www.propack.pro August 2022People Technology ProBusinessPack .pro ALSO INSIDE... OMET’s new demo centre A FOCUS ON: Leading in digital with EFI Nozomi Learn the potential of EFI’s digital Nozomi range and the opportunities it creates in packaging All attention on Labelexpo Americas 2022’s biggest label converting show will be in Chicago as Labelexpo Europe gets postponed Shorter runs in focus at Auspack Auspack 2022 was a huge success and the next 2024 show is expected to be bigger and better epson.com.au Epson’s atL-4733AWSurePressnewshinesPacPrint Its other products showcased also attracted attention at the tradeshow
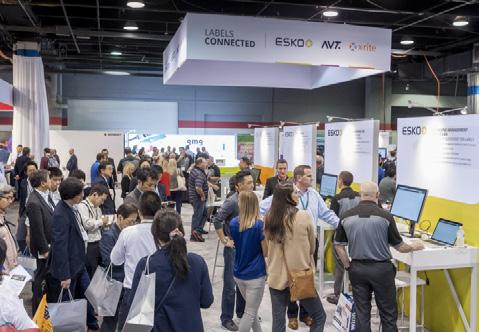
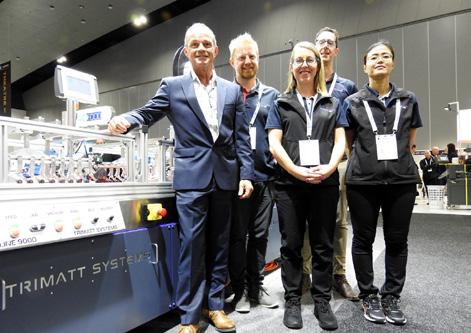

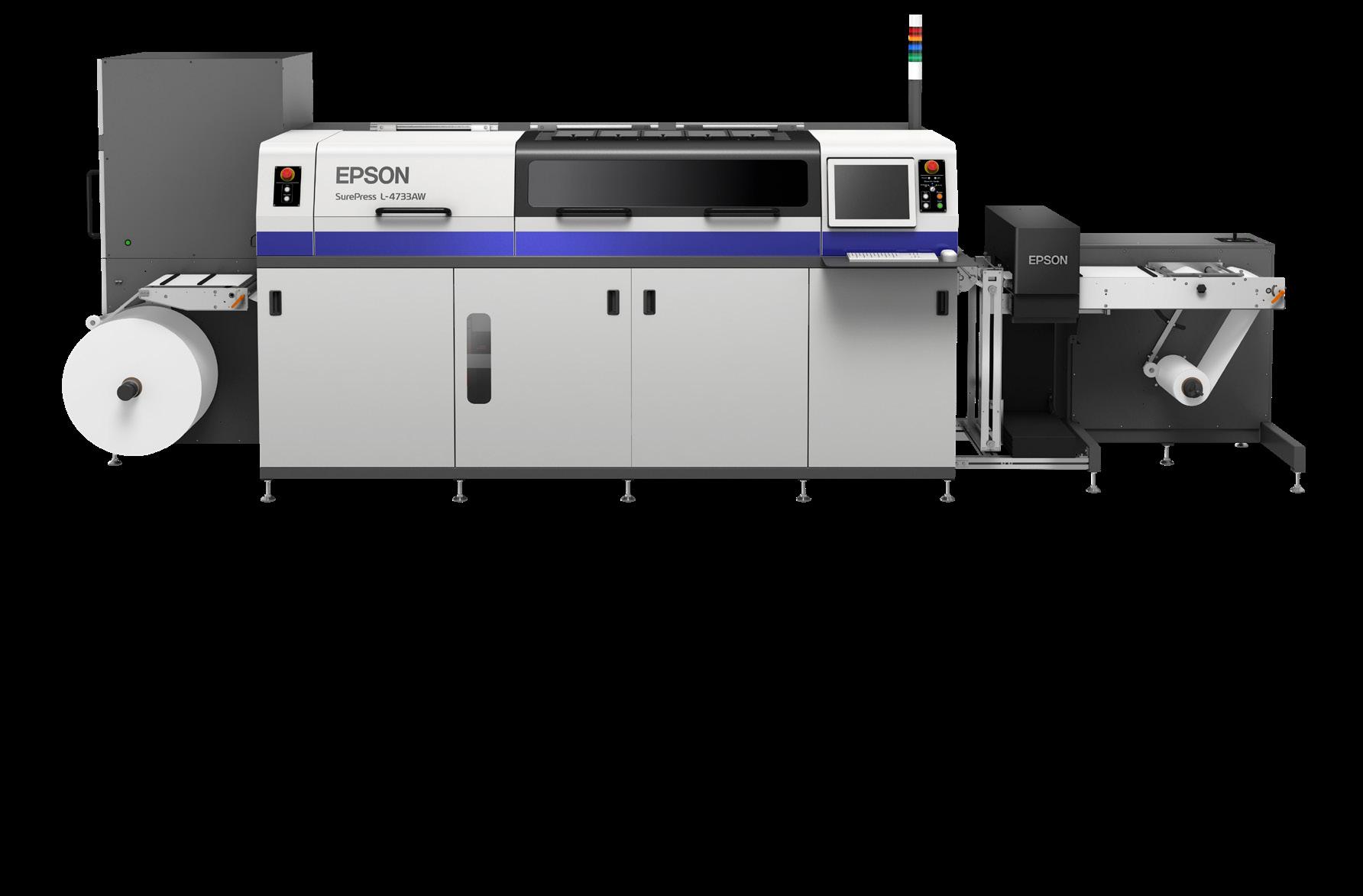
Thank you for being absolute legends as always. We got the flyers delivered yesterday and they are great. Lis
My client is super impressed Mel We just received those 4 kinds x 500 round corner cards back. Wanted to just say a big thanks for getting them done in a hurry for us – they look spectacular, too! Great print & finish. Tom
The client is super happy with how the print job turned out for the box and slips. I wanted to say thank you as I know there was a bit involved with the die cutting. Jessica Marco Thanks for your assistance with this print job. All received and printing looks great! Really appreciate the speedy turnaround.
Just wanted to let you know that we have had a great response to the latest brochure you printed. The retailers love it! Thanks for another great printing job!Nicole
Just want to say thank you for all those urgent jobs. Even the stickers that we didn’t think would make it.
AUSTRALIA’S BEST TRADE PRINTER ‘CUSTOMER IS KING AT HERO PRINT’ ...AND IT SHOWS AUSTRALIA’S BEST TRADE PRINTER o ^Queen
A great label essentially shows the world what your customer stands for, makes people remember their brand and helps end users understand if the product is the right fit for their needs. Labels communicate all that using typography, colour and other design Packagingelements.andprinting companies also need quality machines to be able to produce these labels. Not only should the design of the label be good, but the print itself should be of quality to bring out the best of the label.
© 2022 — Charted Media Group Pty Ltd Hafizahwww.propack.proOsman4 ProPack.pro August 2022
Ph:hosman@intermedia.com.auEditor+61431466140
Hafizah Osman
Consumers interact with labels on a daily basis. It’s no secret that on many occasions, we get drawn to a particular product by the appeal of a well-designed and executed label – a little extra flair is all that’s needed to catch one’s eye. As such, labels are becoming more and more in focus as packaging and printing companies refine them to enhance the premium look and feel of their customers’ products, especially with the surge in the growth of e-Commerce. Companies are experimenting with various substrates and finishes to help their customers create labels that stand out and are works of art.
Copyright
But that’s not the only reason labels are getting a revamp. With sustainability playing a huge role in the entire supply chain of packaging, incorporating clearer recycling directions on labels is now becoming a must.
EDITOR’SStayNOTEinformed… visit www.propack.pro and subscribe to receive the latest packaging industry news and views ProPack.pro is published by Printer Media Group, registered in Australia ABN 47 628 473 334. This publication may not be reproduced or transmitted in any form in whole or in part without the written permission of the publishers. While every care has been taken in the preparation of this magazine, it is a condition of distribution that the publisher does not assume any responsibility or liability for any loss or damage which may result from any inaccuracy or omission in the publication. Labels become more dynamic and powerful ProPack Industry Supporters Managing Director & Publisher: James Wells Editor: Hafizah Osman Design: Sarah Vella Sales Manager: Carmen Ciappara Production Manager: Jacqui Cooper Pre-Press Manager: Tony Willson Printed by: Hero Print, Alexandria, NSW 2015 Mailed by: D&D Mailing Services ThisDISCLAIMERpublication is published by The Intermedia Group Pty Ltd (the “Publisher”). Materials in this publication have been created by a variety of different entities and, to the extent permitted by law, the Publisher accepts no liability for materials created by others. All materials should be considered protected by Australian and international intellectual property laws. Unless you are authorised by law or the copyright owner to do so, you may not copy any of the materials. The mention of a product or service, person or company in this publication does not indicate the Publisher’s endorsement. The views expressed in this publication do not necessarily represent the opinion of the Publisher, its agents, company officers or employees. Any use of the information contained in this publication is at the sole risk of the person using that information. The user should make independent enquiries as to the accuracy of the information before relying on that information. All express or implied terms, conditions, warranties, statements, assurances and representations in relation to the Publisher, its publications and its services are expressly excluded save for those conditions and warranties which must be implied under the laws of any State of Australia or the provisions of Division 2 of Part V of the Trade Practices Act 1974 and any statutory modification or re-enactment thereof. To the extent permitted by law, the Publisher will not be liable for any damages including special, exemplary, punitive or consequential damages (including but not limited to economic loss or loss of profit or revenue or loss of opportunity) or indirect loss or damage of any kind arising in contract, tort or otherwise, even if advised of the possibility of such loss of profits or damages. While we use our best endeavours to ensure accuracy of the materials we create, to the extent permitted by law, the Publisher excludes all liability for loss resulting from any inaccuracies or false or misleading statements that may appear in this publication.
Companies are also choosing to even add smart and virtual elements to their labels, to provide end users with more information about the product and company that produces it, to offer security around its supply chain and for more engagement with the users.
This issue of ProPack.pro looks into the labels world and the latest machines and trends that are moulding this space. We also look at the upcoming Labelexpo Americas tradeshow, and the innovations that will be shown at the event. With highlights from the recent Auspack tradeshow also included in this edition of the magazine, it’s one that will provide an interesting read.
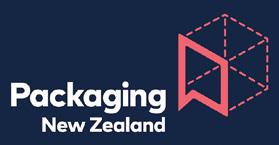
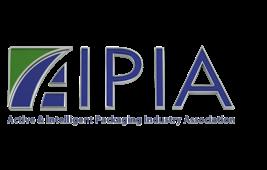
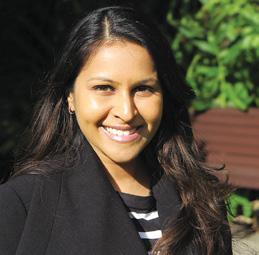
P22-23
With the postponement of Labelexpo Europe until 2023, all eyes are now on Labelexpo Americas 2022, taking place from 13 to 15 September in Chicago Xeikon to showcase TITON technology at Labelexpo P32
Kissel + Wolf prioritises print and packaging at PacPrint P18 Kissel + Wolf showcased its range of innovations at PacPrint, educating and offering its customers solutions in workflow and efficiency
Brand owners and digital print specialists have confided a mild disappointment that some idealistic predictions of digital conquest have not yet come to pass Epson’s new presses attract attention at PacPrint P12-14
www.propack.pro August 2022 ProPack.pro 5
Auspack: Shorter, agile runs power up packaging P24-27
Auspack 2022 was a huge success and, with the change to APPEX for 2024 and the increased floorspace, it will be bigger and better in future
Modern packaging minimises waste of resources P6-8
The new toner formulation offering all the benefits of UV inks without the disadvantages will be on show at Labelexpo in September Pack diary P34 A guide to the upcoming packaging industry events globally
Creating opportunities with EFI’s Nozomi range P22-23
THIS SUPPORTED BY
Digital is part of the mainstream workflow for the Nozomi range, says EFI’s Richard Cotterill as he unpacks the opportunities of the presses
The company has installed a Zünd cutting table with board handling system at one of Opal Kiwi Packaging’s Auckland sites P12-14
ISSUE
What’s holding back digitally printed packaging? P10-11
2022’s biggest label converting show is in Chicago P28-30
The 1,500 square metre showroom in Molteno houses OMET’s new KFlex line, a flexo printing machine capable of being reconfigured at any time
OMET inaugurates new demo centre in Molteno, Italy P20
Aarque brings Zünd to NZ’s Opal Kiwi Packaging P16
P28-30P24-27
CONTENTS IN THIS ISSUE...
The PacPrint tradeshow was the best one for Epson yet, with the company seeing an overwhelming interest in its SurePress label solutions
Food and drug safety remain the benchmark in developing new approaches to waste minimisation, according to VDMA

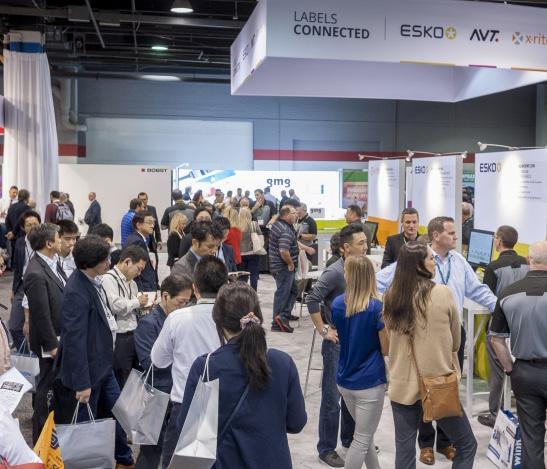
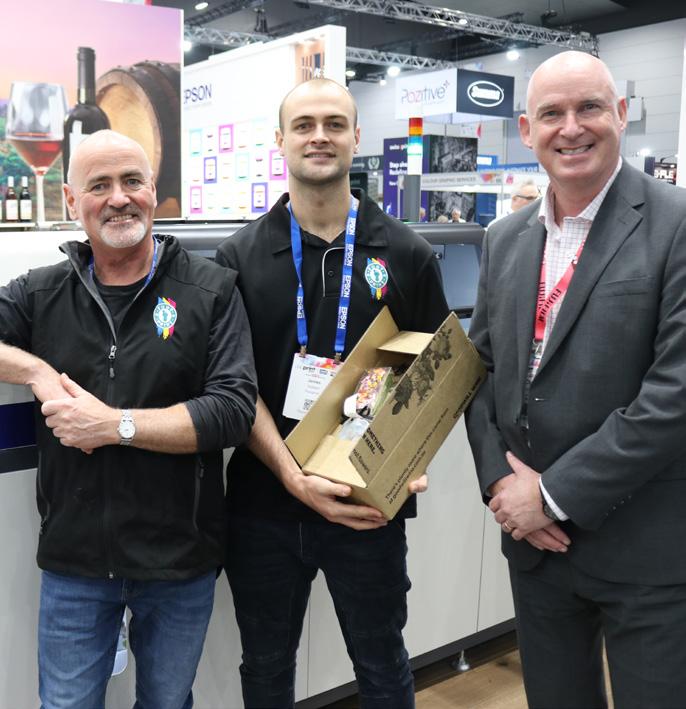
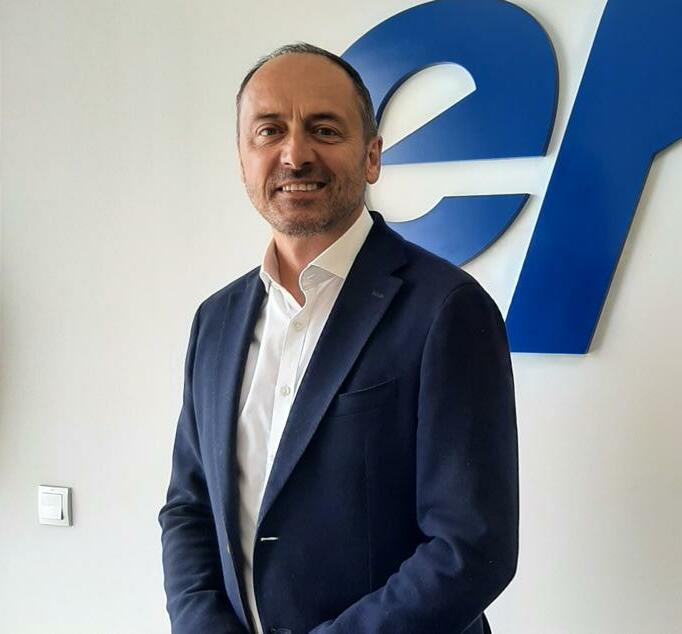
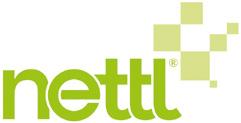
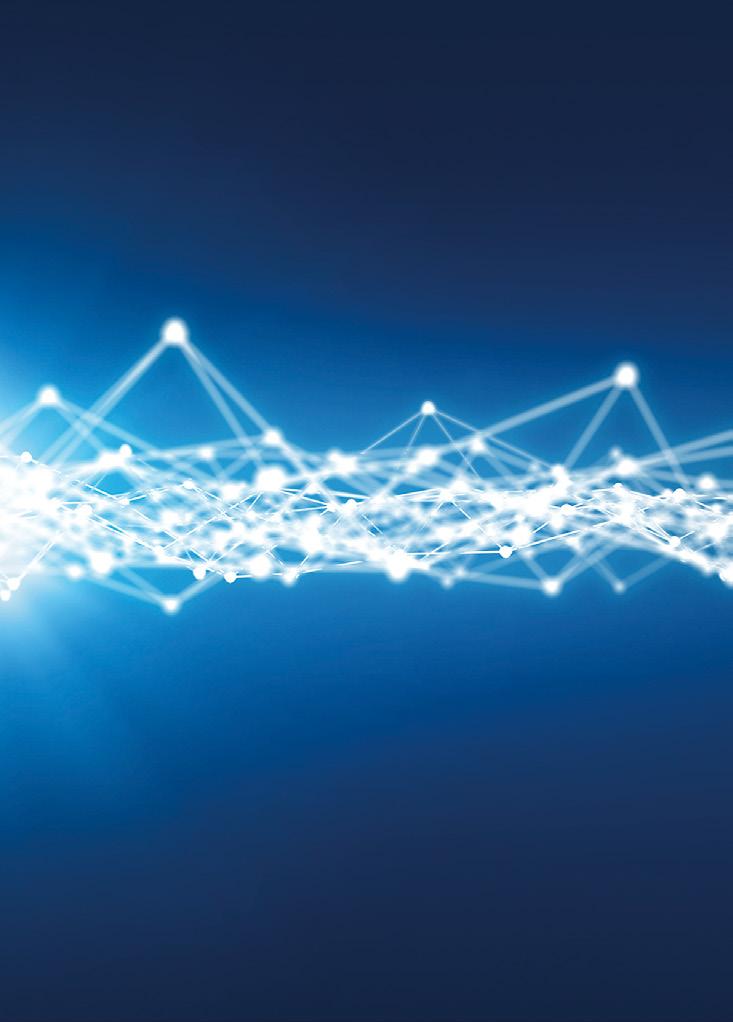
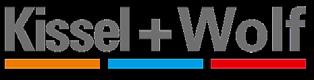


A good third of our employees now come to work by bike. The electric support is welcome to them in our mountainous region. In our production and assembly, we rely on state-of-the-art energy-efficient machinery from machining to painting. Especially in the paint shop, it’s not just about saving energy, but we also have cleaning systems with solvent recovery there to make the processes as environmentally friendly as possible.
Timo Kollman (TK), managing director of packaging solutions manufacturer Hugo Beck, discusses the steps the company has taken towards the circular economy.
www.propack.pro6 ProPack.pro August 2022 LABELS & PACKAGING
Food and drug safety remain the benchmark in developing new approaches to waste minimisation, according to VDMA
VDMA: Do you use recycling and waste avoidance concepts in your own production?
Modern packaging minimises waste of resources
TK: In addition to the now obligatory sorted disposal of production waste and operating materials, we generate electricity for our production, assembly, and administration building with our own photovoltaic system. We also feed some of it into the power grid. We have also invested in charging points for electric vehicles and have a very wellreceived leasing offer for e-bikes.
The Hugo Beck plant near Stuttgart, Germany I n the “Circular Competence” interview series, the VDMA Printing and Paper Technology Association asks its member companies about their plans, challenges, and solutions on the road to a circular economy. What can the industry do to minimise the ecological footprint of packaging and other printed products?
VDMA: What circular economy solutions do you offer your customers?
TK: This starts with the drives of the packaging machines we build. Here we consistently use servo motors that recover energy during braking and feed it back into the system. With modern drive technology, however, we are above all able to optimise the packaging processes themselves. In this way, our customers save on consumables on a grand scale. This applies to both their films and paper packaging. A good example is the cucumber. After discounters stopped shrink-wrapping them in film, they had to dispose of up to 40 per cent due to transport damage and premature spoilage. We have developed solutions to work with much thinner films. Instead of 40 to 60 micrometres (μm), they are now less than 10 μm thin and made of recyclable monomaterial. With the same amount of plastic, four to six times more cucumbers are packed and the unnecessary waste of energy and resources due to the losses is put to an end. Our machines can not only process thinner material, but also make better use of the films through optimised cutting. And on top of that, our customers can use films with a high recyclate content. Among other things,
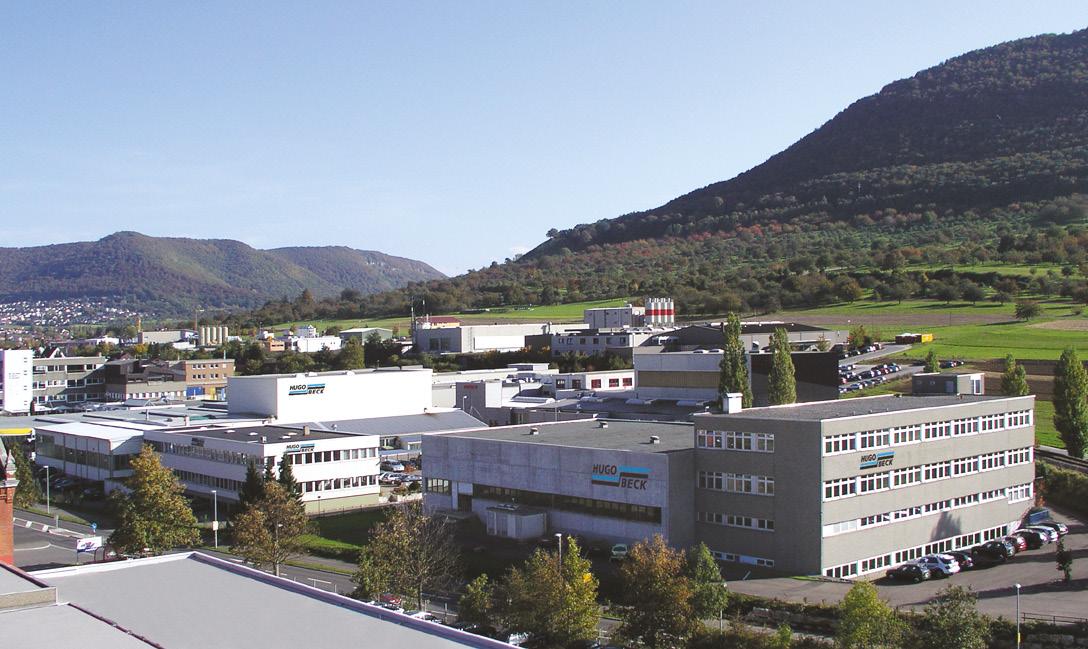
www.gd90.de
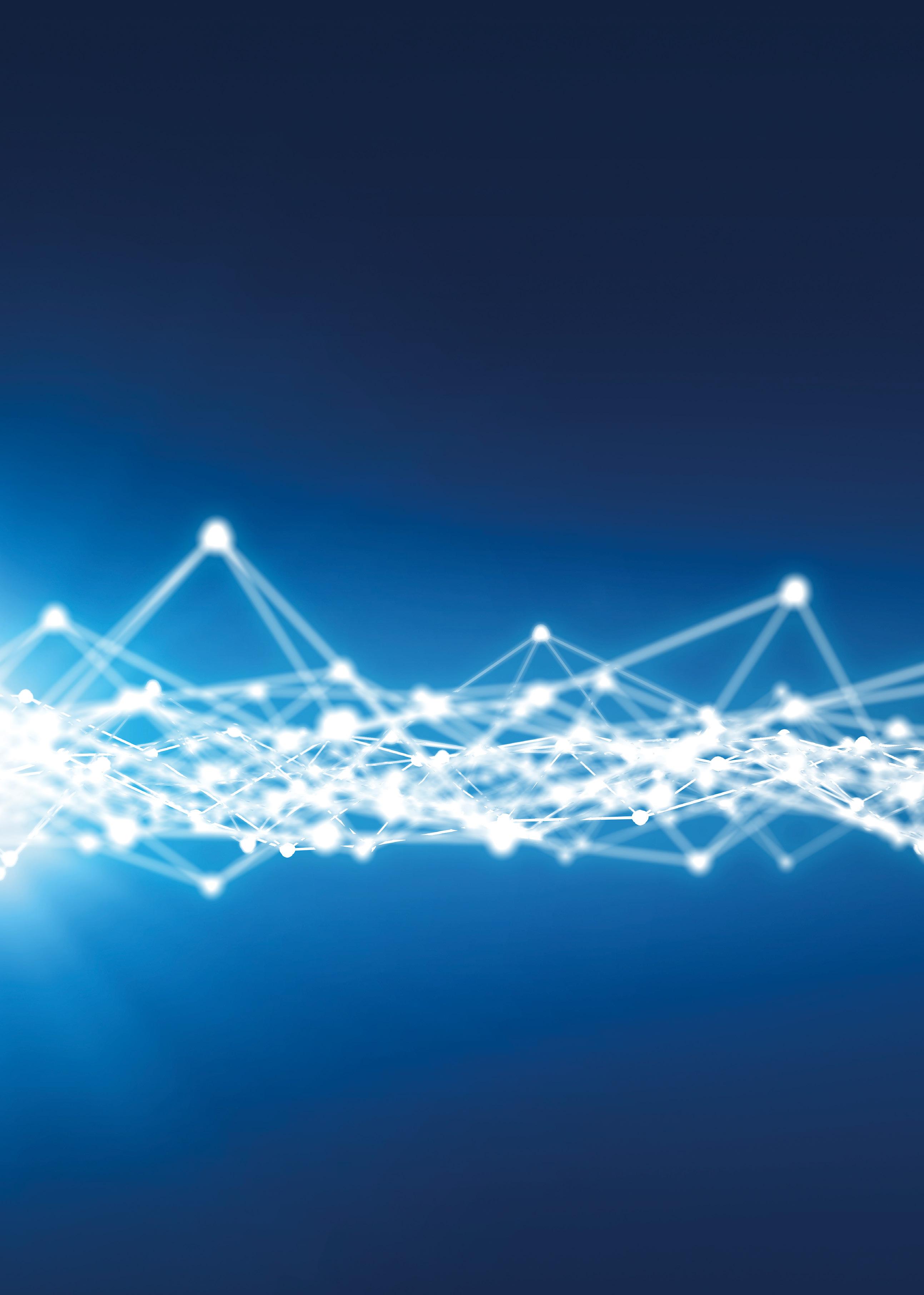
TK: We are working more closely together and jointly scrutinising which material meets the requirements for the respective application with the lowest energy and ecological footprint. Currently, many customers rely on paper. We are working on expanding its range of
Timo Kollman, managing director of Hugo Beck
www.propack.pro8 ProPack.pro August 2022 LABELS & PACKAGING
Hugo Beck is successful with both film and paper packaging technology. So, I am not biased, but simply wish for regulatory decisions that are preceded by wellconsidered and technically sound decisionmaking processes. Only in this way will we succeed in effectively reducing the burden on the environment. We no longer have time for pure symbolic politics.
Food and drug safety remain the benchmark when we develop new approaches. In other areas, I too consider some packaging to be dispensable. In close cooperation between material evelopment, mechanical engineering, and users, we should use all possibilities to minimise the ecological footprint of packaging. The key to this is reduced material use and recycling-friendly monomaterials. At the same time, it is important to establish functioning disposal and recycling systems all over the world.
applications. For example, in a funded research project with a university, we are developing bio-based coatings from waste from wine production, which make paper water-repellent but still recyclable. Our part is to develop the processing methods for these papers. But there are regulatory limits to their use. Frozen pizza, for example, may not simply be packed in a carton: The obligatory film prevents contamination by outgassing chemicals.
VDMA: Is the demand for your circular competence increasing worldwide? Or is this more of a regional phenomenon?
It is not the case that paper is always the more ecological solution than plastic. The weighting is shifting towards plastics as the proportion of recycled materials increases. This is because a certain amount of fresh long fibres will always be necessary in packaging paper and cardboard.
VDMA: Environmental protection is often driven by regulation. Are the framework conditions right for entering the circular economy?
TK: Fortunately, this is now a global trend. Whereby the orientation also depends on regional conditions. Where no trees grow, our customers tend to use plastics rather than paper. In densely wooded regions it is the other way round. But in general, environmental awareness is on the rise and is increasingly influencing which machines our customers invest in.
The VDMA Printing and Paper Technology Association represents 170 European equipment and systems manufacturers of printing, print processing, paper manufacturing, converting, and auxiliary materials and equipment, around 90 per cent of the industry in Europe.
TK: Even before the plastics debate, we worked hard to make packaging as environmentally friendly as possible. Because they are often indispensable. Worldwide, about one third of all food is lost every year along its value chain, i.e., from harvest to consumer. Not only food is lost, but also the resources used for cultivation, harvesting, processing, transport, and storage.
The trade association offers its members services, for example on topics such as trade fairs, public relations, technology and research. we have very good experience with films made of up to 80 per cent recyclate.
One key to minimising this waste of resources is packaging. In pharmaceutical, medical, and other sectors with high hygiene requirements, products will remain packaged. It is therefore important to search with a cool head on a scientific basis for those solutions with which the respective packaging requirements can be implemented with the smallest ecological footprint.
VDMA: How does the topic affect your research and development and your co-operations with customers and material suppliers?
The technical design plays a decisive role here: if you invest in cheap drive technology and immature web guiding, you end up paying for it through the additional consumption of film, paper, and energy - and thus pollute the environment. The extra cost of modern technology is usually amortised within the first two years.
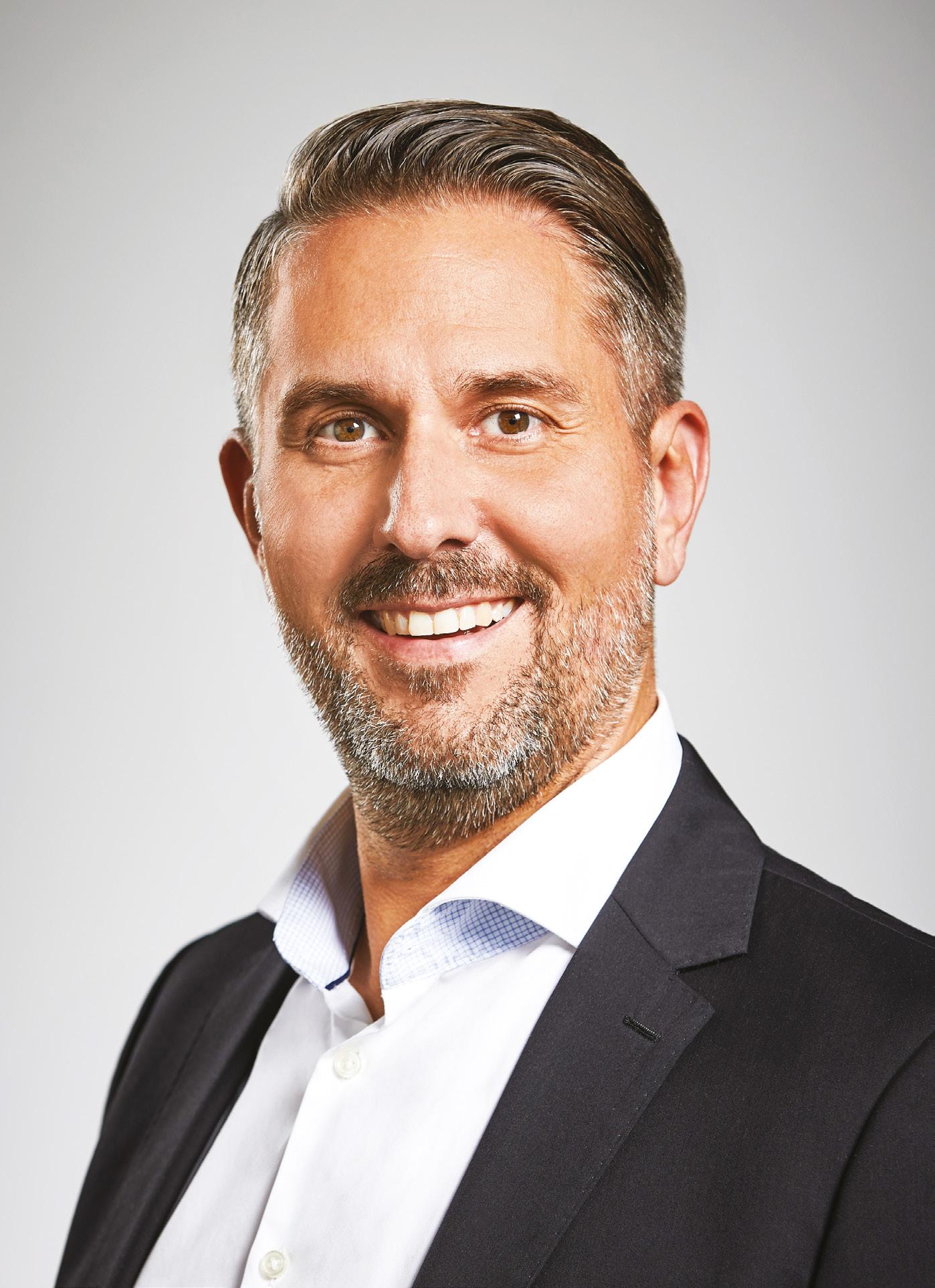
Ideal Solutions for Your Plate Making Needs DuPont Australia Pty Ltdwww.cyrel.comWith20+ years of history in technology and innovation on thermal plate processing for the flexographic printing industry, DuPont™ Cyrel® Solutions is the most experienced partner your company can count on. Be it for the Wide Web Flexible Packaging Industry or for the Tag & Label Industry. The Cyrel® FAST thermal workflow delivers on your in house plate making needs. Cyrel® Fast flexographic plate processing enables cost savings, delivers on your sustainability needs whilst producing high-quality print results for your customers. DuPont™ Cyrel® FAST TD 2000

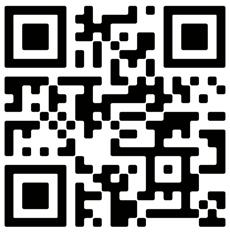
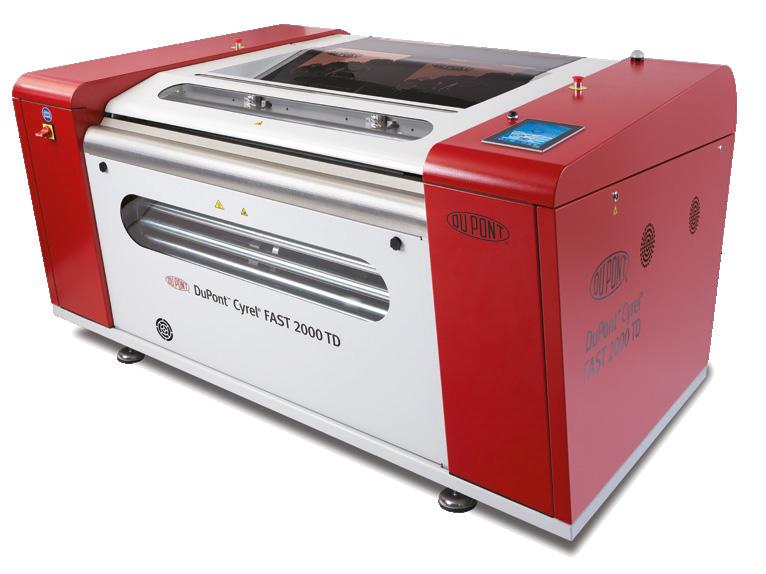
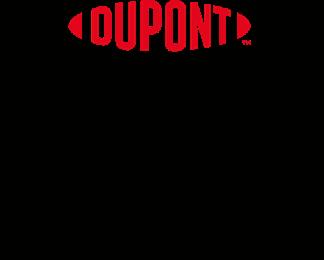
Digitally printed packaging caters to a swathe of different markets The future promises changes to the entire packaging production chain
By Tim Sykes, Packaging Europe brand director
What’s holding back digitally printed packaging?
W hen all the market research of recent years is projecting market growth of between 10 and 15 per cent compound annual growth rate over the coming years, with corresponding advances in market share, it may sound unnecessarily provocative to suggest that digital print in packaging has failed to fulfil expectations.
However, in off the record conversations over the last couple of years, both brand owners and digital print specialists have confided a mild disappointment that some of the more idealistic predictions of digital conquest have not yet come to pass.
What are the reasons for this? And is the post-COVID world closer to the tipping point? Not bespoke We’ll start with perhaps the most basic and obvious point: the largest chunk of the market is still serving long run jobs for packaging destined for the shelves of bricks and mortar retailers.
Conversely, as analogue print technologies are adapted to function within this connected ecosystem, they will become quasi-digital themselves. Rewriting the rules Digital print facilitates an altogether more intimate degree of consumer engagement just as the broader digital transformation of our world is making consumers expect
However, all too often the end user isn’t thinking as fast as the technology. As a major corrugated converter recently observed to me, they can handle an artwork change in little more than a day on traditional presses. If the brand owner’s marketing sign-off takes days or weeks, is it possible that the bottleneck is as much a business systems problem as a technological one?
Of course, there remains huge demand for generic packaging produced in high volumes and at high speeds. And analogue presses still handle the bigger runs more cost effectively, in addition to which they tend to be a considerably less costly investment. This is hardly news, but those of us who get intoxicated by disruptive innovation could do well to remind ourselves of the enduring gravitational pull of simple mathematics. As long as not everyone needs bespoke, there will be a place for analogue. Time to market
The value proposition of digital print is familiar enough: the ability to go from PDF to POS in a matter of hours doesn’t just make short runs and cool customisation campaigns economical but enables supply chain efficiencies and leaner stock management.
Digitally printing a package thus caters to a swathe of key market trends and demands from agile marketing campaigns and proliferation of SKUs to streamlining processes for faster time to market.
As Montserrat Peidro, former head of Heidelberg’s digital print business, remarks: “The main advantages of digital print can be quantified in terms of cost per box in short-mid runs, in faster turnaround times resulting in a leaner supply chain and in its ability to produce unique boxes profitably. Examples include packages with security features, unique identifiers for track and tracing of goods, codes for connected packaging and those personalised for a specific individual.”
www.propack.pro10 ProPack.pro August 2022
There is a significant and growing packaging market space where digital print can add value. Brand owners need to differentiate their multiple SKUs and increase frequency of marketing campaigns to maintain consumer attention. In this landscape, flexibility rather than raw throughput is key to productivity.
Marcelo Akierman, HP Indigo marketing manager for the EMEA region, says: “The printing speed of analogue does not take into consideration all the presses set-ups, including colour calibrations, waste and plates making and mounting. The time to market printing digitally is dramatically reduced; brand owners can do the proofing on site and when the target is achieved sign on the final substrate.”
Brands need to become as agile as digital presses if they are to leverage their full potential, and they need to get used to making more decentralised marketing Harnessingdecisions.thevalue of digital print will rely on integration into the wider value Françoischain.Martin, senior communication advisor at Bobst, says: “We often forget it, but packaging production is more than printing and part of a longer supply chain, from packaging design to printers, converters, packers, retailers on-line or “Printingphysical.digital will save a few hours, even a few days, in a process taking months. The entire packaging production chain needs to be rewritten. Digital printing will be part of the new Industry 4.0 packaging landscape, but the digitalisation of an entire process will be the most important element.”
DIGITAL INTRODUCTION
Brand owners and digital print specialists have confided a mild disappointment that some idealistic predictions of digital conquest have not yet come to pass
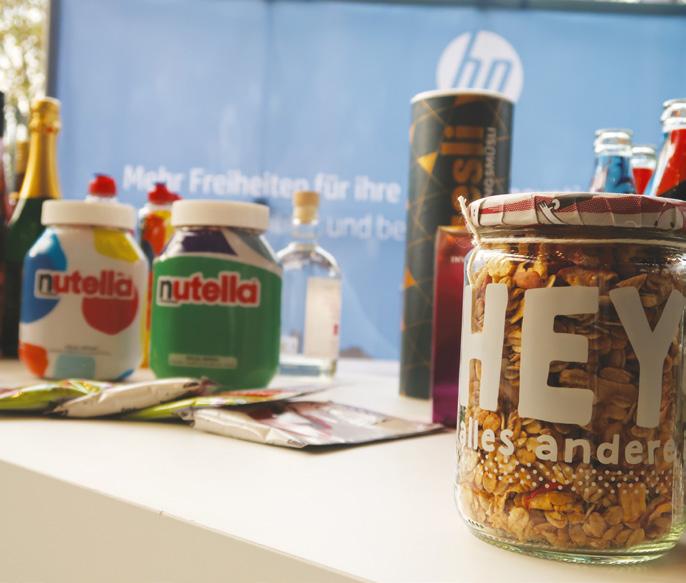
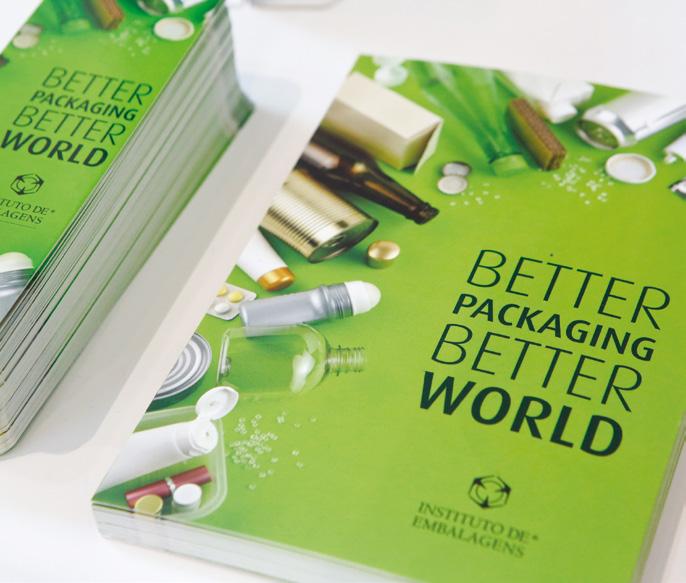
“When packaging is produced in a latestage customisation process, using digital printing is not only possible, it is preferred by brands that want to connect with their consumers by adding personalised messages and images to their packaging. These messages can include support of regional sports teams, seasonal messages, and/or images of local interest.
“Compare this close customer relationship with the more traditional process whereby brands ship products to distribution centres. In this supply chain, products are distributed to vast geographic and demographic markets, with little opportunity for personalised packaging experiences.”
Jose Gorbea, head of brands and agencies at HP GSB EMEA (and formerly of Mondelez), says: “Personalisation goes far beyond customising or styling products. It is about intelligently curating and shaping the whole experience for those in our community: makers, designers and consumers alike.
However, return on investment will increasingly require more sophisticated strategies than the now familiar ‘product with your name on it’. This is a new game, and the rules of how to create meaningful experiences through customised packaging are still being written.
Another consideration is that industry earthquakes don’t always happen overnight.
Even in industrialised countries many fields were being cultivated by manual labour decades after the invention of the mechanical plough. We tend to embrace change when we must, especially when we suspect that return on investment may be Speakremote.toany of the big players about the enablers of digital print and eventually they will acknowledge that getting the market to understand the opportunity is the key challenge.
www.propack.pro August 2022 ProPack.pro 11 gratifying communication from brands across every moment of truth.
“Meanwhile, if they don’t have digital, converters may prefer still to keep running longer runs in their existing presses without the need to invest further.
Late-stage customisation, at least in higher value goods, will surely become the Meanwhile,norm.
Even before the coronavirus changed everything, it seemed inevitable that the irresistible rise of e-commerce would be the ultimate catalyst for growth in digitally printed packaging. In the first place, the online brand or vendor has a much more personal relationship with me than the traditional shopper in a conventional supermarket. It’s a oneon-one communication.
As a direct to consumer brand of a different sort, and on a very different scale, to the FMCG giants, Packaging Europe back in 2019 conducted a customisation experiment of our own. We distributed our magazine in corrugated sleeves featuring 20 localised designs and printed on a HP PageWide C500 press.
DIGITAL INTRODUCTION
target messages directly at individual groups of customers and join social movements. The speed of digital printing also allows brands to interact with real world events. For example, you can now print the daily news on a package to communicate product freshness.”
“The solution comes in educating both brands and converters about the possibilities of digital, and every day, we can see more and more digitally printed products in the supermarkets and online.”
“One industry shift is personalised storytelling, with mass customisation seen as the next frontier for global brands. With digital print, design runs that used to number in the tens of thousands can now vary unit by unit, making labels, cases, POS materials and direct mail more relevant and personal than ever “Companiesbefore.cannow
Amid such endless possibilities and several truly impressive applications there is also a sense that brands are only beginning to map the new landscape. If digitally printed packaging represents a cultural, as well as a technological, revolution, I have the sense that what we are seeing today is an influential counterculture rather than mainstream. Inertia and investment
Direct to consumer I made the connection above between digital printing and the broader digital transformation of manufacturing. Of course, with online retail we can see this in the context of a wider digital transformation of our culture and commerce.
The brand knows who I am, where I am, what I like. It is going to deliver a product, possibly tailored to my needs, directly to me. Leveraging consumer data enables brands to communicate in a personally meaningful way.
The same dynamic applies to the new and emerging supply chains, vastly accelerated by COVID, that are based around personalised consumption, and served by emerging direct to consumer, on demand or subscription models.
In this ecosystem, relevant communication that reflects the consumer’s needs and identity are likely to distinguish the most successful brands.
successive advances in technology are cumulatively eroding all those barriers to adoption. We will see improved quality, higher speeds, lower costs, more viable market entry points, more seamless integration, and developments in design tools such as algorithmically generated iterative engines. All this innovation will be on show at drupa 2024, and I can’t wait to see it.
The #unboxingEurope campaign got a warm response from our readers – ‘love’ that came from the ability to leverage individual subscriber data. Knowing our readers’ location enabled us to give each one not just a nice surprise, but a personally meaningful one.
Donald Allred, vice-president of packaging at Memjet, says: “There’s no question customisation is one of the biggest trends driving the adoption of digital package printing.
Klaus Lammersiek, marketing manager for HP Indigo Labels & Packaging EMEA, says: “Brands are facing more SKUs and shorter runs but are quite busy in their day to day preoccupations to understand that digital can go beyond the ‘special projects only’.
Visitors to drupa 2024 will see innovations in digitally printed packaging
Montserrat Peidro, former head of Heidelberg’s digital print business, echoes this perspective, saying: “In my personal experience in recent years, the main enablers have been the ability to integrate digital technology into existing prepress and post-press processes, sell new benefits to customers, and manage lots of smaller jobs per day in an efficient way, with as few touchpoints as possible.
“But not all companies are aware of these enablers or take these topics into account when planning their investments.”
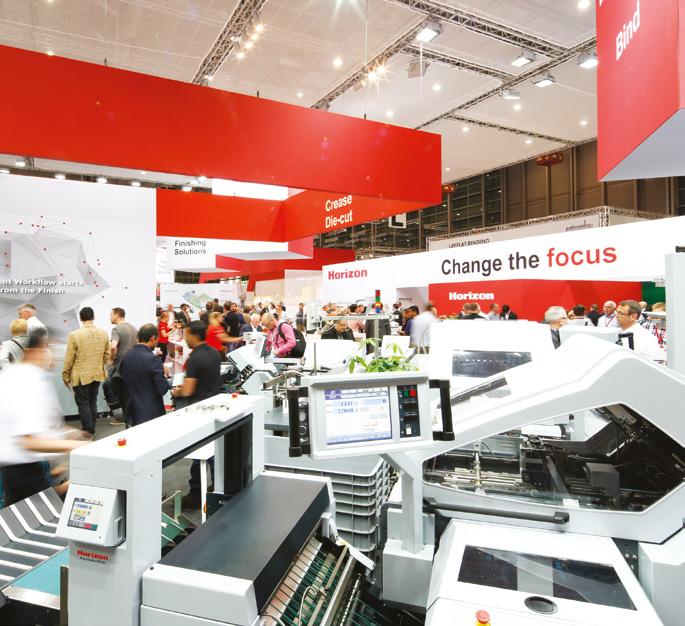
“PacPrint was the most successful event to date for Epson Australia, with an overwhelming number of enquiries and interest for Epson SurePress label solutions,” Epson Australia general manager of marketing Bruce Bealby said.
The company showcased a range of its latest innovations at the event, including its SurePress L-4733AW with its inline spectrophotometer, and the SureColor V7000 UV flatbed printer.
E pson Australia saw an overwhelming interest in its new label presses featured on its stand at the recent PacPrint tradeshow.
The SurePress L-4733AW is a water-based resin ink digital label press, which aims to deliver improved automation.
“Or you could be thinking that you need to reduce running costs and invest in a versatile digital label press which delivers the most cost-effective entry solution into short-run label production. We have a solution for you too.”
With the optional SureSpectro AS-4000 inline spectrometer for real-time automated measurements to speed profiling and ensure consistent output for multi-plant networks, the L-4733AW delivers accurate spot colours and gradients required for brand-quality colour prime labels and packaging.
Epson has been manufacturing digital label presses for over 10 years in Japan, with over 500 installations globally. Global customers include the Osaka Sealing Printing company that just installed its 29th SurePress L-4000 series label press.
www.propack.pro12 ProPack.pro August 2022
“Epson is a world leader in inkjet technology with its own patented inkjet printhead and robotic controller technology. Epson continues to develop cutting edge product design which is innovative and ultimately exceeds customers’ expectations in terms of print quality, build and after-sales service,” Bealby said.
“The current pandemic could have created a situation of ‘technology deprivation’ over the past two years, or perhaps it’s just time for label converters, commercial printers and manufacturers to seriously consider a digital label printing investment.”
The L-4733AW also supports a range of substrates, including off-the-shelf flexo materials, without the need to surface prime. Its inks meet the latest safety standards and regulations, such as REACH, and deliver high-quality images, making it a versatile press for converters focusing on food and beverage and health and beauty Footprintlabels.Printing, based in Mandurah in Western Australia, took to PacPrint to purchase a new Epson SurePress L-4533AW digital label printer.
A solution for each and every label printing application “If your company requires a highly productive digital label press with features including a jumbo unwinder, automatic visual inspection system and inline finishing with fully integrated die cutting, UV varnish, lamination and slitting. Epson has a solution for your needs,” Bealby said.
Epson’s new presses attract attention at PacPrint
The recent PacPrint tradeshow was the best one for Epson yet, with the company seeing an overwhelming number of enquiries and interest for its SurePress label solutions
COVER STORY
Footprint Printing took to the recent PacPrint tradeshow to purchase a new Epson SurePress L-4533AW digital label printer
The SurePress L-4733AW builds on the success of its predecessor, the L-4533AW, to offer advanced automation and unattended printing features, higher productivity with improved print speed on film and support for printing on a wider range of substrates.
This new addition to the SurePress line offers higher levels of print quality, consistency, flexibility and value for label converters, specialty printers and vertical manufacturers.
Australia and New Zealand have also been keen early adopters of this innovative inkjet technology with over 17 installations to date and climbing. Epson continues to invest in the label printing sector globally including R&D into MIS integration, colour management software, application specific ink technology and future press platform designs to address the on-demand label market.
Additionally, an optional inline spectrometer is Thisavailable.solution was created as label converters and specialty printers are looking for solutions that are simple and cost-effective to operate and maintain, and can deliver on stable, predictable production.
Epson enhanced its industrial SurePress line-up by adding new capabilities to the L-4733AW which can help businesses save on upfront costs and maintenance. These advancements come without the compromise of simple operation and maintenance, production or print quality.
The company, thus far, has been a lithographic printer offering design, full colour printing and digital printing but will soon expand its offerings into the labels space once the machine has been installed at its premises.
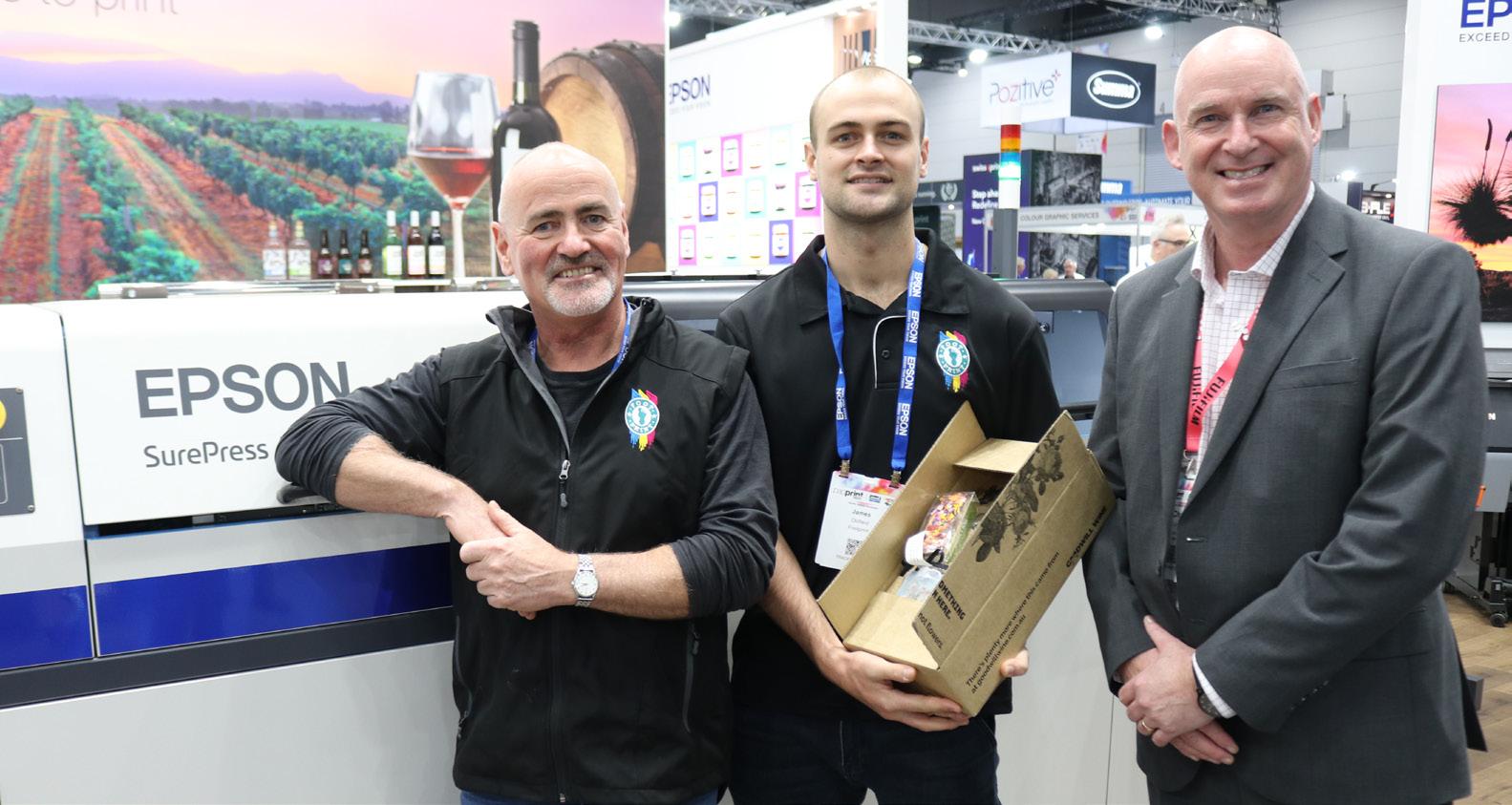
• Jumbo unwinder – By minimising operator intervention, the GM LUW500 maximises productivity. The unwind module is fully synchronised to the press with stepless electronic tension setting, roll pick up from the floor and an easyto-use graphic touch screen.
As for the SurePress L-6534VW, it is Epson’s latest UV inkjet digital label press which is now able to run in-line with a GM LUW500 jumbo roll unwinder, an AVT or BST inspection station, and a GM DC330 finishing line.
Footprint owners and father-son duo Patrick Oldfield and James Oldfield made the purchase through Epson distributor Fujifilm Business Innovation Australia.
in here COVER STORY
The SurePress L-4733AW is a water-based resin ink digital label press
The SurePress L-4533AW digital label press incorporates Epson’s MicroPiezo inkjet printhead and uses industrial grade Epson SurePress AQ ink. It is designed for converters who wish to produce general purpose and specialised labels in short and ultra-short print runs on paper and film stocks. It produces output on coated and uncoated substrates with a high colour gamut, high colour accuracy, and outstanding print resolution and Fujifilmprecision.Business Innovation Australia senior product specialist Darren Yeates said its output is compatible with a wide range of industry standard finishing equipment for a low set-up cost with maximum production flexibility.
New in-line connection options available for the SurePress L-6534VW include:
A one-of-a-kind UV solution designed for optimal performance
This new capability is targeted at label converters looking to improve operational efficiency for longer print runs, while maintaining the versatility needed for shorter print jobs.
“Footprint needed to diversify its offerings as opportunities presented itself. And that’s exactly the reason for our partnership with Epson – that their existing customer base can diversify into labels,” Yeates said.
“We have been doing a lot of sheetfed label work for short-runs. Our client is getting bigger and doesn’t want to be hand labelling. So, we’re going to be doing a lot of it on the Epson SurePress L-4533AW printer,” Patrick added.
To enable this, Epson recently extended its partnership with GM, providing an integrated, productive and streamlined label printing and finishing solution to meet high volume label production demands.
The SureColor V7000 is a flatbed printer that delivers flexible production with outstanding image quality and a reduced running cost
“There is a low barrier to entry in terms of skillset with the machine and as general commercial printers, Footprint can easily transition and diversify into labels. We’re hoping to schedule the install in the next month or so and are excited to see what they can do with the machine.”
• Inspection system – Available from AVT or BST, inspection systems provide
“We do a lot of digital work and offset lithographic. We saw an opportunity to diversify into labels as we’re very close to the Margaret River Winery region and want to create solutions in-house for Caption to go
The SurePress L-6534VW is Epson’s latest UV inkjet digital label press
our customer, Margaret River Wines,” James Footprintsaid.has thus far been outsourcing most of its labels work.
Footprint has been a Fujifilm customer for cut sheet innovation and an Epson customer for wide format, but this is the first customer for both companies through their distributorship deal.
“The lithographic side of our business is getting smaller and smaller too, so we will be filling up that gap with more labels work. This machine will support us because the quality that it produces is great and it’s easy to operate. It’s everything we need.”
www.propack.pro August 2022 ProPack.pro 13
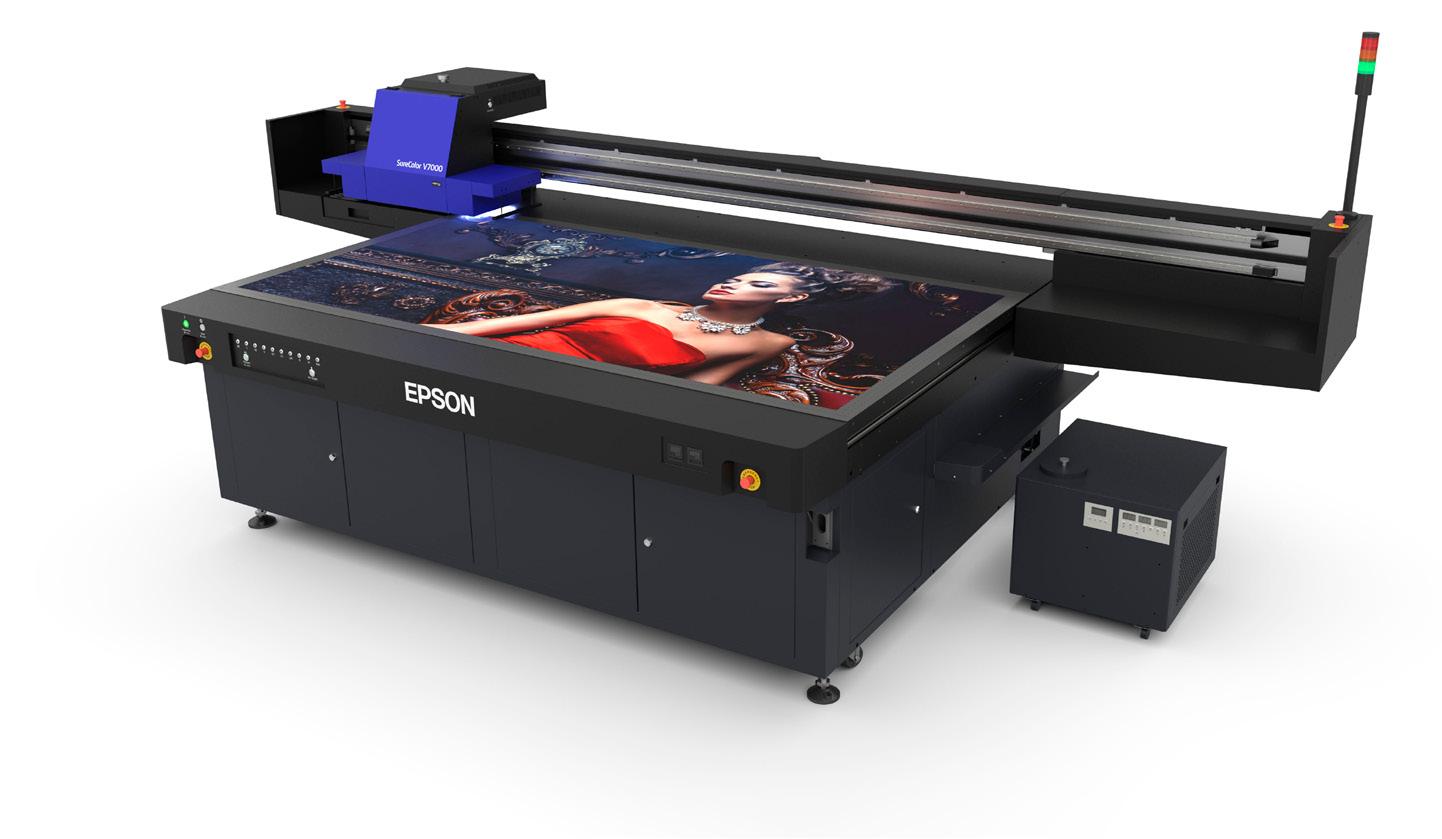
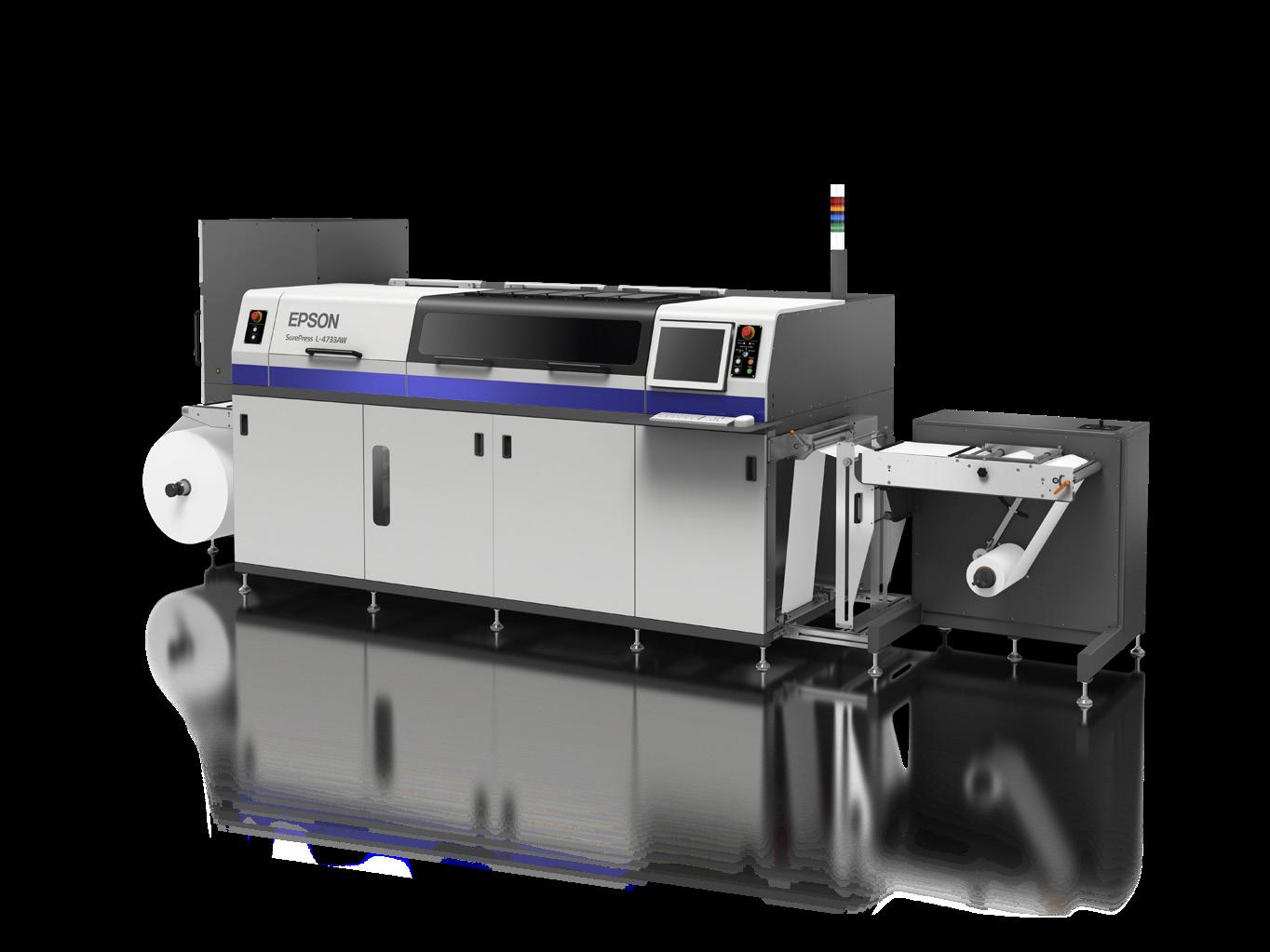
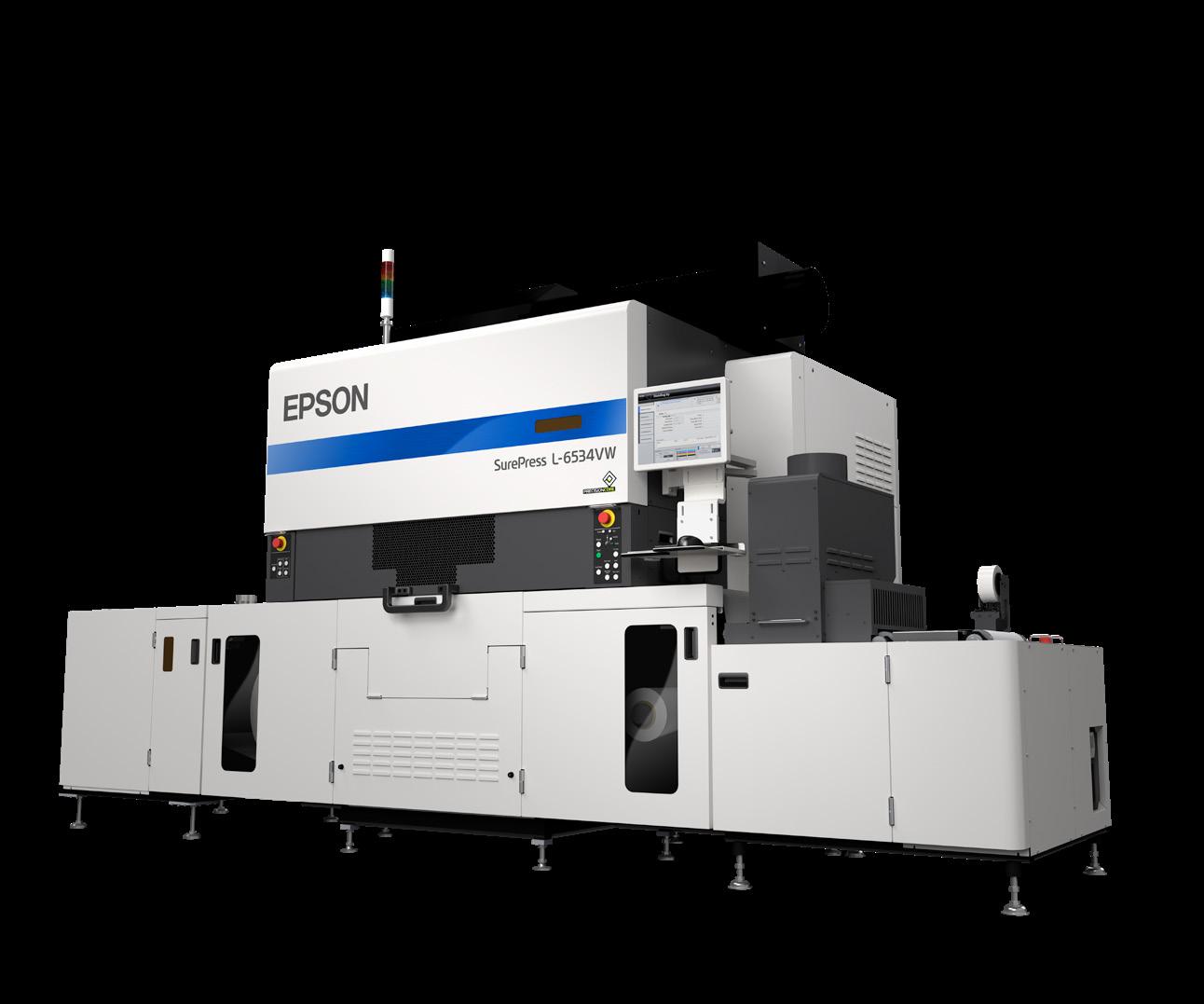
“The result of over 10 years’ collaboration with GM, these innovative and proven connection options for our SurePress UV inkjet digital presses will provide an even more productive solution for streamlined, end-to-end, high volume label production.
“Golden Signs’ volume of printing was over a thousand square metres in a fortnight since using the SureColor V7000. We were pleasantly surprised to see just how much they were putting through it.”
“Our old printer couldn’t keep up with our growth. We started having issues with our printer, and not the best support for it. We needed a printer that could keep up with our growth and our demand. We didn’t look anywhere else except Epson as it is a world-class company with leading print technology, and it is reliable.
Golden Signs Australia, a Western Sydney based custom sign specialist involved in the design and manufacture of signage, was one of the most recent companies in the A/NZ region to install an Epson SureColor V7000 UV flatbed printer. It has seen massive improvements in its efficiencies since installing the machine.
Epson Australia also directly sells and services its label press solutions – this means online remote diagnostics, real-time customer management systems and a national onsite service program are backed by a highly efficient service team.
Epson Australia marketing communications manager Nathan Fulcher said when Golden Signs needed to upgrade its printer to a fast, affordable, and reliable solution that can keep up with the business’ growth, it turned to the SureColor V7000.
A SureColor like no other Epson Australia also displayed its first-ever flatbed printer, the SureColor V7000, at PacPrint – a press that delivers flexible production with outstanding image quality and a reduced running cost.
www.propack.pro14 ProPack.pro August 2022
“Partnering with Epson puts us at the forefront of technology in our space. With that sort of technology, it will ensure that we carry on into the future for another 40 years and hand on our business to future generations.”
It prints on a wide range of substrates including paper, film, Coreflute, vinyl, canvas, aluminium and acrylic, and produces image quality to suit the most exacting applications including signage, POS/POP, premium packaging, décor, custom cabinetry and fine art.
The SurePress L-6534VW digital inkjet label press aims to provide high productivity and outstanding finish at print speeds up to 50m/min. Its key features include: built-in reliability and stability functions, UV LED pinning between colours, Nozzle Verification Technology, support for a wide range of paper and film label substrates between 80 and 320 microns in thickness, with a printable width of 330mm, standard configuration including corona treater, web cleaner, white ink, digital varnish, and an additional UV curing unit, in addition to other features.
• In-line finisher – The GM DC330 finisher is capable of high-speed production. It can be operated as a fully integrated in-line converter or off-line for flexible finishing options.
The printer incorporates eight Epson MicroPiezo printheads. Each head features 1,440 microfine nozzles with variable size dots as small as four picolitres. Working in conjunction with a new 10 colour Ultrachrome UV ink set, it will produce images with a very wide gamut and fine gradation. White and varnish can even be applied as spot colours for enhanced detail and finish.
“The V7000 is perfect for the work that they do. It fits into a very niche space where customers require high quality, wide gamut print with options such as varnish, white, and additional colours such as red and grey. It allows us to provide a full gamut print at quality, with speed,” he said.
COVER STORY
It’s an exciting development that we are confident will open even greater possibilities for our customers,” Bealby said.
“Golden Signs was established in 1980 by my parents. The business has flourished under their watch. My brother Brad and I have taken on the reins and taken the business to new heights. Our business now consists of serving the retail industry and we’ve been in the business of UV flatbed printing for about five years now,” he said.
Epson Australia’s Nathan Fulcher and Ryan Warby The SureSpectro AS-4000 inline spectrometer delivers on real-time measurementsautomated additional support for process control and quality assurance where necessary, to meet specific production demands.
The SurePress L-6534VW also comes with optional digital varnish for high valueadded tactile effects or orange ink for expanded colour gamut to achieve 91 per cent of the Pantone range. Additional options also include automated workflow options and highly productive inline unwinding, inspection system and finishing options.
The SC-V7000 offers a 1.25m by 2.5m print area that supports media up to 80mm thick and 50kg/m2. It features a vacuum system with four independently adjustable zones for flexible operation. Integrated layout pins and a height sensor on the head carriage enable easy media setting while an ioniser ensures reliable and consistent output. The print heads are mounted in a staggered array that enables up to three layers to be applied in a single pass (white + colour + varnish).
Golden Signs owner Danny Awad said the company didn’t set its sights far from Epson when selecting a printer.
It is also supplied complete with Epson Edge Print RIP software and Flatbed Controller software. It can be managed from the desktop using Epson Edge Dashboard and supports Epson’s new Cloud Solution PORT service.

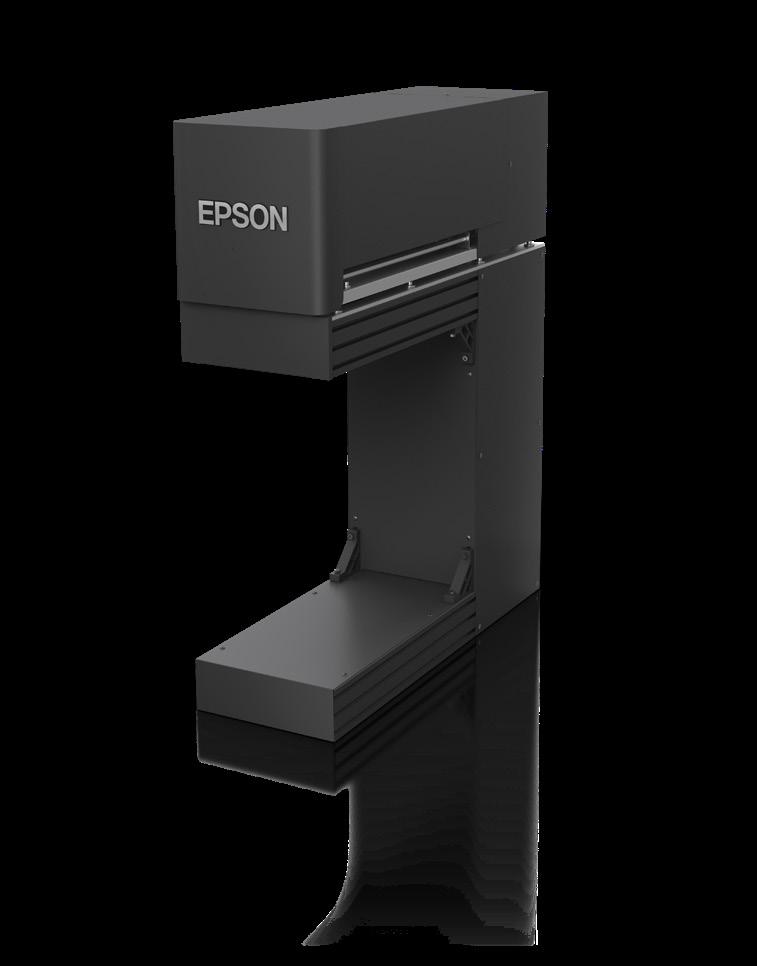
Expand your service offering with high quality short-run digital labels of exceptional quality and improve your bottom line. SurePress is easy to operate, offering consistent colour reproduction and precise colour matching. • Extra wide colour gamut including Orange, Green & Opaque white inks • Improved turn-around times • Proven Epson technology • Non-contact Epson micro-piezo printhead array delivers high quality results even on textured and uncoated materials THE NEW SUREPRESS DIGITAL LABEL PRESS Versatile ConsistentPrinting.Quality. Learn more, visit www.epson.com.au/surepress • Extra wide colour gamut including Orange, Green & Opaque white inks SurePressMODELNEWL-4733AW *Product shown includes Epson SureSpectro AS-4000 option
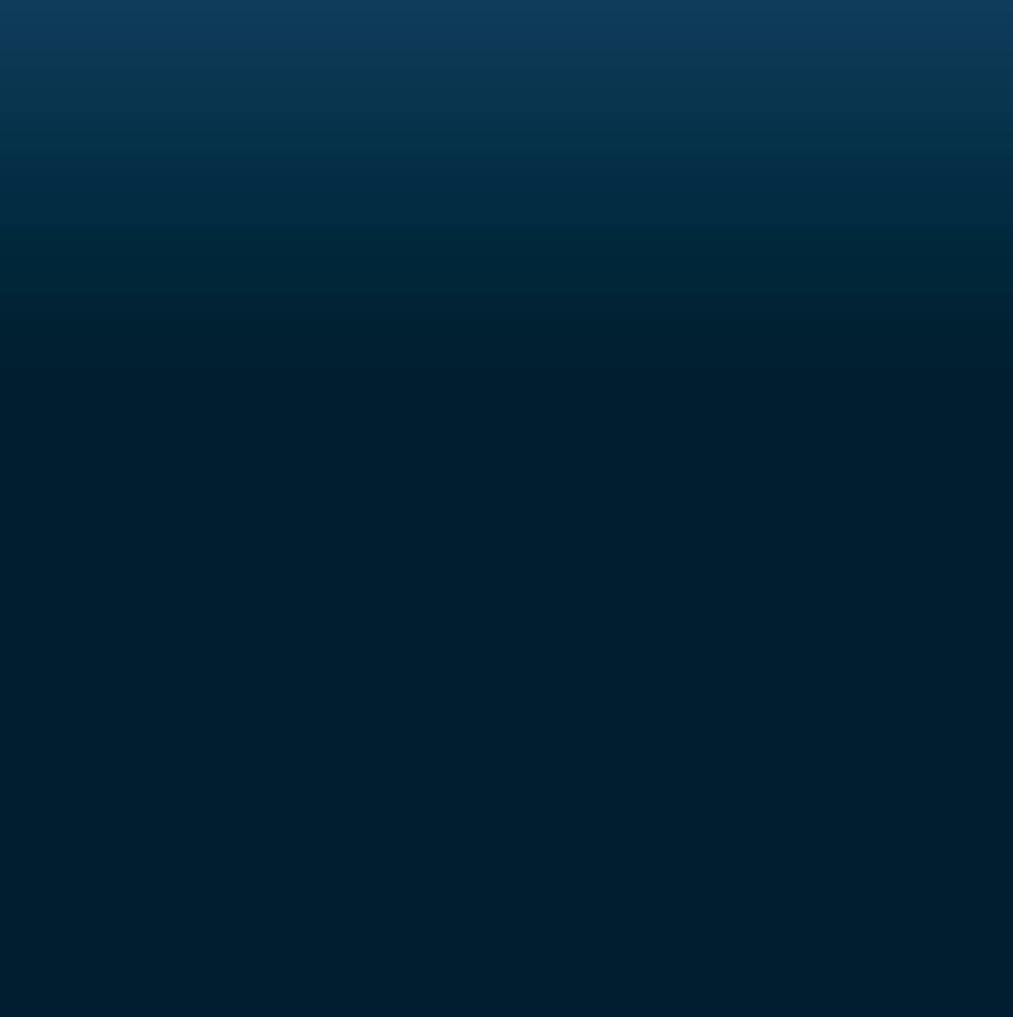
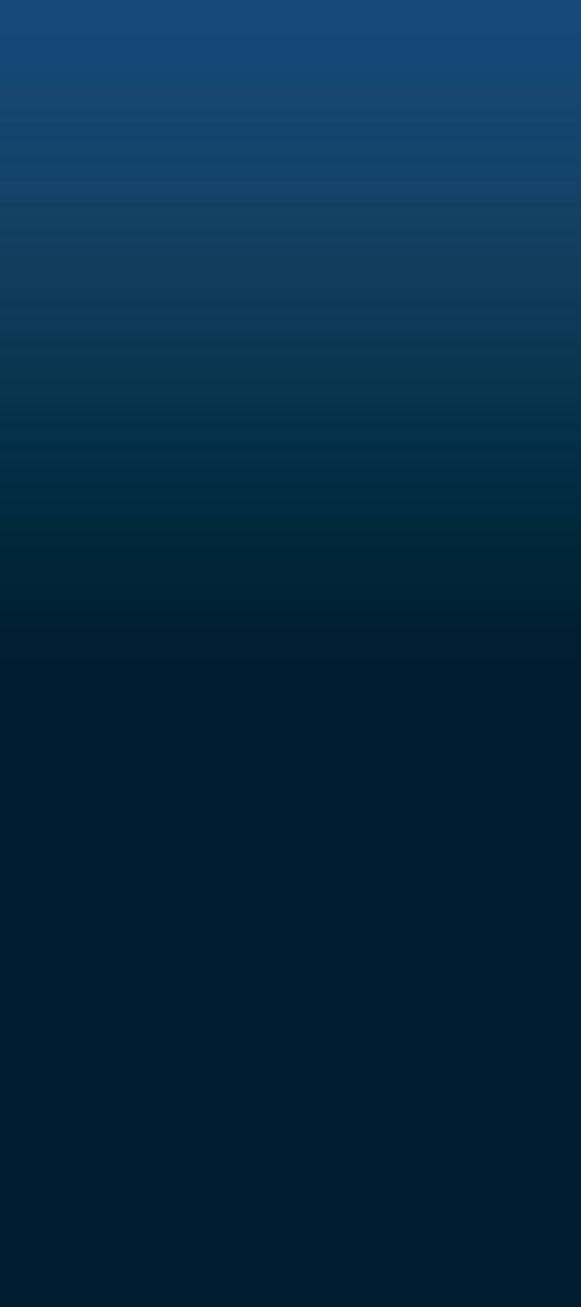

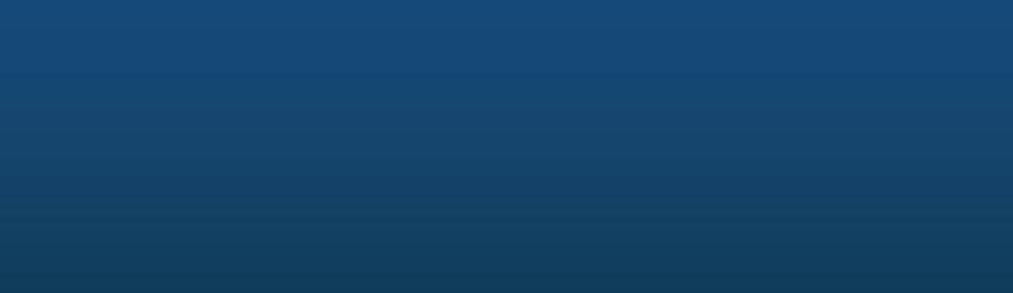
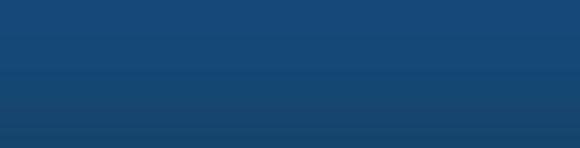

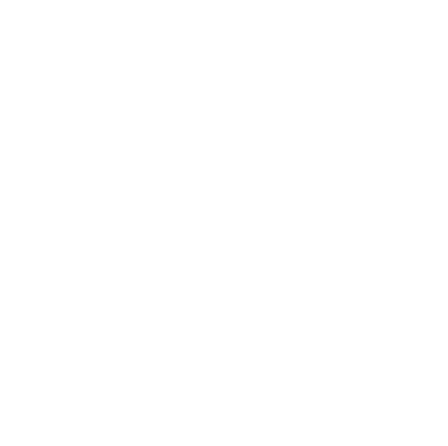
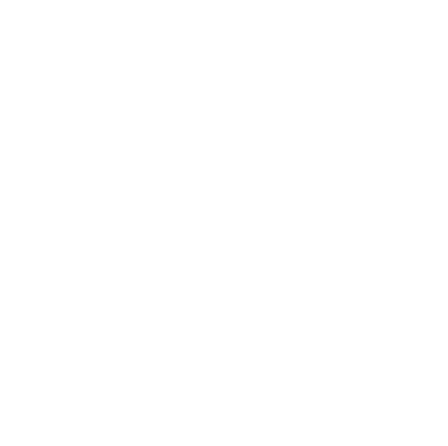
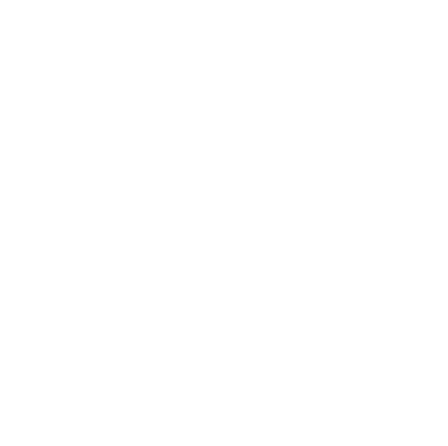
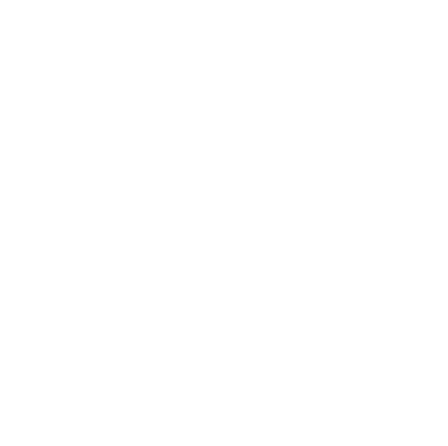
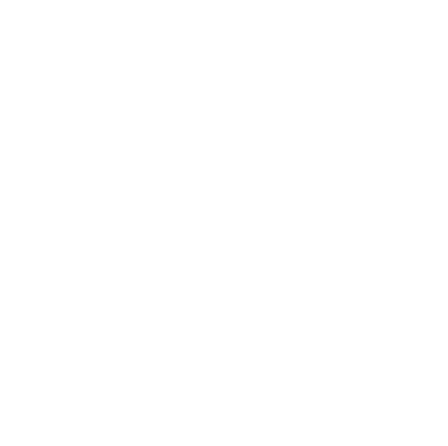

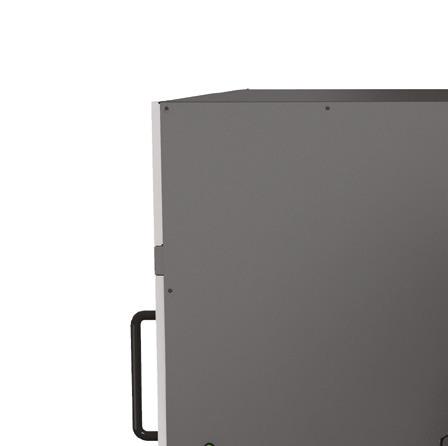
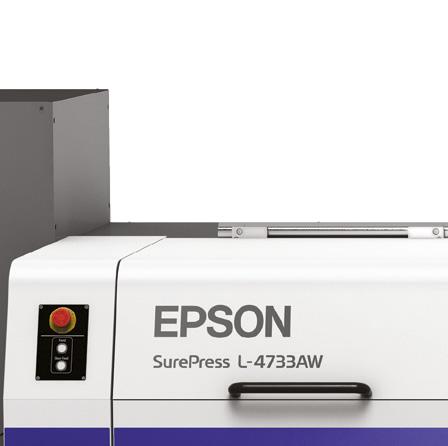


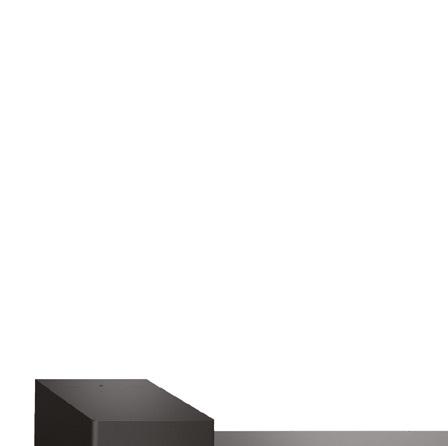
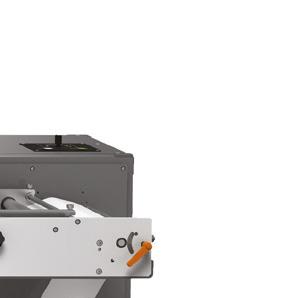

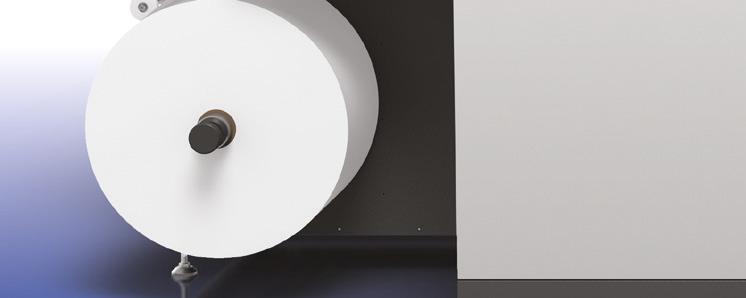

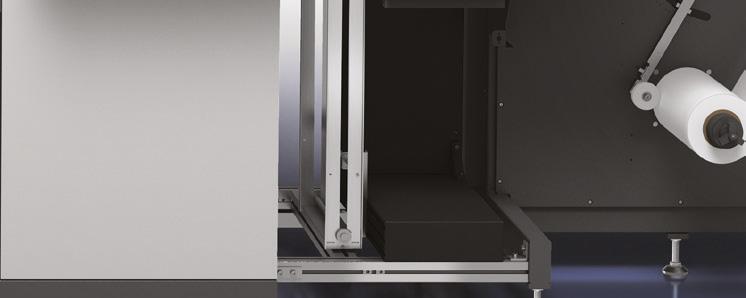
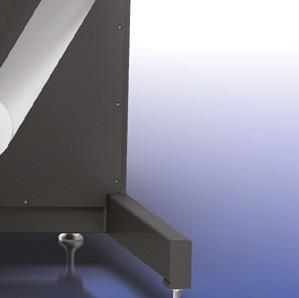
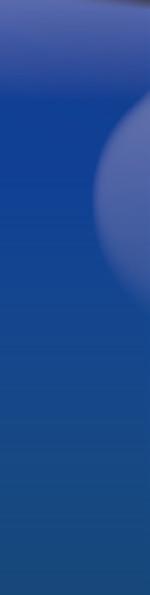

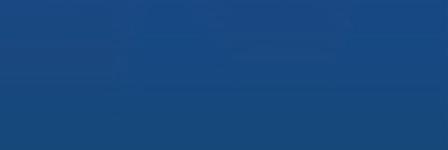
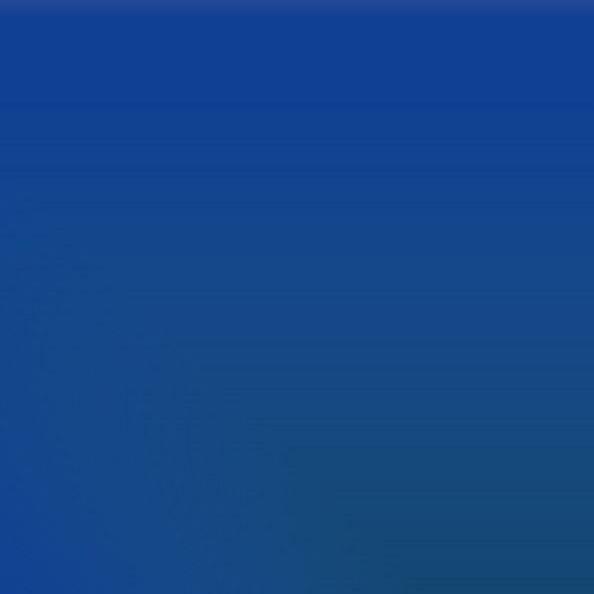
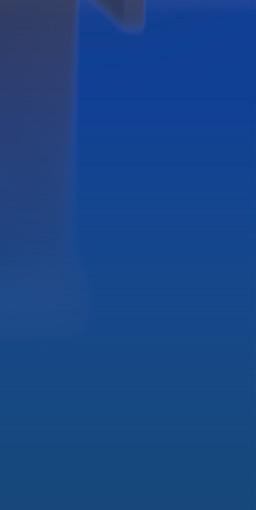
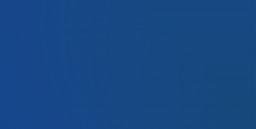
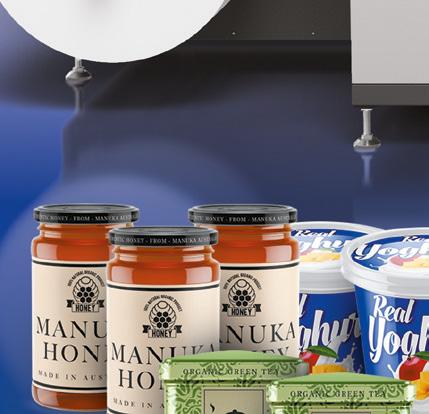
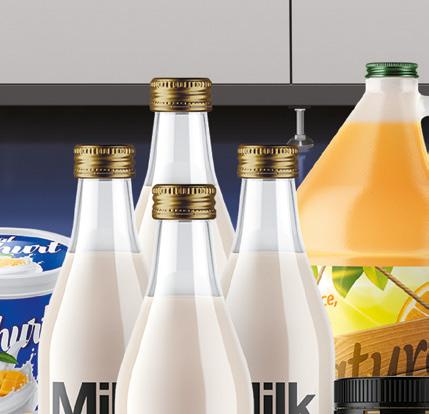
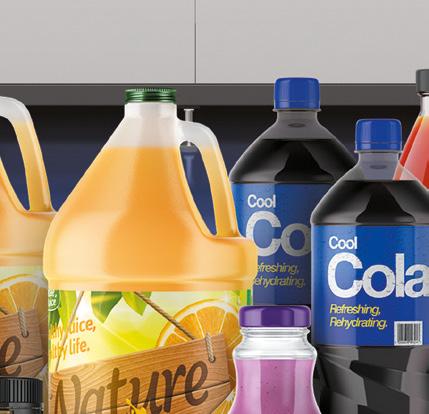
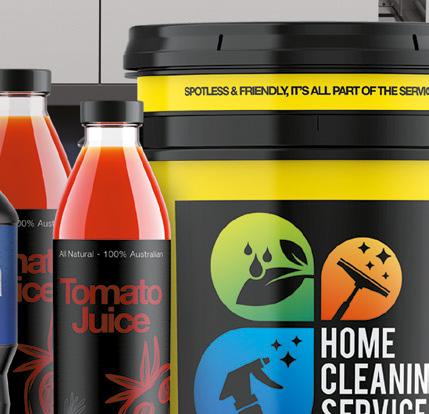
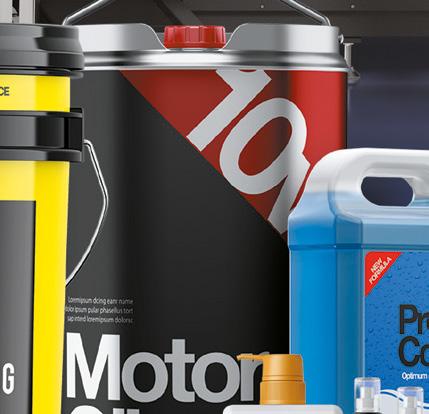
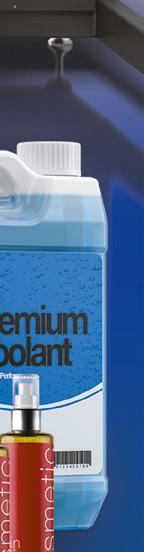
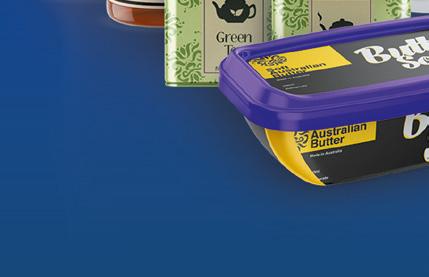
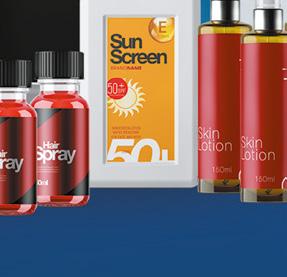
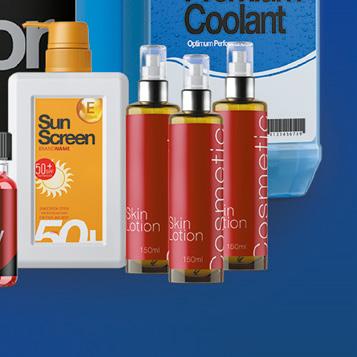

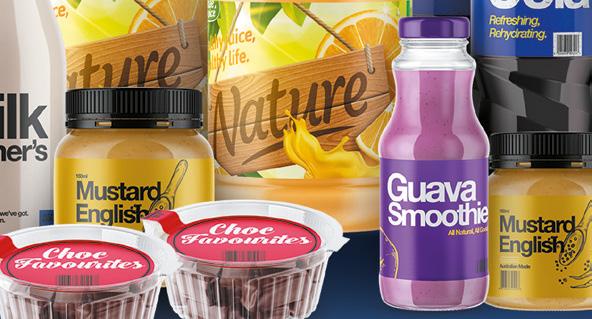
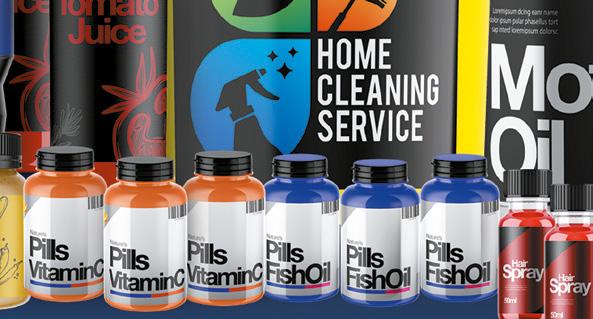
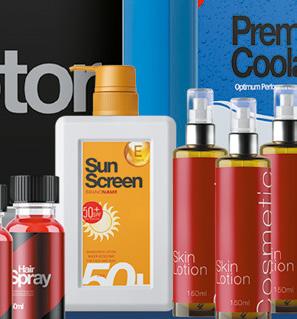

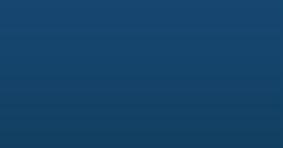
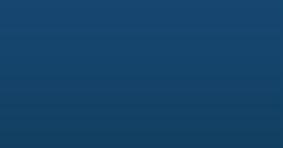

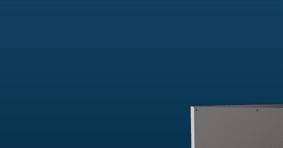

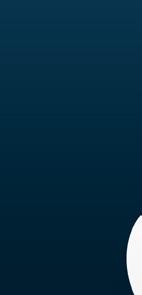
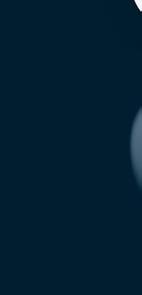
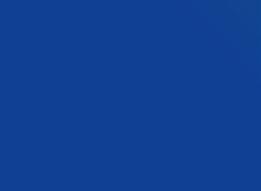
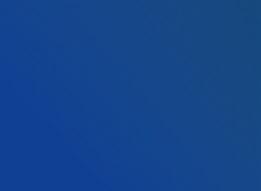



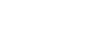


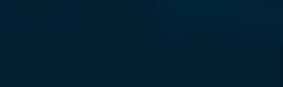


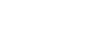
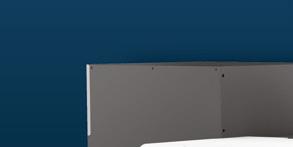
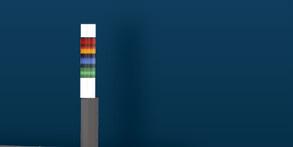
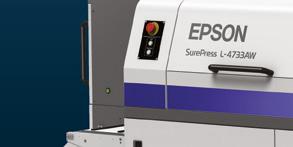
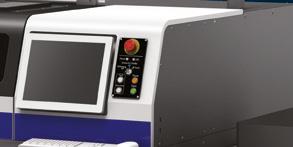

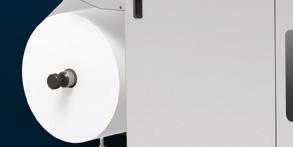
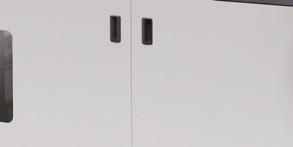
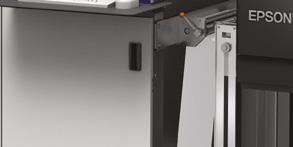
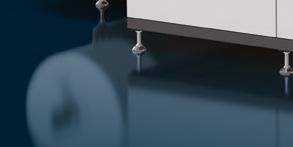
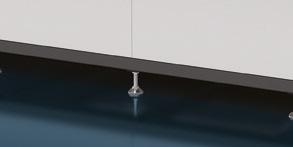
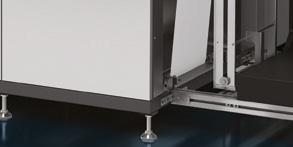
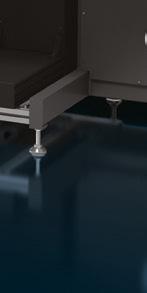
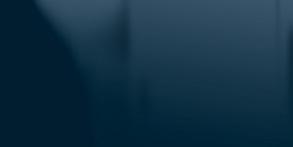
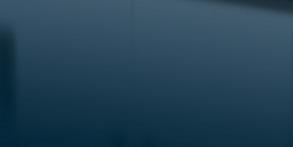
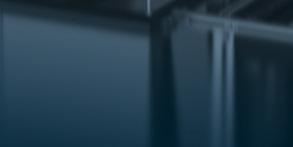
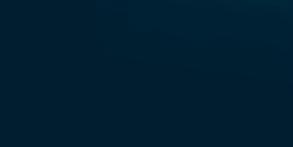
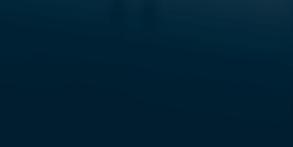
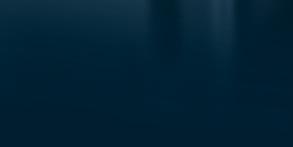

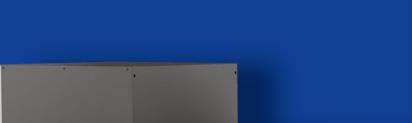
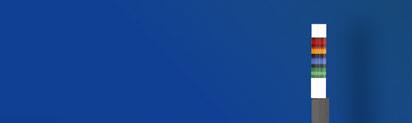
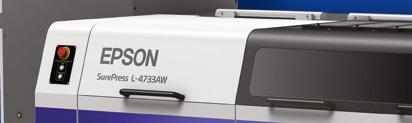
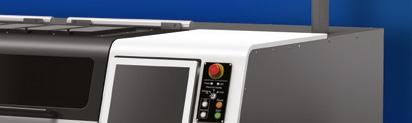
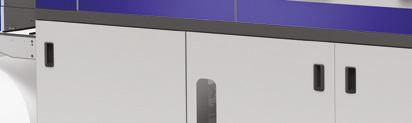

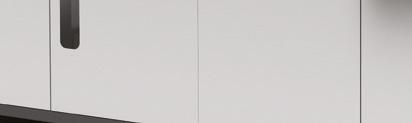

“This is the first major project where we have worked closely with Aarque. We already knew some of the team there as Aarque supplies us with HP digital ink for our Scitex printer.
“Anything that can be cut from corrugated board, we can run on the Zünd!”
Emma Webb, general manager of the Specialty division within Opal Kiwi Packaging, said, “We offer to our market the ability to provide corrugated product with quick turn around on small runs, and the Zünd helps to provide the cutting equipment for speed to market as tooling is not required. We purchased the Zünd cutting table because of the quality of the machine. It is also important that we have the New Zealand support based in Auckland as we do with the Aarque team.”
Wilton-Jones said, “Modularity means you can expand their use as your business needs dictate. Their full automation saves you time and Opalmoney.”KiwiPackaging has provided packaging products locally for a number of years, however, the name Opal only appeared in the market last year when Orora sold its Australia New Zealand packaging division to NPI from Japan. Opal has three divisions in New Zealand. Webb said, “The packaging industry is in good shape with lots of positives, especially when the New Zealand economy is doing well. As most consumables travel to market in a box of some format, Opal Kiwi Packaging provides this to our customer base.
The company’s New Zealand Specialty Packaging business offers bespoke packaging solutions for small, medium or large businesses. This includes everything from packaging design to manufacturing material and point-of-purchase displays for retailers.
Aarque brings Zünd to New Zealand’s Opal Kiwi Packaging
The Zünd BHS unit can feed multiple sheets at once to make full use of the cutting area. This ensures maximum throughput even with smaller format media.
Up to three different methods can be used for any given job with no need to interrupt production for tool changes.
During loading, the system automatically scans printed QR codes and retrieves corresponding file information.
An off-load conveyor and stacking system deposits cut boards in a stack on the pallet.
It allows you to select processing methods.
Board handling Aarque Group has supplied Zünd cutting tables for a number of years. Steve WiltonJones, national equipment sales consultant at Aarque Group, said, “Zünd cutting tables deliver high productivity and unparalleled quality across numerous applications and their modularity gives you options for your business. Opal chose the Zünd BHS (board handling system), which extends operating time while decreasing operating costs.”
N ew Zealand’s leading supplier of fibre packaging, Opal Kiwi Packaging provides tailored customer solutions through its local manufacturing sites based in Auckland, Hastings and Christchurch. It specialises in manufacturing innovative, purpose-built corrugated fibre cartons and boxes for a range of key New Zealand markets including fresh produce, meat, seafood and poultry, FMCG, wine and beverage, and industrial.
ZÜND INSTALL
“We have found that Aarque has a similar mindset to our business. Like Aarque, we believe that good working relationships and working alongside customers is a key way to do business.”
Depending on the job, this stacking process eliminates the need for bridges to hold cut pieces in place and enables separation of cut parts.
The company has installed a Zünd cutting table with board handling system at one of Opal Kiwi Packaging’s Auckland sites
16 ProPack.pro August 2022 www.propack.pro
Working with a diverse range of customers and market sectors, Opal, requires technology that it can rely on. Webb said, “The Zünd handles everything we throw at it in full production mode, from large cartons to high end displays. Before we installed the Zünd, we had an older machine running this type of work but the Zünd has really added further capacity to our service offering.
Recently, the company installed a Zünd G3 XL L-3200 cutting table with board handling system at one of its Auckland sites. Supplied through Aarque, the Zünd cutting table has numerous innovations the company can use to its advantage.
It processes different material thicknesses up to 110 mm and a stack height of 1.5m enables longer uninterrupted operating time. Operators can remove finished stacks without interrupting the production process.
Board handling made easy: The Zund G3 XL-3200 cutting table with board handling system at Opal Kiwi Packaging
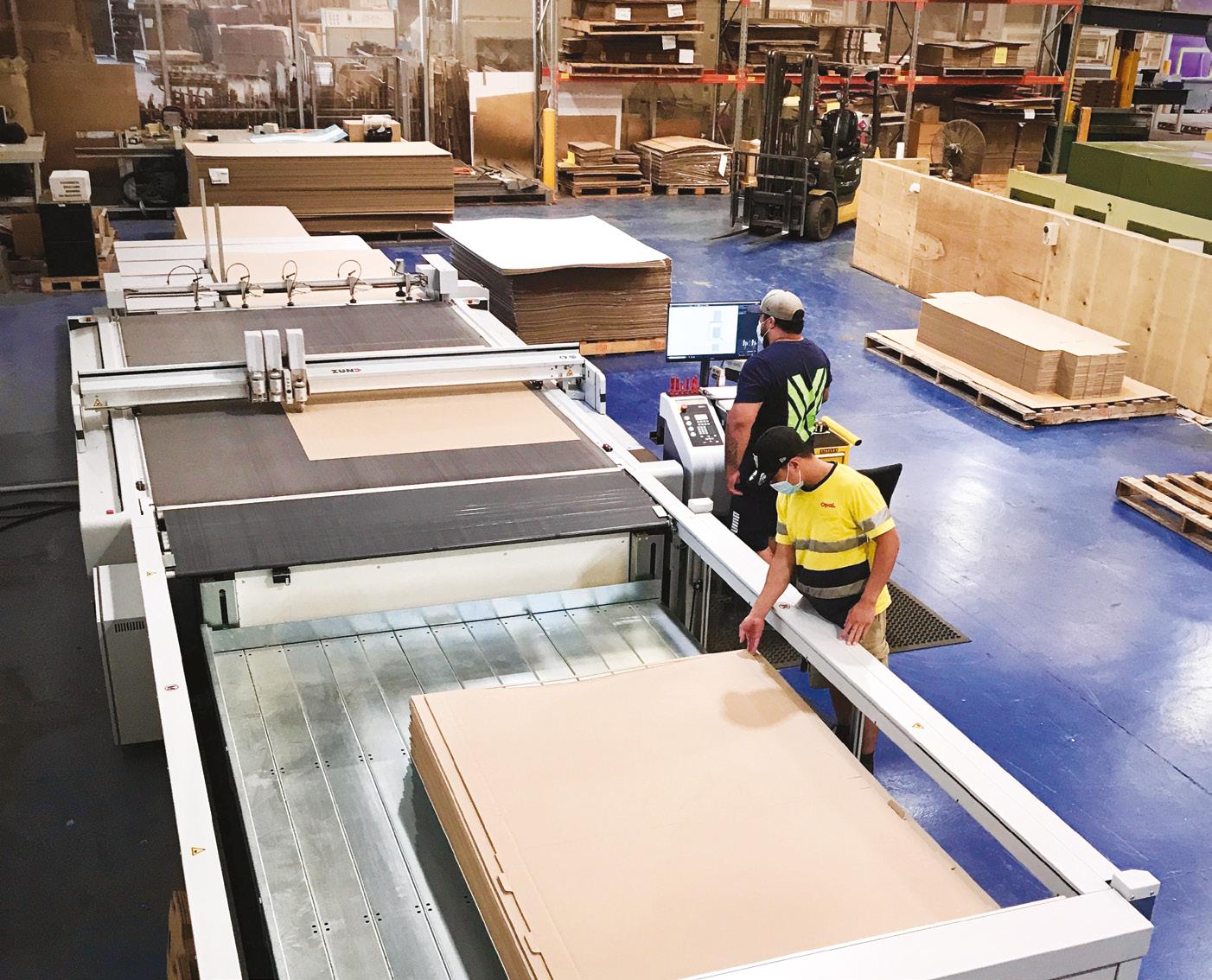
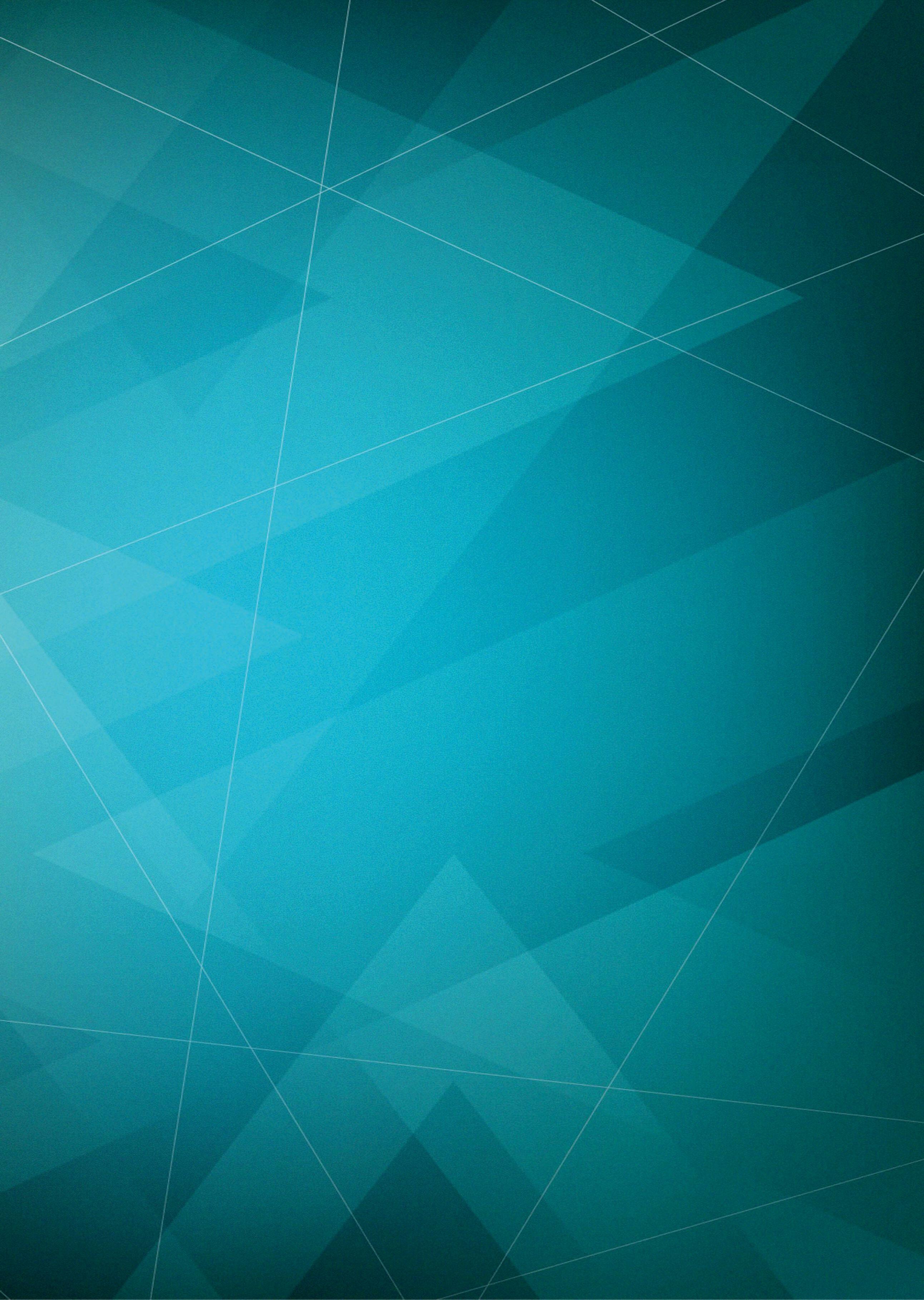
TRADEONLY! INTERESTED NEWPRINTTRADEINPRICESFORYOURZEALANDCUSTOMERS? Register with New Zealand’s largest and most reliable wholesale print company for trade print prices www.wholesaleprint.co.nz
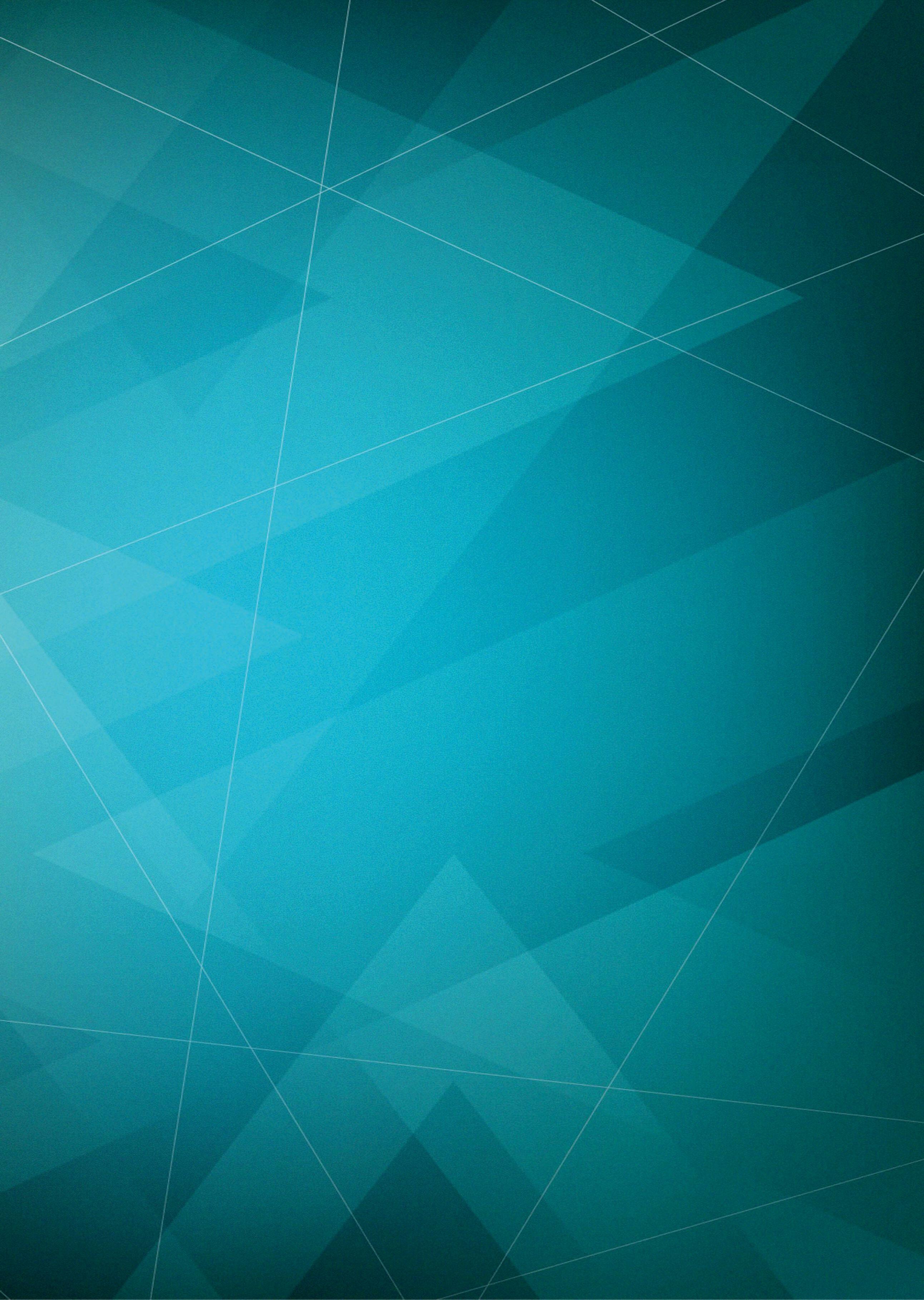
Kissel + Wolf Australia director of business development – Industrial Print and Packaging – Jamie Weller said, “With cost pressures increasing and customers looking for a more agile production environment, the eProductivity Software Solutions we offer are affordable Software-as-a-Service solutions for the print and packaging market.
“Having our partners from ePS positioned just opposite of our booth helped to guide our customers in the right direction too.”
The trend towards short-run packaging also requires a different approach to finishing.
“As digital die cutting using sample tables is well-established in Australia and technology has evolved over the years – allowing them to cut all sorts of material, be much faster, and offer automated loading/unloading of digitally printed boards – allowing digital creasing and cutting of short- to mediumruns is the route to take,” Weller said.
“Customers were impressed by the iECHO digital creasing and cutting solution we are distributing in Australia and New Zealand, PacPrint was also the first show where Kissel + Wolf had a QR code activating an animated 3D model of the Revo 2500W Pro high-speed corrugated board packaging printer, adding AR visualisation to its stand and showing the machine printing at full speed.
K issel + Wolf showcased its range of innovations at the recent PacPrint tradeshow in Melbourne, educating and offering its customers solutions in workflow and efficiency.
In addition, Kornit DTG shared the stand with Kissel + Wolf, showing the true partnership between the two companies. Physical samples from the very latest Atlas Max
KISSEL + WOLF
Kissel + Wolf also took the opportunity to address trends within the print and packaging spaces with its solutions.
Kissel + Wolf prioritises print and packaging at PacPrint
The Kissel + Wolf team at PacPrint
e-commerce and mailer box samples attracted a lot of interest. Many customers also scheduled follow-up demos of our digital corrugated printer in our Melbourne showroom. Also important to note is that customers are asking for water-based pigment ink,” Weller mentioned.
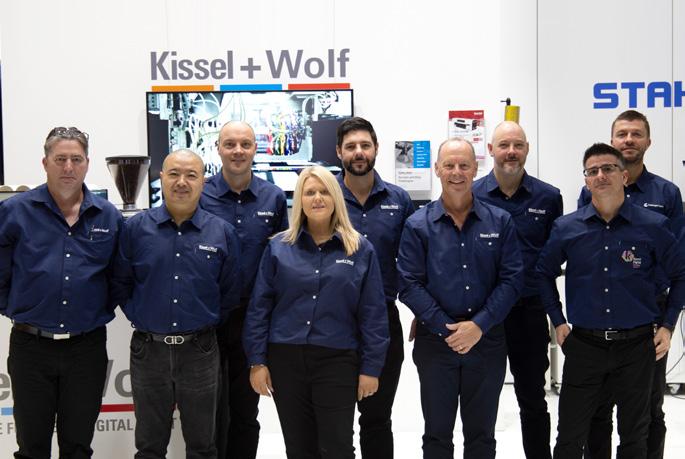
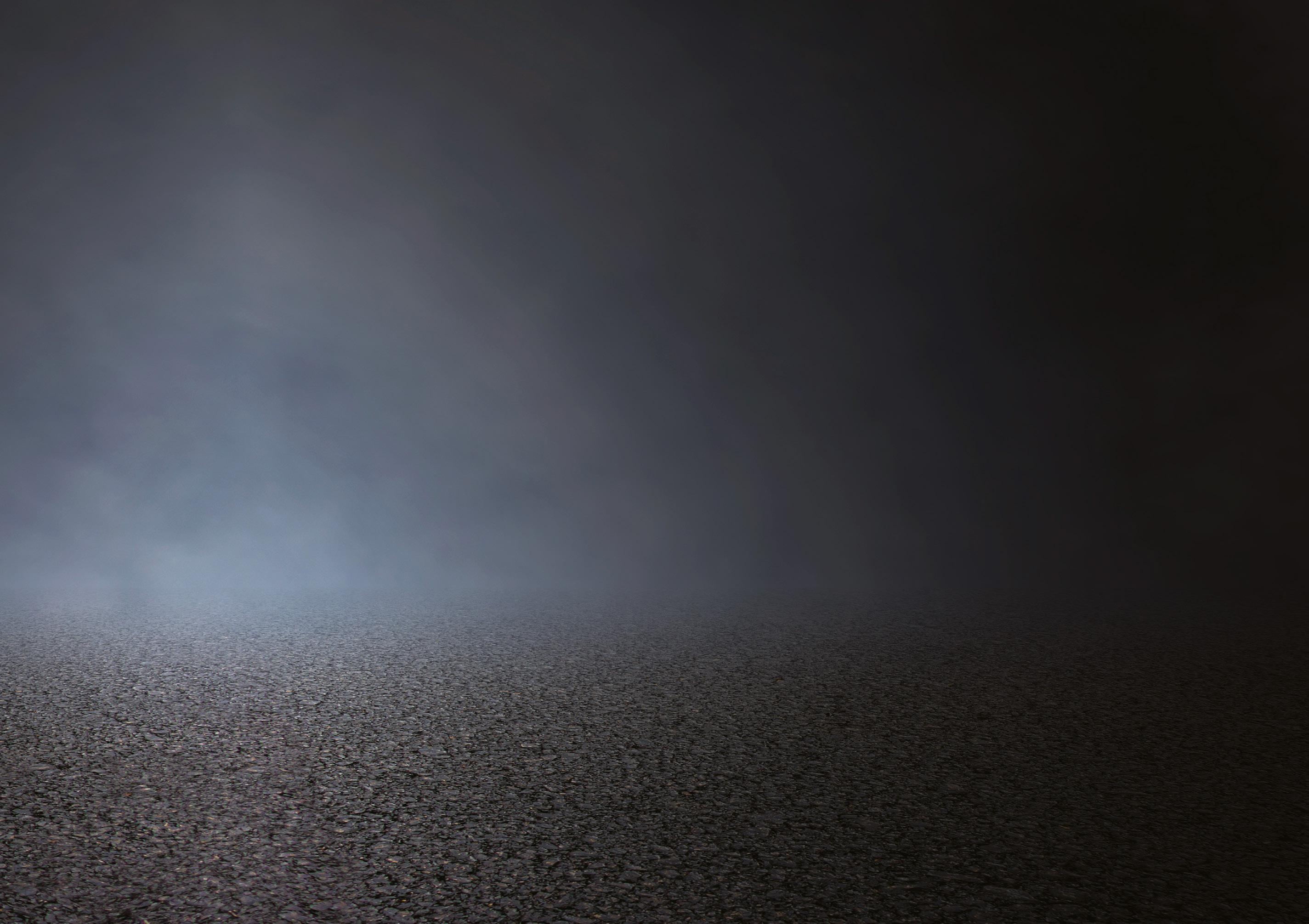
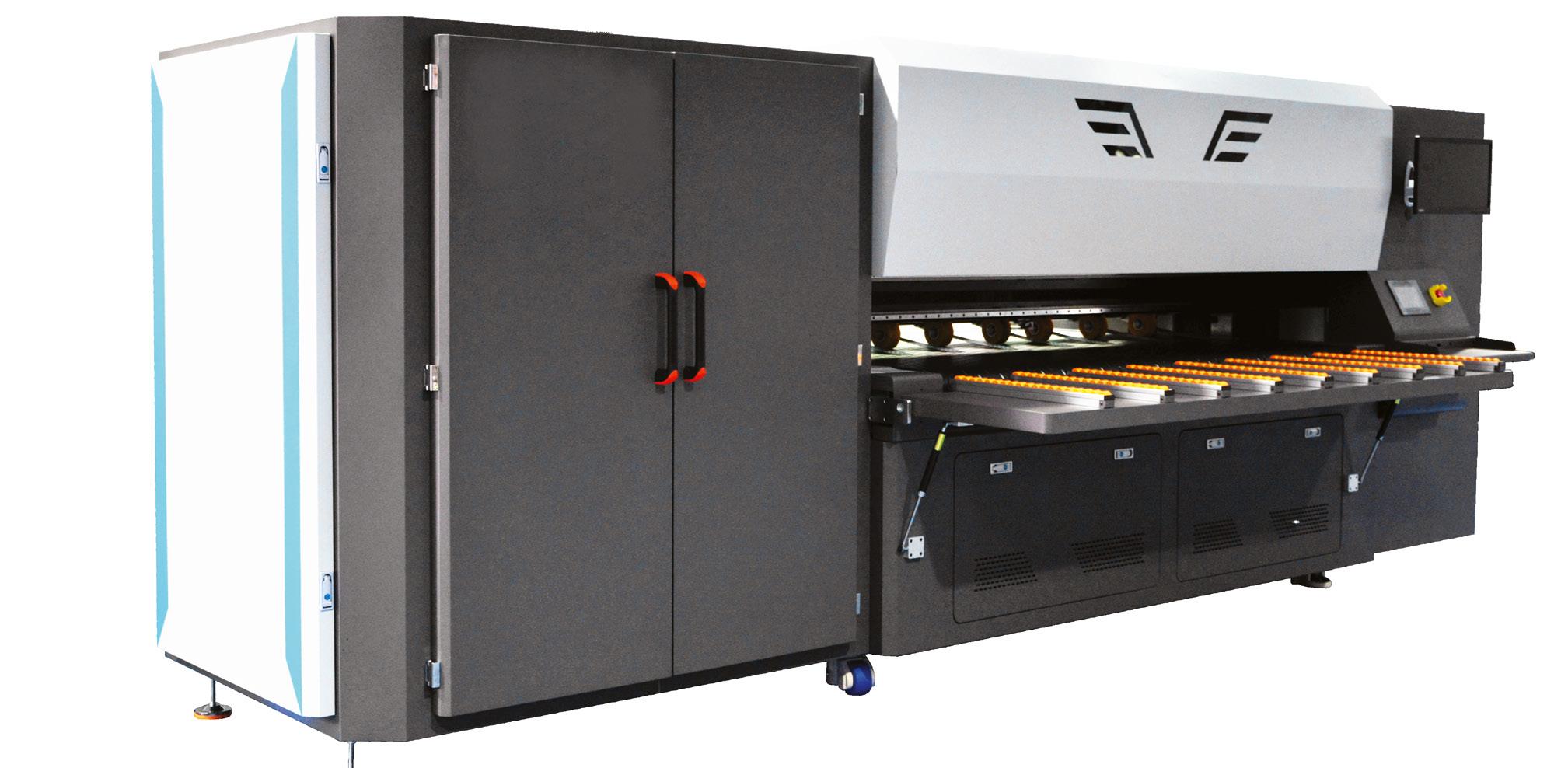
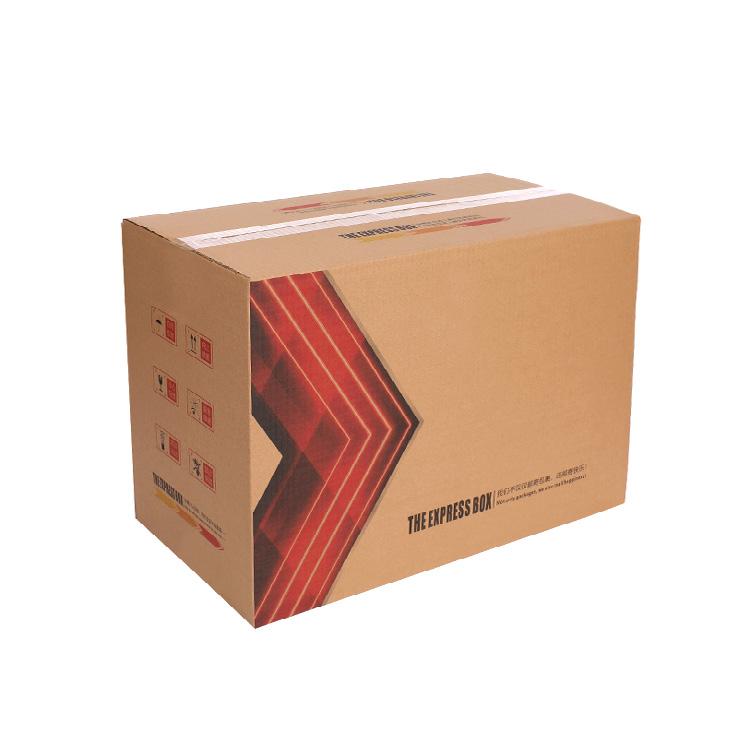
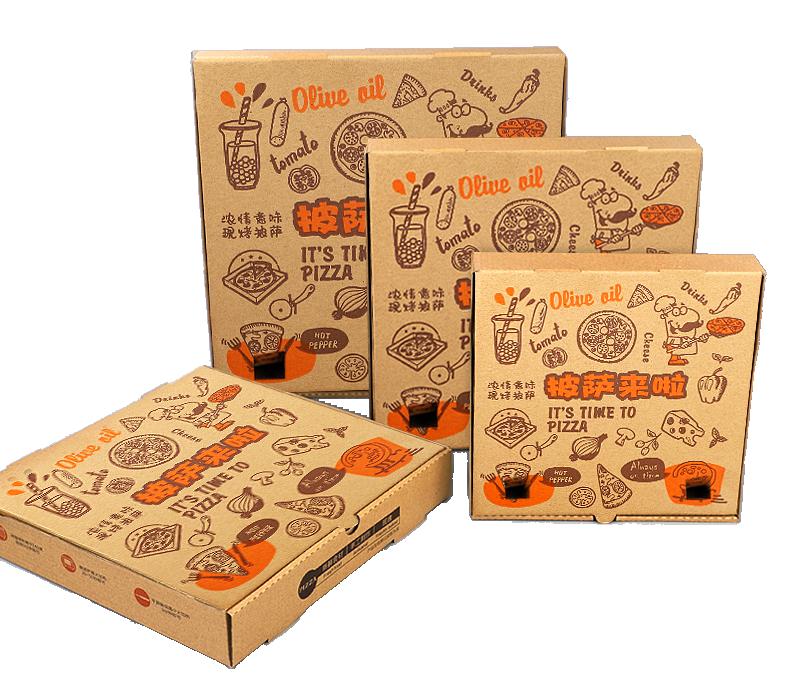
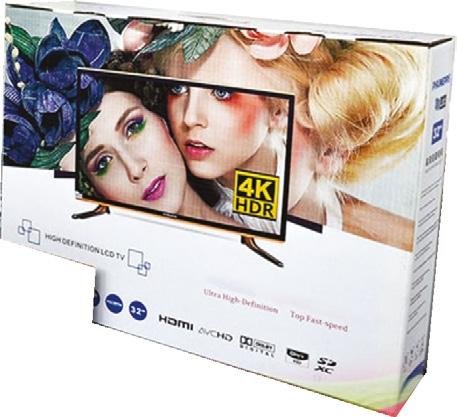
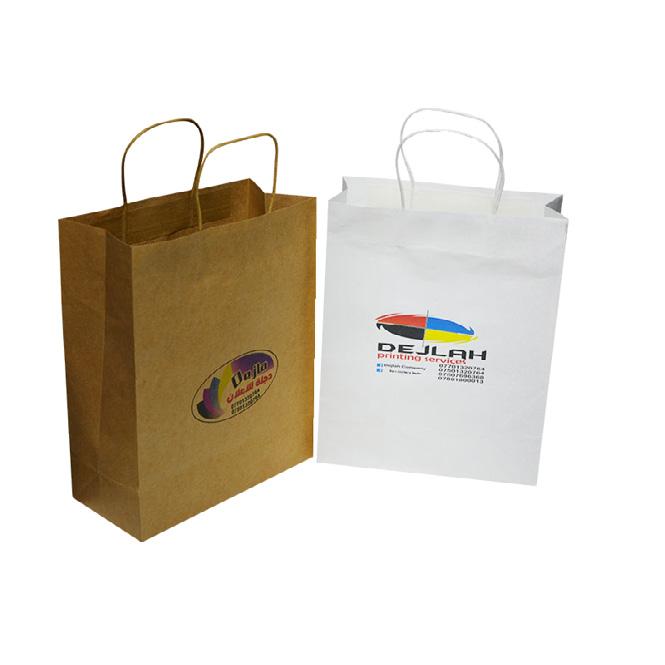
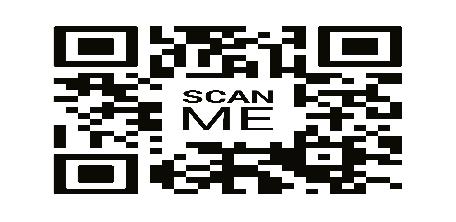
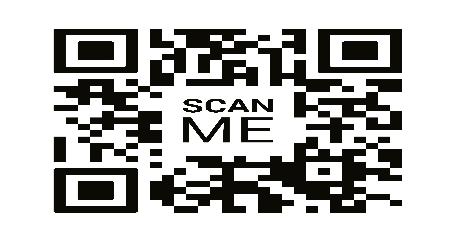
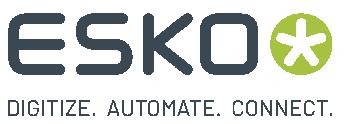
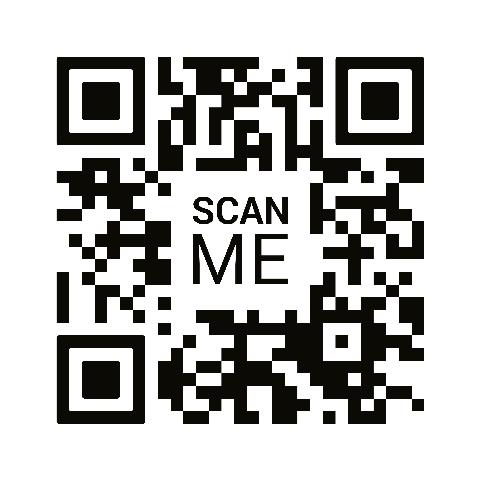
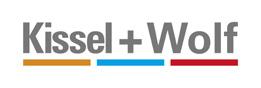
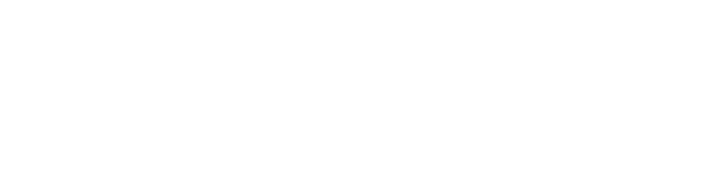
The L350UV is the most flexible and automated label production system in its class. The machine offers 7 vibrant colours, and speeds of 50 mpm and is fully supported by local Jet Technologies and Screen factory-trained engineers.
“Jet Technologies was really pleased with the industry attention our stand received at PacPrint. There was strong interest in our range of printing solutions and services, with the L350 machine sold just days before the exhibition and a number of strong enquiries from PacPrint itself. The volume of business interest we experienced at PacPrint is a good indicator that the sector is returning to health after the disruption of the previous years,” said Jack Malki, Director of Jet Technologies. films remain fully recyclable, ensuring that clients can enjoy the functional benefits of plastic films, whilst ensuring that they work within a sustainable circular Theeconomy.Encore films are presently BOPP based, with PET options on the near horizon. The films look and feel like regular films and run-on various machinery in a normal way, ensuring that clients do not have to make any adjustments at all to existing films. Costs are also comparable to existing films, with a small premium of approximately 15-20% being very well received by brand owners looking for solutions to meet various APCO targets.
et Technologies enjoyed a successful return to PacPrint, attracting strong industry interest in its stand at the recent PacPrint 2022 exhibition in Melbourne. The event saw the company showcase the SCREEN Truepress Jet L350UV, which many attendees remarked was their “top pick” label printing machine at the show.
www.jet-ap.com
The L350 delivers unrivalled colour reproduction as well as superior We heard you. Jet Technologies is helping to advance sustainability in the printing industry through a range of innovative options.
Introducing new film ranges is always a challenge but this is the one area where we have found a constant demand by band-owners for better solutions in order to meet their environmental pledges. These films satisfy those demands in a very honest manner and we see them as quickly replacing traditional films. We also expect the percentage of recycled content to be increased over time as the technology permits it,” said Jack.
JetTechnologies SalesTeam and SCREEN team.
“As a market leader in Australia for various films, Jet Technologies accepts that it is our own responsibility to provide the market with the very best options in order to improve the environment.
Jet encoresustainabilityadvancesJetPacPrintenjoysTechnologiesasuccessful2022Technologiesprintingwithfilms
Encore films J JetTechnologies
for businesses looking to shift away from using plastics and from either PLA (corn starch) or woodbased alternatives in their printing and packaging today, is Encore films available from Jet Technologies.
Encore films are made with 30% recycled content, providing a sorely needed path for recycled plastics to function within the circular economy. At the same time, the scalability, enabling it to meet an even wider variety of market needs.
“Environmental waste and sustainability are top priorities in printing and packaging sectors today, driven by consumer demands that businesses operate in an environmentally responsible manner,” said Jack Malki, Director of Jet ATechnologies.leadingoption
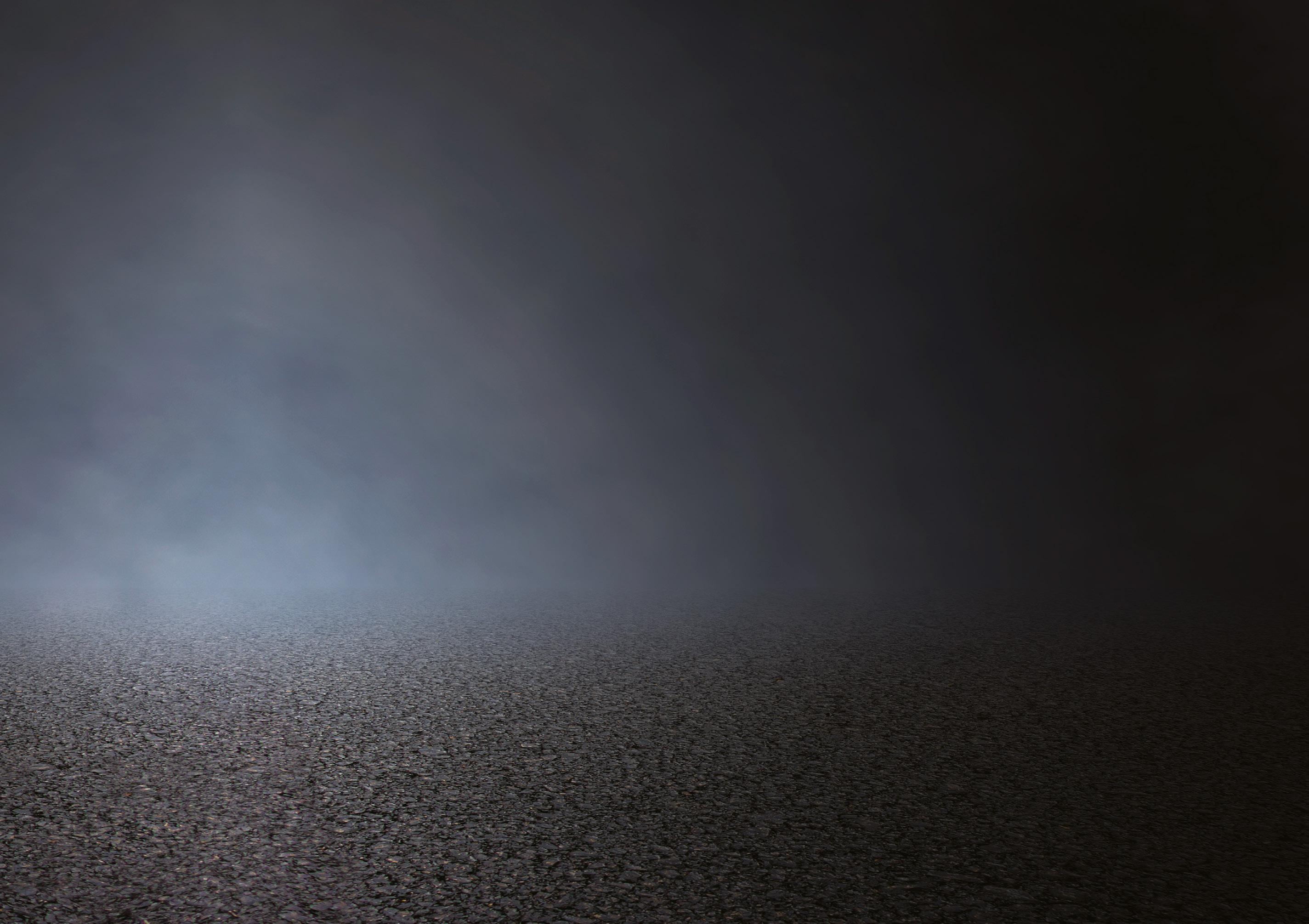

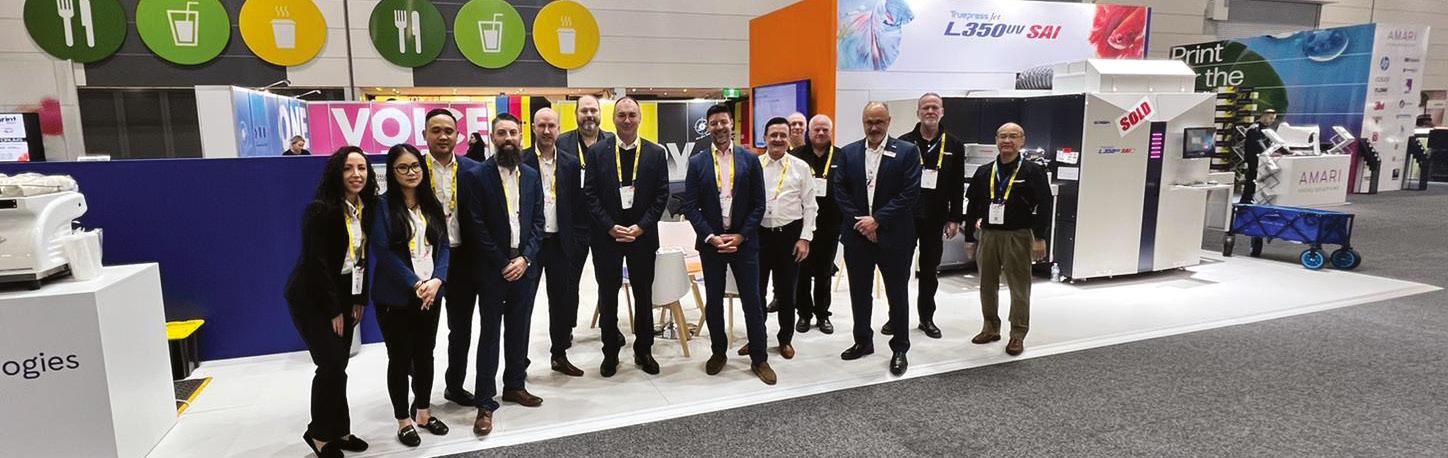
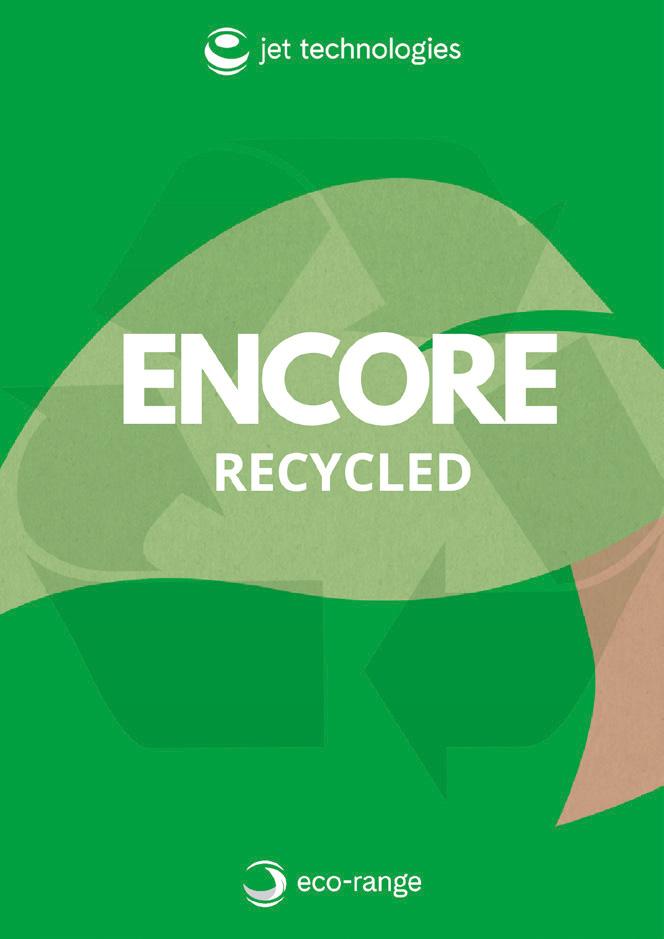
In the exhibition area, there are reserved boxes and machinery from the Innovation Park’s technology partners: Tesa, Simec Group, BST, GEW, Flexowash, Zeller+Gmelin, Simonazzi, Nazdar, Actega Ecoleaf and OMETRossini.marketing and sales director Marco Calcagni said the potential of the Innovation Park is the possibility for printers to use the OMET machines in the showroom to support their production, making not only samples but proper production lots that they are unable to produce at their sites.
OMET said its headquarters represent the beginning of a path of change that aims to increase production capacity and make processes more efficient, indispensable factors for a breakthrough in terms of growth and innovation.
Everything is done with the will of improving not only the purchasing process, but above all the production process, strengthening a relationship of trust between sellers and buyers.
industry players attended the official inauguration, with OMET CEO Antonio Bartesaghi welcoming the guests and presenting the OMET Group’s exponential growth over the last 10 years, culminating in the relocation to the new headquarters in Molteno in 2021 and the realisation of the Innovation Park in 2022.
The KFlex was officially unveiled during the opening of the Innovation Park
There was also a stand by Ribes Tech, the OMET Group’s start-up company that focuses on printed electronics, in particular smart labels, and offers integrated IoT solutions.
www.propack.pro20 ProPack.pro August 2022
OMET PARK
INNOVATION
OMET’s product range is suited to converting and printing labels and flexible packaging with narrow- and medium-web machines. It is now enriched by a new printing line: the KFlex, which was also officially unveiled during the opening of the Innovation Park.
The Innovation Park is located a few steps away from the new OMET headquarters in Molteno
Angeli added that there are many other innovations presented on this line, which is extremely scalable in its offer to meet the different needs of printers.
Attendees also got a tour of the Innovation Park, where OMET also showcased an iFlex and an XJet.
Guests also had the option to visit the new OMET headquarters inaugurated in 2021, to allow further growth to the company’s production reality, which extends over an area of more than 30,000 square metres – of which more than 20,000 are dedicated entirely to the production of label and flexible packaging printing machines.
O MET recently opened the doors to its new Innovation Park demo centre in Molteno, Italy, with a high-profile event and showing off its new KFlex line – a flexo printing machine with an ergonomic and flexible design, capable of being reconfigured at any time by the printer.
The Innovation Park is a 1,500 square metre space that OMET set up with the aim of allowing printers, converters and suppliers to meet and collaborate, to host printing demonstrations and also to do trials of new materials on OMET machines.
OMET sales area manager Andrea Angeli unveiled the new machine at the event, highlighting the machine’s incredible Tailor-madeflexibility.fortheprinter’s needs, it has a design that allows total accessibility and easy maintenance, a new flexo printing unit with a contrasting UV lamp and, a new innovation – the Switch System: the possibility of changing any of the machine’s modules (printing units, pull-out die, digital print-bar, hotfoil and screen printing) in a minute and in an extremely simple way.
OMET inaugurates new demo centre in Molteno, Italy
The Innovation Park is located a few steps away from the new OMET headquarters in MoreMolteno.than150
OMET is distributed in the A/NZ region by Currie Group.
OMET CEO Antonio Bartesaghi welcomed the guests and presented on the group’s growth
The 1,500 square metre showroom in Molteno houses OMET’s new KFlex line, a flexo printing machine capable of being reconfigured at any time by the printer
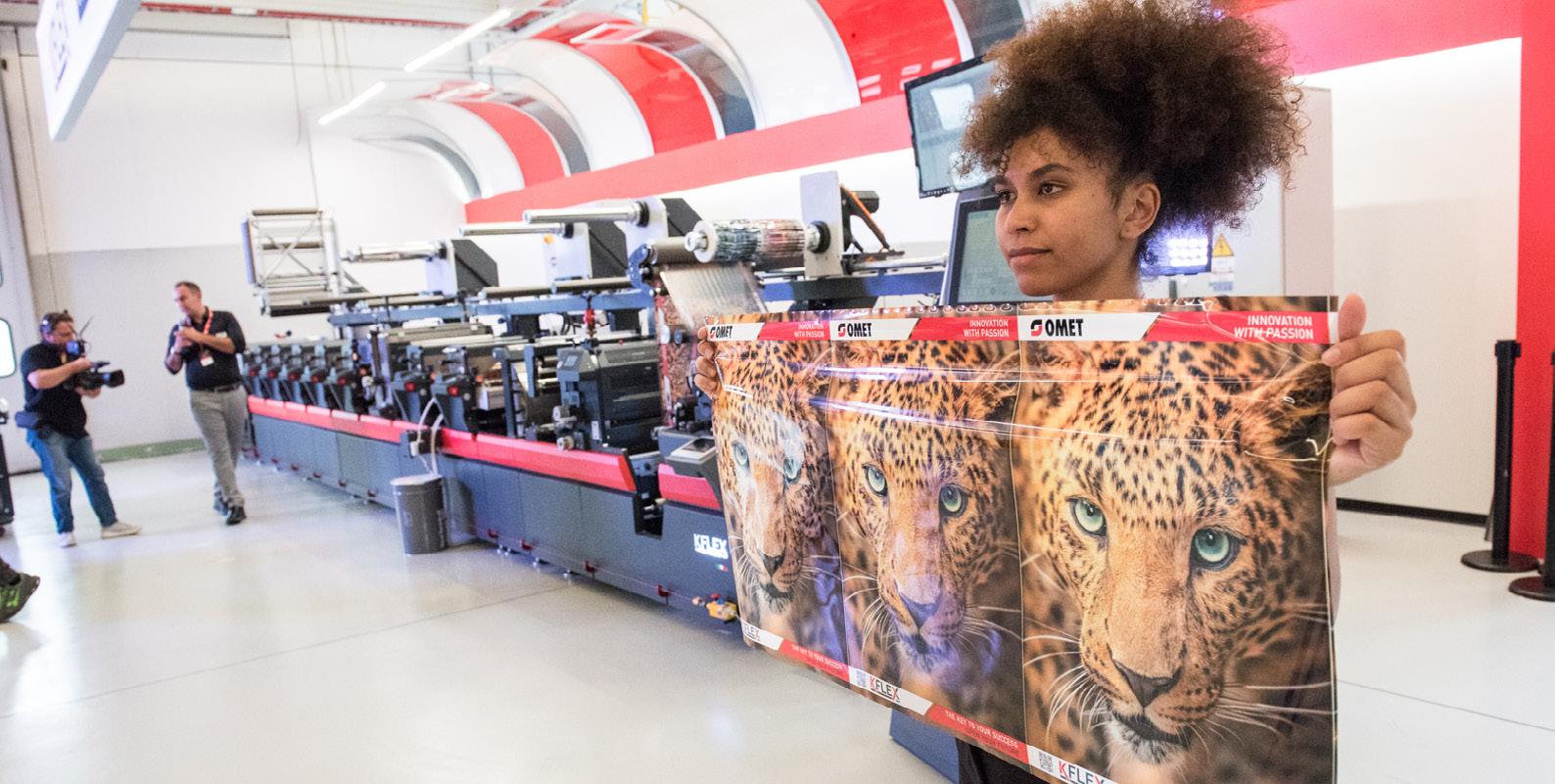
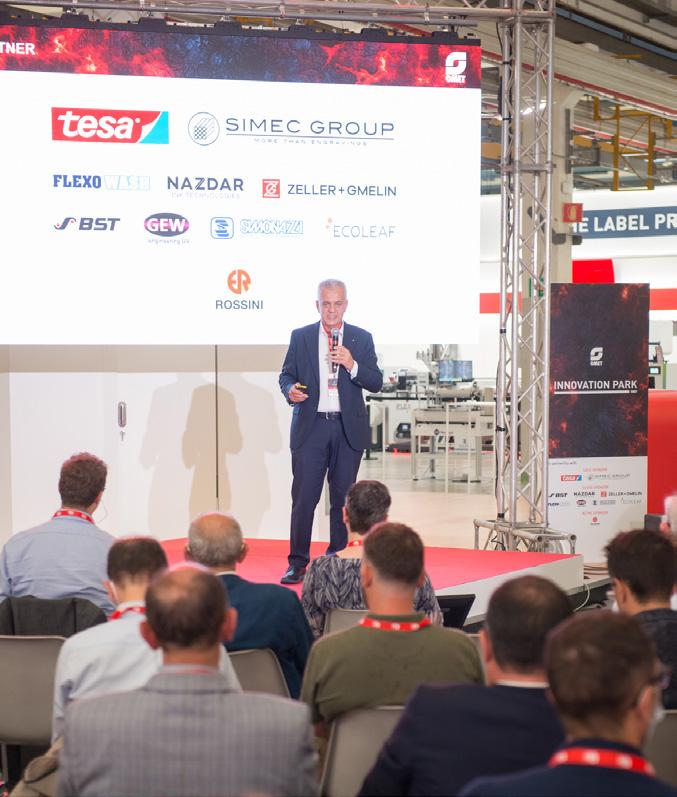
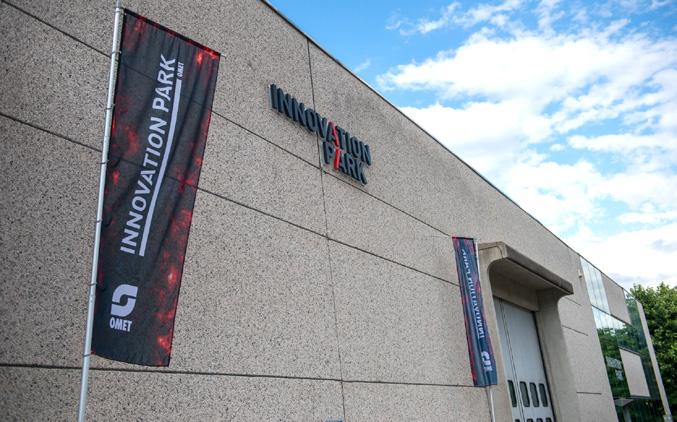
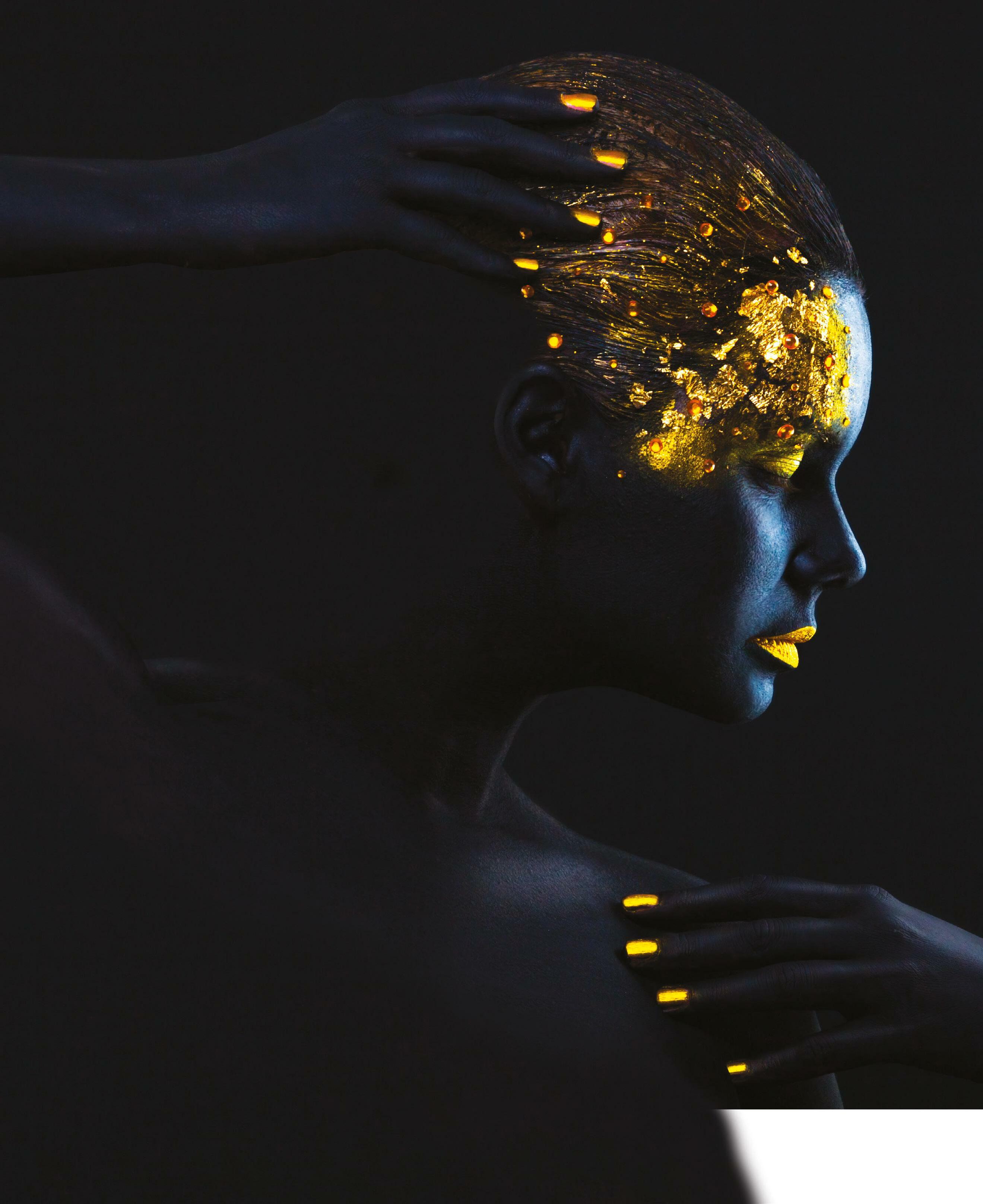
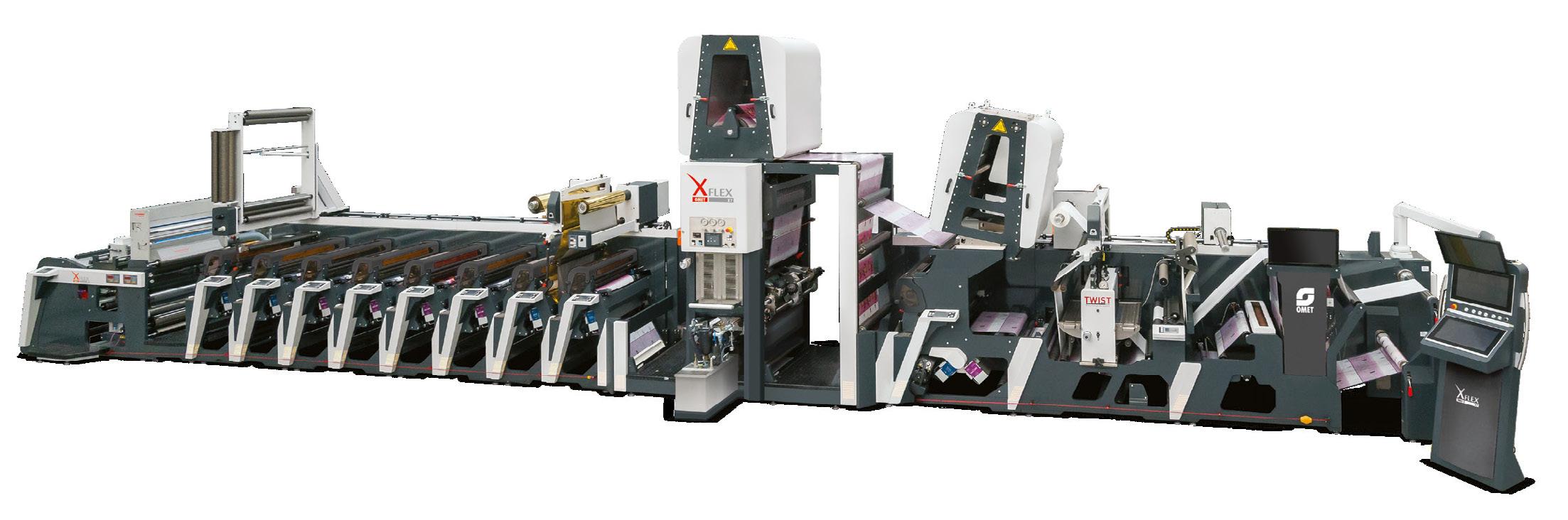
EFI has the capability to bring to this market the technology that can grow the amount that is digitally printed. We’re offering to our customers a solution that fits alongside their current technologies and makes their businesses more profitable.
Q: Why is single pass an area of focus for EFI?
Looking at EFI’s history, we focus on converting analogue printing businesses to digital. And corrugated is probably the biggest opportunity right now in terms of volume – of that 250 billion square metres, there’s probably only one per cent that is digitally printed at the moment.
RC: There are several drivers, with the most important being that e-Commerce has probably made 10 years’ of advancement in a year as a result of COVID. So, we’re seeing a big demand for e-Commerce.
EFI has already completed an installation of the new EFI Nozomi 14000 LED product at UK-based corrugated packaging manufacturer Caps Cases. We’ve also sold the first 14000 LED in the US to Complete Design & Packaging. These installs validate the direction we’ve taken in terms of our development.
The next phase of that is the Nozomi 14000 LED, which has just been launched and is already proving to be very successful with our customer base.
Digital is part of the mainstream workflow for EFI’s Nozomi range, says its packaging global sales director, Richard Cotterill as he unpacks the opportunities of the presses
Today, in our customer base, we have a global footprint of 40 Nozomi machines installed globally. And this year, those machines will produce over 200 million square metres of packaging and display. That’s quite a significant footprint. Our development has been focused on making sure we have a truly industrial solution.
Q&A EFI
EFI packaging global sales director Richard Cotterill
RC: In the corrugated market, there’s around 250 billion square metres of corrugated produced a year – and that’s just growing every year. In addition, paperbased packaging is replacing a lot of plastic packaging, and it all needs decorating.
Q: How has the EFI Nozomi portfolio developed over the years? Richard Cotterill (RC): When we look at digital printers for packaging, the Nozomi was well ahead of its time back in 2016 when it was first shown at drupa. In 2017, following our first Nozomi customer installation, single-pass and digital very much became a new buzzword.
Q: What are some market trends for packaging and drivers for the adoption of digital packaging?
Leading in packaging and creating opportunities with Nozomi
S ince it was first shown on a global platform in 2016, the EFI Nozomi range has become one of the leading digital presses in packaging. EFI packaging global sales director Richard Cotterill spoke to ProPack.pro about its plans for the range during his recent visit to Australia.
The Delta Group in London has also purchased Europe’s first EFI Nozomi 18000 Plus LED single-pass printer for display graphics. The fundamental technology in these presses is the proven head and ink technology that EFI has, but in a more compact footprint on the new 14000 LED model. We’re also focused on keeping the performance and reliability that we’ve developed within the Nozomi.
www.propack.pro22 ProPack.pro August 2022
What we’ve done since has made the product very robust. We’ve focused on making a platform that is reliable in the market and machines that consistently deliver.
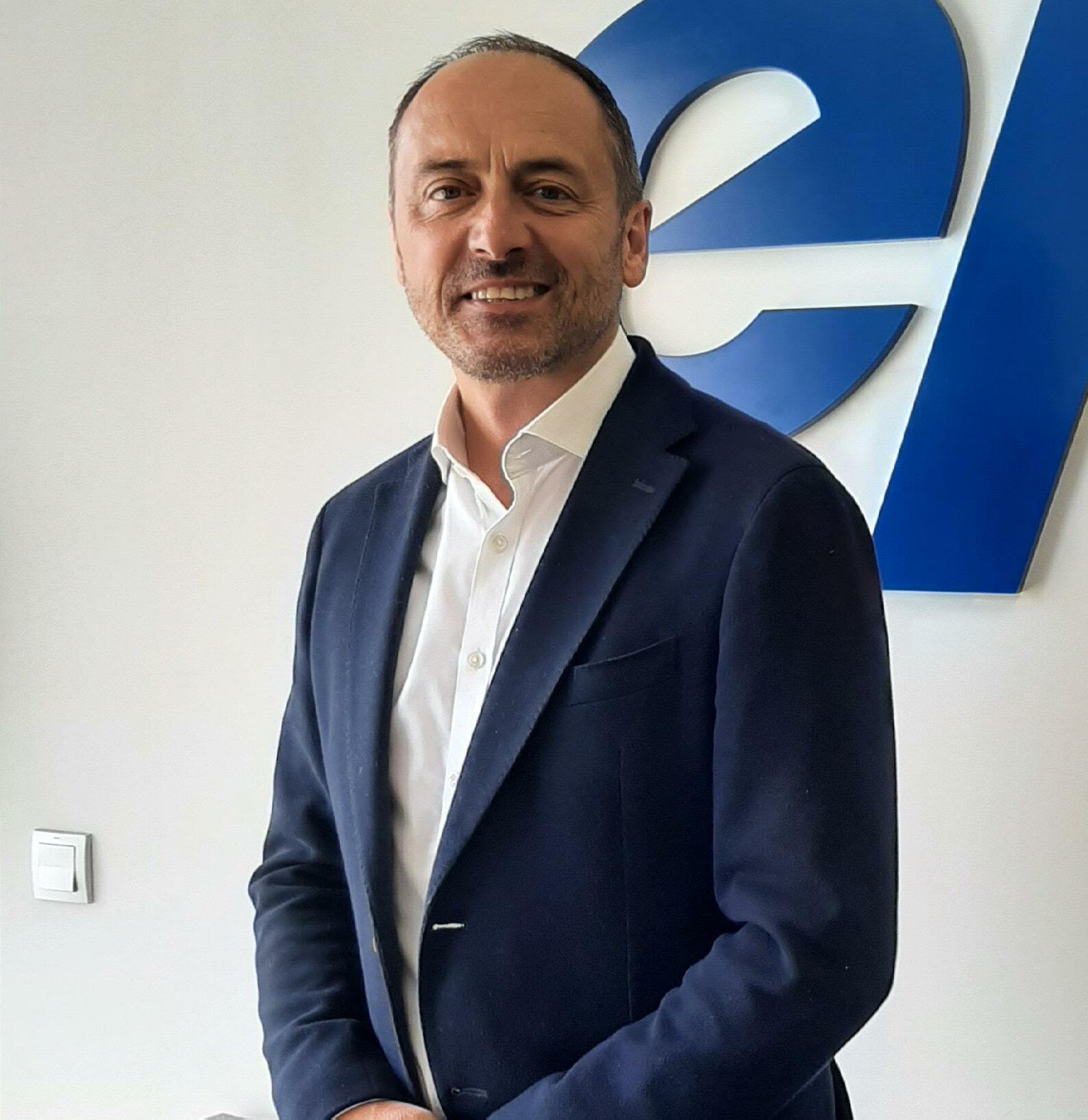
The new Nozomi 18000 Plus model is created for signage and display graphics customers
The new Nozomi 14000 LED is already proving very successful with EFI’s customer base
RC: Digital offers the value in sustainability and in the circular economy. The Nozomi is a UV LED system, so the energy usage is very low. When we talk about carbon footprint, it uses about a fifth of the energy of a traditional flexo printing press for example, or a waterbased digital press. So, it has a low carbon footprint and low energy usage which contributes to sustainability.
Q: What are some of the recently launched Nozomi 14000 LED’s features that address current market needs?
The corrugated business is a closed loop circular economy. In terms of costs, paper prices these days are constantly rising, so people are looking to reduce wastage, which digital certainly lends itself to. When considering the ink that is used in this business, businesses must be able to de-ink the corrugated, which we have the certification for, in addition to the repulpability of the corrugated used. So printed with the Nozomi, customers can put their corrugated into the traditional recycling methods.
Q: How is EFI adapting its future Nozomi presses to lead in the packaging space?
RC: Digital used to be a nice add on. But today, we’ve made it part of the mainstream workflow. We traditionally reinvest 15 to 20 per cent of our turnover in R&D every year and this translates into constant innovation in the Nozomi singlepass inkjet printing technology. We’re working with not only the printhead manufacturers but other partners such as the peripherals that go into the machine to improve the total workflow solution that our customers need. We’re taking a holistic approach to the business. We’re also listening to our customers as to what they want in future presses. EFI will continue to remain at the forefront of single-pass digital printing for packaging and we will be bringing new things to market. We will also continue to develop our software packages because everything we do is underpinned by our digital Fiery front end. We have some new software developments that we’ll bring to market later this year and in 2023. As always, EFI will be taking a consultative approach with its customers, tailoring the Nozomi to best suit their needs. It’s all about finding areas of profitability for our customers.
Personalisation is also growing –consumers want their products to really mean something to them, and brands want to build that connection with these consumers. With digital, businesses can be very flexible in switching between files quickly. Here in Australia, there’s also the demand for just-in-time packaging. Businesses don’t want to hold quantities of packaging. So having the ability to produce packaging just-in-time is a big advantage and digital lends itself to these situations as it offers that flexibility.
RC: Alongside its compactness, the speed of the printer is amazing – it prints at 75m per minute in very high quality, and it can print in up to 100m a minute. It gives customers the throughput that they need to produce volume work. This isn’t a digital printer just for short-run specialist applications; this is an industrial printer that fits into a customer’s workflow.
Q: How can A/NZ printers and packaging companies create opportunities from the Nozomi 14000 LED and the C18000 Plus? RC: It’s a case of looking at what they do today and how they produce things today. Printers and packaging companies may consider shifting some of their short-run jobs from analogue presses to digital presses where it is more cost-effective. This would drive overall greater efficiency and profitability on their analogue presses which could now focus on delivering longer-run jobs.
Samples printed on the new Nozomi 14000 LED
Q&AEFI
And when we look at trends, such as the unboxing experience, people want nice graphics with bright colours. This lends itself to digital as UV LED allows them to create that real ‘pop’ in colour.
www.propack.pro August 2022 ProPack.pro 23
It also gives them the opportunity to plug into new segments such as e-Commerce and deliver the level of personalisation and customisation that consumers are looking for today. There’s also the opportunity to use special features such as white ink, where customers can use it to print on uncoated brown craft liners, then print vibrant colours over the top of the white. This results in bright, eyecatching colours on a brown craft liner.
Q: Sustainability is such a huge part of the world today, especially in packaging. How does Nozomi play into that space?
We have found that it is key to our customers to being able to produce dayin-day-out sellable work and have that level of reliability. We’re also supporting them in terms of maintenance interventions and remote technical assistance, and we’ve applied this to the 14000 LED as well, to give our customers the all-round solution that they need.
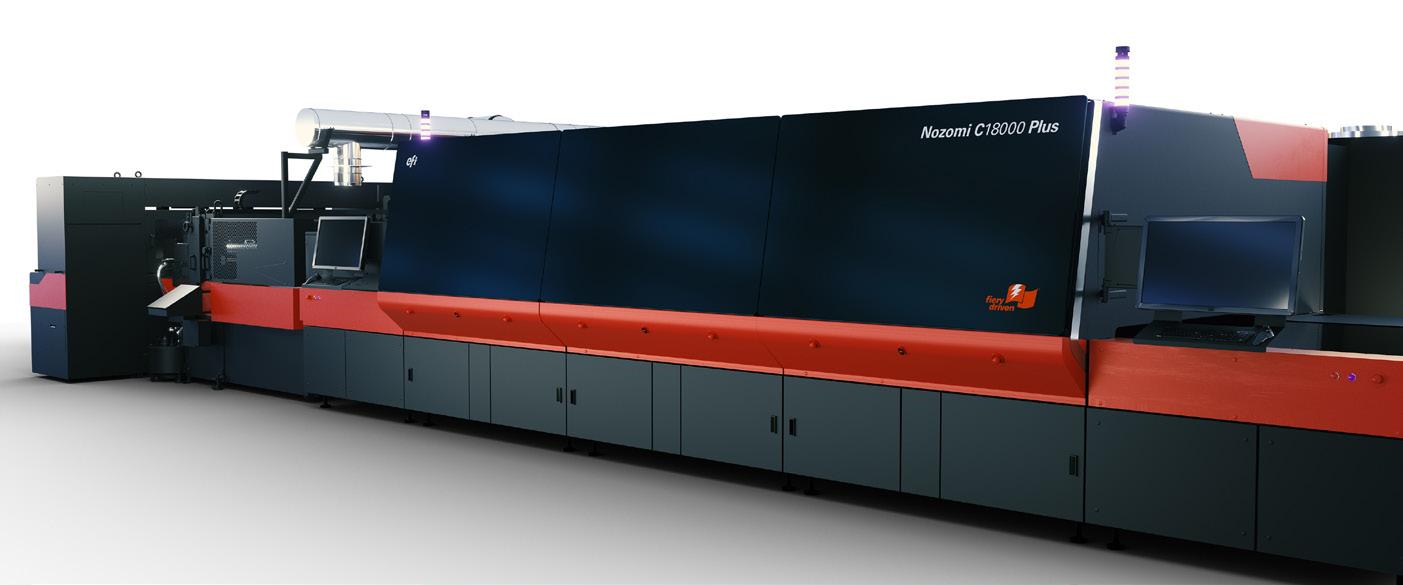
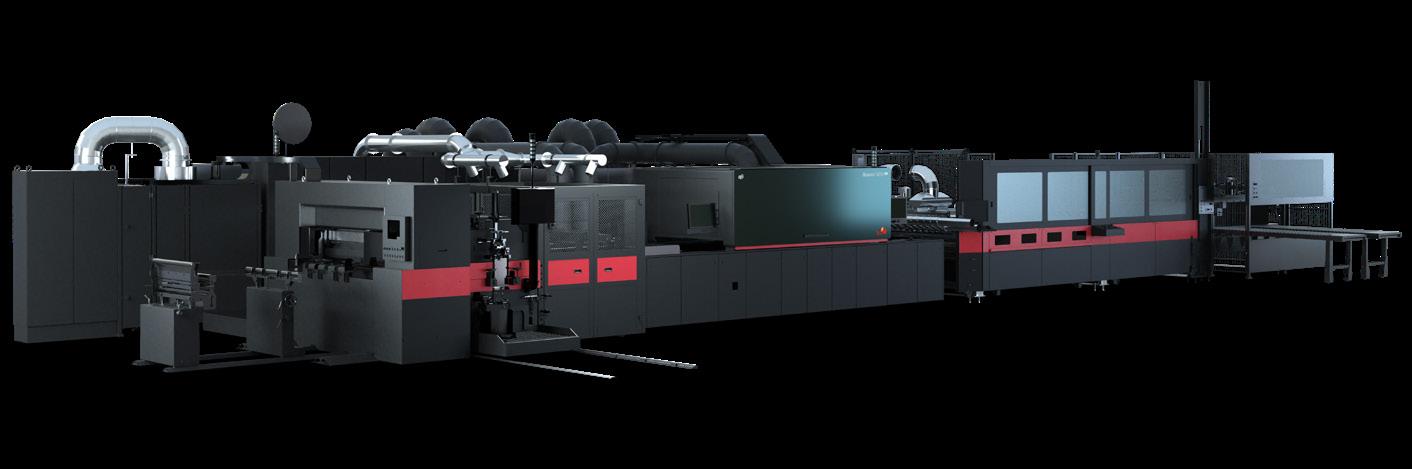
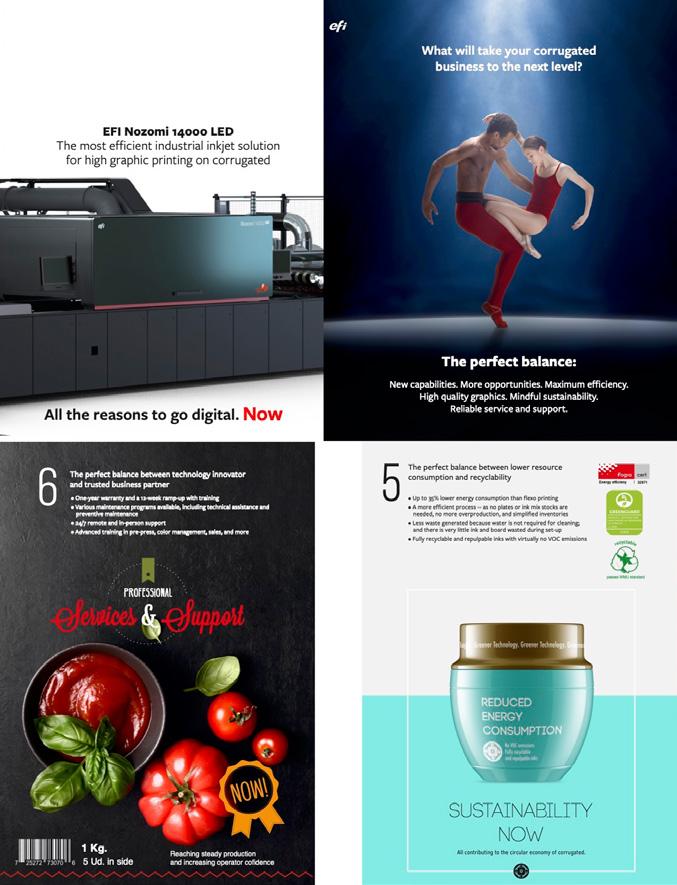
www.propack.pro24 ProPack.pro August 2022 AUSPACK 2022 Shorter, more agile runs power up packaging at Auspack Auspack 2022 was a huge success and, with the change to APPEX for 2024 and the 50 per cent increased floorspace, it will be bigger and better in the years to come By Andy McCourt (l-r) The Close the Loop Group stand, Jet Technologies stand, Matthews stand and Result Group stand at Auspack
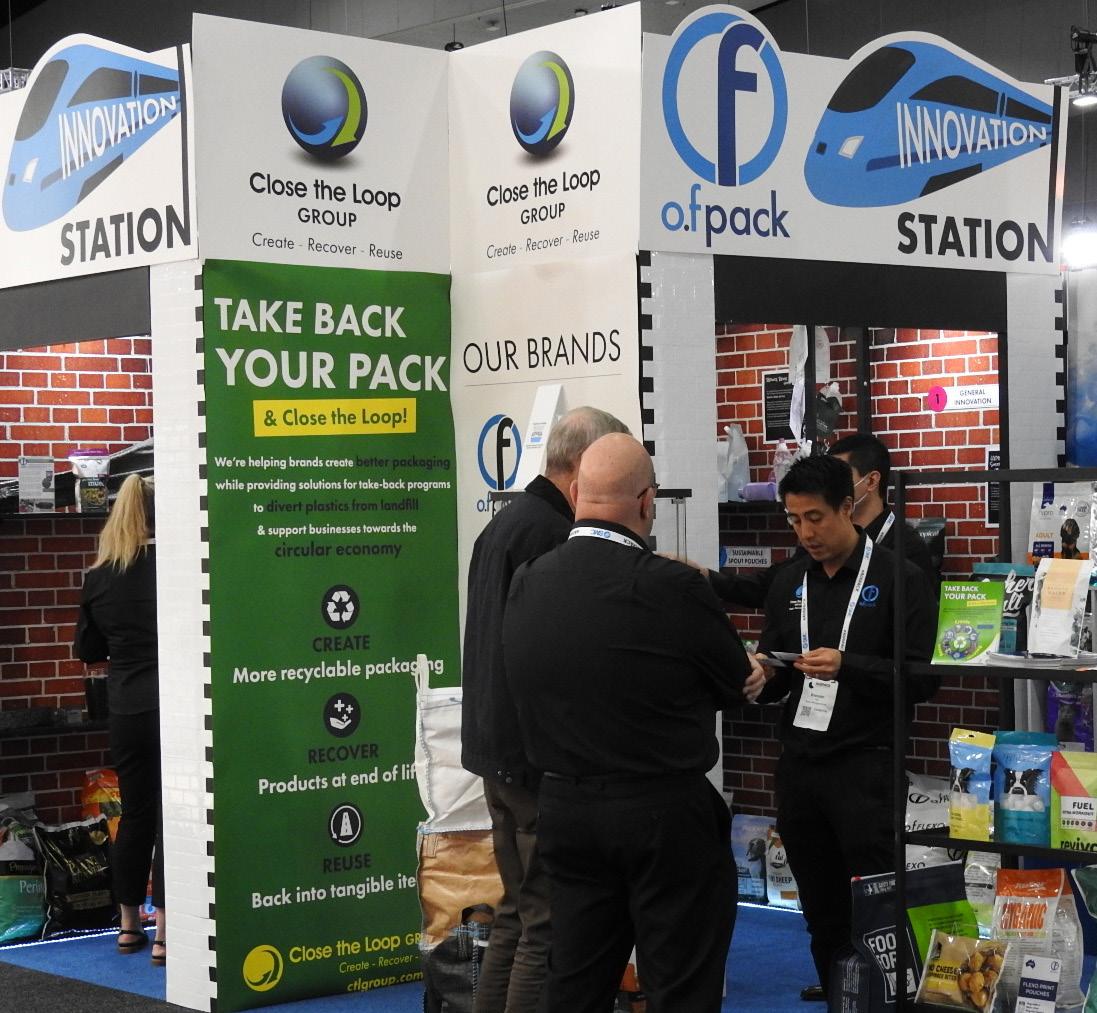
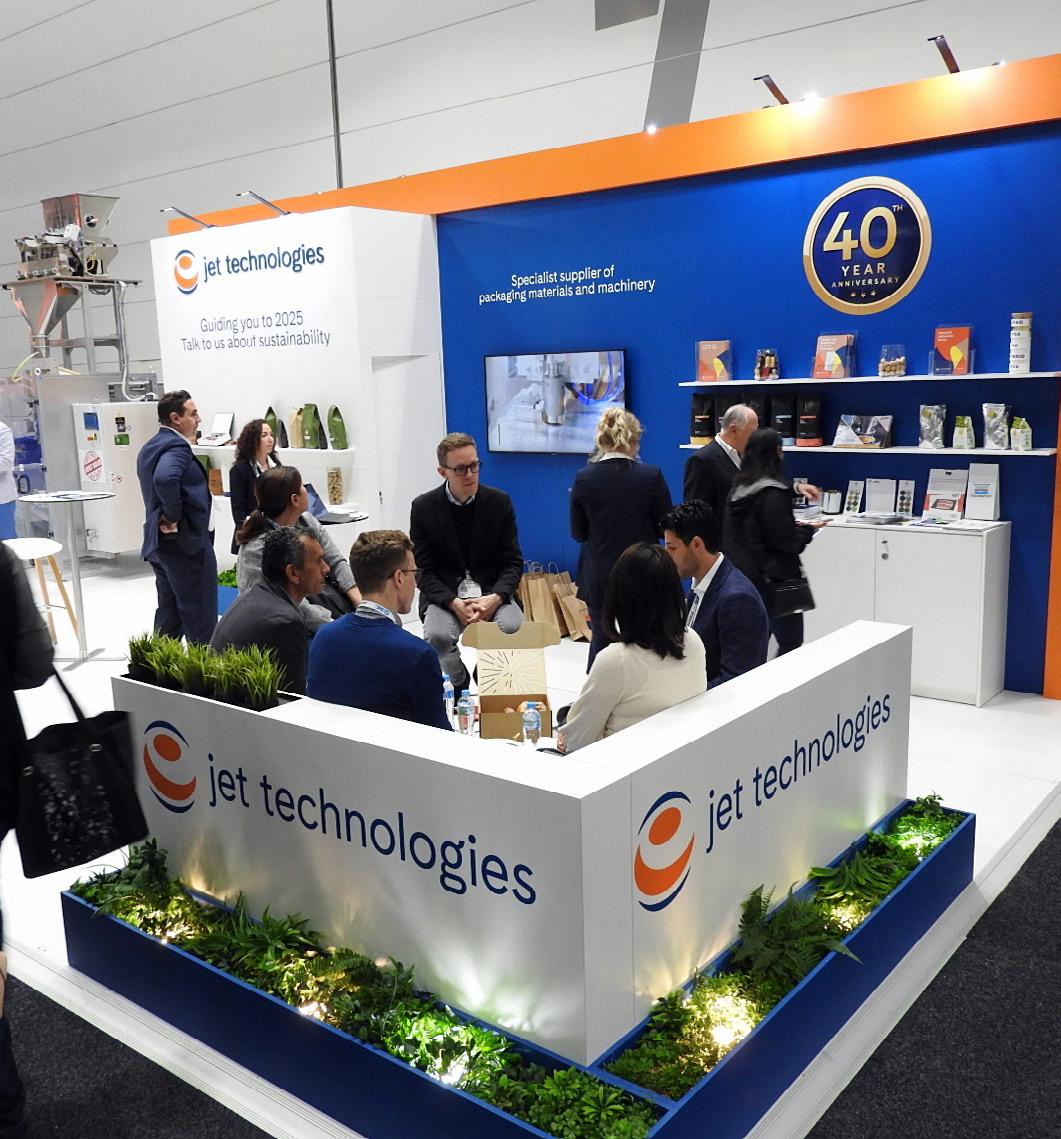

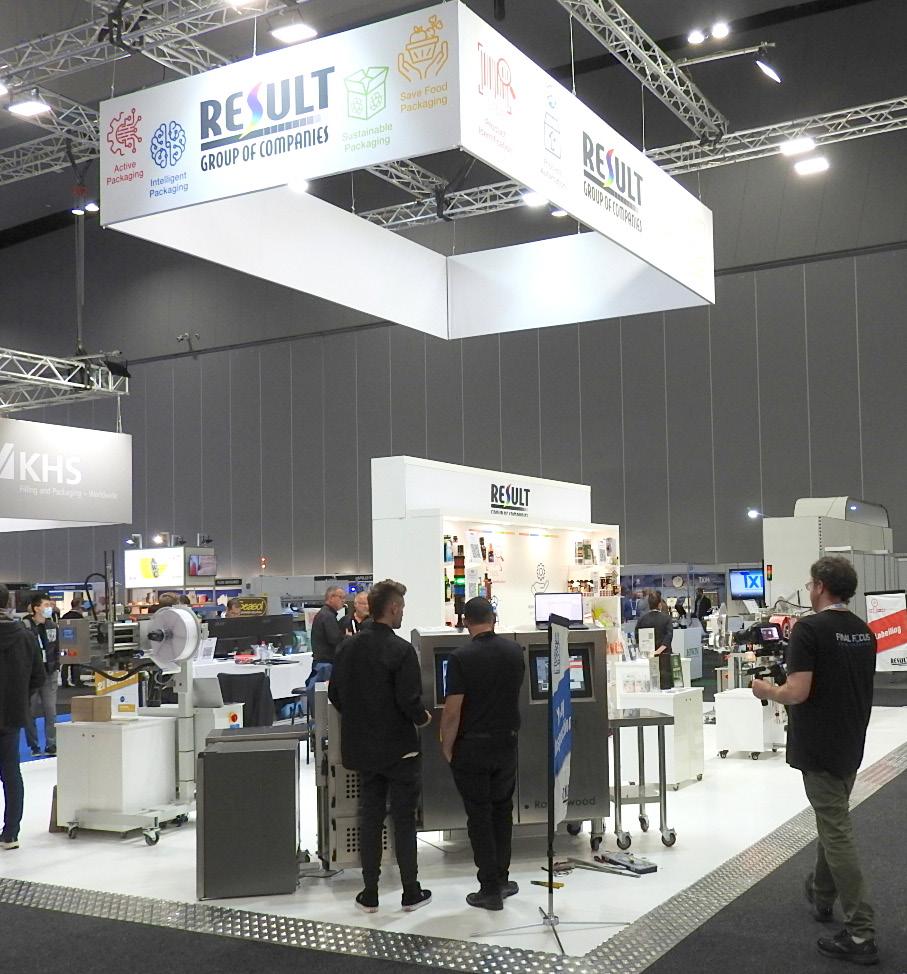
This was the remarkable Boxway Fitsize 2500 where corrugated up to 8mm thick is fanfold or sheet-fed in from one side and ready-toerect die-cut boxes are delivered on the other side. It is economical from a single box up to 1,000 and the touch-screen menu carries instructions for over 200 box types and is very easy to operate.
Job preparation is as little as 10 seconds and then all the operator needs to do is select a box style, enter the dimensions and a right-sized box is then produced.
Graph-Pak managing director Tom Ralph said the Boxway Fitsize is particularly useful for online sellers in need of a quick madeto-measure box instead of an oversize one filled with padding.
Output is four to nine boxes per minute depending on size and specification.
The minimum corrugated width is 400mm up to a maximum of 2500mm. Built in Taiwan, it uses Japanese-made Mitsubishi servo motors and control system for total accuracy. Standard box designs are FEFCO (European Federation of Corrugated Board manufacturers) – code approved.
The trend towards shorter, just-in-time or on-demand production – probably honed by the siren call of the Covid pandemic with hand sanitiser, wipes and masks – was perhaps best echoed by a new product shown in live demonstration on the Graph-Pak stand.
“Now is the right time to truly bring everyone together across the spectrum of processing and packaging into one show.”
Like PacPrint, Auspack was re-scheduled from 2021 to 2022 due to COVID and, as APPEX, will remain on a three-year cycle after the March 2024 event. Around the floor With over 200 exhibitors representing over 1,000 brands, Auspack 2022 buzzed with the pent-up demand for knowledge and
APPMA chairman Mark Dingley
(l-r) Graph-Pak’s Wayne Noyes and Tom Ralph with the Boxway Fitsize 2500 (l-r) Jet Technologies’ Natalie Marciano, Albert Malki and Olivia Novita
See a video of the BoxWay Fitsize 2500 here: https://tinyurl.com/4u8hw7na Filling the cups, pouches and bottles Jet Technologies’ stand was perpetually busy during Auspack, thanks to its broad range of T he trend towards shorter, more agile runs of packaging was prominent at Auspack, held in Melbourne in May about one month before PacPrint. Automation also had a strong showing with touch-free processes and robotic arms everywhere. This was the final Auspack under that name – the show transitions to APPEX for the 2024 event. Auspack was a watershed event for many reasons, not the least as the first major industrial trade show in post-lockdown Melbourne. It also heralded a new era for the show when, during the award presentations, the Australian Packaging and Processing Machinery Association (APPMA) chairman Mark Dingley announced that the event would be re-branded as APPEX to reflect: “one exhibition for the industry, run by the industry”.
The aim is to unify all aspects of processing with packaging and double the number of exhibitors from 200 to 400. Physical size will also increase, by 50 per cent with the organisers booking 20 bays of the MCEC instead of Auspack’s 13. A target of more than 10,000 visitors has been set. Remaining “anchored in Melbourne” at the MCEC, for logistical reasons, Dingley added, “We’re proud of how Auspack has grown, and the value that it gives exhibitors and visitors. Auspack is more than just a packaging-only exhibition, it is a show aimed at encompassing the total processing and packaging sector – from machinery, ancillary equipment, materials, packaging, and food processing, right through to industry services.
www.propack.pro August 2022 ProPack.pro 25 new products for Australia’s burgeoning packaging and processing industry.
AUSPACK 2022
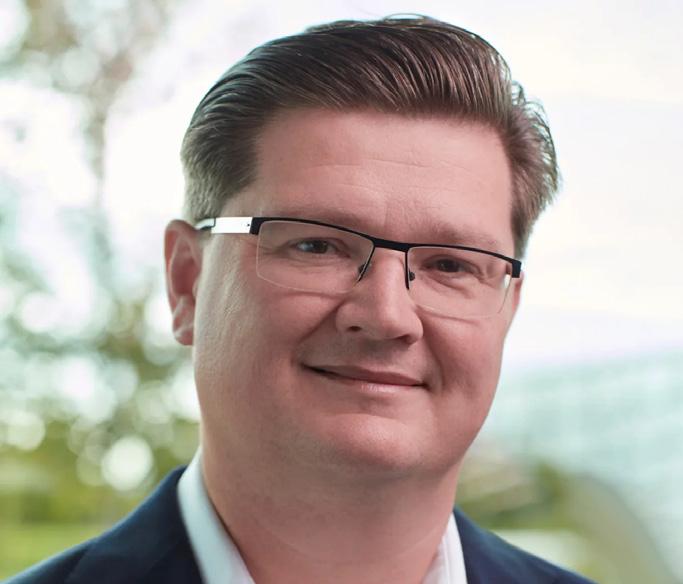
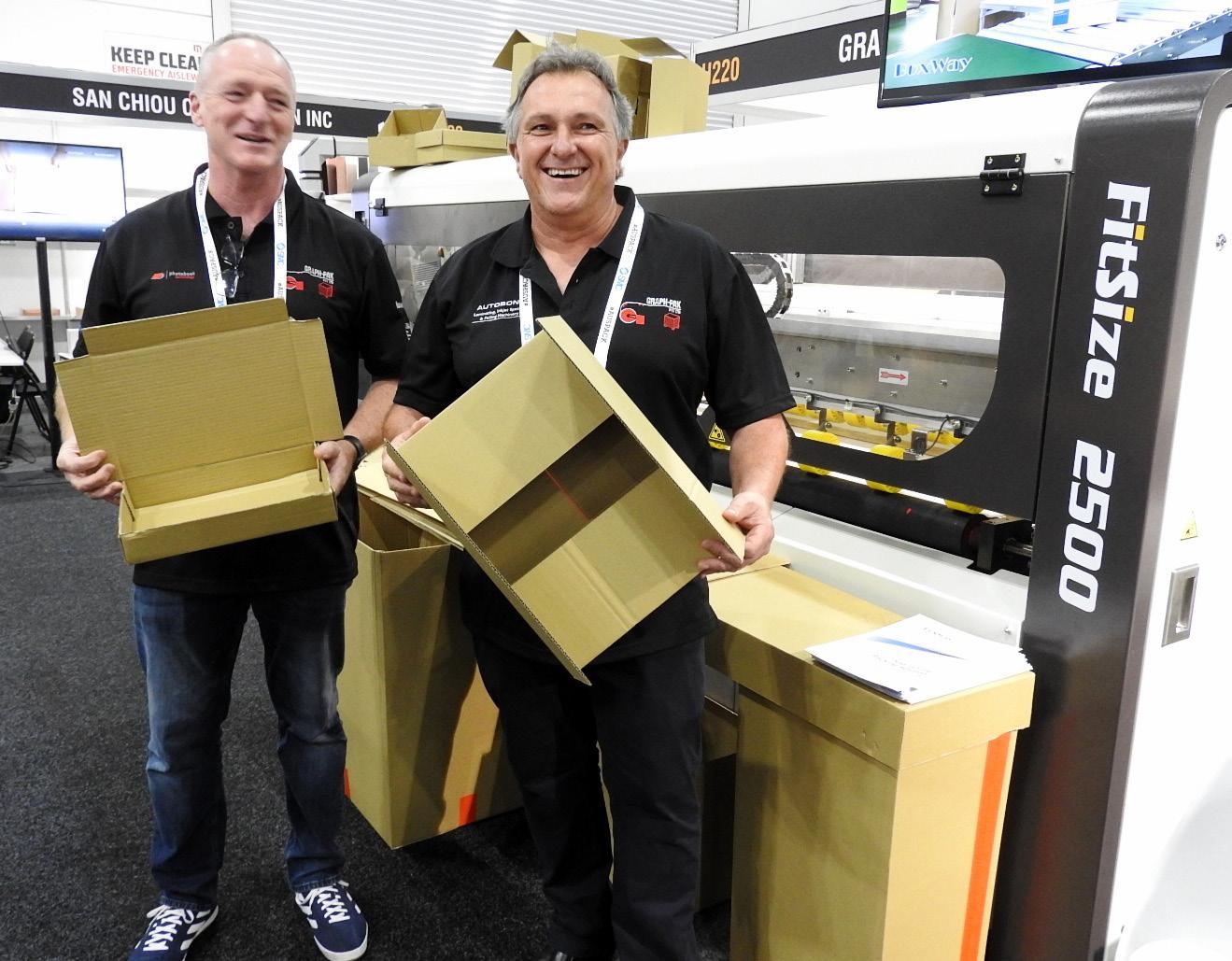

Visiting Jet Technologies from European and global packaging giant Constantia Flexibles was Nicola Pozzan, based in the Italian lidding division. Of interest was the Constantia approach to reducing plastic waste and throw-away lids for beverages and dairy products. This cup features a peel-back lid that stays with the cup. Once peeled back, it reveals a cold seal translucent cover with drink opening. The whole cup assembly stays as one piece for recycling and serves as a very secure and hygienic way of retailing beverages. Wine closures and packaging is an important area for Jet Technologies and present for its Vinventions range was Marc Schelcher with ‘The Art of Wine Packaging’. Jet Technologies has sustainable options for its hoods and closures, which are recyclable. Its sparkling wine hoods are 80 per cent composed of plant-based biocarbons.
Corks, both natural and synthetic, are still used extensively for premium wine closures and Jet’s Normacorc and Subr range eliminates TCA taint (‘mustiness’) that can occur with pure cork stoppers. Jet even has closures with liners that can regulate the rate of oxygen ingress into the wine. Jet Technologies also showed its wide range of flexible and vertical fill form seal (VFFS) solutions for the coffee sector including resealable pouches with air escape valves for the roasters. A Gogilo VFFS machine stood proudly on the stand, with one recently sold to Little Marionette.
Local innovation and manufacturing Packaging is an area that Australia has excelled in on the world stage. Amcor, for example just posted total revenues of US$14.9 billion in the year to end of March 2022, a 12.26 per cent increase on the previous year.
The award-winning Cardline 7000 has now been adapted to become the Foldline 9000
www.propack.pro26 ProPack.pro August 2022 machinery and packaging with sustainable options targeting the coffee, wine and spirits, dips and dairy, as well as ready meals sectors.
Founding father Albert Malki, who started the company 42 years ago, was present with son Daniel and a broad team of local and international product experts. A strong sustainability theme permeated the stand.
Advanced Robotics managing director Chris Scott noted, “The cost of robotics has come way down, making them attractive to packaging businesses of all sizes. Robotics make sense for several reasons – occupational health and safety, productivity, accuracy and dependability – robots don’t take sickies”.
On a smaller scale, Melbourne-headquartered Trimatt Systems took out the Australian Machinery Manufacturing Award – SME, at the 2022 APPMA Awards of Excellence held during Auspack. The award was for Trimatt’s Cardline 7000 line that attaches any kind of card or SIM to a carrier sheet, using proprietary gluing and folding methodology.
Innovation and bespoke customisation are things that Trimatt does very well. Founded by Matt Johnson in 2005, Trimatt automation systems for packaging, product handling, product inspection and imprinting have found customers all over the world.
AUSPACK 2022
Advanced Robotics specialises in system design and configuration, programming and total turn-key solutions based on customer needs, working with several robotics suppliers. At Auspack it showed two of its Qjar, Chinese-made multi-axis robot arms picking, rotating, and placing boxes.
Increased use of robotics Robotic palletisers have been used for a few years in packaging but Auspack saw a proliferation of robot arms performing many tasks. There were around 25 exhibitors showing robots and cobots (collaborative robots).
Marc Schelcher with Jet Technologies’ presentation box ‘The Art of Wine Packaging’ Matt Johnson (l) and team at Auspack with the Foldline 9000 Advanced Robotics’ Chris Scott showed two Qjar Chinese-made robots, precisely picking and placing boxes Nicola Pozzan from Constantia Flexibles with the double-seal cup concept
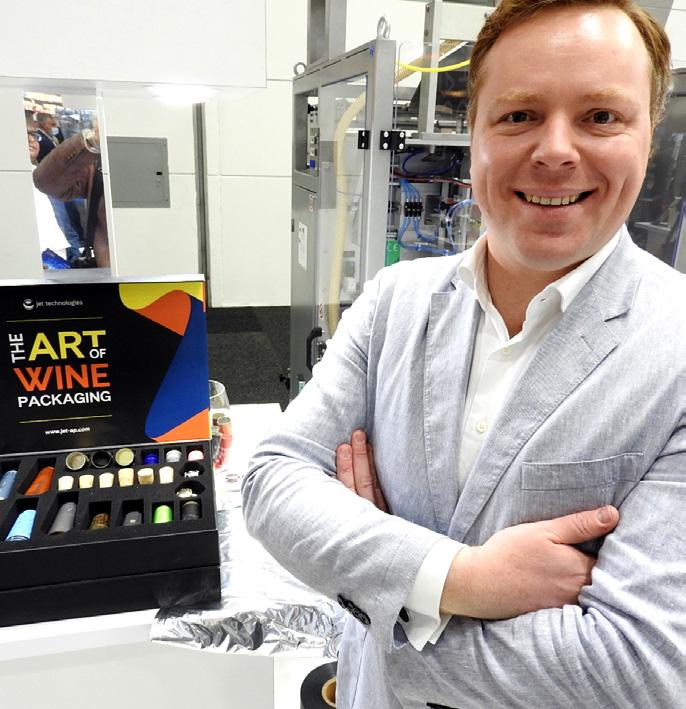
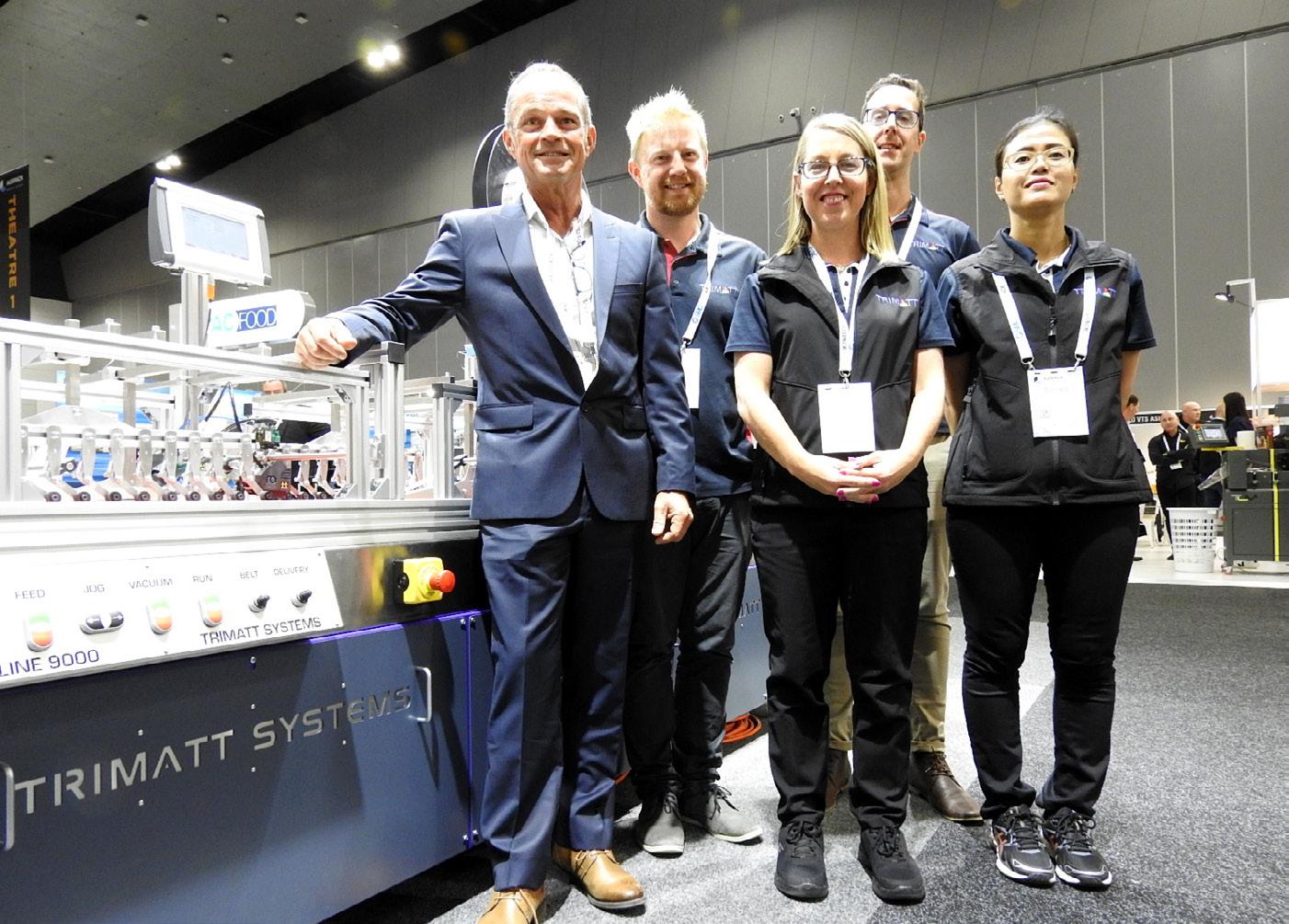
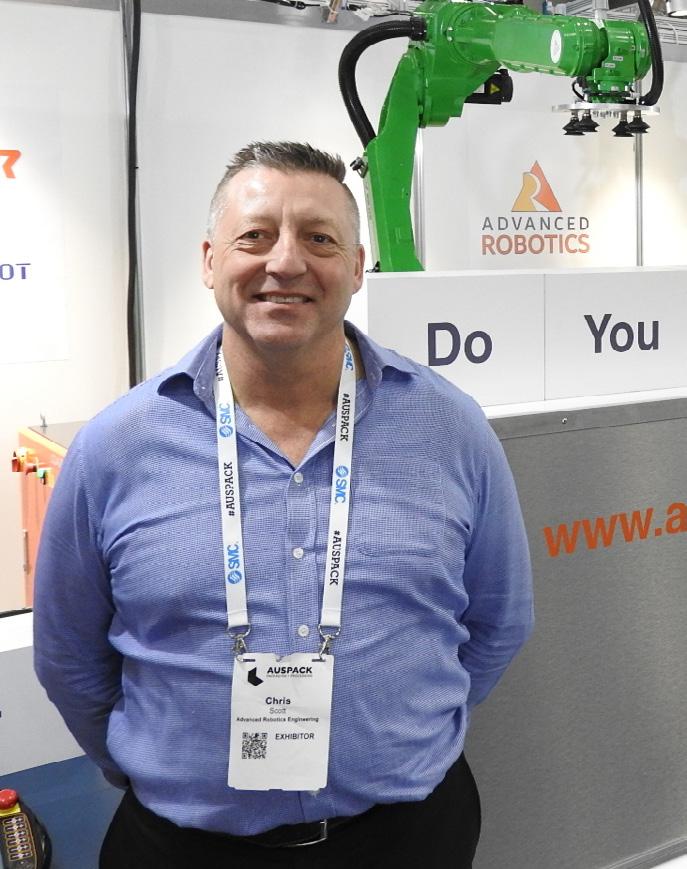
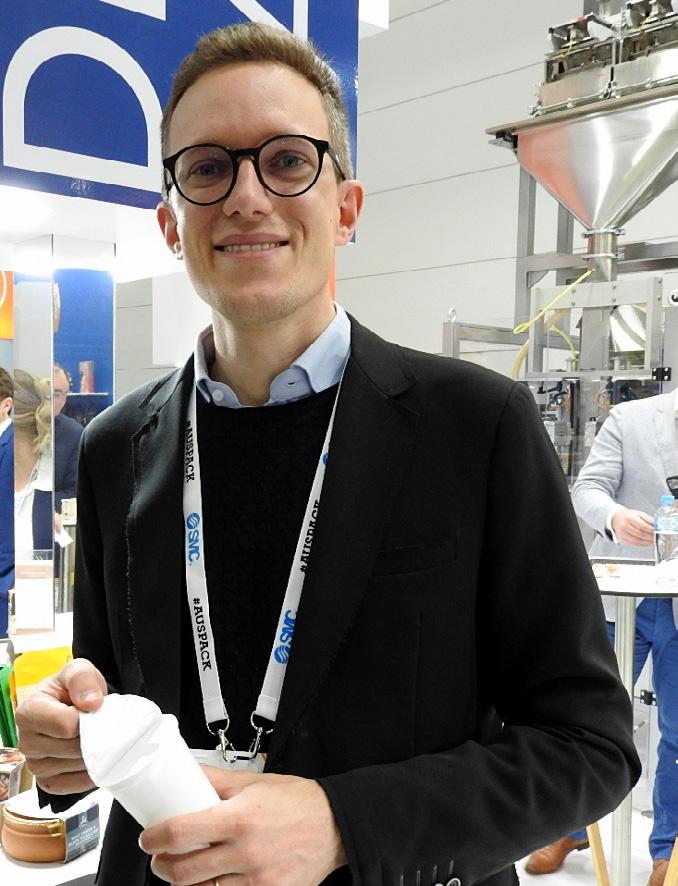
Chocolate lamb chops
Result Group reported “massive interest” in the new Ravenwood Nobac 5000 linerless fruit lid applicator at Auspack. Taking a fibreboard fruit tray to the next level of marketing appeal with a full colour printed cover, it is an extremely sustainable, linerless solution for applying the labels and wraparounds to replace plastic. Speeds of up to 70ppm can be achieved with label widths from 100mm to 255mm.
Auspack 2022 was a huge success and with the change to APPEX for 2024 and the 50 per cent increased floorspace, it will be a fullblown aisle-pounding expedition! Australian packaging is a vibrant, smart and well-resourced industry with no end in sight to its growth potential. It is also increasingly sustainable and, with APCO 2025 coming up, we can look forward to even more initiatives that keep plastics out of landfill.
Other Nobac configurations cater for linerless labelling of susages, ready meals and protruding proteins such as roast meat joints.
Johnson said his company invests 27 per cent of its revenue back into R&D and custom product development, which often becomes mainstream machinery.
Result Group’s stand was a hive of packaging activity including a clever way of demonstrating linerless labeling of fresh meat protein – lamb chops – by putting Cadbury’s chocolate inside instead!
Examples of sleeves for FMCG food trays, produced on Trimatt’s Foldline 9000
‘digitalmorewheregenerationDosserResultyoutube.com/watch?v=-CUteVc75Cs&t=1shttps://www.GroupmanagingdirectorMichaelisalsoastrongadvocateofnextQRcoding–GS1DigitalLink–thedatamatrixcancarrymuchinformationandbecomelikeachannel’ofproductinformation.
In summary...
One example is his adaptation of HP inkjet technology to create the Trimatt 1170 allpurpose inline printing system which can print in full colour boxes, bags, trays and more, up to 100mm in height.
www.propack.pro August 2022 ProPack.pro 27 AUSPACK 2022
Chocolate lamb chops from Result Group at Auspack
Result Group managing director Michael Dosser
The Foldline 9000 can also be fitted with an imprinter for variable date codes or even names and addresses for mailed-out A4 envelopes such as magazine subscriptions.
Result Group technical operations manager Paul Rushton demonstrated the machine and a video that explains it all can be seen at: introducedAnotherhttps://youtu.be/_RcqsvPNJEclinerlessmachinethatwasatAuspackistheHERMA Labeling Machines InNo-Liner. The Herma InNo-Liner applicator and label material is a linerless alternative; no silicone liner or coatings are used in this method therefore no landfill. Shipping labels can be printed, re-moistureable applied and coded using paper with no silicone waste. An explanatory video is here:
“We’re a hybrid company of marketing demand and engineering,” Johnson said.
to feed, fold and glue wrap-around sleeves for food product trays. It can produce up to 20,000 sleeves per hour, making it ideal for smaller manufacturers to present their produce with a ‘big brand’ look.
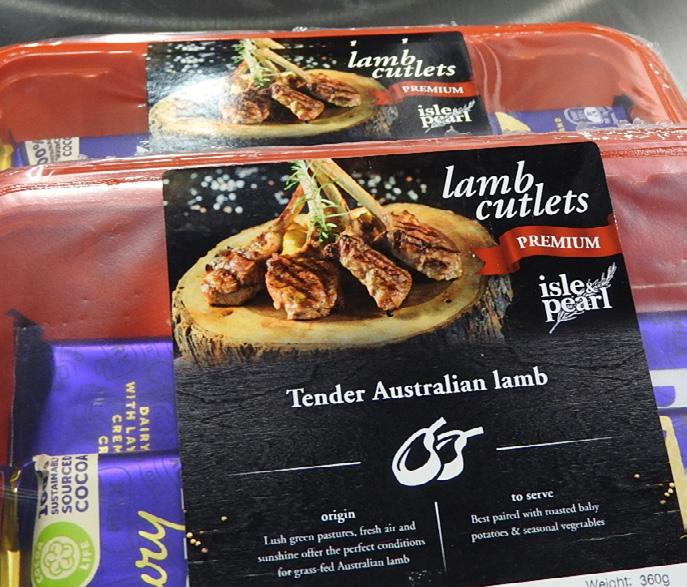
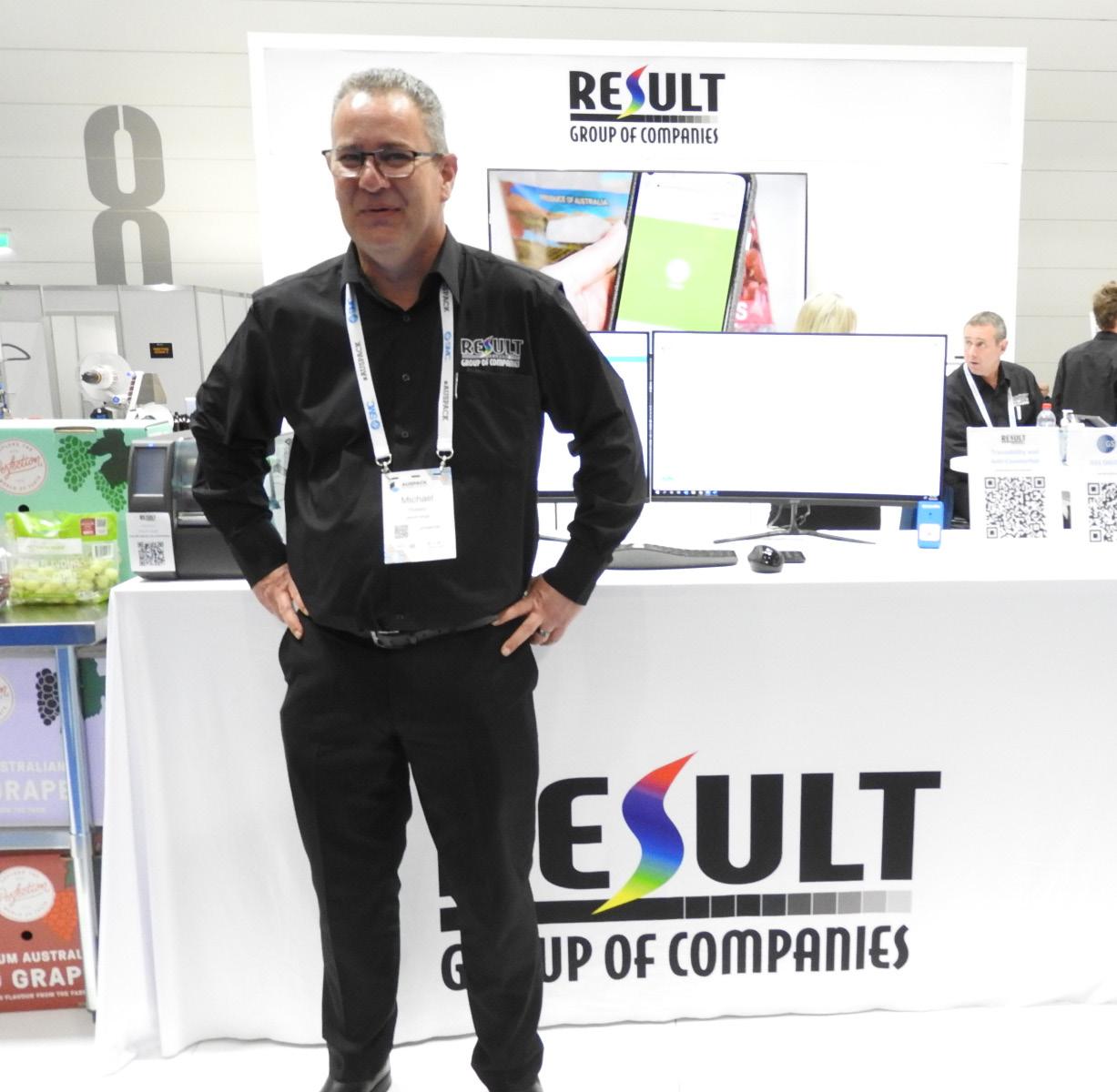
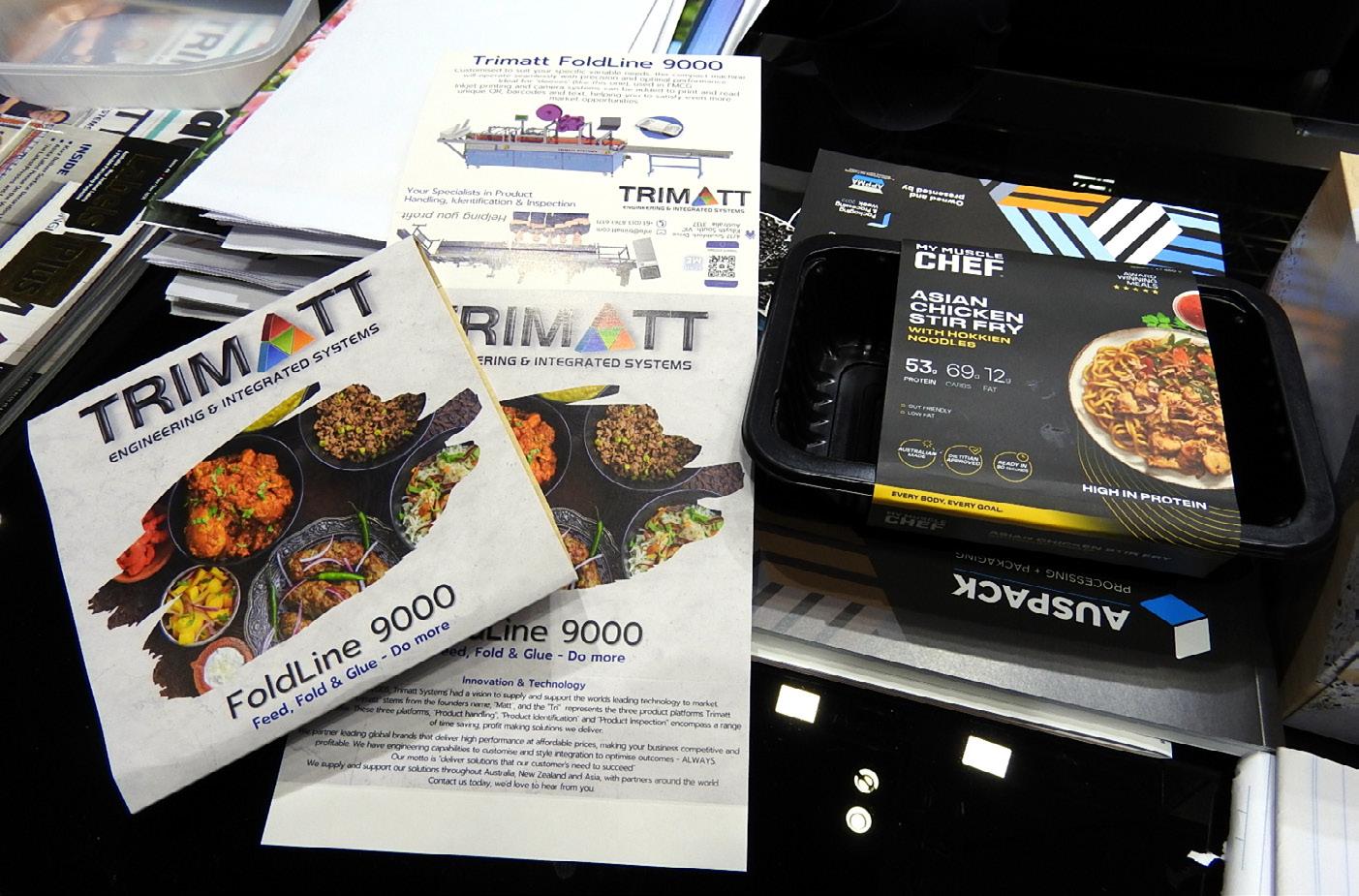
Exhibiting companies include ABG, Asahi Kasei, Avery Dennison, Böttcher, Cartes, Domino, DuPont, Durst, Epson, Esko, Fedrigoni, Fujifilm, Heidelberg, HP, Hybrid Software, Konica Minolta, Kurz, Mark Andy, MPS, printIQ, Omet, Ricoh, Screen US, Sun Chemical, Tharstern, UPM Raflatac and Xeikon. Labelexpo Americas will feature hundreds of live demonstrations, a digital embellishment trail, a two-day topical conference and two expert-led master classes.
In recognition of the importance of the show and the delaying of Labelexpo Europe, the European organisation FINAT is taking a large delegation of converters across the Atlantic for the Labelexpoevent.Americas show director Tasha Ventimiglia said, “Our whole team is very excited to be finally welcoming the industry back to a Labelexpo. Labelexpo Americas 2022 will be the first time since the start of the global pandemic that many suppliers have had the chance to showcase their latest technology developments and we are thrilled to see the amount of working equipment that will be running at Labelexpo this year.”
LABELEXPO AMERICAS
There are advantages for Australian and New Zealand converters, that our changing times have bestowed on Labelexpo Americas.
www.propack.pro28 ProPack.pro August 2022
From Good to Great’, the focus for this year’s show is on improving converting business. Complementing the main exhibition is a digital embellishment trail, which will highlight experts in this area with live demonstrations showcasing the ways it can transform a converting business.
Some of the products that will be shown include Durst’s Tau RSCi 510 line with flexo stations, as well as a Tau RSC E 330 standalone unit, marking this show as the company’s biggest Labelexpo booth to date.
2022’s biggest label converting show is in Chicago
The floorplan looks very impressive, with the largest area taken by HP. All the major suppliers of both hardware and consumables have large stands.
O rganised by the same company as Labelexpo Brussels and other events – Tarsus Group – Labelexpo Americas has grown into a label converting event of similar size and importance. Given the deferment of Labelexpo Europe to September 2023, the Americas edition now serves as the world’s premier label conference and trade fair for 2022. Labelexpo Americas will take place from 13 to 15 September at Chicago’s Donald E. Stephens Convention Center, right next to O’Hare International Airport in Rosemont. Over 400 exhibitors will fill five halls. The last show, held in 2018, attracted almost 17,000 visitors from 86 countries.
Themed ‘Turn Your Converting Playbook
By Andy McCourt
Pre-show announcements
The crowds from the last LabelexposhowAmericasin2018
The Tau RSCi 510 is a 510mm the printer designed to take over mid-to long-run jobs and is also able to produce short-run jobs in the most economical way. The Tau RSCi is also equipped with a chill roller and jumbo winders to guarantee material flexibility and maximum ease of use.
With the postponement of Labelexpo Europe until 2023, all eyes are now on Labelexpo Americas 2022, taking place from 13 to 15 September in Chicago
Labelexpo Americas show directorVentimigliaTasha
There will be no language barriers for English-speakers and, with the tragedy of the Ukraine-Russia conflict blighting European safety and logistics, trans-Pacific travel is a better option with one-stop travel time very similar to European destinations.
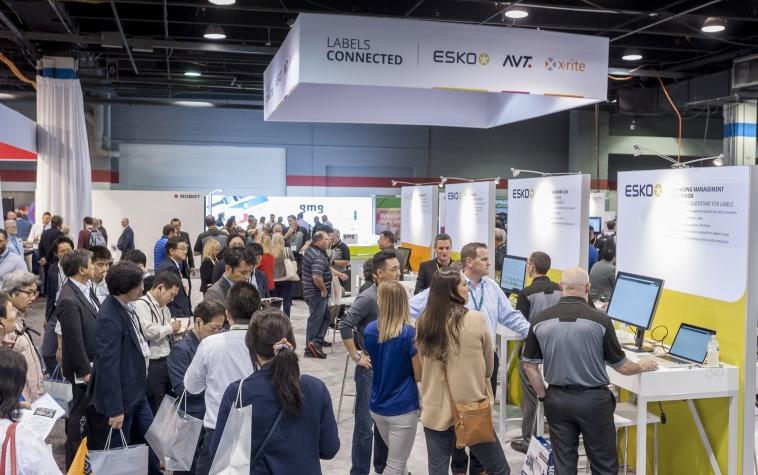
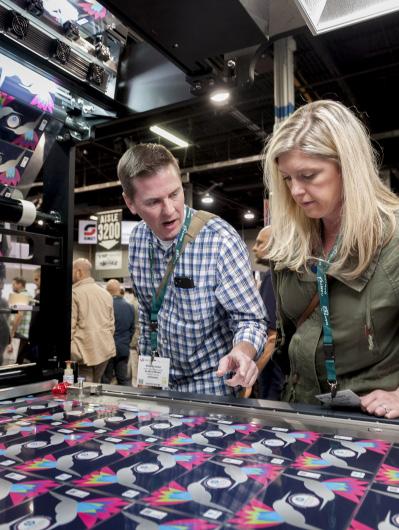
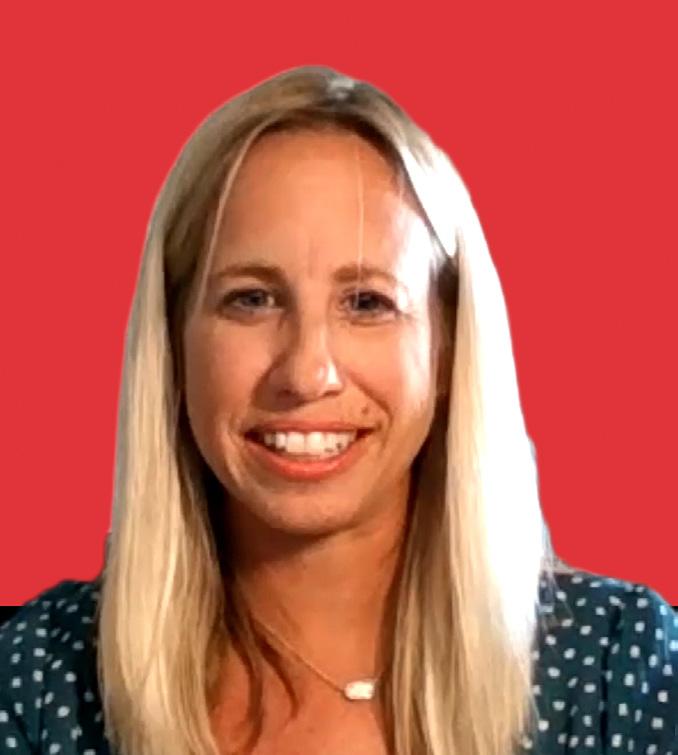
The Sitexco Label L10 Anilox Cleaning System, from Eaglewood Technologies, will also be on show
Top shelf conference presenters US trade shows always include a comprehensive conference and seminar program, and attendees will also be able to learn about ways in which they can make their business and the wider label and package printing industry, more sustainable by attending a themed area sponsored by Tag & Label Manufacturers Institute (TLMI).
NeuraLabel Printing Solutions will be debuting the Callisto at Labelexpo Americas
Likewise, Flexography will be everywhere at Labelexpo Americas and one notable launch will be the eco-friendly the Sitexco Label L10 Anilox Cleaning System, from Eaglewood Technologies. Based on the Sitexco Laser Anilox System, the L10 is a slimmed-down version specially designed for the narrow web printer. This is the most sustainable technology available, using no chemicals, water and generating no waste.
www.propack.pro August 2022 ProPack.pro 29
Epson’s booth will feature the SurePress L-6534VW UV press r-Polyart is the first synthetic paper made of 30 per cent post-consumer recycled material
Two half-day expert-led master classes on 14 to 15 September, run in association AMERICAS
The L10 is safe for aniloxes, employees and the Italianenvironment.digitalfinishing manufacturer Cartes will demonstrate its new Jet D-Screen module GE363VJL, which offers specially designed technology to create outstanding labels embellished by multi-layer effects, spot coating, complex tactile raise volumes and braille printing as well as detailed foiling and metallic doming transferring.
Italian digital finishing manufacturer Cartes will demonstrate its new Jet D-Screen module GE363VJL Durst’s Tau RSCi 510 line with flexo stations will be shown at Labelexpo Americas
On the consumable side, Frenchheadquartered Polyart Group will launch r-Polyart – the first synthetic paper made of 30 per cent post-consumer recycled material. r-Polyart looks and prints like 100 per cent virgin material, and has the same mechanical properties, but has a lower carbon footprint. The Labelexpo floor map will be printed on this sustainable material, to ensure a low carbon footprint to the show. R-Polyart is used for industrial, VIP and prime labels.
Screen Americas will use Labelexpo for the first North American public showing of its new Truepress Jet L350UV SAI version, which features additional orange and blue inks, high-speed white and advanced CGS colour management. With Australia jumping the gun with several SAI version installations, converters will get to see the stunning array of colours achievable with the CMYK+O+B+W seven-colour inkset and white ink running at The50m/min.veryshort run benchtop label market will not be overlooked, with NeuraLabel Printing Solutions debuting the Callisto, an industrial desktop label printer ideal for short- to mid-run on-demand printing. Callisto is based on the HP A3 PageWide printhead technology and uses highcapacity, durable pigment ink.
The popular educational program comprises a two-day conference program on 13 to 14 September tackling the industry’s biggest issues including M&A, automation, diversification, and supply chain challenges.
Using laser die-cutting, the new screen module enables process automation, such as automatic job changeover by barcode reading, automatic slitting positioning and turret rewinding systems, creating a perfect combination for digital finishing.
As for the Tau RSC E 330, it is a standalone UV inkjet label press for small and medium size companies in the label printing business. Equipped with latest RSC technology, the machine combines best-in-class print quality with an economic investment. Fully upgradable to an eight-colour, the machine has a print speed of 80 m/min, guaranteeing increased production capacity. Epson’s booth will feature the SurePress L-6534VW UV press available with digital varnish or orange ink. Digital varnish offers spot varnish, simulated foiling, and embossing all in line with the label production. Labelexpo will also be another chance to see Epson’s new SurePress L-4733AW water-based resin press, first seen at PacPrint in Melbourne. This press delivers low-cost white ink label printing, ideal for food production packaging including PS labels, IML, shrink, and confectionery wrappers.
LABELEXPO
Speakers and panelists include TLMI president Linnea Keen, Fortis Solutions Group CEO John Wynne, FINAT managing director Jules Lejeune, Procter & Gamble innovator Ken McGuire, Mark Andy CBO Tom Schlembauer, Ferrari Innovation Solutions president Mike Ferrari, Baldwin Technology CTO Steve Metcalf, CERM MD Geert van Damme, HP Indigo global BDM Christian Menegon, Label Traxx president Rob Mayesron, Durst product manager Martin Leitner and ePac GM Robert Schultz.
This is the first time the North American industry will see a public showing of Screen’s new Truepress Jet L350UV SAI version
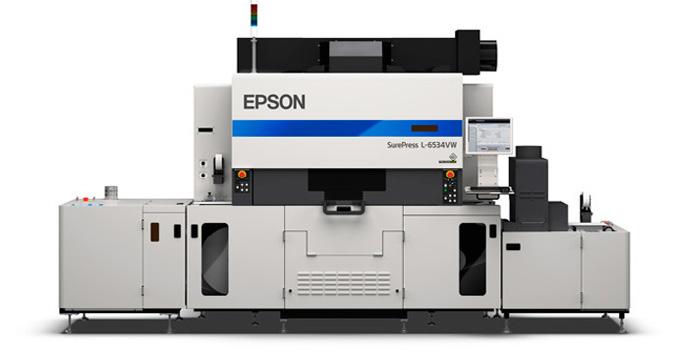
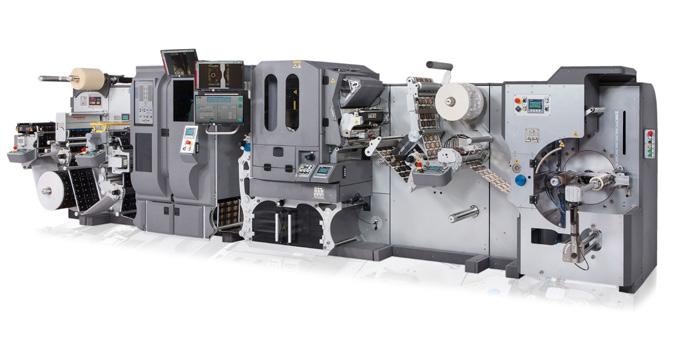

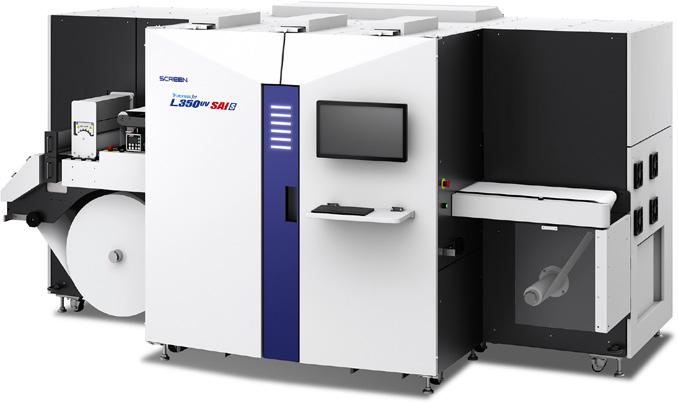
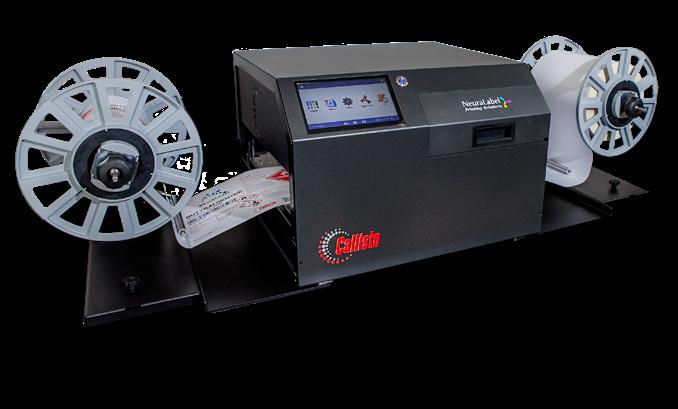
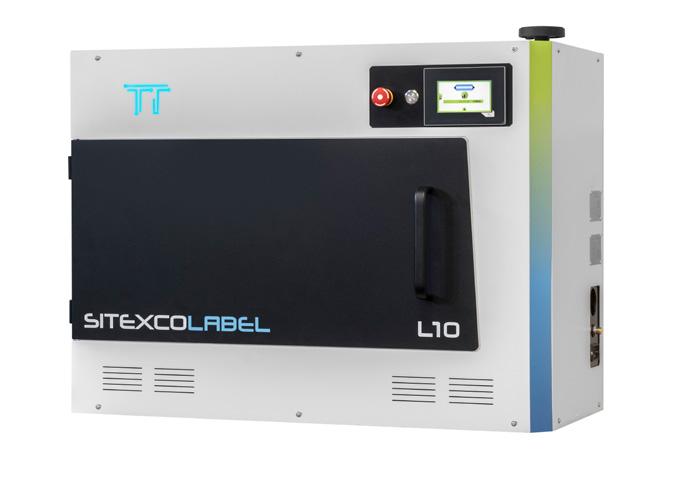
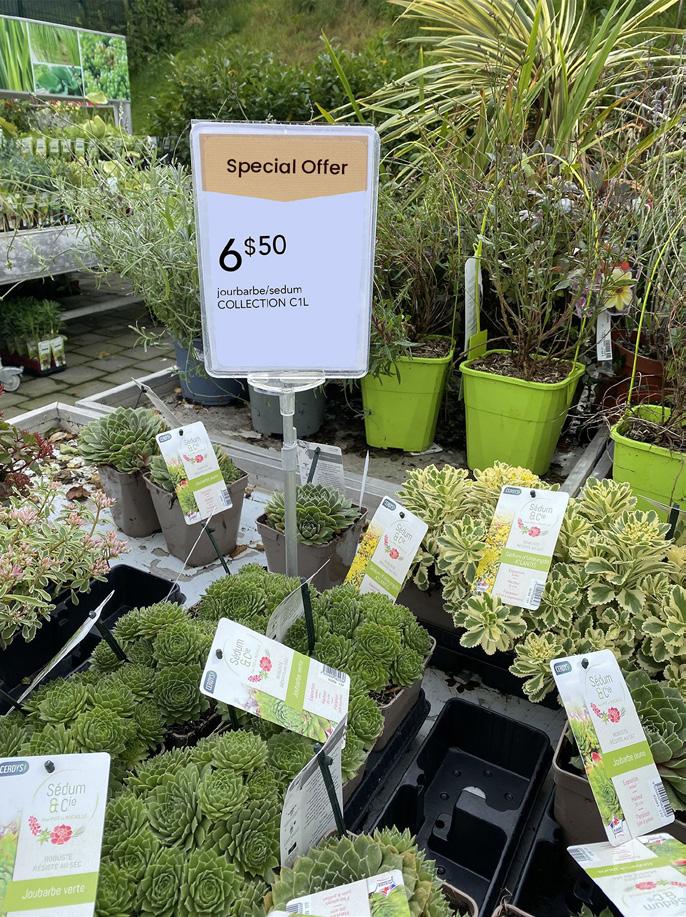
said, “What’s truly so special is that business doesn’t only happen within the convention centre walls. Rosemont is unique in that over the past few years, they have created a community.
Labels are always front-and-centre of brands. Even with the move to pouches, it’s label converting technology that is the main driver. Labelexpo Americas covers all of these aspects including the brand sectors of:
Presentersmaterials.from Xeikon, Sun Chemical, Kurz, Cartes, EcoLeaf, GM, Prati, Epson and HP Indigo will cover embellishment while presenters from Labelexpo, UPM Raflatac, Henkel, Avery Dennison, 3M, Mactac and Fedrigoni will cover self-adhesive materials. Further speakers are to be announced.
www.propack.pro30 ProPack.pro August 2022 with the Label Academy, will cover digital embellishment and self-adhesive label
One such example will be HP’s first showing of its V12 narrow web press, previewed at PacPrint. Key features of the HP Indigo V12 Digital Press include: printing up to six colours at 120 linear metres per minute, using six inline imaging engines running simultaneously; new high definition imaging; up to 12 colours on press capabilities; and one-pass, high-speed finishing capabilities provided by AB Graphic, manufacturer of the Digicon finishers.
There is nothing better than great labels to build great brands
Labels – the power in front of the brands
After hours networking Trade shows are more than expo floor and conference – after hours is just as important and the Chicago suburb of Rosemont will not disappoint – or you can venture closer downtown or take in the famed blues and jazz Ventimigliaclubs.
An early bird entry price of US$60 is available for visitors who register prior to 28 August
The latest Smithers report on the global label sector values it at US$41.75 billion in 2021, growing at around four per cent per annum up to 2026, reaching around US$46.16 billion. It’s a multi-faceted part of the printing and packaging industry, far more complex than the popular perception of ‘stickers’ would suggest.
If you want to be ultra-informed about what is happening and will happen in the label converting industry, there is no better place to be in 2022 than Chicago, at Labelexpo Americas, 13 to 15 September! Registration is online via: www.labelexpo-americas.com.
Show hours are 9am to 5pm, apart from the last day when it closes at 4pm.
beverages, wine (separate because of sheer size and variety), dairy, personal care, proteins (meat etc.), general FMCG, pharmaceutical/healthcare, chemicals, fertilisers, pet foods and others.
Costs and conference
The label converting sector is process agnostic and often combines several print disciplines. Naturally, digital will be prominent in Chicago since it accomodates micro and short runs with variable content so well. Nevertheless, visitors to Labelexpo Americas will witness label production using flexography, gravure, offset, digital inkjet, digital toner and liquid toner, screen process and ‘Hybrid’thermal.presses may feature several of these processes in one line – plus there are sure to be a few surprises in store also.
There is no doubt that labels and allied converting technologies are ‘on a roll’.
“After the Labelexpo show ends at 5pm, networking can continue across the street at the entertainment district; where you can find a wide variety of restaurants, nightlife, comedy club, bowling, movie theatre, concert venue and much more. There is even a casino just a few blocks away. Rosemont really does have everything you need.”
The V12 is also able to print up to 130,000 linear metres a day with a single operator and can print at 1600dpi, at maximum speed.
Technical methods are diverse and include: in-mold labels, shrink sleeves and linerless, self-adhesive (permanent and removable), wet gum, multi-part, wash-off, tie-on tags, pouch converting and the ever-increasing array of embellishments such as hot/cold foiling, powder metallics, high-build spot varnishes, tactile or haptic effects, holograms, screen printed effects, multilayer die-cutting, laser die-cutting, lam/ de-lam reverse print – and combinations of all these.
HP will host its first showing of its new V12 narrow web press at Labelexpo Americas, which it previewed at PacPrint
LABELEXPO AMERICAS
The Xeikon presentation on inkjet coating and varnishing will be given by Filip Weymans, vice-president marketing, digital solutions for Xeikon. Since moving into inkjet digital label presses with the Panther series, Xeikon has enabled ‘haptic white’ for embellished four-colour printing on highbuilt Needlesswhite.to say, sustainability will be a major theme – waste materials printed/ converted at the show will be collected and processed by Convergen, into fuel pellets, which can substitute for coal but with a lower carbon and emmissions impact.
2022, after which the cost is US$80. An early bird rate of US$396 is available for a single day conference pass and US$636 for both days if booked before 28 August. The Masterclasses cost US$700 each. Members of the Flexographic Technical Association receive a 20 per cent discount.
This converting technology is also complemented by marking, encoding and increasingly, ‘smart labels’ with QR or GS2 codes that link to detailed information on contents, sustainability, advice, marketing, recipes or anything you want in the IoT.

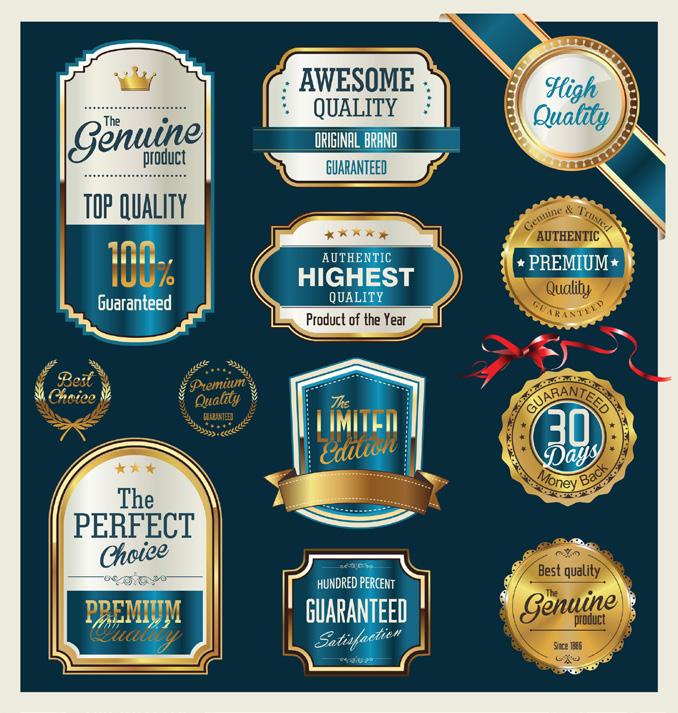
REACH & BS5609HEAVYCOMPLIANTSVHCMETALFREEVOCFREESECTION 3 COMPLIANT For more information, please visit durst-group.com/label Industrial scalability 330 / 420 / 510 m m print width Jumbo winders Flexo-likeCompetitiveproductivityinkpricingLowinkconsumptionPrint quality 1200 x 1200 dpi @ 2 pl Up to 95 % P antone coverage BEST IN CLASS COMPETITIVE EDGE SCALABILITY TAU RSCi INNOVATES YOUR BUSINESS
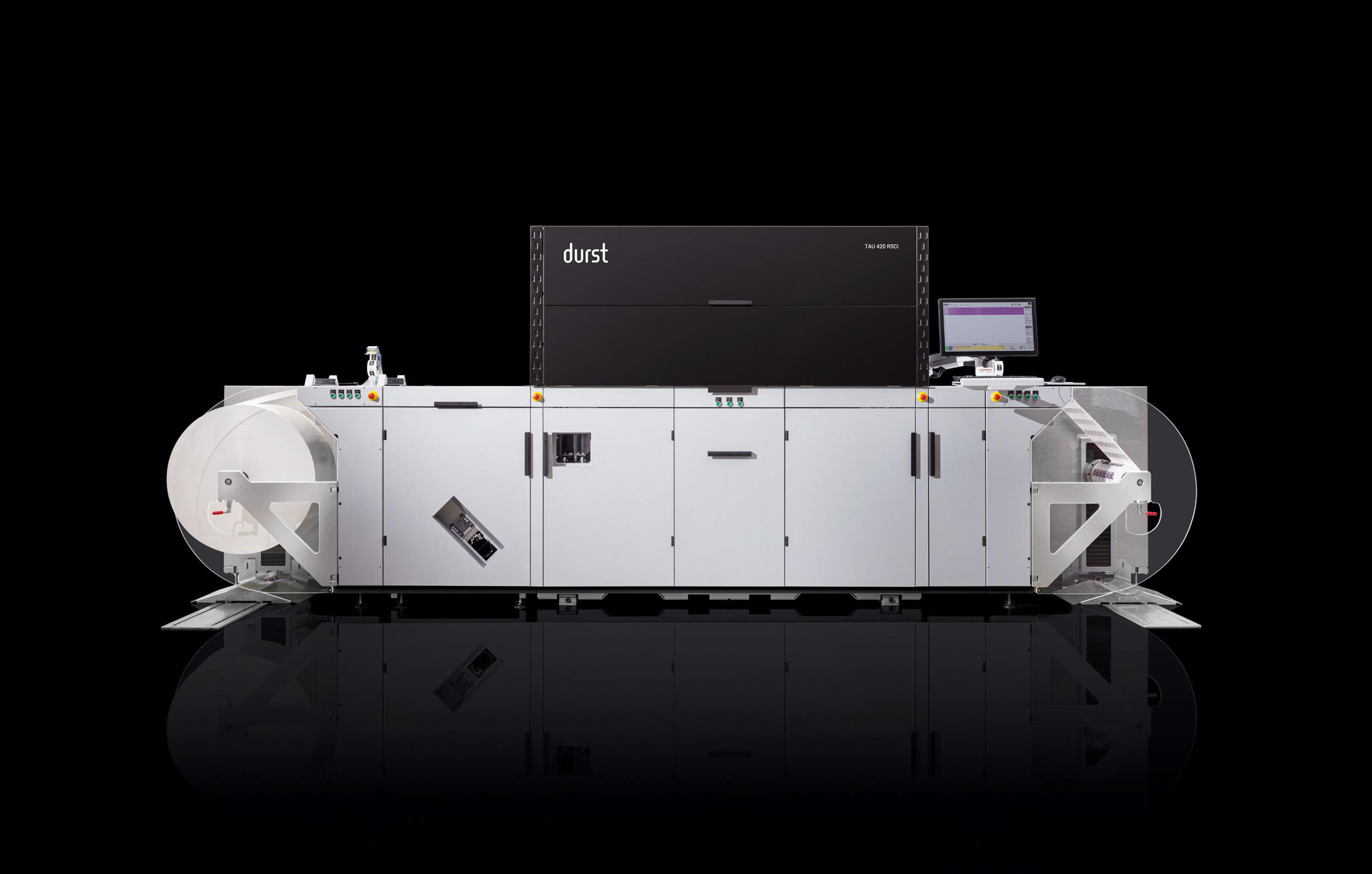
As brand owners continue to convert film-based packaging to paper, TITON can be employed to print many types of flexible packaging for food products. It can be used for papers that are coated on one side for bags, pouches and sachets, or on both sides for wrappers such as baked goods, confectionery, sugar, flour, herbs and spices, and coffee and tea.
In addition, varnishing and lamination require additional setup time and create more waste in the process. Furthermore, water-based varnishes used to achieve food safety require a significant amount of maintenance, which eats into productive uptime. Lamination can also negatively affect the recyclability of the packaging.
D uring Xeikon Café, in April this year, Xeikon revealed a new toner technology that offers the best of both worlds for food applications: food compliance and durability. This new TITON technology opens up new areas of applications for digital print manufacturing.
TITON toner also impresses by the excellent resistance to scuffing and scratching, water, sunlight, high temperatures and a large set of liquid chemicals, without any type of protective layers such as varnishing or lamination. A substantial feature is the ability to withstand heat sealing temperatures of up to 220-260°C, which is crucial to maintaining the pack’s integrity and protecting the product. This solution aligns with Xeikon’s broader strategy of providing complete digital printing solutions for package printing –workflow, presses, toners and substrates.
• Silver and gold toners: Within its Creative Colours range, Xeikon recently introduced metallic toners such as silver and gold. Traditionally, these colours are added by label converters via conventional processes, such as flexo and hot foiling, resulting in added production complexity and costs. Adding these metallic toners during the regular printing process in the extra printing station works very well for many applications and dramatically increases productivity.
As it is also completely odourless and tasteless, it will not affect the customer experience when the product is consumed. These key characteristics make TITON toner suitable for a broad range of applications with indirect and direct food contact.
Allowing brand owners to move to recyclable paper-based packaging puts TITON technology in a unique position in the digital printing landscape, and it gives printers the opportunity to expand their capabilities into applications that could not previously be addressed with digital, complementing their conventional flexo presses.
“Our Cheetah technology changed the game a few years back as it was the first food-safe toner in the market. But the tricky part was still serving label applications requiring heat resistance such as the process of shaping the package. As such, in 2022, Xeikon introduced the heat-resistant and food-safe toner TITON. Adding extra capabilities to the successful 508mm (20 inches) wide machine, with the new toner technology, allows converters to broaden their reach and enter new market segments.”
Find out more information about Xeikon’s new TITON technology and its other toners
Other highlights at the Xeikon exhibit during this year’s Labelexpo show will include:
• Haptic printing: the unique combination of the Xeikon X-800 workflow and the PantherCure UV ink that can generate a tactile layer, responsible for a so-called “haptic effect” in print. Printers can easily create designer labels with enhanced tactility, textures and a luxury feel. Xeikon’s new haptic printing process not only boosts and expands the range of possible applications for high-end label markets, it helps make significant time savings by avoiding any modifications to the prepress files. Tactile effects on labels are greatly appreciated by the beer, beverage, food, and health and beauty markets.
https://xeikon.com/en/contacthere:
LABELEXPO AMERICAS
TITON is a toner suitable for a broad range of applications
www.propack.pro32 ProPack.pro August 2022
“For label printing applications, Xeikon promotes two technologies: UV inkjet (aka Panther) which is the best choice for durable health and beauty labels, or drytoner technology (aka Cheetah) for highquality labels such as wine & spirits and all types of food applications,” Xeikon labels and packaging marketing and business development director Filip Weymans said.
TITON is a new toner formulation offering all the benefits of UV inks without the disadvantages. It builds on the core value of Xeikon dry toner technology which, due to the absence of any liquid (mobile) components, is a food-safe technology in the digital landscape, even with only paper as the main functional barrier.
“TITON toner is the only digital solution that can address this market without the time and cost implications of further surface processes, thereby improving speed to market, profitability, and productivity,” Weymans said.
The first digital press model to run TITON technology is the Xeikon CX500t, a new member of the CHEETAH series.
For those unable to make it to Labelexpo this year but want some TITON print samples mailed to you, get in contact with Xeikon’s experts
All about toner and inks for Xeikon at Labelexpo Americas
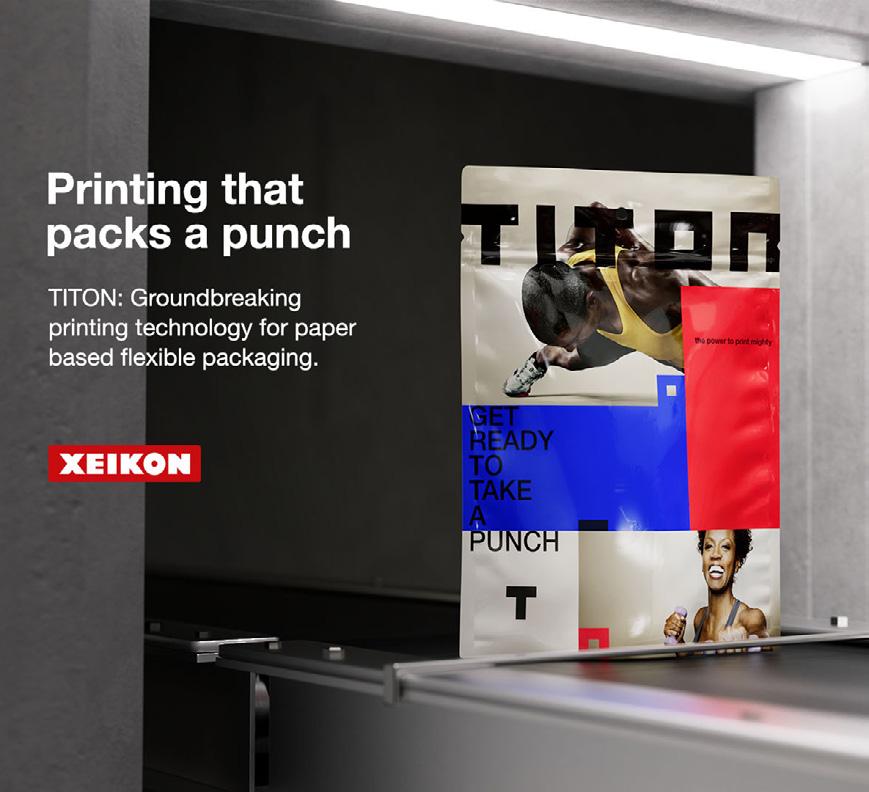
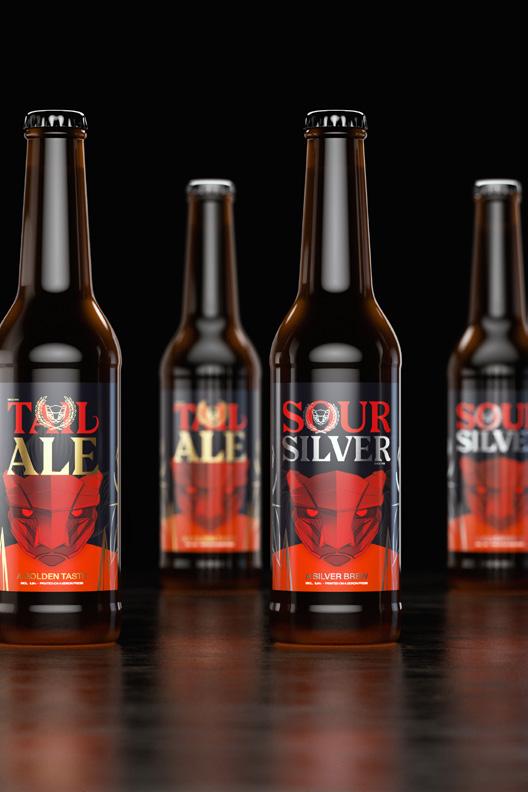
STAY ON TOP of your game in label printing S | Entry level Xeikon PX2200 4 or 5 50m/mincolors|164 ft/min Up to 220mm / 8.7’ S | Entry level Xeikon CX30 20m/minNarrow-web|65 ft/min Up to 330mm / 13’ M | Entry level Xeikon PX3300 4 or 5 50m/mincolors|164 ft/min Up to 350mm / 13.8’ M | Entry level Xeikon CX50 20m/minWide-web| 65 ft/min Up to 520mm / 20.47’ L | XeikonHigh-endPX3300 4 or 5 colors - inline finishing 50m/min | 164 ft/min Up to 350mm / 13.8’ L | XeikonHigh-endCX300 30m/minNarrow-web|98 ft/min Up to 330mm / 13’ XL | Flagship speed Xeikon PX30000 6 or 7 75m/mincolors|246 ft/min Up to 340mm / 13.4’ XL | Flagship speed Xeikon CX500 30m/minWide-web| 98 ft/min Up to 520mm / 20.47’ With Panther UV Inkjet Technology And Cheetah Dry Toner Technology
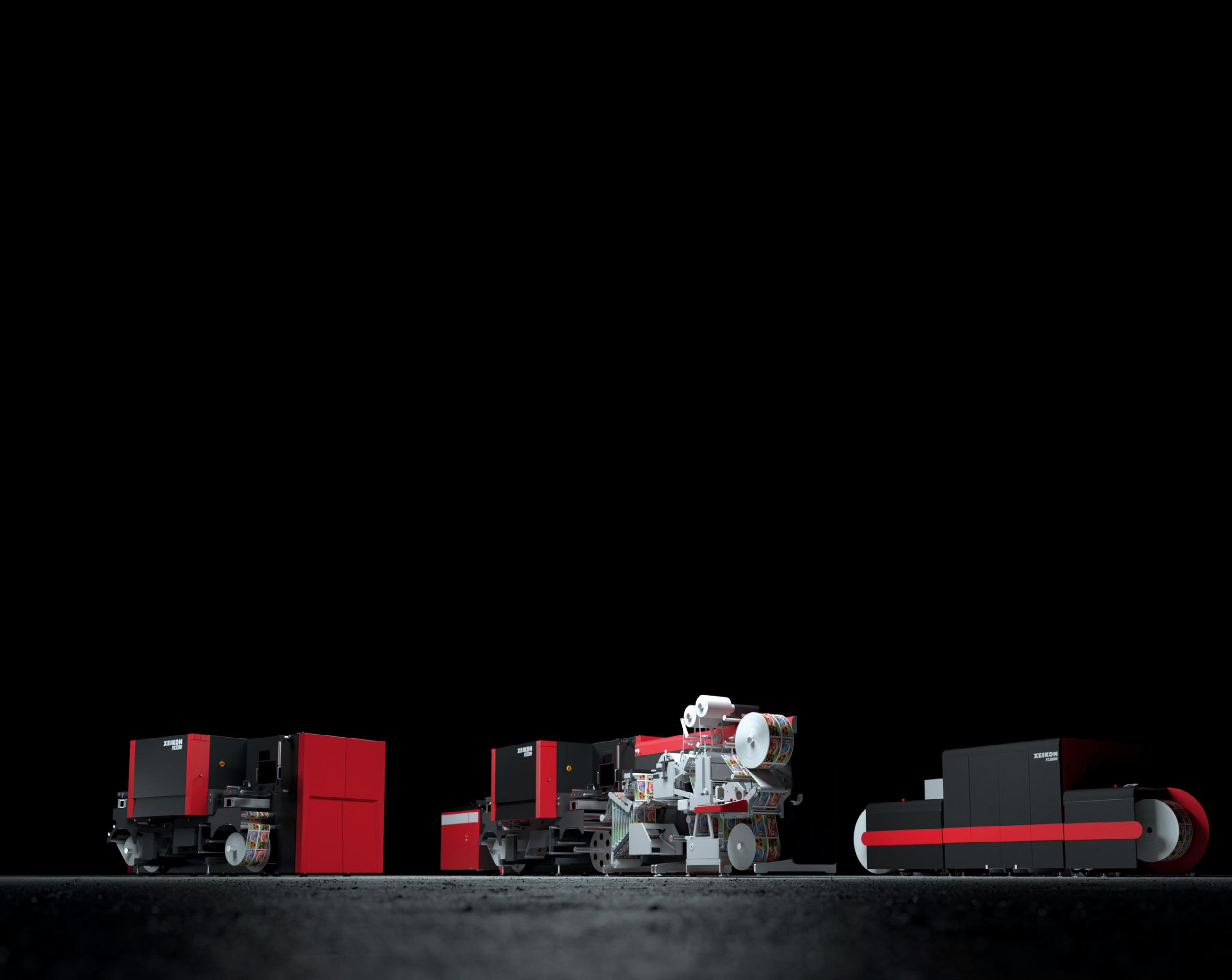
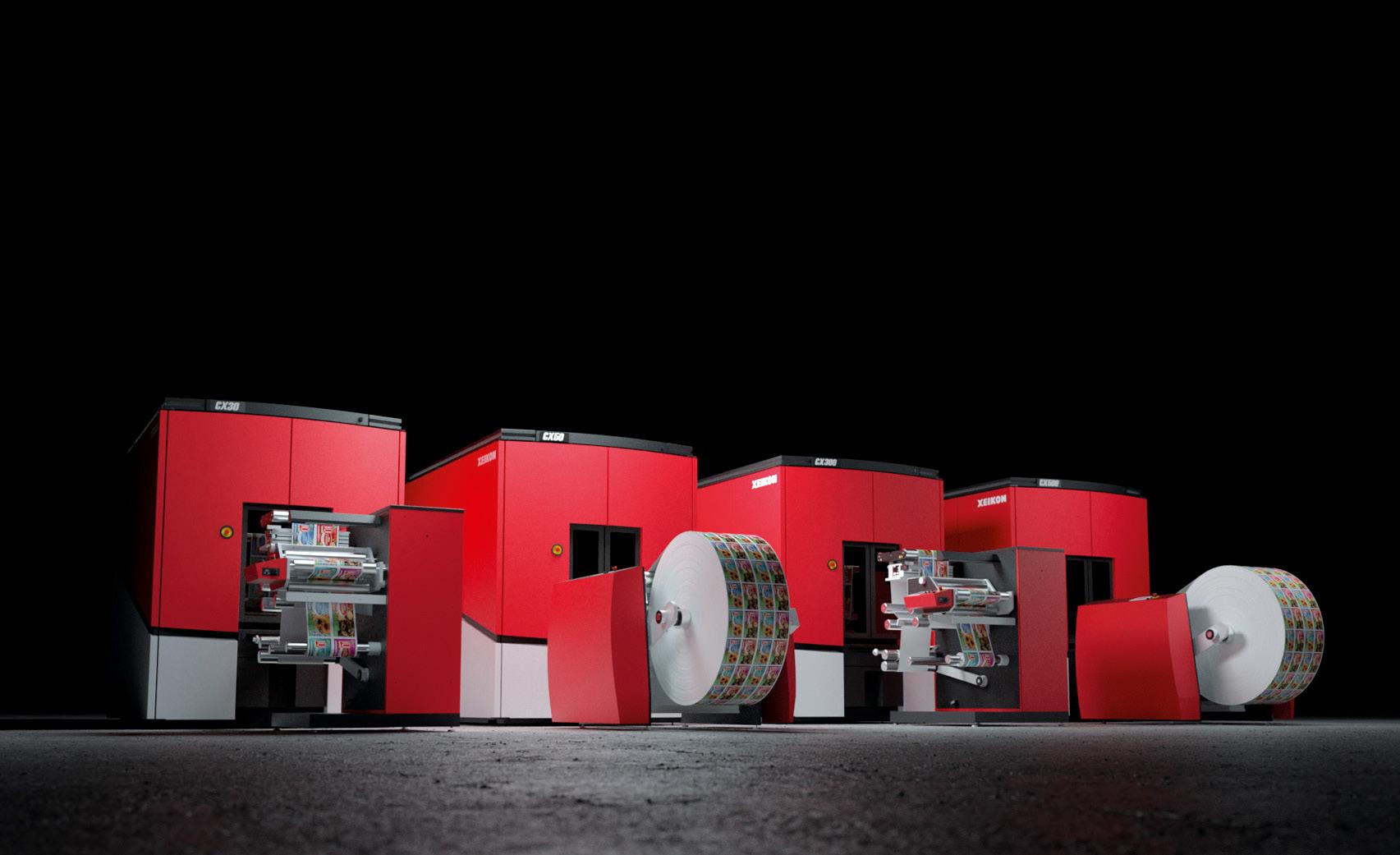
Upcoming Industry Events Labelexpo Americas September 13-15, 2022 Chicago, labelexpo-americas.comUS Modern Manufacturing Expo September 20-21, 2022 Sydney, modernmanufacturingexpo.comAustralia Foodtech Packtech 2022 September 20-22, 2022 Auckland, New foodtechpacktech.co.nzZealand Pack Expo International October 23-26, 2022 Chicago, packexpointernational.comUS Waste Expo Australia October 26-27, 2022 Melbourne, wasteexpoaustralia.com.auAustralia AIPIA World Congress November 14, 2022 Amsterdam, aipia.info/congress-exhibition.phpNetherlands Labelexpo Southeast Asia 2023 February 9-11, 2023 Bangkok, labelexpo-seasia.comThailand Label & Packaging Expo May 3-5, 2023 Sydney, visualimpact.org.auAustralia interpack 2023 May 4-10, interpack.comDüsseldorf,2023Germany Labelexpo Europe 2023 September 11-14, 2023 Brussels, labelexpo-europe.comBelgium Got an event? Send an email to hosman@intermedia.com.au with all the details and we will put your event on the page. ROBOTICSADVANCED HIGH QUALITY ROBOTS AT A CHEAPER PRICE. • Utilised around the world. • Backed by complete Australia wide support. www.advancedrobotics.com.au 03 87878778 Concept - Design - Turnkey - Installation - Service PACK DIARY
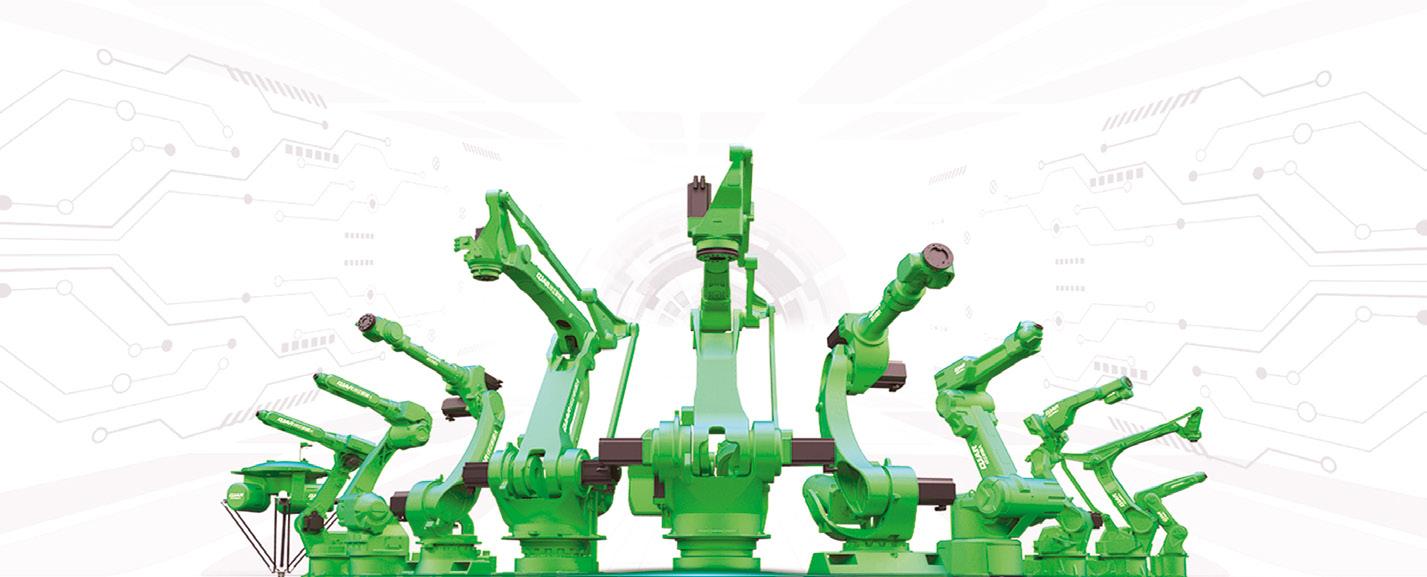
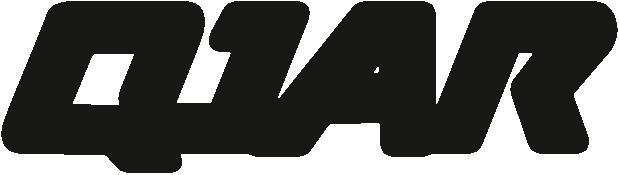
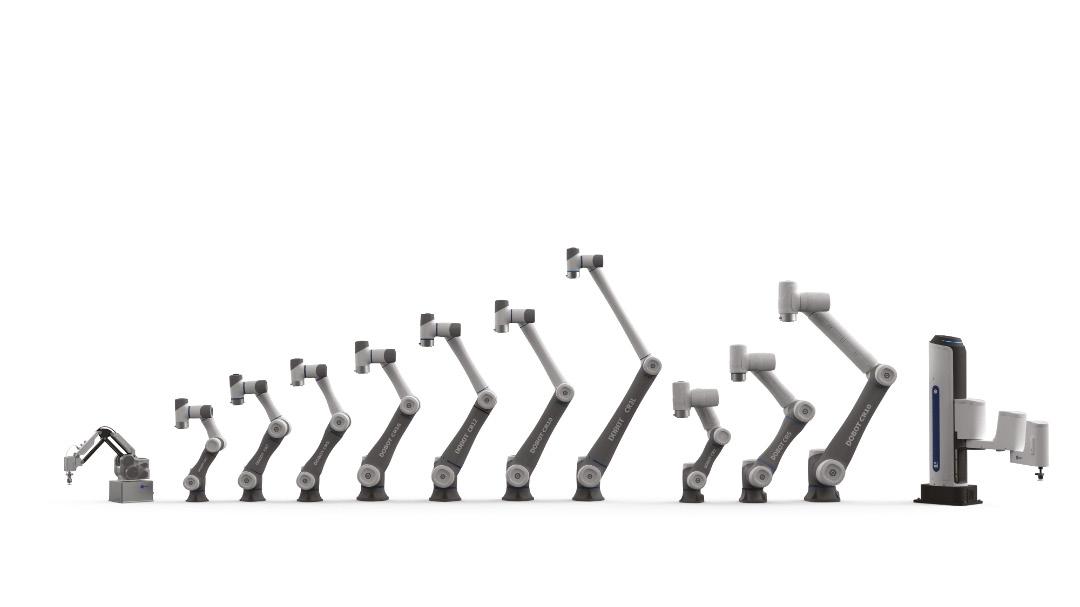
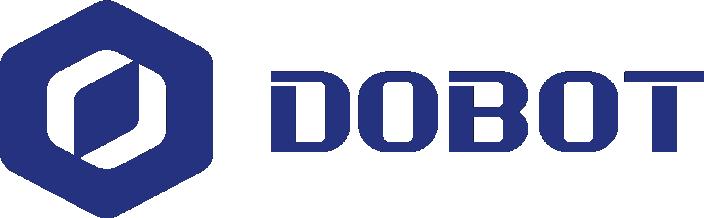

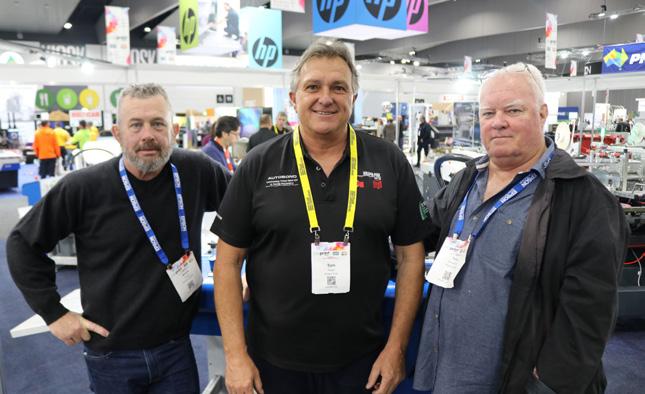
Graffica Pty Ltd PACKAGING AND DISPLAY EQUIPMENTKOLBUSAUTOBOX The original and leading complete custom box machine manufactured in Germany and the UK, since 1979 with 60 plus units installed in ANZ. THE BOXER As demonstrated at PacPrint and sold to APC Innovate, AKL, NZ Box making digitalincorporatingsystemsinlineprinting LargeMULTI-NOVAformat, straight line crash-lock box gluer CENTURY LARGE FORMAT DIECUTTERS Leading large format diecutter in Australia Sizes 1050/1300/1450/1650/1850/2100Available: & 2300 Flute/Solid Fibre/Corflute/Polyprop etc Full & Semi auto; various feeding options With or without stripping AMEIDA CUTTING TABLES Fast, efficient with various tooling 2500mm x 1600mm unit with cut/crease and v-cut DATIENoptionsCUTTING MACHINE High speed, heavy duty, sizes from 115cm to 300cm Phone +61 477 200 854 I Email grafficapl@bigpond.com I Visit Us www.graffica.com.au

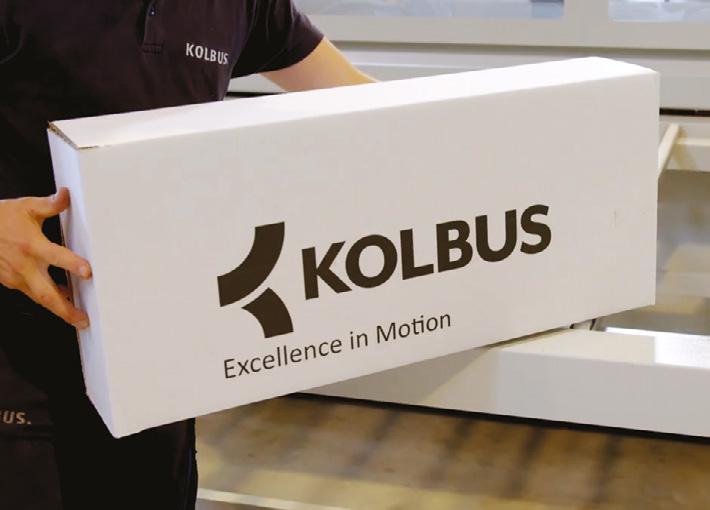
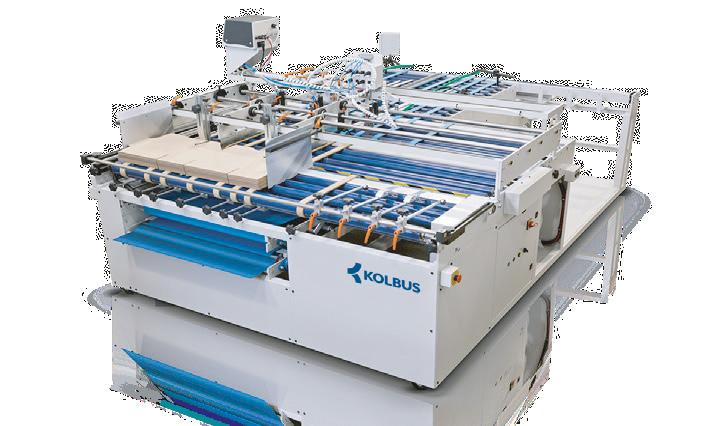
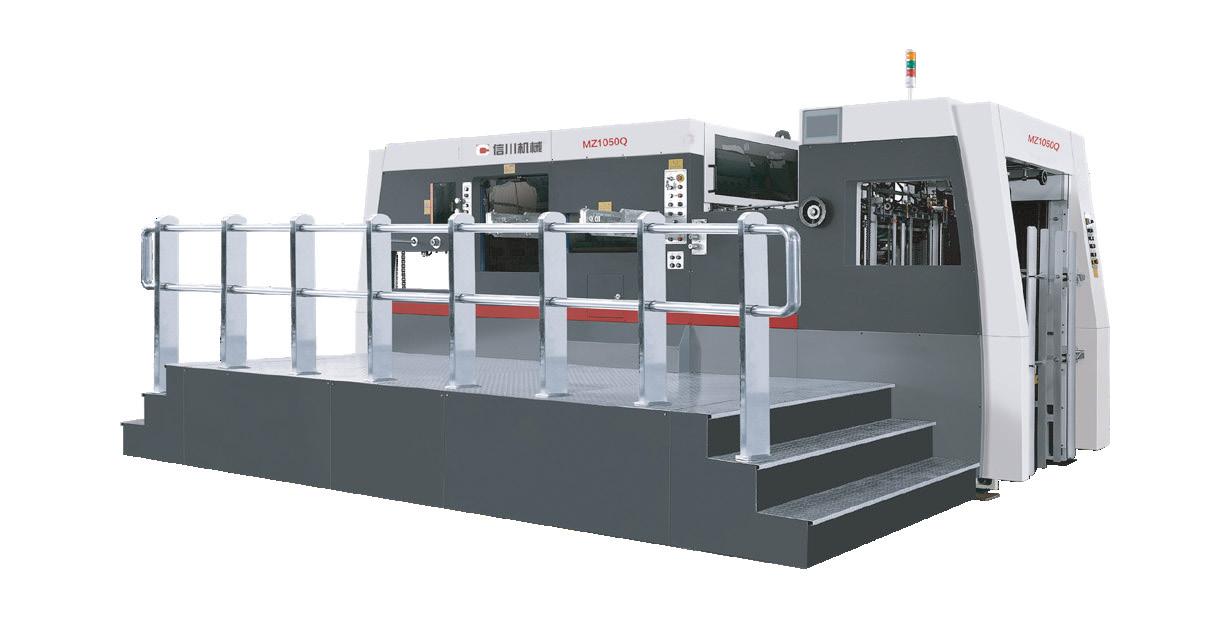
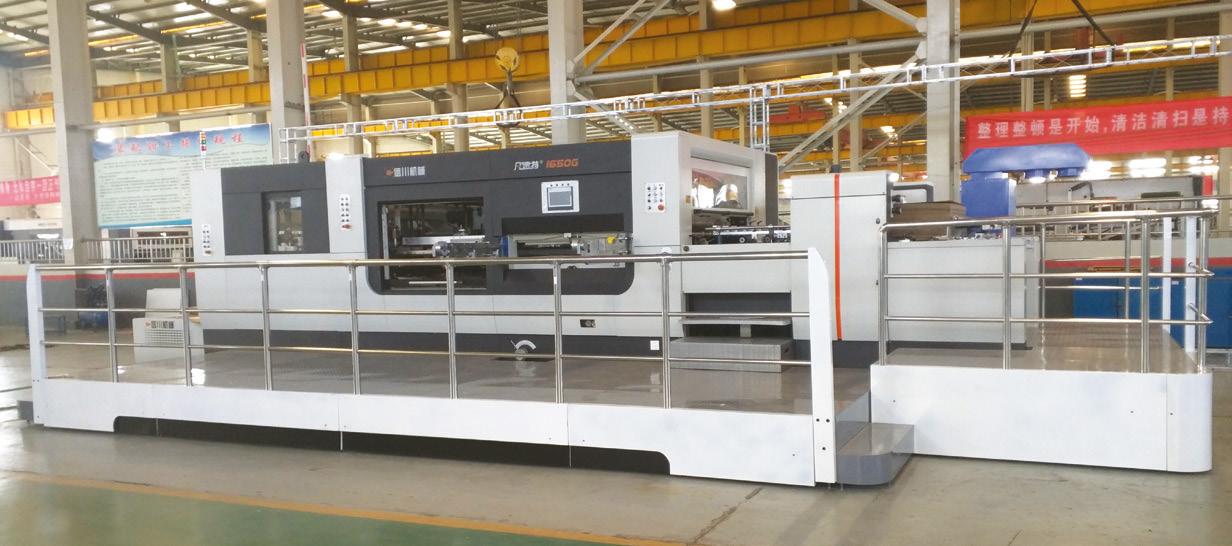
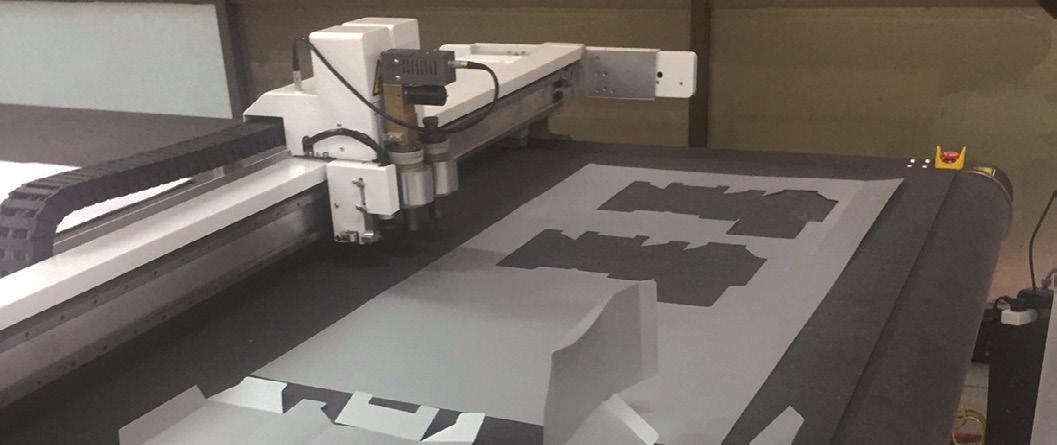
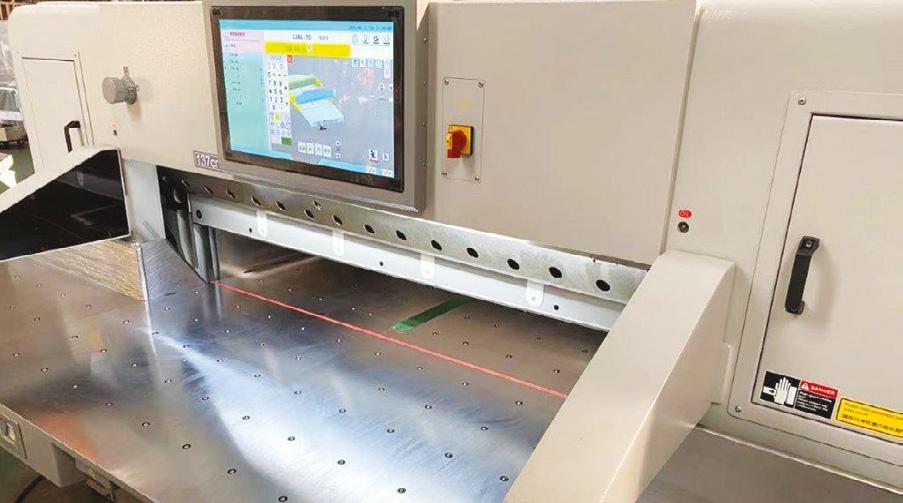

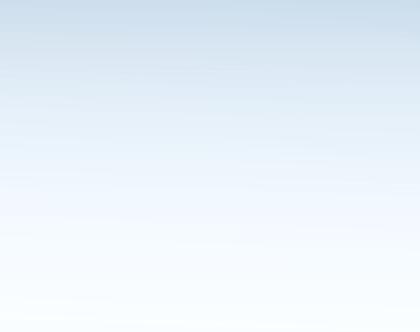
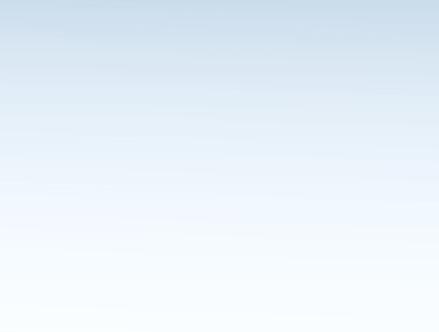
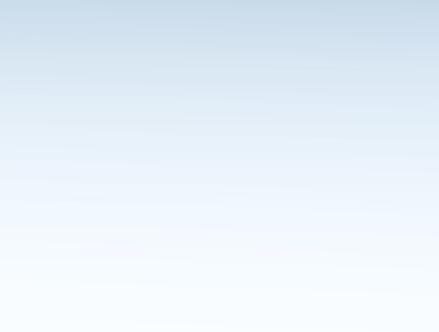

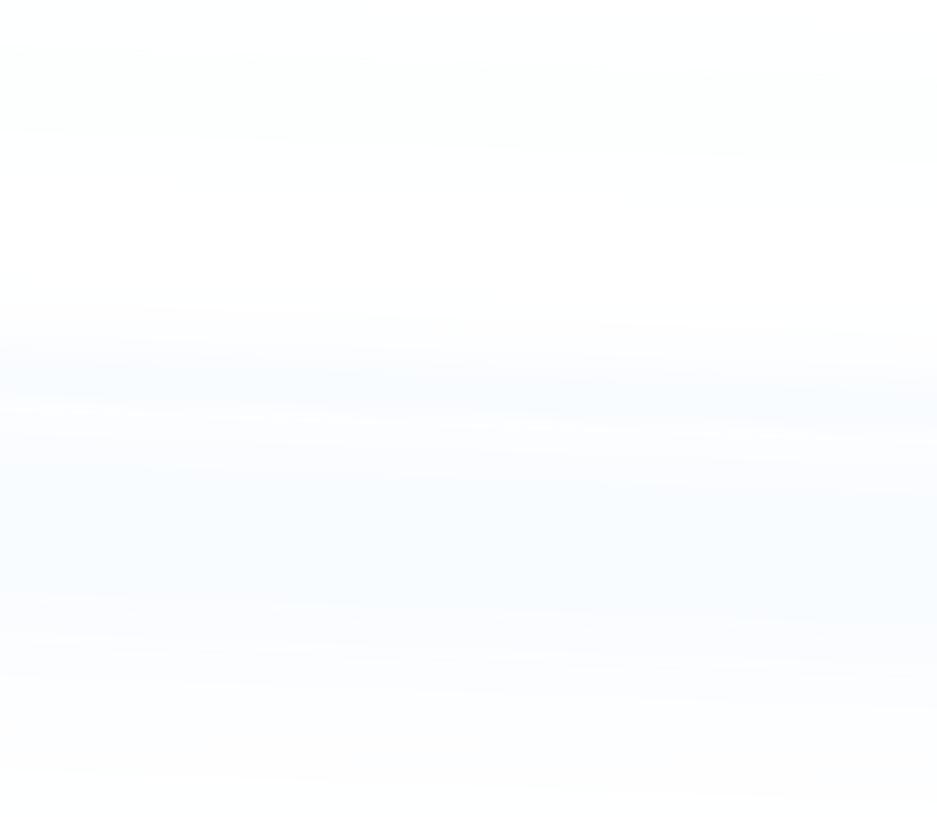
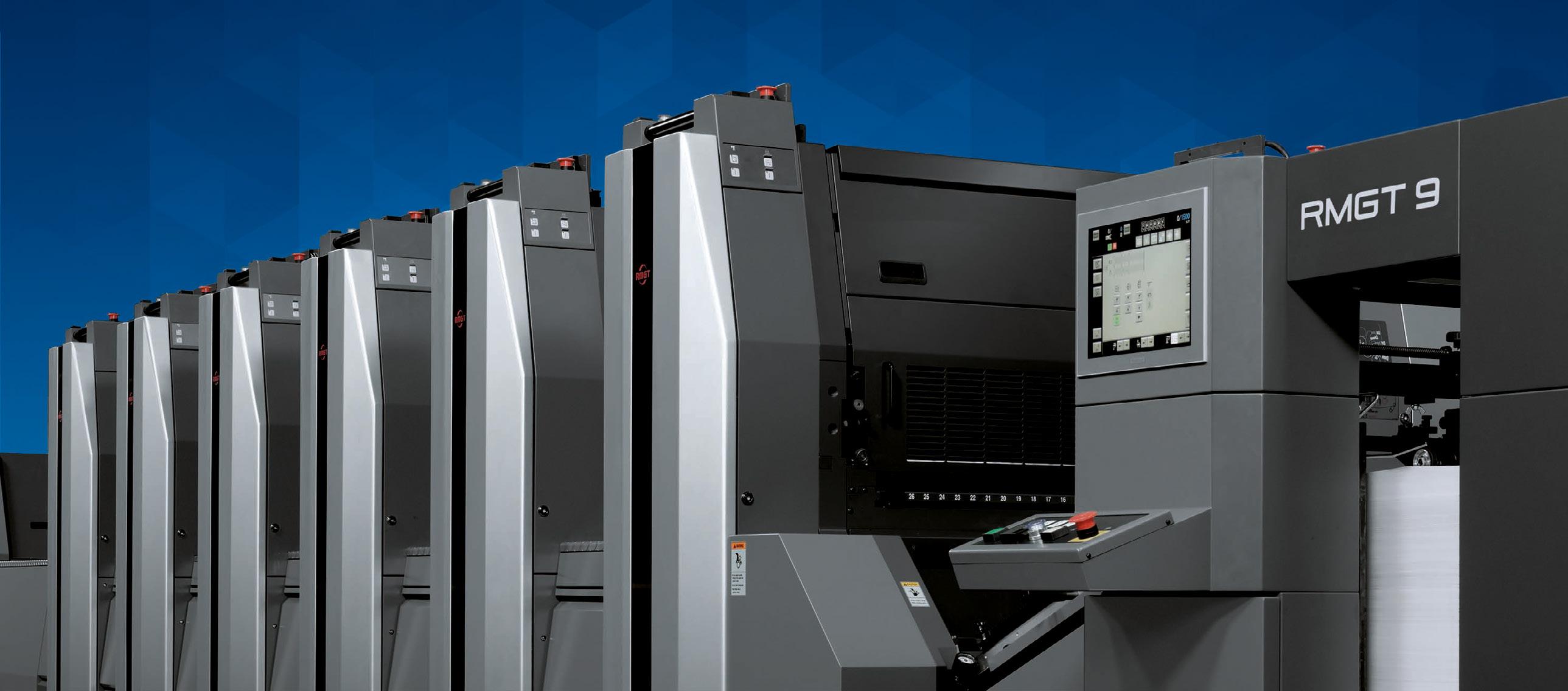

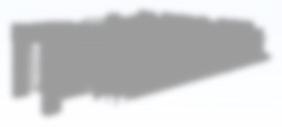
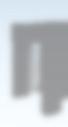
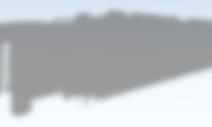
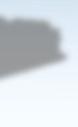
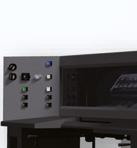

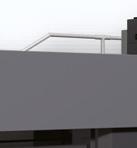
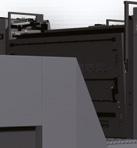
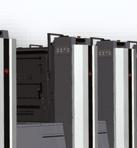
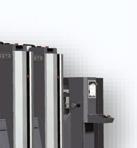
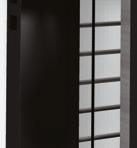
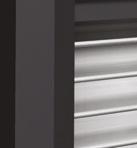
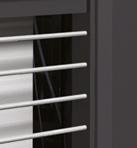
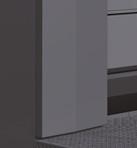
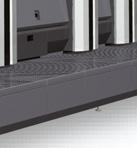
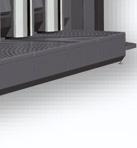

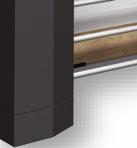

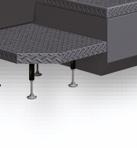
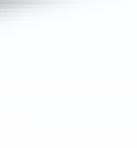
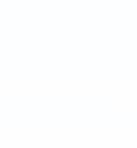
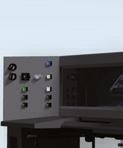

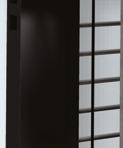
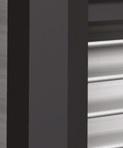
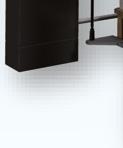
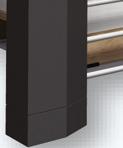

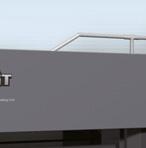
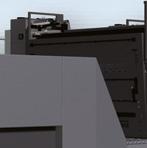
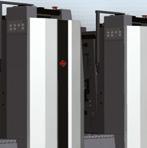
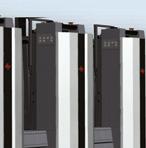

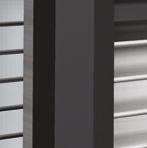
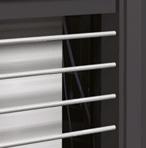


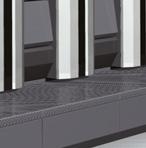



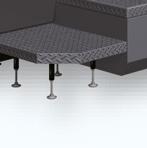

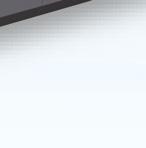
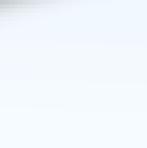
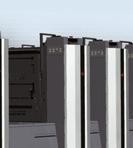
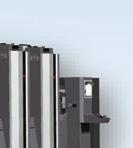


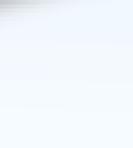

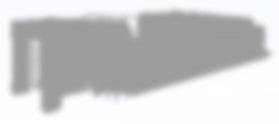
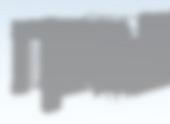
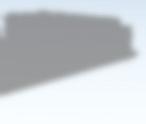
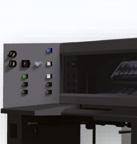
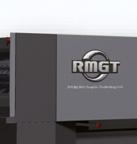
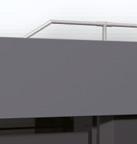
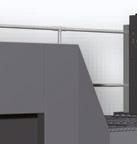
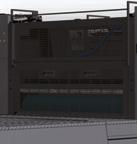
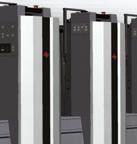
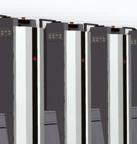
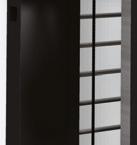
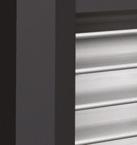
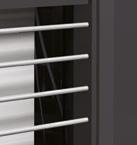
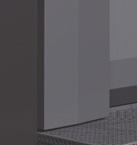
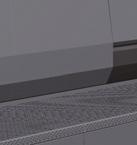
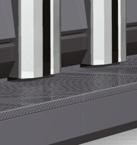
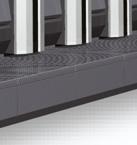

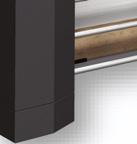

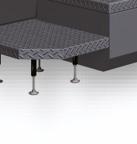
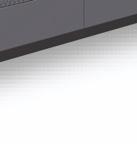

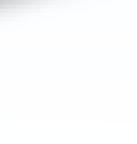
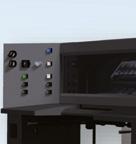
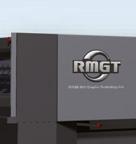

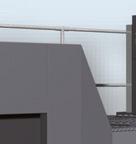

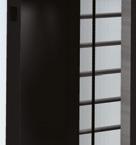
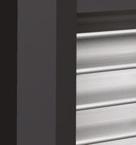
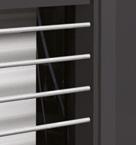
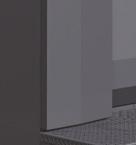
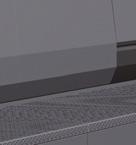

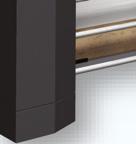
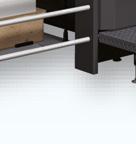
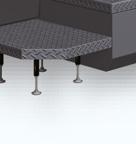

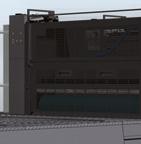
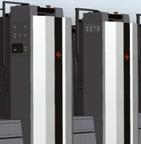
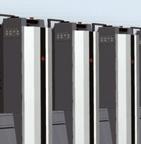
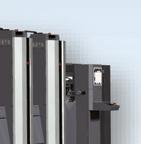
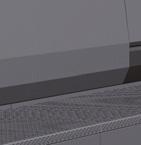
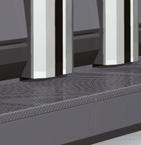



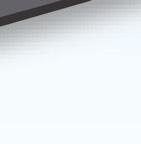
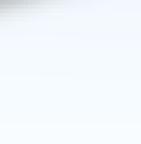
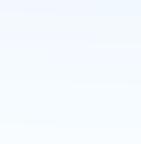
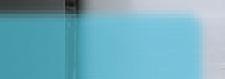



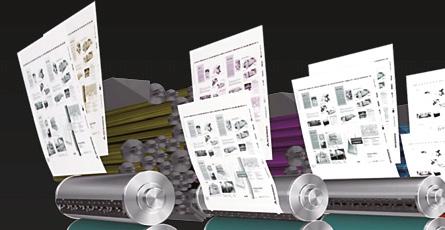
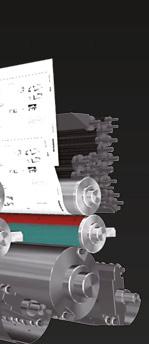
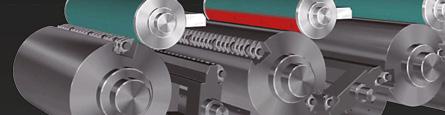


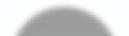
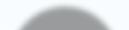

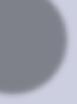
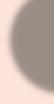
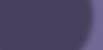

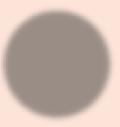


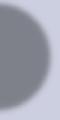



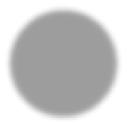
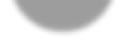
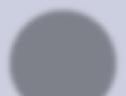

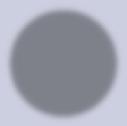

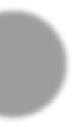
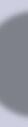
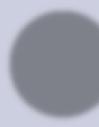

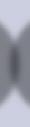



