s 80th anniversary, we established our corporate purpose statement, which reads, “Our philosophy of efficient, compact and precise innovation enriches lives and helps create a better world,” and have demonstrated this aspiration both inside and outside Epson.
“Based on our corporate purpose, we are evolving our approach to sustainability management and aim to solve societal issues while achieving corporate growth. Intellectual property is one of the pillars
Durst Group has announced the 1000th customer installation of Durst Workflow software. This achievement marks a doubling of the customer base since 2022.
Durst Workflow is a high-end solution for fully automated management of prepress and production tasks. The software is compatible with a wide range of printing machinery within diverse segments.
Michael Deflorian, business unit manager of Durst Software Solutions, said: “We are proud that more than 1,000 customers are relying on our solution and are increasing their efficiency by automating their prepress and production operation across different sectors. This underlines the quality of our products and the commitment of our experts, who offer global support to assist our customers in achieving exceptional results.”
of this sustainable management. Our proprietary technologies are protected by our intellectual property rights and support the foundation for our sustained efforts to address societal issues. The top priority of our IP activities is, and will continue to be, finding ways to use Epson’s strengths to help solve issues,” Toshihiko Kobayashi continued.
Clarivate compares and analyses invention data from around the world, assesses the quality of patent ideas using indicators directly linked to innovativeness, annually selects companies and organisations at the
top of the global innovation ecosystem and continuously demonstrates outstanding innovation performance.
A twin-track approach is used in evaluations. The first track focuses on identifying innovating companies and organisations based on the number of patent applications filed and patents held. An “international factor” is then calculated based on the rate and scale of international inventions. The second track scores them on four factors: influence, success, geographic investment, and rarity. Then a comparison against all other patent ideas is made.
Johanna Weber, product manager at Durst Workflow, said, “Durst Workflow is a complete browser-based solution that allows the entire PDF workflow to be easily managed, enabling a higher level of efficiency and automation than comparable stand-alone products. This is what makes it unique.”
Serge Clauss, the product manager of Durst Software Solutions, said Durst is continuously working to make Durst Workflow software the best for customers.
”Our software is engineered to drive
process optimisation and automation, aligning seamlessly with our customers’ objectives,” said Clauss.
Matt Ashman, managing director of Durst Oceania, described the achievement as “an amazing milestone in the evolution of the Durst software ecosystem”.
“Business need robust equipment but also needs equally robust and integrated solutions; this was the aim when Durst Software Solutions was established, and today, the portfolio is at the cutting edge of software development and design.”
The Australian Financial Review (AFR) has become a digital-only news title in Western Australia, with the Nine-owned masthead claiming the Seven-owned printer “demanded a new contract that doubled the cost of printing.”
The AFR reported that “the Seven-owned Colourpress, the only printer of major newspapers in Western Australia, delivered the ultimatum to Nine Publishing MD Tory Maguire”, with the proposed 100 per cent increase in the printing price set to end seven decades of the AFR distributing a printed newspaper in that state.
“Ms Maguire received an email from Shane O’Connor, Seven’s chief financial officer in WA, on April 23. It was the day Nine’s free news site in the state, WA Today, held a launch event. The short email notified Ms Maguire that Colourpress was terminating the contract early in 28 days,” reported the AFR.
“The company had previously agreed that the contract would run until late July. The email attached a new quote for services from the 29th day that would double the fee, sending the operation into loss. There was no other explanation, and none was forthcoming despite repeated requests for information.”
Nine Publishing said it will upgrade the Today’s Newspaper section, a digital version of the physical paper, on the AFR website. Distribution of the Financial Review Magazine and quarterly Fin! The magazine will continue to be sold separately by news agencies.
“This decision is specific to Western Australia and has no impact on our papers and magazines in the rest of the country,” Nine Publishing MD Tory Maguire said in a statement.
“We work very constructively with the printers of our newspapers and magazines to ensure the long-term sustainability of our print products, which continue to be profitable.
“Fortunately, the Financial Review is an incredibly successful digital publication, which has allowed us to make this decision in the best interests of our business,” said Maguire.
A Seven spokesman told the AFR: “It is a commercial decision. To suggest anything else would be inaccurate and disingenuous.”
The widely acclaimed ROLAND 700 EVOLUTION litho press deploys an array of innovative technologies to give unprecedented levels of efficiency, productivity and print quality.
manrolandsheetfed.com
manrolandGoss - Australasia
Tel: +61-2-9645-7900
Students, parents, teachers and careers counsellors embraced the Sign & Print Career Connections initiative at the Brisbane Careers & Employment Expo.
With its colourful design, interactive activities, and real-world advisors, the stand was the centrepiece of an industrywide initiative to attract new talent to the print, sign and graphics sector.
Sarah Moore, general manager of Visual Connections, said the number of serious enquiries received was enormously pleasing. It generated hundreds of enquiries, proving one of the most popular attractions at the Expo.
“Since launching the newly expanded program in Melbourne earlier this year, our team has fielded many hundreds of enquiries, and we have seen thousands of hits to the online resource, providing that there is plenty of interest in careers in the visual communications sector,” she said.
Moore said the ‘Try-A-Trade’ activities were central to engagement, with students getting hands-on with vinyl applications and heat press.
Staff from the local TAFE and several industry volunteers were on hand to assist, providing students with a ‘real-world’ perspective on the industry.
“With the number of enquiries growing at every outing and thousands of hits to our online resource, it’s more important than ever for industry businesses to consider giving a young person the opportunity to start their career,” Moore said.
“If you are looking to expand your team, we encourage you to take advantage of the interest of these bright, motivated young people by considering offering an apprenticeship.
“Positions can be listed on the searchable Sign & Print Career Connections online resource, so students can locate employment opportunities, as well as training options, in their local area,” Moore said.
Interested businesses can find out more about the Sign & Print Career Connections program and list apprenticeship opportunities at https://visualconnections. org.au/careerconnections.
The Sign & Print Career Connections program is led by Visual Connections in partnership with all major industry associations, including ASGA, FESPA Australia, the FPLMA, LIA and VMA.
Major sponsors include Amari Visual Solutions, Ball & Doggett, Cactus Imaging, Fujifilm Graphic Systems, Graphic Art Mart, Mulford Australia, Sign-a-Rama, Pozitive Sign & Graphics Supplies, and ORAFOL,
with partnering sponsors including Böttcher, FPLMA, Hero Print, MacDermid Graphic Solutions and Spicers.
The next Sign & Print Career Connections initiative is in Perth in July and Sydney in August.
E-Bisglobal, a leading Indigenous print management and marketing service provider on the NSW Central Coast, has achieved Supply Nation Certification.
E-Bisglobal is an Indigenous-owned and operated company specialising in print management and marketing services. The company focuses on providing innovative
solutions with a social procurement focus, including other Indigenous-owned businesses and Disability Enterprises throughout its supply chain. E-Bisglobal is dedicated to creating positive social impact while delivering high-quality services to its clients.
Supply Nation is Australia’s leading directory of verified Indigenous businesses, connecting them with government and corporate Australia procurement opportunities. By becoming a certified supplier, E-Bisglobal joins a network of businesses dedicated to driving economic prosperity for Indigenous Australians.
“We are proud to be part of the Supply Nation community and to contribute to the
advancement of Indigenous businesses,” said Paul Freeman, executive chairman of E-Bisglobal.
”This certification aligns with our values of promoting social procurement and creating meaningful partnerships with diverse suppliers, he added.
E-Bisglobal is committed to leveraging its Supply Nation Certification to expand its supply partnerships and create more opportunities for other Indigenous and Disability Enterprises throughout its supply chain. The company aims to continue providing innovative, cost-effective, and sustainable solutions across Australia while fostering social impact.
New ton’s Cradle demonstrated the conser vation of Energy and Motion, We also owe it to Sir Isaac New ton for the discover y of colours in white light – the beginnings of Colour Management 320 years later, SCREEN is honouring that same spirit of innovation, developing the world’s finest inkjet printing machines for commercial, label, packaging and industrial applications. Spot and Pantone ® colours are faithfully reproduced with Screen’s high - definition Tr uepress ink s. Deep blues and oranges make labels come alive with extra colours, plus white on our Tr uepress L abel series. There is more, much more to tell in our stor y of endless innovation. Contac t us today
SCREEN Tr uepre ss Jet 520 ser ie s r ange of book and commercial colour digit al pre sse s with o set qualit y on o set paper s .
SCREEN Tr uepre ss L350 U V SA I digit al label pre ss. Up to 7 colour s inc. High Opacit y W hite 60 m /min across 350 mm web *
SCREEN Tr uepre ss PAC 52 0 P sus t ainable paper- based fle xible pack aging pre ss with water- based ink s .*
SMARTECH’s executive chairman, Vincent Nair, and head of marketing and communications, Ximena Guzman, reflect on the company’s history and discuss what’s next for the print solutions, mailing communications, and eCommerce global provider.
SMARTECH has a rich Australian history and is a regional powerhouse in eCommerce, digital print solutions, mailing technology, and communications solutions. The company has offices and customers across the globe, with particular emphasis on Asia Pacific due to the region’s growing population.
The origins of the Australian business go back to 1927 when the first Neopost mailing technology was introduced in Australia by The Postal Stamping Machine Company Pty Ltd. Through subsequent years, ACCO Brands and GBC acquired Fordigraph, and many years later, in 2011, Euronext listed Neopost, (later rebranded Quadient), procured GBC-Fordigraph and established a direct presence in the Oceania region. In 2021, SMARTECH consequently acquired the Quadient Oceania businesses, re-establishing a renewed focus on digital printing and eCommerce services and maintaining the
growth of the Quadient mailing and parcel locker solutions.
An amazing, rare feat will be achieved in 2027, when the company will celebrate 100 years of Australian presence servicing Australian customers, and its strategic long-term century-old partnership with Australia Post.
“We are very proud of our Australian heritage,” said Nair. ”And we have established a very clear vision to grow our customer base in Australia”.
As the largest mid-volume sign and display solutions supplier in Australia to manufacturers such as HP, Canon and Agfa, SMARTECH continues to invest in its services capability. The company is proud of its customer satisfaction surveys, which show 96 per cent quality of service,
response rates, delivery and service capability. The field service delivery and customer experience teams of over 55 dedicated Australian-based national personnel could not be more flattered by its prominent achievements.
“It‘s not the equipment which the customer is investing in, it‘s actually the quality of service over the life cycle of the asset,” says Nair.
“You cannot have machines in the field breaking down for more time than necessary; customers expect a qualified service technician to be on the case as soon as possible and that is what we get out of bed each morning to do.”
In 2024, SMARTECH became the exclusive channel partner in the Oceania region to Agfa in the industrial print sectors. From
die making in 1867 and then transitioning to chemicals, Agfa colour, photos and film producing, Agfa undoubtedly became a global leader in industrial print solutions due to its immense R&D investments to roll out cutting edge and reliable machines with the ink to support.
“How do you compete with Agfa in the industrial print segment?” asks Nair. “Customers must consider the total cost of ownership, machine efficiency (ink reliability and consumption), field service capability and most importantly, the warranty which upholds the return on customer investment.”
As HP’s largest mid-volume channel partner, SMARTECH continues to actively compete nationally to uphold its leadership position. SMARTECH boasts a field sales force of more than 38 experienced dedicated sales reps across Australia and over 8,000 B2B customers.
“We will continue to invest with HP in training and knowledge management and leverage HP’s leading global expertise in Latex Print solutions.
“Latex is very popular, and customers continue to seek low-cost, end-to-end Latex print-cut, rigid, production and industrial printing solutions,” continues Nair.
Earlier this year, SMARTECH partnered with Canon to launch the Colorado series in Australia.
“We will continue to be selective with quality manufacturers to ensure that we have the best-of-breed solutions for our customers and prospects, and Canon fits the bill with us,” says Nair.
SMARTECH’s focus on employee development and growth has been the best in class. Over the last three years, the company has promoted over 32 per cent of its employees into new roles and over the last 15 months, 50 per cent of its Oceania executive leadership team has come through the ranks, clearing the way for other senior-level promotions. In this age of work-life balancing and mental care awareness, SMARTECH‘s human resources department rolled out an employee satisfaction survey in February 2023. 82 per cent of employees either agreed or strongly agreed that SMARTECH was ticking off the right boxes for them.
In 2024, the second Employee Satisfaction Survey resulted in a 96 per
cent compliance rate, and 95 per cent of employees agreed or strongly agreed that the company satisfied what they were looking for in a company.
“Customers will not love your company unless your employees will love the company first,” says Nair.
In late 2023, the Australian Business Council awarded SMARTECH the prestigious Employer of Choice award.
“We are very proud of the work that has gone into making SMARTECH one of the best employers in Australia and the best in the industry also,” says Nair.
“We are also proud of the fact that we have a 99 per cent employee retention rate. Each day is about employees and customers.”
In an exclusive interview with Channel 9‘s Sophie Walsh during a customer appreciation event in December last year, Nair highlighted SMARTECH’s unwavering commitment to its customers. Amid a challenging year for many businesses, Nair emphasised that SMARTECH’s success is deeply rooted in trust.
”Trust is more than just a buzzword at SMARTECH; it is the foundation of
our business model,” Nair explains. ”Every year, because we have a trusting relationship with our customers, more customers choose to work with us through recommendations.” This trust has fuelled SMARTECH‘s impressive growth, with the company expanding globally at a rate of 15-20 per cent over the past three years.
”Customers are our lifeblood,” says Nair, reflecting a core principle that drives SMARTECH‘s operations.
”In addition to our commitment to trust, we have implemented strong ethical standards and transparent communication to our customers,” comments Ximena Guzman, Head of Marketing and Communications at SMARTECH. ”This approach has reinforced our client relationships and set us apart in the industry.”
SMARTECH is also highly committed to environmental sustainability. Two years ago, it launched its Australian Refurbishing and Remanufacturing Centre at Regents Park NSW.
“We have a zero-landfill mindset,” says Nair. “All equipment, machines, ink cartridges or parts, returning from trade customers are categorised into recycling segments to ensure we do our best to look after our planet.”
The company also loans or sells recycled and refurbished print or mail equipment to assist customers with affordable business continuity.
Nair recalls the time in 2015 when Austin, Texas-based David Moore, the co-owner of SMARTECH Business Systems, discussed launching the SMARTECH brand in Asia Pacific.
“We were both reluctant because David was based in Texas, and I was living in Sydney, and any means to invest in Asia required local presence; but with David’s insistence and guidance, I decided to take on the leadership role, and we have grown tenfold in that time,” says Nair.
“Building an international business requires a trusting relationship with your co-founder and a highly supportive board of directors.”
”As Co-owners of SMARTECH Business Systems, both David and I have made it our passion to ensure we grow and develop our employees and customers, have consequential relations with our suppliers and follow the rule of law when it comes to enterprise governance in each country we operate in,” concludes Nair.
As Visual Impact Brisbane approaches, anticipation is building among industry professionals eager to discover the latest innovations and opportunities in visual communications, and Spicers is set to impress.
Spicers will be demonstrating the Roland AP640 at Visual Impact Brisbane
Spicers, a leading name in the industry, is prepared to amaze with an extensive and diverse portfolio that underscores the value of partnering with a trusted supplier. This year’s event promises to be particularly exciting as Spicers unveils new brands and products that are set to redefine industry standards.
Spicers’ commitment to providing top-tier solutions is evident in their long-standing partnerships with renowned manufacturers like 3M, General Formulations, Mimaki, Roland, and RollsRoller. These collaborations have consistently delivered high-quality products that meet the evolving needs of customers. At Visual Impact Brisbane, Spicers will highlight several new and innovative products that are poised to enhance productivity and creativity in visual communications.
Among the highlights on the Spicers stand will be the Neschen Easy Dot range, known for its ease of installation thanks to its unique dot adhesive. This feature makes it an ideal choice for point-of-sale marketing pieces, offering a hassle-free application process that saves time and effort. Additionally, the General Formulations Wall Graphics GF885 will be showcased, demonstrating its versatility as a wall graphic vinyl suitable for both indoor and outdoor applications on various surfaces, including smooth and rough textures.
Spicers is also excited to feature the Neolt DTF XY Slitter, a cutting-edge solution designed to streamline production processes, and the RollsRoller, often referred to as the ”extra pair of hands” needed to boost efficiency in any production department. These tools exemplify Spicers’ dedication to enhancing operational efficiency for their customers.
Furthermore, Spicers will be demonstrating the Roland AP640 and the Mimaki UCJV300-160, providing attendees with firsthand experience of the advanced technology behind these printers. Understanding the technology that best suits specific applications is crucial for customers, and Spicers’ expert demonstrations will provide valuable insights into making informed decisions.
A significant highlight of Spicers’ participation at Visual Impact Brisbane is the introduction of new brands including Brett Martin and ContraVision. These additions reflect Spicers’ ongoing commitment to expanding their offerings and providing customers with access to the best products available in the market.
3M, a staple in Spicers’ portfolio, will have a strong presence on the stand, showcasing their diverse range of application opportunities. Products like Di-Noc and Fasara architectural
finishes, Paint Protection, Vehicle Wrap, and Reflective solutions will be featured, demonstrating the versatility and potential for growth that 3M products offer. Attendees will also have the opportunity to meet their local QLD 3M representative and gain insights into how these products can drive business growth.
Wayne Hood, Spicers Visual Communications Portfolio Manager, emphasises the importance of these partnerships: ”Our collaboration with suppliers and customers is the cornerstone of our success. It allows us to deliver innovative solutions and create more opportunities for our customers to grow their businesses. We’re excited to showcase this at Visual Impact and demonstrate the value of these partnerships.”
Visual Impact Brisbane is more than just an exhibition; it is an opportunity for industry professionals to connect, learn, and explore new possibilities. Spicers’ comprehensive showcase of innovative products and technologies underscores their position as a leader in the visual communications industry, committed to helping customers achieve their goals through quality, innovation, and partnership.
Come and see the Spicers team at Visual Impact Brisbane, Stand I06.
Australia’s leading supplier of quality materials, equipment and solutions to our customers in commercial print, labelling, packaging, signage, visual communications, dye sublimation and architectural industries.
TAKE ADVANTAGE OF OUR SHOW SPECIALS & OFFERS!
Friday 25 October 2024
Scan to purchase your ticket
Alex Laidler owns Upfront Signage Management. She represents a new generation of women taking on print to work it their way. She talks to Australian Printer about getting her first start, the moment she fell in love with the print industry, and why she believes gender is not important.
When did you first consider a career in the print industry?
I joined Xerox (Rank Xerox) in 1984. At the time, I had been working for many years as a secretary at a large computer company in North Sydney, where I worked for 15 salesmen, 15 IT support guys, and five sales managers. Then, I thought I should try my hand at sales, as I was also assisting in computer demonstrations for clients. Unfortunately, management did not allow it. When Xerox offered me a job in sales for their new Copy Centres, selling instant print, I accepted. The training in Xerox was excellent; we were trained in applying the Xerox Professional Sales Systems and working in production before we could go into the fi eld. It was then I realised I loved the industry. Many projects, opportunities, and challenges moved me along, from instant print, machine sales, offset, direct mailing, database marketing, outdoor advertising, large format print, events and displays to wall graphics and signage.
Alex Laidler
The many opportunities motivated me to take various courses/studies, including Marketing Diploma, Visual Merchandise, Records Management, Database Marketing, Interior Design, Adobe Programs, Project Management, and Way finding Signage.
What triggered you to start your own print business?
After a while and many projects later, I had to set up on my own to offer my clients the quality I wanted to provide. This allowed me to access all equipment and finishing and not be restricted to the type of equipment the company I represented had, especially at the start of the large format printing boom when colour matching and print quality were better in some machines than others. I set up my business, Upfront Directions, in 2003 to provide the best service I could, working with great suppliers, graphic designers and customers I really liked.
In 2021, I set up Upfront Signage Management as my work involved more signage works.
Who inspires you to keep going?
My inspirations come from many areas: life, nice and positive people, and nature. But for the type of work I do, it comes from positive, and creative people, exciting and challenging projects, and beautiful designs.
In your opinion, what is the future of women in print?
I don’t understand why gender differentiation is important, as I don’t focus on gender or age. There is a great future in print, and we have the digital technology to assist us all. Print is needed in every area of life, and we need to keep finding opportunities, uses, and exciting projects. Print and digital complement each other.
What are the challenges you face as a print business owner?
Running out of exciting projects.
Tell us about the project you are most proud of.
I am proud of all the projects I worked on, they were all successful.
One project that comes to mind was the branding rollout of 20 sites located in NSW and ACT for the exterior and interior branding works, including the cladding, painting, illuminated pylons, illuminated signage, way finding signage and interior signage and graphics. This project was very successful; everybody involved did a great job, and I am very grateful.
What machines are you loving working with right now and why?
I do not focus too much on the machines now but on the quality of the work.
I only deal with suppliers with the best and widest printers catering to most of my requirements.
Signarama Tuggerah recently hosted a Sustainable Print & Signage Showcase on the Central Coast in NSW, offering a unique platform to demonstrate its innovative and eco-friendly print solutions.
The event highlighted Signarama Tuggerah’s commitment to sustainable business practices and the strong partnership with HP, a leader in sustainable printing technology.
A gathering of industry leaders and innovators
The open house attracted long-term and new customers from Signarama Tuggerah, which spanned across the spectrum of industries from government, construction, retail, entertainment and local media, including the Central Coast Mariners Football Club from the Australian Football A-League.
Showcasing sustainable innovations
Attendees were treated to a comprehensive tour of Signarama Tuggerah’s production facility, showcasing the latest advancements in sustainable printing.
Melissa Marshall, director of Signarama Tuggerah, and the HP team guided
groups through the facility, highlighting the impressive range of eco-friendly applications made possible by HP’s environmentally certified Latex technology.
The production facility featured Signarama’s state-of-the-art Latex 800W printer, affectionately named ‘Whipper’, and the Latex R 1000 printer, dubbed ‘Whopper’. These printers were in full production throughout the event, allowing attendees to witness HP’s Gen 4 technology in action.
Event highlights
The showcase emphasised several key aspects of sustainable printing:
• Circular Economy Approach: The importance of incorporating the Circular Economy in print production to reduce carbon footprints.
• HP Gen 4 Latex Technology: Utilising water-based inks and recycled plastics, including ocean-bound plastics, in HP Latex printers.
• Versatility and White Ink Capabilities:
Demonstrating the application versatility and white ink capabilities of HP Latex technology.
• Value-Add of Eco-Friendly Print Media: Highlighting the benefits of using sustainable print media in production processes.
Gary Marshall, managing director of Signarama Tuggerah, said the event highlighted the evolving nature of the signage industry and the company’s commitment to sustainability.
“The signage industry is changing immensely. Traditionally, the signage industry has a lot of waste, and we are making a concerted effort to reduce waste. Through our business partners, we are moving in the right direction.“
Craig Hardman, country manager for large-format printing at HP Australia, commended Signarama Tuggerah’s investments and dedication to sustainability.
“Signarama Tuggerah has made huge investments on the Central Coast. Not only have they chosen to go with our brand at HP for their printing equipment, but they have also shown a strong commitment to sustainability,” commented Craig Hardman.
The Sustainable Print & Signage Showcase at Signarama Tuggerah demonstrated the significant strides made by the print industry towards eco-friendly practices. By adopting HP’s cutting-edge technology and embracing sustainable methods, Signarama Tuggerah is leading the way in reducing the environmental impact of print production. This event showcased technological advancements and reinforced the importance of sustainability in the modern signage industry.
Blueprint Digital has installed the first Durst eight-colour P5 TEX iSub printer in Australia, with the new machine set to deliver numerous advantages for the Sydney-based business.
Blueprint Digital has installed the first Durst eight-colour P5 TEX iSub printer in Australia to provide better quality and faster service for its dye sublimation printing business in Sydney.
Marty West from Blueprint Digital said the installation of the machine was a strategic step forward for the business that has been operating for more than 35 years.
“We were originally a screen-printing business called Mirage Graphics that started in 1989 with premises in Marrickville and then Camperdown. Over time this transitioned into large format dye sublimation printing for banners and flags, as well as bar mats for brewing companies which eventually led to us working in wider width printing formats,” West said.
“We moved into our current premises in Marrickville 22 years ago.
“The Durst is certainly an investment – but I am con fi dent it is the best. Considering we will run it over the next 10 years, and if it helps us grow with our customers, it’s well worth it.”
– Marty West, Blueprint Digital
“We have recently doubled our floor space by taking the premises next door. This has allowed us to invest in new machines and create a purpose-built, temperature-controlled environment. Dye sublimation and soft signage remains our
core focus and we now have a growing solid team working in the business.”
The decision to install the Durst P5 TEX iSub came after thorough extensive research and a desire to differentiate within a cluttered print market.
“We were looking at upgrading our 3.2-metre-wide printer about 12 months ago. It took me around four months to look at everything else that was out there at this width, and we decided to go with the Durst towards the end of last year. Our current 3.2 metre machine is coming to the end of its days, so we had to make a decision,” West said.
“The Durst is certainly an investment – but I am confident it is the best. Considering we will run it over the next 10 years, and if it helps us grow with our customers, it’s well worth it.
“Working with the team at Durst the installation was an effortless experience. The machine was unloaded, removed from the crate and positioned by 10.30am. I couldn’t wait to start experimenting with its capability.”
Durst Oceania managing director Matt Ashman said he is very excited to have installed another first in the Australian market.
“All P5 TEX iSUB installations thus far in Australia have been four-colour models. With the first eight-colour model in Australia, Blueprint Digital can bring the highest possible print quality to the Australian market with more pantones and
a wider colour gamut for customers. This machine is fully loaded and provides the ability for paper transfer as well as direct to fabric with dual roll functionality.
“It is great to have Marty and Blueprint Digital join the Durst family and we enjoyed welcoming him to our head office at Brixen prior to drupa.
“It is always good to work with like-minded family-owned businesses and Marty runs a business that is focused on quality and customer service as well as delivering precisely what his customer needs. These are the same values that Durst has built its reputation on and Marty and the Blueprint Digital business fi ts perfectly within that pro fi le.”
– Matt Ashman, Durst Oceania
“It is always good to work with like-minded family-owned businesses and Marty runs a business that is focused on quality and customer service as well as delivering precisely what his customer needs. These are the same values that Durst has built its reputation on and Marty and the Blueprint Digital business fits perfectly within that profile.” Ashman said.
West believes the installation of the new Durst TEX iSub will deliver numerous advantages to his business.
“Adding this machine to our production suite means we can offer a wider range of services, and as it is so efficient and fast – we can keep up with demand,” he said.
“With our previous equipment when we received orders for large campaigns there was a lot of after-hours printing and weekend work to keep the machines running around the clock.
“With this machine we can do it all on an eight-hour shift, rather than a 16-hour or 20-hour shift. This allows us to invest staff time in other areas of the business. The quality and efficiency of this machine will make Blueprint Digital an absolute go-to for soft signage trade printing across Australia.”
On day three of drupa, Ricoh hosted a live stream directly from their stand, offering a firsthand look at their latest and greatest production print technology. The star of the show was ‘The Dragon’ Pro Z75 B2 sheetfed inkjet press, a world first. The live stream was hosted by Henryk Kraszewski, Product Marketing Manager, along with Richard Granger, Michael Crawford, Dean Hennessey, and the Ricoh UK team.
Registrations for Ricoh’s post-drupa highlights event are now open. Visit https://www.ricoh.com.au/events for more information.
After an eight-year hiatus, the industry’s largest printing exhibition took place over 11 days in Düsseldorf, Germany, bringing together 170,000 visitors from 174 countries. Australian and New Zealand delegates networked with their global counterparts forging deals, exchanging ideas, and sharing insights on the progressive world of printing.
FUJIFILM Business Innovation Australia and FUJIFILM Australia hosted a joint drupa networking event in Düsseldorf.
FUJIFILM Business Innovation
Australia and FUJIFILM Australia hosted a joint drupa party for its Australian partners and customers at Vino’s Weinbar in Düsseldorf.
“We are very happy to welcome and host our distinguished customers and partners from both sides of the FUJIFILM business,” said Troy Neighbour, division manager for graphic systems at FUJIFILM Australia.
FUJIFILM Business Innovation
Australia’s general manager of graphic communications solutions, Chris Lynch, gave a short speech to guests at the event.
“The theme of our booth at drupa is
‘Discover The Difference’ and having 90 years of heritage in the print business –being involved in the analogue side plates, ink, film, CTP and from the very beginning of digital – we have something to bring to the business that we think is different. We have a rich heritage, and we have a legacy of fantastic customers who we have worked with for many years. Many of you are here with us tonight.
“We wanted to start this drupa, which in my opinion is the most important drupa there has been for quite some time, by enjoying an intimate time with those people who are invested in FUJIFILM. We cannot do anything alone – we are nothing without our customers, and
together, we achieve success with an ecosystem that includes partners, third parties and even competitors.
“Our mission at FUJIFILM is to make more smiles in the world – and there are many obstacles and challenges in the print business. Over the last eight years, there has been an absence of us coming together; there has been lots of change. Many businesses have gone through mergers and acquisitions, and some have disappeared. We need each other more than ever. By overcoming obstacles and challenges, finding value from innovation and new ways of doing things and opening up new markets for your customers, we bring smiles to people’s faces. Cheers to drupa 2024.”
Messe Düsseldorf in partnership with the Visual Media Association (VMA) and PrintNZ hosted a networking event for Australia and New Zealand delegates at drupa. The networking reception was followed by an ‘after-party’ event sponsored by Ricoh at the Holy Craft Beer Bar.
Eva
Earle
Heidelberger Druckmaschinen AG (Heidelberg) and Canon kicked off drupa, with the announcement of a global co-operation in sheetfed inkjet printing.
According to both companies, the collaboration aims to “support commercial print businesses striving to establish hybrid offset/digital production to meet changing print buyer needs and increase their capability to handle shorter runs of more diverse jobs”.
Heidelberg will expand its technology portfolio by introducing an inkjet product family based on the newly announced Canon B2 sheetfed inkjet press and the well-established B3 sheetfed inkjet press. Both presses will be integrated into the Heidelberg Prinect workflow,
and service and Saphira Ink will be delivered through Heidelberg.
Akira Yoshida, president and CEO and chairman of the board of executive directors of Canon Production Printing Holding B.V. said: “Canon has channelled significant energy and investment to develop its leading inkjet technology and give customers in the commercial printing industry a clear vision of their future. Heidelberg boasts a unique heritage, an extensive customer base and in-depth knowledge of the needs of commercial print businesses. We are confident
our collaboration with Heidelberg will accelerate the move to blended offset/digital production and enable transformative innovation for many more offset print businesses worldwide.”
Dr David Schmedding, head of sales of Heidelberger Druckmaschinen AG, said: “We are confident that Canon is the ideal partner for Heidelberg to support our customers with best-in-class inkjet press technology, backed by deep expertise in digital applications and business development. Our aim is to offer print shops that operate sheetfed offset and digital presses simultaneously an attractive and integrated service and product portfolio. That’s why we’re excited to be able to offer our customers innovative industrial inkjet presses integrated in our Prinect workflow to gain flexible and cost-effective autonomous production.”
More than 650 Canon B3 sheetfed inkjet presses have been successfully adopted by customers worldwide, giving them increased flexibility and agility to produce a broad spectrum of shorter-run work efficiently and profitably. Building on this track record, the new Canon B2 sheetfed press promises ideal levels of digital productivity, quality, and media versatility for industrial customers when it becomes available.
Reacon Group makes multimillion-dollar investment in FUJIFILM JetPress 1160CF
Marketing services specialist Reacon Group purchased the second FUJIFILM JetPress 1160CF in the world in a deal confirmed at drupa 2024.
Reacon Group managing director Jay Khan attended drupa to confirm the deal with FUJIFILM Business Innovation Australia general manager of graphic communication solutions Chris Lynch and managing director Yasuyuki Matsumoto.
“We bought the Jetpress 1160CF because we have previously dealt with FUJIFILM across the SRA3 format. All respective businesses within our group have been working with FUJIFILM for over 20 years, and my personal relationship has been since day one in 2018,” Khan said.
“This is a brand-new machine that will improve both our volume and production capabilities as it prints at 150 metres per minute, but the 1200 x 1200 output is the key and being able to deliver that in a duplex print is very important. We are a big direct mail business, and we produce a lot of marketing material, and the fact that it can also work with stock up to 225 GSM provides us with many applications. We are also looking at some inline finishing products from third party providers to extend the machine‘s capabilities.”
Khan confirmed the FUJIFILM Jetpress 1160CF is expected to be installed at
either the company’s Canberra or Sydney site when the product arrives in July.
Lynch said this was a significant sale for the business.
“We are delighted that Jay has made the investment in the Jetpress 1160CF. It is a testament to his faith in FUJIFILM and also FUJIFILM’s commitment to this business. A lot of the work from Jay and the Reacon Group is perfectly suited to the productivity and quality from the Jetpress 1160CF. This is an exciting time for the Reacon Group – they are a business that is expanding rapidly with high aspirations and great growth plans for the future, and we want to be part of that journey. This is a logical extension of Jay’s involvement with the FUJIFILM business and we can’t wait to get started and install it,” Lynch said.
The Jet Press 1160CF is a continuous feed inkjet device capable of up to 160m/min productivity in full colour. The press can produce up to 20-inch-wide images, which allows for SRA3 size print with bleed. Fundamentally, the output from this press, after finishing, will be A4 to suit the needs of direct mailing applications. The device can be configured either in Roll-to-Roll (RTR), and Roll-to-Loose (RTL) to accommodate third party finishing devices.
Durst launched products across five key platforms at drupa, including large-format printing, label printing, water-based printing, digital corrugated printing, and folding carton production.
With the introduction of the P5 SMP, Durst is expanding its successful P5 Large Format Printing portfolio launched in 2018 for applications in the sign and display, POP/ POS, corrugated packaging and display and industrial decor sectors. Previewed at an event in March, the hybrid LED Super Multi Pass printing system combines efficiency and productivity with maximum versatility. With a print width of 3.5m and a maximum productivity of up to 2,000 square metres per hour, the P5 SMP achieves an annual capacity of 5 million square metres, setting a new benchmark for high-volume digital printing. As a hybrid solution, the P5 SMP can process both roll and sheet material and has the versatile functions of the P5 platform.
Following the acquisition of Aleph in late 2023, Durst has expanded its position in the field of water-based and sustainable printing technologies. On display at drupa was the Aleph Laforte 600 Paper, which was designed for poster and billboard printing. In its most powerful configuration, the printing system achieves an output of 1,000 m2/hour and reaches a new level of quality in poster and billboard printing with six colours and 1,200 dpi.
Durst launched the KJet at Drupa 2024 –the successor to the XJet. The KJet is a new hybrid solution for label printing and is the second product developed in conjunction with Italian family-owned manufacturer OMET. Previewed in March, the KJet is an end-to-end solution that combines OMET’s dual servo flexo printing units with Durst’s state-of-the-art RSCi inkjet technology. In addition, modules for finishing and further processing such as cold foil stamping or die-cutting units can be integrated into the KJet. This flexibility opens up an enormously broad application portfolio for the KJet. The configuration of the KJet is tailored to the specific requirements of each customer.
On display at an exhibition for the first time at drupa 2024, the VariJET 106 is a significant innovation from the Koenig & Bauer Durst joint venture, which will pave the way for the digitalisation of industrial folding carton production. The VariJET 106 was first announced in 2021 and uses water-based inks so that primary packaging for food can be produced. However, the VariJET 106 is also a promising solution for applications in the pharmaceutical, cosmetics and tobacco industries for the economical production of short to medium runs and individualised packaging.
The VariJET 106 covers the B1 format and achieves a printing speed of 5,500 sheets per hour. The monthly print volume ranges from 500,000 to more than 1 million B1 sheets. Thanks to its hybrid design, several finishing units can be optionally integrated into the VariJET. In this way, the VariJET 106 becomes an end-to-end solution that enables economical and fast production of high-quality jobs.
What was missing in industrial digital corrugated printing until now was the colour white. Durst is again taking on a pioneering role in the industry and launching a water-based white ink for the Koenig & Bauer Durst Delta SPC 130. Using white with extremely high opacity on brown corrugated board opens up new design possibilities and enhances transport packaging. By overprinting white, a significantly improved image quality is achieved on almost all topliners and, at the same time, an exact match to spot colours. All inks and fluids used in the Delta SPC 130 meet the current and future requirements of the food industry. The drupa line-up from Koenig & Bauer Durst was revealed in late April.
Durst CEO and co-owner Christoph Gamper told journalists at the company’s drupa press conference that the “little big company” now has more than 1000 staff and 295 registered patents.
“We closed our year a couple of weeks ago with sales revenue of 360 million Euros, shipping 2.2 million litres of ink with 320 service engineers across 33 subsidiaries around the world,” Gamper said.
“We invest 7.5 to 8 per cent of our revenue back into research and development, and we have 4000 installations in 72 countries.”
Pozitive Sign & Graphic Supplies has signed a distribution agreement with automated gluing machine manufacturer, Felix Gluer.
Pozitive owner and managing director, Phil Trumble told Australian Printer he is very excited to confirm the partnership with Felix Gluer – based at Warsaw in Poland.
Trumble is targeting this machine at short to medium run packaging companies that specialise in point of sale displays as well as casemaking, speciality packaging, or boxmaking.
“If you do any kind of hand-gluing, this machine can really automate your
HP announced a strategic multi-year global partnership with Canva, which is set to create unique design-to-print services for more than 185 million monthly users of the Canva platform.
Cliff Obrecht, Canva co-founder and chief operating officer, said the partnership will deliver huge strategic value and fuel customer growth across both organisations.
Canva, founded in 2013, boasts more than 185 million monthly users, including 95 percent of the Fortune 500. In 2017, it launched Canva Print, allowing users to design and print a wide range of products, including business cards, brochures, flyers, stickers, marketing collateral with customisation options, and apparel.
Through this partnership, the Canva community will gain access to professionally printed products directly from HP Print Service Providers (PSPs) worldwide. Canva will expand its print service to 150 countries by 2026, enabling shorter SLAs and significantly reducing its carbon footprint through localised operations.
According to the companies, HP‘s automation software, HP PrintOS Site
production processes. It can apply both cold glue and hot glue simultaneously in any particular shape – whether it is lines or dots or spray,” Trumble said.
“When I met with Felix Gluer, I realised this is a product that many companies should have if they have to apply glue in some way – and a lot of people are still doing this manually,” he said.
Flow, will help Canva extend its reach by automating production and shipping processes for PSPs. This end-to-end solution streamlines print jobs from prepress to post-press with auto-scheduling, delivering colour consistency, security, barcode tracking, optimal productivity, and maximum efficiency through batch production and reduced labour.
Additionally, HP‘s expansion of its PrintOS Suite with new brand-specific features will equip the central Canva Print Operations team with powerful tools to seamlessly identify, connect and manage a vast global SKU catalogue across a network of local HP-enabled PSPs.
Jim Towle, head of print and partnerships, Canva said, ”We‘re excited to partner with HP to accelerate the expansion of Canva Print. HP’s innovations in cloud software, quality management, and digital print have been at the centre of our Canva Print expansion. With our teams now working closer than ever on new products and additional PSP locations, we can expand
Felix Gluer has launched the new twin-head Duet machine at drupa to complement its single-head machine, and Trumble has confirmed he has already received interest from the Australian market.
Felix Gluer head of international sales, Slawomir Marć, said the company now has 200 installations globally through partners in USA, Canada, and Europe since commercialising its products in 2017.
“For Pozitive, this is the missing part of the portfolio. When it comes to packaging on demand you need to print something on carton or corrugated – and then you need to cut it and then you need to glue the box or POS display,” Marć said.
Watch Phil Trumble discuss the partnership with Felix Gluer at drupa
our world-class print capabilities and make it easier than ever for our global community to bring their designs to life.”
In May, Canva introduced Canva Enterprise, a new subscription to meet rapidly growing demand and adoption by large organisations. As part of the multi-year agreement, HP will roll out Canva Enterprise, empowering HP’s global marketing and sales teams to securely create, collaborate, and publish visual content.
Haim Levit, senior vice president and division president of HP Industrial Print, said the announcement with Canva showcases HP‘s commitment to partnerships of this magnitude.
”We‘ve been incredibly impressed by the power of Canva Enterprise and look forward to boosting our team‘s design productivity by removing bottlenecks that stifle creating visual content at scale. Combined with the latest innovations in HP software, we are leading the industry forward for brands and PSPs to become more easily connected, unlocking significant demand to our customers and allowing users to design and print more sustainably.”
Chris Knighton, global sales director, HP Industrial Software, said Canva is leading the way in empowering global teams to collaborate and create high-impact visual content at speed.
”HP PrintOS will accelerate onboarding and ramp of new print volume to our integrated network of HP Print Service Providers, delivering the widest range of print to Canva users in every corner of the world.”
CMYKhub announced the purchase of multiple Canon Colorado M Series with FLXture in partnership with Currie Group at drupa.
“This purchase highlights our commitment to Canon technology, and our belief in the Colorado machines,” Glen Francis, CMYKhub national communications manager, said.
“We’ve been rapt with the two machines that we have already. We bought our first machine at PacPrint in Melbourne and bought the second machine 12 months later because it was just a work horse and we loved it. It’s also a great partnership that we have with Currie Group and we love working with them.”
Dirk Brouns, vice president large format graphics, Canon Production Printing, said the company was thrilled with the purchase from CMYKhub.
“[CMYKhub] run high production volume, which is exactly what these systems are designed for. They are really going to benefit from the next evolution,” said Brouns.
Paul Whitehead, sign & display business unit manager for Currie Group, said the sale extends the partnership in CMYKhub’s growing wide format department adding Canon to the recently announced EFI purchase.
“We’re really looking forward to continuing
Messe Düsseldorf Group and Printing United Alliance announced a strategic partnership at drupa.
Starting in 2024, the partnership of the world’s leading trade fairs drupa and Printing United Expo located in Europe and North America, respectively, will bolster the reach of each brand throughout the industry.
Glen
(CMYKhub), Paul Whitehead (Currie Group), Paul Norton, Alan Nankervis, Dayne Nankervis (CMYKhub) and Craig Nethercott (Canon
our long-term Currie Group partnership with CMYKhub, said Whitehead.
“They’re great machines anyway, and they are reliable, but we certainly wanted to take advantage of this offer while at drupa,” said Francis.
Dayne Nankervis, CEO of CMYKhub, told Australian Printer the company has been in discussions with Canon for two years.
“It’s not an overnight decision and building relationships with the Canon team has really helped this process.
“We don’t work with companies lightly – it takes time, and Canon has proven that they work well with us, so we’re adding them into the fold. They’ll be joining other brands in our business that have been with us long-term.
“We’re very loyal to the brands that we work with, and when it comes to working with a new brand, it’s a combination of things that we look for, and a big part of that is the people in that company.
“Canon has good local staff, good support from their senior leaders in Europe, and their technology has proven to be very
Both organisations will look to make all their events even more relevant and beneficial to both attendees and exhibitors in the everchanging printing technology landscape.
Sabine Geldermann, director drupa, Portfolio Print Technologies, said: “Printing
good, and their future vision and direction matches our business.
“One of the main reasons why we’ve been partners with Currie Group for 10 years is that they continue to service you after you buy the machine. We’ve bought machines from Paul [Whitehead], and he calls us every day after that. It’s not just about the sale, he maintains the relationship.
Alan Nankervis, national wide format manager at CMYKhub, said the company is looking to roll out more Colorado machines across its sites nationally.
“We feel the Colorado model sits on an island. No one else is producing at this speed and quality in this format, and that’s great for us, and it really fits our model.
“We currently have seven Mimaki machines at end of life. We have them in Sydney, Brisbane, Cairns, and Perth, and our one in Melbourne was retired last week.
“They have served us really well and we’ve been really happy with their technology for the time that we’ve had them, but as they’ve gone to end of life we need to start moving on, which is why we’re going to invest into Colorados in all our sites. These machines are much faster and turn out more work, so we probably don’t need as many as we had Mimakis, but we’re going to put them on all our sites, which will produce the same work nationally for our customers.
“Currie Group’s investment in wide format has also been great for us. We’ve purchased a lot of wide format products from them and their investment in service staff to keep those machines running is big for us. This is as big of an investment in Currie Group as it is in Canon for us.”
United Expo’s one-roof approach aligns very strongly with what drupa has brought to the industry over the last seven decades. Showcasing the many applications printing technology has these days, not only in the graphic arts field but in packaging, industrial and textile, is what our attendees appreciate.”
Ford Bowers, CEO, Printing United Alliance, said: “Our partnership with drupa underscores our commitment to advancing the entirety of the printing industry. Together, we will be able to deliver even more opportunities for growth and collaboration to all who participate in the marketplace of events. We look forward in the coming months to sharing our conversations on how this partnership will unfold and the benefits to all our partners.”
X6.0 530
The Van Dyke Press announced the purchase of an OMET XFLEX X6.0 530, in partnership with Currie Group.
Will Tompson general manager of The Van Dyke Press, said the Sydney-based company is thrilled to partner with OMET again after purchasing the first OMET machine in Australia 14 years ago.
“Our relationship with OMET through Currie Group goes back to 2010,” said Tompson.
“We first purchased the OMET [OMET XFLEX X6.0 430], and the machine has been fantastic. But as the business has continued to grow, we needed more capacity, more speed, and more UV power to allow us to run the press faster, and the OMET XFLEX X6.0 530 provides all of that for us,” said Tompson.
“We print aluminium foils, and the OMET XFLEX X6.0 530 allows us to run an additional row for every size. Where we had three across, we now have four, which allows us to pick an additional 33 per cent capacity with no extra operators. Where we were four across, we now go to five and pick up 25 per cent more capacity. We think on a press 100mm wide, we’ll end up with about 60 per cent more output. The speed and width of the machine will make a dramatic difference and allow us to continue to grow and give
Jim Peterson, founder and COO of Vanguard Digital Printing Systems told Australian Printer the company is looking forward to more local growth following the recent installation of its first machine in Australia.
“We’re incredibly excited to have our first couple of installations in Australia,” Peterson said.
“Matt Ashman and the Durst team are
our customers more confidence that we can take on more volume.
“We’re also buying an additional die-cutter for the same work. We will go from three of those to four, and the die-cutters are already set up for 520, so the new wider press will allow us to run our existing three and the new four die-cutters to their full width, so there’s no additional investment. The 530 is a no-brainer for us,” said Tompson.
“Our history is in mold labelling. We’ve been a sheet-fed printing company for 65 years. We started with paper labels such as beer labels, dog food and soup cans. Many years ago, we diversified into mold labels – we were the first company in Australia to do that. Later, we got into sheet-fed lidding for paper-based substrates that could be converted through sheet-fed process because that’s all we had.
“For 15 years, we pursued that business, which went well, but we could never get past a certain point. Too many people were wedded to aluminium lids, and one of the largest customers told us they didn’t want paper anymore; they wanted aluminium, and we had no choice but to buy aluminium or lose a large customer.
carrying the product and we’re so incredibly excited about all the opportunity the Vanguard Digital Printing product has for the area.”
“We went through the research, and we had no pre-conceived ideas of brands of flexo; we had never been in flexo, so we looked at all the presses and believed 14 years ago that OMET was way ahead of the others.
“We had the first OMET in Australia and we were thrilled with it. It was an excellent investment for us, and we thought we might fill half the press with aluminium lidding and then get into shrink sleeve and other associated flexible packaging. We didn’t need to. The aluminium business just continues to grow and now we need more cutters and wider press,” said Tompson.
“Because it was 14 years later, we didn’t go just to an OMET. We had all the main players involved, and we took it very seriously. We took a lot of time researching and having reached this point we’re very happy with our decision.
“My operators weren’t interested in the other machines because they have had such a good experience with OMET in the past. I wanted to do the due diligence and ensure I wasn’t missing something, but my people effectively told me, ‘Why are you bothering? We just want another OMET,’ so we’re very happy.”
According to Tompson, one of the benefits of working with Currie Group is its reliability and extensive network of engineers.
“There are other players out there that don’t have as many feet on the ground as Currie Group. We’re also in sheet-fed, and to see how even the really big players have fewer engineers on the ground, it becomes critical – downtime hurts.
The OMET XFLEX X6.0 530 is expected to be installed before the end of the year.
Vanguard was launched by Durst Oceania at the 2024 FESPA Global Print Expo in Amsterdam. Dan Mantel manages the Vanguard business in Australia and New Zealand. In April, Evan Evans purchased the first Vanguard printer for the local market from Durst Oceania.
Matt Ashman, MD of Durst Oceania, said Durst’s decision to acquire a majority stake in Vanguard Digital Printing fills a gap in the market for Durst for fixed-bed machines.
“We’re really proud to be working with Vanguard. It’s created a huge buzz in the industry because this is the hole Durst needed to fill.”
Watch Jim Peterson discuss Vanguard expansion plans
CMYKhub has made its first investment in cutsheet inkjet production equipment by signing for two Canon varioPRINT iX3200 B3 presses at drupa.
The family-owned company produces a wide range of printed products—from business cards, brochures, stationery, and calendars to banners, signage and display, labels, and packaging for independent printers, franchise groups, print brokers and managers, advertising agencies, and graphic designers.
The investment is the culmination of two years of inkjet research and testing by CMYKhub to find the platform that would best fit its mid-term plans and the needs of its customers.
CMYKhub has confirmed that one of the machines will be located at its new state-ofthe-art headquarters in Melbourne, which
Konica Minolta recorded more than 200 sales at drupa, strengthening its position in digital printing. Its 2,400m² two-storey stand was the seventh largest at the show. The sales and support teams included representatives from Europe and countries worldwide, including Brazil, Korea, Iceland, South Africa, Japan, and Australia.
Konica Minolta introduced more than 20 new products and software innovations, focusing on commercial, label, packaging, and industrial printing, emphasising digital transformation and sustainability. Konica Minolta also showcased advancements in programmatic printing using artificial intelligence (AI) to enhance variable data printing.
Konica Minolta showcased a range of digital presses aiding customers in digital transformation, from the AccurioPress C14000 with more than 2,100 installations worldwide to the AccurioLabel toner presses with 1,500 installs.
is set to open early next year, with the other machine’s location to be confirmed.
“We were already a Canon customer as we have a number of their wide format Colorado devices, so had also followed their cutsheet inkjet developments and had the varioPRINT iX3200 on our list as a potential investment,” said Dayne Nankervis, CEO of CMYKhub.
“We carefully considered a number of other inkjet printers as well but after rigorous testing that included factory and customer visits, it became clear that the iX3200 was the press for us. We trust the technology, and we see some great benefits – the print quality is exceptionally high with vibrant colours and it’s consistent on every substrate.
A key highlight was the integration of processes like foiling, varnishing, printing, and drying into a single production run with MGI’s AlphaJet, demonstrating the efficiency of a complete single-pass digital production line.
Sustainability was a major theme at Konica Minolta’s booth, aligned with the Industry 5.0 philosophy, focusing on efficient, labour-saving, and skill-less operations. Their messaging, “See the Potential in the Future of Print,” emphasised the value of print and sustainable production methods.
Debuting at drupa, the AccurioJet 60000 HS-UV Inkjet Press, capable of producing 6,000 B2 sheets per hour, was a highlight among 30 live-running systems. Konica Minolta also unveiled new configurations and applications with significant implications for commercial printers, brand owners, designers, and agencies. Other attractions included “Ex Kansei,” a predictive software based on eye-tracking insights, and various digital transformation tools.
Olaf Lorenz, general manager international marketing, Konica Minolta Business Solutions Europe, said, “This time more than ever at drupa, we took a unique approach by demonstrating true
“As a B3 printer, it also delivers an excellent level of productivity. And, it’s also so easy to run and has an intuitive user interface. I can understand why it has such high uptime, as it’s a simple machine designed extraordinarily well.
“We’ll start by running lighter weight, uncoated and document-based stocks through the iX3200 for letterheads, books and textbooks, and in time, transition across higher coverage products, such as leisure books, a sector that we want to break into. For CMYKhub, this purchase in the Canon varioPRINT is our first step into cutsheet inkjet, but if it works well for our production environment, we could see a further investment in the future.”
Craig Nethercott, managing director of Canon Production Printing Oceania, said he was delighted CMYKhub had chosen the Canon varioPRINT iX3200 as its first investment in cut-sheet inkjet technology.
“The press is a well-tried and tested platform that hundreds of our customers rely on to profitably service the requirements of their customers, and I’m confident that it will prove to be the perfect start to their inkjet journey and the catalyst for the next stage of in their growth,” Nethercott said.
end-to-end print applications. And we achieved exceptional results, all within the Industry 5.0 framework. Our showcase of a range of new presses in toner and inkjet, highlighted how these technologies complement each other.”
Andrew Cocker, Konica Minolta Australia’s general manager — production and industrial print said, “drupa 2024 was a remarkable event for us, showcasing the innovation and leadership that Konica Minolta brings to the industry. The enthusiasm and positive feedback from our customers in Australia were truly inspiring, reaffirming our commitment to delivering cutting-edge solutions. This event has reinforced our belief in the bright future of print, where technology and creativity continue to drive progress.”
Chris O’Hara, Konica Minolta New Zealand national production print manager said, “drupa 2024 exceeded our expectations, highlighting the strength and dynamism of our offerings. The response from the New Zealand market was phenomenal, and it was encouraging to see such high levels of interest and excitement for our latest advancements. We are excited to continue pushing boundaries and exploring new possibilities to better serve our customers.”
Konica Minolta’s AccurioPress
Digital press
Colour
Up to 7,981
A4 pages per hour
SRA3+
C14000 and C12000 are nextgeneration production printers delivering exceptional print quality, media flexibility, and advanced automation without compromising productivity.
Linney, a full-service UK-based marketing agency, has become the first company in the world to invest in the new single-pass HS Series – developed in partnership with Fujifilm and Barberán.
Fujifilm and Barberán confirmed the first global sale of the HS Series single-pass inkjet solution for the sign and display market, with the deal agreed on the Barberán stand.
Linney, founded in 1851, is a full-service creative marketing agency with more than 1200 staff, offering clients a full spectrum of digital services alongside print production.
Charles Linney, a company director and part of the sixth generation of the Linney Family working in the business, sees the investment as hugely significant: “It’s so important for the business to keep on top of the changing technologies available
Heidelberger Druckmaschinen AG (Heidelberg) is expanding its digital printing portfolio, presenting the new Jetfire family for the growing industrial digital commercial printing market.
The systems are based on leading inkjet technology from cooperation partner Canon. The new Jetfire family will be integrated into the Heidelberg ecosystem via the Heidelberg Prinect workflow.
”Our aim is to offer our customers who want to operate offset and digital presses simultaneously an attractive and integrated service and product portfolio,” said Dr. David Schmedding, head of sales at Heidelberger Druckmaschinen AG and chief sales and service officer.
Heidelberg and Canon see growth potential in the expansion of inkjet printing and want to jointly establish this technology in the printing industry for industrial production. With this step,
in the industry, and something we watch carefully. The HS series really does feel like a huge step forward and will help us cater for the ever increasing speed to market that our clients need.
“In 2009, we were among the first adopters of the Inca Onset range, and our relationship with Fujifilm, which began then, has been very important to us ever since.
“We strongly feel that the time for singlepass inkjet is here; we wanted something with reliability, speed, quality and excellent up-time in equal measure.
Heidelberg is adding sheetfed inkjet solutions to its portfolio alongside tonerbased Versafire systems and sheetfed offset presses.
As a first step, Heidelberg will offer an existing B3 digital printing system from Canon with corresponding integration into the Prinect workflow, its own service and consumables under the name Jetfire 50 from drupa 2024.
The machine is planned to be delivered to customers in the first quarter of 2025. In a further phase, Heidelberg is expected to offer an inkjet digital printing press in B2 format for commercial printing from mid-2025, with first shipments planned for early 2026. This machine will use state-ofthe-art inkjet technology to take industrial digital printing to a new level and will be offered as the Jetfire 75 from Heidelberg.
“On all of these measures, the HS Series has hugely impressed us. It’s 5-10 times faster than the previous technology, the quality is fantastic, and our operators have been mightily impressed.
“We’re excited to be investing in this press, and we’re delighted that it will be Fujifilm and Barberan partnering with us as we do that. Both of them have been fantastic to work with.”
David Burton, CCO Fujifilm Wide Format Inkjet Systems, said: “As they approach their 175th anniversary, we’re delighted that Linney, a partner of ours in wide format print for more than a decade, has chosen to invest in the HS Series. We look forward to an even closer partnership in the coming years as we work with them as they develop the business further.”
Jesús Barberán, owner of Barberán, said the company is hugely excited to be working with Fujifilm on the HS Series project and is delighted to welcome its first customer for this platform.
“Linney, like Barberán, is a family business. And like us, over the decades, they’ve grown by investing in the future and by leading the way in adopting new technologies. We look forward to a long, successful future working together.”
The new digital printing systems are intended to be operated fully automatically in an integrated system together with offset presses using Prinect Touch Free via the Prinect workflow from H Heidelberg.
”Heidelberg is the partner for printing companies that can supply and integrate all modern technologies in a technologyneutral and demand-oriented manner,” said Schmedding.
”We offer the entire spectrum from toner to inkjet, from offset printing to flexo printingcontrolled from a common Prinect workflow.”
The Jetfire 50 is the new digital production solution for industrial print service providers looking for alternative production methods. In B3 sheetfed format, the system combines all the flexibility benefits of digital printing with the stability of inkjet for commercial printing. The press is scheduled to be delivered to customers from the first quarter of 2025.
The new Jetfire 75 based on inkjet technology in B2 sheetfed format is targeted to set new standards in industrial digital printing. The system can print 8,700 B2 sheets per hour. This makes the Jetfire 75 more than twice as fast as previous machines on the market.
Pozitive Signs & Graphics announced the sale of a swissQprint Kudu flatbed to Victoria-based printer Briner Signs at drupa.
First launched at FESPA Berlin in 2022, the 3.2 x 2 metre high-end UV LED printer complements the existing SwissQprint flatbed range –Nyala, Impala, and Oryx. It offers 10 colour channels and three rows of printheads, giving it a new level of versatility in terms of colour options while maintaining speed due to the increased number of printheads.
“The Kudu is the latest and greatest new innovation from swissQprint,” said Warren Davey, national equipment sales, Pozitive.
“Con [Tsakonas, owner of Briner Signs] knew it was the right solution for him based on the machine’s reliability and overall quality. From a business owner’s point of view, it’s about being able to get work out easily because that’s what makes you money. The machine doesn’t make you money, it’s the production that comes off it that does.”
Con Tsakonas told Australian Printer that the swissQprint Kudu suits Briner Signs’ market offering. “I have a new product that is going to be released in the next six to 12 months printing on some real estate
Canon announced an expansion of its production portfolio and its entry into the B2 sheetfed inkjet market with the varioPRESS iV7, a new inkjet press capable of producing 8,700 B2 4/0 sheets per hour (4,350 B2 4/4 sheets per hour).
According to Canon, the varioPRESS iV7 aims to set a new standard in the digital B2 segment by printing up to 4.5 million B2 images per month in 24/6 operation. The first installations of the press in the EMEA region will take place in the second half of 2025.
The new varioPRESS iV7 has also been engineered to address the increasing pressures of commercial print service
A-frames directly on to foam board and this machine ticks the boxes for that.
“In Melbourne, we probably hold about 18 per cent of the [real estate A-frame] market, with about 40,000 real estate signs a year. We’ll get up to 300 signs in and out in 24 hours.”
Tsakonas said the Springvale-based business is also currently trialling a swissQprint Karibu.
“If the trial works, we’ll phase out four HP 3600s and bring swissQprints in to replace them by early next year,“ Tsakonas said.
According to Philip Trumble, managing director of Pozitive, one of the benefits of
The varioPRESS iV7 is capable of producing 8,700 B2 4/0 sheets per hour (4,350 B2 4/4 sheets per hour)
providers (PSPs), online and publishing printers and book producers. Its print quality, productivity and extensive The varioPRESS iV7 will join the new varioPRINT iX1700 and the varioPRINT iX3200/2100 to create a Canon portfolio of sheetfed inkjet presses that serves a greater number of PSPs and delivers a broader range of print products with monthly volumes from 300,000 A4 images up to 4.5 million B2 images.
Printing up to 8700 B2 4/0 sheets per hour, regardless of media weight, the varioPRESS iV7 delivers industrial productivity with minimal operator intervention, as printhead and image quality control are automated and ink can
the swissQprint Kudu is its modularity.
“With the Kudu, what you see today, you can add tomorrow. You’re not going to see something new and be left behind because something else comes out,” said Trumble.
“A lot of people have been watching swissQprint for many years. We talked to Con maybe six years ago, and he made other decisions at the time, which were the right ones for his business then. But, with the Kudu, it seems like we have finally reached that sweet spot of speed and quality in one machine.
“It’s also great working with the swissQprint team because they do things in a very methodical way. Everything they bring to market is reliable, and it’s just a matter of time before they have the next solution that the market is looking for,” said Trumble.
The sale brings the number of swissQprint Kudu flatbeds in production to four, with a fifth to arrive later this year and be housed at Pozitive’s showroom.
“We have machines in the field, but there’s nothing like having a machine in the showroom to see it live in action,” said Trumble.
“The machine will be arriving in July in our Sydney showroom, and we will then move it to Melbourne. We have plans to host an event in Sydney before it is relocated, as well as hold an event in Melbourne once it arrives.”
be refilled without stopping the print run.
Jennifer Kolloczek, senior director, marketing and innovation, production printing, Canon EMEA, said, “Canon has led the evolution of production inkjet for over 15 years, helping customers worldwide to manage their business challenges and gaining vast experience in successfully supporting commercial printers to transition to digital.
“By introducing the varioPRESS iV7 to join the varioPRINT iX1700 and iX3200,, we’re making sheetfed inkjet printing an attractive proposition for operations with volumes as low as 300,000 A4 images per month all the way up to 4.5 million B2 images per month. And we’re achieving this while delivering an unsurpassed combination of print quality, productivity, reliability and media versatility, together with the digital benefits of variable data and on-demand printing.
“Commercial printers searching for the ultimate B2 sheetfed factory should take a very close look at the new Canon varioPRESS iV7.”
Auckland-based printer Torque Digital Print purchased a second Durst P5 350 HS at drupa.
“We purchased our first Durst last year and that’s been going really well for us, so we were keen to have a dual platform of Durst machines,” said Angela Nauck, general manager of Torque Digital Print.
The P5 350 is the hybrid solution for roll and board printing up to 3.5m and reaches in the high speed version a productivity up to 708 sqm/h (7,620 sq.ft/h).
“Our company’s been on a great growth trajectory so we will be taking some of our
older machines and replacing them with the Durst,” Nauck said.
“It’s a new relationship for us with Durst, but we have been really well looked after and well hosted the past few days.
Landa Digital Printing has announced it is launching the next generation of its B1 digital print technology, the Landa S11 and S11P Nanographic Printing Presses.
Commercially available at drupa 2024 and utilising artificial intelligence technology, the new Landa presses can reach 11,200 SPH print speed.
Gil Oron, CEO, Landa Digital Printing said the new Landa S11 and S11P models ”take Nanography to its next level”.
”Following the success of our customers with current Landa S10 and S10P models and based on deep understanding of the industry’s future needs, we are taking Nanography to its next level. The
new Landa models enable printers and packaging converters to not only increase print quality, but also elevate productivity and profitability while further reducing job turnaround times.
“As a mature and proven technology platform, we’re proud that over 50 Landa presses are now at the heart of many businesses in 14 countries around the world - with more than 20 per cent of our customers having placed a repeat order for a second or third press.
”Considered a critical growth engine for folding carton converters, commercial printers, and point of purchase specialists, we’ve entered a new era of print production with Nanography. A time when
“It was fantastic to go to Brixen earlier this week and see the site and meet the team, and now having Graham [Blackall] on the ground for Durst in New Zealand is also great for us.”
Matt Ashman, managing director of Durst Oceania said he is absolutely thrilled to have Torque choose Durst as its exclusive wide format provider.
“Torque is a real tour de force in the New Zealand print industry and the business has evolved tremendously since installing their first Dust hence their need to invest in a second,“ Ashman said.
“The P5 350 HS will enable them to have higher volumes and be able to use both machines to fulfill their jobs.
“The machine is expected to arrive in Q3 this year and we look forward to installing the machine at Torque and sharing the installation story when it arrives.”
previous technology limitations have been removed, and print buyers can finally have what they want when they want it – beautiful print with unlimited design potential produced economically, at market-leading turnaround times, and with the environment always in mind.”
The new Landa S11 and S11P models include a new ink drying system that enables transfer of dry ink from the blanket to the media, at the higher speed of 11,200 SPH. Unlocking additional productivity and improving economic benefits, the new high-speed capability is key for printers and converters looking to produce more jobs with shorter deadlines.
The new Landa S11 and S11P can be customised to the exact requirements of every customer. This means that each new press comes with a choice of four or seven colours, a continuous printing capability, an optional in-line coating unit, and the opportunity to purchase the 11K Module elevating productivity to 11,200 SPH and/or the PrintAI module.
“The new Landa modules provide a significant premium to customers. While much of the new S11 series is based on the same robust and proven S10 platform, with the additional capabilities launched today, customers can expand their service offering or break into profitable new markets. More widely, there’s no question that the B1 digital print revolution is underway, with Landa presses helping many print houses and converters to meet some of the industry’s biggest challengesand take advantage of some of its biggest opportunities.”
Got an event? Send an email to chibbit@intermedia.com.au with all the details and we will put your event on the page
* event dates correct at time of publishing
Visual Impact Brisbane 17-19 July 2024
Brisbane, Australia www.visualimpact.org.au
Printing United 10-12 September 2024 Las Vegas www.printingunited.com
Labelexpo Americas 10-12 September 2024 Chicago www.labelexpo-americas.com
2024 ProPrint Awards 25 October 2024 Sydney, Australia www.proprintawards.com.au
FESPA Australia Annual Conference 25 October 2024 Sydney, Australia www.fespa.com
Heimtextil 14-17 January 2025 Frankfurt, Germany www.heimtextil.messefrankfurt.com
FESPA Global Print Expo 2025 6-9 May 2025 Berlin, Germany www.fespa.com
PacPrint 2025 20-23 May 2025 Sydney, Australia www.pacprint.com.au
Labelexpo Europe 2025 16-19 September, 2025 Barcelona, Spain www.labelexpo-europe.com
Imagination Graphics is your trusted partner in digital printing, graphic and web design solutions. Our team of skilled professionals are ready to assist you with all your design and printing requirements, regardless of size or complexity. Let us transform your ideas into reality and help your business thrive.
Our comprehensive range of trade services include:
• CTP – Computer to Plate
• Graphic Design
• Business Cards
• Brochures
• Posters
• Forms Printing
• Annual Reports
• Books and Magazines
• Signage of all varieties
Partner with Imagination Graphics to take your printing business to new heights.
Co-located with the
This is a rare opportunity to purchase a unique business with a strong customer base and substantial growth potential within the fast-paced outdoor advertising industry.
Since the company’s inception in 1997, we have always strived to provide a unique product supported by our reliable and prompt sales service.
• ADCOAT Graphic Solutions has developed a range of specialised coatings that we supply and/or apply as liquid laminates on a variety of substrates and inks used in the outdoor media industry.
• We have an in-house coating room where we can laminate large-format banners of virtually any size.
• All our coating systems are locally manufactured here in Sydney under our designed formulations.
• Our customer base is built on a long-standing repeat business model for both our coating service and product sales. We supply to local government departments, infrastructure units, and small and large print companies.
For all inquiries and further information on this unique opportunity, please contact Paul Elliott at 0412 383 240 or email paul@adcoatgraphicsolutions.com.au
US T O M LAB E L SP E CI A LIST S 24- 4 8 HO U R P RO D U CTIO N
G E T Y O U R R E SE LL E R S A M P L E P A C K T O D AY
JTS Engineering servicing the industry for all machinery and engineering requirements, has partnered with Longer Machine Industrial Co Ltd to supply a specialised range of paper guillotines systems featuring high speed, precision and safety.
JTS Engineering Services Pty Ltd
Jim Strounis, Owner
•
•
• Large Format Sickers
• Vinyl Cut Decals (transfer stickers)
• Transparent Stickers (white ink)
anything Contact us anytime for all service and guillotine requirements
Mobile: 0433 100 243 Email: jim@jtsengineering com.au
Scott Mohammed, Service & Account Manager
Mobile: 0431 887 501 Email: scottm@jtsengineering.com.au
Unit 5, 80-82 Seville Street, Fairfield, NSW, 2165 Web: jtsengineering com.au
• Specialty Stickers and more for vehicles, shop windows, products, promotion
Revolutionise Your Bookbinding with Our State-of-the-Art Hard Case Solutions.
Print Logistics is proud to offer cutting-edge, hard case binding technology that delivers a new level of durability and sophistication. Our innovative process involves expert casing of the hardcover, resulting in a final product that exceeds the competition in both robustness and elegance.
Elevate your publications, specialty books, and projects to new heights with our superior hard case binding solutions, perfect for customers who refuse to compromise on quality.
• Fast turnaround times
• Competitive trade-only pricing
• Privileged communication
• Family owned and run
• Variety of customisation options to meet your specific needs
“We’ve relied on Print Logistics for years and couldn’t be happier with their service. Their professionalism, precision, and dedication to confidentiality make them invaluable partners. We highly recommend Print Logistics for exceptional printing and binding services.” Principle Design
Print is perception and we treat it accordingly.
Contact Us Today
Phone: 1300 659 029
Email: contactus@printlogistics.com.au
Visit: www.printlogistics.com.au