Boosting business with Durst Tau
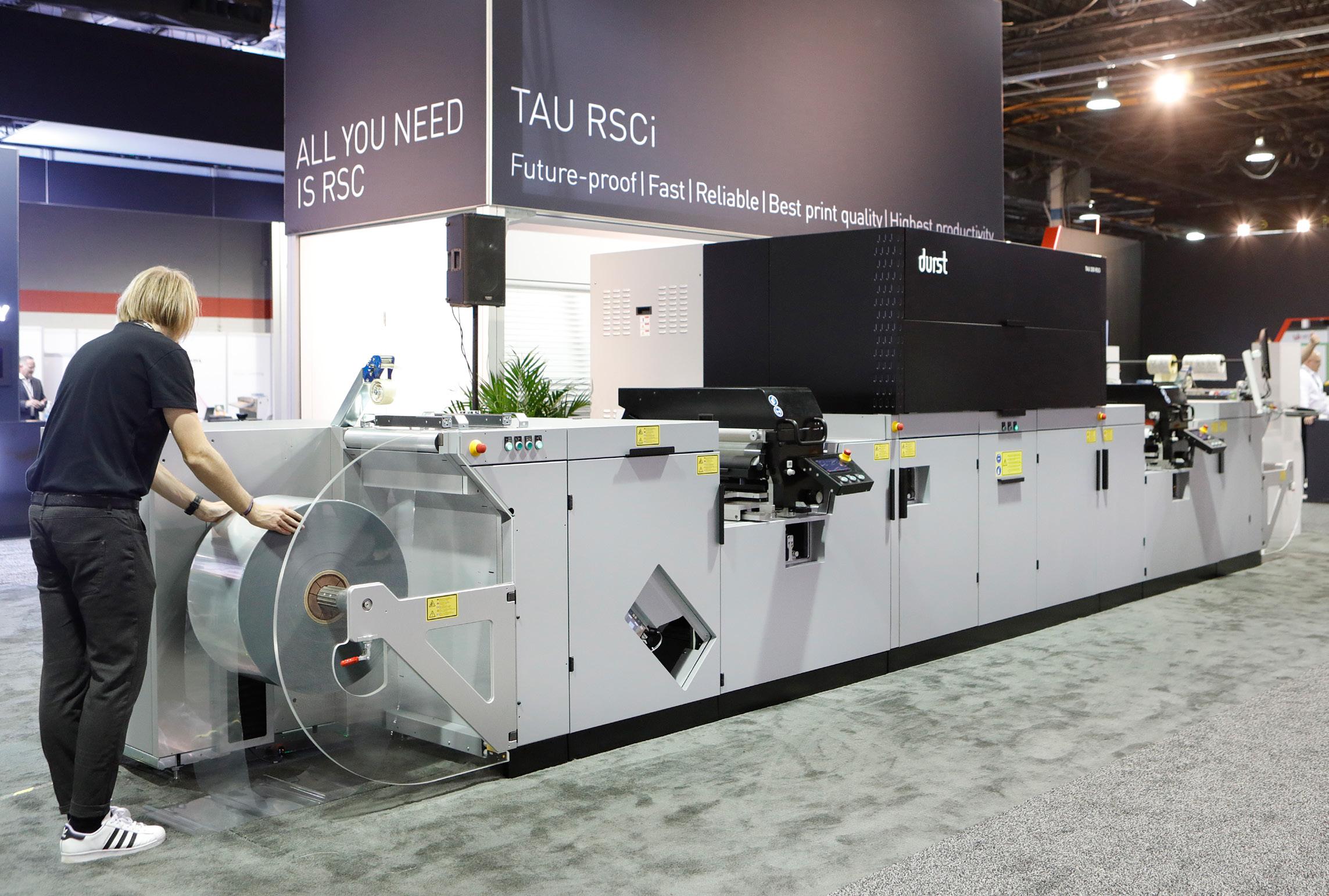
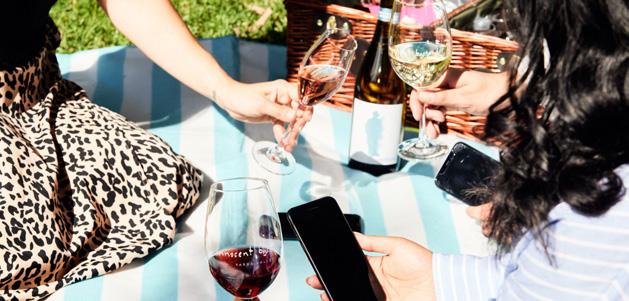
Getting
Please pass on our thanks to the team for the quality and service for both prints this week. Arrived on time and in good shape which is a pleasant change from some of the jobs we have received from other places.
Kevin
I just wanted to say thank you for rushing those 2 banners through for me, I really appreciate how quickly you made that happen, pretty amazing service.
Kelly
Thank you for having this order completed so promptly, the print quality is faultless and the blind shipping is very much appreciated
Donna
The postcards were delivered to them this morning and the client is impressed bordering on disbelief. Not sure exactly how you and the team did it all so fast but thank you.
Tom
Great job on the books Wade - client is stoked! Thanks again for suggesting the extra laminate - it really made a huge difference! Appreciate it!
James
Loving the magnetic boxes the velvet cards come in, a great way to present the card to the client.
Sarah
Labelexpo Americas took the spotlight on a global scale recently, following the postponement of the European show to September 2023.
The show promised to be the venue for international suppliers to connect with industry in person and showcase the latest and greatest solutions for labelling – and it didn’t fail to deliver.
Whether you’re choosing machinery or materials, it is vital you feel confident about your decisions. Labelexpo Americas had all these options together, in one place. Attendees had the chance to hear the noise of the machinery in operation, feel the textures of the substrates and see the print quality for themselves.
Labelexpo Americas 2022 was also the first time since the start of the global pandemic
that many suppliers had the chance to showcase their technology developments.
The team at ProPack.pro was thrilled to see the amount of working equipment that was running at the tradeshow.
Not only were there inkjet printing, digital printing and digital embellishment machinery, there were converting and finishing solutions, inks and coatings, security labels, anilox cleaning, LED curing, plate mounting, cold foil, sleeve films and even software products on show.
And among the many businesses that exhibited at the show were: HP, Flint Group, MPS, Avery Dennison, UPM Raflatac, Domino, Screen, Epson, Durst, AB Graphic, Esko, printIQ, Actega, Dantex, DuPont, Gallus, Hybrid Software, Konica Minolta, Karlville, and Kurz.
This issue of ProPack.pro provides a review of the technologies that were showcased at the tradeshow, delving into the key features of the solutions and the opportunities that they present the market with.
It also addresses the trend of Packvertising, looking at the ways some companies have used it to maximise their packaging designs and bring their brand propositions to life. After all, packaging is a powerful marketing and advertising tool that influences customers’ purchasing decisions.
With highlights from Avery Dennison’s official Melbourne office opening also included in this edition of the magazine, it’s one worth the read.
Hafizah Osman | Editor hosman@intermedia.com.au Ph: +61 431 466 140
Graffica makes profitable short-run packaging a reality P6
Graffica offers a range of solutions for a variety of packaging needs
A new and green beginning for Avery Dennison A/NZ P8-10
The company invited customers to the launch of its environmentally friendly and smart new Melbourne premises
Boosting business with Durst Tau RSC technology P12-14
Durst had its Tau RSCi and Tau 330 RSC E machines running at the recent Labelexpo Americas tradeshow to show attendees the potential of the presses
Labelexpo Americas: The latest technologies on show P16-20
Labelexpo Americas welcomed attendees from all over the globe to Chicago, putting on its best in terms of technology
Gallery: Labelexpo Americasthe people spotted at the trade show P22-23
Labelexpo Americas recently took place in Chicago, with thousands of people from all over the world flocking the halls of the event to view the latest technologies on offer. We spotted a few familiar faces in the crowd
The future unfolds with the HP Indigo 35K digital press P24
With customers increasingly looking for packaging boxes that go beyond basic and the trend toward boxes with digital features continuing to gain momentum, Currie Group and HP Indigo make digital folding cartons a reality
How can tech-enhanced labels benefit retailers in the wine industry? P26-27
The wine industry, like other industries, should accept smart labels and the progress it provides sooner rather than later, and challenge the concept of a divide between the ‘real world’ and the digital space
Driving solutions for a carbon neutral industry with seriousness P28-29
Heidelberg head of corporate sustainability Dr. Eva Boll explains what the industry needs to do to minimise the ecological footprint of packaging as well as other printed products
Labels and packaging innovations shine at Pride in Print P30-31
Amcor Flexibles, ABC Original Print, Kiwi Labels, Sealed Air and Logick Print all won packaging and labels awards at the event
Global plastic waste set to almost triple by 2060, says OECD P32
A new Global Plastics Outlook report calls for radical action to curb plastic waste
Pack Diary P34
A guide to the upcoming packaging industry events globally
THIS ISSUE SUPPORTED BY
a number of these. For higher volumes, we have a rotary slitter/creaser.”
Graffica has also announced a new flexo printer/die cutter: The Kolbus RD115S. This modular concept offers from one to eight print units plus a die cutting module for corrugated board in one highly automated inline system.
Targeting large format sheet sizes from 1060mm through to 2300mm, with many sizes between, Century die cutters are fast, safe, easy to operate and able to strip in-line. Neil says, “These machines have relatively low entry costs and have a fast return on investment. We offer numerous options in configuration, different stripping, feeder and delivery styles depending on your work load.
industry supplier Graffica has further cemented itself into the burgeoning packaging market with a range of solutions from box makers to die cutting systems.
Neil Southerington, director at Graffica, said, “As a one stop shop, we offer a range of solutions for anything from folding boxes, cartons and trays, through to shelf-ready and tertiary packaging.”
For companies moving into box making, Kolbus Autobox takes the struggle out of the process. In this expanding sector, Graffica has already installed 60 Kolbus units across Australia and New Zealand.
Graffica supplies four models of box makers from Kolbus Autobox. Neil said, “The Kolbus low cost, entry level box maker fits well in small to medium businesses that have the need for small volume production, around a few hundred a day.
“The next model up, the Kolbus Boxer, addresses the world’s fastest growing packaging market: short volume, just in time, on demand custom boxes in many styles. This includes Fefco 0401, the first choice of many display printers. We exhibited this machine at PacPrint and recently sold one to a leading Auckland company”.
The Kolbus Autobox 300 is a modular box making system. Units include multi-cut, flexo print, digital print, auto feeder, and auto stacker. Neil adds, “This flagship model is the high end solution that covers the biggest range of shipping boxes on the market today. It’s the market leader for custom boxes in Australia and New Zealand.
“While similar to the AB 300, the Autobox 310 also incorporates many features of the AB 300 with a multi-cut unit in one piece. It can be equipped with digital print or flexo, and two feeding and delivery systems.
Graffica also offers a comprehensive portfolio of solutions for associated packaging processes. Neil said, “The Kobus MultiNova gluing system is a fast setup multi-point gluing machine for quick and efficient gluing of straight line boxes, slotted boxes, die cut boxes, three-point crash-lock boxes. It has a small footprint as the compression section is located underneath the gluing section.
“The Kolbus Progluer is a popular straight line gluer with a small footprint that is ideal for boxes up to 3m wide.
“At PacPrint, we also showed the Kolbus Promelt hot melt gluer for short run, on demand or just in time packaging. We also have simple slitter solutions, which are ideal for full start up plants; we have sold
“The 1650 manual feed version is the most popular, easily capable of 3000 per hour plus on corrugated and corflute to 7.5mm with one operator. This makes old slow and dangerous clam shell cutters obsolete. It is the first choice for display and short and medium run packaging printers.
“One Century machine with a single operator will do the work of four clam shell cutters with four people and many cutting tables.
“We have already made an impact across Australia and New Zealand with 13 installations, which vary massively. The latest one at Wengers Cutting Formes in Sydney was a fully automatic 1060 raised with thin plate system, and triple action stripping, to replace a hand fed clam shell and two cylinders.
“A month before that, we installed a whopping 2300mm x 1550mm with triple action stripping and chase changer at Styleprint in Melbourne. We have also placed two fully automatic machines, 1450mm size, in Auckland and Melbourne, as well as an 1850mm semi-automatic machine in Melbourne.”
The company also supplies Century’s partner in folding box gluers. The Rollem range offers motorised carriage pre-set, or full auto-set, straight line crash lock plus four/six corner hot and cold glue, carton board and corrugated.
AWelcome to Country, product demonstrations, plant tours and lots of industry camaraderie have marked the opening of Avery Dennison’s dynamic new Melbourne warehouse.
Avery Dennison A/NZ used to have a facility in Tottenham, in Victoria, some years ago, with a manufacturing site in Adelaide. The company then closed its Tottenham manufacturing facility and only had manufacturing in Adelaide in 2016.
Shortly after, it shut the doors of its Adelaide facility, but retained its head office in Oakleigh South, near Melbourne.
With this new facility, Avery Dennison gets new offices and a distribution centre at Moorabbin in Melbourne’s south-east, providing a much larger facility and space to showcase eye-grabbing wall graphics and window films.
Avery Dennison said the new building reflects its core values of sustainability and its goal of carbon neutrality by 2050. The new building has features designed to reduce CO 2 emissions, conserve water and produce better air quality.
At the September 15 launch, event host Amy Simpson, marketing manager at
Avery Dennison A/NZ, reflected, “One thing the past few years has taught us is to take the opportunity to celebrate what you can, when you can. So today we are here to celebrate with you in person the opening of our new distribution centre.”
Avery Dennison A/NZ labels, packaging and materials commercial manager Cath Cornaggia said the new warehouse has allowed the business to have a larger facility to organise itself more safely and efficiently.
“We had been in our old premises for a while, and our lease there ran out. So, this presented us with a wonderful opportunity to look for a bigger space to service our customers,” she said.
“This building does a lot in terms of sustainability, collaboration, as well as diversity and inclusion.
“We have a gym, a quiet space for prayers or breastfeeding and the like, to foster the different needs of our team and make sure that we give them valuable space to work, which in turn, helps us with staff retention. Avery Dennison has been certified as a great place to work three years in a row, so having spaces like these is necessary for our future.
“By creating a positive workspace for our team, we hope to cultivate meaningful and valued interactions with our customers. The design of this facility has great environmental credentials, and we’re able to showcase to our customers our fabulous wall graphics and films. The workspaces enable us to foster more collaboration, as well as drive efficiency and innovation, that will be necessary to participate successfully in reimagined value chains.”
She paid tribute to Avery Dennison’s site relocation committee, which masterminded the move from Oakleigh South.
Cornaggia said the new facility has stateof-the-art environmental safeguards. She pointed out the plant’s 152-kilowatt solar power system capable of fulfilling 50 per cent its energy requirements, saving an estimated 20 tonnes of CO 2 emissions every month.
“Our new building will help Avery Dennison meet our 2030 sustainability goals of conserving water and reducing carbon emissions by 70 per cent,” she said.
“The building also features rainwater harvesting tanks for water reuse in our toilets and landscaping, a catch-
According to Cornaggia, this new facility presents an opportunity for the various Avery Dennison business units to come together and collaborate on new solutions.
“About four years ago, we introduced RFID into our label and packaging business. We hadn’t seen a place for the physical label to match with the digital label. But now, RFID and digital solutions will be part of our future. This facility marks the collaboration of teams and through that, we will endeavour to continue to stay ahead and invest in that technological space,” she said.
By becoming a more efficient and less wasteful business, it has helped us offset the rising costs of manufacturing.
“It is a physical space for us to reduce our environmental footprint and extend our ecological handprint as we lean into the regenerative economy.”
For Avery Dennison there are three key areas involved in improving efficiencies. The first is technological investment to build a successful regenerative economy, where a combination of material and digital solutions will enable a zero-waste future.
“The second is working with our extended value chain in new ways to support a digital supply chain that can trace raw materials, other industries’ waste or even recycled material to foster a circular economy,” Cornaggia said.
“And the last is investing in RFID and other digital technologies to bridge them all together. Our physical labels will always have a place, but the future is hybrid, where we enrich packaging by providing both physical and digital solutions that connect brands and consumers. To really drive this change, we need to empower the entire industry; we all need to be better aware of what it means to be part of a regenerative economy.
“In moving towards the circular economy, we’ve revamped our material and adhesive solutions. For example, we have recycled content in both our adhesives and face materials, and we have a liner recycling program named AD Circular, which takes our glassine liner and recycles that back into tissue paper, which itself is recyclable.”
Avery Dennison’s liner recycling programme is progressing strongly, Cornaggia reported, with more than 500 tonnes of liner already recycled.
“With the ambition of being carbon neutral by 2050, this is a building that all of us at Avery Dennison and its community can feel good about,” she said.
Cornaggia highlighted Avery Dennison’s launch of atma.io – its connected cloud product – which is an end-to-end platform capable of creating, assigning, and managing unique digital identities for every physical item in the world.
This technology provides businesses unparalleled supply-chain transparency by tracking, storing and managing all the events associated with each individual product from source to consumer and beyond. Circularity of product life enables re-commerce, product authentication and traceability.
“We’re very excited to launch the new season’s release of atma.io this month. We’re very strong in RFID labels and have played in the apparel space for a long time. That has now expanded into other areas such as food and beverage, pharmaceuticals, and aviation,” she said.
“Becoming digitally enabled is a bit of a journey but we expect to see change here like what Walmart has done in the US, where every single product that it has is RFID enabled. Avery Dennison has played a part in that project. Low-cost digital triggers are available today and sooner rather than later, and we believe they will be ubiquitous on every piece of packaging.”
Cornaggia also mentioned that Avery Dennison’s pioneering accelerator programme for the label industry, AD Stretch, is partnering with start-up innovators to solve key challenges and create opportunities within sustainability, customer experience and more efficient value chains.
Out of a pool of over 200 applicants, it has already announced the first five start-ups it will be collaborating with – including an Australian-based business, Cellr.
“This is an example of the kinds of things that we are doing to try and stay ahead of the curve. We need to be preparing ourselves for the future by working right at the cutting edge with those tech companies,” she said.
At the official opening, Avery Dennison A/NZ graphics business director, Jordan Leach, offered a sneak peek at new nonPVC products, including vehicle wraps, soon to be released commercially. He said Avery Dennison is continuing to drive more sustainable solutions, both in its products but also in its use.
Avery Dennison senior technical specialist Theo Kostarakis led customers on tours of the new site, which comprises 5,000 square metres of warehouse space and 1,200 square metres of office space, with around 70 staff.
Customers were treated to product demonstrations, particularly the latest technologies in vehicle wrapping, using products such as Avery Dennison SP1504 Easy Apply.
Imparting traditional significance to the event, Uncle Mick Edwards of the Bunurong Land Council gave a Wominjeka (Welcome) address, and his son, Uncle Eric Edwards performed Indigenous music.
Teresa Laing of Mildura Print won the launch event’s door prize, a $100 voucher for a Red Balloon experience, presented to her by Amy Simpson.
Durst had its Tau RSCi and Tau 330 RSC E machines running at the recent Labelexpo Americas tradeshow to show attendees the potential of the presses
Durst created its Tau RSC platform to offer the benchmark in productivity and flexibility. And to improve reliability, simplicity, speed and cost effectiveness so label converters can better meet changing market needs with digital technology, the company has been constantly updating the fleet.
Durst took to the recent Labelexpo Americas tradeshow in Chicago to showcase this highly successful and globally placed Tau RSC range, offering attendees a unique experience by having on display the Durst Ecosystem of printers and software, and providing visitors access to experienced industry experts.
Durst not only had on display the Durst Tau RSCi and its Durst Tau 330 RSC E machines but also had the presses running to show attendees the potential of the units.
“As the label market shows an unstoppable level of growth, Durst is committed to match that with innovation and investment. As such, Durst Oceania is pushing heavily into the labels and packaging sectors,” Durst Oceania managing director Matt Ashman said.
“We’ve significantly grown our label press installation base this year, and we’re going into more high-speed packaging
production. Oceania is a positive growth region, and Australia is a very vibrant, innovative and young market when it comes to labels and packaging.
“There are plenty of great businesses here and we just want to be a part of that upward trajectory.”
According to Durst, Tau single pass printing systems now have a market share of around 40 per cent of the UV inkjet market segment, with an installation base of more than 320 printing presses worldwide.
Designed for an industrial level of productivity, the Durst Tau RSCi offers the highest quality, in the most economical way. Available in printing widths of 330mm, 420mm or 510mm, the printer is designed to take over mid- to long-run jobs and is also able to produce short-run jobs.
The user-friendly design including jumbo winders and roll lifts allows fast roll changes and good accessibility to print heads, UV-lamps and transport rollers. The integrated large inspection table provides space for visual inspection. The Tau RSCi is equipped by default with a chill roller to guarantee maximum material and application flexibility.
“At the start of 2021, we finalised the beta of the RSCi – the industrial platform leveraging all benefits of the standard RSC but with print widths up to 510mm and printing speeds up to 100m/min, and optional inline flexo stations prior and after the printing unit,” Ashman said.
“The introduction of the Tau RSCi has generated a large amount of interest in the marketplace since it was launched in September 2020.”
Durst labels product manager Martin Leitner was at the Labelexpo Americas tradeshow, explaining to attendees about the capabilities of the company’s RSCi technology.
“Labelexpo Americas was a great event, with lots of people showing interest in our products. The RSCi printer that we had on the show floor was a 330mm-wide, sevencolour model – white, violet, orange and CMYK,” he said.
“The press shown had a print engine with the standard high-performance RSC technology – so we print at 1200 by 1200 dpi, two picolitres and up to 100m/min.
“We had our standard equipment with unwinder and Corona pre-treatment stations as well as a flexo station on the machine as we showed some new applications using
“Something new that we have launched on this press is a feature specially designed for customers that are printing heavily on transparent materials, such as personal care and beauty products. This feature allows customers to use two white stations, which we call double white, which increases white productivity.
“This allows the machine to print white and all the other colours at 80m/min. In addition, our high opacity white mode has been increased from 40m/min to 52m/ min for better productivity levels. That’s what our customers need.
“The printer almost does everything by itself including the maintenance and cleaning, so there is no need for the operator to constantly clean things like the print heads. Our machines are of solid construction, and ready for production.
“The configuration that we had on the show floor had another flexo station after the print station for shrink sleeves. IML and shrink sleeves generate a lot of interest, with IML not traditionally done on digital machines. But with the RSCi, this is now possible and done with quality and high productivity levels.
“This press, in this configuration, is made for heavy work. That matches production speeds of our customers as evidenced by the many global customers that have installed the machine.”
Businesses such as LabelPrint OÜ in Estonia and All4Labels Global Packaging Group in Germany have experienced the benefits of the Tau RSCi range.
All4Labels installed a Tau 510 RSCi at its Gebesee plant in mid-2020 and tested the press under real production conditions for a dedicated range of label and package printing applications.
Thanks to the positive performance of the beta machine, another machine has been installed in the same press room to further increase production capacity needs in the premises, followed by multiple installations in other All4Label plants across Europe.
At LabelPrint OÜ, the company has been using the Tau RSCi to actively develop digital print services to its client base.
“Some of our customers have installed three or four of these Durst Tau RSCi machines as these presses are workhorses and can keep up with heavy workloads. The technology, quality, and productivity of inkjet is now available with this machine,” Leitner added.
“In addition, Durst has invested and is continuing its investment in the knowledge of applications using the Tau RSCi as customers not only need a good machine but also the support from us to help them use the press for a range of applications.”
In addition, Durst showcased its standalone UV inkjet label press, the Durst Tau 330 RSC E at Labelexpo Americas. Designed to evolve with a business, the machine is fully upgradeable to grow with customers.
Similar in construction to the RSC E, the adaptation of the press includes the new Durst corporate design, with all wellknown features installed. These include the infeed section which has sensors, a double-sided web cleaner, a corona treatment feature and an insetter for reinsertion and double-sided printing.
The outfeed section is where the final curing takes place with two UV lamps around a chill roller and an operator inspection table with a camera for automatic nozzle compensation.
The printing unit centrepiece holds eight colours, including white and optional green, violet and orange, cyan, magenta, yellow and black. New added options such as the high-speed white function allows operators to print with all colours and white.
All colours have eight printheads which can print 80m/min, guaranteeing that future increased production capacity requirements are covered, at 1200 dpi resolution, offering superior print quality at all levels of investment.
“Durst had a second booth at Labelexpo Americas, showcasing the Durst Tau 330 RSC E. Durst has a complete range of presses in our portfolio, all with the same printing quality but only variations in the productivity,” Leitner said.
“The Durst Tau 330 RSC E is ideal for customers that want to start with inkjet or want to increase their digital capacity. For customers that print one to 1.5 shifts, and up to 50,000 or 60,000 square metres a month, this model is really their ideal press.
“The press that we had on the show floor was in a five-colour configuration – CMYK plus white, as well as several new features included. This press has been installed in more than 200 premises around the world and customers love it. They make labels with it, so what we wanted to do was improve on automation and provide them with a stable production press.
“So, the main new feature for this model is a Durst-developed camera system for
density alignment of the press – we want to ensure that all the prints have the same colour on them. We also use the camera system for offset and print head alignment.
“Humans have different perceptions of quality so with this camera system, that quality is now measurable. The camera system pairs with Durst’s software which ‘tells’ the technician when he installs the press how to reach the ideal result.
“Durst has automated and continues to automate our presses to offer very competitive solutions.”
All Durst printers come fully equipped with Durst Workflow and Durst Analytics software, and optional Durst Smart Shop software, enabling web-to-print solutions.
“Our software also includes the LinkSafe feature, which helps reduce ink costs on average of about 12 per cent. This makes it much more competitive, and our customers that have used this feature have provided us with feedback that it works much better than they expected.
“This feedback is great for us as it tells us that our customers are successful – and that’s our goal.”
Visitors to the Durst booth at Labelexpo Americas were also able to view the vast functionally of the company’s software and received demos on special features such as precise ink cost analysis, exact colour rendition, and high-speed ripping.
The Tau RSC platform printers can print on a large variety of substrates and the software solutions offered by Durst Workflow Label ensure an integrated workflow combined with secure handling of sensitive job data. Ease of use, intuitive and automated, the Durst Label Software tools are also included to help businesses organise their production workflow to be more efficient and cost effective.
Applications for the Tau RSC range include, but are not limited to, the beauty and care, food and beverages, and chemicals industries.
In beauty and care, the Tau RSC provides the highest opacity white, vivid colours and a screen-like feeling of the label prints. Patternware adds additional value, to further enhance the appearance on the shelf.
In food and beverage, abrasion resistance and temperature stability are key for these applications. Furthermore, it also enables labels to be produced in a vivid and strong manner, in compliance with general industry regulations and standards.
In chemicals, the Tau RSC UV ink provides excellent durability, resistance, and light fastness. Resistance has been proven, for example, with tests against gasoline or methylated spirit. Many Durst Tau RSC clients produce millions of labels for chemical applications such as oil bottles, fertilisers, detergents, hand sanitisers and many other industries.
Durst USA labels and packaging director Steve Lynn said, “We were excited to be back on the Labelexpo show floor, showing the strengths of our RSC portfolio with 1200 dpi inkjet technology. Durst equipment has a reputation for reliability, quality and speed – LabelExpo Americas 2022 allowed us to show those strengths to the entire label community. It was a great show, and Durst was proud to be there.
“It was certainly an exhilarating event for people to see how and why Durst keeps them printing.”
Labelexpo Americas welcomed attendees from all over the globe to Chicago, putting on its best in terms of technology and solutions
Machines on display included: ABG’s flagship Digicon Series 3 beverage specification, including Big Foot, Flat Bed Screen and even more retrofittable modules; ABG’s new SRI3 incorporating enhanced functionality and ease of use for operators, while being fully retrofittable; DigiLite; DigiLase with a new decal option for roll-to-roll, individual pieces and A4 sheets; Vectra ECTR – for efficiency in turret rewinders; and an RTS Sheeter.
Designed for any digital printing application, the Digicon Series 3 can be used roll-to-roll or roll-to-sheet.
Some of its key features include:
• Die plate loading and un-loading
• Fast Track Die Cutting – the world’s fastest semi-rotary die cutting system – able to run at 180 metres per minute and work in-line with the world’s fastest digital print engines
• Gap sensing and knife setting – to save time on set up and changeovers
• Big Foot 50-ton capacity hot foil and embossing module – with multiple foil feeding across and along the web – to create new effects and finishes that will give you a competitive advantage
• Flatbed screen printing module – to add value with relief varnishes or vibrant screen inks
• Crossover module – to create multilayered, novelty or promotional labels, digitally
Labelexpo Americas recently took place in Chicago, and ProPack.pro was in attendance to check out the latest of technologies on show and meet industry professionals face-to-face in one of the first global packaging events since the pandemic.
Many manufacturers and suppliers were at the event, which ran from 13 to 15 September at the Donald E. Stephens Convention Center in Rosemont, with representation from 86 countries. The last time the show took place was in 2018.
Print finishing specialist, A B Graphic International (ABG), took to the show to present new developments from its product portfolio. The company showcased more finishing machines than ever, demonstrating how it is constantly innovating to improve efficiencies and workflows for its customers.
• Lamination in register module – enables pre-printed web to be laminated to the main web in perfect register
• DigiJet – digital embellishment module to create high quality digital embellishments
ABG also had on show the first Actega Ecoleaf unit in North America – this was a stand-alone unit highlighting the machine’s innovative technology.
Members of Enprom, ABG’s latest acquisition were also available to talk about the latest additions to the ABG portfolio, including Non Stop Winding Technology and a range of shrink sleeve product. Staff from ABG’s A/NZ distributor Currie Group were at the show to educate attendees on these machines.
Actega, manufacturer of specialty coatings, inks, adhesives and sealing
Here’s a summary of some of the technologies that were on show:Currie Group’s Jon Murray, QLM’s Lindsay Nutley and Jesper Noisen, Currie Group’s Mark Daws and Simon Pugh, HP’s Craig Walmsley and Currie Group’s Wayne Quayle The first glimpse of the Indigo V12 Digital Press Heidelberg America’s Felix Mueller, Gallus’ Dario Urbinati and Helidelberg USA’s Dan Maurer ABG’s Mark Hyde with the Digicon Series 3 machine
compounds for the print and packaging industry, brought its latest ranges of product-enhancing inks and coatings to Labelexpo Americas.
The solutions showcased included a brand-new line of inks as well as some of the company’s most innovative inks and coatings for the food, cosmetics and pharma industries.
The applications on display included labels and narrow web pouches showcasing Actega’s LED-UV and waterbased flexo inks and coatings. Samples of haptic and visual effect coatings for shrink sleeves were also on display.
These coatings are applied on the outside of the shrink sleeve to give extra impact on the shelf and the variety of high-value effects achievable include soft touch, matte and raised image. Special LED-UV coatings for the internal part of the sleeves were also on display and experts from the Actega team were on hand to explain the numerous functional benefits of applying these coatings.
In addition, information, samples and news about Actega’s solutions for sustainable label decoration including Signite and Ecoleaf were available.
Actega’s Signite decoration solution enables brands and converters to significantly reduce waste, while providing expanded design flexibility and recyclability and reuse possibilities. As for Ecoleaf, it was demonstrated live on press with AB Graphic.
substrates. It also incorporates static control, web cleaning and corona treatment for wide choice substrate printing capability.
Dantex’s Pico range of digital UV inkjet printing presses, as well as its related consumables for the A/NZ region, is available from Nekkorb Solutions.
DuPont presented its latest Cyrel technologies and solutions to improve label printing/converting and create new business goals.
At its booth, DuPont focused on highperforming innovative technologies to address label converters’ challenges to achieve their sustainability, productivity, and quality goals, including Cyrel FAST, which is a thermal platemaking system that consists of a thermal processor and a large variety of photopolymer printing plates for flexible packaging, labels and other applications.
The Cyrel FAST system offers superior productivity and performance while helping to reduce processing costs, time, and environmental impact compared to the existing solvent method. By eliminating the use of solvents – including water – from the platemaking process, the Cyrel FAST system requires no drying time and plates can be ready for print under 45 minutes, according to the company.
“The system is an achievement of more than 20 years of continuous evolution and investment into this platform and has resulted in more than 1500 installations globally. And this year we hit the 200th installation of our most popular version, the FAST 2000 TD,” DuPont Cyrel general manager Tucker Norton said.
“We consider the show a great opportunity to get closer to the label converters, and reinforce our solutions for a more sustainable printing in flexo.”
Dantex Digital, part of the Dantex Group, was at Labelexpo Americas showcasing its Dantex PicoJet 1200S hybrid press.
The machine has a print width of 330mm (13-inches) and runs at high speed – 75m per minute. It can be custom configured either as CMYK, CMYK plus white and/or additional colours stations of orange, violet and green. The PicoJet 1200S is the latest version of the Picojet 330S. The PicoJet also uses energy-efficient LED final cure with temperature-controlled backup roller for temperature-sensitive
that it says delivers on the need of brand owners and converters to connect and integrate the entire value chain through upstream digitalisation.
Esko said the acquisition was made as Tilia Labs’ range of intelligent algorithms for sheet layout, estimation, and planning complements its existing software suite, with the two companies now working together to develop next-generation integrated solutions.
“Converters are coming under increasing pressure to deliver more volume with shorter print runs to bring versatility to the market, while the adoption of digital printing continues to grow,” Danaher Corporation (Esko parent company) product identification vice-president and group executive Mattias Byström said.
“This acquisition demonstrates our ongoing commitment to providing integrated software and hardware solutions that accelerate the go-to-market process for consumer-packaged goods.”
Byström said the combined solutions within its software platform enable Esko to better serve its customers in the packaging, label, and wide format markets.
“This acquisition also underlines our commitment to delivering the tools that serve to connect brands and converters upstream. For all our customers continuing their digital transformation journey, the integration of these next generation tools means businesses will be able to digitise, automate and connect more efficiently to drive significant workflow and operational advantages, as well as sustainability benefits.”
Esko took to Labelexpo Americas to discuss its recent acquisition of Canadian AI software company Tilia Labs, in a deal
Flint Group Narrow Web took to Labelexpo Americas to showcase new waste and cost-saving ink and coating products that offer improved recycling, food safety, global quality consistency and lower energy consumption.
Flint Group’s Evolution series of UV-flexo coatings allow the substrates and containers they are used on to be recycled without contamination, and therefore be reused more easily.
The Evolution Deinking Primer is applied to shrink sleeves to allow the ink to be released during the recycling process. The ink is removed from the sleeve material without contaminating the valuable bottle flake. The materials are then rinsed and pelletised into recycled polyester (rPET) for reuse.
The Evolution Caustic Resistant Over Print Varnish facilitates the recycling of PET bottles utilising pressure-sensitive labels. The varnish prevents contamination of the wash-water and bottle flake in the initial recycling process by keeping the ink secured to the label substrate. When immersed in the float-sink bath, the intact label floats to the surface where it is separated from the bottle recycling stream.
Flint Group Narrow Web also presented its expanded range of Dual Cure UV-flexo inks that are curable under LED lamps as well as mercury lamps. The company’s new Dual Cure products focus on ultraclear non-yellowing performance and food contact materials (FCM) applications.
Dual Cure Ultra Clear is a UV-flexo clear overprinted coating, that does not yellow over time. Free of benzophenone, it offers long-term brand integrity and product safety.
At Labelexpo Americas, Gallus and Heidelberg confirmed that their first fully-digital label press, the Gallus One, will be released at the beginning of the second quarter of 2023.
The Gallus One machine was not shown at LabelExpo in Chicago. The company told ProPack.pro it was decided that removing a prototype from the research and development phase could set back the planned release date.
The fully digital Gallus One label printing system is based on the Gallus Labelmaster press platform.
The system is geared toward the costefficient and sustainable production of high-quality labels, aiming to deliver a reliable return on investment (ROI) for a wide range of customers.
As a reel-to-reel UV inkjet digital inline label press with a width of 340mm, a resolution of 1,200 dpi, four colours plus white, and a print speed of up to 70 metres per minute, it is suitable for a whole host of applications.
Gallus One can also be fully integrated into the Prinect workflow from Heidelberg. Developed jointly by Heidelberg and Gallus, the system combines the digital printing and
software know-how of Heidelberg with the extensive expertise of Gallus in label printing.
While the Gallus One is currently available for pre-order, there has been no sales confirmed currently from the entire Southern Hemisphere including the Asia Pacific region.
At the show, Gallus also confirmed that a new Experience Centre previously slated to open at the end of this year will also open in April 2023 at St Gallen in Switzerland.
Gallus chief sales and service director, Dario Urbinati, spoke at Labelexpo in Chicago and told visitors the Gallus One “is not just a new printing machine but the start of a new era for Gallus and Heidelberg”.
HP
HP has provided the label industry with the first glimpse of the Indigo V12 Digital Press with a show-stopping arrival on its stand at Labelexpo in Chicago.
Visitors were three and four deep across the 15-metre face of the machine for most days of the show to see the new printer for themselves.
The Indigo V12 is the first press to utilise LEP X technology that the company claims will be ‘industry-altering’ –delivering 120 linear metres per minute with 12 HP ElectroInk stations and 1600dpi image resolution.
The LEP X multi-imaging architecture incorporates six imaging engines – each making its own colour separation on the blanket belt simultaneously. The new LEP X writing heads feature thousands of LEDs to compose an image as an electrostatic field at 1600dpi.
The V12 is HP’s Series 6 press and it is completely redesigned from the ground up. The V12 is a press that has been in development for several years. It runs narrow-web at a speed of four times faster than anything seen before with the traditional HP Indigo ElectroInks.
The machine can run 12 colours on it simultaneously and is expected to be globally released at the end of 2023 locally through Currie Group.
Key features of the HP Indigo V12 Digital Press include: six inline imaging engines running simultaneously; new high definition imaging; up to 12 colours on press capabilities; and one-pass, highspeed finishing capabilities provided by AB Graphic.
The Indigo V12 also meets sustainability targets with up to 90 per cent saving in
media waste as there are no plates to discard and requires no hazardous cleaning fluids.
Labels and packaging software solutions company Hybrid Software showcased its recent acquisition of iC3D by showing 3D visualisation throughout the entire prepress process at Labelexpo Americas.
One of the highlights was the integration of PACKZ and iC3D, allowing Hybrid Software users to visualise 3D packaging in real time, from labels and flexible packaging to shrink wrap products. iC3D is an all-in-one visualisation software package that lets users generate live 3D virtual mockups on-the-fly.
Other highlights at the show included:
Version 8 version of PACKZ – Hybrid Software’s native PDF editor with enhancements including complex layered artwork that can now be viewed in colour and wired modes simultaneously, and object-based screenings can be inspected per separation.
STEPZ 8 – An interactive software package based on the award-winning technology of PACKZ, which allows for the preparation and execution of step-and-repeat and variable data tasks for high-speed digital printing of labels.
Variable Data Printing (VDP) – Highlighting the ease of use and capabilities of the variable data preparation and execution of files, while providing customers the use of any open output device they require.
CLOUDFLOW – Demonstrating workflow management controlled from a webbrowser.
SmartDFE – Combining products from all Hybrid Software Group companies to provide a turnkey digital front end (DFE) for high-speed digital presses.
Converting and packaging machines supplier Karlville put its K3 Plus shrink sleeve seaming machine on display at the tradeshow.
The new Plus series is one of the most advanced seamers in the industry. Karlville said this is the third generation of seamers which eliminates the forming tool.
This new design makes the most operator friendly machine available, facilitating training with an automated machine. The difference between a K2 and a K3 model is that the K2 utilises a brake on the unwind, while the K3 is motorised.
The machine has three tension zones, which allows for a dedicated tension zone for the forming section for better lay flat control. The unwind tension zone is now free to add innovations like laser integration or pin hole perforation while the film is flat.
The Plus also offers a long list of advantages that aims to solve the issues that come with the previous generation of machines that use forming tools. This new machine promises to revolutionise the way shrink sleeves are converted.
Karlville has support facilities in US, Europe, and Asia, servicing a global customer base. It is available locally through Currie Group.
For packaging manufacturers, it also offers a solution for quickly creating mock-ups of packaging designs, helping to improve time-to-market and reduce waste.
The company also unveiled the AccurioLabel 400 five-colour label press for the first time in the US. The AccurioLabel 400 allows customers to expand their businesses in the growing markets of digital label production and packaging. The press incorporates all of Konica Minolta’s technology, including the Intelligent Quality Optimiser (IQ-520) colour management functionality for real-time colour stability and registration control.
The AccurioLabel 400 offers a fifth well for white toner to expand creative label applications, plus resolution equivalent to 3600 x 2400 dpi and many automated control features for highly productive output.
Konica Minolta also showcased the AccurioLabel 230 digital label press and GM DC330 Mini. Together with Konica Minolta’s label presses, the GM DC330 Mini aims to provide an end-to-end, compact digital label print and finishing solution. This label finisher allows users to add UV varnish with options for spot UV varnish, laminate, super-gloss and cold foil. It can also die-cut, slit and rewind to provide finished labels.
terms of finishing time – for smooth, fast processes with low amounts of waste. Its performance and process reliability are specifically tailored to industrial requirements, so that finishing, even of the shortest runs, always remains profitable.
Depending on the substrate, the DM-Uniliner 2D can process up to 75 roll metres per minute. Roll diameters up to 800mm enable long running times without roll changes. The designs to be finished can be metallised either before the overprinting process or afterwards.
The stand-alone unit is therefore predestined for the finishing of web labels. In addition, the Kurz Multi-Use function is also available in the DM-Uniliner 2D as up to three transfer runs are possible depending on the design – for maximum usage of the metallisation layer and increased sustainability of the product.
Xeikon, a division of the Flint Group, had on display a range of its latest solutions and applications including its hybrid printing machines, Cheetah 2.0 portfolio and Panther 2.0 technology.
Xeikon Cheetah 2.0 dry toner technology is now cloud-connected with man/machine and machine/machine interfaces where the machines are in constant communication with each other, driving and monitoring print jobs with full automation.
Earlier last year, Xeikon introduced two new models: the CX30 and the CX50 entry level dry-toner presses. With each cloudconnected solution, operators can monitor print manufacturing from anywhere on the shop floor by viewing the interfaces/dashboards 24/7 on a smartphone or any other device.
Kurz was at Labelexpo Americas, showcasing its DM-Uniliner 2D digital embellishment machine, which is a stand-alone metallisation unit for brilliant 2D effects on labels.
Konica Minolta unveiled two important new products at Labelexpo Americas – the PKG 1300 packaging press for boxed material and the AccurioLabel 400 label press.
The PKG 1300 is an upgrade to Konica Minolta’s PKG line, and now includes an automatic feeder and stacker. It is a highquality inkjet printer for printing short-runs of custom corrugated and folding cartons, flat or pre-cut, quickly and economically.
The digital embellishment unit, which is independent of printing systems and equipped with inkjet technology, was designed for the narrow-web sector. The special feature – metallisation – can be applied in pre-print or postprint processes.
The overprinting of the metallised designs or holographic structures creates a variety of iridescent colour and light effects. The DM-Uniliner 2D transfer machine aims to offer maximum flexibility in
At Labelexpo Americas, Xeikon introduced new application capabilities for Cheetah 2.0, including gold and silver toners.
Xeikon was also at the event to provide more information about its Titon toner technology. This was not on demonstration at Labelexpo Americas.
Xeikon’s Titon technology is a new heatresistant, food-safe and dry-toner formulation offering all the benefits of UV inks without the disadvantages. It aims to meet industry needs for sustainable printing methods and environmentally friendly paper-based flexible packaging production.
The other technology that was on display is Xeikon’s Panther 2.0 technology for UV inkjet, which is targeted at durable labels as well as health and beauty labels.
Labelexpo Americas recently took place in Chicago, with thousands of people from all over the world attending the event. Printers/converters, brand owners, designers, and suppliers from the labels, flexible packaging and folding carton industry flocked to the Donald E. Stephens Convention Centre, where it was held. Many familiar faces were spotted in the halls of the tradeshow, as pictured here:
Two significant innovations in the HP Indigo 35K Digital Press are Spot Master and High Definition (HD).
Patented by HP, Spot Master is an automated colour calibration process. With spot master, the machine will create a number of patches to reach the target shade. The sheet printed with these patches goes through an inline spectrocolorimetric control. It reaches the target on average in only three sheets. This process saves time and waste and allows the operator to easily validate the colour.
Daws says, “You can have confidence in your colour performance with the automated tools and reporting system to easily reach and maintain colour, ensuring consistency and accurate repeatability, time and again.”
HP said its HP Indigo customers created the digital box packaging market, using the platform’s capabilities such as on demand printing and sustainable packaging.
Supplied through Currie Group, and dedicated to the folding carton sector, the HP Indigo 35K Digital Press delivers a range of benefits.
Currie Group A/NZ director of labels and packaging Mark Daws said, “The HP Indigo 35K Digital Press answers the market demand for short, medium and value add print runs, enabling you to occupy a position in the high value market with its wide application range. It offers an end-to-end approach with inline priming, fully coupled coater, and the HP PrintOSX workflow ecosystem.”
With customers increasingly looking for boxes that go beyond basic, HP Indigo has filled the HP Indigo 35K Digital Press with capabilities that cater for the growing interest in product authenticity, sustainability, and a higher level of enduser engagement.
HP Indigo has also responded to the need for greater environmental responsibility, more SKUs, personalisation, and faster time
to market. HP internal analysis shows B2 as the optimal, more cost-effective format for short runs.
The trend toward boxes with digital features continues to gain momentum. Daws said, “The HP Indigo 35K Digital Press enables you to cater for both ends of the spectrum and the points between, giving you the flexibility you need to compete.”
The HP Indigo 35K Digital Press enables you to produce dozens of jobs per day and up to one million B2 sheets per month. It prints on paper and cardboard from 150 – 250 microns (pre-primed paper), and 250 to 600 microns thick. It also prints PVC, polypropylene and PET, depending on media thickness. Daws added, “You can expand your offering with off-the-shelf boards, from paperboards, through metallised and synthetics media, to high-end coloured substrates. The HP Indigo 35K Digital Press meets the most stringent brand colour and quality needs. You can achieve up to 97 per cent Pantone gamut on press using CMYK, OVG, and spot colours.
“It also offers HP Indigo ElectroInk Premium White for higher opacity and the new ElectroInk Invisible Yellow for track-and-trace solutions and security elements for multilayered brand protection applications.”
The new High Definition (HD) writing heads feature allows for an increase from 800 dpi to 1600 dpi. With HD writing heads, and HD RIP, print dots are up to 30 per cent smaller and screen ruling reaches 290 LPI. HP says you can produce smoother colour tints, more detailed small images, and finer small/ micro text with the HD Imaging System.
High Definition also has specific application for the secure printing of packaging. It allows for micro text, and combined with HP’s other capabilities (such as invisible inks or personalisation), this option enables the manufacture of value-added products.
Unlike offset, HP Indigo technology offers customisation and serialisation, all in one pass. There is no need to transfer products to a second machine to apply a unique serial number or QR code. This generates a saving of space; reduction in waste; an increase in reactivity; and a reduction in costs.
You can also offer value added packages like multi-layered brand protection solutions and distinctive designs by HP SmartStream Mosaic and HP SmartStream Collage.
TRESU iCoat II, an optional feature, enables high-accuracy embellishment features. You can produce offset quality for overprint varnish and coating applications using industry standard UV or water-based varnish in a single production pass, now optimised for high accuracy varnish registration at full speed.
The industry should accept smart labels and the progress it provides sooner, and challenge the concept of a divide between the ‘real world’ and the digital space
By Seamus MayAcross the Australian wine industry, producers both big and small are considering inventive new ways to engage with consumers through their packaging.
The progress of ‘smart’ technologies shows little signs of slowing, and the drinks industry is no exception. Over recent years, producers and brands have looked to augmented reality (AR), apps and QR codes to provide their products with an edge when connecting with drinkers in the increasingly contested retail market.
Mount View Media is a Hunter Valley based digital and multimedia company working with producers to add technological
enhancements to their products, as owner, Andy McLennan, explained.
“We’ve got about 10 different winery clients here in the valley, and we work closely with Hunter Valley Wine and Tourism, producing digital content and media for them,” McLennan said.
“Labelling is a new thing we’re delving into. We’ve always done branding and packaging, and we’ve designed lots of traditional labels, but now we’re looking at doing some things where the label does more than just telling you what’s in the bottle.”
One project Mount View Media is currently working on is the placement of QR codes on certain bottles of De Iuliis wines. Customers will be able to scan the codes,
which will take them to a landing page where they can view videos and tasting notes from the winemaker.
“So whether you’re at home, buying online, wherever you may be, you can hear from the person who’s making this product – what they’ve done to create this wine, what the intention is with it, what it is like, and the things that get the winemaker excited about it,” McLennan said.
“Mix it up with some nice graphics and it can be quite an engaging experience to learn about the wine.”
McLennan said AR is another area that his company are exploring, developing graphics that would appear around bottles when consumers point their camera or an app
at the label – providing almost ‘visual tasting notes’.
“You could have a vine growing outside of the bottle, but you could also have food matching, or flavour profiles,” McLennan said.
This is almost exactly what South Australian wine brand, Press + Bloom have developed in partnership with LabelMotionAR, an app that allows brands to add AR technology to their packaging.
Sam Evans, assistant brand manager for Vok Beverages (the owner of Press + Bloom), provided some context as to how this feature functions.
“The technology we use with LabelMotion is similar to a QR code, where the camera recognises certain shapes in our label artwork and allows a video to play on the application,” Evans said.
“The video is a highlight reel showcasing some of the stages of production and our winemaking team hard at work, giving a glimpse of the brand’s story.”
Evans said the labels have been a hit with consumers, adding, “We’ve had fantastic response, which created a lot of buzz at our launch and provided great a talking point at a store level for our customers to share with shoppers, with many Press + Bloom advocates in stores nationally showing shoppers how to use the app.
“The highlight has been the social media engagement from consumers and getting to see people drinking our wine with friends and watching our labels on Instagram.”
Evans said there is great value in this technology for retailers, and this was a significant motivating factor for the brand to create the AR feature in the first place.
“For us the added level of value to consumers is what drew us. Giving them a more interactive experience with our
bottles, as opposed to being a vessel that’s opened, consuming and discarding,” he said.
“It gives us a platform to story tell and allow them to visual that our hardworking team do to turn grapes into liquid in a bottle. From a business-to-business perspective, it gives our customers something fun and engaging to talk to their customers about, which is always one of goals for our wines.”
Another brand that is innovating in this area is Yarra Valley based winery, Innocent Bystander, which has developed a social game that consumers can access by scanning a QR code on its wines. The game, named ‘Who Of Us?’ is designed to provoke conversation and connections between drinkers.
The game requires no additional downloads and can simply be accessed through the internet.
Innocent Bystander brand manager, Andrew Dix, said, “In its simplest form, Who Of Us is a game to enjoy with your friends while you kick back with a glass of Innocent Bystander wine. You can access by scanning a QR code featured on our most popular bottles including Innocent Bystander Pinot Noir, Pinot Gris, Moscato, Prosecco and Rose.
“Think ‘Kahoot’ meets ‘Cards Against Humanity’ – it’s a multiple-choice trivia game, where you nominate friends who you are playing with, who are likely to display a provocative series of wicked or innocent behaviours.
“We wanted to create something unique to the alcohol industry that adds value to the consumer and that genuinely adds to the drinkers enjoyment of the occasion.”
While Dix said there is no immediate conventional financial benefit, the game does serve to find new audiences and deepen consumer relationships.
“You get a deeper level of engagement when someone proactively scans a QR code with the line ‘a social game for the wicked’ as the driver,” Dix added.
“It does a pretty amazing job in finding your like-minded humans, and the feedback we have been getting has really been exceptional by way of building a community.”
Eventually, Dix said he believes technology like this will increase purchases, and impact the bottom line for both brands and retailers.
“As people rely more and more on their device as the main source of truth for their shopping visit – reviews, tasting notes, rankings and competitor pricing is at their fingertips, Innocent Bystander is using this packaging innovation to offer an unconventional experience to consumers and create a little intrigue and enjoyment as a way to encourage people to pick up a bottle of Innocent Bystander over the next competitor,” Dix said.
In the same vein, McLennan said there is the opportunity to take these features even further, adding, “I’d have the winemaker all of a sudden appear next to the bottle talking about it, as a hologram almost.”
McLennan also said there are hardnosed business opportunities contained within the creativity of AR-enhanced labels.
“With permission from the consumer, we can capture where it was scanned, how many times it was scanned, which product it was, how many times that product has been activated,” he said.
“And the data captured there is very useful. You might find that ‘Hey, down on the coast, we seem to be getting more rosé and Semillon, while up in the Hunter it’s generally Shiraz.’ That’s kind of a phase two of the development.”
McLennan added that the industry should accept this technology and the progress it provides, sooner rather than later, and challenged the concept of a divide between the ‘real world’ and the digital space.
“There can be a lot of resistance against change or something with technology. But I feel like these technologies are worth exploring, to bring older brands into the current digital market we have. The digital world is the future, you’ve got to constantly evolve,” he said.
“It’s as ‘real’ as what people emote from it. A movie on your screen is just ones and zeros, but it makes you feel a certain way, so it’s just as real as anything else.”
What does the industry need to do to minimise the ecological footprint of packaging as well as other printed products?
As part of its ‘Circular Competence’ series, the VDMA Printing and Paper Technology Association has asked some of its member companies about their plans, solutions, and challenges on the road to a circular economy.
In this article, Dr. Eva Boll, head of corporate sustainability at Heidelberg, explains how the group is proceeding to meet its voluntary commitment to climate neutrality by 2030.
Q: By the middle of the century, the leading industrial nations want to have a climate-neutral economy. Is this goal realistic in your view?
Dr. Eva Boll (EB): In view of the progressing climate change and the global political situation, which makes us painfully aware of our dependence on fossil energy sources, I see the goal as quite realistic. However, it demands massive transformation efforts from the industrialised nations.
EB: In view of the voluntary commitment to climate neutrality by 2030, we are putting all processes to the test.
We have had an environmental management system for several years, are certified according to 14001 and defined clear environmental goals for our production sites years ago, which we implement through continuous improvement processes. It’s all about energy efficiency, which is usually directly linked to greenhouse gas (GHG) emissions.
With a view to our 2030 target, we are developing a transformation concept that considers the changed political framework conditions. After all, politics also clearly stipulates that we must become climate neutral. This forces us to question every process.
We are carrying out potential analyses at all production sites, with which we can reduce GHG emissions. Every kilowatt hour saved counts. We will also increase our own production of renewable energy. We already have photovoltaic systems, but we still see a lot of potential here. The purchase of green energy is another option.
On the other hand, we are critical of the purchase of GHG certificates for the neutralisation of our production sites. Offsetting is only an option for unavoidable emissions – for a transitional period until 2040, at the latest, after which we want to operate climate-neutrally under our own steam.
We can currently see how challenging this goal is with our combined heat and power plant, which runs on natural gas to generate electricity and heat. We need to find a new solution quickly. Whether hydrogen comes into question, biomass or a heat pump will
have to be clarified. What currently helps us is that we have developed many energy efficiency concepts in recent years that were not economically feasible due to low energy prices.
We are now drawing on this pool and exploiting all the potential: green electricity for the electric melting furnaces in our foundry, optimised compressed air, drive and drying technology and LED lighting. In the search for solutions, we exchange ideas with partners from research and our networks to learn from their best practices.
less energy than 20 years ago. On request, we equip the presses with energy meters to create transparency.
We also offer targeted advice to teach them energy-efficient operating strategies. This includes printing faster because the basic load is distributed over more output. A lot of attention is also paid to efficient drive technology, which is important in view of decreasing print runs and more frequent starts and stops.
Every development project goes through it. This ensures that every project is also based on ecological criteria.
In addition, we are pushing ahead with projects that focus on energy efficiency. We have been working in close partnerships with our suppliers for many years because innovations and the integration of more efficient solutions usually have an impact on installation spaces. This creates a need for coordination.
EB: Here, too, we can draw on years of experience. We have been carrying out life cycle assessments of our products since 2012 and have been offering our customers the option of making their machines climate-neutral through offset certificates for many years.
In our development, we generally subject new developments to an ecological product review, in which we focus not only on compliance with environmental laws in the target market, but also on energy efficiency.
These efforts are having an impact: to print 1,000 sheets with our presses, our customers need on average 40 per cent
Reducing waste and more efficient drying technologies are also on the agenda. The latter include the use of UV LEDs in UV printing, turbo radial instead of side channel blowers and reduced distances between the sheet and the dryer.
The push-to-stop philosophy we have introduced can also shorten makeready times, which also saves energy. In fact, more and more customers are asking for efficiency solutions because their clientele is also taking a closer look and the demand for climate- and environmentally friendly print products is rising rapidly.
Q: What role does the topic play in your research and development?
EB: The ecological product review already mentioned has been firmly anchored in our guidelines since 2013.
Our partners also give us information when regulatory innovations are announced in their area, so that we can develop solutions at an early stage. Of course, this also applies to climate neutrality throughout the entire supply chain.
Co-operation with research institutes and universities is also important – both regarding technological innovations and for questions of environmental and climate accounting. Because there is a lack of binding standards here, we are involved in standardisation committees under the umbrella of the VDMA.
Q: What would you like to see from legislators with regards to the road to climate neutrality?
EB: The industry needs planning security and binding rules that remain valid for longer than one legislative period. Compromises between security of supply and reduction targets as well as practicable support offers are needed.
In principle, the EU has set the right direction with the “Green Deal”. In Germany, there is broad agreement on the climate targets. However, the current need to compensate for the lack of natural gas with coal shows us the challenges of the transformation.
For companies that are not yet involved in European emissions trading, regulations such as the Corporate Sustainability Reporting Directive and the new EU taxonomy bring major changes. They are increasingly under pressure to minimise their GHG emissions and document their measures.
Despite all the criticism of the taxonomy, which also poses problems for us because it ignores large parts of our economic activities, I think the path we have taken is basically the right one. GHG emissions and the ecological footprint of products must first be recorded to develop meaningful reduction strategies.
There is a willingness to do this in the mechanical and plant engineering sector. Our industry has long since set out and is pushing forward engineering solutions for a climate-neutral industry with great seriousness. We at Heidelberg are actively pushing this development.
Q: How do you support your customers in producing more energy efficiently?
New Zealand’s premier awards, Pride in Print, recently took place at Christchurch’s new Te Pae events centre attracting a larger than expected audience of industry professionals and supporters. Labels and packaging was in the limelight with innovative businesses taking home wins.
Freyas wraps a double for Amcor Flexibles
Amcor Flexibles Asia Pacific Christchurch produced Freyas Gluten Free Mixed Seed Soft Wraps to win the Flexible Packaging Category and Flexographic Process Awards.
Designed as a pouch where the product, the wrap, forms part of the design presentation to the consumer, the job received high praise from judges.
They said, “Involving the reverse-printing of nine colours while simultaneously surface-printing an overgloss and then laminating and pouch-converting, this high complexity job has delivered crisp print and bright imagery to achieve a very realistic food picture.”
Mark Thian from Amcor Flexibles, said, “Our clients will be over the moon with the result. Amcor Christchurch has made a deliberate decision to move to lower ink film weights and where possible use water-
based alternatives to lower the process’ environmental footprint, but without detracting from the end results.
“The way the colour and matt finish has captured the look and feel of paper is most impressive. By winning these awards, the Freya’s pouch shows that there need not be a comprise on quality by adopting alternative methodology.
“The pouches are an in-house product. We extrude the sealant layer and print on the reverse-printing web.
“The printing process is a challenge involving reverse printing and surface printing inline as well as applying the patterned waterbased matt overgloss by gravure cylinder, totalling 11 flexographic stations overall, all in one printing pass and in register. We then laminate to our in-house sealant layer, slit and pouch, and install a resealable zip.”
ABC Original Print won the Structural Design Packaging Category with the Garnier Fructus Hair Food Presentation Box.
James Hedger from ABC Original Print, said, “We had limitations in the size and weight of the box as it was to be used for deliveries throughout New Zealand’s courier network.
“This was a challenge as L’Oreal New Zealand requested four large and heavy bottles of product be accommodated in the design. We used two inserts, one over the other, to separate and position each product to avoid movement, making it practical and making the products look organised and according with the concept.
“The 40EW2 corrugated cardboard gave us the flexibility to make detailed inserts capable of housing the product and acted as support to give the whole package the structural integrity required to withstand the rigors of the courier network.
“We printed the boxes digitally and doublesided. It was a challenge to register both printing sides accurately. Also, the inserts and handles of the box required precision in the cutting and assembly. However, it required very few points of glue, which made the box quite affordable, sustainable and efficient to produce.
“The artwork complemented the quality of the production with a play on the fruit extracts Garnier uses within its products, giving it a fun, striking aspect, while still communicating its brand effectively.
“Our team feels extremely grateful and proud to win the Structural Design Packaging Category and we would like to take this chance to thank our client, L’Oreal New Zealand, to trust us in the production of this job. They can feel confident that we have a great team who can design and produce projects from scratch with great design, great print and great customer service.
“Our client was extremely happy with the result. The pre-launch teaser they used
the box for was a success and resulted in higher-than-forecast sales.”
An uncompromising commitment to deliver a next level gin bottle label has seen Kiwi Labels claim the Labels Category.
Printed on an uncoated Forest Stewardship Council- certified stock produced from elemental chlorine free pulp, the job featured a high contrast hologram effect in perfect register.
Andrew Thomson from Kiwi Labels said, “Holland Road Gin is meticulously hand crafted and bottled in Eureka, New Zealand, and distributed to bars and restaurants throughout the country.
They had faith in our ability to lift the label to the next level and this collaborative response resulted in an amazing looking label.”
In addition to delivering brand credibility to Waitoa’s new sustainability drive, the award win also provided recognition to the environmental endeavours of Sealed Air and the overall SEE Corporation, Robinson said.
Logick Print won the Paper and Board Packaging Category with a set of Pure Mama Product Packaging boxes.
Judges remarked on the “excellent detailing, with elements such as pearlescent foiling, embossing and printing on foil”. They said, “It is quite rare to see a set of three product boxes delivered with no faults. The quality of the work stood out immediately.”
Holland Road Wild Ginseng 500ml Gin helped Kiwi Labels win the Labels Category
“The distinctive artwork and magical symbols in the label are a tribute to the ancient healers whose folk medicine pioneered modern distillation practices and a reflection of the passion that goes into each batch of this premium gin.
“When we received the captivating design, we wanted to take it to the next level to deliver striking artwork printed on a challenging double-sided black stock with detailed foiling and embossing. This required multiple passes to complete, but it was worth the effort.
“The five-colour digital print process built the foundation for this stunning label. We used a Xeikon press to transform the dense black stock into a highly detailed label. Prepress and production equally brought this detailed label to life with multiple hours invested into refining the artwork and tooling files to land on a superb- looking label that we are all proud of.
“Holland Road supported us throughout the process and were very happy with the result.
A high-quality example of print work, created with sustainability at the fore, has seen Sealed Air Hamilton claim the Industry Development and Creativity Category.
The Waitoa Applewood Smoked Chicken food wrap is a product of Sealed Air Hamilton’s 2018 global environmental pledge.
Judges said, “A clean and very wellexecuted print, this flexographic job has innovatively used a 70 per cent post-consumer recycled PET substrate that has FDA food compliance, with the final product achieving 91 per cent total recycled content.”
Damion Robinson from Sealed Air said the wrap marked the commercial rollout of the Waitoa brand refresh and highlighted the Carbon Zero delivery to market of its poultry offer.
“The print quality and ease of delivery for such an important brand refresh in the time slot given was impressive. Maintaining the Carbon Zero credentials is critical to the brand integrity. As the consumer continues to be overcome by so many sustainability aspects to their lives, Carbon Zero is tangible, and the packaging supports this effectively,” he said.
“Using recycled content input materials requires a lot of research, trials, review and collaboration of various teams, so that the final product exceeds the buyers’ and ultimately the consumers’ expectations, all the while being completely certified food safe.
“Our integration of FDA Food Law Approved for Direct Food Contact recycled content resin supports SEE Corporation’s drive to support circulatory of post- consumer use of food packaging.”
David Gick from Logick Print said, “The client’s brief was to deliver a luxurious packaging box, with clean uncomplicated embellishments, that was sustainable and locally produced. It was something different from the norm. This style of design highlighted layers of tactility to be luxurious, modern and minimalist.
“So Colour Plan was the board chosen in Pristine white colour shade, then the foils to complement that with a pearlescent solid bar and a new Foilco sheen foil, finishing it off with a sharp blind emboss of the Pure Mama logo.”
Logick has worked with several start-ups.
Gick said, “It is always interesting to follow them on their journey. Pure Mama has been no different, we have followed their growth through the local market. They are now exporting to Australia with more export markets coming online shortly.
“One of their customers provided feedback that the packaging ‘blew them away’, so they knew the product was good. The connection between the packaging and product has been correctly linked.”
A set of three Pure Mama Product Packaging boxes earned Logick Print the Paper and Board Packaging Category award
continue to account for around 20 per cent and 50 per cent of plastic waste respectively.
The share of plastic that evades waste management systems – ending up instead in uncontrolled dumpsites, burned in open pits or leaking into the soil or aquatic environments – is projected to fall to 15 per cent from 22 per cent.
The new report builds on the OECD’s first Global Plastics Outlook: Economic Drivers, Environmental Impacts and Policy Options, released in February 2022.
That first report found that plastic waste has doubled in two decades, with most ending up in landfill, incinerated or leaking into the environment.
The amount of plastic waste produced globally is on track to almost triple by 2060, with around half ending up in landfill and less than a fifth recycled, according to a new OECD report.
Global Plastics Outlook: Policy Scenarios to 2060 says that without radical action to curb demand, increase product lifespans and improve waste management and recyclability, plastic pollution will rise in tandem with an almost threefold increase in plastics use driven by rising populations and incomes.
The report estimates that almost two-thirds of plastic waste in 2060 will be from shortlived items such as packaging, low-cost products, and textiles.
“If we want a world that is free of plastic pollution, in line with the ambitions of the United Nations Environment Assembly, we will need to take much more stringent and globally co-ordinated action,” OECD secretary-general Mathias Cormann said.
“This report proposes concrete policies that can be implemented along the lifecycle of plastics that could significantly curb –and even eliminate – plastic leakage into the environment.”
The report (available as a preliminary version ahead of its full publication later this year) projects global plastics consumption rising from 460 million tonnes (Mt) in 2019 to
1,231 Mt in 2060 in the absence of bold new policies, a faster rise than most raw materials.
Growth will be fastest in developing and emerging countries in Africa and Asia, although OECD countries will still produce much more plastic waste per person (238 kg per year on average) in 2060 than non-OECD countries (77kg).
Globally, plastic leakage to the environment is seen doubling to 44 Mt a year, while the build-up of plastics in lakes, rivers and oceans will more than triple, as plastic waste balloons from 353 Mt in 2019 to 1,014 Mt in 2060.
Most pollution comes from larger debris known as macroplastics, but leakage of microplastics (synthetic polymers less than 5mm in diameter) from items like industrial plastic pellets, textiles, and tyre wear is also a serious concern.
The projected rise in plastics consumption and waste will come despite an expected increase in the use of recycled plastic in manufacturing new goods as well as technological advances and sectoral economic shifts that should mean an estimated 16 per cent decrease by 2060 in the amount of plastic required to create USD 1 of economic output.
The share of plastic waste that is successfully recycled is projected to rise to 17 per cent in 2060 from nine per cent in 2019, while incineration and landfilling will
Since that report release, UN member states have pledged to negotiate a legally binding international agreement by 2024 to end plastic pollution.
Global Plastics Outlook: Policy Scenarios to 2060 looks at the impact of two potential scenarios.
The first, a regional action scenario comprising a mix of fiscal and regulatory policies primarily in OECD countries could decrease plastic waste by almost a fifth and more than halve plastic leakage into the environment without a substantial impact on global GDP, which would be lower by 0.3 per cent by 2060.
The second, a global action scenario comprising more stringent policies implemented globally, could decrease plastic waste by a third and almost eliminate plastic leakage to the environment while lowering global GDP by about 0.8 per cent.
The report also looks at how actions to reduce greenhouse emissions could reduce plastic pollution given the interplay between the plastics lifecycle, fossil fuels and climate change.
Policies to reduce the environmental impacts of plastics and encourage a more circular use of them should include: Taxes on plastics, including on plastic packaging Incentives to reuse and repair plastic items Targets for recycled content in new plastic products Extended producer responsibility (EPR) schemes Improved waste management infrastructure Increased litter collection rates.
NEW! LED-UV now available to all 2021 ushers in a new chapter to LED-UV dry-to-dry printing system. It is now made available to all makes and models of offset printing machines. Starting from $90,000, come join the LED-UV revolution.
Energy-Saving & Environmentally-Friendly LED-UV dry-to-dry printing system. Pioneering success, first introduced in Drupa 2008. Ryobi single-handedly led the industry in LED-UV printing. This revolutionary, award winning printing system offers impressive cost-savings by greatly reducing replacement frequency, power consumption, installation space and peripheral equipment space, while eliminating the odor of UV printing.
The defecto standard for small lot on-demand printing today, it is an important strategic advantage in being able to provide high-quality, small lot on-demand printing at low cost.
Now, 13 years later, Cyber is applying our wealth of expertise as an LED-UV pioneer to provide the printing industry with innovative solutions that meet your needs.
Rediscover the joy of printing…
Printing
Sydne